Werksbesichtigung:Holland Composites, Lelystad, Niederlande
Katamarane folieren, Fassaden bauen und mehr. Holland Composites liegt weniger als eine Autostunde von Amsterdam entfernt und verfolgt auf seinen 4.500 m² 2 . eine Vielzahl hochtechnischer Projekte Einrichtung. Quelle, alle Bilder | Holland Composites
Holland Composites (Lelystad, Niederlande) ist in einem 4.500 Quadratmeter großen Gebäude weniger als eine Autostunde von Amsterdam entfernt und konzentriert sich auf vier Märkte:Marine/Offshore, Architektur, erneuerbare Energien und Sonderprojekte. Holland Composites verwendet eine Mischung aus kohlenstofffaserverstärktem Prepreg-Polymer (CFK) und Nomex-Wabenstruktur für hochbelastete Teile sowie Harzinfusion und Glasfaser für die Bauindustrie und Projekte mit geringeren Margen. „Selbst mit diesen kostengünstigeren Konstruktionen sind wir in der Lage, eine hohe Leistung zu erbringen, und wir halten die Gemeinkosten für die Teile mit fortschrittlichen Materialien niedrig“, sagt Sven Erik Janssen, Co-Geschäftsführer von Holland Composites, zusammen mit Gründer Pieterjan Zwergenhaus. „Das ist einzigartig.“
Das Unternehmen betreibt auch die Marke DNA Performance Sailing und produziert folierende Mehrrumpf-Segelboote, darunter den 5,5-Meter-Katamaran F1X, den 11-Meter-Trimaran TF10 und den 14-Meter-Katamaran F4. Der 12 Meter lange G4-Katamaran wird nicht mehr produziert, „aber er demonstriert unsere Fähigkeiten für den fortschrittlichen Yachtbau aus Verbundwerkstoffen und hohe Leistung“, bemerkt Janssen. „Dieses Boot ist ein Zweizweck-Foiling-Racer und Familienkreuzer mit Kojen, Küche und Kopf, erreicht aber eine Geschwindigkeit von mehr als 35 Knoten. Die Fähigkeit, mit mehr als 4.000 Kilogramm Gewicht und nur einer sechsköpfigen Crew zu folieren – es gibt auf diesem Gebiet noch keine Konkurrenz außer den millionenschweren America’s Cups-Yachten.“
Marine-zu-Straße und Luftverkehr
Bevor der Rundgang beginnt, gibt Janssen einen Überblick über die Geschichte des Unternehmens und der von ihm hergestellten Verbundkonstruktionen. Holland Composites wurde 1992 von Janssen und Dwarshuis gegründet, die zu dieser Zeit Studenten an der Technischen Universität in Delft (TU Delft, Niederlande) waren. Sie bauten Kohlefasermasten für Hobie-Segelkatamarane, 1993 einen 18-Meter-Yacht-Tender aus CFK und Nomex-Waben und 1994 eine 100-Fuß-Segelyacht mit Harzinfusionsverarbeitung Kohlefaser mittels Prepreg oder Infusion“, erinnert sich Janssen. Da das Geschäft jedoch den typischen Höhen und Tiefen des Schifffahrtsmarktes und einmaligen Projekten ausgesetzt war, fügt er hinzu:„Wir wollten diversifizieren, wollten aber bei fortschrittlichen Verbundwerkstoffen gegenüber FRP bleiben [was weniger fortschrittliche, mehr handelsübliche Glasfasern bedeutet und Polyesterharz].“
Das Unternehmen begann mit der Erforschung von Leichtbaulösungen für den Straßenverkehr und produzierte 35 Lkw-Anhänger mit einem Monocoque-Chassis aus Glas-Kohle-Faser-Verbundstoff, die 3.500 Kilogramm Gewicht einsparen. „Die Lastwagen trugen dichte Ladungen wie Kartoffeln und erreichten ihr maximales Gewicht, bevor sie ihr Volumen füllten“, erklärt Janssen. Holland Composites stellte auch Kühlanhänger her, fügt er hinzu:„Aber wir waren etwas zu früh; Der Markt war noch nicht bereit – Unternehmen konnten noch nicht berechnen, welche jährlichen Gewinne durch den Transport von mehr Fracht und Wartungseinsparungen der Verbundanhänger im Vergleich zu ihren höheren Anschaffungskosten erzielt werden.“
Etwa zur gleichen Zeit trat VRR (Rotterdam, Niederlande), ein Anbieter von maßgeschneiderten Luftfrachtlösungen, an das Unternehmen heran. „Sie haben für Airbus, Boeing und die Fluggesellschaften gearbeitet“, erinnert sich Janssen. „Wir haben einen federleichten Container mit einem Monocoque aus Carbon/Aramid-Faser-Verbundwerkstoff entwickelt, der in Sachen geringes Gewicht bis heute seinesgleichen sucht“, sagt er. Obwohl Holland Composites einige Tausend davon herstellte, war der Markt schnell mit kostengünstigen GFK-Produkten gesättigt.
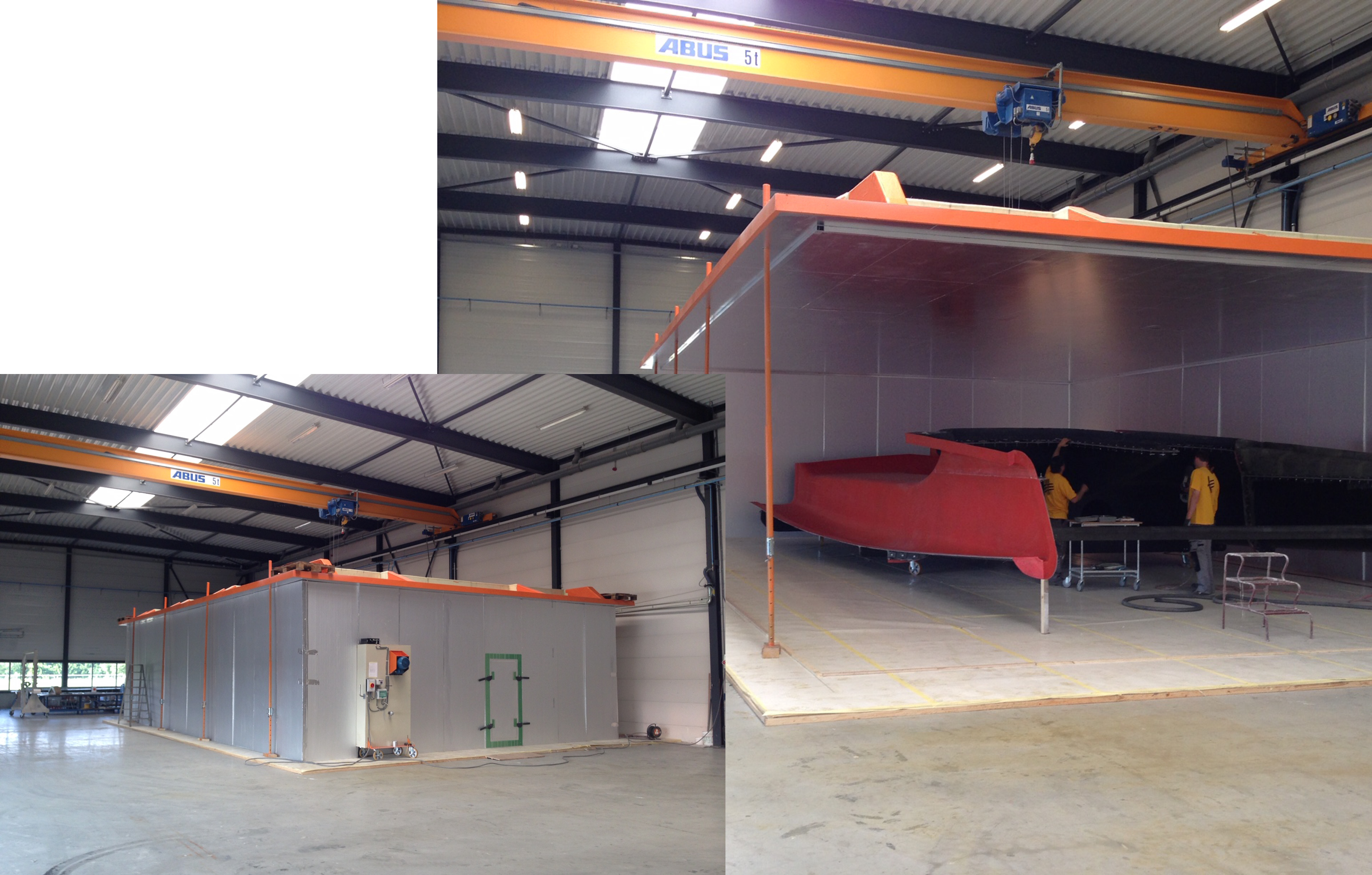
OOA-gehärtete Strukturen. Große Carbon-Verbundstrukturen für die Multihull-Segelboote der Marke DNA Performance Sailing werden in flexiblen Öfen (rechts) aus isolierten Paneelen mit Heizung und Luftzirkulation computergesteuert von einer Außeneinheit (Einschub) ausgehärtet.
Marine bleibt eine Kernstärke
1999 wandte sich die niederländische Marine an Holland Composites, um Sonarkuppeln aus massivem Glasfaserverbundstoff für U-Boote herzustellen. „Diese wurden traditionell in zwei Hälften gebaut, die zusammengeklebt wurden“, sagt Janssen, „aber die Naht verursacht eine Störung im ‚Sichtfeld‘. Wir wurden gebeten, diese in einem Stück zu bauen. Diese Sonarkuppeln sind groß – 11,5 mal 3 mal 3 Meter und 45 bis 110 Millimeter dick – und schwer zu infundieren, sie bestehen aus 5.000 Kilogramm Vinylester/Epoxid-Hybridharz von Romar-Voss Composites (Roggel, Niederlande). Die fertige Struktur wiegt 6.500 Kilogramm. Sie müssen steif sein und knallenden Belastungen standhalten, da sie sich im vorderen Teil des Rumpfes befinden. „Außerdem müssen wir die Dichte und Sonartransparenz des Wassers anpassen“, sagt Janssen. „Wir tun dies für Schiffe vom Zerstörertyp für einige Seestreitkräfte auf der ganzen Welt.“
Am anderen Ende des Gewichtsspektrums stehen die DNA Performance Multihulls. „Unsere kleinen Boote waren die ersten Foiling-Katamarane im Wettbewerb“, sagt Janssen. Holland Composites produziert auch die Verbundtragflächen für rekordverdächtige Rennyachten wie das MOD70 Team ARGO und Beau Geste . „Wir haben eine interne Technik, die wirklich hochbelastete Teile fehlerfrei herstellen kann, und ein einzigartiges One-Shot-Produktionsverfahren für diese sehr leistungsstarken Folien“, fügt er hinzu. „Wir arbeiten mit den besten Seglern der Welt zusammen, um die nächste Stufe der Foiling-Leistung zu erreichen und alle Foils für die Boote der NACMA17 Olympic-Klasse zu produzieren.“
Das leichte CFK-Deckhaus, das Holland Composites für Service-/Supportschiffe von Windcat Workboats produziert (siehe „Gewichtsreduzierung durch Verbunddeckhäuser“), verwendet eine harzverstärkte CFK-Schaum-Sandwich-Konstruktion für Steifigkeit, um eine große, offene Spannweite ohne Säulen in der Kabine zu erreichen. „Das Monocoque-Deckhaus ist leicht genug, dass wir es auf gute Dämpfer setzen können, um es von Motor- und Wellenvibrationen im Rumpf zu isolieren“, sagt Janssen. „Windcat ist bekannt für seine wirklich leise Fahrt, und die Boote sind bei den großen OEMs von Windkraftanlagen sehr beliebt. Alle diese Windparks müssen instand gehalten werden, daher gibt es einen neuen Markt für Hochgeschwindigkeits-Katamarane mit einer Länge von 50 bis 60 Fuß.“

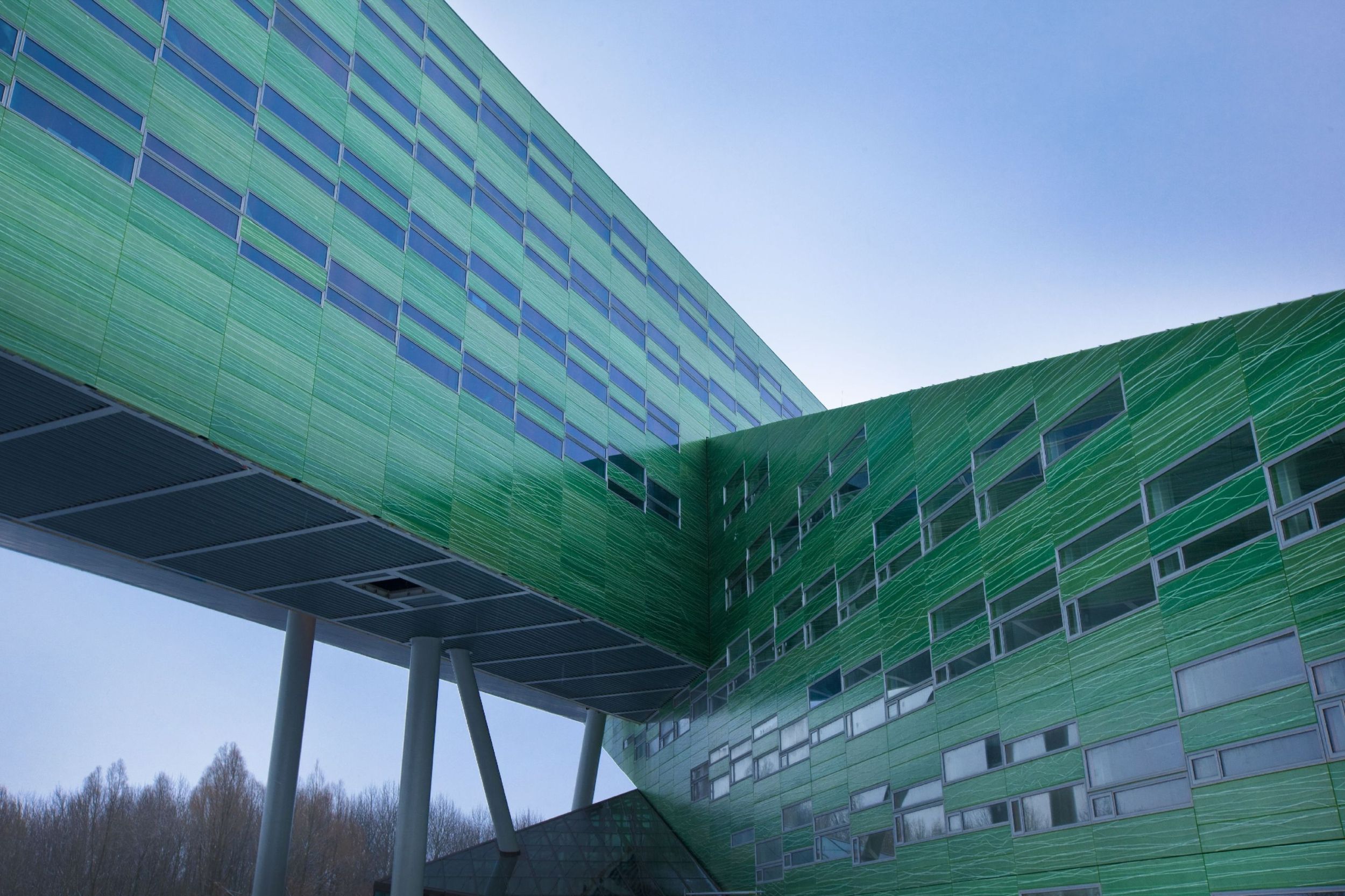
Holland Composites lieferte die strukturelle Verbundfassade für die University of Groningen Life Wissenschaftsgebäude mit ihrem lichtdurchlässigen RAFICLAD-Plattensystem und großen Plattengrößen (3,6 x 3,3 Meter) für Gewichtseinsparungen und maximale Wärmedämmung.
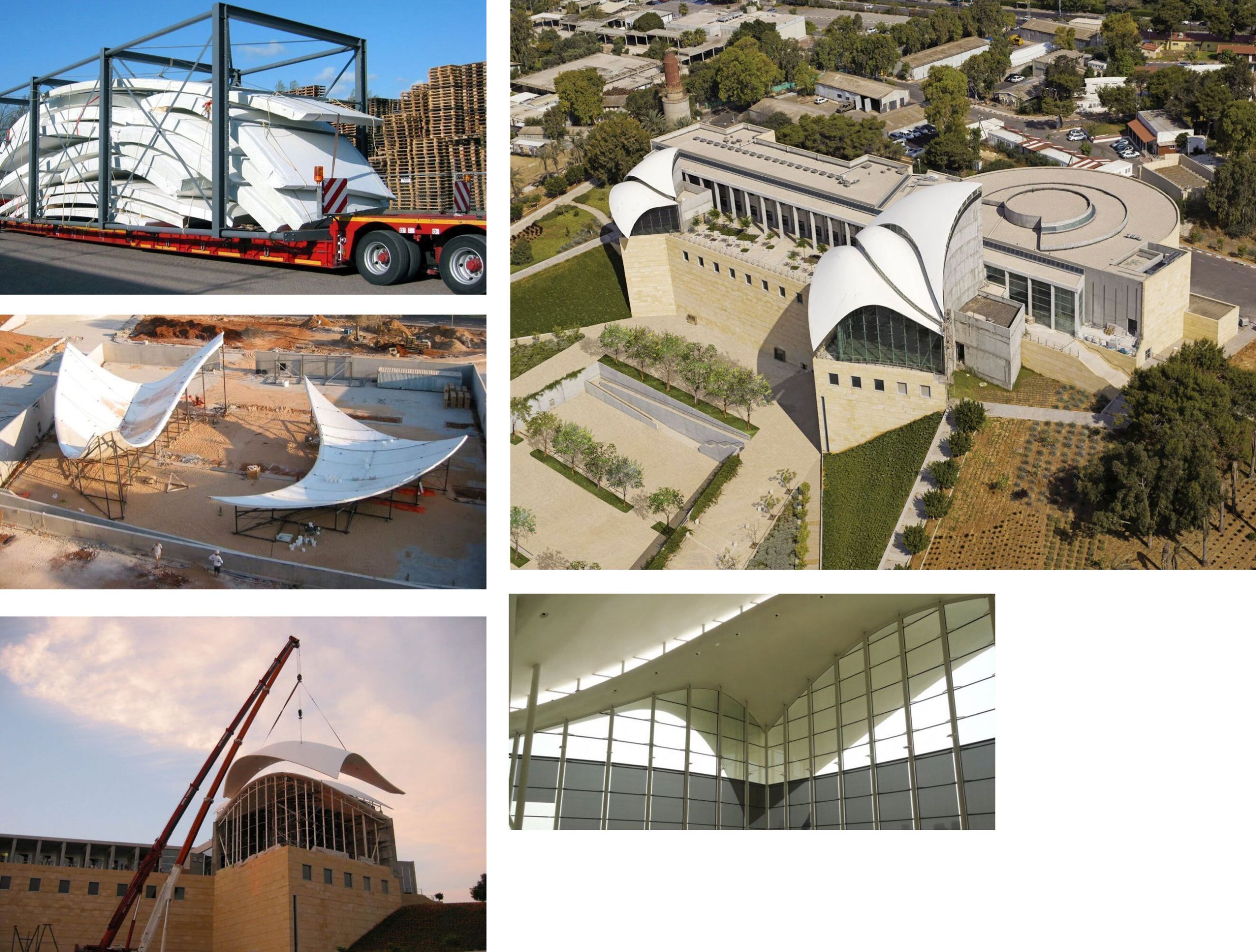
75 40 mal 60 Meter große Verbundteile wurden nach Israel verschifft, zusammenlaminiert und an Ort und Stelle gehoben, um die flügelartigen Dachteile für das Yitzak Rabin Center in Tel Aviv zu schaffen.
"Alles, was wir tun, ist strukturell"
Für das Yitzak Rabin Center (Tel Aviv, Israel) wurde das Unternehmen beauftragt, flügelartige Dachkonstruktionen zu bauen, die aus Beton zu schwer wären. „Wir haben auch hier die größtmöglichen Schnitte möglich gemacht“, sagt Janssen. Fünfundsiebzig 40 x 60 Meter große Abschnitte wurden mit Glasfasern und Vinylesterharz auf Epoxidbasis mit Harz infundiert und dann nach Israel verschifft. Diese wurden vor Ort kopfüber zu Vorrichtungen gelegt, um sie zu „Flügeldächern“ mit einer maximalen Spannweite von 31 Metern zusammenzulaminieren. Janssen merkt an, dass das Projekt strukturell sehr anspruchsvoll war. „Diese Paneele sind 200 bis 300 Millimeter dick und halten die Glasfassade inklusive einer 11 Meter langen Auskragung zusammen. Der Verbundwerkstoff hält allen Kräften stand und gibt Ihnen die Möglichkeit, solche freihängenden Dachspannweiten zu gestalten.“
Der Fletcher Hotel Tower ist ein weiteres solches Projekt, das in den Jahren 2012-2013 fertiggestellt wurde. Es begann als Einkaufszentrum neben einer Autobahn, erforderte jedoch nach der Entscheidung, das Gebäude in ein High-End-Hotel umzuwandeln, eine erhebliche akustische Dämpfung in der Struktur. „Das Betonskelett konnte keine große zusätzliche Belastung aufnehmen, daher waren wir gefragt, eine Leichtbaulösung zu bieten“, sagt Janssen. Holland Composites entwickelte 8,5 mal 3 Meter große Verbundplatten, an denen die Flachglasfassade befestigt werden konnte. „Das Glas hängt tatsächlich an unseren Paneelen, was hilft, die Last zu tragen“, betont er. „Wir haben unsere Platten dann am Betonskelett befestigt. Diese Kombination des Glases vor den Verbund-Sandwich-Paneelen mit dem Luftspalt dazwischen schafft eine enorme akustische Barriere.“ Jede Verbundplatte wurde auf einer Seite für Innenwände lackierfähig und auf der glasseitigen Außenseite mit UV-beständigen Beschichtungen versehen.
„Dies war auch eine sehr schnelle Methode, um eine Verkleidung an einem runden Gebäude anzubringen“, sagt Janssen. „Wir haben die komplette Fassade in einem Schritt montiert und einen Dämm-R-Wert erreicht von 8, was doppelt so hoch ist wie bei normalen Gebäudeaußenmaterialien.“ Janssen erweitert diese Idee und ist der Ansicht, dass Energieneutralität für den zukünftigen Bau von Gebäuden von entscheidender Bedeutung ist. „Es wird nicht viel Energie benötigt, um die Gebäude zu beheizen, die unsere strukturellen Verbundverkleidungen verwenden, daher ist unser Ansatz sehr effizient, um einen Netto-Null-Fußabdruck zu erreichen. BREEAM ist die niederländische Zertifizierung für Energieeffizienz und die ersten beiden Gebäude, die dies erreicht haben, verwenden unsere Verbundwerkstoffe.“
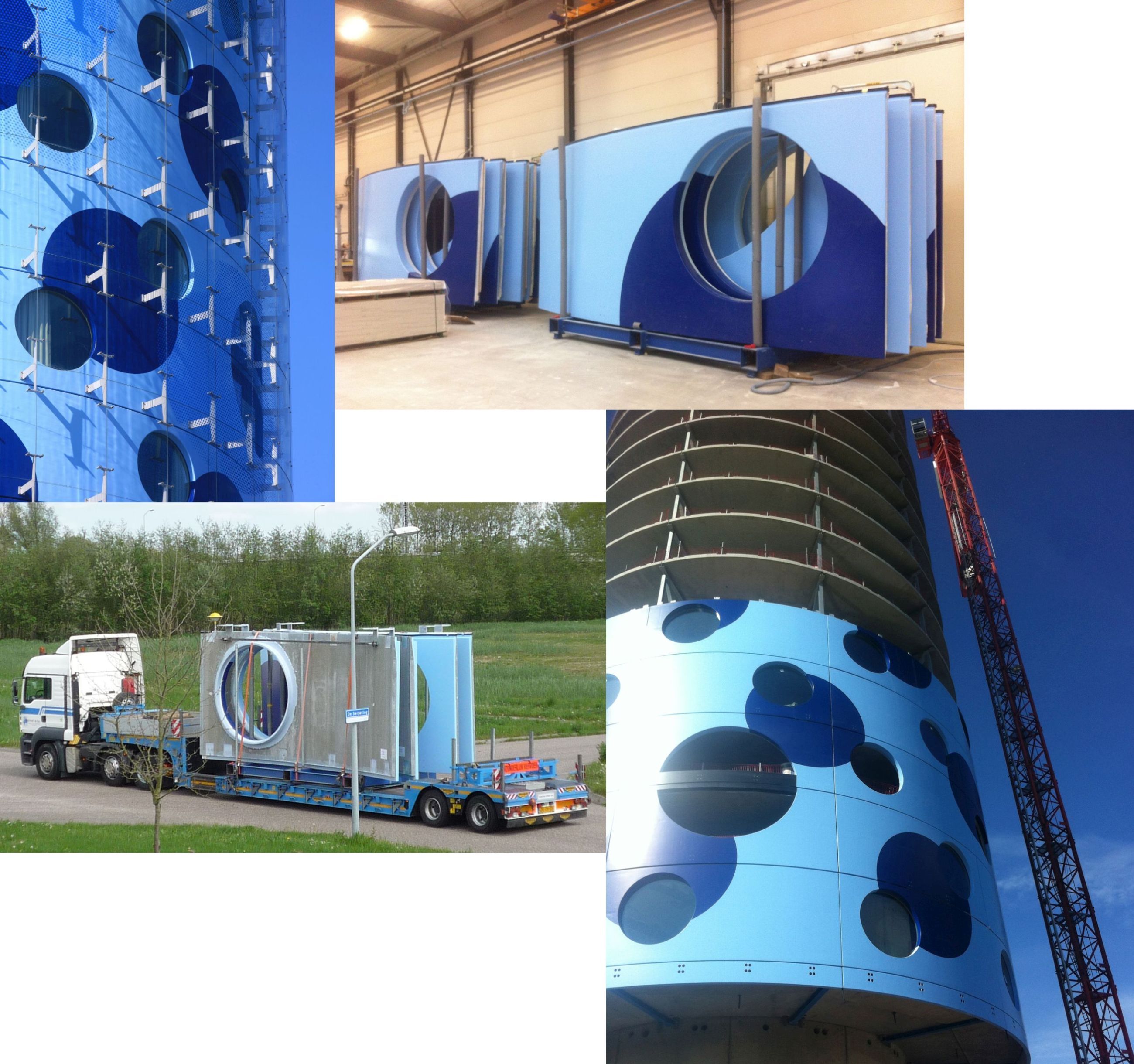
Für das Fletcher Hotel realisierte Holland Composites ein ästhetisches, lärmminderndes Äußeres durch die Anbringung von gebogenen Verbundplatten am Betonskelett des Gebäudes, an denen die Glasfassade ohne übermäßiges Eigengewicht befestigt werden konnte.
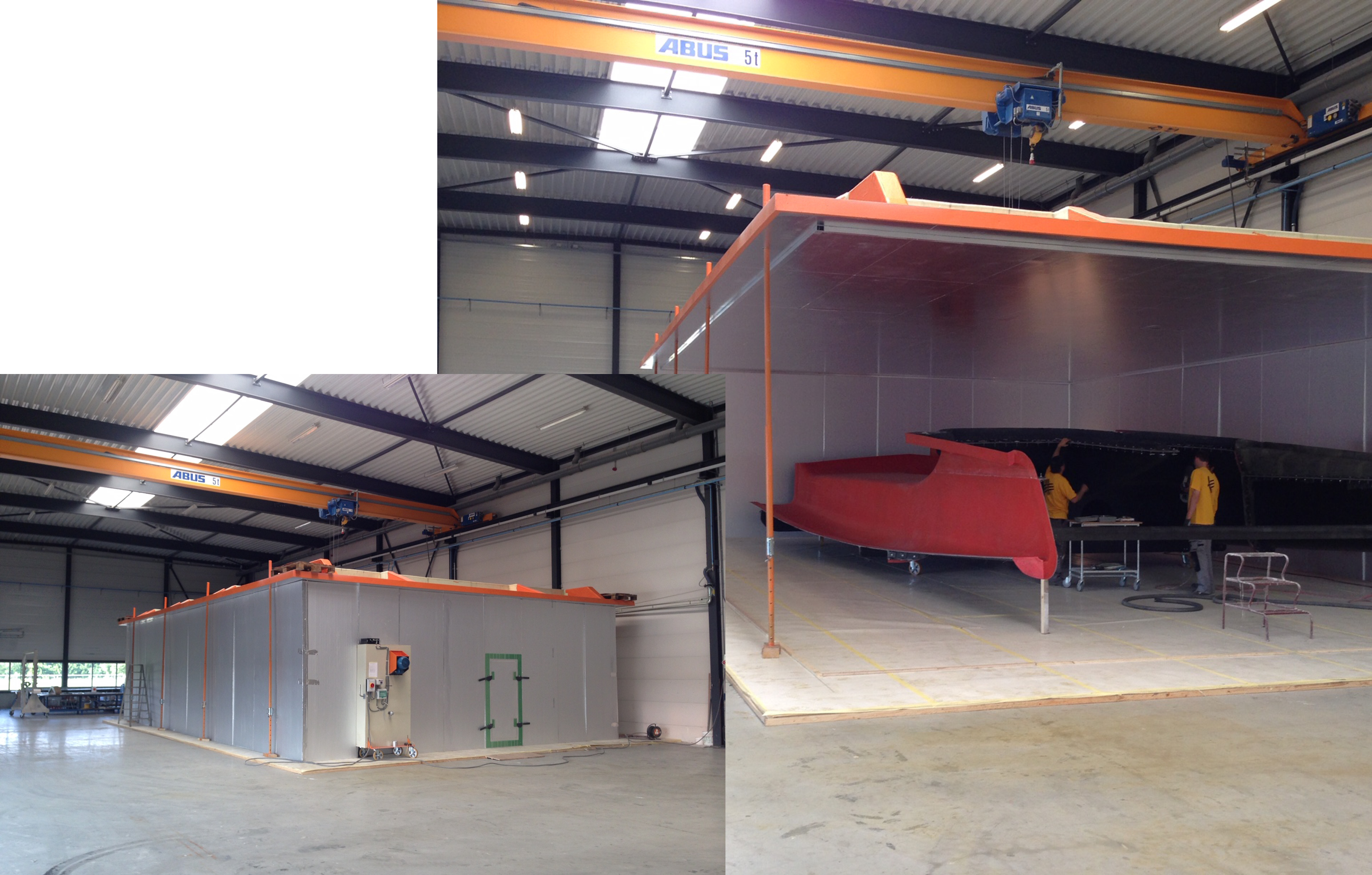
Janssen hebt das Stedelijk Museum für zeitgenössische Kunst in der Amsterdamer Innenstadt als Höhepunkt der technischen Bauprojekte von Holland Composites hervor (siehe „Großes Museum, große Strukturen“). „Es war eine extreme Übung im Umgang mit der Wärmeausdehnung und zeigt, was wir tun.“ Holland Composites hat auch Pionierarbeit bei erdbebensicheren Strukturfassaden geleistet, die jetzt in bestimmten Teilen der Niederlande erforderlich sind, erklärt Janssen, weil der Boden durch Hydrofracking (Fracking) destabilisiert wurde. Das Wiebenga-Gebäude in Groningen verfügt über eine erdbebensichere Fassade, die sich störungsfrei um 30 Zentimeter bewegen kann. „Normaler Stahl und Beton können diese Art von Bewegung nicht bewältigen“, fügt er hinzu.
Obwohl es beim Bau von Strukturen eine Herausforderung ist, die unzähligen Anforderungen mit Kosten und Zeitplan in Einklang zu bringen, stellt Janssen fest, dass das derzeit größte Problem der Feuerwiderstand ist. „Die falsche Implementierung von Verbundwerkstoffen hat der Verbundwerkstoffindustrie einen schlechten Ruf eingebracht diesbezüglich“, erklärt er. „Wir verwenden jetzt bei diesen Bauprojekten nur feuerbeständige Materialien und führen Brandprüfungen gemäß den genehmigten Vorschriften durch.“
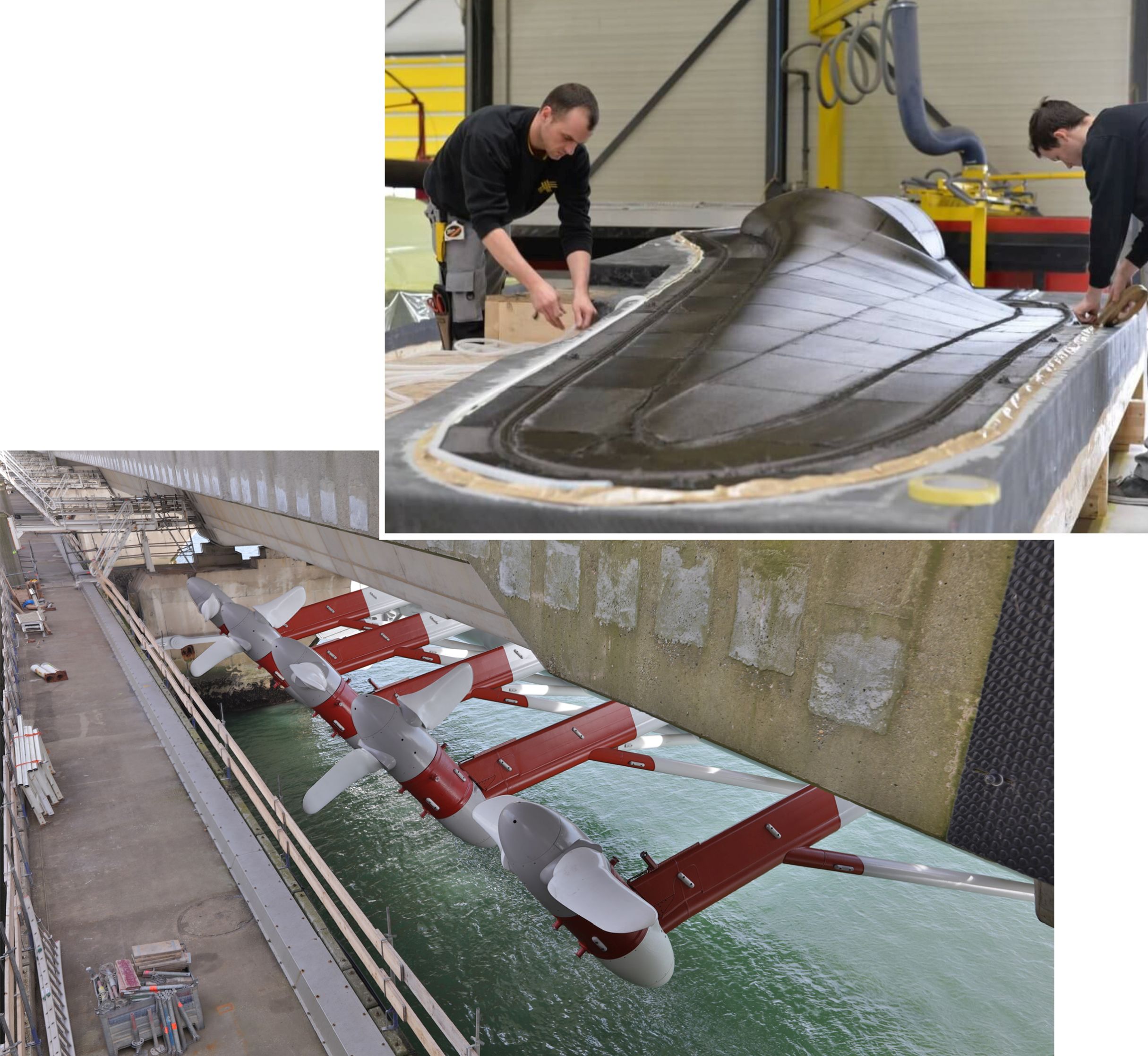
Holland Composites baut Schaufeln für Gezeitenturbinengeneratoren aus Kohlefaser-Prepreg, das in einem Autoklaven ausgehärtet wird, um die großen Belastungen zu bewältigen, die auf diese Strukturen mit niedriger Geschwindigkeit und hohem Drehmoment ausgeübt werden.
Offshore und erneuerbare Energien
Holland Composites hat auch langfristige Verträge in der Offshore-Öl- und -Gasindustrie. „Verbundwerkstoffe bieten hier nicht nur geringes Gewicht und Korrosionsbeständigkeit, sondern auch eine einfache Reparatur“, sagt Janssen. „Offshore-Bohrinseln und -Schiffe dürfen keine Ausfallzeiten haben. Die Reparatur von Metallkonstruktionen erfordert jedoch Schweißarbeiten und Funkenbildung, sodass die Produktion aufgrund von Brandgefahr eingestellt werden muss. Wir können Verbundwerkstoffe ohne diese Unterbrechung patchen.“ Das Unternehmen hat neue Kunden, die solche Produkte für eine Vielzahl von Offshore-Konstruktionen nachfragen.
Es hat auch Schaufeln für Gezeitenturbinen hergestellt. Die Gewinnung von Gezeitenenergie sei noch neu, sagt Janssen, aber die ersten Projekte seien abgeschlossen und die Ergebnisse beeindruckend. „Gezeitenturbinen bieten eine zuverlässige Energiequelle“, erklärt er. „Die Gezeiten sind im Vergleich zu Wind und Sonne immer da, sodass Sie die Stromabgabe zuverlässig vorhersagen können, was für Energieversorger entscheidend ist.“ Holland Composites verwendet für diese Blätter autoklavgehärtetes Kohlefaser-Prepreg, da die Belastungen enorm sind. „Die Messer bewegen sich mit niedriger Geschwindigkeit, aber mit hohem Drehmoment“, sagt Janssen. „Sie wollen die maximale Übersetzung der Rotordrehzahl in den Motor, um Leistung zu erzeugen, daher brauchen die Turbinenhersteller starke, aber effiziente Strukturen, die so geformt sind, dass sie so viel Energie wie möglich aus den Gezeitenbewegungen gewinnen.“
Jede Turbine hat zwei 3 Meter lange Schaufeln mit einer Dicke von 18 Millimetern. Es gibt fünf Turbinen pro Gezeitengenerator. „Die Belastung dieser Turbinenschaufeln wird mit einem 13.600-PS-Schlepper bei voller Leistung gleichgesetzt“, sagt Janssen. Stahl wäre zu schwer gewesen und die Generatoren weniger effizient.“ Holland Composites stellt nur die Klingen her; Verkleidungen, Nasenkonus und nicht tragende Verkleidungen werden von FRP-Herstellern hergestellt.
Zukunftsorientierte Einrichtung
Die Tour beginnt im Layup-Bereich, in dem ein großer Layup-Tisch, Teile für die DNA-Performance-Segelboote und verschiedene CFK-Folien für den Einbau vorbereitet werden. Die Decke ist hier wegen eines Zwischengeschosses zur Materiallagerung niedrig. Diese öffnet sich zu einer hohen Produktionshalle mit einem Zünd (Altstätten, Schweiz) Schneideautomaten gleich hinter dem Auflegebereich. Der Cutter hat einen Schnittbereich von 5,7 x 2,8 x 0,3 Meter, um Prepreg, trockene Faser- und Schaumstoffmaterialien bis zu 25 Millimeter Dicke zu verarbeiten.
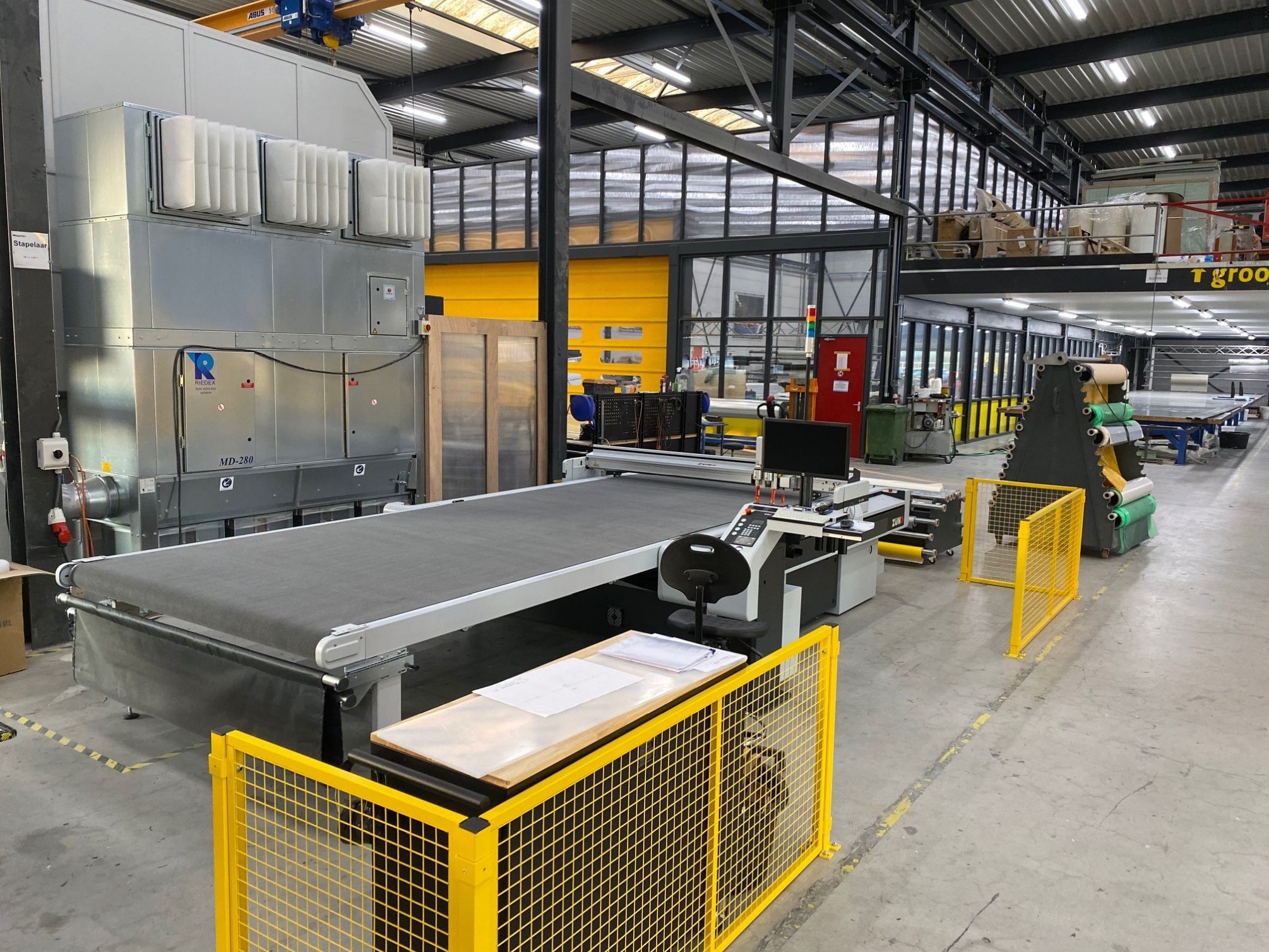
Der Zünd-Schneidautomat im Vordergrund versorgt den rechts hinten zu sehenden Layup-Bereich mit Schnittverstärkungen und Schaumstoff und darüber das Materiallager-Mezzanine. Der geschlossene Werkzeugbereich liegt hinter dem gelben Rolltor, hier zu sehen hinter der Seite des CMS Bearbeitungszentrums, das sich neben dem Zünd Schneidetisch befindet.
Wir drehen uns vom Zünd Cutter um und gehen zu einem verglasten Werkzeugraum, der an den Auflegebereich angrenzt. Beim Betreten durch ein gelbes Rolltor werden mehrere Werkzeuge verarbeitet und Teile werden unter Vakuumbeuteln ausgehärtet. „Wir stellen unsere eigenen Formen her“, sagt Janssen. „Bei CFK-Teilen verwenden wir CFK oder Aluminium für die Werkzeuge sowie Belüftungslöcher für die Luftzirkulation in den Werkzeugen, die eine gleichmäßige Aushärtung des Teils gewährleisten.“
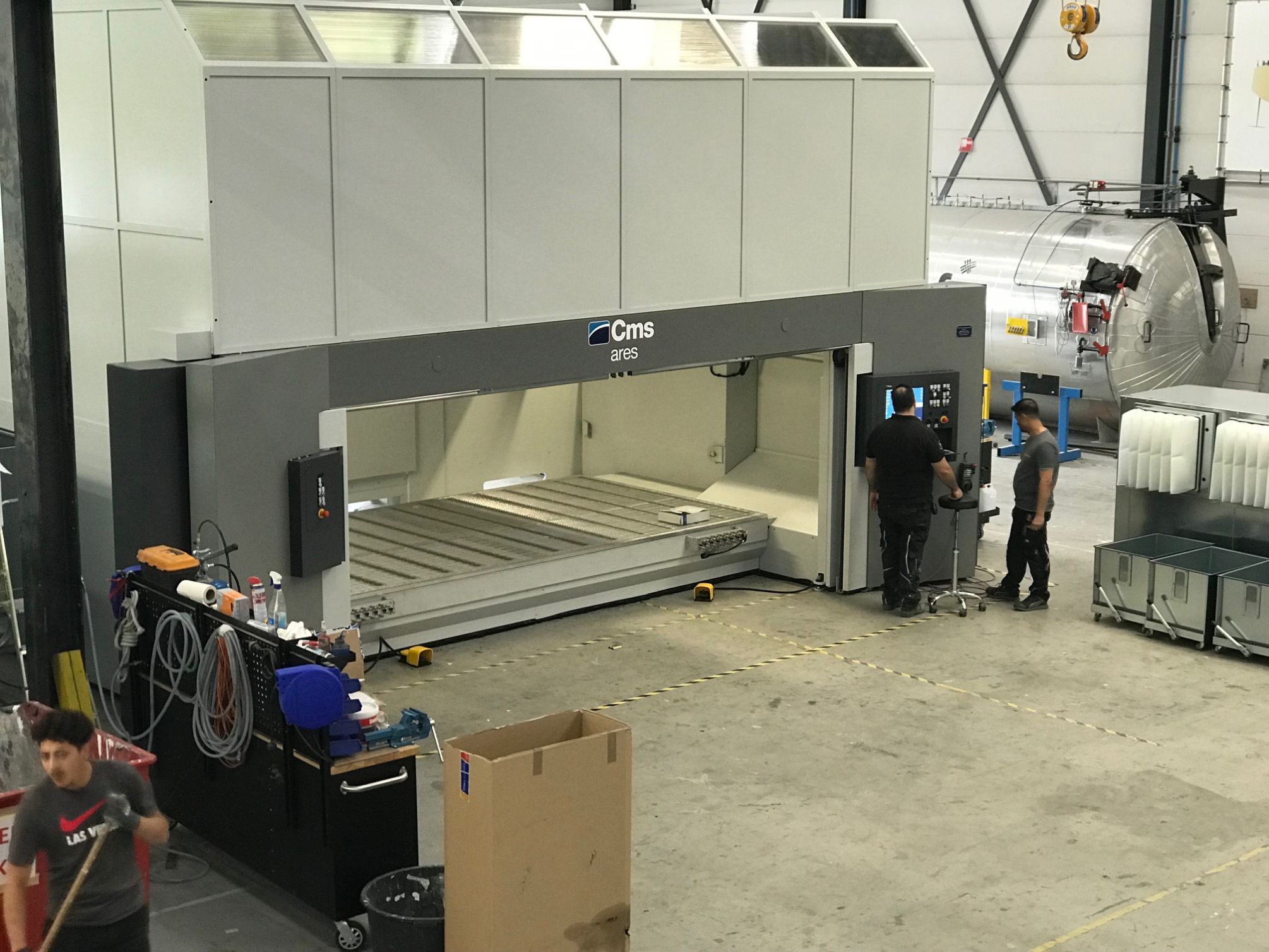
Das CMS-Bearbeitungszentrum befindet sich zwischen dem Schneidtisch links (außer Sicht) und dem Autoklav (ganz rechts, an der Wand).
Zurück aus dem Werkzeugraum kommen wir am 5 mal 2 mal 1,8 Meter großen 5-Achs-CNC-Fräszentrum (CMS SpA, Zogno, Italien) vorbei und sehen den 6,5 mal 2,2 Meter großen Autoklaven (Tankbouw Rootselaar, Nijkerk, Niederlande). „Wir heilen normalerweise bei 125° C mit einem Druck von 6 bar“, bemerkt Janssen.
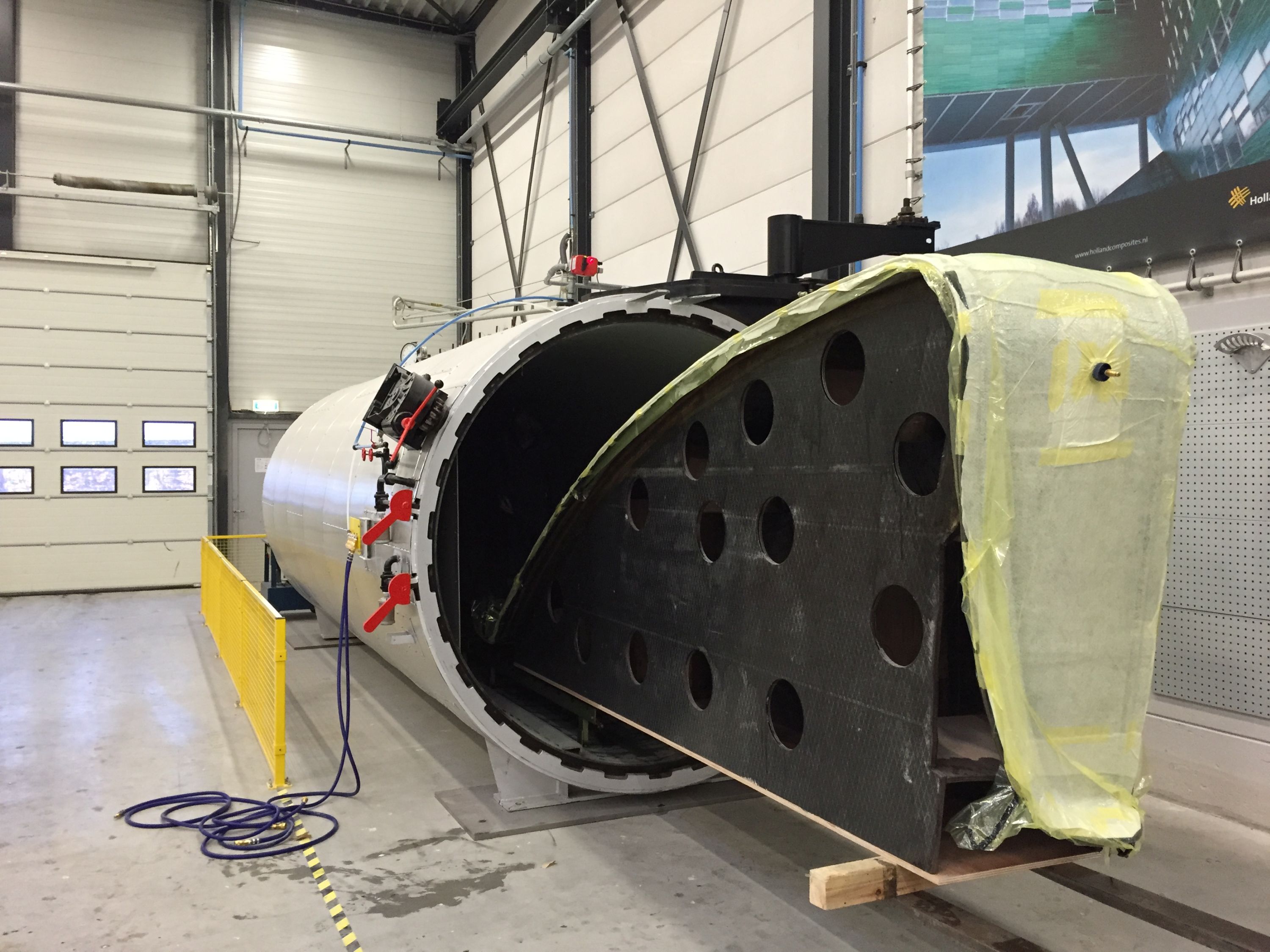
Der Autoklav ist auch unten mit einem CFK-Werkzeug (beachten Sie die Löcher für die Belüftung) und einer großen CFK-Folie, die unter einem Vakuumbeutel für ein leistungsstarkes Mehrrumpf-Segelboot ausgehärtet wird.
Die Wand neben dem Autoklaven teilt den Produktionsbereich in zwei Hälften, die sich über die gesamte Gebäudelänge entlang des Werkzeugraums erstrecken. Wir drehen uns um und gehen durch eine Tür in die zweite Hälfte des Werks von Holland Composites, die eine Wasserstrahlschneidmaschine (8 x 2 x 0,5 Meter Schneidbereich), mehrere Öfen mit einer Größe von bis zu 15 x 10 Zoll enthält -3,5 Meter und die 19 mal 12 mal 3,5 Meter große Lackierkabine des Unternehmens. „Derzeit produzieren wir große Platten für ein Projekt in Katar und eine Reihe von CFK-Deckhäusern für die Windcat-Boote“, sagt Janssen.
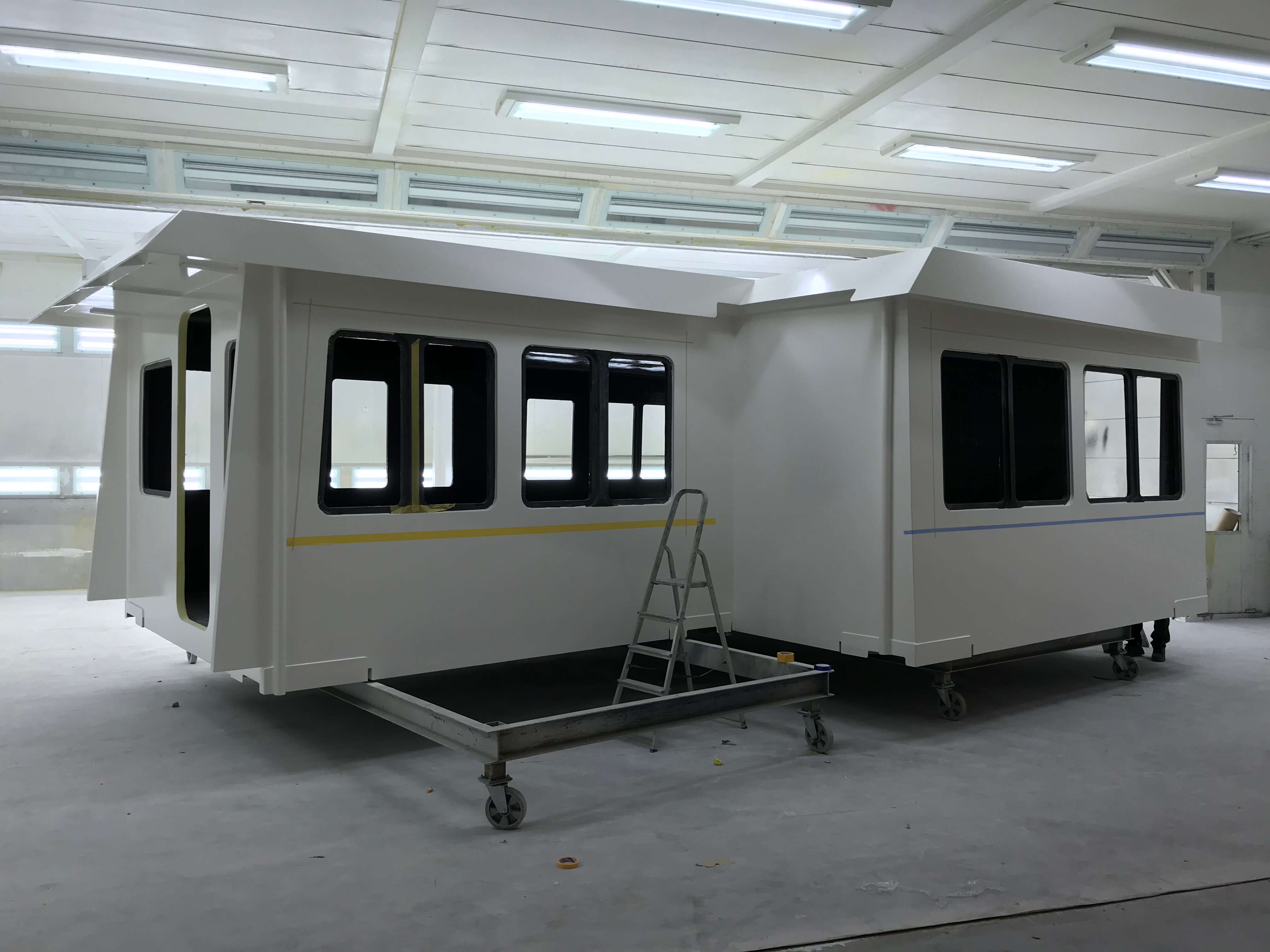
Die CFK-Deckhäuser, die Holland Composites für die Katamarane von Windcat Workboats produziert, werden in der 19 mal 12 mal 3,5 Meter großen Lackierkabine des Unternehmens lackiert.
Die neueste Installation von Holland Composites ist ein Massivit 3D (Lod, Israel) 1800 Pro-Drucker mit einem Bauvolumen von 145 x 111 x 180 Zentimetern. „Wir sind Partner, die den 3D-Druck von Formen mit drei Druckköpfen innovieren, wobei zwei die Häute eines Sandwichs drucken und die mittlere Düse die Füllung oder die Gitterstruktur dazwischen druckt“, erklärt Janssen. „Wir werden bei zukünftigen Entwicklungen faserverstärktes Material verwenden, aber im Moment können wir präzise Werkzeuge mit minimalem Fräsaufwand drucken. Wir verbrauchen deutlich weniger Material und sehen sehr schnelle Formenbauzeiten. Wir verfügen jetzt über eine komplette Prozesskette mit der Möglichkeit, in kurzer Zeit vom Design über die Formen bis hin zu lackierten Teilen zu gelangen.“
Er stellt fest, dass das Unternehmen immer noch untersucht, wie es seinen Einsatz von Automatisierung erhöhen kann, um seine Produkte weiterzuentwickeln, ohne jedoch die Kosten in die Höhe zu treiben. „Es kommt auf den Einfallsreichtum an. Uns reizen hochkomplexe Probleme, an die sich nur wenige andere wagen, aber als Bootsbauer mussten wir schon immer mit begrenzten Ressourcen sehr kreativ sein. Für das, was wir im Bereich Verbundwerkstoffe tun, sehen wir in Zukunft viele Möglichkeiten.“
Harz
- Hersteller besuchen United Safety für Werksbesichtigung und Diskussion über bewährte Verfahren
- CompositesWorld SourceBook 2022
- Fehlerbehebung beim Thermoformen von thermoplastischen Verbundwerkstoffen
- Die Entwicklung additiver Verbundwerkstoffe
- Thermoplastische Verbundwerkstoffe:Strukturelle Stoßstangenhalterung
- Verbundwerkstoffe als Karosserieverstärkungen
- Die Niederlande präsentieren die Verbundwerkstoffkompetenz des Landes auf der JEC World 2019
- TPAC und TPRC entwickeln Recyclingprozess für thermoplastische Verbundwerkstoffe
- Schweißen von thermoplastischen Verbundwerkstoffen
- Hochleistungsverbundwerkstoffe in Israel