WMG-Prototypen CFK-Rahmen für Very Light Rail (VLR) Demonstrationsfahrzeug
Revolution VLR ist ein Konsortium in Großbritannien – unter der Leitung von Transport Design International Ltd (TDI, Stratford upon Avon) – das 2013 Fördermittel für die Entwicklung eines selbstfahrenden Schienendrehgestells mit einem integrierten Hybridantriebssystem erhielt. TDI ist der Ansicht, dass die Entwicklung leichterer „Light Rail“-Fahrzeuge – d. h. Very Light Rail (VLR) – entscheidend für die Bereitstellung der nächsten Generation eines nachhaltigen öffentlichen Verkehrs ist. In Phase 2 des VLR-Projekts wird 2020 ein komplettes 18 Meter langes Diesel-Batterie-Demonstratorfahrzeug zum Testen zur Verfügung stehen.
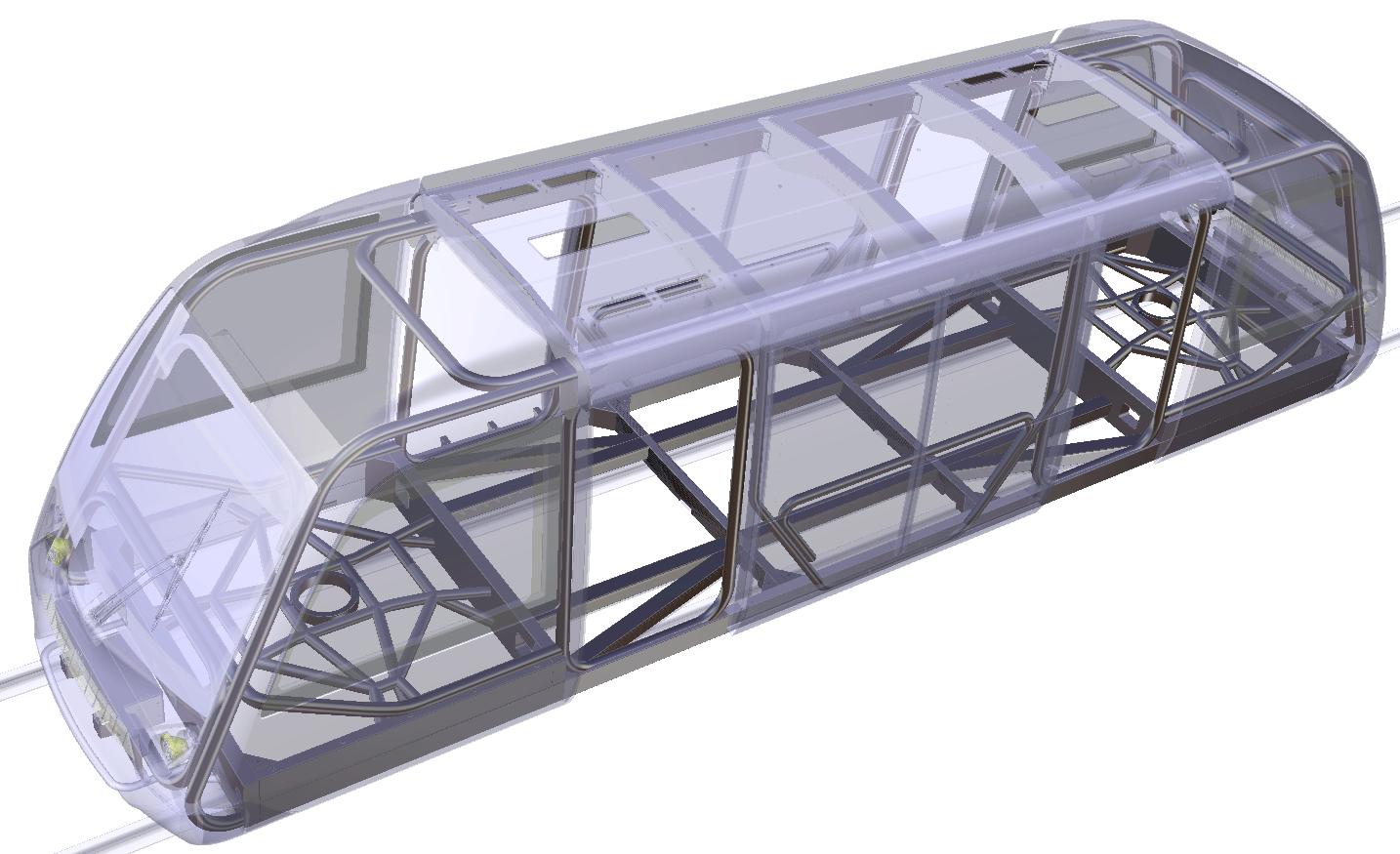
Der Demonstrator Very Light Rail (VLR) ist ein 18 Meter langes Drehgestell mit integriertem Diesel-Batterie-Hybridantrieb und einem leichten Chassis aus geflochtenen Verbundrohren. QUELLE | Universität von Warwick.
Ein ursprüngliches Mitglied von Revolution VLR, WMG an der University of Warwick, hat einen Rahmen aus kohlenstofffaserverstärktem Kunststoff (CFK) für dieses VLR-Demonstrationsfahrzeug entwickelt. WMG ist ein langjähriger Unterstützer von Verbundwerkstoffen mit Initiativen wie dem National Automotive Innovation Center, dem Materials Engineering Center und dem International Institute for Nanocomposites Manufacturing. Zu den Partnern von WMG für dieses „BRAINSTORM VLR“-Projekt gehören TDI, Innovate UK der britischen Regierung (die Verbundwerkstoffe finanziert), der Entwickler von Leichtbau-Verbundkomponenten Far Composites und Composite Braiding. Der Rahmen besteht aus einer Reihe von geflochtenen thermoplastischen Verbundrohren, die durch Kleben und einfaches Schweißen leicht zusammengebaut werden können.
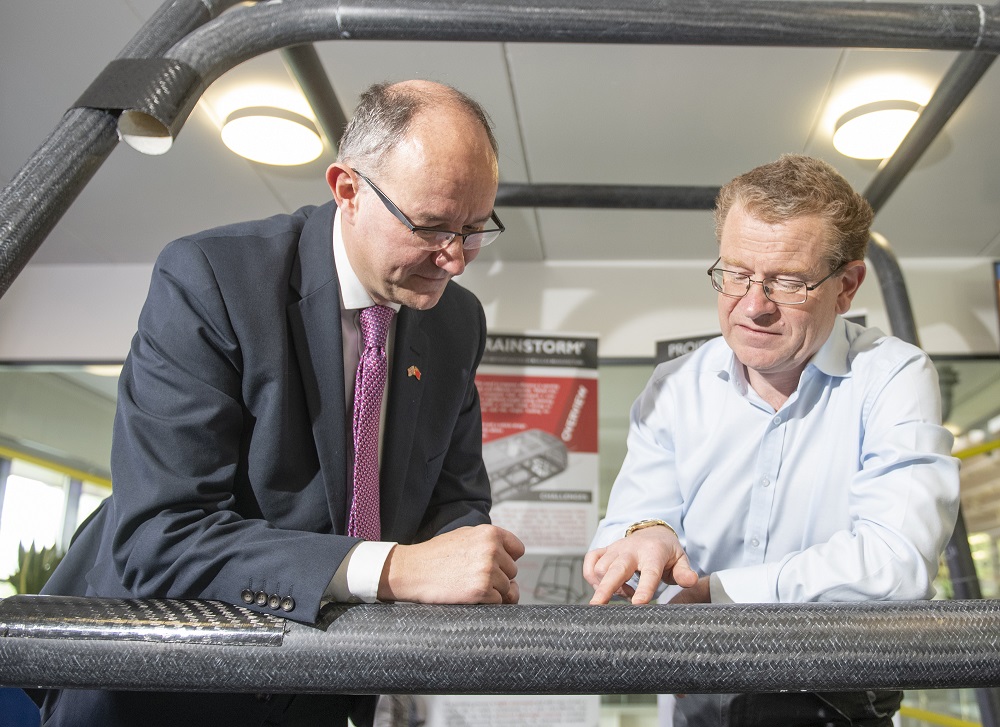
Das VLR-Prototyp-/Demonstratorfahrzeug wird ein Spaceframe-Chassis aus geflochtenen kohlenstofffaserverstärkten thermoplastischen Verbundrohren verwenden, die durch Kleben und einfaches Schweißen einfach montiert werden können. QUELLE | Universität von Warwick.
Die Rohraußendurchmesser werden gleich gehalten, wobei unterschiedliche Belastungs- und Befestigungsanforderungen durch Variation der Wandstärken bewältigt werden. Dies hält die Werkzeugkosten niedrig und ermöglicht eine standardisierte Verbindung. Flechten ermöglicht einen hochautomatisierten Herstellungsprozess – die Rate allein für die Verstärkung kann 1 Meile/Tag überschreiten – sowie einen maßgeschneiderten Satz von Materialien, einschließlich anderer Fasern (z. B. Glas, Aramid, Thermoplast) und thermoplastischer Matrixmaterialien aus kostengünstigem Polypropylen bis zum High-End-Polyetheretherketon (PEEK). Inzwischen hat WMG einen vollständigen Formzyklus demonstriert, der auf weniger als fünf Minuten verkürzt werden kann, was das Potenzial dieses kostengünstigen Verfahrens für Großserienanwendungen unterstreicht.
Thermoplaste bieten auch Recyclingfähigkeit, so David Goodwin, Engineering Manager bei Far-UK. „Mit Verbundwerkstoffen lässt sich viel Gewicht einsparen, was für den Betrieb des [Bahn-]Wagens natürlich reizvoll ist“, beginnt er, „aber bei herkömmlichen Verbundwerkstoffen wird der Wagen am Ende der Lebensdauer einfach deponiert, was“ ist nicht optimal. Bei diesem [Design] gibt es einen Weg, die Karosserie zu recyceln, wenn sie irgendwann außer Betrieb geht oder alternativ, wenn sie einen Aufprall erleidet und ein Teil davon repariert und ersetzt werden muss.“
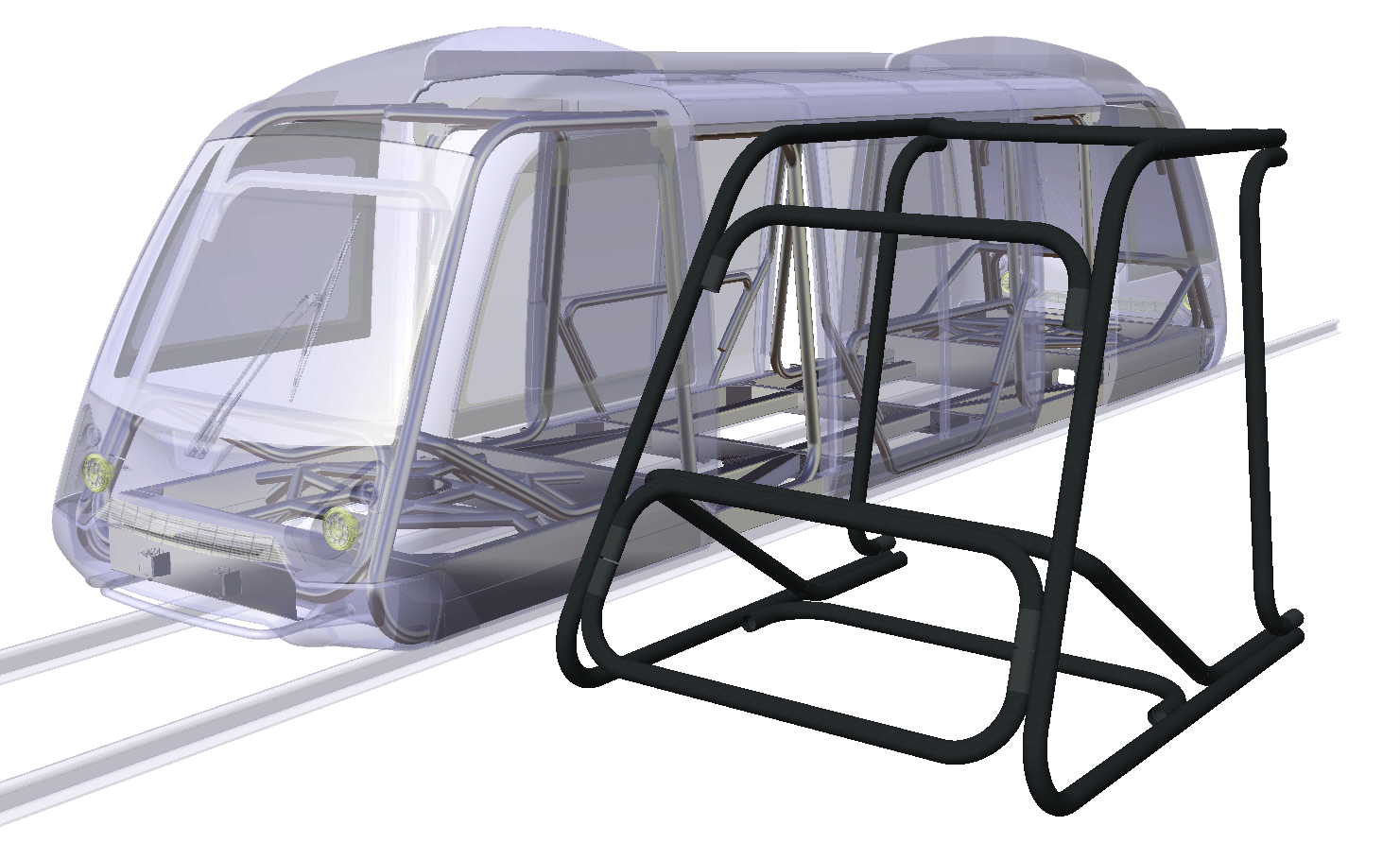
Universität Warwick
Auch die Konstruktion des Gitterrohrrahmen-Chassis unterstützt diesen Ansatz, da beschädigte Rohre einfach entfernt und durch neue oder reparierte Rohre ersetzt werden können. „Unsere BRAINSTORM VLR-Forschungspartnerschaft hat erhebliche Gewichtseinsparungen erzielt, sodass die VLR-Dienste mehr Passagiere aufnehmen können und gleichzeitig die zum Antrieb des Fahrzeugs erforderliche Energie und die Gewichtsbelastung, die es auf Schienen und Straßenoberfläche ausübt, reduziert“, erklärt Dr. Darren Hughes, außerordentlicher Professor für Werkstoffe und Fertigung an der WMG University of Warwick. „Die Technologie sorgt auch dafür, dass das Fahrzeug eine lange Lebensdauer hat, bei Unfällen leicht repariert werden kann und stark genug ist, um die Passagiere an Bord zu schützen.“
„Das BRAINSTORM-Projekt fühlt sich für das Team von Far Composites wie ein echter Fortschritt an“, sagt Lyndon Sanders, Direktor und General Manager von Far-UK. „Es war großartig, auf die Branchenerfahrung von TDI zurückzugreifen, um das Prinzip einer neuartigen Karosseriestruktur für Nahverkehrsanwendungen zu verfeinern. Hinzu kommt, dass die Zusammenarbeit mit Composites Braiding und WMG, um dieses Denken in einen physischen Demonstrator zu verwandeln, um zu zeigen, wie es in der Praxis aussehen würde, wirklich mächtig war. Jetzt ist es mehr als eine gute Idee, es ist ein Augenöffner für Branchenakteure, die es sehen, anfassen und sogar in die Hand nehmen können.“
Harz
- Ultraleichte TPE-Verbundwerkstoffe für Schuhe
- Konstruktion für die automatisierte Herstellung von Verbundwerkstoffen von kleinvolumigen Flugzeugstrukturen
- Wiederaufbereitbare, reparierbare und recycelbare Epoxidharze für Verbundwerkstoffe
- Kombination von AC- und DC-Dielektrizitätsmessungen zur Überwachung der Härtung von Verbundwerkstoffen
- Perseverance Rover macht einen Schritt für Komposite auf dem Mars
- RS Electric Boats wählt Norco für die Herstellung von Verbundwerkstoffen
- PEEKSense Hochtemperatur-Thermoelement für die Aushärtung von PEEK-Verbundwerkstoffen
- Solvay-Verbundwerkstoffe für Rennkatamarane ausgewählt
- Thermoplastische Tür eine Premiere für Automobilverbundwerkstoffe
- Ashland arbeitet mit Velox für den Vertrieb von Verbundwerkstoffen in Frankreich zusammen