Hey, Job Shops:Zeit für Automatisierung!
Denken Sie, dass Automatisierung in einer High-Mix-, Low-Volume-Umgebung zu schwierig ist? Denken Sie noch einmal nach
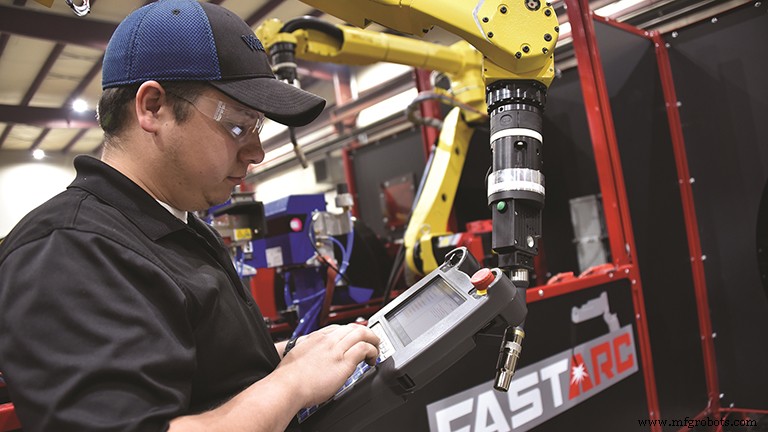
Über Roboter und Jobshops wurde normalerweise nicht zusammen gesprochen. Schließlich weiß jeder, dass die Automatisierung nur für die Massenproduktion geeignet ist und der typische Tante-Emma-Betrieb alles andere als das ist – sein Zeitplan ist gefüllt mit Aufträgen für High-Mix-, Low-Volume- und oft hochkomplexe Arbeiten. Wer braucht einen Roboter in dieser Umgebung, in der mehrmals pro Woche oder sogar täglich Setups durchgeführt werden?
Bevor Sie jedoch zum nächsten Artikel übergehen, sollten Sie einige Dinge berücksichtigen. Für den Anfang sagen viele Experten, dass Lohnfertiger die niedrigste Maschinenauslastung in der Branche haben, unabhängig davon, was die Eigentümer sagen mögen. Gesamtanlageneffektivität (OEE)-Werte von 50 Prozent oder weniger sind keine Seltenheit. Automatisierung ist eine klare Lösung, um diese Zahl zu verbessern.
Und da Maschinenwechsel in Lohnfertigern häufiger sind, werden für einrichtungsbezogene Tätigkeiten qualifiziertere Maschinisten und Programmierer benötigt – Leute, die höhere Gehälter erzielen und schwer zu finden sind. Dies treibt die Betriebskosten in die Höhe, verringert die Möglichkeiten für zusätzliche Arbeit und macht die Produktion rund um die Uhr zu einer extremen Herausforderung. Angesichts des Fachkräftemangels sollte die Automatisierung daher der heilige Gral für jeden Lohnfertiger sein, auch wenn die Umsetzung vielleicht kein einfacher Weg ist.
Plug-and-Play-Möglichkeiten
Die Frage ist, wo fängt man an? Zach Spencer hat ein paar Ideen. Als Ingenieur für kundenspezifische Vorschläge bei Methods Machine Tools Inc., Sudbury, Mass., stellte er fest, dass die Automatisierung einer Plug-and-Play-Angelegenheit nahe kommen kann, insbesondere wenn sie Teil des Kaufs einer neuen Werkzeugmaschine ist.
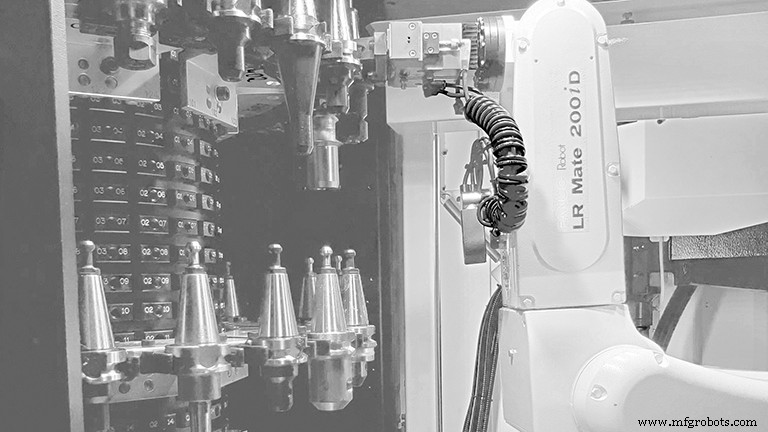
„Wir haben unsere JobShop-Zelle vor fast 15 Jahren entwickelt und sie ist seitdem zu einer unserer beliebtesten Automatisierungslösungen für den FANUC RoboDrill geworden“, sagte er. „Es ist für Läden konzipiert, die jeden Tag mindestens einige Umstellungen haben, über eine begrenzte Stellfläche verfügen und die Flexibilität benötigen, einfach von einem Teil zum anderen zu wechseln.“
Die JobShop-Zelle ist in zwei Konfigurationen erhältlich, erklärte er. Einer verwendet eine Ober-/Unterfördereranordnung, um Rohmaterial zum Roboter zu bringen und fertige Teile zu entfernen, während der andere einen Schrank mit einer Reihe von Schubladen zur Aufbewahrung von Werkstücken und Materialien verwendet. Beide verwenden einen FANUC-Roboter zum Be- und Entladen der Maschine (oder eines Maschinenpaars im Fall der Twin RoboDrill JobShop Cell von Methods) und beide bieten die Möglichkeit, eine CNC je nach Bedarf stundenlang oder sogar eine ganze Schicht lang unbeaufsichtigt zu lassen Werkstück.
Für größere Mengen bietet Methods sein Plus-E an, ein Automatisierungssystem mit mehreren Paletten im Aufzugsstil für Aufträge mit mittlerem bis hohem Volumen, sowie das Plus-K für Geschäfte, die sowohl die Einrichtung als auch den Betrieb der Maschine automatisieren möchten. mit der Möglichkeit, Werkzeughalter, vorinstallierte Schraubstöcke und Vorrichtungen auszutauschen. „Sie können dem System mitteilen, dass diese fünf Schraubstöcke Teil A sind, die nächsten beiden Schraubstöcke Teil B, der nächste Teil C und die nächsten zehn Teil D“, sagte Spencer. „Danach belädst du es einfach mit Material und gehst nach Hause. Beide Maschinen der Plus-Serie sind eigenständige Einheiten, die neben einem RoboDrill stehen und sich perfekt für Werkstätten eignen, die einen einfachen Einstieg in die Automatisierung suchen.“
Nimm den Trolley
Methods ist nicht der einzige Anbieter, der diesen Ansatz verfolgt. Eric Nekich, verantwortlich für Betrieb, Technologie und Vertriebsinnendienst bei Lang Technovation Co., Hartland, Wisconsin, sagte, dass die RoboTrex-Automatisierungssysteme des Unternehmens einen FANUC-Roboter und bis zu vier bewegliche Wagen verwenden, die jeweils eine Reihe vorbeladener Schraubstöcke enthalten. Der RoboTrex 52 zum Beispiel kann bis zu 42 Schraubstöcke pro Wagen lagern (basierend auf Teilegröße und Wagenkonfiguration), was potenziell eine unbeaufsichtigte Bearbeitung von 168 Werkstücken ermöglicht.
Wie der JobShop Cell ist der RoboTrex in sich geschlossen und vollständig geschützt, kann aber auch in eine Vielzahl von Bearbeitungszentrenmarken und -modellen integriert werden. Die einzige Hürde besteht darin, sich um die Notwendigkeit zu kümmern, in ein paar Makro-Grip-Fünfachsen-Schraubstöcke von Lang zu investieren, die für die Verwendung mit dem System erforderlich sind (und zufällig auf 50 mit RoboTrex ausgestatteten Bearbeitungszentren in Langs Werk in Deutschland hergestellt wurden). . „Es ist jedoch eine Investition mit einem sehr schnellen ROI, da Ihre Spindelbetriebszeit mit dem RoboTrex USA-System drastisch steigen wird“, sagte Nekich.
Michael Gamache ist Business Development Manager bei Gamache Systems mit Sitz in New Berlin, Wisconsin, einem Geschäftsbereich von Metalcraft aus Mayville und exklusiver Integrator für RoboTrex-Systeme in den Vereinigten Staaten. Er erkennt an, dass einige Kunden vielleicht davor zurückschrecken, in ein neues Spannsystem zu investieren, hat aber einige gute Gründe dafür genannt.
„Als Geschäftsinhaber verstehe ich, dass Schraubstöcke nicht billig sind, aber aus Sicht der Automatisierung ist eine hochwertige Werkstückspannung die halbe Miete“, sagte er. „Sie müssen das Rohmaterial wiederholt und genau zum Roboter bringen, und das Makro-Grip-System ist eine der besten Möglichkeiten, dies zu erreichen. Darüber hinaus ist das System sehr einfach einzurichten und zu bedienen, da der Roboter die Schraubstöcke handhabt und nicht eine Vielzahl von Rohmaterialgrößen; Aus diesem Grund funktioniert ein Programm für alle Teile.“
In den Griff bekommen
Tyler Mardaus, Konstrukteur bei der in Minneapolis ansässigen Kurt Manufacturing – Industrial Products Division, stimmte der Notwendigkeit einer hochwertigen Werkstückhalterung zu, obwohl sich der Ansatz seines Unternehmens erheblich von dem von Lang vorgeschlagenen unterscheidet. „Unser Team für Custom Engineered Workholding (CEW) entwirft viele magnetgesteuerte, doppelt wirkende Hydrauliksysteme“, sagte er. „Hydraulik bietet einen höheren psi und damit eine größere Spannkraft als manuelles Spannen, während das Solenoid die elektronische Aktivierung des Schraubstocks durch die Roboter- oder Maschinensteuerung unterstützt, wodurch ein wirklich automatisiertes System entsteht.“
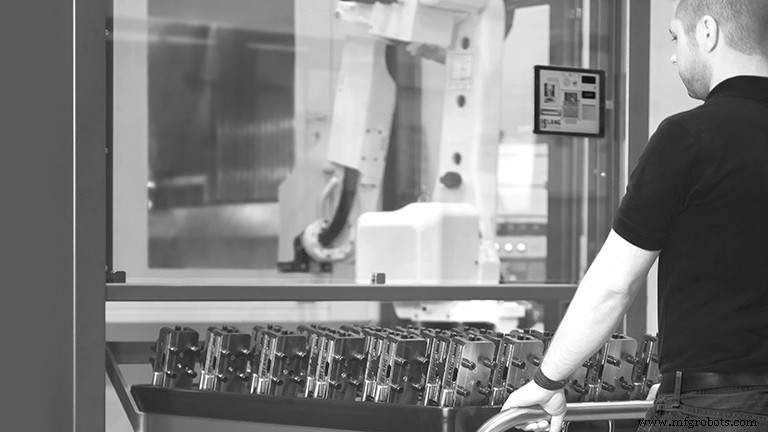
Er fügte hinzu, dass Shops ihre Automatisierungsreise beginnen sollten, indem sie auf die Jobs mit dem höchsten Volumen abzielen. Und wenn es Teile gibt, für die ein Schraubstock (oder mehrere Schraubstöcke) mit bearbeitbaren Backen verwendet werden können, können diese während der Umstellung ausgetauscht werden, was die Rüstzeit verkürzt. Was die Investition anbelangt, führt kein Weg an der Notwendigkeit einer Hydraulikpumpe und Rohrleitungen vorbei, aber es könnte möglich sein, die vorhandenen manuellen Schraubstöcke einer Werkstatt mit hydraulikfreundlichen Mutter-Schrauben-Baugruppen nachzurüsten.
„Sie sollten sich bemühen, ein Regelsystem mit geschlossenem Regelkreis zu schaffen“, sagte Mardaus. „Dies beginnt mit der Installation einer Art Vorrichtung zur Bestätigung des Teilesitzes, aber Sie müssen auch überprüfen, ob der Schraubstock mit der richtigen Kraft gespannt wurde, bevor der Zyklus gestartet werden kann, und ob der Schraubstock gelöst ist, bevor der Roboter versucht, den zu entfernen Werkstück. All diese Schritte sind entscheidend für jede automatisierte Bearbeitungslösung.“
Beschleunigung des Arbeitshaltungsaustauschs
Der Kommentar von Mardaus zur Reduzierung der Rüstzeit ist goldrichtig. Warum sollten Sie sich schließlich die Mühe machen, die Arbeitskosten durch Automatisierung zu senken, wenn Sie bei jedem Jobwechsel stundenlange teure Ausfallzeiten hinnehmen müssen? Die von ihm erwähnten Schnellwechselbacken sind ein ausgezeichneter Ausgangspunkt, aber wenn das Budget es zulässt, macht ein Nullpunkt-Positionierungssystem, wie das von Langs Makro-Grip (und anderen), den Wechsel der Spannmittel zu einer einminütigen Übung. Es sollte auch robuste CAM-Funktionen mit Simulationssoftware geben, die die nachbearbeiteten Werkzeugwege, Werkzeughalter, Schneidwerkzeuge, Werkstücke, Werkstückhalterungen und die Werkzeugmaschine selbst auswertet.
Und wie Dietmar Moll, Director of Business Development bei Zoller Inc., Ann Arbor, Michigan, erklärte, sollten Werkstätten dem Werkzeugmanagement eine hohe Priorität einräumen, beginnend mit einem Offline-Voreinstellsystem und der dazugehörigen Software. „Einer der größten Vorteile jeder Automatisierungsstrategie besteht darin, dass die Maschinenbeschickung und andere nicht wertschöpfende Arbeiten von einem Roboter oder Cobot übernommen werden, wodurch qualifiziertes Personal für wichtigere Aufgaben frei wird“, sagte Moll.
Die Offline-Werkzeugvoreinstellung ist eine dieser Aufgaben, aber es gibt auch eine gründliche Arbeitsplanung, Werkzeughalterwartung und -organisation, Schneidwerkzeuginspektion und Analyse von Fertigungsdaten. Dafür bietet Zoller eine Vielzahl von Lösungen weit über den Werkzeugbau hinaus. Seine Werkzeugverwaltungslösungen (TMS) auf Bronze-, Silber- und Gold-Level ermöglichen es einer Werkstatt, ihre Fähigkeiten nach Bedarf zu erweitern, was eine deutlich höhere Sichtbarkeit von Produktionsprozessen und werkzeugbezogenen Vermögenswerten bietet. Und weil diese mit dem kollaborativen Roboter »cora« von Zoller kommunizieren können, so Moll, dienen sie dazu, „den Kreis zu schließen“, indem sie Aufgaben im Werkzeugbau wie Werkzeugreinigung und -lagerung automatisieren.
In ähnlicher Weise helfen die integrierten Werkzeugspeicherlösungen des Unternehmens bei der Organisation dieser Ressourcen, wodurch Ausfallzeiten und Ineffizienz weiter reduziert werden. Und wenn der Auftrag abgeschlossen ist, können dieselben Systeme verwendet werden, um Werkzeuge wieder in das Lager einzuchecken, ihre Leistung zu überprüfen und die verbleibende Werkzeuglebensdauer aufzuzeichnen. „Dies hilft Werkstätten besser zu verstehen, welche Schneidwerkzeuge gut funktionieren und welche nicht, und gibt ihnen die Möglichkeit, Prozesse weiter zu verbessern und Werkzeugkosten zu senken“, sagte er.
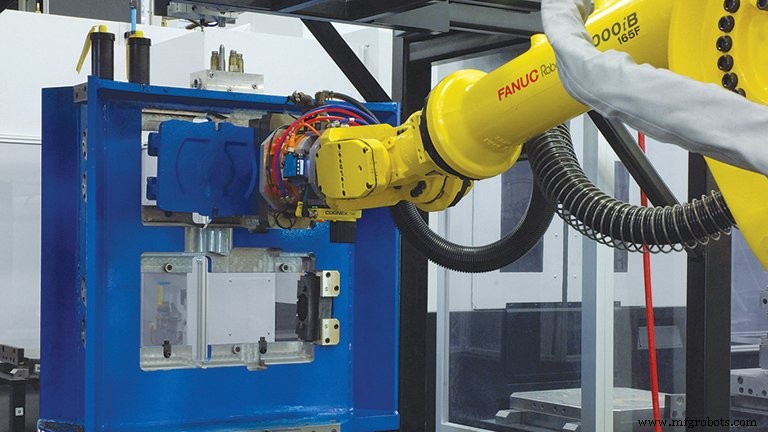
Planungsvorschläge
Ein robustes Werkzeugmanagement ist auch ein wesentlicher Bestandteil der Auftragsplanung, was sowohl für die Werkzeugmaschinen- als auch für die Roboterauslastung von entscheidender Bedeutung ist. Für Moll bedeutet das, zu wissen, welche Jobs als Nächstes anstehen und welche Tools dafür benötigt werden. Für Daniel Carranco bedeutet es mehr als das, insbesondere im Zusammenhang mit der Automatisierung. Als Direktor für kontinuierliche Verbesserung bei Global Shop Solutions Inc., The Woodlands, Texas, stellte er fest, dass alle Geschäfte – ob automatisiert oder nicht – über ein gutes ERP- und Planungssystem verfügen sollten, eines, das auch die Produktionsfläche überwachen und Informationen darüber sammeln kann der Bearbeitungsprozess.
Um den Überwachungs- und Datenerfassungsteil dieser Gleichung zu erreichen, sind jedoch integrationsfreundliche ERP-Software, Werkzeugmaschinen und Robotik erforderlich. „Wir hatten Situationen, in denen der Kunde seine Geräte in unser System integrieren wollte, aber feststellte, dass die von diesen Geräten verwendete Softwareplattform für uns fast unmöglich war, damit zu arbeiten“, sagte er. „Also ist der erste Ratschlag für alle, die eine integrierte Produktionsumgebung anstreben, sicherzustellen, dass alles effektiv kommunizieren kann und dass allen klar ist, welche Arten und Mengen von Daten ausgetauscht werden.“
Kommunikation, so scheint es, bedeutet mehr als früher. Während sich ERP-Systeme lange Zeit darin auszeichneten, Daten von Menschen in der Fertigung zu sammeln, müssen sie diese jetzt auch von Robotern und Maschinensteuerungen sammeln. Darüber hinaus enthalten diese Daten nicht nur die allgegenwärtige Auftragsnummer, Produktionszeit und fertiggestellte (oder verschrottete) Menge, die die Benutzer erwarten, sondern können auch den Materialverbrauch in Echtzeit, Inspektions- und Teilequalitätsinformationen sowie den Maschinen- und Roboterstatus anzeigen. und so weiter.
„Heute sind sicherlich viel mehr Informationen verfügbar als früher, und mit der richtigen ERP-Software, -Ausrüstung und -Integration können sie alle nahtlos und automatisch erfasst werden“, sagte er. „Dies bietet völlig neue Möglichkeiten zur kontinuierlichen Verbesserung, aber was noch wichtiger ist, es gibt den Mitarbeitern die Möglichkeit, sich auf wichtigere Dinge zu konzentrieren. Es wird keine Zeit mehr mit der ohnehin oft lückenhaften manuellen Datenerfassung verschwendet, und die Mitarbeiter können an der Prozessplanung und -analyse arbeiten.“
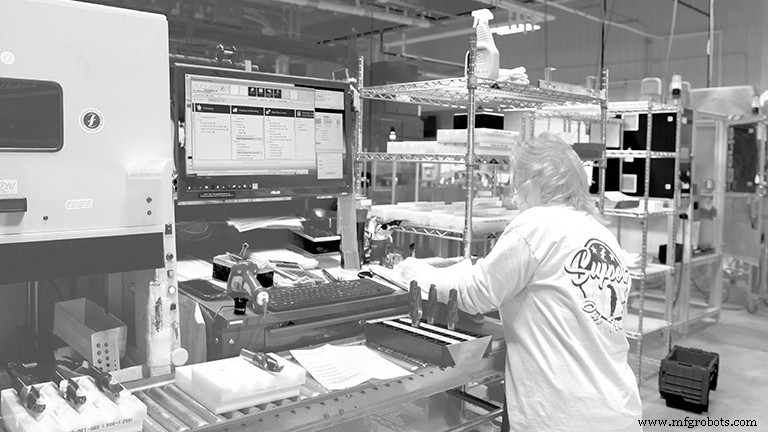
Best Practices einen Schub geben
Wie Carranco vorgeschlagen hat, sollten diese Technologien unabhängig von den Automatisierungsplänen eines Geschäfts weiterverfolgt werden, da alle dazu dienen, den Betrieb effizienter und seine OEE-Niveaus viel höher zu machen. Und wenn der nächste Schritt unternommen wird – die Implementierung eines Roboters oder Materialhandhabungssystems – wird sich die Investition umso schneller auszahlen. Angenommen, Sie interessieren sich nicht für eines der bereits besprochenen vorkonfigurierten Systeme oder können es nicht verwenden, stellt sich die Frage:„Welchen Roboter sollten wir kaufen und wie sollten wir ihn implementieren?“
Dean Elkins kann einen empfehlen. Elkins, Segmentleiter für Materialhandhabung bei der Motoman Robotics Division von Yaskawa America Inc., Miamisburg, Ohio, sagte, dass Job Shops oft eine Reihe geeigneter Roboteranwendungen anbieten, sei es Maschinenbeschickung, Teileentgratung, automatisierte Montage oder Roboterschweißen. Finding the right equipment for these applications, though, requires a good deal of evaluation and talking to knowledgeable people.
“Justifying an investment in automation depends on several factors,” said Elkins. “Obviously, the larger the production quantity, the more it makes sense to automate it. But even lower volume, repeat work can be profitable, provided the shop takes the necessary steps to reduce setup time as much as possible. Parts with longer run times are also good candidates, as are parts with simple handling requirements.”
Elkins noted that most job shops find a small to medium-sized floor-mounted robot—meaning a payload of 5-25 kg—is all that’s needed to deburr a batch of parts, weld a crateful of brackets, or tend a CNC lathe after everyone’s gone home for the night. With that, however, some level of safety guarding will be required, as will grippers, an interface to the machine tool, and possibly programming and simulation software.
Tomorrow, Today
And don’t forget the training, he warned. Automation is much simpler than it once was, yet the savvier job shop owner is still going to make an additional investment in training, and have a dedicated person on staff to manage the shop’s robotics. That said, collaborative and force-limiting robots are becoming quite popular, especially where floor space is a concern. Robots can be equipped with self-changing or quick-change grippers, increasing flexibility. Vision systems can often eliminate or at least simplify part conveying systems, and the ability to teach a robot its tasks helps reduce the need for offline programming systems. “There’s a lot to consider,” said Elkins. “That’s why I encourage anyone interested in automation to do their homework, ask questions, and partner with a reputable integrator.”
Acieta LLC, Waukesha, Wis., is one such company. Steve Alexander, vice president of operations, warns that not all integrators are created equal. “Make sure you work with someone who has experience with your type of work and the skill level to implement your robotic automation project,” he said. “Get references, go see their previous installations, and understand the quality of their work. Industrial robots are designed to last well over 10 years, so you want to make sure everything else in the cell is designed for an automated environment and is just as reliable as the robot itself.”
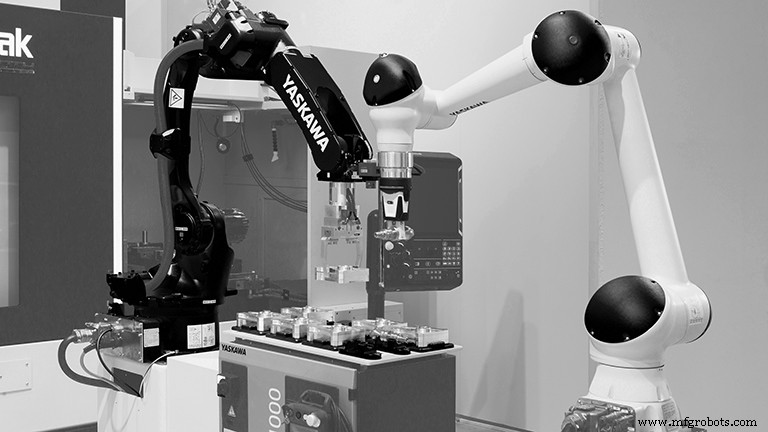
Doing so can lead to a return on investment (ROI) of just a few months, although a year or two is probably a more realistic expectation. Much of that depends on the application, of course, but the type of robot also plays a role. As Elkins noted, collaborative robots—or cobots—have become all the rage over the past few years, mainly due to their ease of use and seemingly safer operation in proximity to humans. Yet appearances can be deceiving. Cobots can be slower and less accurate than so-called “industrial robots,” possibly slowing ROI, and even the friendliest cobot can harm a human if established safety procedures aren’t followed.
This is why Elkins and others strongly recommend a risk assessment with any robot installation. He also suggested that the best approach for automation newbies is to start small and easy. “Find a single pain point and conquer that one first before looking at adding additional processes or complexity,” he said. “You want to have success right out of the gate so that everyone—the shop owner, the machine operators, and the people doing the integration—are comfortable moving on to larger or more complex projects. Sometimes, the biggest challenge is getting employee buy-in. There’s always the fear that robots will replace humans, so it’s important to make them part of the implementation. Educate them, get them involved in the roll-out, and when they find that the robot actually makes their job easier and more interesting, they’ll end up being your biggest cheerleaders.”
Automatisierungssteuerung System
- Automatisieren ... oder anders
- Hahn präsentiert auf der Automate
- Wie Automatisierung helfen kann, einen Impfstoff zu beschleunigen
- Erreichen des vollen Automatisierungspotenzials – Automatisierungsbetriebsmodell (Teil 3)
- Aufbau des Teams – Automatisierungsbetriebsmodell (Teil 2)
- Könnte Automatisierung der Schlüssel zur Schaffung von Arbeitsplätzen in der Fertigung sein?
- Bin ich zu klein, um nicht zu automatisieren
- Festlegen, wann in Automatisierung investiert werden sollte
- Insider-Tipp des Systemintegrators:Wann sollte man automatisieren?
- Präzise Automatisierung – Automate 2019 Pressemitteilung