Automatisierung für alle
Automatisierung war früher nur etwas für große Fabriken, aber jetzt können auch kleine Lohnfertiger davon profitieren
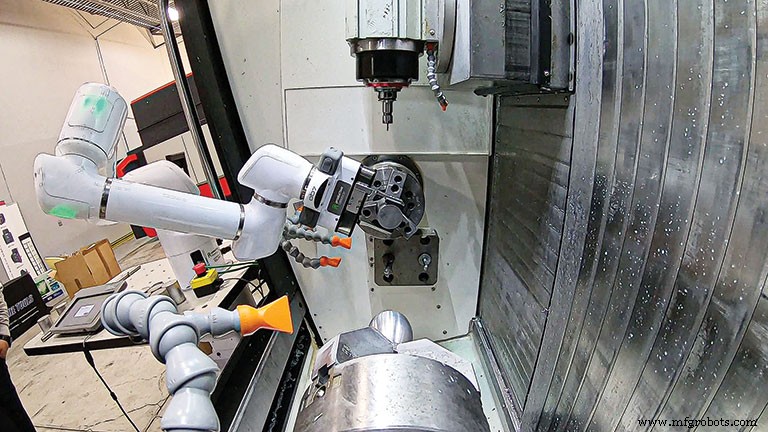
Die Automatisierung von Job Shops beschleunigt sich, angetrieben durch den kombinierten Einfluss von Industrie 4.0, dem anhaltenden Mangel an qualifizierten Arbeitskräften in der Fertigung und der COVID-Pandemie.
Die Verfügbarkeit von mehr kundenspezifischen Roboter- und Materialtransportoptionen als je zuvor hilft kleineren Herstellern, mehr zu produzieren, während die Bediener zu Aufgaben mit höherem Mehrwert überführt werden. Die steigende Nachfrage nach persönlicher Schutzausrüstung (PSA) in Verbindung mit der Notwendigkeit, die Arbeitnehmer zu schützen, hat auch die Automatisierungsbemühungen der Geschäfte verstärkt.
Die Vorteile der Automatisierung, die während der Pandemie deutlich verstärkt wurden, wurden von Courtney Ortner, Chief Marketing Officer von Absolute Machine Tools mit Sitz in Lorain, Ohio, treffend zusammengefasst:„Durch den Einsatz von Cobots (kollaborative Roboter) haben Sie einen Arbeitspartner und Sie Don Sie müssen sich keine Sorgen um soziale Distanzierung machen. Außerdem verlieren viele Geschäfte Mitarbeiter durch Quarantäne, sodass ein Geschäft auch mit dem Verlust von Personal weitergeführt werden kann. Und wir dürfen nicht vergessen, dass Lights-out-Fertigungsmöglichkeiten aufgrund des Einsatzes von Automatisierung häufiger sind; Selbst mit einem Cobot können Sie einen Auftrag freitagabends einrichten und am Montagmorgen erledigen – was Ihnen oft ermöglicht, Ihrem Produktionszyklus voraus zu sein.“
Marsch der Cobots
Roboter sind oft das Erste, woran man denkt, wenn es um automatisierte Fertigung geht. Ihre menschensichere Variante, Cobots, wird in Bezug auf einfache Einrichtung, Flexibilität und Nutzlast weiter verbessert.
Seit ihrer Einführung vor 15 Jahren haben sich die Einheiten von Universal Robots (UR), Boston, zu einer tragenden Säule in Lohnfertigern entwickelt, insbesondere in Umgebungen mit hohem Mix und geringem Volumen. Mit einer 2019 eingeführten 16-kg-Nutzlastversion (UR16) erweitert UR weiterhin die Grenzen, wo Roboter in einen Produktionsablauf passen können.
2020 war ein besonders arbeitsreiches Jahr, bemerkte Joe Campbell, Marketingleiter von UR für Nordamerika. Zwei Themen haben sich herauskristallisiert:pandemiebedingte Reorganisation und die Einführung neuer Produktionsmodelle.
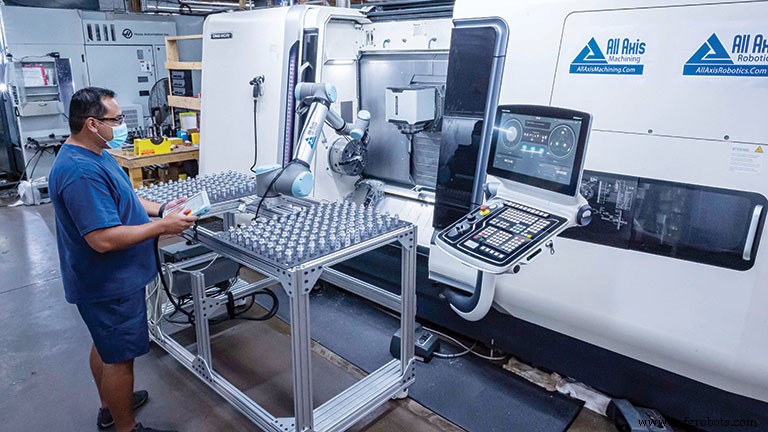
Vor allem kleine Geschäfte – die gezwungen sind, jeden Zentimeter begrenzter Immobilien effizient zu nutzen – setzen Cobots ein, um die Arbeiter sozial distanziert zu halten, bemerkte er. „Wenn Sie ein Cluster aus drei Werkzeugen haben, setzen Sie einen oder zwei Cobots ein, um den Bedienern Raum zum Atmen zu geben.“
Darüber hinaus erkennen die Geschäfte, wie Cobots das Endergebnis steigern können. „Geschäfte betrachten den Zeitplan nur an Wochentagen mit anderen Augen“, „und die Suche nach dem Fertigungsteam ist offen für mehr Flexibilität.“ Ein UR-Kunde richtete eine Wochenendschicht ein und stellte fest, dass viele Teammitglieder die neue Gelegenheit nutzten. In anderen Fällen haben Werkstätten, die zuvor einen erfahrenen Bediener hatten, der die Maschineneinrichtung und das Beladen durchführte, Cobots für die Ladefunktion hinzugefügt, während der Bediener mehrere Maschinen überwacht.
UR-Einheiten sparen Werkstattstunden bei der Einrichtungszeit. Sie können über den Touchscreen so eingerichtet werden, dass sie auf einem Boden, einer Wand oder einer Decke funktionieren; Andere Roboter sind oft speziell für eine bestimmte Ausrichtung gebaut. Auch die Zykluszeiten werden reduziert, zumal UR-Cobots mit einem Doppelgreifer konfiguriert werden können, um gleichzeitig ein fertiges Teil zu entladen und ein neues Rohteil einzulegen.
Entscheidend für die Flexibilität von UR ist die Fähigkeit, seine Cobots mit einer Reihe von Geräten und Software von Drittanbietern zu kombinieren. Auf diese wird über das Programm UR+ zugegriffen, „eine Art App Store“ für UR, sagte Campbell. Mechanische, elektrische und Softwareschnittstellen für UR-Roboter werden veröffentlicht, und Dritte entwickeln Produkte, um diese Spezifikationen zu erfüllen. „Noch wichtiger ist, dass sie sie uns zum Testen und zur Validierung vorlegen. Wenn wir sagen, ein Greifer ist Plug-and-Play, dann ist er es – weil wir ihn getestet haben.“
Zu URs Ökosystem aus 288 Peripheriegeräten gehören Teilemagazine, Bildverarbeitungssysteme, Sensoren, Montageoptionen, Roboterabdeckungen und Apps. Mit Beacon von Hirebotics beispielsweise können Bediener Cobots über die Cloud überwachen. „Sie können Produktionsstatistiken einsehen und spontan Anpassungen vornehmen“, sagte Campbell.
Im März wurde das UR+-Programm um Anwendungskits erweitert, die Komponenten wie Greifer mit Software kombinieren, „um ein bestimmtes Anwendungsproblem zu lösen“. Ein Kit von Robotiq umfasst einen Exzenterschleifer, Befestigungsmaterial, Vakuumschläuche und Software, mit der Benutzer ein Schleifprotokoll für ein Produkt wie Möbel oder Schränke programmieren können. „Sie können komplexe Konturen in Minuten programmieren, nicht in Tagen“, sagte Campbell. Das ActiNav-Kit von UR ist ein flexibles Maschinenladekit, mit dem Benutzer Teile aus einem Behälter entnehmen und mit einer präzisen Ausrichtung in verschiedene Maschinen laden können. „In weniger als einer Stunde können Sie ein neues Teil in das System einführen.“
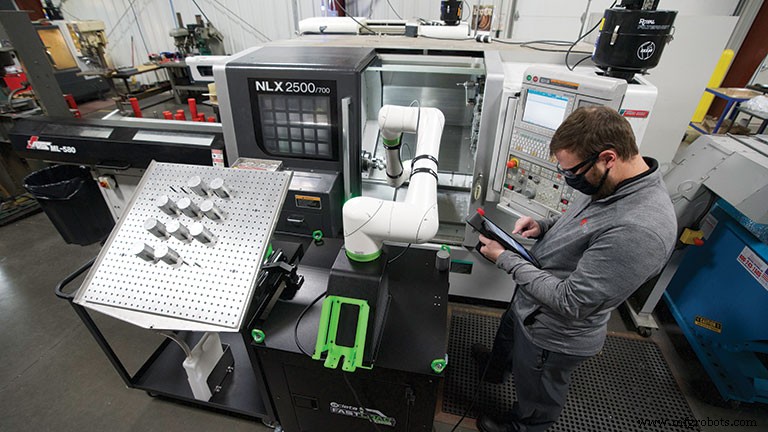
Ein weiterer Schlüssel, um Shops zur Einführung der Automatisierung zu bewegen, ist die Möglichkeit der virtuellen Schulung. UR hat kürzlich einen Meilenstein der Online-Schulung von mehr als 100.000 Bedienern über die UR Academy erreicht, die kostenlose Schulungsmodule zur Programmierung und Bereitstellung von UR-Cobots bietet.
„Wenn Sie Ihre drei leitenden Maschinisten für den größten Teil einer Woche zur Schulung an einen anderen Standort schicken müssen, wird Ihre Produktion zerstört“, sagte Campbell. Kleine Geschäfte sind „wirklich von der Möglichkeit angezogen, 90 % ihrer Schulungen online durchzuführen.“
Schnelles Laden für die Zukunft
Neben dem Automatisierungsdruck der Pandemie ist die Verlagerung der Produktion in die USA ein weiterer wichtiger Treiber für Roboter und Ladeeinrichtungen für Lohnfertiger.
„Hersteller und Lohnfertiger, die Robotik in der Vergangenheit nur langsam eingeführt haben, beginnen sich mehr denn je für Robotik einzusetzen“, sagte Jake Corning, Produktmanager und Maschinenbauingenieur bei Acieta LLC, Waukesha, Wisconsin. „Da es mehr Bekannte als Unbekannte gibt, beides Interesse und Bestellungen sind seit Beginn der Pandemie gestiegen. Sie sehen den Vorteil, den die Robotik bietet, wenn es darum geht, ihre Maschinen am Laufen zu halten und Teile herzustellen, selbst in Zeiten von sozialer Distanzierung, kranken Mitarbeitern und/oder Stillständen, die die Produktionskapazitäten beeinträchtigen.“
Da die globale Lieferkette unterbrochen ist, „sehen sie auch, dass die Pandemie eine enorme Menge an Onshoring zurück in die Vereinigten Staaten bringen wird. Sie werden mit einem noch größeren Arbeitskräftemangel konfrontiert sein als vor der Pandemie, wenn sie die Automatisierung nicht annehmen. Letztendlich, trotz der Tragödie, die die Pandemie in unserem Land verursacht hat, nehmen US-Hersteller die Robotertechnologie bereits besser an und sehen die Vorteile, die ihre Wettbewerbsfähigkeit verbessern, die Arbeitszufriedenheit und Loyalität der Arbeitnehmer verbessern und den amerikanischen Verbraucher wettbewerbsfähiger beliefern werden Preise.“
Acieta bietet eine Reihe von Lösungen an, die sich besonders für Routinen mit hohem Mix und geringem Volumen eignen, erklärte Corning.
„Die FastLOAD CX1000- und CR2000-Systeme sollen für Robotereinsteiger einfach zu bedienen sein“, sagte er. „Unsere Touchscreen-Oberfläche für den CR2000 macht es sehr einfach, den Roboter mit unterschiedlichen Teilegrößen zu betreiben. Der Bediener muss nur die Teileparameter eingeben, und das System passt das Programm automatisch an, um die neuen Teile zu verarbeiten. Die Robotergreifer und die Teilehalterung sind flexibel für eine Vielzahl von Teilegrößen, sodass viele verschiedene Teile auf demselben System laufen können.“
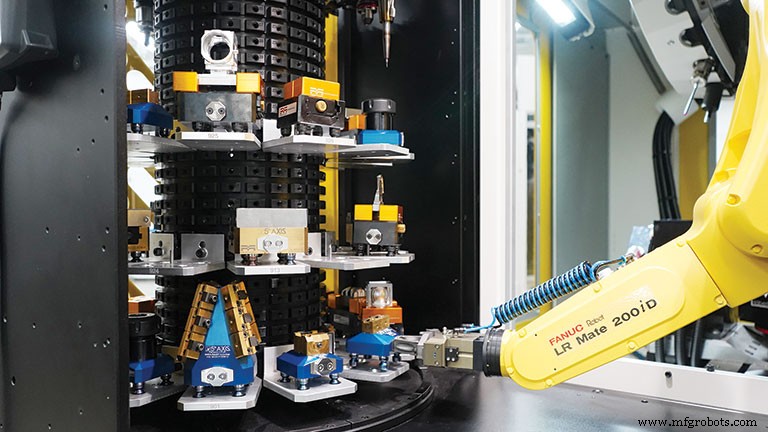
Umstellungen am CR2000 können in Minuten erfolgen, und die Systeme CX1000, CR2000 und DR2000 sind so konzipiert, dass der Roboter weiterlaufen kann, während der Bediener Teile be- oder entlädt. „Dadurch können die Maschinen in Pausen, Mittagspausen und sogar außerhalb der Schicht ununterbrochen arbeiten, solange genügend Teile eintreffen.“
Der auf Rädern montierte CX1000 lässt sich in der Werkstatt leicht manövrieren. Es ist auch mit mehreren Schnellwechsel-Halterungswagenoptionen erhältlich und verwendet den CRX-10iA/L-Roboter von FANUC, „der über eine sehr einfach zu bedienende Touchscreen-Oberfläche mit Drag-and-Drop-Programmiersymbolen verfügt“, sagte Corning. „Wenn Ihre Herausforderungen komplexer oder umfangreicher sind, können unsere kundenspezifischen Lösungen auch für Teileserien mit hoher Produktvielfalt und geringen Stückzahlen entwickelt werden, indem Technologien wie Vision, End-of-Arm-Werkzeugwechsler und flexible Spannvorrichtungen verwendet werden.“
Die begleitenden maschinellen Pflegezellen von Acieta haben sich als beliebt erwiesen, bemerkte Corning. „Es handelt sich um Standard-Robotersysteme, die für die Arbeit mit einer Vielzahl von Teilen ausgelegt sind. Da es sich um vorgefertigte Standardprodukte handelt, sind sie viel kostengünstiger als herkömmliche kundenspezifische Systeme und können in nur einer Woche geliefert werden. Alle drei Systeme können mehrere Werkzeugmaschinen gleichzeitig beschicken. Darüber hinaus verwenden unsere CX1000- und CR2000-Systeme kollaborative Roboter, die dazu beitragen, die Nutzung der Bodenfläche zu maximieren, da sie keine Sicherheitszäune benötigen.“
Für Lohnfertiger, die zum ersten Mal automatisieren, ist der kollaborative CX1000 ein guter Ausgangspunkt, sagte Corning. Indem die Mitarbeiter von sich wiederholenden Aufgaben befreit werden, können sie durch die Automatisierung „lernen, wie man ein Robotersystem programmiert oder wartet. Ein Bediener, der zuvor eine Maschine betreut hat, kann jetzt Robotersysteme auf mehreren Maschinen verwalten.“
Grundlegende Probleme lösen
Methods Machine Tools Inc., Sudbury, Mass., hilft Herstellern mit seinem genauen Verständnis der einzigartigen Bedürfnisse von Zerspanungs- und Lohnfertigern bei der Automatisierung mit dem Ziel, mehr Geschäfte zu machen und gleichzeitig qualifiziertere Arbeitskräfte zu schaffen.
„Wir brauchen mehr gute Maschinisten“, bekräftigte John Lucier, FANUC-Automatisierungsmanager für Methods. „Dabei helfen uns Roboter. Roboter helfen Geschäften dabei, mehr Jobs zu bekommen, damit sie mehr Maschinisten beschäftigen können.“ Ein gut ausgebildeter Maschinist be- und entlädt keine Maschinen, „er richtet sie ein, wählt Werkzeuge aus und schreibt Programme.“
Wie andere Anbieter hat auch Methods einen Anstieg der pandemiebedingten Automatisierung erlebt, sagte er, insbesondere bei der Herstellung von Teilen für Beatmungsgeräte.
Lucier erinnerte sich, dass er vor der Pandemie viele Geschäfte mit geringem Volumen besucht hatte, die sich zum ersten Mal mit Automatisierung befassten. Betriebe mit mittlerem Volumen, die Zellen zwei- oder dreimal pro Woche wechseln, um etwa 5.000 Teile zu produzieren, werden immer häufiger, und Methods bietet die förderbandbasierte Job Shop Cell Pro-Linie für diese Umgebungen. Verstellbare Bahnteiler ermöglichen einen schnellen Wechsel zwischen kleinen und großen Teilen. Eine weitere beliebte Option ist eine Reihe von Schubladen mit einer Stahl- oder Aluminiumplatte mit Löchern für 20 bis 40 Teile.
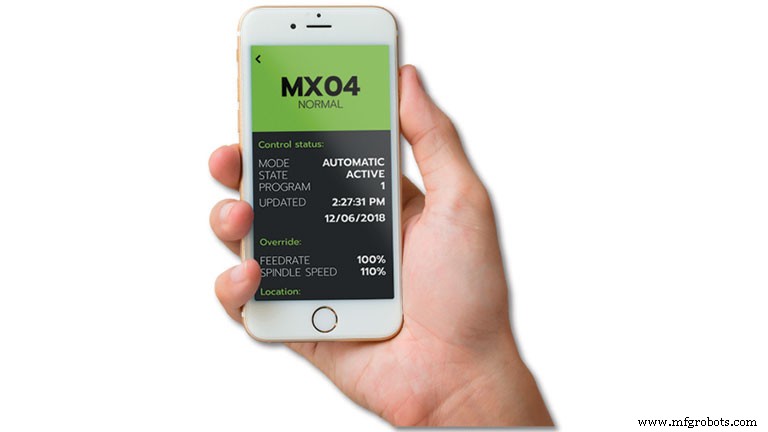
Die Aufspannung ist ein weiterer wichtiger Aspekt, fügte Lucier hinzu; automatisierte Schraubstöcke sind eine relativ einfache Lösung. „Es muss nicht kompliziert sein, mit Schwenkspannern und so. Es könnte so etwas wie ein gutes altes Spannfutter oder ein Schraubstock mit Pneumatik oder Hydraulik zum Öffnen und Schließen sein, und Sie stellen Ihre eigenen Backen her – nicht anders als das, was viele Geschäfte mit Auflagen von etwa 50 Teilen machen.
Für Teile mit geringerem Volumen, selbst ab einer Losgröße von 1, bietet Methods die Roboter-Rotationslagerkarussellsysteme Plus-K und Plus-K 60 an. „Wir machen den Roboter nicht teilespezifisch; Der Roboter ist so eingerichtet, dass er allgemeine Werkstückhalterungen in die Maschine ein- und ausfährt, egal ob es sich um einen kleinen Schraubstock oder eine Palette handelt. Der Roboter ist so eingerichtet, dass er ein gemeinsames Merkmal an der Vorderseite der Werkstückhalterung greift.“ Die Teile werden in einen manuellen Schraubstock geladen, und der Roboter ist so vorprogrammiert, dass er wie ein Palettenladesystem funktioniert; Es ist keine Endbenutzerprogrammierung erforderlich. Dieses System erweitert auch das Standardwerkzeugangebot des RoboDrill von 21 auf optional 161 Werkzeuge.
Mit Lösungen wie diesen erzielen Lohnfertiger in der Regel eine Kapitalrendite in weniger als 12 bis 18 Monaten. „Unser Ziel ist es, Sie davon zu überzeugen, es in zwei oder drei Schichten zu betreiben – eine Roboterzelle zu nehmen, das Zuführsystem mit Teilen zu füllen und um 17:00 Uhr nach Hause zu gehen und zwei bis sechs Stunden Laufzeit zu haben. Wenn ich ein automatisiertes System bekommen kann, das 80 % der von Ihnen geplanten Arbeit erledigt, machen wir unsere Sache verdammt gut.“
Die Lösungen von Informing Methods sind eine langjährige Verbindung zu Lohnfertigern und wissen, wie sie funktionieren, bemerkte Lucier, selbst Maschinenschlosser von Beruf. Beispielsweise erinnert er die Werkstätten oft daran, dass sie ihre eigenen Greifer aus Stahl oder Aluminium bearbeiten können. Und das Optimieren der auf Robotern vorinstallierten Programme kann einfacher sein als die CNC-Programmierung. Die Automatisierungsintegrationsgruppe des Unternehmens ist sich der Probleme rund um Werkzeugmaschinen sehr bewusst, von Kühlmittel und Spänen bis hin zu Werkzeugrotation, Standzeit, Entgratung und mehr.
„Wenn Sie Roboter an Werkzeugmaschinen anbringen wollen, brauchen Sie einen Roboterintegrator, der das tut“, schloss Lucier. „Die Vorteile von Robotern sollten nicht schwer zu rechtfertigen sein.“

Bedarf einschätzen, beschleunigen
Das Verständnis des Automatisierungsbedarfs eines Job-Shops beginnt mit einer gründlichen Bewertung des Volumens, das zur Steigerung der Produktivität erforderlich ist.
Bei der Beauftragung durch einen Kunden, sagte Ortner von Absolute, „erstellen wir ein Systemlayout, entscheiden über bewährte Vorgehensweisen für die Automatisierung – Fördersysteme, Roboter, Rohmaterialhandhabung, Fertigteilhandhabung – und entwerfen es dann in CAD, um sicherzustellen, dass alle Teile in ihren Boden passen planen, während sie gleichzeitig innerhalb ihres Budgets arbeiten.“
Zusätzlich zum Angebot einer Reihe von Standardautomatisierungsgeräten, von Cobots über die Teilehandhabung bis hin zur Überwachung, bietet Absolute „ein schlüsselfertiges Paket“, sagte Ortner. „Wir beziehen die unseres Erachtens beste Lösung und arbeiten mit diesen Lieferanten zusammen, um den Erfolg sicherzustellen.“
Die Erfahrung von Absolute bei der Beschaffung der richtigen Ausrüstung zahlt sich eindeutig aus, stellte sie fest. „Ein Kunde, der einen OB7-Cobot verwendet, erzielt 20 Prozent mehr Effizienz und viel weniger Ausschuss in einer Schicht. Sie können die Lieferzeiten bei diesem speziellen Lauf um zwei Wochen verkürzen, wodurch die Maschine oder Zelle für zusätzliche Arbeit für einen höheren ROI geöffnet wird. Da sie sich nicht so oft wiederholende Aufgaben erledigen müssen, gibt es weniger Schadensersatzansprüche der Arbeitnehmer für das Unternehmen – und die Arbeitnehmer melden sich auch nicht so oft krank, wodurch [der Laden] viel Geld gespart wird.“
Wie andere Geschäfte festgestellt haben, bedeutet die erhöhte Verfügbarkeit von Bedienern für andere Aufgaben oft, „dass sie mehr Zeit haben, zu den Gesamtprozessen beizutragen, wie z. B. Qualitätskontrollen. Sie sind mehr in das Prozessmanagement involviert, anstatt nur Knöpfe zu drücken, und sind weniger gelangweilt und erschöpft.“
Die Erzielung dieser Vorteile kann überraschend kostengünstig sein, fügte Ortner hinzu. „Unsere Cobot-Linie von Productive Robotics beginnt bei 34.900 US-Dollar für das Basis-CNC-Paket. Sie können von einem Basis-CNC-Paket zu einer vollständig integrierten Zelle aufrüsten, indem Sie mehrere Cobots, Förderbänder, In-Prozess-Messungen und Teilepräsentationsmethoden verwenden.“
Überwachung für mehr Output
Um Werkstätten dabei zu unterstützen, Aufträge im Zeitplan zu halten und mehr Projekte unbeaufsichtigt auszuführen, bietet Mitsubishi Electric Automation Inc., Vernon Hills, Illinois, seine MTConnect-basierte Integrated Machine Analytics (IMA) zur Maschinenüberwachung an. Die IMA Mobile App bietet einen einfach zu installierenden Einstieg in die Maschinenüberwachung.
Mit IMA „sind Geschäfte in der Lage, die Produktion besser zu verstehen, was bei der genauen Planung von Aufträgen hilft, um die verfügbaren Maschinen und Arbeitszeiten voll auszunutzen, sowie genauere Gebote für mehr Aufträge abzugeben“, sagte Robert Brodecki, IMA Mobile Service Product Manager für Mitsubishi Electric Automation.
Die einzige Hardware, die erforderlich ist, ist eine Ethernet-Verkabelung und ein Hub/Switch, wenn mehrere Maschinen verbunden werden, und die Einrichtung einer Maschine dauert nur 5 bis 10 Minuten, erklärte er. „Mit dem Low-Cost-Punkt können Benutzer den ROI innerhalb weniger Tage sehen, insbesondere wenn sie unbeaufsichtigt oder ohne Licht produzieren und Produktionszeit verloren haben, weil eine Maschine ausfällt und es erst später herausfindet. Mit den Benachrichtigungen von IMA Mobile wissen Sie innerhalb von 10 bis 15 Sekunden, ob eine Maschine aufgehört hat zu schneiden, egal wo Sie sich befinden.“
Die Maschinenüberwachung verbessert den Durchsatz erheblich, fügte er hinzu. „Wenn man sich nur den Ausführungsstatus ansieht, haben viele Jobshops Maschinen, die Jobs zwischen 25 und 40 Prozent ihrer verfügbaren Zeit ausführen. Durch einfache Überwachung des aktuellen Status über IMA Mobile können sie diesen schnell auf 50 Prozent oder mehr erhöhen, indem sie sich sofort um jede Maschine kümmern können, die aus irgendeinem Grund die Produktion eingestellt hat. Auch dies sind aktuelle Daten direkt von der Maschine; es beseitigt das Ratespiel, wie lange die Maschine geschnitten hat, im Leerlauf oder ausgeschaltet.“ Die verfügbaren Maschinenstunden werden erweitert, indem mehr Schichten mit weniger Arbeitern – oder unbeaufsichtigt – ausgeführt werden, ohne dass die Produktion aufgrund eines unerwarteten Stillstands verloren geht.
Mit IMA Mobile können Bediener zu wertschöpfenden Aufgaben wechseln, „in dem Wissen, dass die App sie benachrichtigt, wenn der Job beendet oder durch etwas unterbrochen wird, das Aufmerksamkeit erfordert.“
Mit relativ niedrigen Einstiegskosten, so Brodecki, ermöglicht IMA den Benutzern, „ihre Produktion zu verstehen und Verbesserungen vorzunehmen sowie einfachere, unbeaufsichtigte Bearbeitungsprojekte zu starten, während sie sicher sein können, dass ihre Maschinen weiterlaufen. Da alles um den MTConnect-Standard herum aufgebaut ist, muss ein Benutzer, wenn er sich entscheidet, zu einem umfassenderen, anpassbaren Überwachungssystem zu wechseln, nicht dafür bezahlen, dass seine Maschinen wieder verbunden werden; Sie richten die neue Software einfach auf die MTConnect-Agenten aus, und die Maschinendaten sind schnell zugänglich.“
Diese einfache Eingabe sei für die Automatisierung in Zeiten von COVID besonders wichtig gewesen, schloss er. „Das ist sinnvoll, da Unternehmen mehr automatisieren wollen, aber es ist schwierig, genau zu wissen, wo und wie, ohne genaue Produktionsdaten, um die zu automatisierenden Bereiche zu identifizieren. Zu Beginn der Pandemie standen viele Unternehmen, mit denen wir sprachen, beim Thema Maschinenüberwachung noch auf der Kippe. Als sich die Pandemie fortsetzte und Unternehmen erkannten, dass sie Automatisierungs- und Telearbeitslösungen nicht länger vermeiden konnten, haben sie diese Projekte ganz oben auf die Liste gesetzt.“
Automatisierungssteuerung System
- Automatisierung:Neue Greifer für Cobots
- Automatisierung:Starker Vakuumgreifer für Cobots
- Automatisierung:Neues Zubehör für Cobots
- Automatisierung:Kompatible Entgratklinge für Roboter
- Automatisierung:Plug-and-Play-Schraubendreher für Cobots
- Automatisierung:Was sie für die Zukunft des Geschäfts bedeutet
- ABB pilotiert Automatisierungslösung für Rechenzentren
- Ein Handbuch zur Implementierung intelligenter Automatisierung heute
- Was Hyperautomatisierung für RPA-Benutzer bedeutet
- Schneider Electric fordert eine durchgängige Industrieautomation