Formsand – Eigenschaften, Typen, Verfahren, MCQs
In diesem Artikel lernen wir etwas über Was ist Formsand ,Eigenschaften von Formsand und Formsandarten .
Das Hauptmaterial, das in der Gießerei zum Formen verwendet wird, ist der Sand. Denn es besitzt die für Gießereizwecke wichtigen Eigenschaften.
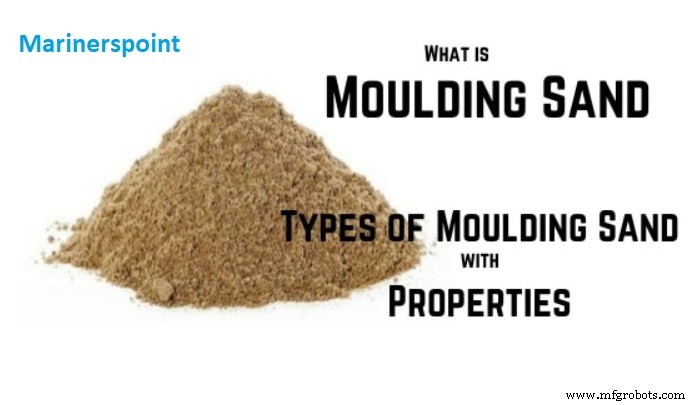
Quellen
Alle Sande entstehen durch das Aufbrechen von Felsen aufgrund der Einwirkung von Naturkräften wie Frost, Wind, Regen, Hitze und Wasserströmungen. Felsen sind jedoch in ihrer Zusammensetzung sehr komplex, und Sande enthalten die meisten Elemente der Felsen, von denen sie Fragmente sind. Aus diesem Grund Formsande in verschiedenen Teilen der Welt sehr unterschiedlich. Heute wird Sand aus Stellen gewonnen, die einst wahrscheinlich Grund und Ufer von Flüssen und Sanddünen waren.
In Indien findet man Gießereisande in den Gebieten Damodar und Barakar, Santhal Pargana (Bihar), Batala (Gurdaspur, Punjab), Bhavnagar (Saurashtra), Londha (Maharashtra), Avadi und Veeriyambkam (Madras), Kanpur, Jabalpur, Rajkot, Guntur , im Ganges und an vielen anderen Orten.
Hauptbestandteile
Die wichtigsten Inhaltsstoffe von Formsanden sind:(1) Quarzsandkörner (2) Ton (3) Feuchtigkeit und (4) verschiedene Materialien.
Kieselsäure in Form von körnigem Quarz, selbst ein Sand, ist der Hauptbestandteil von Formsand. Quarzsand enthält 80 bis 90 Prozent Siliziumdioxid und zeichnet sich durch eine hohe Erweichungstemperatur und thermische Stabilität aus.
Es ist ein Produkt des Aufbrechens von Quarzgestein oder die Zersetzung von Granit der aus Quarz und Feldspat besteht . Der Feldspat wird bei seiner Zersetzung zu Ton (wässriges Aluminiumsilikat). Quarzsandkörner verleihen dem Sand jedoch Feuerfestigkeit, chemische Beständigkeit und Durchlässigkeit. Sie werden nach ihrer durchschnittlichen Größe und Form spezifiziert.
Ton ist definiert als Sandpartikel (unter 20 Mikron im Durchmesser), die sich nicht mit einer Geschwindigkeit von 25 mm pro Minute absetzen, wenn sie in Wasser suspendiert sind. Lehm besteht aus zwei Zutaten:feiner Lehm und echter Lehm . Feinschlamm ist eine Art Fremdkörper oder mineralische Ablagerung und hat keine Bindekraft.
Es ist der echte Ton, der dem Formsand die nötige Haftfestigkeit verleiht, damit die Form nach dem Stampfen nicht ihre Form verliert. Echter Ton besteht aus extrem winzigen Aggregaten kristalliner, normalerweise flockenförmiger Partikel, die als Tonmineralien bezeichnet werden. Die meisten Formsande für verschiedene Arbeiten enthalten 5 bis 20 Prozent Ton. Feuchtigkeit in der erforderlichen Menge liefert die Bindewirkung des Tons.
Wenn Wasser zu Ton hinzugefügt wird, dringt es in die Mischung ein und bildet einen Mikrofilm welches die Oberfläche von flockenförmigen Tonpartikeln beschichtet. Die Bindungsqualität von Ton hängt von der maximalen Dicke des Wasserfilms ab, den er aufrechterhalten kann. Die Bindungswirkung wird als am besten angesehen, wenn das zugesetzte Wasser genau die Menge ist, die zur Bildung des Films erforderlich ist. Andererseits wird die Bindungswirkung verringert und die Form wird geschwächt, wenn das Wasser zu viel ist. Der Wassergehalt sollte zwischen 2 und 8 Prozent liegen.
Verschiedene Materialien, die neben Kieselsäure und Ton in Formsand gefunden werden, sind Eisenoxid, Kalkstein, Magnesia, Soda und Pottasche. Die Verunreinigungen sollten unter 2 Prozent liegen.
Klassifizierung
Arten von Formsanden:Sie können allgemein in drei verschiedene Arten eingeteilt werden:(1) natürliche Formsande , (2) synthetischer Sand oder Sand mit hohem Quarzgehalt , und (3) Spezialsande .
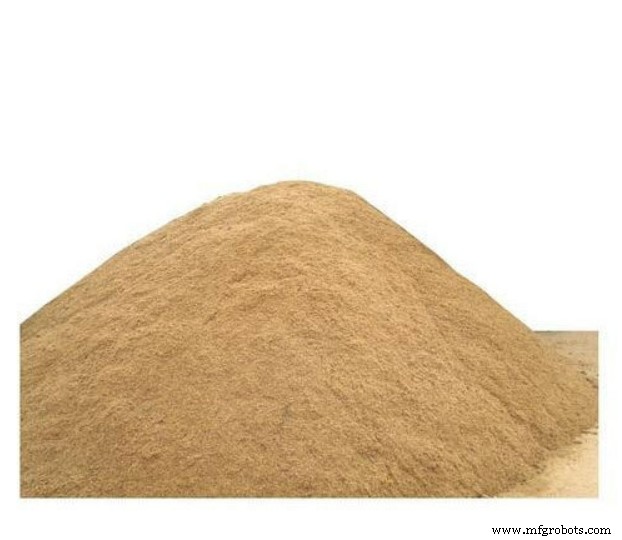
1. Natürliche Formsande
Natürliche Formsande , grüne Sande genannt, werden aus Flussbetten entnommen oder aus Gruben gegraben. Sie besitzen eine beträchtliche Menge Ton, der als Bindeglied zwischen den Sandkörnern dient, und werden wie erhalten mit zugesetztem Wasser verwendet. Die Menge und Art des vorhandenen Tonminerals beeinflussen die Festigkeit, Zähigkeit und Feuerfestigkeit des Sandes.
Diese werden auch durch Zerkleinern und Mahlen von weichem gelbem Sandstein, Karbongestein usw. gewonnen. Während des Mahlvorgangs werden Tonaggregate zersetzt und Tonpartikel werden gleichmäßig über die Sandkörner verteilt. Die Kornform dieser Sande muss subeckig bis rund sein.
Aufgrund ihrer einfachen Verfügbarkeit, niedrigen Kosten und hohen Betriebsflexibilität werden natürliche Formsande für die meisten Eisen- und Nichteisen-Leichtgussteile verwendet. Die Anforderungen dieser Sande werden von IS:3343-1965 erfüllt , das sie in drei Grade A eingeteilt hat , B und C , je nach Tongehalt und Sintertemperatur.
2. Synthetischer Sand
Synthetischer Sand sind grundsätzlich Sande mit hohem Quarzgehalt, die wenig (weniger als 2 Prozent) oder kein Bindemittel (Ton) in natürlicher Form enthalten. Sie treten als lose oder schlecht konsolidierte Ablagerungen sedimentären Ursprungs, von der Küste ins Landesinnere gewehte Dünen oder angesammelte Ablagerungen in Flussmündungen und Flüssen entlang der Küste auf.
Sie werden auch in Gießereien hergestellt, indem zuerst Quarzit-Sandsteine zerkleinert und diese dann gewaschen und sortiert werden, um eine Sandsorte mit der erforderlichen Form und Kornverteilung zu erhalten. Die gewünschten Festigkeits- und Bindungseigenschaften dieser Sande werden durch separate Zusätze wie Bentonit, Wasser und andere Materialien entwickelt.
Dies ermöglicht eine größere Flexibilität beim Gehalt an Eigenschaften wie Grün- und Trockenfestigkeit, Durchlässigkeiten und anderen, die leicht nach Belieben variiert werden können. Tatsächlich sind synthetische Sande daher teurer als natürliche Sande.
IS:1987-1974 deckt die Anforderungen an Sand mit hohem Quarzgehalt für den Einsatz in Gießereien ab und teilt ihn je nach Quarzgehalt in drei Klassen ein .
3. Spezielle Sande
Spezialsande sind ideal, um spezielle Eigenschaften zu erhalten, die normalerweise in anderen Sanden nicht erhalten werden. Als Spezialsande werden häufig Zirkon, Olivin, Schamotte, Chromit und Chrom-Magnesit verwendet. Zirkonsande eignen sich für Kerne aus Messing- und Bronzeguss. Einige Gießereien verwenden Olivinsand für komplizierte Nichteisengussteile. Schamotte ist wertvoll für schwere Stahlgussteile.
Chromit- und Chrom-Magnesit-Sande sind besonders nützlich, wenn die Abkühlungstendenz erhöht werden soll, um die Verfestigung zu steuern. Sie eignen sich auch als Verkleidungsmaterialien in Formen für Stahlguss.
Formsandarten
Formsande können wiederum nach ihrer Verwendung in verschiedene Sorten eingeteilt werden. Diese werden unten beschrieben.
Formteil aus grünem Sand
Es ist eine Mischung aus Quarzsand mit 18 bis 30 Prozent Ton und einem Gesamtwassergehalt von 6 bis 8 Prozent. Ton und Wasser liefern die Bindung für grünen Sand. Es ist fein, weich, leicht und porös. Feucht, in der Hand zusammengedrückt, behält es die Form, die ihm unter Druck den Eindruck gibt. In diesem Sand hergestellte Formen werden als grüne Sandformen bezeichnet.
Trockensandformung
Grüner Sand, der getrocknet oder gebacken wurde, nachdem die Form hergestellt wurde, wird als trockener Sand bezeichnet. Sie eignen sich für größere Gussteile. In diesem Sand hergestellte Formen werden als Trockensandformen bezeichnet.
Lehm Sand
Lehmsand ist reich an Ton, bis zu 50 Prozent oder so, und trocknet hart. Dies wird insbesondere beim Lehmformen in der Regel für große Gussstücke eingesetzt.
Mit Blick auf Sand
Sichtsand bildet die Stirnseite der Form. Es wird direkt neben der Oberfläche des Modells verwendet und kommt beim Gießen der Form mit dem geschmolzenen Metall in Kontakt. Folglich wird es den härtesten Bedingungen ausgesetzt und muss daher eine hohe Festigkeit und Feuerfestigkeit besitzen.
Es besteht aus Quarzsand und Ton, ohne Zusatz von Altsand. Um zu verhindern, dass sich das Metall in den Sand einbrennt, werden verschiedene Formen von Kohlenstoff verwendet. Sie werden manchmal mit der 6- bis 15-fachen Menge feinen Formsandes vermischt, um Verkleidungen herzustellen.
Die Decksandschicht in einer Form beträgt üblicherweise 20 bis 30 mm. 10 bis 15 Prozent der gesamten Formsandmenge, die in der Gießerei verwendet wird, ist Vorsatzsand. Eine Vorsatzsandmischung für das Grünsandformen von Gusseisen kann aus 25 % frischem und speziell aufbereitetem Sand, 70 % altem Sand und 5 % Meereskohle bestehen.
Backing Sand
Stützsand oder Estrichsand wird verwendet, um den Decksand zu unterstützen und das gesamte Volumen des Kolbens zu füllen. Hierfür wird hauptsächlich alter, mehrfach gebrauchter Formsand verwendet.
Der Grundsand wird manchmal auch Schwarzsand genannt, da alter, immer wieder verwendeter Formsand durch die Zugabe von Kohlenstaub schwarz gefärbt ist und bei Kontakt mit geschmolzenem Metall brennt.
System Sand
In mechanischen Gießereien, in denen maschinell geformt wird, wird ein sogenannter Systemsand verwendet, um den gesamten Formkasten zu füllen. In maschinellen Sandaufbereitungs- und Handhabungseinheiten wird kein Decksand verwendet. Der Altsand wird durch Zugabe von Wasserbindern und speziellen Additiven gereinigt und reaktiviert. Dies wird als Systemsand bezeichnet. Da die gesamte Form aus diesem Systemsand besteht, muss die Festigkeit, Durchlässigkeit und Feuerfestigkeit des Sandes höher sein als die des Grundsandes.
Abschied von Sand
Trennsand wird verwendet, um zu verhindern, dass der Grünsand an dem Muster klebt, und um auch zu ermöglichen, dass sich der Sand auf der Trennfläche der Kappe und des Widerstands ohne Anhaften trennt. Dies ist sauberer, tonfreier Quarzsand, der denselben Zweck erfüllt wie Trennstaub.
Kern Sand
Sand, der zur Herstellung von Kernen verwendet wird, wird als Kernsand bezeichnet, manchmal auch als Ölsand. Dies ist Quarzsand, vermischt mit Kernöl, das sich aus Leinöl, Harz, leichtem Mineralöl und anderen Bindemitteln zusammensetzt. Pech oder Mehle und Wasser können aus wirtschaftlichen Gründen in großen Kernen verwendet werden.
Eigenschaften von Formsand
Welche Eigenschaften hat Formsand ?
Richtiger Formsand muss sechs Eigenschaften besitzen. Formsandeigenschaften sind:Es muss Porosität, Fließfähigkeit, Kollabierbarkeit, Haftfähigkeit, Kohäsion oder Festigkeit und Feuerfestigkeit aufweisen.
- Porosität :- Die wichtigste Eigenschaft von Formsand ist die Porosität, auch Permeabilität genannt. Es bezieht sich auf die Fähigkeit des Formsandes, Gase durchzulassen. Beim Gießen von geschmolzenem Metall in den Sandhohlraum entstehen Gase und Dampf. Diese Eigenschaft wird nicht nur durch die Form und Größe der Sandpartikel beeinflusst, sondern auch durch die Menge an Ton, Bindemittel und Feuchtigkeit in der Mischung.
- Fließfähigkeit :- Die Fähigkeit des Sandes, kleine Lücken im Muster zu füllen. Eine hohe Fließfähigkeit erzeugt eine präzisere Form und ist somit nützlich für detaillierte Gussteile.
- Zusammenklappbarkeit :- Die Fähigkeit der Sandmischung, unter Krafteinwirkung zu kollabieren. Eine größere Formkollapsfähigkeit ermöglicht es dem Metallguss, beim Erstarren frei zu schrumpfen, wodurch Heißrisse oder Risse vermieden werden.
- Klebkraft :- Haftvermögen ist die Eigenschaft von Sand, die bewirkt, dass Sandpartikel an den Seiten des Formkastens haften. Die Haftung des Sandes ermöglicht das ordnungsgemäße Anheben der Kappe zusammen mit dem Sand.
- Zusammenhalt :- Die Kohäsion von Sand ist die Fähigkeit seiner Partikel, zusammenzuhalten. Es ist die Zugfestigkeit des Formsandes. Diese Eigenschaft ist entscheidend, um die komplizierten Formen der Form beizubehalten. Eine unzureichende Festigkeit kann dazu führen, dass die Formpartikel während der Handhabung, des Umdrehens oder des Schließens kollabieren. Die Zugabe von Ton und Bentonit verbessert die Bindekraft.
- Refraktärheit :- Die Feuerfestigkeit von Sand bezieht sich auf seine Fähigkeit, hohen Temperaturen von geschmolzenem Metall ohne Schmelzen oder Erweichen standzuhalten. Formsande mit geringer Feuerfestigkeit können Feuer fangen, wenn geschmolzenes Metall in die Form gegossen wird. Sandformen sollten typischerweise Temperaturen von bis zu 1650°C standhalten.
- Stärke :- Die Festigkeit des Standes, der getrocknet oder gebacken wurde, wird als Trockenfestigkeit bezeichnet. Es muss dann stark genug sein, um den Erosionskräften von geschmolzenem Metall standzuhalten und seine Form zu behalten.
Sandformverfahren
Sandguss , auch als Sandformguss bekannt oder Sandformverfahren , ist ein gussbasiertes Herstellungsverfahren, das eine Sandform verwendet. Daraus werden Metallgegenstände und -komponenten in verschiedenen Größen und Formen hergestellt. Um seine Verbreitung ins rechte Licht zu rücken:Sandguss macht über 60 % aller Metallgussteile aus. Die sechs Hauptphasen des Sandgusses werden unten im Detail beschrieben.
Schritt 1:Legen Sie das Formmuster in den Sand
Das Einbringen des Formmodells in Sand ist die Anfangsphase des Sandgusses. Die Form hat einen direkten Einfluss auf die Größe und Form des Gussstücks. Folglich müssen Hersteller neue Formen entwickeln, um Metallgegenstände und -komponenten in bestimmten Größen und Formen herzustellen.
Schritt 2:Richten Sie ein Gating-System ein
Ein Angusssystem wird in fast jedem Gießprozess verwendet, und der Sandguss ist keine Ausnahme. Es leitet die geschmolzene Form mithilfe eines Gießbechers in den Formhohlraum und führt Tunnel oder „Tore“ zur Form. Fertigungsunternehmen werden ein solches Angusssystem aufstellen, nachdem sie das Formdesign in Sand gesetzt haben.
Schritt 3:Schimmelmuster sollten entfernt werden
Fertigungsunternehmen können dann das Formmuster aus dem Sand entfernen, nachdem das Angusssystem vorhanden ist. Zu diesem Zeitpunkt ist das Formmuster irrelevant. Der Sand nimmt die Form des Formmusters an, wenn er darin platziert wird. Dadurch ist es möglich, das Formmuster zu entfernen.
Schritt 4:Gießen Sie geschmolzenes Metall in den Hohlraum der Form
Jetzt ist es an der Zeit, das geschmolzene Metall in den Hohlraum der Form zu gießen. Eisen, Stahl, Aluminium, Bronze, Magnesium, Zink und Zinn sind nur einige der Metalle und Legierungen, die in Sand gegossen werden können. Fertigungsunternehmen müssen Metalle oder Legierungen je nach verwendetem Metall oder Legierung möglicherweise auf bis zu 3.000 Grad Fahrenheit erhitzen. Das Metall oder die Legierung wird in den Formhohlraum gegossen, sobald es sich von einem festen in einen flüssigen Zustand verwandelt hat.
Schritt 5:Warten Sie, bis das Metall abgekühlt ist
Fertigungsunternehmen müssen warten, bis das geschmolzene Metall abgekühlt ist, nachdem es in das Formloch eingebracht wurde. Auch hier erfordern unterschiedliche Metallarten unterschiedliche Abkühlzeiten. Das geschmolzene Metall kühlt ab und geht von einer flüssigen in eine feste Form über.
Schritt 6:Brechen Sie die Form auf, um den Metallguss zu entfernen
Das Aufbrechen der Form zur Entnahme des neu entstandenen Metallgusses ist der sechste und letzte Schritt beim Sandguss. Formmuster sind normalerweise wiederverwendbar, Formen selbst jedoch nicht. Folglich muss jedes Mal, wenn ein Fertigungsunternehmen ein neues Metallprodukt oder eine Komponente im Sandguss herstellen möchte, eine neue Form entwickelt werden.
Kollabibilität von Formsand
Kollabibilität von Formsand bezieht sich auf die Fähigkeit des Sandes, sich nach dem Erstarren leicht vom Guss zu entfernen. Sande mit geringer Kollabierbarkeit haften hartnäckig am Gussstück. Ein Sand mit schlechter Kollabierbarkeit führt zu Rissen und Heißrissen in Metallgussteilen, die sich beim Abkühlen stark biegen oder lange Gefriertemperaturbereiche aufweisen. Um die Zusammendrückbarkeit zu verbessern, können bestimmte Zusätze eingeführt werden.
MCQ
1. Durchlässigkeit kann als Eigenschaft von Formsand definiert werden
A. um Sandkörner zusammenzuhalten
B. um Gase leicht aus der Form entweichen zu lassen
C. um der Schmelzwärme zu widerstehen, ohne Anzeichen von Erweichung zu zeigen
D. keines der oben genannten
Antwort:Option B
2. Warum sollte der Formsand porös sein?
A. Damit Gase eindringen können
B. Damit Wasser eindringen kann
C. Damit Gase entweichen können
D. Damit Wasser entweichen kann
Antwort:Option C
Erklärung : Als Formsand wird ein Sand bezeichnet, der Löcher aufweist und eine gewisse Feuchtigkeit enthalten kann. Ein Formteil sollte Poren enthalten und porös sein, damit Gase ungehindert entweichen können.
Hier drehte sich alles um Formsand, wo wir alle Themen behandelt haben, wie z. B. Was ist Formsand, Beschreibung der Eigenschaften von Formsand, Grünsand-Formverfahren, Trockensand, Kollabierbarkeit und einige MC-Fragen, die auf diesen Themen basieren.
Industrietechnik
- Arten und Eigenschaften von Tantalpulver
- Formsand:Arten und Bestandteile | Gießen | Metallurgie
- Eigenschaften von Formsand | Materialien | Gießen | Metallurgie
- Was ist Formen? Arten von Umformprozessen [Notizen &PDF]
- Was ist Formsand? - Arten und Eigenschaften
- Arten von Lichtbogenschweißprozessen
- Definition, Prozess und Typen von Fräsmaschinen
- Bedeutung und Typen des Herstellungsprozesses
- Arten von Sandgussgeräten
- AMPCO® 25 Sandguss