Groupe Beneteau reduziert manuelle Verarbeitung um 60 % durch automatisierte Bootsbearbeitung
Groupe Beneteau ist ein Hersteller von Luxusyachten und Segelbooten mit Sitz in Frankreich und Niederlassungen in Polen, Italien und den USA. Rümpfe, Decks und andere Bootskomponenten müssen aufgrund der Dicke und Festigkeit des Glasfasermaterials mit CNC-Maschinen bearbeitet werden. Die Bearbeitung per Hand würde zu lange dauern und die Auswirkungen auf die Gesundheit und Sicherheit der Mitarbeiter wären zu groß.
Aufgrund der Länge der hergestellten Verbundteile (bis zu 17 m) können sich diese Teile verdrehen, wenn sie auf ihren Ständern platziert werden. Das Ausführen von Standardprogrammen würde also dazu führen, dass Fenster und Speicherlöcher an den falschen Stellen bearbeitet werden.
Um diese Herausforderung zu meistern, verwendet Groupe Beneteau Autodesk Fusion 360 mit PowerInspect, um lokale Ausrichtungen für die einzelnen Schnitte zu erstellen. Mithilfe der On Machine Verification (OMV) können sie Datenpunkte auf den Bootskomponenten nehmen und das erforderliche Maschinenkoordinatensystem berechnen, um die Komponenten genau zu bearbeiten. Werkzeugwege werden mit Autodesk Fusion 360 mit PowerMill erstellt und mit einem modifizierten Maschinenkoordinatensystem ausgeführt, das aus PowerInspect erstellt wurde.
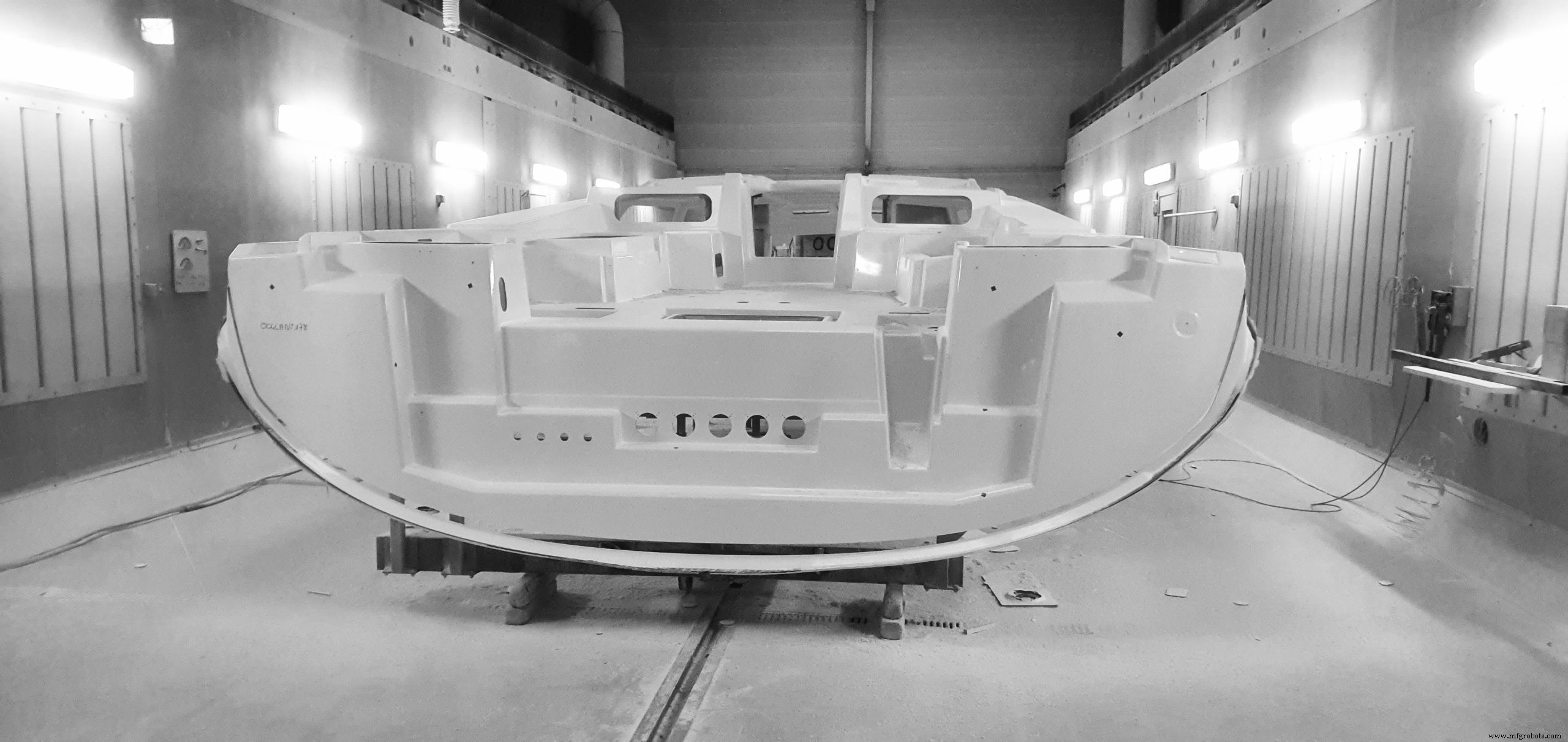
Die Verwendung von PowerInspect zur Berechnung von Transformationen ist viel schneller als der Versuch, eine Ausrichtung mit manuellen Methoden zu bestimmen – es dauert normalerweise nur wenige Minuten, um Punktdaten zu importieren und die Transformation zu berechnen. Viele Kunden, die diese automatisierte Methode verwenden, können gegenüber manuellen Methoden Stunden oder sogar Tage sparen.
Eine weitere Herausforderung für die Groupe Beneteau besteht darin, dass jedes Boot nach individuellen Kundenspezifikationen hergestellt wird. Jede Komponente erfordert je nach Bestelldetails unterschiedliche Zuschnitte. Um die Herausforderung zu bewältigen, nur die erforderlichen Schnitte zu bearbeiten und sicherzustellen, dass die richtigen Ausrichtungen für die richtigen Programme in die Maschine geladen werden, wandte sich Groupe Beneteau an Autodesk, um dieses System zu automatisieren.
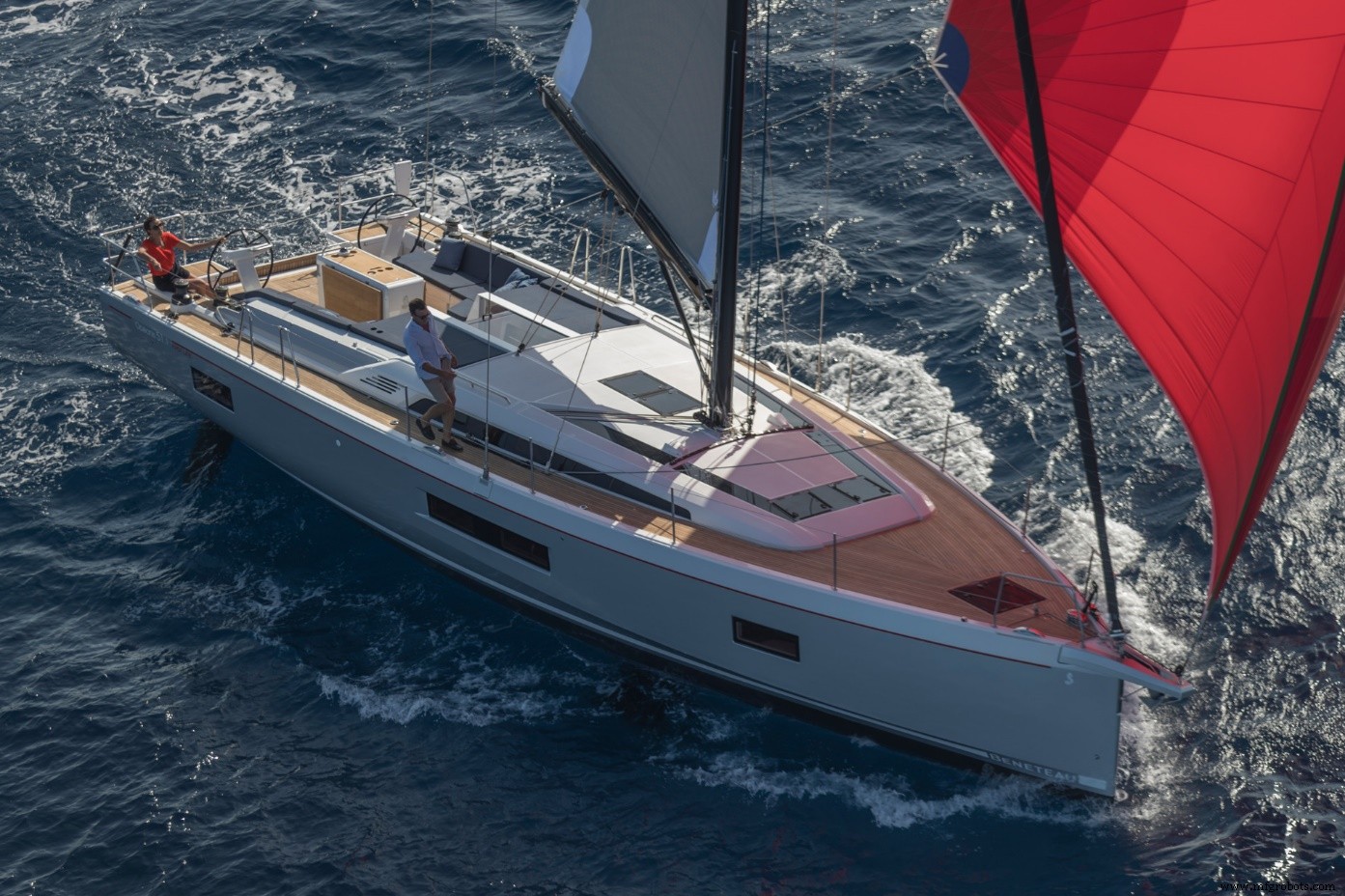
Mit einer Kombination aus PowerInspect und Autodesk Manufacturing Automation Utility (einem Tool, das vom Global Consulting Delivery-Team von Autodesk zur Automatisierung des Werkzeugmaschinenbetriebs verwendet wird) erstellte Autodesk eine vereinfachte Front-End-Anwendung für die Groupe Beneteau. Dieses System ermöglicht es dem Bediener, den Bootstyp und die Seriennummer auszuwählen, bevor das automatisierte System gestartet wird.
Das automatisierte System kommuniziert mit der Werkzeugmaschine, um die richtigen Prüfprogramme für die Komponente auszuführen, um sie zuerst zu lokalisieren und dann zu inspizieren. Die Messergebnisse werden automatisch von der Maschine zurückgelesen, bevor sie PowerInspect durchlaufen, um die Ausrichtungen auszugeben. Alle Ausrichtungen außerhalb der Toleranz werden dem Bediener gemeldet, bevor die Werkzeugwege in die Werkzeugmaschine geladen und automatisch ausgeführt werden.
Die Verschrottung einer großen Rumpfkomponente würde die Groupe Beneteau potenziell Tausende von Euro kosten, daher müssen die Teile korrekt und toleranzgerecht bearbeitet werden. Darüber hinaus ist die manuelle Nachbearbeitung von Teilen zeitaufwändig und wirft Gesundheits- und Sicherheitsprobleme auf, sodass die Teile beim ersten Mal ohne Fehler korrekt bearbeitet werden müssen. Wenn das System nicht vollständig automatisiert wäre, müssten die Bediener schließlich Dateien zwischen den Maschinen hin und her kopieren und Offsets manuell aktualisieren. Dieser Prozess wäre zeitaufwändig und birgt die Gefahr von Fehlern.
Durch die Automatisierung hat die Groupe Beneteau die Anzahl der manuellen Schritte von 15 auf sechs reduziert und so die Möglichkeit von Fehlern vollständig beseitigt. Sie haben nicht nur die Zeit verkürzt, die für die Herstellung eines fertigen Teils benötigt wird, sondern auch die Zeit, in der die Maschinen große Teile unbeaufsichtigt laufen lassen, von drei Stunden auf vier Stunden pro Teil erhöht. Dadurch hat der Maschinenbediener mehr als zwei Stunden pro Tag Zeit, um andere Aufgaben wie Teilehandhabung und Endbearbeitung zu erledigen und sich besser um die Maschinenwartung und Prozessverbesserung zu kümmern.
Arbeiten Sie mit einem fortschrittlichen Fertigungsprozess, der optimiert und automatisiert werden könnte? Entdecken Sie hier die Vorteile der Fertigungsmöglichkeiten in Fusion 360.

Industrietechnik
- Automatisierungslinie mit hoher Flexibilität in der CNC-Bearbeitung
- CNC-Bearbeitung:Definition und Arten von CNC-Maschinen
- Was ist NC-Bearbeitung? - Definition und grundlegende Anleitung
- Aluminiumbearbeitung:So bearbeiten Sie Aluminiumlegierungen effektiv
- G-Codes und M-Codes der CNC-Maschine mit PDF
- Der Wert der manuellen Bearbeitung in der heutigen Fertigung
- Wie sich KI und maschinelles Lernen auf die CNC-Bearbeitung auswirken
- Abstechen mit Y-Achsen-Bearbeitung
- Wie bearbeitet man Schmuck mit CNC-Bearbeitung?
- Die Bedeutung von Kühlmitteln bei der Bearbeitung