Wie der Werkzeugausgleich die Standzeit und Produktivität von Werkzeugen erhöht
Rundlauf des Schneidwerkzeugs und Unwucht des Werkzeughalters machen die Bearbeitung zu einer Herausforderung. Hier ist, was Sie über Werkzeugauswuchttechniken wissen müssen und wie Sie durch die richtige Vorgehensweise Vibrationen minimieren und sowohl die Oberflächenbeschaffenheit als auch die Lebensdauer der Werkzeuge verbessern können.
Das Auswuchten von Werkzeugen ist ein Muss für die Hochgeschwindigkeitsbearbeitung, bei der Spindeldrehzahlen 20.000 U/min oder mehr erreichen. Aber viele Experten werden Ihnen sagen, dass das Auswuchten schon bei 6.000 U/min beginnt und dass das Überspringen dieses kritischen Schritts sowohl die Standzeit als auch die Produktivität verringert.
Brendt Holden, Präsident von Haimer Inc., ist einer dieser Menschen. Er erzählt gerne eine Geschichte von vor 15 Jahren über eine Maschinenwerkstatt in Wisconsin, die mit einem langweiligen Betrieb zu kämpfen hatte. Nach der Installation einer Werkzeugauswuchtmaschine von Haimer konnte die Maschinenwerkstatt den Durchsatz bei diesem Auftrag und vielen anderen erheblich steigern.
„Dieser spezielle Betrieb hatte keine einzige Maschine, die schneller als 6.000 U/min war“, erinnert sich Holden. „Es war ein wunderbares Zeugnis für die Bedeutung des Werkzeugausgleichs, unabhängig von der Spindeldrehzahl.“
Sie waren nicht allein. Ein großer US-Motorenhersteller sparte nach der Implementierung einer Werkzeugauswuchtlösung jährlich 250.000 US-Dollar an ungeplanten Ausfallzeiten ein. K&G Manufacturing in Minneapolis stellte fest, dass offline voreingestellte Werkzeughalterbaugruppen beim ersten Auswuchten auf Maß geschnitten werden. Auch die Schleifindustrie kennt den Wert des Auswuchtens, wie der Schneidwerkzeughersteller OSG bestätigen kann:Nach dem Auswuchten von Scheibenpaketen konnte das Unternehmen eine um 20 Prozent gesteigerte Leistung, eine um 30 Prozent längere Spindellebensdauer und einen um 18 Prozent geringeren Stromverbrauch feststellen.
Wenn diese Anekdoten die Skeptiker da draußen nicht überzeugen können, hier ist ein wissenschaftlicheres Beispiel – eines, das hilft, die Effektivität des Tool-Balancing zu erklären.
Haimer-Ingenieure montierten Schaftfräser in zwei Werkzeughaltern, einer ausgewuchtet, der andere nicht. Beide wurden auf einem der Werkzeugvoreinstellgeräte des Unternehmens überprüft und hatten weniger als 2 Mikron Unrundheit. Dann drehten sie jede Werkzeughalterbaugruppe mit 18.000 U/min, während sie sie mit einem Beschleunigungsmesser analysierten. Die Ergebnisse? Wo die ausgewuchtete Baugruppe den gleichen Unrundheitswert von nahezu Null beibehielt, stieg die unausgeglichene auf 11 Mikrometer (0,0004 Zoll) – eine fünffache Steigerung.
Wenn der die Lebensdauer des Werkzeugs zerstörende Rundlauf nicht ausreicht, um Sie zu überzeugen, versuchen Sie Folgendes:Fragen Sie einen Instandsetzer für Werkzeugmaschinenspindeln nach der Hauptursache für einen vorzeitigen Ausfall. Die meisten werden vermuten, dass es sich entweder um a) Abstürze oder b) Unwucht des Werkzeughalters handelt. Bei vielen Bearbeitungszentren – insbesondere solchen mit Hochgeschwindigkeitsspindeln – kann ein Austausch leicht mehr kosten als eine Werkzeugwuchteinheit, und das ohne Berücksichtigung von Maschinenstillständen und den daraus resultierenden Produktionsverzögerungen.
Du denkst vielleicht:„Ich verstehe. Deshalb kaufen wir ausgewuchtete Meißelhalter.“ Und während Holden und andere Ihnen sagen werden, dass dies ein guter Anfang ist, ist es das Äquivalent zum Kauf hochwertiger Reifen für Ihr Auto – sie müssen immer noch ausgewuchtet werden, und wie bei Schneidwerkzeugen und Werkzeughaltern muss dies als vollständige Baugruppe erfolgen .
Ausrichten von Werkzeughaltern
Ironischerweise ist der Prozess gar nicht so unterschiedlich. So wie ein Automechaniker kleine Gewichte an einer Seite des Rads anbringt, um Unwucht auszugleichen, kann auch ein Werkzeugkistenbegleiter schwere Metallschrauben oder seltsam geformte Ringe an den Werkzeughalter anbringen und jedes sorgfältig justieren, bis die Unwucht beseitigt ist storniert worden. Es ist auch möglich, den Werkzeughalter selbst zu bohren oder zu fräsen, wobei kleine Metallmengen entfernt werden, bis das Gleichgewicht erreicht ist, obwohl dies offensichtlich ein kostspieligerer (und dauerhafterer) Ansatz ist.
Reifen und Werkzeughalter leiden ebenfalls unter den gleichen Arten von Unwucht, nämlich statisch und dynamisch. Entfernen Sie eine Radmutter vom Rad Ihres F-150 und Sie erzeugen eine statische Unwucht, die einfach als zu viel Gewicht auf einer Seite angesehen werden kann. Wenn Sie mit dem Propeller Ihres Fischerboots auf einen Felsen schlagen, stehen Sie wahrscheinlich vor einem dynamischen Ungleichgewicht oder einem Ungleichgewicht in zwei Rotationsebenen. Dieser letzte Zustand tritt am häufigsten bei CNC-Bearbeitungszentren auf, insbesondere bei längeren Werkzeugen und Werkzeughaltern.
Ironischerweise sind Werkzeughalter im CAT-Stil – ein Favorit der Werkzeugmaschinenhersteller hier in den USA – aufgrund der asymmetrischen Schlitze des Flansches von Natur aus unausgeglichen. Dies gilt auch für Werkzeughalter im Weldon-Stil mit ihrer Feststellschraube auf einer Seite. Sogar HSK-Werkzeuge, insbesondere die gebräuchlichere A-Form, leiden unter einem gewissen Maß an Unwucht, obwohl es bei weitem nicht das von Steilkegel-Werkzeughaltern ist. Werkzeughersteller versuchen, diese unglücklichen Bedingungen auszugleichen, aber befestigen Sie einen Halteknopf an einem Ende des Werkzeughalters, einen Bohrer oder Schaftfräser am anderen, und alle Wetten sind aus. Daher der Rat, Werkzeughalter immer als komplette Baugruppe auszuwuchten.
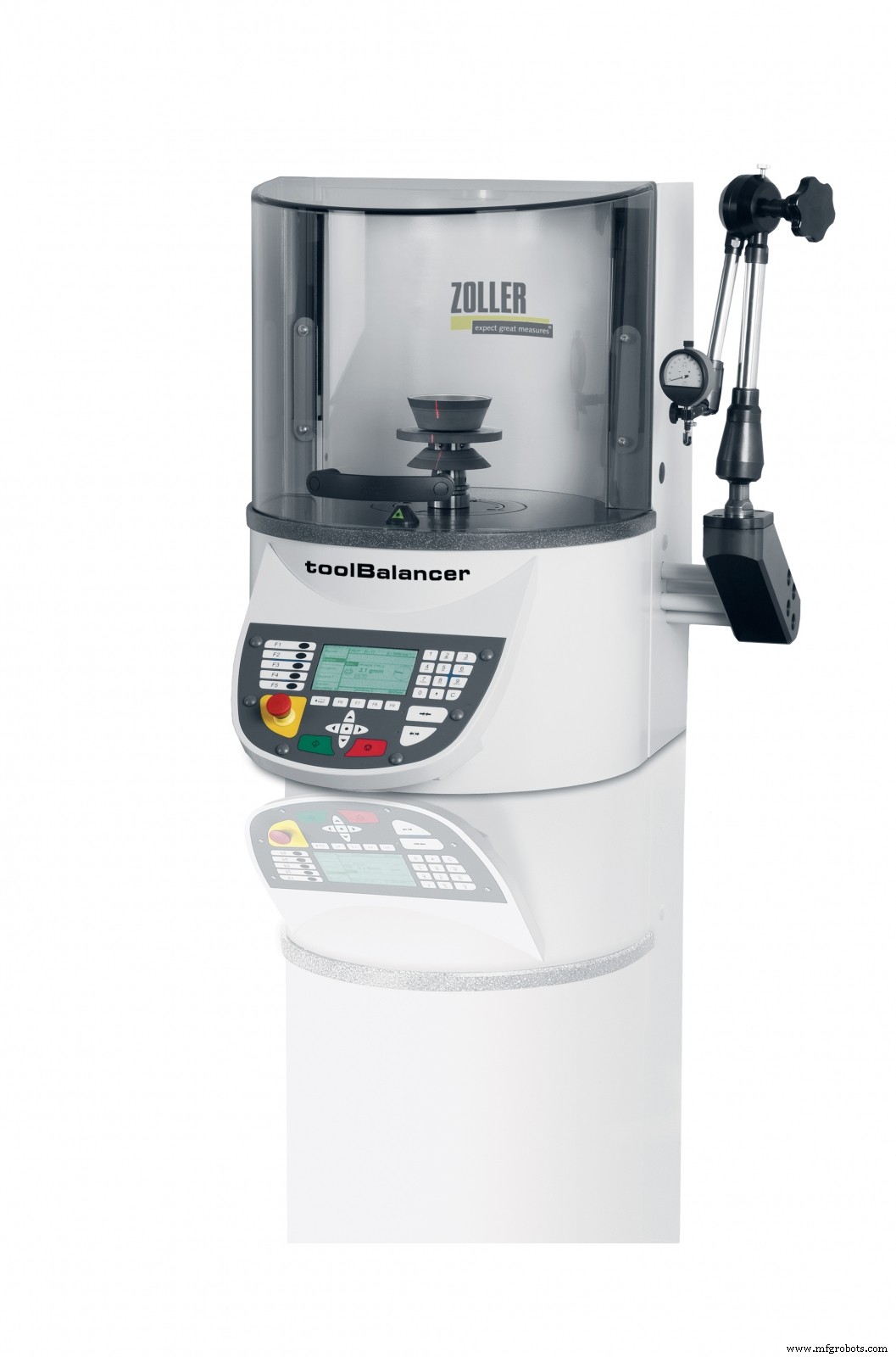
Die Beweise von Tool Balancing im Pudding
Dieses Ungleichgewicht ist quantifizierbar. Er wird als G-Wert bezeichnet, und die meisten Branchenexperten schlagen vor, dass Werkzeuge auf 2,5 G oder besser ausbalanciert sein sollten (was einen Wert unter 2,5 bedeutet). Für Mathematiker bietet die Haimer-Website hier verblüffende Formeln zur Wissenschaft des Werkzeugauswuchtens sowie zusätzliche Gründe, warum es für jeden wichtig ist, der daran interessiert ist, seine Fräs-, Bohr- und Bohroperationen zu verbessern.
Was also tun? Die Antwort sollte inzwischen klar sein:Investieren Sie in eine Werkzeugauswuchtmaschine, so wie es ein anderer Kunde von Brendt Holden vor einigen Jahren tat, als er sein erstes Bearbeitungszentrum mit 20.000 U/min kaufte. Die Ergebnisse waren so gut, dass er anfing, alles in der Werkstatt auszuwuchten, sogar für seine älteren Maschinen, die auf 8.000 U/min begrenzt waren.
„Die verbesserte Standzeit und Oberflächengüte waren eine Nebenbemerkung“, sagt Holden. „Was ihm am meisten auffiel, waren die verbesserten Zerspanungsraten. Wo er zuvor ein Teil mit 3.000 U/min geschnitten hätte, stellte er fest, dass er diese normalerweise durch Auswuchten mit einer entsprechenden Erhöhung der Vorschubgeschwindigkeit verdoppeln konnte. Er war begeistert."
Über die Werkzeugbalance hinausgehen
Matt Brothers, Industry 4.0 Tech Center Manager bei Zoller Inc., kann ähnliche Erfolgsgeschichten von Kunden erzählen, die eine der Werkzeugauswuchtlösungen des Unternehmens implementiert haben. Er weist jedoch schnell darauf hin, dass eine Auswuchtmaschine nur ein Teil einer viel größeren Werkzeuglagerstrategie ist. Ebenso wichtig ist die Notwendigkeit, Werkzeuge offline voreinzustellen, wodurch das Risiko von Bedienerfehlern beim Ansetzen an der Werkzeugmaschine ausgeschlossen und die Maschinenverfügbarkeit erheblich erhöht wird.
Aufgrund der fortschrittlichen optischen Abbildungsfähigkeiten der meisten Voreinstellgeräte ermöglichen sie es auch dem Werkzeuglagerpersonal, Werkzeuge vor dem Einsatz gründlich zu inspizieren und den zuvor erwähnten äußerst wichtigen Rundlauf zu messen. Und für Betriebe, die Schrumpfwerkzeuge verwenden, bieten Zoller (und Haimer) Kombimaschinen an, die beides in einem Arbeitsgang erledigen können.
Brothers schlägt vor, dass Offline-Werkzeugvoreinstellgeräte, wenn sie mit einer Werkzeugverwaltungslösung (TMS) implementiert werden, einen Überblick über die Werkzeugnutzung von der Wiege bis zur Bahre bieten und gleichzeitig den gesamten Programmier- und Einrichtungsprozessablauf verbessern.
„Das TMS von Zoller kann direkt mit der Werkzeugmaschine kommunizieren“, sagt er. „Es kann mit dem CAM-System der Werkstatt, ihrer Simulationssoftware oder ihrem Werkzeuglebensdauer-Überwachungssystem verbunden werden. Das Speichern von Informationen zu Schneidwerkzeugen und Werkzeughaltern in einer einzigen Datenbank bietet viele Vorteile, darunter eine verbesserte Datengenauigkeit, reduzierte Werkzeugbestände, weniger Ausfallzeiten und effizientere Prozessabläufe. Aus diesem Grund sind wir der Meinung, dass TMS ein integraler Bestandteil jedes auf Industrie 4.0 ausgerichteten Geschäfts sein sollte.“
Für Geschäfte, die an einer dieser produktivitätssteigernden Technologien interessiert sind, ist es jetzt an der Zeit, nachzuforschen. Der Geräteabzug gemäß Abschnitt 179 endet im Dezember. Wenden Sie sich an MSC – oder an eines der in diesem Artikel aufgeführten Unternehmen –, um mehr zu erfahren.
Nutzen Sie die Vorteile des Werkzeugausgleichs?
Werkzeugauswuchten wird oft nur für die Hochgeschwindigkeitsbearbeitung als notwendig angesehen, aber viele Betriebe können davon profitieren.
Experten werden Ihnen sagen, dass das Auswuchten bereits bei 6.000 U/min beginnt und dass das Überspringen dieses kritischen Schritts sowohl die Standzeit als auch die Produktivität verringert.
Nehmen Sie unten an unserer Umfrage teil, um Ihre Meinung zum Tool-Balancing mitzuteilen und zu sehen, was andere denken.
Balancen Sie Ihre Werkzeuge schon?
Welche Vorteile haben Sie beim Werkzeugausgleich gesehen? Welchen Herausforderungen sind Sie begegnet? Teilen Sie Ihre Gedanken in den Kommentaren unten mit.
Industrietechnik
- Was ist 6G und wie schnell wird es sein?
- So stellen Sie Genauigkeit und Präzision beim CNC-Fräsen sicher
- So maximieren Sie die Lebensdauer von Maschinen und Komponenten in der Fertigung
- Was ist Kupferlöten und wie wird es gemacht?
- Wie die Schaftfräser TuffCut XT von M.A. Ford Ihnen helfen, die Produktivität zu steigern
- 5 Wege zur Verlängerung der Werkzeuglebensdauer und Steigerung der Produktivität
- Was ist Standzeit? Werkzeugoptimierung mit Maschinendaten
- Wie man Ausfallzeiten reduziert und die Produktivität steigert
- Wie man die Produktivität und Fertigungsqualität in industriellen Umgebungen verbessert
- Was ist ein J-Hook in Punch und wie kann er verhindert werden?