Verwalten der Spankontrolle und Verbessern der Standzeit und Produktivität
Ein schlechtes Spanmanagement kann zu Problemen für Maschinisten führen, wie z. B. kürzere Werkzeuglebensdauer, schlechte Oberflächenbeschaffenheit und Sicherheitsrisiken. Diese Probleme kosten Unternehmen unzählige Stunden Produktionszeit und entgangene Einnahmen. Hier ist, was Sie dagegen tun können.
Das Packen von Spänen während des Gewindeschneidens führt zu minderwertigen Gewinden, verkürzter Werkzeuglebensdauer und sehr wahrscheinlich zu einem katastrophalen Ausfall. Unter der Annahme, dass ein Teil überhaupt geborgen werden kann, führt das letzte dieser Ereignisse zu zusätzlichen Kosten und Zeitverlust, während Senkerodieren oder mechanische Methoden zum Entfernen des gebrochenen Gewindebohrers verwendet werden.
Das mit diesem Szenario verbundene Risiko hilft, die Popularität des Gewindefräsens zu erklären, das Maschinenbedienern nicht nur eine weitaus bessere Kontrolle über den Gewindeschneidprozess gibt, sondern auch Probleme mit dem Spänemanagement weitgehend eliminiert.
„Gewindefräsen bietet die ultimative Spankontrolle bei der Bearbeitung von Innengewinden“, sagt Mark Hatch, Produktdirektor bei Emuge Corp.
„Während das Gewindebohren ein kontinuierlicher Bearbeitungsprozess ist und daher kontinuierliche Gewinde in duktilen Materialien erzeugt, ist das Gewindefräsen ein unterbrochener Prozess und zerbricht selbst das härteste Material in kleine, handhabbare Späne“, sagt er. „Aus diesem Grund bevorzugen die Luft- und Raumfahrtindustrie und tatsächlich alle Betriebe, die hochwertige Teile herstellen, das Fräsen gegenüber dem Gewindeschneiden, da es sowohl Präzision als auch Vorhersagbarkeit bietet.“
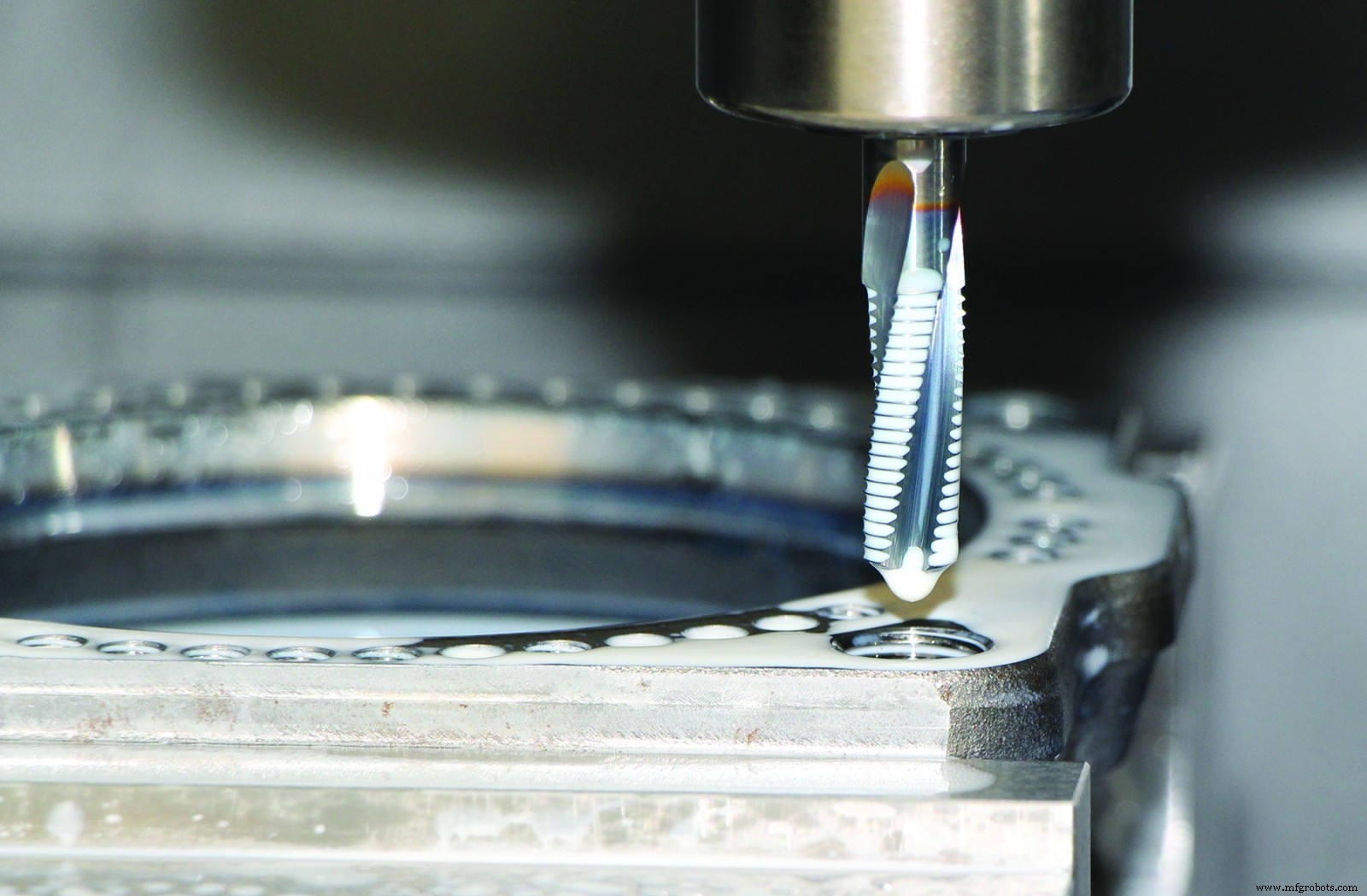
Gewindefräsen und mehr
Hatch stellt fest, dass dieser wichtige Fadenherstellungsprozess in den letzten Jahren einfacher geworden ist. Praktisch alle CNC-Werkzeugmaschinen sind heute mit der zum Fräsen von Gewinden erforderlichen helikalen Interpolationsfunktion ausgestattet, und die meisten bieten auch Kühlmittel durch die Spindel – vorzugsweise mit hohem Druck –, um Späne effektiv aus der Bohrung zu spülen. Das, und CAM-Systeme sind im Allgemeinen gewindefräsfreundlicher als früher, wodurch Bedenken hinsichtlich der manuellen Programmierung der Bogen-Ein- und Bogen-Aus-Bewegungen beim Fräsen von Gewindelöchern beseitigt werden.
Auch die Schneidwerkzeuge sind effektiver geworden. Die Gewindefräser der ZGF-Serie von Emuge sind beispielsweise in 3xD-Längen erhältlich, was ihre Reichweite erweitert. Das Unternehmen bietet auch mehrere zusätzliche Gewindefräserlinien an, darunter eine Wendeschneidplattenserie, die alles von UNC und UNF bis hin zu Rohr-, STI-, Miniatur- und „Gigant“-Gewinden abdeckt. Dank der großen Auswahl an hochwertigen Werkzeugen, die heute von Emuge und seinen Mitbewerbern auf dem Markt sind, gibt es kaum etwas, das nicht gewindegefräst werden kann, sodass Probleme mit der Spankontrolle der Vergangenheit angehören.
Meinungsbildung
Trotz seiner vielen attraktiven Qualitäten ist das Gewindefräsen jedoch kein Allheilmittel. Seine Alternative – das Gewindebohren – ist sowohl schneller als auch einfacher, weshalb es die erste Wahl für Anwendungen mit höheren Stückzahlen, auf manuellen Maschinen oder dort ist, wo die Werkstatt aus welchen Gründen auch immer auf das Gewindefräsen verzichten möchte. Hatch wird Ihnen sagen, dass die nächstbeste Alternative – sicherlich aus Sicht der Spankontrolle – das Kaltumformen oder Gewindeschneiden ist, bei dem Material verdrängt, anstatt es zu entfernen.
„Die Automobilindustrie nutzt die Kaltumformung ausgiebig für das Tieflochgewindeschneiden von Zylinderköpfen und Getriebekomponenten, da sie starke, qualitativ hochwertige Gewinde herstellen und Probleme im Zusammenhang mit Spänen beseitigen kann“, sagt er. „Die einzige Einschränkung ist die Tatsache, dass beim Formen eine sehr kleine, fast U-förmige Vertiefung am Gewindescheitel zurückbleibt. Bei bestimmten medizinischen Komponenten und Lebensmittelverarbeitungsgeräten schafft diese Unvollkommenheit einen Bereich, in dem sich Bakterien ansammeln können, daher sind rollgeformte Gewinde in diesen Anwendungen oft nicht zulässig.“
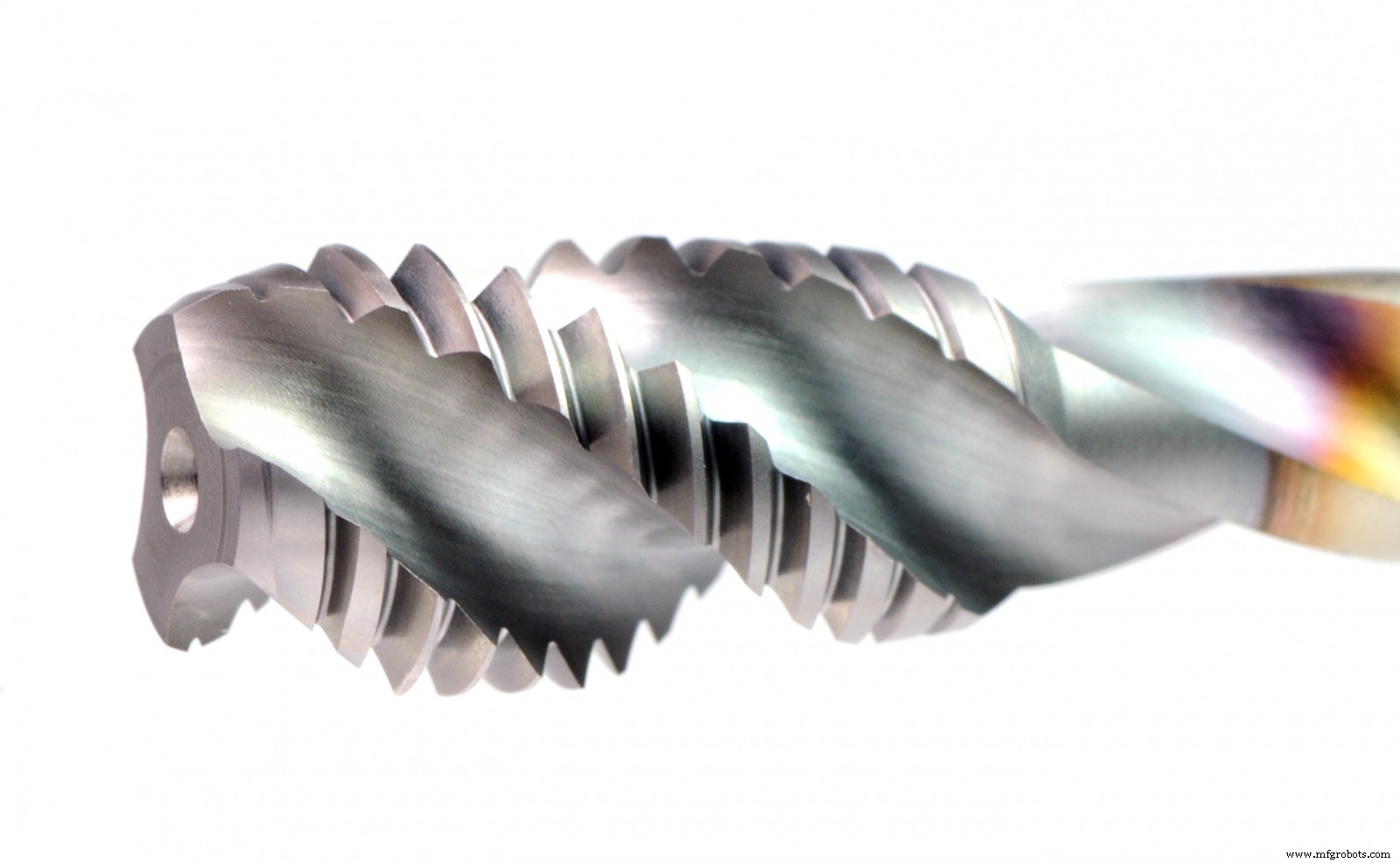
Tolle Taps
Sind Gewindefräsen und rollgeformte Gewinde out, bleiben geschnittene Gewindebohrer übrig. Glücklicherweise haben Emuge und andere Hersteller von Schneidwerkzeugen ein breites Angebot an universellen und materialspezifischen Gewindebohrern entwickelt, die selbst in Sacklöchern hervorragende Arbeit leisten, um Späne nach oben und aus dem Werkstück zu ziehen. Kyle Matsumoto, Produktmanager bei OSG USA Inc., schlägt vor, dass der A-Tap genau dafür entwickelt wurde.
Der A-Tap, erklärt er, verwendet eine variable Führungsnut für eine stabile Spanbildung und zur Beschleunigung der Evakuierung. Das Ergebnis ist ein vorhersagbarer, spiralförmiger Chip, ganz anders als das verdrehte Vogelnest, das so oft beim Klopfen stört. Das Werkzeug soll auch eine außergewöhnlich scharfe Schneide haben, was die Spanform weiter stabilisiert und dazu beiträgt, Festfressen zu vermeiden. Beide dienen dazu, eine glatte Gewindeoberfläche zu schaffen, die weniger wahrscheinlich an vorbeilaufenden Spänen hängen bleibt, und verbessern gleichzeitig die Teilequalität.
„Durch die Verwendung einer variablen Wendelgeometrie können wir einen spitzeren Winkel direkt an der Fase des Gewindebohrers erzeugen, wo das gesamte Schneiden stattfindet“, sagt Matsumoto.
„Dies macht nicht nur den Schneidvorgang glatter, sondern trägt auch dazu bei, die Späne schön und kompakt zu halten“, fügt er hinzu. „Und dann nimmt der Spiralwinkel gegen Ende der Nut ab, wodurch der Chip schneller austritt. Der A-Tap ist für Stähle und rostfreie Stähle ausgelegt, funktioniert aber auch recht gut in Gusseisen und noch härteren Materialien bis etwa 35 Rockwell.“
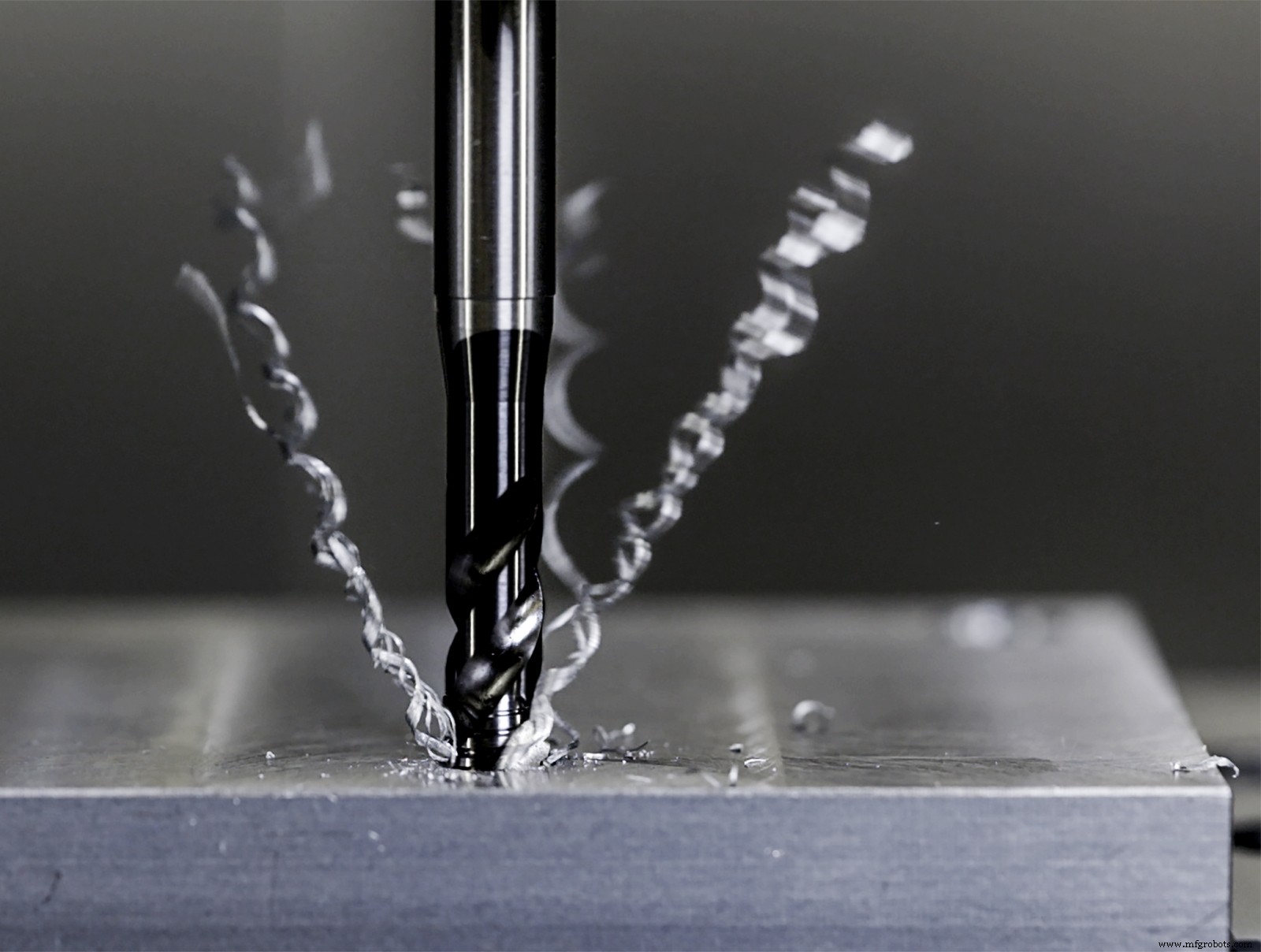
Fröhliche Chips machen!
Eine ähnliche Lösung hat Paul Motzel, Produktmanager für Gewindewerkzeuge bei Gühring Inc.. Er sagt, dass die Pionex-Reihe von Wasserhähnen des Unternehmens in Schnitt- und Rollenform erhältlich ist. Je nach Werkzeug werden diese typischerweise mit den Sirius- oder Slidur-Beschichtungen des Unternehmens behandelt, um die Reibung zu verringern und die Spanabfuhr zu unterstützen. Pionex-Gewindebohrer werden nach dem Schleifen auch geschliffen und poliert und nach dem Beschichten erneut poliert, um eine glatte, starke Schneidkante zu erzielen und die Lebensdauer des Werkzeugs zu verlängern. Er erwähnt auch, dass die Formversion des Pionex-Gewindebohrers weniger Oberflächenkontakt und eine Schmierrille hat, die die Gewindeschneidkräfte um 30 Prozent reduziert.
„Vor vielen Jahren sagte mir einer meiner Kollegen in Deutschland, dass ein guter Chip ein glücklicher Chip ist“, sagt Motzel. „Das heißt, es gibt einen Ort, an den man gehen kann, und einen Weg, um dorthin zu gelangen. Wenn Sie darüber nachdenken, dass vielleicht 90 Prozent der Tapping-Probleme mit Chips zusammenhängen, werden Sie verstehen, dass er mit seinen Kommentaren genau richtig lag.“
Abgesehen von fortschrittlichen Beschichtungen und Werkzeuggeometrien schlägt Motzel vor, dass einer der häufigsten Fehler, den Werkstätten machen, darin besteht, den falschen Gewindebohrertyp auszuwählen.
„Gewindebohrer mit Spiralspitze drücken den Span nach vorne und sollten daher niemals in einem Sackloch verwendet werden, selbst wenn unten viel Platz ist“, sagt er. „Sie sind so konzipiert, dass sie das Werkstück vollständig durchdringen, und wenn sie dies nicht tun, können herumhängende Späne hinter der Freifläche eingeklemmt werden und möglicherweise den Gewindebohrer sprengen.“
„Die Lösung besteht darin, bei Sacklöchern immer Gewindebohrer mit Spiralnut zu verwenden, da ihr größerer Spiralwinkel dazu beiträgt, Späne aus dem Werkstück auszuwerfen und die Spiralspitzen für Durchgangslöcher aufzusparen“, fügt er hinzu.
Welche Tipps, Tricks und Techniken zum Chip-Management können Sie teilen? Teilen Sie Ihre Gedanken in den Kommentaren unten mit.
Sie sind sich nicht sicher, ob wasserbasierte Kühlmittel für Ihre Werkstatt geeignet sind? Sehen Sie sich dieses Video an, um eine Einführung zu flüssigen Kühlmitteln zu erhalten:
Industrietechnik
- Wie die Schaftfräser TuffCut XT von M.A. Ford Ihnen helfen, die Produktivität zu steigern
- 8 wichtige Tipps zur Verbesserung der Spankontrolle beim Bohren
- 5 Wege zur Verlängerung der Werkzeuglebensdauer und Steigerung der Produktivität
- So maximieren Sie die Maschinenproduktivität:Chip Thinning
- So maximieren Sie den Durchsatz und die Teilequalität beim Gewindeschneiden
- OEE-Software:Verstehen Sie, wie Sie die Produktivität verfolgen und verbessern können
- Wie man die Maschinenverfügbarkeit berechnet und verbessert
- So entschärfen und verwalten Sie Ihre Fabrik nach einem Unfall
- Wie man Ausfallzeiten reduziert und die Produktivität steigert
- Wie man die Produktivität und Fertigungsqualität in industriellen Umgebungen verbessert