Wichtige Merkmale des Walzens von Walzdraht
Wichtige Merkmale des Walzens von Walzdraht
Walzdraht wird normalerweise in einem Hochgeschwindigkeitswalzwerk gewalzt, wo die Stahltemperatur über 1.000 °C liegt, die maximale Walzgeschwindigkeit 120 Meter pro Sekunde (m/s) übersteigt und die hergestellten Walzdrahtspulen bis zu 10 Kilometer (km) lang sein können . Beim Walzen von Walzdraht werden üblicherweise 25 bis 30 Stiche in einem kontinuierlichen Walzwerk durchgeführt.
Walzdraht ist ein Werkstoff, der eine sehr breite Anwendung hat. Von Komponenten für die Automobilindustrie, Reifencord, Elektroden, Verbindungselementen wie Schrauben und Muttern, Federn, Draht und Drahtprodukten, Stahlarmierungen usw. basiert alles auf Walzdraht. Aus diesem Grund ist ein Drahtwalzwerk normalerweise auf Vielseitigkeit ausgelegt. Da es sich bei der Mühle um eine energieintensive Mühle handelt, ist es erforderlich, dass die optimalen Lösungen in das Mühlendesign integriert werden, ohne Kompromisse bei der Flexibilität einzugehen. Alle Abmessungsbereiche, Werkstoffe und Legierungen müssen in der Drahtstraße effizient und mit hoher Produktivität produziert werden.
Walzdrähte müssen die Anforderungen der Walzdrahtanwender an die Oberflächen- und Innenqualität sowie an die physikalischen, chemischen, mechanischen und metallurgischen Eigenschaften erfüllen. Walzdrähte werden einer Nachbearbeitung wie Ziehen, Schmieden oder maschineller Bearbeitung in gewünschte Formen und einer Wärmebehandlung unterzogen, damit das Produkt die gewünschte Festigkeit erreichen kann. Daher müssen die Walzdrähte in der Lage sein, eine gute Leistung der hergestellten Teile zu gewährleisten, wo immer sie verwendet werden, und gleichzeitig eine gute Bearbeitbarkeit in verschiedenen Stadien der Nachbearbeitung aufweisen.
Der Benutzer von Walzdraht hat drei grundlegende Anforderungen, nämlich (i) eine oder mehrere der sekundären oder tertiären Bearbeitungen zu eliminieren oder zu vereinfachen, um die Produktivität zu verbessern und die Bearbeitungskosten zu senken, (ii) die Funktionalität zu verbessern, d. h. die Lebensdauer zu verlängern das Gewicht zu reduzieren oder dem Endprodukt, für das der Walzdraht verwendet wird, andere Vorteile zu verleihen, und (iii) die Verwendung umweltschädlicher Substanzen während der Nachbearbeitungsprozesse zu eliminieren.
Um den immer strengeren Anforderungen des Verbrauchers gerecht zu werden, muss das Drahtwalzwerk über die Gesamtfähigkeiten des Walzdrahts unter den verschiedenen Gesichtspunkten verfügen, nämlich (i) Verbesserung der Maßhaltigkeit, (ii) Umsetzung des größenfreien Walzens (d. h. Walzen Produkte unterschiedlicher Größe ohne Rollenwechsel), (iii) Verbesserung der Produktivität durch Beschleunigung der Rollenwechselarbeit (Verkürzung der Rollenwechselzeit) und (iv) Verbesserung der Produktoberflächenqualität durch Verhinderung des Auftretens von Oberflächendefekten während des Transports den Walzprozess.
Das Drahtwalzwerk soll nicht nur das Material liefern, sondern auch Walzdraht für die lange Weiterverarbeitung, die er in den Sekundär- und Tertiärprozessen bis zum endgültigen Endprodukt durchläuft. Da die Endprodukte in vielen Fällen als wichtige Teile in verschiedenen Industriebereichen verwendet werden, besteht außerdem Bedarf an Prozessrationalisierungen in integrierten Kooperationen mit Kunden. Die Mühle soll also in der Lage sein, nicht nur die Qualitätsanforderungen der Anwender zu erfüllen, sondern auch deren Anforderungen an Produktivität, Ausbeute, Flexibilität und Produktionskosten bei der Weiterverarbeitung zu erfüllen. Eine hohe Mühlenausbeute zusammen mit der angemessenen Produktqualität ist von größter Bedeutung für die Kontrolle der Produktionskosten.
Die Produktionskapazität eines Drahtwalzwerks hängt entweder von der Massenproduktion einiger weniger Standardprodukte oder von einem diversifizierten Produktmix ab, der aus Walzdraht mit einer großen Anzahl von Stahlsorten und spezialisierten Produktqualitäten besteht.
Ein Drahtwalzwerk benötigt grundsätzlich (i) Heizeinrichtungen zum Erwärmen des Ausgangsmaterials (Knüppel) auf Walztemperaturen, (ii) Walzeinrichtungen bestehend aus Walzgerüsten mit Walzen, Einbaustücken, Führungen und Schutzvorrichtungen, (iii) Verlegung, Wärmebehandlung und Wickelausrüstung und (iv) Förder- und Handhabungsausrüstung. Alle Anlagen müssen in enger Abstimmung mit einer Kontrolle der Walztemperaturen, Lückenzeitverluste, Geschwindigkeitsverluste, Kopfsteinpflaster, fehlerhafter Produkte und Qualitätsabweichungen arbeiten, die zu Umleitung oder sogar Ablehnung führen.
Anforderungen an ein modernes Drahtwalzwerk
Beim Walzen von Walzdraht in einer Drahtstraße gibt es mehrere wichtige Parameter (Bild 1). Ein modernes Drahtwalzwerk ist im Allgemeinen so konzipiert, dass es mit der Philosophie der „Gesamtanlageneffektivität“ (OEE) arbeitet. Der OEE-Wert der Mühle ist der Wert, der sich aus der Multiplikation der Mühlenauslastung, der Mühleneffizienz und der Mühlenausbeutezeit ergibt. Die Mühlenauslastung ist die verfügbare Betriebszeit dividiert durch die geplante Produktionszeit und wird in Prozent ausgedrückt. Der Mühlenwirkungsgrad ist die Laufzeit dividiert durch die verfügbare Betriebszeit der Mühle und wird in Prozent ausgedrückt. Die Mühlenausbeutezeit ist die Zeit zur Herstellung des Hauptprodukts bezogen auf die Laufzeit. Die Produktausbeute wird als das Gewicht des akzeptierten Coils geteilt durch das Gewicht der Knüppel ausgedrückt und in Prozent ausgedrückt.
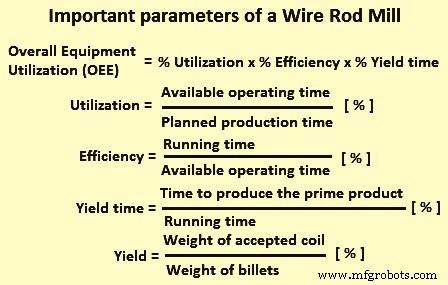
Bild 1 Wichtige Parameter einer Drahtstraße
Drahtwalzwerke haben normalerweise eine niedrigere OEE als andere Arten von Walzwerken aufgrund der höheren Stillstandszeit für Walzenwechsel und Gerüstwechsel sowie Rillen- und Führungseinstellungen während des Verschiebens der Produkte. Die OEE des Werks kann verbessert werden, wenn diese Ausfallzeit reduziert werden kann.
Die theoretische Produktionskapazität einer Mühle ist die Kapazität, die ohne Verluste erreicht werden kann, d. h. bei 100 % Auslastung, 100 % Wirkungsgrad und 100 % Ausbeute. Die tatsächliche Kapazität hängt jedoch vom OEE-Niveau der Mühle ab. Wenn das OEE-Niveau des Werks 60 % beträgt, beträgt die Produktionskapazität des Werks 60 % der theoretischen Kapazität. Das OEE-Niveau in einem hochmodernen Drahtwalzwerk mit einem gut definierten optimierten Walzwerk liegt normalerweise bei 80 %.
Die Kosten für schlechte Qualität im Drahtwalzwerk werden im Allgemeinen als die Summe der Inspektionskosten und der Zurückweisung/Umleitung von Walzdrähten aufgrund von inneren und äußeren Fehlern bestimmt. Bei einer Hochleistungsmühle können es rund 10 % sein. Sie kann in einem Drahtwalzwerk mit einem diversifizierten Produktmix, bestehend aus Walzdraht mit einer großen Anzahl von Güten und spezialisierten Produktqualitäten, um bis zu 30 % gesteigert werden.
In einem modernen Drahtwalzwerk stehen Produktivität und Qualität im Vordergrund. Hohe Auslastung, Effizienz und Ausbeute sorgen für hohe Produktivität. Aber nicht nur die hohe Produktivität allein entscheidet über den Erfolg einer Drahtstraße. Es muss Produkte herstellen, die den Kunden einen Mehrwert bieten, und sie erhalten Qualitätswalzdraht, der die Zahlungen wert ist, die sie für den Walzdraht leisten.
Die Produktivität und Auslastung der Mühle hängt von der Stillstandszeit in der Mühle ab, die aus mehreren Gründen verursacht wird, einschließlich der Mühlenanordnung und dem Produktmix. Im Werk wird die Ausbeute vom Knüppel bis zum Endprodukt in allen Schritten registriert und die Nachverfolgung des Materials im Werk verfolgt die im Werk stattfindenden Verluste. Die Hauptkategorien der Verluste, die in der Mühle auftreten, sind (i) Lückenzeitverluste, (ii) Geschwindigkeitsverluste, (iii) Verluste aufgrund von Kopfsteinpflaster, (iv) Verluste aufgrund von Qualitätsabweichungen, (v) Verluste aufgrund von Mühlen Stillstandszeiten, (vi) Verluste aufgrund von Umleitung/Zurückweisung von Walzdraht während der Inspektion in der Endbearbeitungsseite des Walzwerks und Zeitverluste aufgrund von wertsteigernden Vorgängen im Fall der Produktion von spezialisierten Walzdrahtprodukten.
Mühlenflexibilität
In einem Drahtwalzwerk wird Stahl (Knüppel) über seine Rekristallisationstemperatur erhitzt und durch mehrere Rillen der Walzen im Walzwerk geführt. In Drahtwalzwerken verwendete übliche Walzstichkonstruktionen sind Diamant-Quadrat, Diamant-Diamant, Kastenstiche, Quadrat-Oval, Falsch-Rund-Oval und Rund-Oval. In den Drahtwalzwerken wird normalerweise größenfreies Walzen durchgeführt, was bedeutet, dass Walzdrähte jeder Größe gewalzt werden können, ohne die Beschränkungen der Stichgrößen der im Walzwerk gehaltenen Walzen. Dies wird auch als Flexibilität der Serie bezeichnet. Darüber hinaus ermöglicht die Vereinfachung des Stichplans eines vorgeschalteten Walzwerks, dass die Häufigkeit des Walzenwechsels wesentlich gesenkt werden kann. Je breiter der Bereich der Produktgröße ist, die mit den gleichen Walzen gewalzt werden kann (größenfreier Bereich), desto größer ist der Effekt der verringerten Häufigkeit des Walzenwechsels. Das größenfreie Walzen ist nicht auf das Fertigwalzwerk beschränkt. Es kann auch auf Vorfertigwalzwerke angewendet werden.
Zur Verbesserung der Produktivität liegt der Fokus auf der Minimierung der Ausfallzeit der Drahtstraße. Die Wirksamkeit einer solchen Fokussierung wird gewöhnlich dadurch verbessert, dass die Zeit und der Bedarf für das Auswechseln von Walzen reduziert werden, wenn neue Endabmessungen und neue Stahlgüten und -formen hergestellt werden sollen. Erreicht wird dies durch die Verbesserung des Arbeitsbereichs, auch Flexibilität der Baureihe genannt. Eine verbesserte Flexibilität wird erreicht, wenn eine große Menge unterschiedlicher Stahlsorten mit unterschiedlichen Formen und Abmessungen mit einer minimalen Änderung des Walzplans gewalzt wird. Jede Stahlsorte zeichnet sich durch ihre spezifische Art des Materialflusses, wie z. B. unterschiedliche Spreizung, beim Passieren des Walzspalts aus. Auch die Anlaufzeit und die Wartezeit auf die richtige Walztemperatur müssen je nach Stahlsorte verringert werden. Unterschiedliche Heizzyklen verursachen jedoch immer noch zu hohe Stillstandszeiten, wenn ein breites Gütespektrum gewalzt werden soll. Um den heutigen Marktanforderungen mit kleineren Losgrößen und zahlreichen Stahlsorten gerecht zu werden, ist es zu einer Notwendigkeit geworden, dass moderne Drahtstraßen ein hohes Maß an Flexibilität aufweisen.
Ein besonderer Aspekt in einem Drahtwalzwerk ist die Verwendung eines flexiblen Walzkaliberdesigns oder flexibler Nuten mit hohem Arbeitsbereich. Durch die Verwendung flexibler Stichfolgen kann das Walzen in den gleichen Nuten für eine Vielzahl von Endprodukten durchgeführt werden, indem einfach der Walzenabstand geändert wird. So kann der Rillenwechsel durch ein einfaches Verschieben des Walzenspalts ersetzt werden, was die Stillstandszeit für den Produktwechsel reduziert. Es besteht eine starke gegenseitige Abhängigkeit zwischen der Flexibilität des Walzkaliberdesigns, der Mühlenauslastung und der Ausbeute.
Durch den Einsatz eines flexiblen Walzkaliberdesigns kann ein wichtiger Teil der Verluste im Walzwerk reduziert werden. Ein flexibles Rollpass-Design minimiert das Risiko einer Rillenüberfüllung und der Bildung von Steinen während des Wechsels der Stahlsorte. Ein flexibles Walzkaliberdesign hat auch Vorteile für die Produktentwicklung, wenn neue Größen oder Stahlsorten eingeführt werden müssen. Auch eine wichtige Verbesserung der wertsteigernden Laufzeit kann mit einem flexiblen Walzkaliberdesign erreicht werden.
Mühlenproduktivität
Durch einen Kühlbettauslauf vor dem Fertigblock kann die Drahtstraße mit einer Stabstraße kombiniert werden. Dies geschieht normalerweise, um die Kapazität des vorgeschalteten Walzwerks auszunutzen. Beim Walzenwechsel im Walzdrahtblock produziert das vorgelagerte Walzwerk Stangen, um die Gesamtstillstandszeit des Walzwerks zu reduzieren.
Moderne Drahtwalzwerke sind im Allgemeinen Einzelstrangwalzwerke. Im Fall eines mehrsträngigen Walzwerks wird ein zweites Zwischenwalzwerk an jedem der Stränge eingeführt, um den Einfluss einer Änderung der Anzahl gleichzeitiger Stränge zu verringern. Das zweite Zwischenwalzwerk kann als Vorfertigblock ausgebildet sein. Es kann auch die Form eines Walzwerkblocks mit drei Walzen haben. Das Hauptmerkmal des Dreiwalzen-Walzwerks ist seine Fähigkeit, die Abmessungsabweichungen zwischen den drei genuteten Walzen, die den gesamten Umfang eines Walzguts walzen, zu unterdrücken und dadurch die Streuung im Vergleich zu einem herkömmlichen Duo-Walzwerk zu verringern. Dieses Zwischenwalzwerk ist als Maßwalzwerk bekannt, bei dem die Formgebung durch geringe Reduktion erfolgt. Dies trägt dazu bei, dass dem Werk eine Familienwalzphilosophie vorgelagert ist, wodurch die Umrüstzeit verkürzt wird.
Zur Erhöhung der Mühlengeschwindigkeit und damit der Mühlenproduktivität wird nach einem konventionellen Fertigblock ein Reduzier-/Maßwalzwerk (RSM) installiert. Die Integration eines RSM nach dem konventionellen Fertigblock verbessert die Walzwerksproduktivität bei kleinen Formaten erheblich (um bis zu 60 %). Seine extreme Präzision hat sich in vielen Installationen bewährt. Darüber hinaus führt dies in Kombination mit dem Walzen bei sehr niedriger Temperatur zu einer verfeinerten Mikrostruktur, die zusätzliche Sekundärprozesse eliminieren kann. Das RSM bietet sowohl Produktivitäts- als auch Qualitätsverbesserungen des Endprodukts, reduziert gleichzeitig die Betriebskosten und erhöht die Qualität des Walzdrahtprodukts. Es bietet Platz für eine Konstruktion mit einem einzigen Walzdurchgang von Gerüst 1 in der Vorgruppe bis zum letzten Gerüst des Endbearbeitungsblocks. Da es ein gleiches Einzelfamiliendurchgangsdesign ermöglicht, kann eine hohe Mühleneffizienz unabhängig von der endgültigen Produktgröße aufrechterhalten werden.
Spannungen zwischen den Gerüsten werden normalerweise beim Walzen von Walzdraht so weit wie möglich vermieden, da ansonsten Kopf- und Fußenden außerhalb der Toleranz liegen, weil die freien Enden nicht unter Spannung gewalzt werden können. Diese Tatsache kann zu überfüllten Rillen und Enddefekten wie Rippen führen. Im Hochgeschwindigkeitsblock ohne Verdrehung mit fester Übersetzung werden jedoch Spannungen zwischen den Gerüsten verwendet, um stabile Walzbedingungen zu erreichen. Wenn Spannungen zwischen den Gerüsten auf den gewalzten Stab aufgebracht werden, werden die Rillen so eingestellt, dass sie die erforderliche Toleranz ergeben.
Walzdrahtqualität
Walzdrähte werden in mehreren Anwendungen verwendet. Bei vielen Anwendungen sind die Qualitätsanforderungen an die Walzdrähte sehr streng. Eine minderwertige Qualität der Walzdrähte erhöht die Fehler/Abweichungen der Endprodukte und wirkt sich nachteilig auf die Ausbeute beim Kunden aus, was zu Unzufriedenheit bei den Kunden führt.
Da das Walzen von Walzdraht ein energieintensives Walzen ist, ist es immer erforderlich, dass das Walzen von fehlerhaften Walzdrahtbunden auf ein Minimum reduziert wird. Wenn der Mangel im Knüppel ziemlich groß ist, kann es manchmal sogar zu Pflastersteinen in der Mühle kommen. Da die Länge des Walzdrahts von einem Knüppel sehr lang ist, erfordert die Qualitätssicherung über die gesamte Länge des Walzdrahts nach dem Walzen Zeit und Mühe. Aus diesem Grund ist die Qualitätskontrolle von Knüppeln (dem Ausgangsmaterial vor dem Walzen) von großer Bedeutung. Die fehlerhaften Knüppel müssen durch Knüppelinspektion identifiziert, ausgesondert und entfernt werden. Knüppel sind sowohl auf Oberflächenfehler als auch auf innere Fehler zu untersuchen. Kleinere Oberflächenfehler können durch Schleifen (Konditionieren) des Knüppels entfernt werden.
Die wichtigen Eigenschaften, die von den Walzdrähten (insbesondere von dünnen Walzdrähten) gefordert werden, sind die hohe Produktivität bei der Nachbearbeitung und die hohe Festigkeit nach dem Fertigziehen. Die hohe Produktivität bedeutet Minimierung des Drahtbruchs während des Ziehens und Bündelns oder idealerweise kein Bruch, höhere direkte Ziehbarkeit und gute Ziehbarkeit unter schwierigen Ziehbedingungen wie hoher Ziehgeschwindigkeit. Diese immer anspruchsvolleren Anforderungen der Kunden werden durch die Anwendung strenger Standards für Qualitätskontrollelemente wie nichtmetallische Einschlüsse, Segregation, Entkohlung, mechanische Eigenschaften und Mikrostruktur erfüllt.
Normalerweise gibt es für viele Anwendungen drei Hauptanforderungen an die Walzdrähte. Diese sind (i) höhere Festigkeit, (ii) Wegfall bzw. Vereinfachung der Nachbearbeitung und (iii) weniger Einsatz umweltbelastender Stoffe. Eine höhere Stahlfestigkeit ist aufgrund von Kostensenkungen auf der Benutzerseite und aus vielen anderen Gründen erforderlich. Denn auf der Anwenderseite werden Walzdrähte verschiedenen Arten von Nachbearbeitungen wie Schmieden, Ziehen und maschineller Bearbeitung sowie einer Wärmebehandlung zum Glühen, Abschrecken, Anlassen usw. unterzogen
usw., daher drängen Anforderungen im Hinblick auf Kostenreduzierung, Energieeinsparung und Umweltschutz stark auf die Eliminierung oder Vereinfachung der Wärmebehandlung und maschinellen Bearbeitung (wie z. B. netznahe oder spanlose Formgebung).
Die Kontrolle von nichtmetallischen Einschlüssen, Ausscheidungen, Umwandlungen und metallographischen Strukturen ist eine metallurgische Schlüsselmaßnahme zur Verbesserung der Eigenschaften von Walzdraht. Die Kontrolle von nichtmetallischen Einschlüssen ist eine der wichtigsten Ausgangstechniken zur Festigkeitssteigerung von Federstählen, zur Verlängerung der Lebensdauer von Lagerstählen und zur Eliminierung von Blei aus Automatenstählen usw. Kontrolle der Struktur und Form von Oxiden und Sulfide ist wirksam bei der Verwirklichung der gewünschten Eigenschaften dieser Stähle.
In einer Drahtstraße gibt es keine Kompromisse, wenn es darum geht, vorgegebene Bandmaterialeigenschaften präzise zu erfüllen. Hier spielt das Controlled Cooling Conveyor (CCC) System eine Schlüsselrolle. Die gleichbleibend hohe Qualität im gesamten Walzdrahtbund muss kontrolliert werden.
In dieser Hinsicht spielt das CCC-System eine wichtige Rolle für die Verarbeitung hochwertiger Walzdrahtprodukte, das Erreichen der gewünschten Gleichmäßigkeit sowie der metallurgischen und mechanischen Eigenschaften. Es kontrolliert die Schwankungen der Zugfestigkeit rund um den Ring bei schnell abgekühlten Produkten streng auf eine Standardabweichung innerhalb von 1 % der durchschnittlichen Zugfestigkeit.
Das CCC-System ermöglicht durch eine geeignete Auswahl des Kühlregimes die Produktion aller herkömmlichen Stahlsorten sowie spezieller Produktsorten mit alternativen Kühlmodi. Es optimiert auch die Verarbeitung von unlegierten und legierten Stahlgüten, wenn es in Verbindung mit dem RSM für Niedertemperaturwalzen und kontrolliertes Abkühlen verwendet wird, wodurch eine sehr gute Kombination von Eigenschaften und Maßhaltigkeit erreicht wird.
Das CCC-System erleichtert die Verarbeitung unter einer Vielzahl von Bedingungen, einschließlich sowohl Schnellkühl- als auch Langsamkühlmodi innerhalb eines einzigen Systems. Diese Fähigkeit ermöglicht es dem Drahtwalzwerk, ein breites Spektrum an unlegierten und legierten Stählen sowie rostfreien Stählen und anderen Spezialgüten herzustellen. Das CCC-System führt zu verbesserten Walzdrahteigenschaften der Walzdrähte, die die Produktion von mehr Güten in einem direkt verwendbaren Zustand ermöglichen und nachgelagerte Prozesse, wie z. B. Kugelglühen, reduzieren oder eliminieren.
Das thermomechanische Walzen (TMR) in der Drahtstraße verfeinert die Endkorngröße durch dynamische Rekristallisation. In Kombination mit der abschließenden Inline-Wasserkühlung und der überlegenen kontrollierten Kühlung im CCC-System spielt TMR eine bedeutende Rolle bei der Bestimmung der Endprodukteigenschaften. Dies ist besonders vorteilhaft für niedrig- und mittellegierte Stahlprodukte, die anschließend in der Weiterverarbeitung kugelrundgeglüht werden. Die Fähigkeit, die Korngröße stark zu steuern, beeinflusst auch die nachfolgende Umwandlung in harte Produkte wie Bainit und Martensit durch Verschieben der Umwandlungsstartzeit und -temperatur. Somit kann TMR die direkt nachgelagerte Kaltumformung minimieren und die Glühzeiten verkürzen.
Die Kombination aus Verarbeitung im CCC-System und niedrigen Walztemperaturen bietet die Möglichkeit, die Härtbarkeit bei einigen kritischen Walzdrahtqualitäten zu reduzieren. Letztendlich fördert dies die Ferritbildung und verzögert die Entwicklung zu Bainit und Martensit. Die durch TMR erzielte verfeinerte Korngröße verbessert die Diffusion während der Wärmebehandlung und kann zu reduzierten Wärmebehandlungszeiten und -temperaturen führen. Bei nicht wärmebehandelten Stäben erhöhen die verfeinerten und komplexen Strukturen die Zugaufnahme während der Kaltverformung, was zu mehreren Vorteilen führt, wie z Härtbarkeit. Die Verbesserungen stammen aus der Kornverfeinerung und der mikrostrukturellen Kontrolle. Die gute Kontrolle des Kühlprozesses im CCC-System in Kombination mit der reduzierten Härtbarkeit der Walzdrähte macht den Prozess sehr stabil und verringert die Wahrscheinlichkeit der Bildung unerwünschter harter Phasen.
Herstellungsprozess