Bessere Wartungsplanung ist das Allheilmittel von MillerCoors
MillerCoors Asset CARE-Planer Tim Davison
Planung ist nicht sexy. Tom Clancy wird keinen Spionagethriller mit dem Titel „The Maintenance Planner“ schreiben.
Sie werden Ihre Kumpels nicht auf den Rand ihrer Barhocker setzen, wenn Sie die Zeit erzählen, in der Sie alle erforderlichen Schritte unternommen und für einen reibungslosen Ablauf des Überholungsprojekts gesorgt haben. („Alter, was ist dann passiert?!“)
Es gibt keinen Glanz oder Blitz oder Augenschmaus.
„Wenn eine Wartungsabteilung nach Verbesserungen strebt, liegt der Schwerpunkt in der Regel darauf, Siege zu zeigen und Vorher-Nachher-Bilder zu machen – Wow-Zeug“, sagt Dan Roberts, Asset CARE Director of Reliability bei Miller Coors in Golden, Colorado.
„Vorausschauende Wartung ist sexy. Bei der Infrarot-Thermografie machen Sie einen Schnappschuss und sagen:„Schauen Sie, was ich gefunden habe.“ Bei der Schwingungsanalyse schließen Sie es an, drucken Ihre Messwerte aus und sagen:„Ja, ich habe eine schlechte Peilung gefunden.“ Das ist alles wichtig und notwendig, aber im Kern wird gute Arbeit geleistet. Es ist einfach nicht sexy. Wie zeigen Sie die Ergebnisse einer effektiven Planung und Terminierung? Mit Vorher-Nachher-Fotos geht das nicht.“
Im Stillen und im Verborgenen nutzt die Wartungs- und Zuverlässigkeitsorganisation von MillerCoors Planung und Terminplanung als Verbesserungsinstrument. Es sorgt für Gleichgewicht in einer Umgebung, in der ein Ungleichgewicht schwerwiegende Folgen hat.
Aufrechterhaltung der Kette
MillerCoors, Amerikas drittgrößter Brauereikonzern, setzt seit mehr als einem Jahrzehnt auf Verbesserungen bei der Wartung, und das aus gutem Grund. Die Brauerei Golden braut 24 Stunden am Tag, sieben Tage die Woche, um täglich 217 Millionen Unzen Bier zu brauen.
„Es gibt vielleicht zwei Tage im Jahr, an denen wir nicht produzieren“, sagt Tim Davison, ein Asset CARE-Planer im Brauereiteil des großen Mehrwerkskomplexes in Golden.
Der Prozess der Bierherstellung – vom Rohstoff bis zur verpackten und versandten Ware – verläuft in einer eng verketteten Kette, und viele Prozesskomponenten verfügen über nicht redundante Maschinen. Wenn ein mechanischer Ausfall auftritt, ist die Verlagerung der Arbeit auf ein ähnliches Gerät möglicherweise keine Option. In diesen Fällen kommt der Prozess zum Erliegen.
„Wenn es eine Panne gibt, ist das normalerweise ein großes Problem“, sagt Ron Kerr, Asset CARE-Manager für Versorgungsunternehmen. „Es betrifft fast alle vor- und nachgelagert.“
Presseführer Craig Doebele bedient die Steuerung entlang der Produktionslinie
bei Rocky Mountain Metal Container, das Joint Venture von MillerCoors/Ball.
Ziel ist es, die Maschinen monatelang ununterbrochen laufen zu lassen, insbesondere während der Hauptsaison im Sommer, bis ein kurzes Wartungsfenster eingeplant werden kann.
Die einzigartige Struktur der Golden Business Units belastet die Kette zusätzlich. Während MillerCoors Eigentümer der Brauerei ist, ist es ein gemeinsamer Partner in den Bereichen Dosenherstellung (mit Ball Corporation) und Flaschenherstellung (Owens-Illinois). Es ist notwendig, dass alle in dieselbe Richtung ziehen, aber es erfordert Geduld.
The Missing Ingredient
Das Tempo der seit Jahren langsamen und stetigen Wartungsverbesserungen beschleunigte sich Ende der 1990er Jahre, nachdem Top-Player Anheuser Busch Preissenkungen angekündigt hatte. Um wettbewerbsfähig zu bleiben, versuchte MillerCoors, in das Front-End des Unternehmens zu reinvestieren.
„Die Kosten für unsere Waren mussten stark sinken“, sagt Roberts. „Wir mussten einer Reihe von Elementen nachgehen, darunter Operationen. Die Chance und das Ziel war es, der zuverlässigste Betrieb zu werden.“
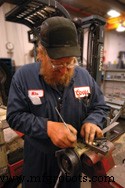
Asset CARE (ein Akronym für Capability, Availability, Reliability and Enhancement) wurde zum Sammelruf. Zuverlässige Wartung (RCM), Fehlerursachenanalyse (RCFA) und vorausschauende Wartung (PdM) wurden eingesetzt. Trotz dieser positiven Fortschritte fehlte etwas.
Roberts führt das Beispiel eines Lüfters an, der innerhalb von 18 Monaten drei dynamische Ausfälle erlebte. Nach dem ersten Ausfall identifizierte RCFA die Schmierung als Grundursache. Ein automatisches Schmiersystem wurde installiert. Nach dem zweiten Ausfall wurden die Autoschmieranlagen als problematisch eingestuft. Nach dem dritten Fehler traten die Wartungsleiter einen Schritt zurück.
„Wir nehmen jetzt an Ursachenkartierungsübungen teil, die uns dazu bringen, mehrere Grundursachen zu untersuchen“, sagt Roberts. „RCFA sagt nicht, dass es eine Ursache gibt, aber es führt die Leute in diese Richtung.“
Indem man tiefer ging, erwiesen sich Planung und Terminplanung als Mitverantwortliche für das Problem.
Einen Monat vor dem dritten Ausfall hatte eine Schwingungsanalyse Auffälligkeiten festgestellt. Es wurden jedoch keine geeigneten Schritte unternommen, um die Wartung zu planen und zu einer Priorität zu machen, bevor ein Fehler auftrat. Die Lektion:Erhebliche Gewinne sind unwahrscheinlich, wenn keine grundlegende Planung und Planung vorhanden ist.
„Vor unseren konzentrierten Bemühungen haben wir nicht per se geplant und geplant“, sagt Roberts. „Planer prüften Arbeitsaufträge im Computersystem, druckten sie aus, gaben sie einem Vorgesetzten und warteten darauf, dass der Vorgesetzte sie der Crew aushändigt. Es wurde wenig Mühe darauf verwendet, sich wöchentlich mit dem Betrieb zusammenzusetzen und zu überprüfen, was ansteht, Prioritäten zu bestimmen und Ressourcen zu identifizieren.“
Die Anlagen arbeiteten in einem reaktiven Wartungsmodus. Planer verbrachten viel Zeit damit, Ersatzteile zu beschaffen, zu lagern und zu verteilen.
„Wenn unsere Organisation zukunftsorientiert ist, finden wir die Dinge, die korrigiert werden müssen, schreiben den Arbeitsauftrag, planen den Arbeitsauftrag und erledigen die Arbeit. Wenn es reaktionär ist, kaufen wir erstklassige Sitze in Flugzeugen, um einen Motor zu verschiffen“, sagt Bobby McCall, Wartungsmanager für Verpackungsbetriebe.
Reaktives Arbeiten zahlte sich aus – Schulterklopfen und Dankeschön aus der Produktion. Dem Planer, der für die meisten Übernacht-Lieferungen verantwortlich war, wurde jedes Jahr ein Wanderpokal überreicht.
Dann hat MillerCoors einen besseren Weg gefunden, indem es wesentliche Komponenten einer effektiven Wartungsplanung identifiziert hat. Diese maximieren die Ressourcen, minimieren die Kosten und erhöhen die Gesamtzuverlässigkeit der Ausrüstung. In den folgenden Abschnitten werden einige dieser Komponenten beschrieben.
Dan Roberts ist der Asset CARE-Direktor für
Zuverlässigkeit bei MillerCoors Brewing Unternehmen in
Golden, Colorado. Obwohl die Werke des Unternehmens
bedeutende Fortschritte gemacht haben,
gibt er zu, dass „wir noch nicht da sind.“
Wirklich engagiert
Wie bei jeder Anstrengung ist Engagement der Schlüssel zum Erfolg. Bei MillerCoors beginnt zukunftsorientierte Wartung mit engagierten Planern und Ressourcen.
Eine Planungsorganisation braucht die entsprechende Anzahl von Planern. Jeder Planer muss einen Verantwortungsbereich haben, der lautet:
• angemessene geografische Größe;
• angemessene Zahl des vertretenen Handwerkspersonals; oder,
• angemessene Anzahl an Ausrüstungsgegenständen.
Wie kann der Planer ohne solche Grenzen die richtige Zeit und die richtigen Ressourcen aufwenden, um diesen Bereich effektiv zu pflegen?
Davison sagt, dass bei einem zu großen Bereich ein Planer sich nicht auf den gesamten Umfang konzentrieren kann, sondern nur auf die schlechten Akteure und Notfallsituationen, die auftreten. Wenn sich ein Planer auf schlechte Akteure und Fehler konzentriert, lässt er die notwendige vorausschauende und proaktive Planung nicht zu.
„Zwei Leute können nicht mit 4.000 Geräten planen“, sagt Davison. „Sie haben nur noch Zeit, Teile zu bestellen.“
Gabelstaplermechaniker Jerry Mitchell entfernt ein Rad in
um eine Lager für vorbeugende Wartungsarbeiten.
In Bezug auf die Abdeckung vom Planer zum Handwerk, sagt Roberts, sein derzeitiges Ziel sei ein Planer für alle 15 bis 18 Handwerker. Die allgemeine Regel ist, dass Sie mit zunehmendem Fortschritt in Richtung Weltklasse mehr Handwerker pro Planer haben können. Wenn Sie sich auf den unteren Sprossen der Leiter befinden, ist ein höherer Prozentsatz von Planern angemessen.
Ziel des Brauers ist es, seine Planer gezielt auf Aufgaben zu beschränken, die die Zuverlässigkeit und Aufrechterhaltung des definierten Verantwortungsbereichs betreffen. Andernfalls können Planer leicht von Aufgaben abgelenkt werden, die außerhalb ihrer Rolle und Funktion liegen.
„Die Produktion kann den Planer als „Go-Fer“ oder Wal-Mart betrachten, der alle seine Bedürfnisse und Wünsche erfüllt“, sagt Brad Simpkins, ein Asset CARE-Manager, der für mobile Geräte verantwortlich ist.
Das Werks- und Abteilungsmanagement kann Planer auch bei Verwaltungs-, Berichts- und Dateneingabeaufgaben behindern.
„Ohne die Fähigkeit, sich wirklich zu konzentrieren, wird die Planung reaktiv“, fügt Simpkins hinzu.
Ebenso wichtig ist, dass diese Planer auch dedizierte Ressourcen (Zeit und Manpower) benötigen, um geplante und geplante Arbeiten auszuführen. Dies kann für einige Wartungs- und Produktionsarbeiter eine bittere Pille sein.
„Einige der stündlichen Mechaniker sagten:‚Uns gefällt, was wir jetzt machen.‘ Sie kommen gerne mit dem weißen Pferd und retten den Tag“, sagt Jay Johnson, der Wartungsmanager für Prozessabläufe. „Aber sie haben gesehen, dass das Management zu 100 Prozent dahintersteckt. Das würde nicht weggehen.“
Produktionsleiter und Bediener waren auch misstrauisch, wenn es darum ging, das weiße Pferd auf die Weide zu bringen.
In der Verpackungsorganisation von MillerCoors war die Wartungsmannschaft zu gleichen Teilen auf drei Schichten verteilt. „Ihre Aufgabe war es, Maschinen zu reparieren und zum Laufen zu bringen“, sagt Kerr.
Dann kamen die ersten Terminänderungen. Ein beträchtlicher Prozentsatz der Handwerker, die nachts und am Wochenende arbeiteten, wurde auf die geplante Arbeit in der Tagschicht umgestellt.
„Die Produktion hat uns gesagt:‚Ihr unterstützt nicht unsere Pannen!‘“, sagt Kerr. "Du hast recht. Ich werde deine Pannen nicht unterstützen. Ich werde die proaktive Arbeit unterstützen. Sie dazu zu bringen, das zu akzeptieren, erforderte einen Vertrauensvorschuss.“
Unter den funktionalen Abteilungen innerhalb von MillerCoors ist die Verpackung derzeit der Vorreiter, um dedizierte Ressourcen für proaktive, geplante Arbeit einzusetzen.
„Wir werden 100 Prozent der verfügbaren Stunden für geplante Wartungsarbeiten einplanen“, sagt McCall. „Wir hören immer noch:‚Das kannst du nicht machen; Sie müssen für Pannen planen.“ Nein, wir werden keine Pannen planen. Wir planen geplante Arbeiten. Wir werden uns um die Pannen kümmern, wenn sie passieren.“
Auf allen Ebenen muss die Organisation erkennen, dass in einer Produktionsstätte Bediener und Handwerkspersonal vorhanden sind, da ein Prozess betrieben und gewartet werden muss. Es gibt Planer, um die Effektivität von Betreibern und Wartungspersonal zu maximieren. Wenn alle Ebenen im Betrieb beginnen, als Team für ein gemeinsames Ziel einer verbesserten Betriebssicherheit und Leistung zusammenzuarbeiten, liegt der Fokus nicht mehr auf „weißen Pferden“, sondern auf langfristigen, nachhaltigen Gewinnen.
Zeitmanagement
Ein weiterer Schlüssel zum Planungserfolg von MillerCoors besteht darin, die Zeit optimal zu nutzen.
Wie im vorherigen Abschnitt erwähnt, war die Produktion etwas skeptisch. Wenn Wartung die Produktion erleichtern sollte, mussten sich diese „Vordenker“ bewähren. Denken Sie daran, dass eine Offline-Maschine enorme Auswirkungen haben kann.
Eine Herausforderung bestand darin, der Produktion klarzumachen, dass ein 40-minütiger Stillstand einer Maschine zur vorbeugenden Wartung zu einer festgelegten Zeit und einem Tag besser ist als ein dreistündiger Ausfall nach einem Ausfall zu einer unbekannten Zeit und an einem unbekannten Tag. Die zusätzliche Herausforderung bestand darin, die Produktion davon zu überzeugen, dass ihre wertvolle Zeit nicht verschwendet wird.
„Wir hatten eine schlechte Erfolgsbilanz bei der Planung und Terminierung. Wir mussten beweisen, dass wir die geplante, proaktive Arbeit erledigen, wenn Sie uns die Zeit geben“, sagt Davison. „Sie haben die Linie heruntergefahren. Sie verlieren Geld. Du musst das Beste aus diesem Fenster machen.“
Die Zeitmaximierung erfolgt durch effektive Planung und Terminplanung.
Zunächst muss ein Wartungsfenster klar definiert (geplanter Zeitpunkt, Datum, Umfang und Dauer) und von Wartungsplanern und Produktionsleitern vereinbart werden. Von dort bestellt der Planer alle benötigten Teile und Materialien und stellt sicher, dass die richtigen Ressourcen für die Auftragsabwicklung zur Verfügung stehen. Der Planer achtet darauf, dass beim Öffnen des Fensters keine Überraschungen oder gar Stornierungen auftreten. Gestrandete oder nicht produktive Wartungsarbeit wirkt sich direkt auf die Kosten des Unternehmens aus.
Das Engagement endet hier nicht. Während des Fensters beobachtet, assistiert und bewertet der Planer die Arbeit, um die Arbeit umfassend zu kennen. Dieses Wissen wird angewendet, um ähnliche Aufgaben in der Zukunft besser planen und planen zu können. Ein gewisses Maß an Respekt und Wertschätzung erwirbt er sich auch von den Handwerkern, die an der Arbeit arbeiten. Dies ist wichtig, wenn zu einem späteren Zeitpunkt technische Ratschläge und Fragen auftauchen.
Bei MillerCoors handelt es sich zwar um die konventionelle Plan-as-work-ares-Methode, es gibt jedoch auch spezialisierte Planungs- und Planungsmethoden.
Die Dosenherstellungsanlage, die ständig laufen muss, um den Bedarf der Brauerei zu decken (12 Millionen Dosen pro Tag), verwendet einen 12-monatigen Stillstandsplan, der gemeinsam von Betriebs-, Wartungs-, Engineering-, Prozesskontroll-, Qualitäts-, Lager- und Disponenten entwickelt wird.
Der Plan 2005 listet die Daten, Standorte, Wartungsaktivitäten und Projektdetails für 1.655 Stunden geplanter Ausfallzeiten auf. Der Plan für 2006 wurde im September ausgearbeitet.
„Wir setzen 20 Leute in einen Raum und finden es als Team heraus“, sagt David Miller, der Direktor für technische Dienste bei Rocky Mountain Metal Container (dem MillerCoors/Ball-Joint-Venture). „Wir setzen alles auf den Zeitplan und erkunden, was wir während dieses Ausfalls noch tun können? Wie können wir diese Zeit maximieren? Wir können während des Jahres keine Überraschungen erleben. Wir müssen dem Spiel voraus sein. Daher ist der Ausfallzeitplan unser Leitdokument, um die Zuverlässigkeit der Ausrüstung und die Lieferung von Aluminiumdosen zu gewährleisten, um die Anforderungen der Brauerei zu erfüllen.“
Die Flaschenherstellungsanlage, die täglich 3 Millionen Flaschen produziert, verwendet vorausschauendes Denken für geplante Stillstände einzelner Maschinen und ganzer Anlagen.
„Früher haben wir das ganze Jahr über gearbeitet und dann zu Weihnachten wegen vorbeugender Wartung (PM) geschlossen“, sagt Tim Hood, der Engineering Services Manager bei Rocky Mountain Bottle Company (dem Joint Venture von MillerCoors/Owens-Illinois). „Für den Rest des Jahres würden Sie sich mit Ausfällen auseinandersetzen, wenn sie auftraten, weil wir keine anderen Ausfallzeiten eingeplant haben.“
Heute planen Planer, Wartungs- und Produktionsleiter in diesem Werk Ausfallzeiten, die als „Maxi-Boxenstopps“ bezeichnet werden. Ähnlich wie beim Stillstandsplan der Dosenfabrik werden diese Stopps für PMs und Überholungen lange im Voraus festgelegt.
„Wir planen verschiedene Maschinen zu unterschiedlichen Zeiten“, sagt Hood. „Auf diese Weise haben Sie nicht Ihre gesamte Ausrüstung auf einmal. Wir verschieben die Ressourcen, um die Ausfallzeiten auszugleichen.“
Im September findet ein jährlicher Anlagenstillstand unter der Leitung eines einzigen Planers statt.
„Er ist in den gesamten Plan involviert und versucht herauszufinden, welche Arbeiten während des Ausfalls zu erledigen sind“, sagt Hood. „In dieser Zeit führen wir eine Dampfreinigung der Maschinen und PM aller elektrischen Verteilungsgeräte durch. Es ist ein riesiges Unterfangen. Wenn wir einen Stillstand beenden, erstellt der Planer bereits den Plan für den nächsten.“
Der Brauprozess beginnt mit dem Mälzen der Gerste.
Gerste is in Wasser eingeweicht und zum Keimen angeregt.
Nach vier bis fünf Tagen wird das „Malz“ erhitzt, um das weitere Wachstum
zu stoppen. Das Malz wird dann von Stahlwalzen geknackt, um
seinen Inhalt freizulegen.
Nützliche Informationen
Der Planungserfolg von MillerCoors hängt auch davon ab, das Beste aus Informationen herauszuholen. Es beginnt mit etwas so Grundlegendem wie der Bereitstellung genauer Informationen zu verfügbaren Ressourcen für eine bestimmte Schicht.
"Wer ist hier? Wie lange sind sie hier? Mit wie vielen Ressourcen müssen Planer planen? Früher war es wie in jeder reaktiven Organisation nebulös“, sagt McCall. „Bei SAP haben wir es auf den Punkt gebracht. Planer sehen:„Ich habe ein Acht-Stunden-Fenster und 10 Leute. Ich kann 80 Stunden Arbeit einplanen. Hier sind 80 Stunden Arbeit, um diesen Plan zu verwirklichen.’“
Eine weitere ehemalige Grauzone waren Arbeitsaufträge. Wie in den meisten Werken wird ein Arbeitsauftrag erstellt, wenn Arbeit identifiziert wird. Aber welche Informationen sind in diesem Arbeitsauftrag enthalten?
Aus der Vergangenheit gelernt, sagen die Wartungsleiter von MillerCoors heute, dass ein Arbeitsauftrag in der Lage sein muss, den korrekten Geräteladecode, die gesamte Gerätehistorie, Arbeits- und Materialkosten sowie Vertragsserviceanforderungen zu erfassen. Um Gerätefehler genau zu verfolgen, wird bei der Auftragserstellung eine detaillierte Arbeitsbeschreibung und nach Abschluss des Arbeitsauftrags eine genaue Beschreibung der Maßnahmen zur Behebung des Fehlers eingegeben. Wenn dies nicht geschieht, ist die Historie für ein bestimmtes Gerät verzerrt und kann Störungen oder Ausfälle nicht genau berücksichtigen. Außerdem wird die richtige Gerätenummer in den Arbeitsauftrag eingetragen. Ohne dies sind wichtige Verlaufsverfolgungsmaßnahmen wie Materialverbrauch und berechnete Arbeitsstunden mit dem falschen Gerät verknüpft oder fehlen ganz.
„In der Vergangenheit wurden schlechte Entscheidungen getroffen, weil wir keine genauen Arbeitsauftragsinformationen hatten“, sagt Davison.
Wenn bei MillerCoors ein Arbeitsauftrag erstellt wird, werden Notizen gemacht, um Folgendes zu identifizieren:
• alle Teile, Fähigkeiten oder externen Ressourcen, die benötigt werden, um die Arbeit abzuschließen;
• alle möglicherweise erforderlichen Spezialwerkzeuge, Ausrüstungen oder Ressourcen; und,
• mögliche Sicherheits- oder Umweltbedenken.
Mit diesen Vorabinformationen beschafft der Planer die benötigten Teile und Materialien, sammelt die erforderlichen Ressourcen und plant und terminiert die Arbeiten genau. Dies verlängert die Schraubenschlüsselzeit.
Wenn die Arbeit abgeschlossen ist, gibt ein Handwerker detaillierte Informationen ein, um den Arbeitsauftrag ordnungsgemäß abzuschließen. Im SAP-Arbeitsauftragssystem des Unternehmens gibt er oder sie einen Ursachencode, einen Fehlercode und einen Objektteil genau in den letzten Verlaufsteil der Benachrichtigung ein. Eine ausführliche Langtextbeschreibung der durchgeführten Arbeiten wird zusammen mit eventuellen Problemen oder Abweichungen dokumentiert.
Aber all diese Schritte sind wertlos, wenn Sie die Informationen nicht verwenden.
Wartungsarbeiten wiederholen sich. Was heute über eine Maschine gelernt wird, erweist sich als hilfreich, wenn in Zukunft dieselbe oder eine ähnliche Maschine gewartet werden muss. Historien identifizieren Trends und helfen bei der Entwicklung effektiver Zuverlässigkeitsstrategien.
„Wenn die Daten für dieses Gerät nicht genau sind, erhalten Sie kein vollständiges Bild und machen Fehler bei der Wartung dieses Geräts“, sagt Davison. „Wenn es nicht im System aufgezeichnet wird, haben Sie keine Daten zum Analysieren. Die Planer brauchen dies, um zu entscheiden, wie sie das nächste Mal planen, es besser machen und es für Ursachenzwecke verwenden.“
Mit korrekt eingegebenen Arbeitsauftragsinformationen können die Mitarbeiter von MillerCoors auf die Arbeitsauftrags- und Kostenhistorie für ein einzelnes Gerät, eine Abteilung, eine Kostenstelle oder die gesamte Einrichtung zugreifen. Mit diesen Daten bestimmen Planer den PM-Abschlussprozentsatz, die Durchlaufzeit von Arbeitsaufträgen, die durchschnittliche Reparaturzeit und die durchschnittliche Zeit zwischen Ausfällen. Sie greifen auch auf den prozentualen Mix von PM-, Korrektur-, Pannen- und Projektarbeitsaufträgen für einen bestimmten Zeitraum zu. Diese Berichte geben ihnen die Werkzeuge, um die PM-Frequenzen entsprechend der generierten Bestellungen und der MTBF anzupassen.
„Bei einigen Geräten stellten wir fest, dass unsere PM-Frequenzen zu hoch waren“, sagt McCall. „Unsere Planer schauen sich regelmäßig PMs an. Sie stellen sicher, dass die richtige PM mit der richtigen Frequenz vorhanden ist. Die Idee ist, dass die Arbeit, die wir planen, die Arbeit ist, die getan werden sollte. Wir wollen unsere Zeit und unser Geld am besten nutzen und uns um die richtigen Dinge kümmern.“
Asset CARE-Manager Bobby McCall (links) und Ron Kerr
diskutieren Motoren und Getriebe in der Verpackungslinie der Brauerei.
Goldene Ergebnisse
Planungsverbesserungen und Planungskompetenz haben sich bei MillerCoors ausgewirkt.
„Wir hatten schon immer großartige Leute mit dem Wunsch, die richtigen Dinge zu tun“, sagt Anlageningenieur Mike Fognani. „Durch Planung und Terminierung können wir diese großartigen Leute mit den Tools, Materialien und der Zeit kombinieren, die für den Erfolg erforderlich sind.“
Geplante und geplante Arbeiten an vielen Baustellenbereichen machen inzwischen mehr als 60 Prozent des Wartungsaufwands aus; in der jüngsten Vergangenheit waren es weniger als 30 %.
Abgeschlossene PM-Arbeiten haben dramatisch zugenommen. Im Gabelstaplerbereich beispielsweise ist die Fertigstellungsrate laut Simpkins in weniger als 18 Monaten von 31 % auf 82 % gestiegen.
Anlagenverfügbarkeit, Produktivität und Betriebszeit sind gestiegen. All dies hat zu geringeren Wartungskosten geführt.
„Früher hieß es ‚Wartung kann es nicht am Laufen halten‘, ‚Sie sind nicht zuverlässig‘ und ‚Sie geben zu viel Geld aus‘“, sagt McCall. „Seit wir uns stabilisiert und proaktiver gemacht haben, sind unsere Wartungskosten gesunken.“
Es gibt noch viele Möglichkeiten.
„In vielen Bereichen tun wir, was wir tun müssen, und erzielen die gewünschten Ergebnisse“, sagt Roberts. „Wir sind auf dem richtigen Weg, aber wir sind noch nicht da. Wir haben bei der Planung und Terminplanung noch immer viele Möglichkeiten und konzentrieren uns auf Möglichkeiten, schrittweise Änderungen vorzunehmen, selbst nach der bereits geleisteten großartigen Arbeit.“
Reduzierte Kosten. Erhöhte Zuverlässigkeit. Bessere Entscheidungen. Höhere Stabilität.
MillerCoors hat vielleicht einen Weg gefunden, die Planung sexy zu machen.
Nur die Fakten Website :MillerCoors-Werke in Golden, Colorado (einschließlich Brauerei und zugehöriger Produktionsunterstützungsbereiche) und Rocky Mountain Metal Container und Rocky Mountain Bottle Company (zwei Joint-Venture-Werke).Beschäftigung :Fast 2.000 Mitarbeiter in den Produktionsstätten von Golden.
Standortgröße :Befindet sich hauptsächlich in einem 8 km langen Tal in Golden.
Produkte :Fast ein Dutzend Biermarken, darunter Coors, Coors Light, George Killians Irish Red Lager, Aspen Edge und Keystone. Außerdem Malzgetränke der Marke Zima.
Produktionsvolumen :Mehr als 20 Millionen Barrel Bier werden jährlich in Golden gebraut.
Gerätewartung und Reparatur
- Durch die richtige Planung mehr Wartungsarbeiten erledigen
- So erreichen Sie eine effektive Wartungsplanung
- Morgenbesprechungen:Wartungsplanung und -planung
- Bei der Wartung können zwei plus zwei acht ergeben
- Wartungsplanung:Was haben Sie davon?
- Teamarbeit, Planung und Terminplanung
- Kontrollbereiche für Wartungsplaner und andere
- Boeing stimmt der Verbesserung der Wartungsplanungsprozesse zu
- Ist vorbeugende Wartung oder vorausschauende Wartung besser?
- Warum proaktive Wartung besser ist als nur vorbeugende Wartung