Anwendungs-Spotlight:Wie 3D-Druck leistungsfähigere Hydraulikkomponenten ermöglicht
[Bildnachweis:Renishaw]
Die Nachfrage nach neuen Ansätzen in der Konstruktion und Herstellung von Hydraulikkomponenten steigt. Eine Technologie, die es Herstellern ermöglicht, neue Möglichkeiten in der Hydraulikfertigung zu erkunden, ist der 3D-Druck.
Von Liebherr über Ford bis Bosch Rexroth setzen Unternehmen auf den 3D-Druck, um energieeffizientere, leichtere und kostengünstigere Hydraulikkomponenten herzustellen.
Das heutige Application Spotlight befasst sich mit den Vorteilen des 3D-Drucks für Hydrauliksysteme und -komponenten und erforscht die aufregendsten Beispiele der Technologie in Aktion.
Schauen Sie sich die anderen Anwendungen an, die in dieser Serie behandelt werden:
3D-Druck für Wärmetauscher
3D-Druck für Lager
3D-Druck für die Fahrradherstellung
3D-Druck für die digitale Zahnheilkunde und die Herstellung von Clear Alignern
3D-Druck für medizinische Implantate
3D-gedruckte Raketen und die Zukunft der Herstellung von Raumfahrzeugen
3D-Druck für die Schuhherstellung
3D-Druck für elektronische Komponenten
3D-Druck in der Bahnindustrie
3D-gedruckte Brillen
3D-Druck für die Endfertigung
3D-Druck für Halterungen
3D-Druck für Turbinenteile
Wie 3D-Druck Innovationen in der Kernkraftindustrie unterstützt
Warum 3D-Druck für Hydraulikkomponenten verwenden?
Hydraulik ist eine der effizientesten Möglichkeiten, um Bewegung zu erzeugen, wenn schwere Lasten beteiligt sind oder sich wiederholende Bewegungen erforderlich sind.
Hydrauliksysteme verwenden Pumpen, um eine Flüssigkeit unter Druck zu setzen, und ihre Bewegung wird dann verwendet, um alles anzutreiben, von Kränen bis hin zu Autos.
Hydraulik ist überall um uns herum. Es wird in Fahrzeugen, Baumaschinen, Gebäuden und Produktionsstätten verwendet.
Hydraulikkomponenten werden traditionell durch Zerspanen oder Gießen hergestellt. Viele Hersteller von Hydraulikausrüstungen interessieren sich jedoch zunehmend dafür, Hydraulikkomponenten wie Verteiler, Servoventile und Hydraulikadapterblöcke im 3D-Druck herzustellen. Aber was bringt sie dazu, die Technologie überhaupt in Betracht zu ziehen?
Laut Steffen Haack, Leiter des Geschäftsbereichs Industriehydraulik der Bosch Rexroth AG, prägen viele Trends die Hydraulikbranche, darunter:
- Energieeffizienz (reduzierte Strömungskräfte, geringerer Druckverlust, höhere Effizienz)
- Rauschunterdrückung
- Reduziertes Tankvolumen
- Höheres Druckniveau und reduzierter Bauraum
- Verbesserte Material- und Öleigenschaften
- Höhere Verfügbarkeit und vorausschauende Wartung
- Benutzerfreundlichkeit
- Sicherheit
Der 3D-Druck, insbesondere mit Metallen und Sand, spielt eine wichtige Rolle, um einige dieser Trends wie erhöhte Energieeffizienz und kleinerer Bauraum voranzutreiben.
Wie? Durch die Ermöglichung fortschrittlicher Designs, die es ermöglichen, neue Funktionen zu integrieren, Gewicht und Größe der Komponenten zu reduzieren und die Leistung des gesamten Hydrauliksystems zu verbessern.
Lassen Sie uns tiefer in die Vorteile des 3D-Drucks für die Hydraulik eintauchen.
Verringerung von Gewicht und Größe von Hydraulikkomponenten
Der 3D-Druck ermöglicht es Herstellern von Hydraulikkomponenten, Teile leichter und kleiner zu machen.
Nehmen Sie als Beispiel einen Hydraulikverteiler. Dieser Teil, der hilft, den Flüssigkeitsfluss zwischen den Komponenten eines Hydrauliksystems zu regulieren, wird normalerweise aus einem massiven Metallblock hergestellt.
Das Entfernen von mehr überschüssigem Metall als nötig ist teuer, und häufig wird das überschüssige Metall nicht entfernt, was zu einem Teil führt, das mehr wiegt, als es möglicherweise könnte.
3D Drucken hilft, dieses Problem zu lösen, da fast die gleiche Menge an Material benötigt wird, die für die Herstellung eines Verteilers benötigt wird.
In einem Metall-3D-Druckverfahren, wie dem selektiven Lasersintern, zeichnet ein Laser einen mikrometerdünnen Querschnitt eines Teils nach, wobei ein Metallpulver Schicht für Schicht selektiv geschmolzen und verschmolzen wird. Auf diese Weise können Ingenieure die Materialmenge, die in das Teil eingeht, kontrollieren und dabei weniger Metall verwenden, als die CNC-Bearbeitung erfordern würde.
Der 3D-Druck reduziert nicht nur das Gewicht der Komponenten, sondern ermöglicht auch kompaktere Teile, die besser in konstruktionsbedingte Räume passen. Dieser Vorteil macht 3D-gedruckte Hydraulikkomponenten besonders bei Anwendungen gefragt, die hohe Präzision und geringes Gewicht erfordern.
Spotlight:Aidros 3D-gedruckter Verteiler
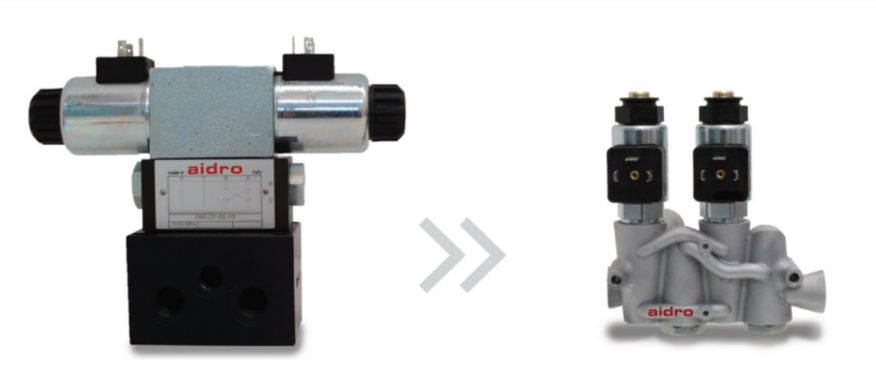
Ein Beispiel für eine 3D-gedruckte Hydraulikkomponente stammt vom italienischen Hersteller Aidro.
Der Hydraulikverteiler von Aidro, der in Landmaschinen verwendet wird, wurde überarbeitet, um Gewicht und Platz in einem System zu sparen, in dem es verwendet wird. Der 3D-gedruckte Aluminiumverteiler erfüllt die gleichen Funktionen wie die Einheit, die er ersetzt, ist aber halb so groß Größe und 75 Prozent leichter als der bisherige Verteiler.
Teilekonsolidierung
Der 3D-Druck ermöglicht auch die Verkleinerung von Komponenten, indem mehrere Teile zu einem zusammengefasst werden – ein Ansatz, der als Teilekonsolidierung bekannt ist.
Dies ermöglicht es Herstellern, komplexe Baugruppen von Komponenten zu eliminieren und die strukturelle Integrität eines Teils zu verbessern, da es weniger schwache Verbindungsstellen gibt, die Undichtigkeiten verursachen können.
Effizienzoptimierung
Der 3D-Druck ermöglicht es, die Innengeometrien einer Hydraulikkomponente neu zu gestalten, um den Flüssigkeitsfluss zu optimieren und den Druckabfall zu reduzieren.
Am Beispiel Verteiler können Ingenieure Strömungskanäle innerhalb eines Verteilers genau dort positionieren, wo sie sind benötigt und in verschiedenen Formen und Größen. Dies bedeutet, dass Strömungskanäle gekrümmte Formen haben und enger beieinander angeordnet werden können als bei herkömmlichen Verteilern, was das Endprodukt kompakter und leichter macht.
Gekrümmte Strömungswege können Berichten zufolge die Strömungseffizienz um 30 bis 70 Prozent verbessern.
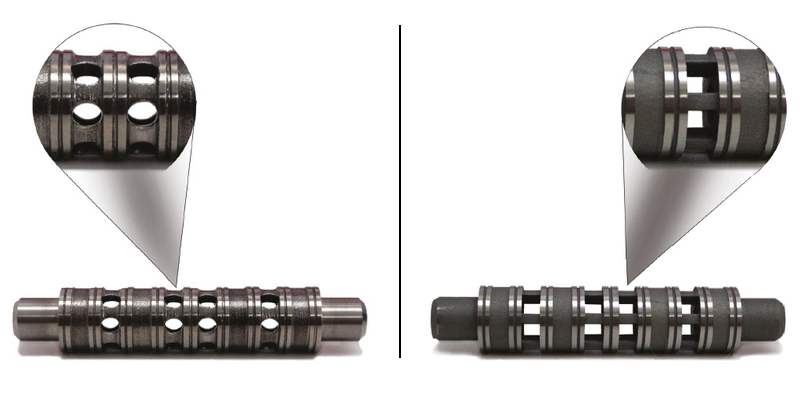
Eine Neugestaltung des Querschnitts von Strömungskanälen kann ebenfalls einen Unterschied machen. Fließwege in Ventilspulen haben beispielsweise typischerweise eine runde Form, da sie mit rotierenden Fräsern bearbeitet werden.
Der 3D-Druck ermöglicht es Ingenieuren, Querschnitte von Strömungswegen quadratisch statt rund zu gestalten, was die Strömungskapazität um bis zu 20 Prozent erhöhen und den Druckabfall reduzieren kann.
Darüber hinaus erfordern herkömmliche Hydraulikkomponenten, wie beispielsweise Verteiler, häufig die Bearbeitung von quergebohrten Kanälen, die anschließend verschlossen werden müssen, um ein Auslaufen von Öl zu verhindern. Diese verstopften Kanäle erzeugen jedoch potenzielle Leckpfade, die einen Systemausfall verursachen können. Der 3D-Druck beseitigt dieses Problem, indem es überhaupt nicht mehr erforderlich ist, quergebohrte Passagen zu erstellen.
Weitere Beispiele für 3D-gedruckte Hydraulikkomponenten
3D-Druck eines hydraulischen Adapterblocks
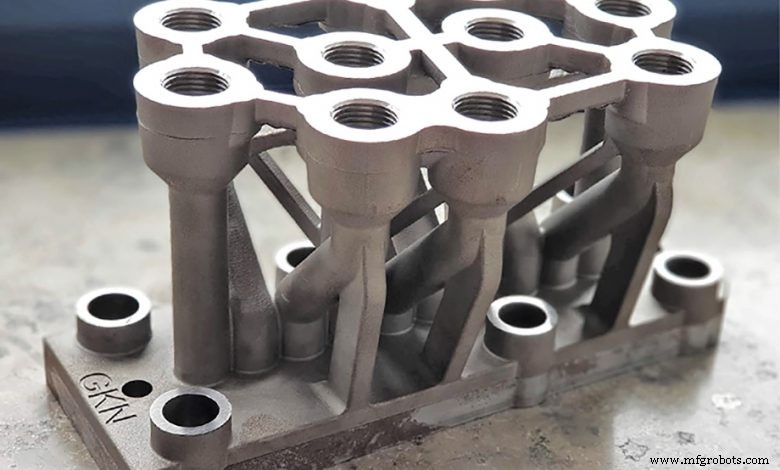
GKN Additive hat einen hydraulischen Adapterblock in 3D gedruckt, bei dem es sich um einen Verteiler handelt, der den Flüssigkeitsstrom in einem Hydrauliksystem leitet und Ventile, Pumpen und Aktoren verbindet.
Traditionell verwendete Hydraulikblöcke haben in der Regel ein blockiges Design mit einer Reihe von darin gebohrten Innenkanälen. Der Herstellungsprozess von Hydraulikblöcken beginnt mit dem Bohren von Löchern von oben und unten.
Die vertikalen Löcher werden dann durch horizontale Kanäle verbunden und die Gewinde werden hineingeschnitten. Um ein Austreten von Öl aus den offenen horizontalen Kanälen zu verhindern, werden sie mit Madenschrauben verschlossen und abgedichtet.
Dieses Verfahren ist jedoch aus mehreren Gründen höchst ineffizient. Zum einen erzeugen die gebohrten und gefrästen Kanten scharfe Grate, die in der Nachbearbeitung schwer zu erreichen sind. Diese können im Betrieb manchmal abbrechen und einen Systemausfall verursachen.
Zweitens erzeugen die scharfen Eckverbindungspunkte eine turbulente Strömung, was zu Energieineffizienzen führt. Drittens können ungenutzte horizontale Kanäle Schmutz ansammeln und die Lebensdauer des Hydrauliksystems verringern.
3D-Druck half GKN Additive, die oben genannten Herausforderungen zu überwinden, um einen leistungsstärkeren Hydraulikblock zu schaffen.
Das Gewicht des Hydraulikblocks wurde von 30 kg auf 5,5 kg reduziert, ohne an Funktionalität einzubüßen. Mit einem neuen Design war es möglich, überschüssiges Material zu entfernen und sicherzustellen, dass es keine Bohrungsüberlappungen innerhalb des Teils gab.
Außerdem verzichtet das neue Design komplett auf die ungenutzten horizontalen Kanäle, sodass sich Schmutz nirgendwo ansammeln kann. Um die turbulente Strömung im System zu reduzieren, ersetzten die Ingenieure schließlich scharfe Innenecken durch glatte Rohrleitungen.
Um die Vorteile des 3D-Drucks für diese Anwendung zusammenzufassen, ermöglichte der 3D-Druck dem Hersteller, die Funktionalität des Bauteils zu verbessern und gleichzeitig weniger Material zu verbrauchen. Dies führte zu einem geringeren Gewicht des Teils und zu geringeren Herstellungskosten.
Der 3D-gedruckte Hydraulikventilblock von Liebherr
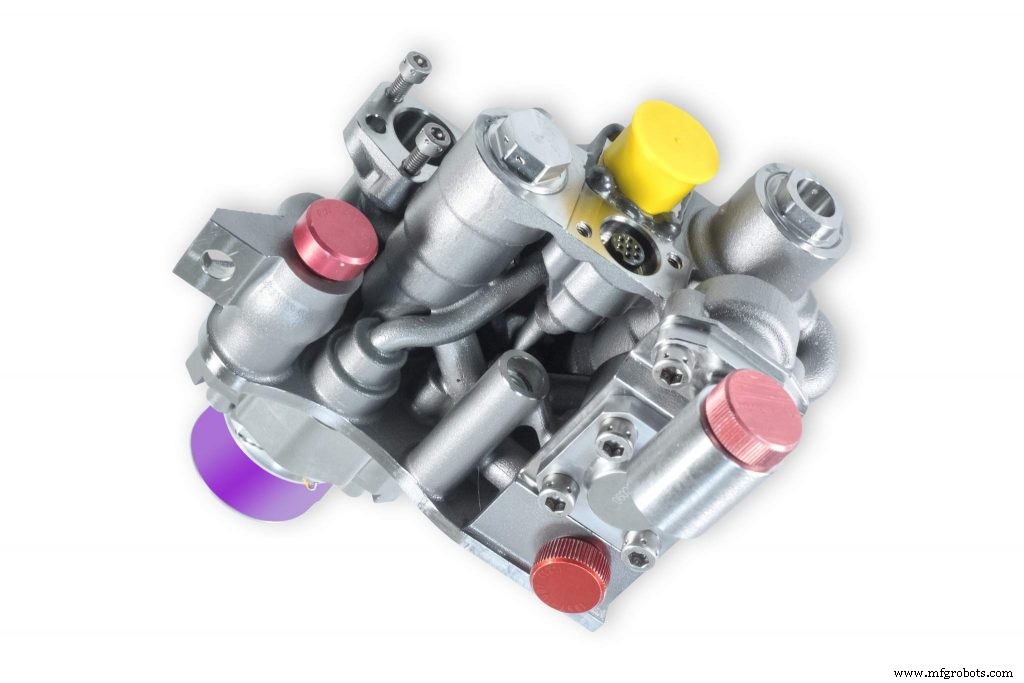
Ein weiteres gutes Beispiel für 3D-Druck für die Hydraulik stammt aus der Firmengruppe Liebherr. Mithilfe des 3D-Drucks konnte das Unternehmen einen Hochdruck-Hydraulikventilblock, der in Flugzeugen verwendet wird, leichter und effizienter gestalten.
Das Liebherr-Team hat 10 Funktionselemente in den neuen Ventilblock integriert, wodurch das komplexe Verrohrungssystem mit vielen Querbohrungen entfällt. Das Ergebnis ist ein 35 Prozent leichterer Ventilblock, der aus weniger Teilen besteht.
Das 3D-gedruckte Teil wurde in einem Testflug des A380-Flugzeugs erfolgreich getestet.
Domin Fluidtechnik erfindet seine Fluidtechniksysteme mit 3D-Druck neu
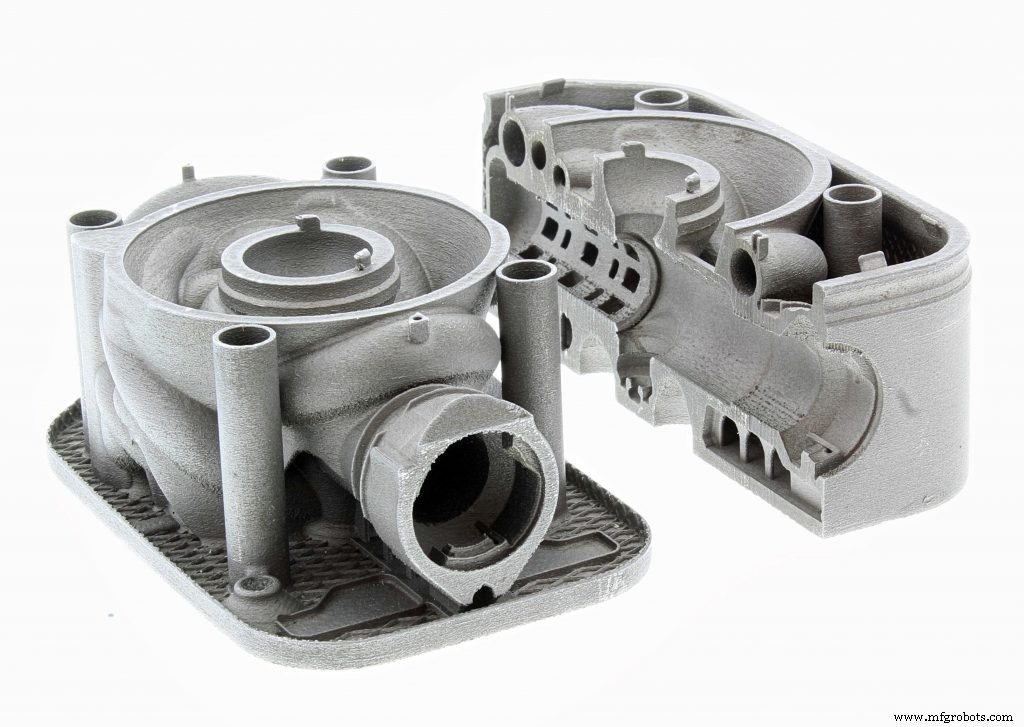
Der britische Hersteller von Hydrauliksystemen Domin hat sich dem 3D-Druck zugewandt, um seine Hochleistungs-Servoventile mit Direktantrieb, die zur Umwandlung von Signalen in Druck verwendet werden, neu zu entwickeln.
Domin erklärt, dass der 3D-Druck es ihm ermöglicht, komplexe Teile schneller und ohne Werkzeug zu bauen. So hat das Unternehmen beispielsweise einen seiner Antriebe auf 25 Prozent der ursprünglichen Größe und 25 Prozent leistungsstärker ausgelegt. Das Teil wurde zu einem Drittel der Kosten produziert und die Fertigungszeit konnte von 5,5 Stunden auf nur noch 1 Stunde verkürzt werden.
Solche Ergebnisse wären mit herkömmlichen Methoden unmöglich zu erreichen, behauptet Domin.
Ford 3D druckt einen Ansaugkrümmer
Während wir die Beispiele für 3D-gedruckte Hydraulikkomponenten für schwere Maschinen und Flugzeuge gesehen haben, war Ford Vorreiter beim 3D-Druck für Automobilhydrauliksysteme.
Letztes Jahr präsentierte der Autohersteller den angeblich größten 3D-gedruckten Metall-Ansaugkrümmer, der jemals in ein funktionierendes Fahrzeug eingebaut wurde.
Bei diesem Fahrzeug handelt es sich um den "Hoonitruck" von Ken Block. Ford-Pickup.
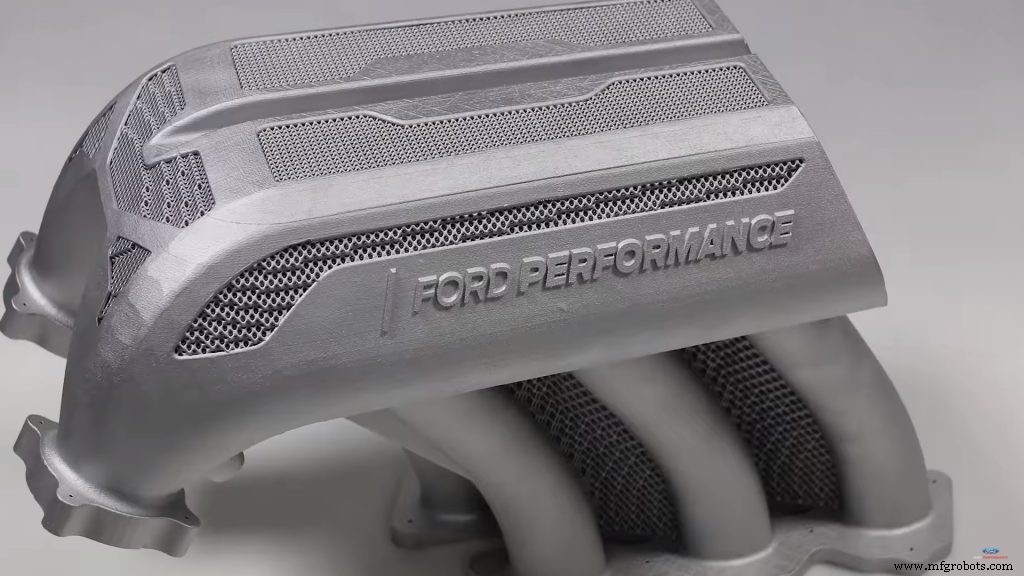
Das Fahrzeug benötigte einen speziellen Ansaugkrümmer, um die Zylinder des Motors mit Luft aus den Turboladern zu versorgen, und Ford entschied sich für den Metall-3D-Druck.
Das Teil wird mit einer Concept Laser-Maschine aus Aluminium 3D gedruckt und die Herstellung dauerte 5 Tage. Durch den Einsatz modernster CAD-Software war es möglich, eine komplexe netzartige Struktur zu erstellen, die mit herkömmlichen Herstellungsverfahren nicht hergestellt werden konnte. Das Design ist auf bessere Leistung und geringeres Gewicht optimiert – das fertige Teil wiegt nur 6 kg.
Bosch Rexroth verwendet Sand-3D-Druck für Verteiler
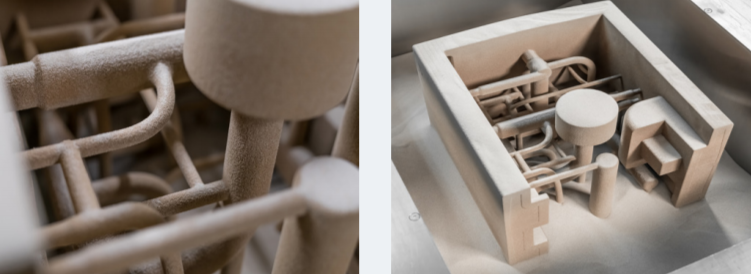
Neben dem Metall-3D-Druck besteht auch die Möglichkeit, einen Sandkern in 3D zu drucken, der anschließend zum Gießen eines Hydraulikbauteils verwendet werden kann. Das für diese Anwendung verwendete Verfahren wird als Binder Jetting bezeichnet und funktioniert durch selektives Abscheiden eines Bindemittels auf einer Quarzsandschicht.
Bosch Rexroth setzt bereits seit mehreren Jahren Sand-3D-Druck zur Herstellung von Gusskernen für Steuerblöcke ein.
Zu den wesentlichen Vorteilen dabei nennt Bosch Rexroth die Möglichkeit, Maschinenkomponenten wie Filter in den Verteiler zu integrieren, und eine Gewichtsreduzierung um bis zu 30 Prozent.
Zu den weiteren Vorteilen zählen der Wegfall von Hilfsbohrungen, die Undichtigkeiten verursachen können, und die Optimierung der internen Strömungskanäle, die die Energieeffizienz verbessern.
Hydraulikkomponenten mit 3D-Druck neu denken
Da die Hydraulikindustrie nach energieeffizienteren und kleineren Hydraulikkomponenten strebt, bietet der 3D-Druck eine Möglichkeit, leistungsfähigere Designs zu entwickeln und zu produzieren.
Angesichts der Vorteile in Bezug auf Vorlaufzeit, Gewichtseinsparungen und Kosten und Leistung, die der 3D-Druck ermöglicht, beginnen viele Hersteller von Hydraulikkomponenten, diese Technologie für ihre Produkte zu erkunden.
Wir erwarten, dass die Rolle des 3D-Drucks bei der Herstellung von Hydraulikkomponenten in Zukunft zunehmen wird und Unternehmen in der Hydraulikindustrie dabei hilft, mit aktuellen und zukünftigen Trends Schritt zu halten.
3d Drucken
- Anwendungs-Spotlight:3D-Druck für medizinische Implantate
- Anwendungs-Spotlight:3D-Druck für die digitale Zahnheilkunde und die Herstellung von Clear Alignern
- Anwendungs-Spotlight:3D-Druck für die Fahrradherstellung
- Anwendungs-Spotlight:3D-Druck für Lager
- Anwendungs-Spotlight:3D-Druck für Wärmetauscher
- Anwendungs-Spotlight:3D-Druck in der Bahnindustrie
- Anwendungs-Spotlight:5 elektronische Komponenten, die vom 3D-Druck profitieren können
- Anwendungs-Spotlight:3D-Druck für Schuhe
- Anwendungs-Spotlight:3D-gedruckte Raketen und die Zukunft der Raumfahrzeugfertigung
- Anwendungs-Spotlight:3D-gedruckte Brillen