Methoden zur Oberflächen- und internen Qualitätsprüfung von Gussteilen
Die Prüfung von Gussteilen umfasst hauptsächlich Maßprüfung, Sichtprüfung des Aussehens und der Oberfläche, Analyse der chemischen Zusammensetzung und Prüfung der mechanischen Eigenschaften. Bei Gussteilen mit hohen Anforderungen ist zusätzlich eine zerstörungsfreie Prüfung erforderlich. Zu den zerstörungsfreien Prüftechniken für die Qualitätsprüfung von Gussteilen aus duktilem Gusseisen gehören beispielsweise die Flüssigkeitseindringprüfung, die Wirbelstromprüfung, die Magnetpulverprüfung, die Durchstrahlungsprüfung und die Ultraschallprüfung.
Prüfung von Oberflächen- und oberflächennahen Fehlern von Gussteilen
Flüssigeindringprüfung
Die Flüssigkeitseindringprüfung wird verwendet, um verschiedene Öffnungsfehler auf der Oberfläche von Gussteilen zu untersuchen, wie z. B. Oberflächenrisse, Oberflächennadellöcher und andere Fehler, die mit bloßem Auge schwer zu erkennen sind.
Die häufig verwendete Eindringprüfung ist die Farbstoffprüfung, bei der das hochdurchlässige Eindringmittel auf die Gussoberfläche benetzt oder gesprüht wird, das Eindringmittel in die Öffnungsfehler eindringt, die Eindringmittelschicht schnell abgewischt wird und dann der leicht zu trocknende Entwickler auf das Gussteil gesprüht wird auftauchen. Nachdem das Eindringmittel, das in den Öffnungsdefekten verbleibt, abgesaugt wurde, wird der Entwickler gefärbt, um die Form, Größe und Verteilung der Defekte widerzuspiegeln.
Es wird darauf hingewiesen, dass die Wirkung der Penetrationsprüfung umso besser ist, je glatter die zu prüfende Oberfläche ist. Die vom Schleifer polierte Oberfläche weist höchste Prüfgenauigkeit auf und sogar Korngrenzenrisse können erkannt werden.
Neben der Farbstoffprüfung ist auch die fluoreszierende Eindringprüfung ein häufig verwendetes Verfahren zur Eindringprüfung mit Flüssigkeiten. Es muss mit einer UV-Lampe zur Bestrahlungsbeobachtung ausgestattet sein, und die Testempfindlichkeit ist höher als die Farbstoffprüfung.
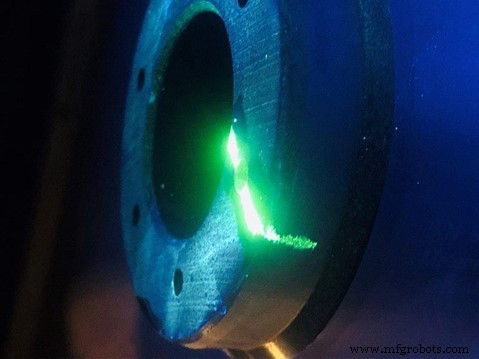
Wirbelstromprüfung
Die Wirbelstromprüfung eignet sich zum Prüfen von Defekten unter der Oberfläche, die im Allgemeinen nicht tiefer als 6-7 mm sind. Die Wirbelstromprüfung wird in zwei Arten unterteilt:das Verfahren mit platzierter Spule und das Verfahren mit durchgehender Spule.
Wenn das Teststück in der Nähe der Spule mit Wechselstrom platziert wird, kann das in das Teststück eintretende magnetische Wechselfeld einen Wirbelstrom induzieren, der in der Richtung senkrecht zum Anregungsmagnetfeld im Teststück fließt. Wirbelstrom erzeugt ein Magnetfeld, das der Richtung des Erregermagnetfelds entgegengesetzt ist, wodurch das ursprüngliche Magnetfeld in der Spule teilweise reduziert wird, was zu einer Änderung der Spulenimpedanz führt.
Wenn auf der Gussoberfläche Defekte vorhanden sind, werden die elektrischen Eigenschaften des Wirbelstroms verzerrt, um das Vorhandensein von Defekten zu erkennen. Die Hauptnachteile der Wirbelstromprüfung bestehen darin, dass sie die Größe und Form der erkannten Fehler nicht direkt anzeigen kann. Im Allgemeinen kann es nur die Oberflächenposition und -tiefe der Defekte bestimmen. Darüber hinaus ist seine Empfindlichkeit für die Prüfung kleiner Öffnungsfehler auf der Gussoberfläche nicht so empfindlich wie die Eindringprüfung.
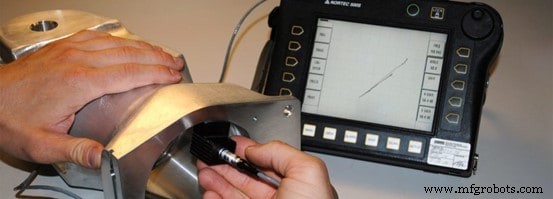
Magnetpulverprüfung
Die Magnetpulverprüfung eignet sich zur Prüfung von Oberflächenfehlern und Fehlern mehrere Millimeter tief unter der Oberfläche. Zum Testen sind DC- (oder AC-)Magnetisierungsgeräte und Magnetpartikel (oder magnetische Suspensionsflüssigkeit) erforderlich.
Magnetisierungsgeräte werden verwendet, um ein Magnetfeld auf den Innen- und Außenflächen des Gussstücks zu erzeugen, und Magnetpartikel oder Magnetsuspensionsflüssigkeit werden verwendet, um Fehler aufzudecken. Wenn innerhalb eines bestimmten Bereichs des Gussstücks ein Magnetfeld erzeugt wird, erzeugen die Defekte im magnetisierten Bereich ein magnetisches Streufeld. Wenn das magnetische Teilchen oder die Suspensionsflüssigkeit versprüht wird, wird das magnetische Teilchen angezogen, so dass die Defekte angezeigt werden können.
Die bei der Magnetpulverprüfung aufgedeckten Fehler sind im Wesentlichen solche, die die magnetische Kraftlinie queren, aber die langen Streifenfehler parallel zur magnetischen Kraftlinie können nicht angezeigt werden. Daher ist es notwendig, die Magnetisierungsrichtung während des Betriebs ständig zu ändern, um sicherzustellen, dass jeder Fehler in der unbekannten Richtung getestet werden kann.
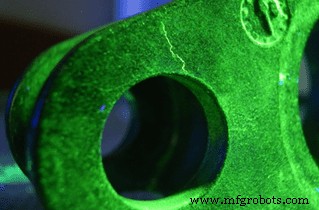
Prüfung innerer Gussfehler
Bei inneren Defekten sind die üblicherweise verwendeten zerstörungsfreien Prüfverfahren die Durchstrahlungsprüfung und die Ultraschallprüfung. Unter ihnen ist die Wirkung der Röntgenprüfung am besten. Es kann ein intuitives Bild erhalten, das die Art, Form, Größe und Verteilung von inneren Defekten widerspiegelt. Bei dickeren großen Gussteilen ist jedoch die Ultraschallprüfung sehr effektiv, die den Ort, die äquivalente Größe und die Verteilung von inneren Defekten genau messen kann.
Durchstrahlungsprüfung
Durchstrahlungsprüfungen, im Allgemeinen Röntgen- oder γ-Strahlen, als Strahlenquelle, Strahlenerzeugungsausrüstung und andere Hilfseinrichtungen werden benötigt. Wenn das Gussstück dem Strahlenfeld ausgesetzt wird, wird die Strahlungsintensität des Strahls durch die inneren Defekte des Gussstücks beeinflusst. Die durch das Gussstück emittierte Strahlungsintensität variiert lokal mit der Größe und Art der Defekte, wodurch ein Röntgenbild der Defekte entsteht, das mit einem Röntgenfilm abgebildet und aufgezeichnet wird.
Das Aufzeichnungsverfahren durch radiografische Filmabbildung ist das am häufigsten verwendete Verfahren, das allgemein als radiografische Prüfung bezeichnet wird. Das von der Radiographie reflektierte Defektbild ist intuitiv, und Form, Größe, Menge, Ebenenposition und Verteilungsbereich von Defekten können dargestellt werden.
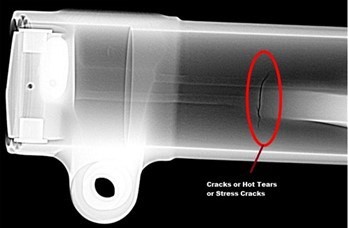
Ultraschallprüfung
Die Ultraschallprüfung nutzt die Ausbreitung von Schallstrahlen mit hochfrequenter Schallenergie innerhalb des Gussteils, um Reflexionen zu erzeugen, wenn sie auf die Innenflächen oder Defekte treffen. Die Größe der reflektierten akustischen Energie ist eine Funktion der Richtwirkung und der Eigenschaften der inneren Oberflächen oder Defekte und der akustischen Impedanz eines solchen Reflektors. Die von verschiedenen Defekten oder inneren Oberflächen reflektierte Schallenergie kann somit angewendet werden, um die Position der Defekte, die Wanddicke oder die Tiefe der Defekte unter der Oberfläche zu erkennen.
Als weit verbreitetes zerstörungsfreies Prüfverfahren bietet die Ultraschallprüfung die wichtigsten Vorteile:hohe Prüfempfindlichkeit, mit der kleine Risse geprüft werden können; große Durchdringungsfähigkeit, die dicke Gussteile erkennen kann. Seine Hauptbeschränkungen sind:schwer zu interpretierende Reflexionswellenformen für diskontinuierliche Defekte mit komplexen Konturabmessungen und schlechter Richtwirkung; Auch unerwünschte innere Strukturen wie Korngröße, Mikrostruktur, Porosität, Einschlussgehalt oder fein verteilte Ausscheidungen erschweren die Interpretation der Wellenform.
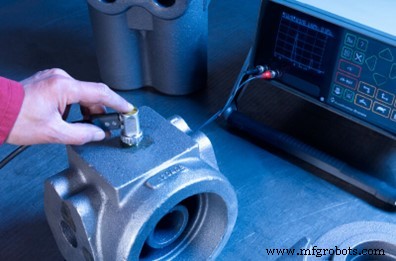
Industrietechnik
- Verbesserung von Qualität und Sicherheit bei der Produktrückverfolgbarkeit
- 4 Gründe, warum Gerätetests und -inspektionen wichtig sind
- Was ist Schweißnahtqualitätsprüfung? - 10 häufige Schweißnahtfehler
- Leitfaden für PCB-Testmethoden
- Einführung in NDT (zerstörungsfreie Prüfung) für Gussteile
- Die Grundlagen der Qualitätskontrolle und Inspektion in der CNC-Bearbeitung
- Rotations-Flächenschleifer und Verarbeitungsqualität
- PCB Testing:Ein Fokus auf In-Circuit und Functional Testing
- Spezialisierte Methoden des Innenschleifens
- Wissenswertes:Robotic Part Testing and Inspection