Die 6 teuersten Lagerfehler (und wie man sie vermeidet)
Lager bleiben eine entscheidende Komponente globaler Lieferkettennetzwerke, da die Verbraucher schnellere Lieferungen erwarten. Die Einrichtung eines Lagers erfordert eine sorgfältige Planung, und mehrere einzigartige Systeme müssen mit Ausrüstung und Software integriert werden. Darüber hinaus erfordert die hohe Priorität, die einem schnellen Umsatz und einer genauen, schnellen Auftragserfüllung beigemessen wird, dass das Management alle Engpässe beseitigt, die zu Verzögerungen führen können.
In diesem Beitrag untersuchen wir sechs kostspielige Lagerfehler und wie Sie sie vermeiden können. Diese häufigen Fehler können während der Planungsphase eines Lagerprojekts leicht übersehen werden. Aber wie wir noch besprechen werden, können viele dieser Probleme zu Störungen im Lager führen und erfordern kostspielige Lösungen, um sie zu beheben. Wenn Sie diese Fehler verstehen, können Sie ähnliche Schwierigkeiten bei Ihren Lagereinrichtungs- und Verbesserungsprojekten vermeiden.
1. Ein schlechtes Lagerlayout

Das Layout eines Lagers legt den gesamten Rahmen dafür fest, wie die Arbeit in der gesamten Einrichtung ausgeführt wird. Es ist von entscheidender Bedeutung, von Anfang an ein optimiertes Design zu erstellen, da es schwierig sein kann, Änderungen vorzunehmen, nachdem Regale, Regale und Geräte installiert wurden. Neben der Wahl eines effizienten Layouts ist es auch wichtig, häufige Fehler zu vermeiden, die später zu Problemen führen können. Zu den häufigsten Lagerlayoutfehlern gehören:
- Überlappende Versand- und Empfangsbereiche
- Keine Räume für Produktrückgaben und Überbestände schaffen
- Wege und Arbeitsbereiche zu klein gestalten
- Versagen bei der Aufrechterhaltung sauberer und ordentlicher Lagerarbeitsplätze
Ein organisiertes Lager sollte klar gekennzeichnete und dedizierte Zonen für verschiedene Arten von Arbeiten und ausgewiesene Fahrwege für Personen, Gabelstapler und andere mobile Geräte haben. Benutzerdefinierte Lagerschilder wie Lagergangschilder, Tür- und Dockschilder für den Innenbereich, Tür- und Dockschilder für den Außenbereich sowie Lagersicherheitsschilder bieten Richtungshinweise und helfen den Arbeitern, die verschiedenen Bereiche des Lagers für eine einfache Navigation zu identifizieren. Lagerbeschilderungslösungen vermitteln wichtige Informationen, um den reibungslosen Verkehrsfluss zu gewährleisten. Ein optimaler Verkehrsfluss verbessert nicht nur die Produktivität, sondern erhöht auch die Lagersicherheit.
2. Ungenaue Prognosen
Selbst das effizienteste Lager kann den Bestand ohne genaue Prognosen nicht verwalten. Dies umfasst die Planung des lokalen Inventars, der Lieferungen und der Auftragserfüllung. Mit genauen Prognosen kann das Management optimale Lagerbestände festlegen und Lagerressourcen anweisen, Arbeitsaufträge zu koordinieren. Diese Informationen sind auch bei der Durchführung von Bestandszählungen hilfreich und können dabei helfen, die Erfüllung und andere wichtige Lagerfunktionen zu rationalisieren.
3. Manuelles Tracking
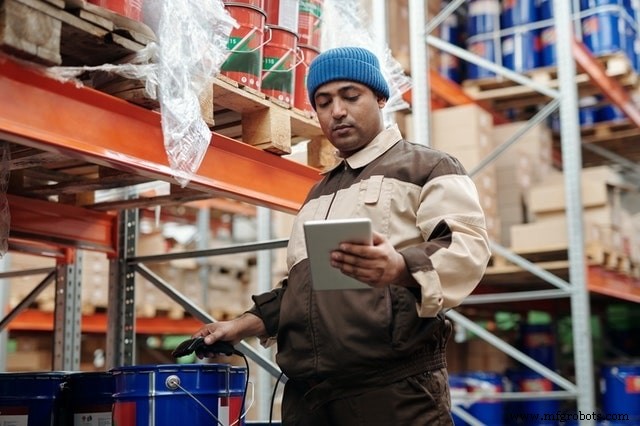
Die Lagerautomatisierungstechnologie ist wirklich zum Mainstream geworden und eine hervorragende Ressource zur Verbesserung der Arbeitsabläufe vor Ort. Die Verwendung von Verfahren, die übermäßigen Papierkram und manuelle Dateneingabe erfordern, kann erheblich Zeit und Aufwand bedeuten. Einer der wichtigsten Schritte zur Eliminierung manueller Arbeit ist die Investition in Lagerverwaltungssoftware (WMS), mit der alle kritischen Arbeitsabläufe im Lager zentralisiert werden können.
Diese Plattformen können auch mit Barcodes und Scannern integriert werden, um mehrere Lagerfunktionen wie Kommissionierung, Verpackung und Versand zu automatisieren. Ein vollständig integriertes WMS ist das Rückgrat eines gut funktionierenden Lagers und kann durch zukünftige Integrationen und Add-Ons kontinuierlich verbessert werden.
4. Kommissionierungsineffizienzen
Der Kommissionierprozess ist ein wichtiger Schwerpunktbereich für das Management und die Mitarbeiter, die mit der Auftragsabwicklung in einem Lager beauftragt sind. Viele moderne Lager verfügen über Förderbänder, Packer und andere Geräte, die den Lagerbestand bewegen, was die Kommissionierung effizienter machen kann, aber auch zu Engpässen führen kann, wenn diese Werkzeuge nicht sorgfältig in die Lagerabläufe integriert werden. Eine optimierte Kommissionierung erfordert sorgfältig geplante Transportwege und ein Layout, das den Bestandsfluss priorisiert. Es wird außerdem empfohlen, im gesamten Lager deutliche Beschilderungen und Regaletiketten anzubringen, um den Bestand leicht identifizieren zu können.
Mit einer Vielzahl von verfügbaren Lager-Barcode-Etiketten und -Schildern, wie z. Tabletts und Behältern können Sie jeden Bereich des Lagers problemlos beschriften, um ein nahtloses Scannen und Nachverfolgen zu gewährleisten und die manuelle Dateneingabe für eine verbesserte Genauigkeit zu eliminieren.
5. Alle Bestände gleichermaßen verwalten
Ein weiterer häufiger Lagerfehler besteht darin, alle Bestände gleich zu behandeln. Jedes Inventarstück kann unterschiedliche Lagerungs-, Bedarfs- und Handhabungsanforderungen haben. Bestände mit hoher Umschlagshäufigkeit sollten an Lager- und Vorwärtskommissionierungsstandorten innerhalb des Lagers gelagert werden, die für Kommissionierer und Gabelstapler leicht zugänglich sind.
Es wird auch empfohlen, Inventar mit geringerer Nachfrage außerhalb von stark frequentierten Bereichen zu lagern, um die Effizienz zu maximieren. Saisonale und verderbliche Bestände sollten sorgfältig geprüft werden, und es kann von Vorteil sein, einen rotierenden Bestandsplatzierungsplan zu haben, der das ganze Jahr über saisonale Trends nutzt. Es ist auch wichtig, den Bestand nicht so zu überlasten, dass er die Effizienz behindert. Zu viel Lagerbestand kann nicht nur die Raumnutzung zu einer erheblichen Herausforderung machen, sondern erhöht auch Ihre Gemeinkosten – insbesondere, wenn Sie über lange Zeit Überbestände halten.
6. Kurzfristige Planung
Sich nicht auf die Zukunft vorzubereiten, ist ein großes Risiko für jedes Unternehmen. Es ist unmöglich, jeden Branchen- oder Kundentrend zu berücksichtigen, aber eine langfristige Planung kann sehr hilfreich sein. Zukünftiges Wachstum kann erhebliche Investitionen in neue Ausrüstung, Systeme und Automatisierungstechnologie erfordern. Das Erstellen eines formellen Plans gibt Ihnen einen Schwerpunkt und eine Basislinie, die regelmäßig überprüft und aktualisiert werden kann, um die neuesten verfügbaren Informationen widerzuspiegeln. Diese Überprüfungszeiträume eignen sich auch hervorragend, um Feedback von Mitarbeitern darüber zu sammeln, was gut funktioniert und wo Verbesserungen erforderlich sein könnten.
Moderne Lager haben bewiesen, dass ein effizientes Layout, eine ordnungsgemäße Planung und die Einhaltung der Best Practices der Branche kombiniert werden können, um ein qualitativ hochwertiges Fulfillment-Center zu schaffen. Die Lagerverwaltung und andere Mitarbeiter sollten auf häufige Fehler achten, die oft durch sorgfältige Planung in den frühen Phasen einer Lagereinrichtung oder -umgestaltung überwunden werden können. Das Vermeiden dieser Fehler gibt Ihrem gesamten Team mehr Energie, die es für wertschöpfende Arbeit aufwenden und einen effizienten Betrieb schaffen kann.
Industrietechnik
- 6 Risiken beim Export von Fertigwaren – und wie man sie vermeidet
- Sechs gängige Logistikfehler und wie man sie vermeidet
- Drei Fallstricke bei der Zustellung auf der letzten Meile – und wie man sie vermeidet
- Sieben häufige Versandfehler und wie man sie vermeidet
- So holen Sie das Beste aus Ihrem Lager-Scansystem heraus
- 4 Hauptursachen für Schaltanlagenausfälle und wie man sie vermeidet
- Was ist Pumpenkavitation und wie vermeide ich sie?
- 3 Hauptlagerprozesse (und wie man sie verbessert)
- 5 häufige Kranichgefahren und wie man sie vermeidet
- Wie Bremsen funktionieren, welche Arten von Industriebremsen es gibt und wie man sie optimal nutzt