Design-Spotlight:Anpassung von Additiven an Spritzguss
Als die COVID-19-Pandemie die Vereinigten Staaten heimsuchte, verlagerte unser Team bei Fast Radius schnell einen erheblichen Teil unserer additiven Fertigungskapazitäten auf die Herstellung von Gesichtsschutzschilden. Bis heute haben wir Tausende von additiv gefertigten Gesichtsschutzschilden hergestellt und versendet, um Mitarbeiter an vorderster Front vor dem Coronavirus zu schützen. Der Schild ist wiederverwendbar, extrem langlebig, einfach zu montieren und komfortabel, aber die Nachfrage hat unsere Kapazitäten für die additive Produktion bei weitem überschritten.

Um unser Produkt mehr Menschen zugänglich zu machen, haben wir uns entschieden, die Produktion auf Spritzguss umzustellen. Das Spritzgießen macht den Schild in zweierlei Hinsicht zugänglicher; Es ermöglicht uns, ein viel höheres Volumen zu produzieren, und das Spritzgießen senkt die Kosten des Produkts aufgrund der geringeren Materialkosten und der schnelleren Herstellung erheblich.
In unserer Arbeit mit Kunden verwenden wir häufig additive Technologien zur Herstellung von Teilen, während wir zur Spritzgussproduktion übergehen. Unsere eigene Geschichte ist ein starkes Beispiel dafür, wie man digitale Fertigungstechnologie nutzt, um ein additives Produkt für den Spritzguss neu zu gestalten.
Schnelle Designiteration mit Simulationstools
Wir mussten erhebliche Änderungen am additiven Design des Schild-„Halo“ (oder Stirnbands) vornehmen, um es für den Spritzguss geeignet zu machen und gleichzeitig seine Leistung beizubehalten. Wir wussten, dass die Steifigkeit optimiert werden musste, um dünne Stahlbedingungen zu reduzieren, die während des Formvorgangs zu Werkzeugschäden führen könnten. Da wir wussten, dass die Steifheit des aktuellen Halo gut funktionierte, simulierten wir die fluktuierende Verschiebung des additiven Halo und verwendeten diese Verschiebung als Ziel für die Steifheit des spritzgegossenen Designs.
Um die Elemente zu verstehen, die zur Steifigkeit beitragen, haben wir die Finite-Elemente-Analyse (FEA) verwendet, um die Konstruktionsvariablen zu lokalisieren, die bessere Ergebnisse erzielten. Wir haben uns auf das Simulationspaket in Autodesk 360 verlassen, ein Tool, das wir für eine Vielzahl von Zwecken verwenden, einschließlich Design, Analyse und Simulation. Wir haben sowohl das Kronen- als auch das Rippenmuster auf der Vorderseite des Außenrings getestet. Während die Riffelung etwas Steifheit hinzufügte, fanden wir heraus, dass das Erhöhen der Krone eine effektivere Methode war, um die Verschiebung zu minimieren.
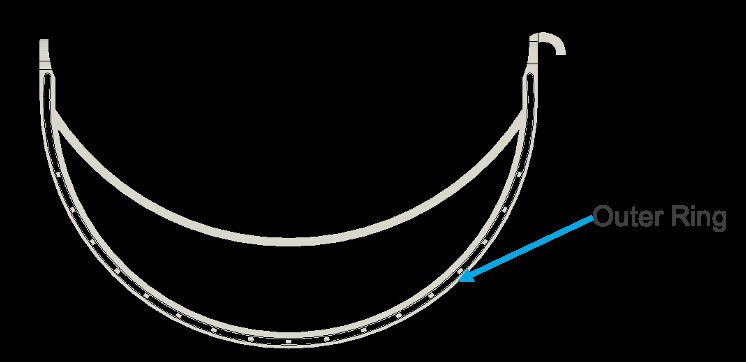
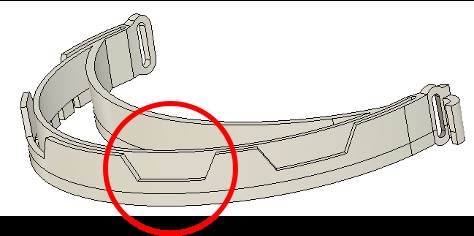
Das Hinzufügen von Höhe zur Krone könnte jedoch schlechte Werkzeugbedingungen (dünner Werkzeugstahl) zwischen dem äußeren und dem mittleren Ring schaffen. Der Schlitz, in den die Abschirmung selbst eingesetzt wird, ist sehr dünn – so dünn wie ein bis zwei Millimeter; Je höher die Abschnitte in der Krone, desto dünnerer Stahl würde für das Werkzeug benötigt, was die Wahrscheinlichkeit erhöht, dass der Werkzeugstahl während des Formvorgangs beschädigt wird.
Wir mussten die optimale Kronenhöhe finden, die dünnen Stahl reduziert und gleichzeitig die Steifigkeit im äußeren Ring des Halo bewahrt. Um dies festzustellen, führten wir 16 Simulationen durch und passten das Design jedes Mal leicht an, um die Leistung zu verbessern. In diesem Stadium des Designprozesses hatten wir unser Ziel bereits erreicht und hatten viele Designs mit ähnlicher oder besserer Verschiebung als der additive Halo.
Schnelles Prototyping mit HP Multi Jet Fusion (MJF)
Aus den von uns simulierten Konzepten haben wir drei für den Druck mit HP MJF ausgewählt, da dies die Technologie ist, mit der wir unseren ursprünglichen additiven Halo hergestellt haben. Normalerweise dauert es drei Tage, bis ein MJF-Teil ausreichend abgekühlt ist, um verwendet werden zu können, aber unser Team von Fertigungsingenieuren hat den Bau so verpackt, dass wir unsere Teile am nächsten Tag zur Hand haben konnten.
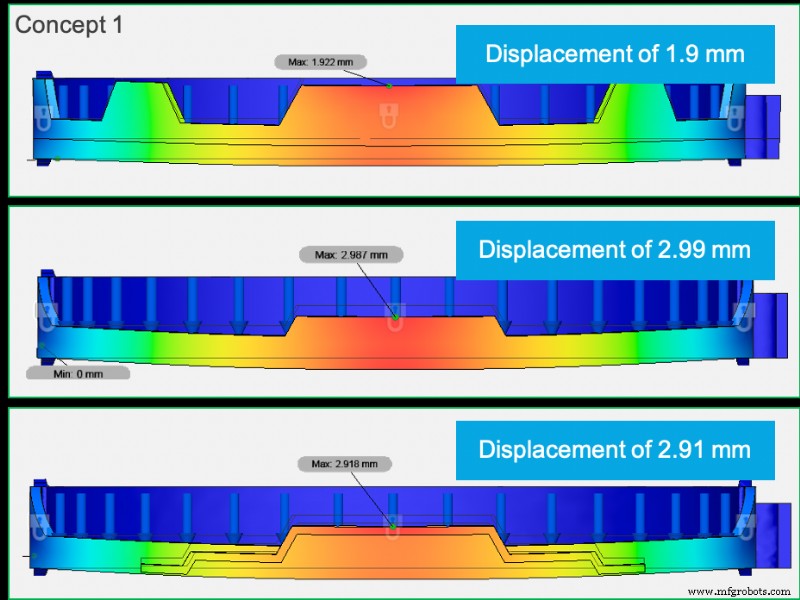
Das Betriebsteam der Fabrik von Fast Radius in Chicago trug die drei Konzepthalos und verglich sie mit der additiv gefertigten Originalversion, um Komfort und einfache Montage zu vergleichen. Konzept 10 (siehe oben, drittes Design) akzeptierte den Schild am einfachsten, aber sie schlugen mehrere Modifikationen vor, um den Komfort zu verbessern und die Montage zu erleichtern. Das resultierende Design (siehe unten) wurde verwendet, um das Spritzgusswerkzeug herzustellen, das die nächste Version unseres Gesichtsschutzschildes Halo herstellen wird.

Letztendlich wird der Wechsel von der additiven Fertigung zum Spritzguss den Halo für diejenigen, die ihn brauchen, viel zugänglicher machen. Wir konnten den Preis um 55 % senken.
Als wir anfingen, additive Lichthöfe herzustellen, erfüllten wir eine Nachfrage, die wir nicht vorhersagen konnten. Als klar wurde, dass wir unser Produkt zugänglicher machen konnten, modifizierten wir unser additives Design für den Spritzguss und brachten ein Werkzeug in nur drei Tagen in Produktion.
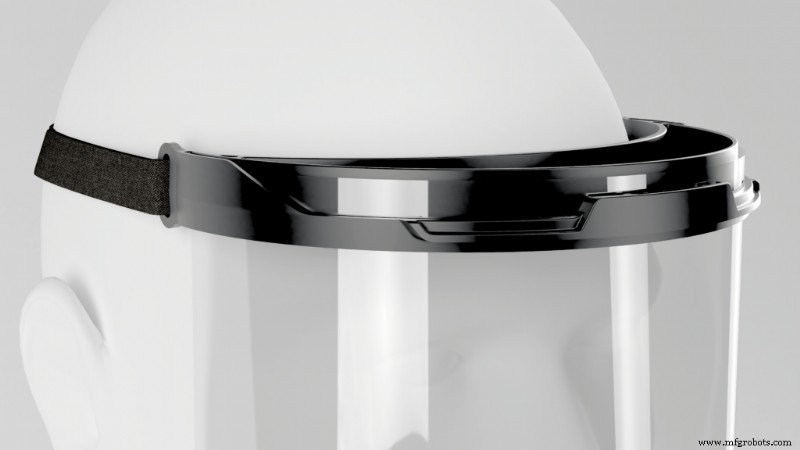
Unser Team arbeitete rund um die Uhr, um dieses wichtige Produkt auf den Markt zu bringen. Wir haben diesen bemerkenswerten Zeitplan zum großen Teil dank Simulationssoftware, digitaler Fertigung und unserem agilen Arbeitsmodell erreicht. Diese Pandemie hat uns gezwungen, bei den Produktentwicklungszyklen flexibler zu werden, ein Trend, von dem wir glauben, dass er noch lange nach der Pandemie anhalten wird.
Sind Sie bereit, Ihre Teile mit Fast Radius herzustellen?
Starten Sie Ihr AngebotIndustrietechnik
- Was ist Reaktionsspritzguss
- Guss vs. Spritzguss
- Thermoformen vs. Reaktionsspritzgießen (RIM)
- Spritzguss vs. Reaktionsspritzguss (RIM)
- Gießformen vs. Reaktionsspritzgießen
- Designtipps für Gussformen
- Design-Services von Protocase:6 Tipps
- Design von Spritzgießanschnitten:Ein ultimativer Leitfaden für die Kunststoffherstellung
- Aluminium-Spritzguss in der Produktherstellung
- Entformungswinkel für Spritzguss:Konstruktionsleitfaden und Best Practices