9 Einheit 4:Drehen
ZIEL
Nach Abschluss dieser Einheit sollten Sie in der Lage sein:
• Beschreiben Sie das Schrupp- und Schlichtdrehen.
• Beschreiben Sie den Wendestreifen.
• Beschreiben Sie den Falzschnitt.
• Erklären Sie, wie Sie für Zentrier-/Punktbohrer einrichten.
• Erklären Sie, wie Sie das Bohren einrichten.
• Erklären Sie, wie Sie das Rändeln einrichten.
• Korrektes Einrichten eines Werkstücks zum Abstechen/Einstechen.
• Bestimmen Sie die Verjüngungsberechnung.
• Werkstück in einem 4-Backenfutter richtig aufspannen.
Das Werkstück wird im Allgemeinen aus zwei Gründen auf einer Drehmaschine bearbeitet:um es auf Maß zu schneiden und um einen echten Durchmesser zu erzeugen. Bei Werkstücken, die auf Maß geschnitten werden müssen und über die gesamte Länge des Werkstücks den gleichen Durchmesser haben müssen, wird parallel gedreht. Viele Faktoren bestimmen die Materialmenge, die auf einer Drehmaschine abgetragen werden kann. Ein Durchmesser soll in zwei Schnitten zugeschnitten werden:einem Schruppschnitt und einem Schlichtschnitt.
Um den gleichen Durchmesser an jedem Ende des Werkstücks zu haben, müssen die Drehmaschinenspitzen in einer Linie liegen.
Um eine genaue Schnittiefe einzustellen
Verfahren:
1. Stellen Sie die zusammengesetzte Ruhe auf 30 Grad ein.
2. Bringen Sie ein Schrupp- oder Schlichtwerkzeug an. Verwenden Sie ein Rechtsdrehwerkzeug, wenn Sie den Sattel in Richtung Spindelstock schieben.
3. Bewegen Sie den Werkzeughalter auf die linke Seite der zusammengesetzten Auflage und stellen Sie den Werkzeugeinsatz auf die rechte Höhenmitte ein.
4. Stellen Sie die Drehmaschine auf die richtige Geschwindigkeit und den richtigen Vorschub für den Durchmesser und die Art des zu schneidenden Materials ein.
5. Starten Sie die Drehmaschine und nehmen Sie einen leichten Schnitt von etwa 0,005 Zoll und 0,250 Zoll Länge am rechten Ende des Werkstücks vor.
6. Stoppen Sie die Drehmaschine, aber bewegen Sie nicht den Griff der Quervorschubschraube.
7. Bewegen Sie das Schneidwerkzeug zum Ende des Werkstücks (nach rechts), indem Sie das Handrad des Schlittens drehen.
8. Messen Sie die Arbeit und berechnen Sie die Menge des zu entfernenden Materials.
9. Drehen Sie den Skalenring um die Hälfte des abzutragenden Materials. Wenn beispielsweise 0,060 Zoll entfernt werden sollen, sollte der Skalenbund auf 0,030 Zoll gedreht werden, da der Schnitt vom Umfang des Werkstücks abgenommen wird.
10. Denken Sie daran , für jede tausendste Schnitttiefe verringert sich der Schaftdurchmesser um zwei Tausendstel.
Grobdrehen
Die Operation Schruppdrehen dient dazu, möglichst viel Metall in kürzester Zeit abzutragen. Genauigkeit und Oberflächenbeschaffenheit sind bei diesem Vorgang nicht wichtig. Daher wird eine maximale Tiefe von 0,030 Zoll und ein Vorschub von 0,020 bis 0,030 Zoll empfohlen. Das Werkstück wird im Allgemeinen in so wenigen Schnitten wie möglich auf etwa 0,030 Zoll der fertigen Größe vorgedreht.
Verfahren:
1. Stellen Sie die Drehmaschine auf die richtige Geschwindigkeit und Vorschubrate für die Art und Größe des zu schneidenden Materials ein.
2. Stellen Sie das Schnellwechselgetriebe auf einen Vorschub von 0,010 bis 0,030 Zoll ein, je nach Schnitttiefe und Zustand der Maschine.
3. Zum Beispiel:.010
4. Bewegen Sie den Werkzeughalter auf die linke Seite der zusammengesetzten Auflage und stellen Sie den Werkzeugeinsatz auf die richtige Höhe zur Mitte ein.
5. Ziehen Sie den Werkzeughalter sicher fest, um zu verhindern, dass sich der Werkzeughalter während des Bearbeitungsvorgangs bewegt.
6. Führen Sie am rechten Ende des Werkstücks einen leichten Probeschnitt auf einer Länge von etwa 0,250 Zoll durch.
7. Messen Sie das Werkstück und stellen Sie den Werkzeugeinsatz auf die richtige Schnittiefe ein.
8. Schneiden Sie etwa 0,250 Zoll entlang, stoppen Sie die Drehmaschine und überprüfen Sie den Durchmesser auf Größe. Der Durchmesser sollte etwa 0,030 Zoll über der fertigen Seite liegen.
9. Stellen Sie ggf. die Schnitttiefe neu ein.
Drehen beenden
Enddrehen auf einer Drehbank, die dem Schruppdrehen folgt, erzeugt eine glatte Oberflächengüte und schneidet das Werkstück auf eine genaue Größe. Faktoren wie der Zustand des Schneidwerkzeugeinsatzes, die Steifigkeit der Maschine und des Werkstücks sowie die Drehzahl und der Vorschub der Drehmaschine können die Art der erzeugten Oberflächengüte beeinflussen.
Verfahren:
1. Überprüfen Sie, ob die Schneidkante des Werkzeug-Bits frei von Kerben, Brandstellen usw. ist. Es ist eine gute Praxis, die Schneidkante zu richten, bevor Sie einen Endschnitt vornehmen.
2. Stellen Sie die Drehmaschine auf die empfohlene Geschwindigkeit und den empfohlenen Vorschub ein. Die verwendete Vorschubgeschwindigkeit hängt von der erforderlichen Oberflächengüte ab.
3. Führen Sie am rechten Ende des Werkstücks einen leichten Probeschnitt von etwa 0,250 Zoll Länge durch, um einen wahren Durchmesser zu erzeugen, stellen Sie den Schneidwerkzeugeinsatz auf den Durchmesser ein und stellen Sie den abgestuften Kragen auf den richtigen Durchmesser ein.
4. Stoppen Sie die Drehmaschine, messen Sie den Durchmesser.
5. Stellen Sie die Schnitttiefe auf die Hälfte des abzutragenden Materials ein.
6. Schneiden Sie 0,250 Zoll entlang, stoppen Sie die Drehmaschine und prüfen Sie den Durchmesser.
7. Stellen Sie ggf. die Schnitttiefe neu ein und drehen Sie den Durchmesser fertig. Um einen möglichst genauen Durchmesser herzustellen, Werkstück auf die erforderliche Größe fertigdrehen. Sollte es notwendig sein, einen Durchmesser durch Filmen oder Polieren fertigzustellen, lassen Sie für diesen Vorgang niemals mehr als 0,002 bis 0,003 Zoll übrig.
Zur Schulter wenden
Beim Drehen von mehr als einem Durchmesser an einem Werkstück. Die Änderung des Durchmessers oder der Stufe wird als Schulter bezeichnet.
Drei gängige Schultertypen:
1. Quadrat
2. Abgerundete Ecke
3. Eckig oder verjüngt
Verfahren:
1. Legen Sie bei einem in einer Drehmaschine montierten Werkstück die Schulterposition vom fertigen Ende des Werkstücks aus. Im Fall von abgerundeten Schultern, alle ausreichend lang, damit der richtige Radius auf der fertigen Schulter geformt werden kann.
2. Platzieren Sie die Spitze des Werkzeugeinsatzes an dieser Markierung und schneiden Sie eine kleine Nut um den Umfang, um die Länge zu markieren.
3. Drehen Sie das Werkstück mit einem Drehmeißel um ca. 0,063 Zoll der erforderlichen Länge vor und fertig.
4. Richten Sie ein Stirnseitenbearbeitungswerkzeug ein. Kreiden Sie den kleinen Durchmesser des Werkstücks und bringen Sie das Schneidwerkzeug nach oben, bis es gerade die Kreidemarkierung entfernt.
5. Notieren Sie den Messwert auf dem abgestuften Kragen des Quertransportgriffs.
6. Richten Sie sich auf die Schulter aus und schneiden Sie mit dem Handvorschub auf die Linie.
7. Stellen Sie für aufeinanderfolgende Schnitte den Quervorschubgriff auf die gleiche abgestufte Krageneinstellung zurück.
Wenn eine abgerundete Ecke erforderlich ist, wird ein Werkzeugbit mit dem gleichen Radius zum Schlichten der Schulter verwendet. Eckige oder abgefaste Kanten können erhalten werden, indem die Schneidkante des Werkzeugeinsatzes auf den gewünschten Abfasungswinkel eingestellt und gegen die Schulter geführt wird, oder indem die zusammengesetzte Auflage auf den gewünschten Winkel eingestellt wird.
Gesicht
Zu bearbeitende Werkstücke werden in der Regel etwas länger als nötig geschnitten und auf die richtige Länge plangedreht. Das Planen ist ein Arbeitsgang, bei dem die Enden eines Werkstücks rechtwinklig zu seiner Achse bearbeitet werden. Um beim Planen eine flache, rechtwinklige Oberfläche zu erzeugen, könnte die Drehbank stimmen.
Der Zweck der Gegenüberstellung ist:
• Um eine echte, flache Oberfläche bereitzustellen, rechtwinklig zur Achse der Werkstücke.
• Zur Bereitstellung einer genauen Oberfläche, von der Messungen durchgeführt werden können.
• Um die Werkstücke auf die erforderliche Länge zu schneiden.
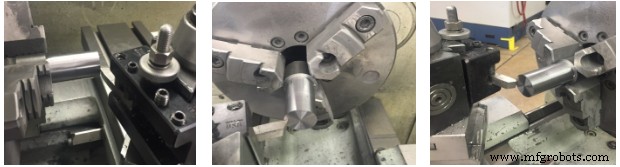
Abbildung 1. Facing Operation
Verfahren:
1. Bewegen Sie den Werkzeughalter auf die linke Seite der zusammengesetzten Auflage und stellen Sie den rechten Werkzeugeinsatz auf die rechte Höhe des Mittelpunkts der Drehmaschine ein. Die zusammengesetzte Auflage kann für eine genaue Endbearbeitung auf 30 Grad eingestellt werden.
2. Spannen Sie das Werkstück stirnseitig in das Spannfutter ein. Verwenden Sie bei Bedarf eine Linie in der Mitte des Endstücks oder ein gerades Lineal, um es wahr zu machen.
3. Setzen Sie ein Plandrehwerkzeug ein.
4. Positionieren Sie das Werkzeug leicht vom Teil entfernt.
5. Richten Sie das Plandrehwerkzeug in einem Winkel von 15-20 Grad nach links aus. Die Spitze des Werkzeugeinsatzes muss dem Werkstück am nächsten sein und seitlich muss Platz gelassen werden.
6. Stellen Sie die Drehmaschine auf die richtige Geschwindigkeit und den richtigen Vorschub für den Durchmesser und die Art des zu schneidenden Materials ein.
7. Bevor Sie die Maschine einschalten, drehen Sie die Spindel von Hand, um sicherzustellen, dass keine Teile die Spindeldrehung behindern.
8. Starten Sie die Drehmaschine und bringen Sie den Werkzeugeinsatz so nah wie möglich an die Mitte der Drehmaschine.
9. Bewegen Sie den Schlitten mit dem Handrad nach links, bis der kleine Schnitt beginnt.
10. Führen Sie den Schneidwerkzeugeinsatz nach innen zur Mitte, indem Sie den Quervorschubgriff drehen. Wenn der Kraftvorschub-Quervorschub zum Vorschub des Schneidwerkzeugs verwendet wird, sollte der Schlitten in Position arretiert werden.
11. Wiederholen Sie die Schritte 6, 7 und 8, bis das Werkstück auf die richtige Länge geschnitten ist. 12. Nach dem Planen entsteht am Werkstück eine scharfe Kante, die mit einer Feile gebrochen werden sollte.
Um ein Werkstück zu erkennen
Spotting Tool Bit wird verwendet, um ein flaches, V-förmiges Loch in der Mitte des Werkstücks zu machen. Bietet eine Anleitung für die zu befolgende Übung. Ein Loch kann schnell und ziemlich genau mit einem Zentrierbohrer entdeckt werden. Für extreme Genauigkeit sollte ein Spotting-Tool-Bit verwendet werden.
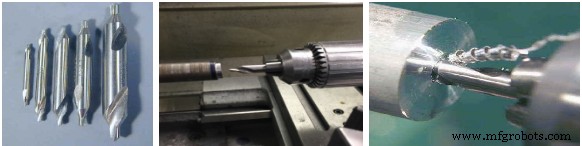
Abbildung 2: Center/Spot Tool
Verfahren:
1. Werkstück fluchtend in ein Futter einspannen.
2. Montieren Sie das Bohrfutter in den Reitstock.
3. Stellen Sie sicher, dass die Angel des Bohrfutters richtig im Reitstock befestigt ist.
4. Bewegen und verriegeln Sie den Reitstock in die gewünschte Position.
5. Bevor Sie die Maschine einschalten, drehen Sie die Spindel von Hand, um sicherzustellen, dass keine Teile die Spindeldrehung behindern.
6. Stellen Sie die Drehmaschine auf die richtige Drehzahl für die Art des anzubohrenden Materials ein.
7. Beginnen Sie das Loch mit einem Zentrierbohrer. 8. Bohren Sie das Loch mit einem Anbohr- oder Zentrierbohrer an.
Bohren
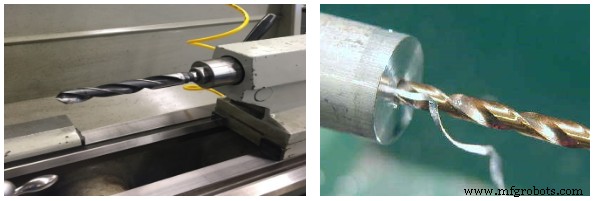
Abbildung 3. Bohrer
Verfahren:
1. Montieren Sie das Bohrfutter in den Reitstock.
2. Werkstück fluchtend in ein Futter einspannen.
3. Überprüfen Sie die Werkzeugmitte und vergewissern Sie sich, dass sie ausgerichtet ist.
4. Stellen Sie sicher, dass die Angel des Bohrfutters richtig im Reitstock befestigt ist.
5. Bewegen und verriegeln Sie den Reitstock in die gewünschte Position.
6. Bevor Sie die Maschine einschalten, drehen Sie die Spindel von Hand, um sicherzustellen, dass keine Teile die Spindeldrehung behindern.
7. Beginnen Sie das Loch mit einem Spotting- oder Zentrierbohrereinsatz.
8. Verwenden Sie bei Verwendung eines Zentrierbohrers immer Schneidflüssigkeit.
9. Ein Zentrierbohrer schneidet nicht so leicht wie ein Bohrer, da er flache Rillen für zusätzliche Steifigkeit hat.
10. Bohren Sie über die gesamte Verjüngung hinaus, um einen Trichter zum Einführen des Bohrers zu schaffen.
11. Montieren Sie den Bohrer in die Reitstockspindel, in ein Bohrfutter oder in einen Bohrerhalter.
12. Stellen Sie die Drehmaschine auf die richtige Drehzahl für das zu bohrende Material ein.
13. Starten Sie die Drehmaschine und bohren Sie gemäß der Planzeichnung bis zur gewünschten Tiefe, wobei Sie Schneidflüssigkeit auftragen.
14. Um die Tiefe des Lochs zu messen, verwenden Sie die Skalen auf der Reitstockspindel oder verwenden Sie ein Stahllineal, um die Tiefe zu messen.
15. Verwenden Sie die Lochbohroperation, um die Späne zu entfernen und die Tiefe des Lochs zu messen.
16. Nehmen Sie beim Bohren höchstens einen oder zwei Bohrerdurchmesser an Material ab, bevor Sie zurücksetzen, Späne entfernen und erneut Schneidflüssigkeit auftragen.
17. Wenn der Bohrer gegen den Schaft quietscht, mehr Schneidflüssigkeit auftragen.
18. Um das Bohrfutter vom Reitstock zu entfernen, ziehen Sie es etwa eine Vierteldrehung weiter zurück, als es leicht geht.
19. Verwenden Sie einen Stift, um das Futter aus der Spannzange zu drücken.
Langweilig
Aufbohren ist eine Operation zum genauen Vergrößern und Endbearbeiten von Löchern. Abrichten eines Lochs durch Entfernen von Material von Innenflächen mit einem Einpunkt-Werkzeug-Bit-Fräser. Bohrungen mit Sonderdurchmessern, für die keine Bohrer verfügbar sind, können durch Aufbohren hergestellt werden.
Beim Bohren wird ein Einpunkt-Schneidwerkzeug verwendet, um ein Loch zu vergrößern. Dieser Vorgang sorgt im Gegensatz zum Bohren für ein genaueres und konzentrischeres Loch.
Da sich der Fräser von einer Bohrstange aus der Maschine erstreckt, wird das Werkzeug nicht so gut gestützt, was zu Rattern führen kann. Je tiefer die Bohroperation, desto schlimmer das Geschwätz. Um dies zu korrigieren:
1. Reduzieren Sie die Spindeldrehzahl.
2. Erhöhen Sie den Vorschub.
3. Mehr Schneidflüssigkeit auftragen.
4. Kürzen Sie den Überhang der Bohrstange.
5. Schleifen Sie einen kleineren Radius an der Werkzeugspitze.
Verfahren:
1. Spannen Sie das Werkstück in ein Spannfutter ein.
2. Planen, anpeilen und bohren Sie das Loch auf dem Werkstück.
3. Prüfen Sie, ob die Bohrstange genügend Spiel hat.
- Wenn das Loch zu klein für die Bohrstange ist, verklemmen sich die Späne während der Bearbeitung und verschieben die Stange aus der Mitte.
4. Stellen Sie sicher, dass die Spitze des Bohrwerkzeugs der einzige Teil des Fräsers ist, der die Innenfläche des Werkstücks berührt.
5. Wenn der Winkel keine ausreichende Entlastung am Ende bietet, ersetzen Sie den Fräser durch einen mit einem schärferen Winkel.
6. Positionieren Sie die Bohrstange so, dass die Spitze des Fräsers mit der Mittellinie des Schafts positioniert ist.
7. Ein Werkzeug, das nicht in einer Linie mit der Mitte des Werkstücks platziert ist, schleift an der Werkstückoberfläche entlang, selbst wenn ein ausreichender Endfreiwinkel vorhanden ist.
8. Wählen Sie eine Bohrstange so groß wie möglich und lassen Sie sie nur so weit über den Halter hinausragen, dass sie die Tiefe des zu bohrenden Lochs freigibt.
9. Montieren Sie den Halter und die Bohrwerkzeugstange mit dem Schneidwerkzeugeinsatz auf der linken Seite des Werkzeughalters und drehen Sie das Werkstück.
10. Stellen Sie das Bohrwerkzeug auf die Mitte ein.
- Hinweis:Abhängig von der Steifigkeit des Aufbaus neigt der Bohrwerkzeugeinsatz dazu, nach unten zu springen, wenn Druck auf die Schneidkante ausgeübt wird. Indem der Bohrmeißel etwas über der Mitte eingestellt wird, wurde die nach unten gerichtete Feder kompensiert und der Werkzeugmeißel wird während des Bearbeitungsvorgangs tatsächlich genau in der Mitte des Werkstücks positioniert.
11. Stellen Sie die Drehmaschine auf die richtige Schnittgeschwindigkeit und den richtigen Vorschub ein. a. Hinweis:Wählen Sie als Vorschub einen mittleren Vorschub aus.
12. Tragen Sie Schmiermittel auf das Loch auf, bevor Sie die Maschine einschalten.
13. Schalten Sie die Maschine ein und bewegen Sie das Werkzeug in das vorgebohrte Loch.
14. Starten Sie die Drehmaschine und bringen Sie das Bohrwerkzeug langsam dazu, bis es den Innendurchmesser des Lochs berührt.
15. Machen Sie einen leichten Schnitt (etwa 0,003 Zoll) und etwa -375 lang.
16. Stoppen Sie die Drehmaschine und messen Sie den Lochdurchmesser, verwenden Sie eine Teleskoplehre oder einen Innenmikrometer.
17. Nachdem Sie das Loch gemessen haben, bestimmen Sie die Materialmenge, die aus dem Loch entfernt werden soll. Lassen Sie etwa 0,020 in einem Endschnitt.
18. Starten Sie die Drehmaschine und nehmen Sie den Schruppschnitt vor.
19. Führen Sie die Bohrstange in das Werkstück ein und nehmen Sie bei jedem Durchgang etwa 0,020 ab.
20. Bringen Sie die Bohrstange heraus, sobald die gewünschte Tiefe erreicht ist.
21. Wiederholen Sie die Schritte 19 und 20, bis der gewünschte Durchmesser des Innenlochs erreicht ist.
22. Nachdem der Schruppschnitt abgeschlossen ist, halten Sie die Drehmaschine an und bringen Sie das Bohrwerkzeug aus dem Loch, ohne den Quervorschubgriff zu bewegen.
23. Stellen Sie die Tiefe des Fertigschnitts ein und bohren Sie das Loch auf Maß. Für eine gute Oberflächengüte wird ein feiner Vorschub empfohlen.
24. Stoppen Sie beim letzten Durchgang in der gewünschten Tiefe und bringen Sie den Fräser zurück in Richtung Schaftmitte. Dies wird zur Rückseite des Lochs zeigen.
25. Bringen Sie die Bohrstange aus der Maschine und stoppen Sie die Maschine.

Abbildung 4. Bohren auf einer Drehbank
Rändelung
1. Ein Rändel ist ein erhabener Eindruck auf der Oberfläche des Werkstücks, der durch zwei gehärtete Walzen erzeugt wird.
2. Rändelungen haben normalerweise eines von zwei Mustern:Diamant oder gerade.
3. Gängige Rändelmuster sind fein, mittel oder grob.
4. Das Rautenmuster wird durch eine rechtsgängige und eine linksgängige Spirale gebildet, die in einem selbstzentrierenden Kopf montiert sind.
5. Wird verwendet, um das Erscheinungsbild eines Teils zu verbessern und eine gute Grifffläche für Hebel und Werkzeuggriffe bereitzustellen.
6. Gängige Rändelmuster sind fein, mittel oder grob.
7. Das gerade Muster, das aus zwei geraden Rollen besteht, wird verwendet, um die Größe eines Teils für Presspassungen in leichten Anwendungen zu erhöhen.
8. Es werden drei Grundtypen von Rändelhaltern verwendet:der Kniehebelhalter, der Drehkopfhalter und der Spreizhalter.
9. Rändeln funktioniert am besten bei Werkstücken, die zwischen Spitzen montiert sind.
10. Rändelungen schneiden nicht, sondern verdrängen das Metall mit hohem Druck.
11. Schmierung ist wichtiger als Kühlung, daher reicht ein Schneidöl oder Schmieröl aus.
12. Zum Rändeln werden niedrige Geschwindigkeiten (etwa die gleichen wie beim Gewindeschneiden) und ein Vorschub von etwa 0,010 bis 0,020 Zoll verwendet.
13. Die Rändel sollten vertikal auf dem Werkstück zentriert und der Rändelwerkzeughalter rechtwinklig zum Werkstück sein.
14. Eine Rändelung sollte in weichem Metall etwa auf halber Tiefe begonnen und das Muster überprüft werden.
15. An einem schlanken Werkstück können mehrere Durchgänge erforderlich sein, um eine Rändelung fertigzustellen, da das Werkzeug dazu neigt, es von der Rändelung wegzudrücken.
16. Rändelungen sollten zwischen den Durchgängen mit einer Drahtbürste gereinigt werden.
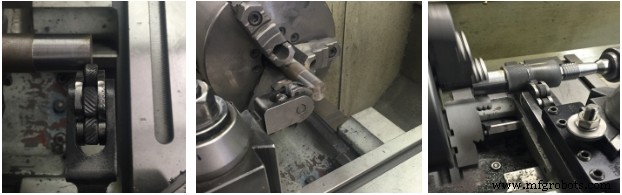
Abbildung 5. Rändelung
Verfahren:
1. Montieren Sie das Rändelwerkzeug in einen Werkzeughalter und stellen Sie es auf die exakte Mittellinie der Drehmaschinenspindel ein.
2. Positionieren und befestigen Sie das Rändelwerkzeug im 90-Grad-Winkel zur Oberfläche der Rändelung.
3. Bewegen Sie den Drehschlitten von Hand und suchen Sie den zu rändelnden Bereich auf dem Werkstück.
4. Drehen Sie den Rändelkopf, um auf die korrekt eingestellten Rändel zu indexieren.
5. Positionieren Sie die Rändelung so an der rechten Kante des Werkstücks, dass die Hälfte der Rändelung die rechte Kante des Werkstücks berührt.
6. Schneidöl auf das Werkstück auftragen.
7. Drehen Sie die Spindel auf etwa 100 U/min und bewegen Sie das Rändelwerkzeug mit dem Quervorschub-Handrad in das Werkstück. Dies sollte ungefähr 0,030 Zoll betragen oder bis die Rändelungen eine Spur bilden und ein gutes Muster bilden.
8. Aktivieren Sie den Kraftvorschub der Drehmaschine, um den Schlitten mit einer Vorschubgeschwindigkeit von 0,010 bis 0,020 Zoll pro Umdrehung zum Spindelstock zu bewegen.
9. Tragen Sie nach Bedarf Öl auf und bürsten Sie den gerändelten Bereich mit einer harten Bürste, um Späne von der Rändelung zu entfernen.
10. Wenn die Rändel das Ende des gerändelten Bereichs erreichen, kehren Sie die Vorschubrichtung des Schlittens um und führen Sie die Rändel weitere 0,005 bis 0,010 Zoll in das Werkstück ein.
11. Fahren Sie mit dem Rändeln vor und zurück fort, bis sich ein scharfer Diamant entwickelt.
Abstechen und Einstechen auf einer Drehmaschine
Zweck des Trennens und Einstechens:
Es kann vorkommen, dass Sie ein Stück vom Ende eines Werkstücks abschneiden oder eine Nut in ein Werkstück schneiden möchten.
Das Nuten, gemeinhin als Versenken, Unterschneiden oder Einschnüren bezeichnet, wird häufig am Ende eines Gewindes durchgeführt, um den vollen Lauf der Mutter bis zu einer Schulter oder am Rand einer Schulter zu ermöglichen, um einen ordnungsgemäßen Sitz der zusammenpassenden Teile sicherzustellen. Es gibt drei Arten von Rillen:quadratisch, rund und U-förmig.
Abgerundete Rillen werden normalerweise dort verwendet, wo das Teil belastet wird und wo eine rechteckige Ecke zum Brechen des Metalls führen würde.
Um eine Nut zu schneiden
Verfahren:
1. Wählen Sie einen Werkzeugeinsatz mit der gewünschten Größe und Form der erforderlichen Nut aus.
2. Legen Sie die Position der Nut fest.
3. Drehen Sie die Drehbank auf halbe Drehzahl.
4. Montieren Sie das Werkstück in der Drehmaschine.
5. Stellen Sie den Werkzeugeinsatz auf Mittenhöhe ein.
6. Führen Sie den Werkzeugeinsatz mit dem Kreuzvorschubgriff langsam in das Werkstück ein.
7. Tragen Sie reichlich Schneidöl auf die Spitze des Schneidwerkzeugs auf. Damit der Schnitt nicht in der Nut klemmt. Wenn Rattern auftritt, reduzieren Sie die Spindeldrehzahl.
8. Stoppen Sie die Drehmaschine und überprüfen Sie die Nuttiefe.
9. Wiederholen Sie die Schritte 6-7, bis das Werkstück auf die richtige Tiefe geschnitten ist.
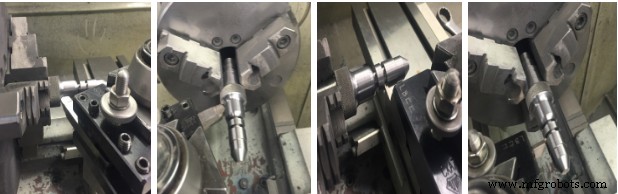
Abbildung 6. Schneiden einer Nut
Abschied
Abstechwerkzeuge, oft Trennwerkzeuge genannt, werden zum Schneiden von Werkstücken verwendet. Es gibt drei Arten von Trennwerkzeugen. Das Abstechwerkzeug besteht aus einem geraden Halter, linksseitig versetzt und rechtsseitig versetzt eingesetzte Klingen werden am häufigsten verwendet.
Es gibt zwei häufige Probleme beim Trennen, Rattern und Umarmen. Ein Rattern tritt auf, wenn das Werkzeug nicht fest genug gehalten wird, jede Lockerung des Werkzeugs, des Halters oder eines Teils der Drehmaschine selbst das Schneiden schwierig, ungleichmäßig und oft unmöglich macht . Umklammern bedeutet, dass das Werkzeug dazu neigt, sich in das Werkstück einzugraben und dazu neigt, über die Oberseite der Schneidkante zu klettern. Dies bricht normalerweise den Werkzeugeinsatz ab oder zerstört das Werkstück. Das Umarmen wird normalerweise verursacht, wenn das Trennwerkzeug zu hoch oder zu niedrig eingestellt ist.
• Abstechwerkzeuge sind schmaler, aber tiefer als Drehwerkzeuge. Abstechwerkzeuge werden verwendet, um schmalere Nuten zu erzeugen und Teile des Materials abzutrennen.
• Der Werkzeughalter sollte das Werkstück kaum freigeben, wenn das Trennwerkzeug installiert ist.
• Stellen Sie sicher, dass das Trennwerkzeug senkrecht zur Rotationsachse steht.
• Stellen Sie sicher, dass die Spitze des Werkzeugs auf der gleichen Höhe wie die Schaftmitte liegt. Dabei kann es hilfreich sein, das Werkzeug gegen die Fläche des Teils zu halten.
• Stellen Sie die Höhe des Werkzeugs ein, legen Sie es gegen die Fläche des Teils und verriegeln Sie das Werkzeug. Denken Sie daran, Schneidflüssigkeit aufzutragen, insbesondere bei tiefen Schnitten.
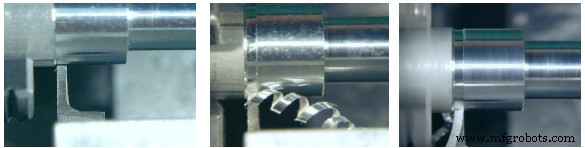
Abbildung 7. Trennung
Vorgehensweise:
1. Spannen Sie das Werkstück so in das Spannfutter ein, dass das abzutrennende Teil so nah wie möglich am Spannfutter liegt.
2. Montieren Sie das Trennwerkzeug auf der linken Seite der Kreuzauflage, wobei die Schneidkante auf Mitte eingestellt ist.
3. Platzieren Sie den Halter so nah wie möglich am Werkzeughalter, um Vibrationen und Rattern zu vermeiden.
4. Stellen Sie den Werkzeugeinsatz ein. Der Werkzeugeinsatz sollte sich vom Halter um etwas mehr als den halben Durchmesser des Werkstücks erstrecken. Stellen Sie die Umdrehung pro Minute (U/min) auf etwa 2/3 der Drehgeschwindigkeit ein.
5. Markieren Sie die Schnittstelle.
6. Bringen Sie das Schneidwerkzeug in Position.
7. Starten Sie die Drehmaschine und führen Sie das Trennwerkzeug langsam von Hand in das Werkstück ein. Greifen Sie den Quertransportgriff mit beiden Händen, um gleichmäßig und gleichmäßig zu füttern. Tragen Sie reichlich Schneidöl auf.
8. Wenn das Werkstück etwa ¼ Zoll groß ist, empfiehlt es sich, das Trennwerkzeug leicht seitwärts zu bewegen. Diese seitliche Bewegung schneidet etwas breiter, um ein Verklemmen des Werkzeugs zu vermeiden.
9. Um Rattern zu vermeiden, halten Sie das Werkzeug scharf und tragen Sie während des Betriebs konsequent Schneidöl auf. Füttern Sie langsam, wenn das Teil fast abgeschnitten ist.
10. Das Werkzeug weiter vorschieben, bis es die Mitte des Werkstücks erreicht. Wenn Sie näher kommen, wird das Werkstück an einem dünnen Metallstab aufgehängt.
11. Das Ende des Werkstücks, das Sie abschneiden, hat im Allgemeinen eine ziemlich raue Oberfläche und einen kleinen Metallstiel, der aus dem Ende herausragt. Siehe Abbildung 19 unten.
12. Der letzte Schritt besteht darin, dieses Stück in das Spannfutter zu montieren und einen Planschnitt zu machen, um das Ende zu reinigen. Ein Problem bei diesem Schritt besteht darin, dass die Spannbacken das fertige Werkstück beschädigen können. Wenn Sie sich Abbildung 20 unten genau ansehen, können Sie tatsächlich den Abdruck der Spannbacken sehen. Um dies zu vermeiden, können Sie das Werkstück vor dem Einspannen in einen dünnen Streifen Schmirgelpapier oder ähnliches Schutzmaterial wickeln.
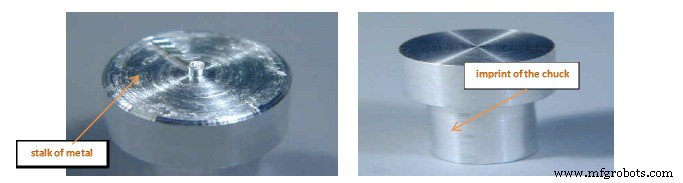
Abbildung 8. Werkstückabschnitt Abbildung 9. Fertiges Werkstück
Ausrichtung der Drehmaschinenzentren
Um bei der Bearbeitung zwischen Spitzen einen parallelen Durchmesser zu erzeugen, ist es wichtig, dass die beiden Drehmaschinen-Zentren aufeinander ausgerichtet sind und mit der Mittellinie der Drehmaschine fluchten. Wenn die Mitte nicht ausgerichtet ist, wird das zu bearbeitende Werkstück verjüngt.
Es gibt drei Methoden, um Drehzentren auszurichten:
1. Durch Ausrichten der Mittellinien auf der Rückseite des Reitstocks zueinander. Dies ist nur eine Sichtprüfung und daher nicht genau.
2. Die Probeschnittmethode, bei der an jedem Ende des Werkstücks ein kleiner Schnitt vorgenommen und der Durchmesser mit einem Mikrometer gemessen wird.
3. Richten Sie die Zentren mit einer Messuhr aus.
Methode 1. Zentrieren durch Anpassen des Reitstocks ausrichten.
Vorgehensweise:
1. Lösen Sie die Reitstockklemmung nicht oder Hebel.
2. Lösen Sie eine der Einstellschrauben auf der linken oder rechten Seite, je nachdem in welche Richtung der Reitstock bewegt werden muss. Ziehen Sie die andere Einstellschraube an, bis die Linie auf der oberen Hälfte des Reitstocks genau mit der Linie auf der unteren Hälfte übereinstimmt.
3. Ziehen Sie die gelöste Einstellschraube fest, um beide Hälften des Reitstocks zu arretieren.
4. Arretieren Sie die Spannmutter oder den Hebel des Reitstocks.
Methode 2. Zum Ausrichten der Mitte durch die Trail-Cut-Methode.
Vorgehensweise:
1. Nehmen Sie einen leichten Schnitt von etwa 0,010 auf einen wahren Durchmesser von Abschnitt A am Ende des Reitstocks mit einer Länge von 0,250 Zoll vor.
2. Stoppen Sie den Vorschub und notieren Sie den Messwert auf dem abgestuften Kragen des Quertransportgriffs.
3. Bewegen Sie das Schneidwerkzeug in die Nähe des Spindelstockendes.
4. Bringen Sie das Schneidwerkzeug in die Nähe der gleichen Krageneinstellung wie in Schritt 1 (Abschnitt A).
5. Bringen Sie das Schneidwerkzeug wieder auf die gleiche Krageneinstellung wie in Schritt 1. (Abschnitt A)
6. Schneiden Sie eine Länge von 0,250 in Abschnitt B und stoppen Sie dann die Drehmaschine.
7. Messen Sie beide Durchmesser mit einem Mikrometer.
8. Wenn beide Durchmesser nicht gleich groß sind, stellen Sie den Reitstock entweder zum Schneidwerkzeug hin oder vom Schneidwerkzeug weg um die Hälfte der Differenz der beiden Messwerte ein.
9. Machen Sie einen weiteren leichten Schnitt an den Abschnitten A und B. Messen Sie diese Durchmesser und stellen Sie den Reitstock ein, falls erforderlich.
Methode 3. Zentrieren mit einer Messuhr.
Vorgehensweise:
1. Drehbank und Arbeitszentren reinigen und Messuhr montieren.
2. Passen Sie die Prüfstange genau zwischen den Spitzen an und ziehen Sie die Reitstockspindelklemmung fest.
3. Montieren Sie eine Messuhr am Werkzeughalter oder Drehmaschinenschlitten. Achten Sie darauf, dass der Anzeigekolben parallel zum Drehmaschinenbett steht und der Kontaktpunkt auf die Mitte eingestellt ist.
4. Stellen Sie den Querschlitten so ein, dass die Anzeige etwa 0,025 Zoll am Reitstockende registriert.
5. Bewegen Sie den Schlitten von Hand, so dass die Testanzeige auf dem Durchmesser am Ende des Spindelstocks ausgerichtet ist, und notieren Sie den Messwert der Testanzeige.
6. Wenn beide Testindikatoren nicht gleich sind. Stellen Sie den Reitstock mit der Einstellschraube ein, bis die Anzeige an beiden Enden den gleichen Wert anzeigt.
Verjüngungsberechnungen
Um die Verjüngung pro Fuß (tpf) zu berechnen. Es ist notwendig, die Länge des Kegels, den großen und den kleinen Durchmesser zu kennen.
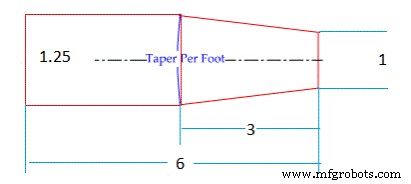
Abbildung 10. Der Hauptteil einer Zollverjüngung
Formel:
Tpf =((D-d) / Länge der Verjüngung) x 12
Beispiel:
Tpf =((1,25 – 1) / 3) x 12 =(0,25 / 3) x 12 =1 Zoll
Reitstockversatzberechnungen
Bei der Berechnung des Reitstockversatzes müssen die Konizität pro Fuß und die Gesamtlänge des Werkstücks bekannt sein.
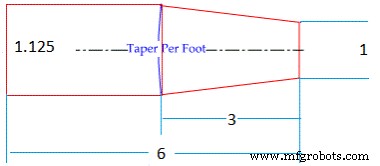
Abbildung 11. Abmessung eines Werkstücks mit einer Verjüngung
Formel:
Reitstockversatz =(tpf x Gesamtlänge des Werkstücks) / 24
Beispiel:
1. Finden Sie tpf:
tpf =((1,125 – 1) x 12) / 3 =(0,125 x 12) / 3 =0,50 Zoll.
2. Finden Sie den Reitstockversatz:
Reitstockversatz =(0,5 x 6) / 24 =3 / 24 =0,125 Zoll
In einigen Fällen, in denen es nicht notwendig ist, die Verjüngung pro Fuß zu ermitteln, kann die folgende vereinfachte Formel verwendet werden.
Formel:
Reitstockversatz =(OL / TL) x ((D-d) / 2)
OL =Gesamtlänge des Werkstücks
TL =Länge des verjüngten Abschnitts
D =Ende mit großem Durchmesser
d =Ende mit kleinem Durchmesser
Beispiel:
Reitstockversatz =(6 / 3) x ((1,125-1) / 2) =0,125
Kegeldrehen
Verwenden der zusammengesetzten Pause, um kurze oder steile Verjüngungen zu erzeugen. Der Werkzeugeinsatz muss von Hand mit dem zusammengesetzten Restvorschubgriff zugeführt werden.
Schneiden Sie einen Verjüngungserzeuger mit zusammengesetztem Rest
Verfahren:
1. Beziehen Sie sich auf die Blaupausenzeichnung für den Betrag der erforderlichen Verjüngung in Grad.
2. Lösen Sie die Feststellschrauben der Compound-Stütze.
3. Schwenken Sie die Compoundauflage in den gewünschten Winkel. (Siehe erstes Bild)
4. Ziehen Sie die Feststellschrauben der Compound-Stütze fest.
5. Stellen Sie den Werkzeugeinsatz auf die Mitte ein und führen Sie den Schneidwerkzeugeinsatz mit der zusammengesetzten Restvorschubschraube zu.
6. Konus auf Größe und Sitz prüfen.
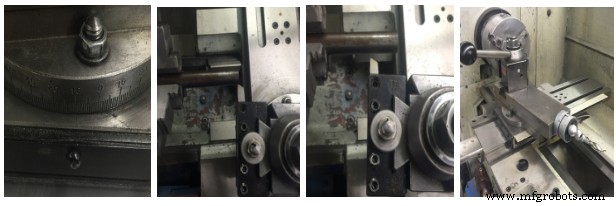
Abbildung 12. Kegeldrehvorgang
Echtes Werkstück im 4-Backenfutter
1. Eine Messuhr oder Prüfanzeige sollte immer dann verwendet werden, wenn ein bearbeiteter Durchmesser auf ein Tausendstel Zoll genau ausgerichtet werden muss.
2. Verfahren:
3. Legen Sie das Werkstück in das 4-Backenfutter ein und zentrieren Sie es ungefähr, entweder mit der Kreide- oder der Oberflächenlehrenmethode.

4. Montieren Sie einen Indikator im Werkzeughalter der Drehmaschine.
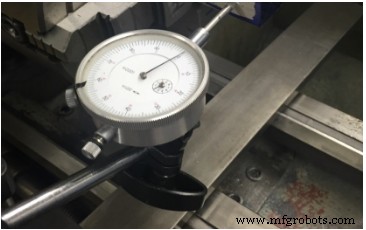
5. Stellen Sie die Anzeigespindel in eine horizontale Position, wobei der Kontaktpunkt auf Mittenhöhe eingestellt ist.
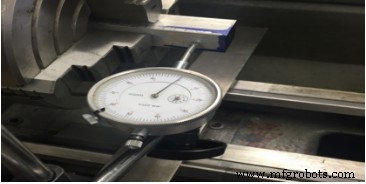
6. Bringen Sie den Anzeigepunkt gegen den Werkstückdurchmesser, so dass er etwa 0,020 ausrichtet, und drehen Sie die Drehmaschinenspindel von Hand.
7. Achten Sie beim Drehen der Drehmaschine auf den höchsten und niedrigsten Messwert auf der Messuhr.
8. Lösen Sie die Spannbacke beim niedrigsten Messwert leicht und ziehen Sie die Backe beim hohen Messwert fest, bis das Werkstück um die Hälfte der Differenz zwischen den beiden Anzeigewerten bewegt wurde.
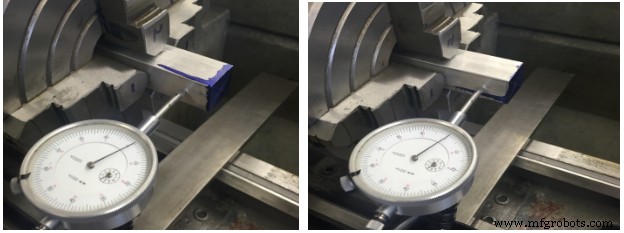
Seite 1. Linke und rechte Seite
9. Fahren Sie fort, nur diese beiden gegenüberliegenden Backen einzustellen, bis der Indikator das an beiden Backen registriert. Ignorieren Sie die Indikatorwerte für die Arbeit zwischen diesen beiden Backen.
10. Stellen Sie den anderen Satz gegenüberliegender Backen auf die gleiche Weise ein, bis der Indikator dasselbe an einem beliebigen Punkt auf dem Werkstückumfang registriert.
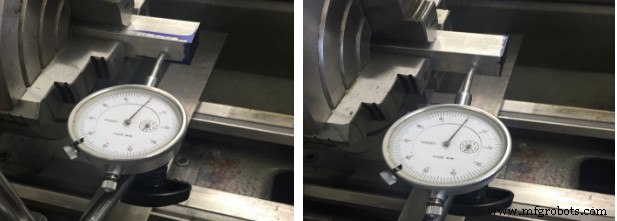
Seite 2. Linke und rechte Seite
11. Ziehen Sie alle Backen gleichmäßig an, um das Werkstück fest zu fixieren.
12. Drehen Sie die Spindel der Drehmaschine von Hand und überprüfen Sie die Anzeige erneut.
EINHEITENTEST
1. The compound rest is set at what angle?
2. Explain the different between rough and finish turning.
3. Should the point of the tool be set above, or at the center of the spindle axis when taking a facing cut?
4. What is the purpose of facing?
5. Why do we spot drill a workpiece?
6. What is the purpose of boring?
7. Name three types of parting tools.
8. Name three methods to align lathe centers.
9. Calculate the offset for the taper if D=2, d=1, OL=6, and TL=3. The formula is:
Offset =(OL x (D-d)) / (2 x TL)
10. Please describe the producer for cut a taper.
Industrietechnik