Leitfaden für Wartungsmanager zum Erstellen und Verwenden von FMEAs
Im März 2018 wurde die Stadt Atlanta von einem bösartigen Ransomware-Angriff heimgesucht. Es war einer der kostspieligsten Angriffe in den letzten zehn Jahren. Der öffentliche Dienst war gestört. Die Abteilungen waren gezwungen, den wesentlichen Papierkram von Hand zu erledigen. Und es hat die Stadtregierung 17 Millionen Dollar gekostet.
Als sich der Staub gelegt hatte, war klar:Die Stadt war auf diese Katastrophe nicht vorbereitet. Ein Audit, das zwei Monate vor der Sicherheitsverletzung durchgeführt wurde, fand 2.000 Schwachstellen im IT-System der Stadt. Es war ein guter Schritt, aber es war zu wenig, zu spät.
Was in Atlanta passiert ist, ist eine warnende Geschichte mit einer großen Lektion:Risiken können nie ausgeschlossen, aber gemanagt werden. Dies gilt insbesondere für die Wartung. Ein Geräteausfall ist unvermeidlich. Aber zu wissen, wie man die Wahrscheinlichkeit eines Scheiterns verringert und wie man reagiert, wenn es passiert, ist entscheidend für den Erfolg.
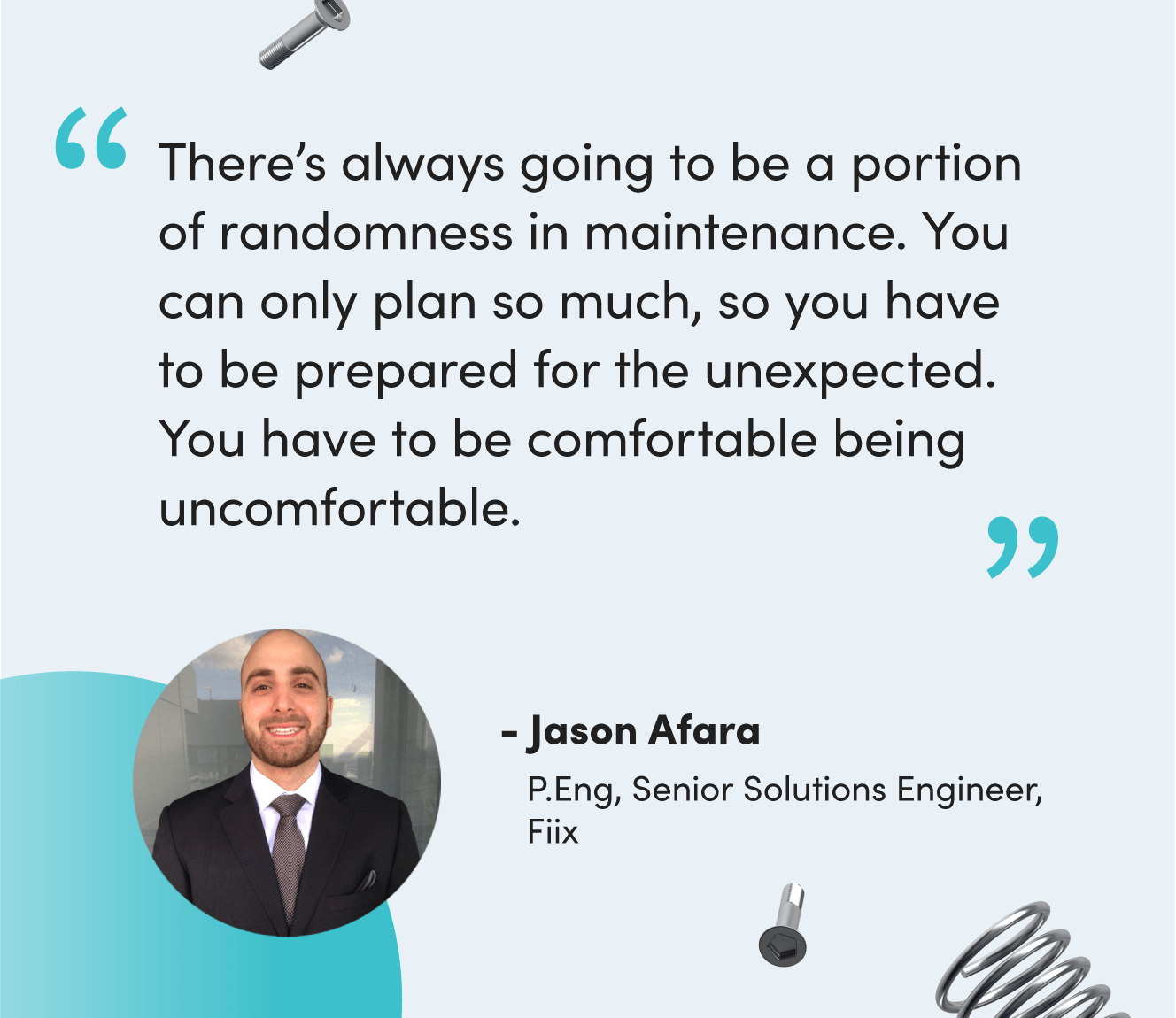
Eine Fehlermöglichkeits- und Auswirkungsanalyse (FMEA) ist ein Werkzeug, um Fehler zu verstehen und zu antizipieren, damit Sie ihre Auswirkungen begrenzen können. In diesem Artikel erfahren Sie:
- Was eine FMEA ist
- Die verschiedenen Arten von FMEAs
- So erstellen Sie eine FMEA
- Und wie Wartungsteams eine FMEA verwenden können
Was ist eine FMEA?
Eine Fehlermöglichkeits- und Auswirkungsanalyse (FMEA) identifiziert und dokumentiert alle Möglichkeiten, wie ein Gerät ausfallen kann, und die möglichen Auswirkungen dieser Fehler. Es beschreibt:
- Fehlermodi für einzelne Komponenten
- Die Folgen von Fehlern auf Produktivität und Sicherheit
- Ein Plan zur Vorbeugung oder Reaktion auf diese Probleme
Die Erstellung von FMEAs ist eine Schlüsselkomponente der zuverlässigkeitsorientierten Instandhaltung (RCM).
Es gibt drei Hauptziele einer FMEA:
- Verhindern Sie zukünftige Ausfälle, indem Sie die Wahrscheinlichkeit häufiger und kritischer Ausfälle durch geplante Wartung und Standardbetriebsverfahren verringern
- Reaktionszeiten reduzieren, Ausfallzeiten verkürzen und Gesundheit und Sicherheit verbessern, wenn Anlagen ausfallen
- Priorität der vorbeugenden und korrektiven Wartung in Situationen, die keine Notfälle sind
Welche verschiedenen Arten von FMEA gibt es?
FMEAs können basierend auf der Art des zu bewertenden Risikos und den Auswirkungen, die sie haben, in Untertypen kategorisiert werden. Hier ist ein kurzer Überblick über jede Art von FMEA:
- FFMEA (Funktionsanalyse von Fehlermöglichkeiten und Auswirkungen) :Eine FFMEA analysiert die Risiken, die die Funktionsweise eines Systems beeinflussen. Das Ziel einer FFMEA (manchmal auch als Systemfehlermodus- und Auswirkungsanalyse bezeichnet) besteht darin, diese Fehler zu verhindern, bevor sie auftreten.
- DFMEA (Design Failure Mode and Effects Analysis) :Eine DFMEA bewertet die Risiken einer Anlage in der Entwurfsphase. Der Zweck dieser Analyse besteht darin, potenzielle Probleme mit einem Asset zu finden und zu beheben, bevor es bereitgestellt wird, um seine Zuverlässigkeit zu erhöhen, den Wartungsaufwand zu reduzieren und den Asset-Lebenszyklus zu verlängern.
- PFMEA (Prozessfehlermöglichkeits- und Auswirkungsanalyse) :Eine PFMEA sucht nach möglichen Fehlern innerhalb eines Prozesses. Der Unterschied zwischen einer PFMEA und anderen Arten von FMEAs besteht darin, dass sie sich darauf konzentriert, was während des Betriebs und der Wartung eines Systems schief gehen kann.
- FMECA (Fehlermodus, Auswirkungen und Kritikalitätsanalyse) :Eine FMECA (oder Kritikalitätsanalyse) analysiert sowohl Fehlermodi als auch das mit diesen Fehlermodi verbundene Risikoniveau.
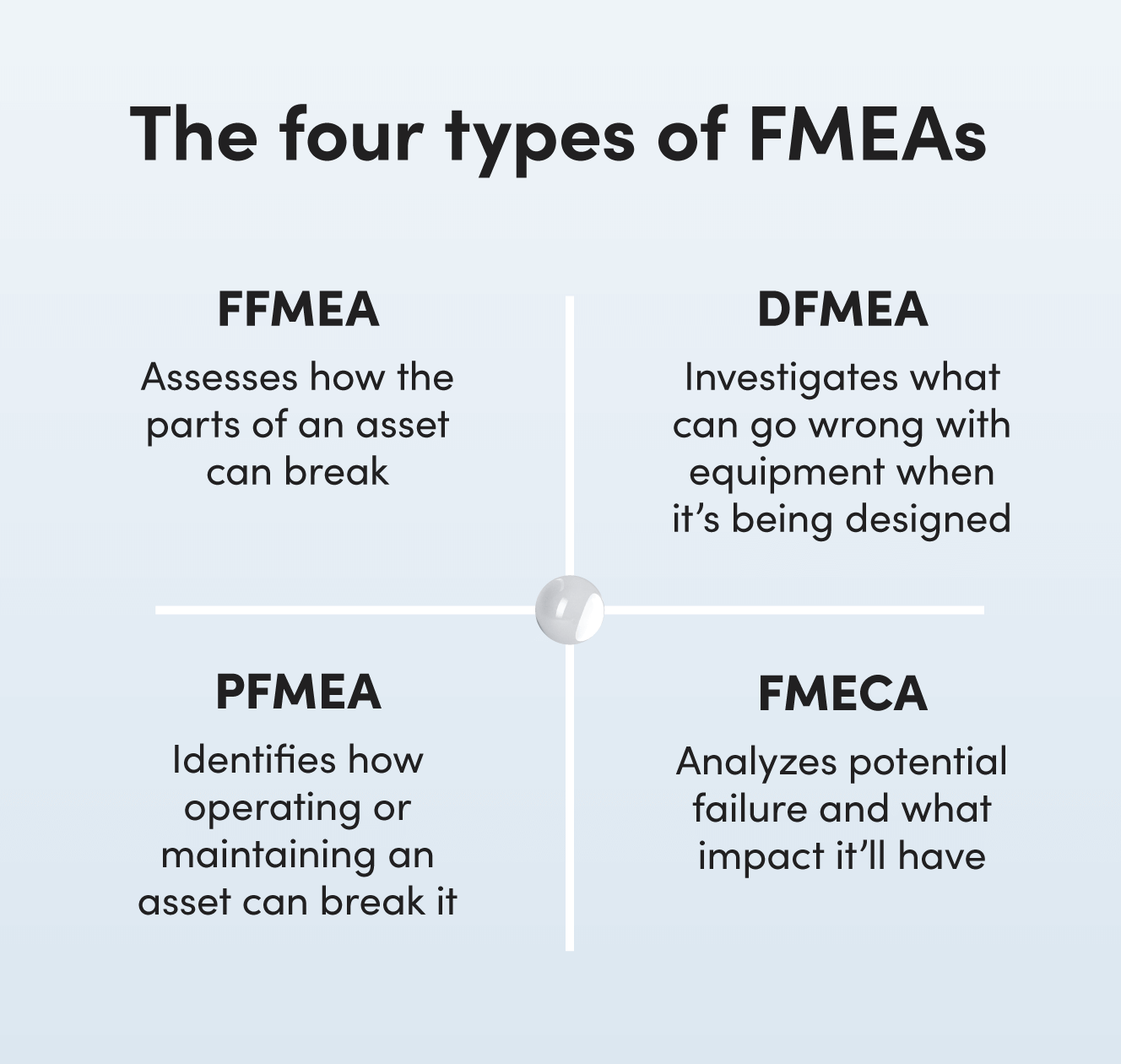
Was ist der Unterschied zwischen einem Fehlermodus und einem Fehlercode?
Ein Fehlermodus ist ein Fehler oder Defekt, der zu einer Fehlfunktion eines Systems führt. Ein Beispiel für einen Fehlermodus bei einem Transferförderer mit variabler Geschwindigkeit kann ein Festfressen eines Lagers sein. Ein gebrochenes Lager führt dazu, dass das Förderband langsamer wird oder nicht mehr funktioniert.
Ein Fehlercode ist ein Fehlermodus, der durch ein alphanumerisches Tag dargestellt wird. Fehlercodes werden in CMMS-Software häufig verwendet, um Informationen schnell zu übermitteln und Fehler zu sortieren oder zu melden. Fehlercodes werden normalerweise durch drei Kontextinformationen unterstützt. Ein Beispiel für einen Fehlercode sieht so aus:
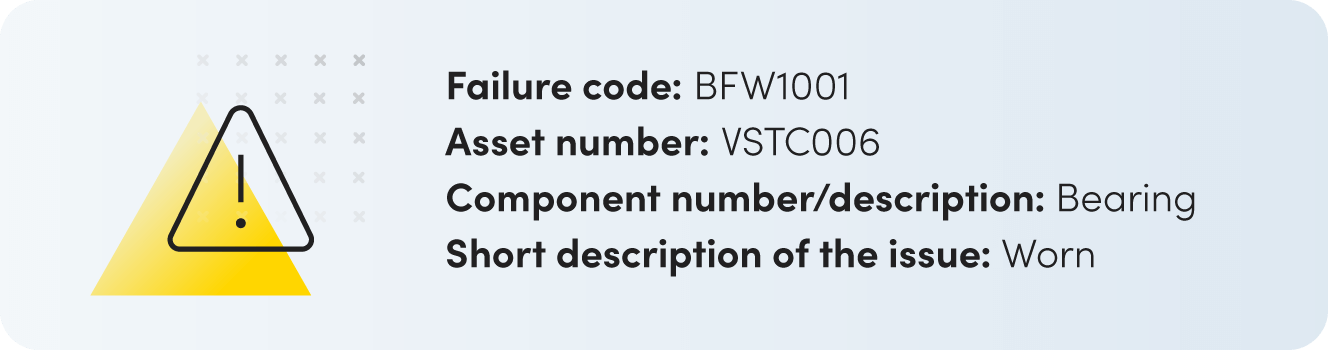
Was ist der Unterschied zwischen FMEA und FRACAS?
Eine Fehlermöglichkeits- und Auswirkungsanalyse skizziert mögliche Fehler, ihre Ursachen und ihre Auswirkungen. Es ist ein Prozess, der mögliche zukünftige Vorfälle und ihre wahrscheinlichen Ursachen auflistet. Es ist eine proaktive Maßnahme.
Ein Fehlermelde-, Analyse- und Korrekturmaßnahmensystem (FRACAS) ist ein geschlossenes Meldesystem, das bereits aufgetretene Fehler analysiert. Es untersucht Fehler in der Vergangenheit, um herauszufinden, warum sie aufgetreten sind und welche Auswirkungen sie hatten, damit sie in Zukunft verhindert werden können. Es ist eine reaktive Maßnahme.
Das Erstellen von FMEAs für die Wartung ist ein wichtiger Bestandteil beim Aufbau eines FRACAS. Tatsächlich ist es der erste Schritt des Prozesses. Eine FMEA ist eine Grundlage für Fehler sowie die Team- und Geräteleistung. Auf Grundlage dieser Informationen können Sie Entscheidungen treffen, z. B. welche Berichte erstellt oder auf Fehler abgezielt werden soll.
Wie Sie FMEAs für die Wartung verwenden können
Es gibt drei Möglichkeiten, wie Wartungsteams eine Fehlermöglichkeits- und Auswirkungsanalyse verwenden können:
- Um einen vorbeugenden Wartungsplan zu erstellen, der die Wahrscheinlichkeit von Anlagenausfällen verringert und Ressourcen optimiert
- Um Notfallwartungen vorzubereiten, damit Anlagen schnell repariert und Ausfallzeiten minimiert werden können
- Um korrigierende Wartungen und Wartungsrückstände zu priorisieren
Verwendung von FMEAs zur Erstellung eines vorbeugenden Wartungsplans
Es gibt drei Möglichkeiten, wie Sie FMEAs verwenden können, um ein erstklassiges vorbeugendes Wartungsprogramm durchzuführen:
- Neue Aufgaben zur vorbeugenden Wartung erstellen
- Vorbeugende Wartung priorisieren
- Präventive Wartung optimieren
Laden Sie diese Vorlage herunter, um einen vorbeugenden Wartungsplan zu erstellen
Der erste Schritt bei der Erstellung eines vorbeugenden Wartungsprogramms besteht darin, zu verstehen, welche Fehler auftreten können und wie oft sie auftreten. Eine FMEA skizziert diese Informationen. Wenn beispielsweise eine neue Anlage entworfen wird, können Sie mithilfe einer FMEA herausfinden, welche PMs erforderlich sind, um mögliche Fehlermodi zu vermeiden, und wie oft sie durchgeführt werden müssen. Auf diese Weise können Sie Eingaben zuordnen, die in die Erstellung neuer PMs einfließen, einschließlich wer der Arbeit zugewiesen wird, was die Arbeit auslöst, was sie kostet und wie lange sie dauert.
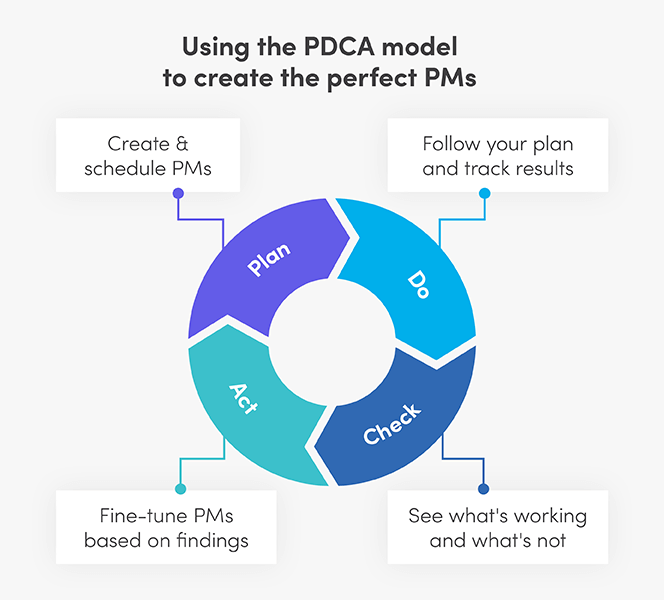
Der Erfolg Ihres vorbeugenden Wartungsprogramms hängt sowohl davon ab, wie viele Fehler Sie finden und beheben, als auch von den Auswirkungen dieser Fehler. Wenn Sie 100 kleine Pannen verhindern, aber die fünf oder sechs Ausfälle, die Ihr Unternehmen Millionen von Dollar kosten, nicht erkennen, ist Ihr Programm fehlerhaft. Eine FMEA enthält alle Informationen, die Sie benötigen, um PMs zu priorisieren und die wahrscheinlichsten und störendsten Ausfälle zu erkennen.
Während FMEAs Ihnen eine Grundlage für die Erstellung eines vorbeugenden Wartungsplans bieten, werden Ihre Pläne nicht ewig Bestand haben. Ihr Betrieb ändert sich ständig. Ihr PM-Zeitplan muss sich damit ändern. Die Verwendung von Arbeitsauftrags- und Reparaturhistorien zum Aktualisieren von FMEAs hilft Ihnen, Ihren Zeitplan zu optimieren und mit anderen Änderungen Schritt zu halten. Ein Fehlermodus tritt beispielsweise möglicherweise nicht so häufig auf, wie Sie es vorhergesagt haben. Diese Daten können dazu führen, dass Sie die Häufigkeit der PM reduzieren, die diesen Fehlermodus verhindern sollen. Sie können diese Ressourcen dann einer anderen Wartungsaufgabe zuordnen.
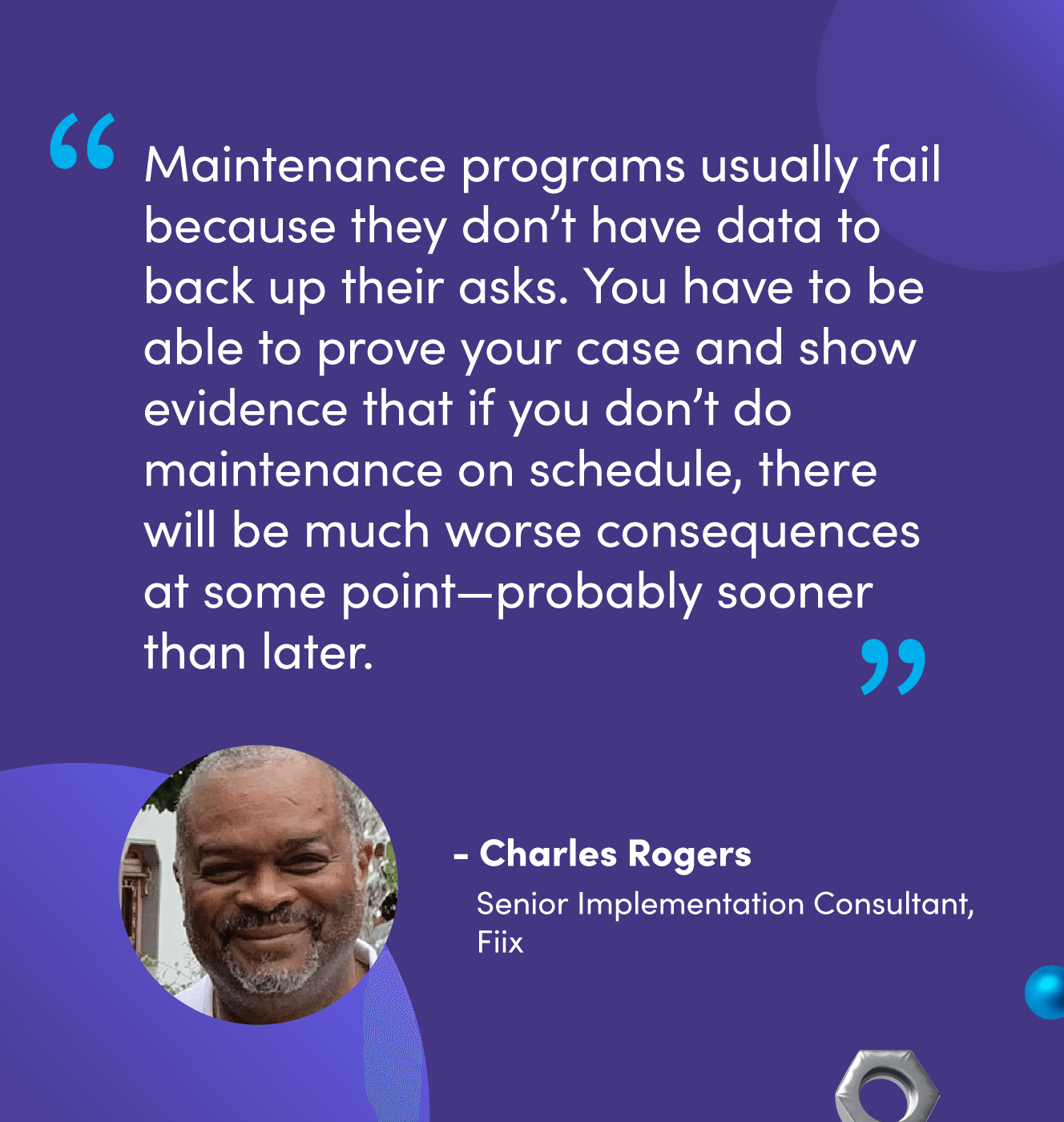
Verwenden von FMEAs zur Vorbereitung von Notfallwartungen
Keine noch so große Wartung wird Fehler vollständig eliminieren. Das Beste, was Sie tun können, ist, Ausfälle mit hohem Risiko und großen Auswirkungen einzuplanen, damit Ihr Team sie in einer statt in zwei Stunden beheben kann. Eine FMEA ist ein wertvolles Instrument zur Umsetzung dieser Notfallmaßnahmen.
Beginnen Sie damit, sich die Fehler anzusehen, die die größten Auswirkungen haben und am häufigsten auftreten. Wählen Sie aus dieser Liste Fehlermodi aus, die schwer zu erkennen sind. Sie werden am Ende mit Fehlermodi enden, die schwer zu erkennen sind und das größte Durcheinander verursachen. Erstellen Sie einen Notfallplan für diese Pannen.
Ihr Notfallplan sollte alle Informationen enthalten, die Reaktions- und Reparaturzeiten verkürzen. Es sollte auch Gesundheit und Sicherheit berücksichtigen. Dies kann Folgendes beinhalten:
- Kitting-Teile, um den Zeitaufwand für das Abrufen wichtiger Ersatzteile und persönlicher Schutzausrüstung zu reduzieren (Laden Sie eine Kitting-Vorlage für Teile herunter)
- Erstellen einer detaillierten Aufgabenliste oder Tipps zur Fehlerbehebung
- Anhängen von Diagrammen, Handbüchern, Fotos und anderen visuellen Hilfsmitteln an Arbeitsaufträge
- Eine Liste von Technikern oder Auftragnehmern skizzieren, die die Reparatur durchführen können
- Etablierung einer Methode zur schnellen Kommunikation mit Technikern, z. B. CMMS-Software
Verwenden von FMEAs zur Priorisierung der korrektiven Wartung und des Wartungsrückstands
Es ist hilfreich, Fehler frühzeitig zu erkennen, aber es bedeutet nichts, wenn Sie keinen Prozess haben, um diesen Fehler schnell und effektiv zu beheben. Eine FMEA hilft Ihnen beim Aufbau dieses Prozesses.
Der erste Schritt besteht darin, Fehlermodi mit einem hohen Schweregrad zu identifizieren (d. h. Vermögenswerte, die Ihr Unternehmen am meisten kosten, wenn sie ausfallen). Korrekturmaßnahmen an diesem Gerät sollten so schnell wie möglich durchgeführt werden. Mit dieser Liste können Sie Schulungsmaterialien und Reaktionspläne erstellen, damit jeder weiß, wie er auf Fehler reagieren kann.
Sie können einen ähnlichen Ansatz bei der Priorisierung des Wartungsrückstands verwenden, mit Ausnahme eines zusätzlichen Schritts. Nachdem Sie die zurückgestellte Arbeit nach Schweregrad sortiert haben, sehen Sie sich die verbleibende Arbeit nach der Fehlerhäufigkeit an. Vergleichen Sie dies damit, wie spät die Arbeit ist. Wenn ein Fehlermodus eine Häufigkeitsrate hat, die die Anzahl der verpassten Inspektionen überschreitet, sollte diese Arbeit Vorrang haben, da die Wahrscheinlichkeit eines Fehlers höher ist.
Diese kostenlose Vorlage hilft Ihnen, Ihren Wartungsrückstand zu priorisieren
So erstellen Sie eine FMEA
Die folgende FMEA-Vorlage hilft Ihnen, Risiken in Ihrem Betrieb zu erkennen und Maßnahmen zu ergreifen, um diese zu verhindern.
Laden Sie hier Ihre eigene FMEA-Vorlage herunter
Aber zuerst erfahren Sie hier, wie Sie Daten für Ihre FMEA erhalten
Gute FMEAs hängen von guten Daten ab. Ohne Daten bauen Sie Ihr Wartungsprogramm auf Vermutungen und Annahmen auf. Doch wie findet man die benötigten Informationen für eine FMEA? Die drei folgenden Quellen bieten Ihnen eine großartige Grundlage:
- OEM-Richtlinien:Dies ist Ihr Ausgangspunkt. Diese Richtlinien geben Ihnen eine Grundlage für das Ausfüllen einer FMEA, wenn Sie keine anderen Daten haben.
- Interviews mit Bedienern und Technikern:Profitieren Sie von den Erfahrungen derer, die täglich mit Geräten arbeiten. Sie geben Ihnen Einblicke, die Sie nirgendwo finden können, beispielsweise wenn eine Komponente doppelt so viel Schmierung benötigt wie vorgeschlagen oder ob die Häufigkeit von Ausfällen aufgrund geänderter Maschinenspezifikationen zugenommen hat.
- Arbeitsauftragsdaten:Ihre Arbeitsaufträge zeigen die Leistung der Ausrüstung und sind eine hervorragende Informationsquelle für die Optimierung und Verbesserung Ihrer FMEAs. Suchen Sie nach häufigen Fehlern, welche Maßnahmen ergriffen wurden, um die Ursache zu finden und zu beheben, was eine Reparatur verzögerte und wie einfach es war, einen Fehler zu erkennen.
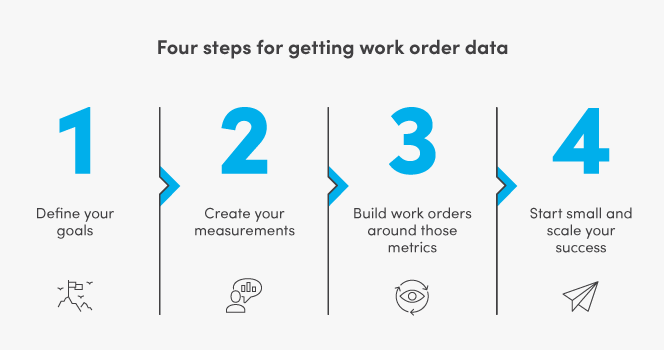
Keine dieser Quellen funktioniert allein. Kombinieren Sie sie, um ein vollständiges Bild davon zu erhalten, wie Ihre Ausrüstung funktioniert, wie sie ausfallen kann, welche Auswirkungen ein Ausfall hat und was dagegen unternommen werden sollte.
Eine FMEA-Vorlage
1. Identifizieren Sie Asset-Komponenten
Dokumentieren Sie jede Asset-Komponente, die kaputt gehen oder sich verschlechtern kann. Zu den Komponenten einer Abfüllanlage können beispielsweise Getriebe, Motoren, Kettenräder, Lager und Düsen gehören.
Beginnen Sie mit Ihrer wichtigsten Ausrüstung und arbeiten Sie von dort aus weiter. Dies ist ein guter Zeitpunkt, um klare Namenskonventionen und eine Asset-Hierarchie zu erstellen, falls Sie diese noch nicht haben.
2. Identifizieren Sie potenzielle Fehlermodi
Es ist an der Zeit, herauszufinden, wie diese Komponenten ausfallen können. Wenn eine einzelne Komponente mehrere Fehlermodi aufweist, listen Sie jeden Fehlermodus entsprechend auf. Zu den Ausfallarten eines Lagers können beispielsweise Fluchtungsfehler, Korrosion oder Verschmutzung gehören.
3. Liste potenzieller Auswirkungen eines Fehlers auf
Beschreiben Sie das Ergebnis eines Fehlers und wie es sich auf die Produktion und die Sicherheit des Personals auswirkt. Ein falsch ausgerichtetes Lager wird beispielsweise eine Linie stilllegen, bis es ersetzt werden kann (etwa drei Stunden), mit einem möglichen Verlust von 1.800 Einheiten.
4. Schweregrad
Dies ist ein Maß für die Auswirkungen eines Fehlers auf Produktion und Sicherheit. Es wird auf einer Skala von 1 bis 10 bewertet, wobei 1 ein Ereignis mit geringer Auswirkung und 10 ein Ereignis mit hoher Auswirkung ist. Berücksichtigen Sie den Zustand des Assets beim Scoring. Bei einem Auto, dessen Reifen beispielsweise bei niedriger Geschwindigkeit platzen, treten leichte Lenkprobleme auf, aber ein Platzen bei hoher Geschwindigkeit ist viel gefährlicher.
Beginnen Sie mit dieser Kritikalitätsanalysevorlage mit der Berechnung des Schweregrads eines Assets
5. Mögliche Ursachen auflisten
Listen Sie alle möglichen Gründe für einen Fehler auf. Gehen Sie über eine direkte Ursache hinaus. Ein korrodiertes Lager kann beispielsweise auftreten, weil Verbrauchsmaterialien falsch etikettiert oder Anweisungen unklar waren, was zu einer unsachgemäßen Schmierung führt.
Gehen Sie Fehlern auf den Grund mit dieser praktischen (und kostenlosen!) Vorlage für die Ursachenanalyse
6. Erwartete Häufigkeitsbewertung
Dies ist ein Maß dafür, wie häufig ein Fehlermodus auftritt. Es wird auf einer Skala von 1 bis 10 bewertet, wobei 1 für ein Ereignis steht, das selten auftritt, und 10 für ein Ereignis, das sehr häufig auftritt.
7. Liste der aktuellen Prozesskontrollen
Dokumentieren Sie alle Maßnahmen, die ergriffen wurden, um einen Ausfall zu verhindern oder zu erkennen. Zu den Prozesskontrollen können wöchentliche vorbeugende Wartungsinspektionen, der monatliche Austausch von Teilen und der Einsatz von Sensoren zur Erkennung gefährlich hoher Vibrationen gehören.
8. Erkennungswert
Diese Zahl bestimmt, wie einfach es ist, ein Problem zu erkennen, bevor es zum Totalausfall führt. Es wird auf einer Skala von 1 bis 10 bewertet. Ein Ereignis, das nie entdeckt werden kann, wird mit 1 bewertet. Ein Ereignis, das fast immer erkannt werden kann, wird mit 10 Punkten bewertet. Zum Beispiel kann ein platten Reifen manchmal in einem frühen Stadium erkannt werden, sodass er mit 5 bewertet wird. Eine beschädigte Windschutzscheibe wird oft durch unvorhersehbare Ereignisse verursacht, was bedeutet, dass er schwer zu erkennen ist und eine 9 erhalten würde.
9. Risikoprioritätsnummer
Die Risikoprioritätszahl berechnet Fehlermodi, die die größten Auswirkungen haben und am besten vermeidbar sind. Um den RPN zu finden, multiplizieren Sie den Schweregrad, die Häufigkeit und die Erkennungsbewertungen. Wenn ein Fehlermodus beispielsweise eine Schweregradbewertung von 8, eine Häufigkeitsbewertung von 5 und eine Erkennungsbewertung von 10 hat, wäre der RPN 400. Je höher die Zahl, desto mehr Ressourcen sollten in die Verhinderung dieses Fehlers investiert werden.
10. Empfohlene Aktion festlegen
Erstellen Sie einen Plan, um die Wahrscheinlichkeit eines Ausfalls zu verringern oder die Chancen einer Früherkennung zu erhöhen. Dies kann die Erhöhung der Häufigkeit von PMs an einer Komponente oder die Investition in Geräte zur Zustandsüberwachung umfassen.
Verwalten von FMEAs
FMEAs sind lebende Dokumente, die regelmäßig überprüft und aktualisiert werden sollten. Hier sind einige Ereignisse, die eine Überprüfung einer FMEA auslösen könnten:
- In Ihrer Einrichtung wird ein neues Asset entworfen oder installiert
- Ein neuer Techniker oder Operator tritt dem Team bei
- Der Betriebsmodus einer Maschine wird geändert (d. h. sie wird häufiger ausgeführt oder die Spezifikationen ändern sich)
- Ein Fehlermodus tritt häufiger auf
- Es wurde eine neue Technologie implementiert, mit der Sie Fehler leichter erkennen oder verhindern können
- Sie finden einen neuen Fehlermodus oder eine Ursache für einen bestehenden Fehler
- Die Auswirkung von Fehlern ändert sich (d. h. es wird ein neues Produkt mit teurerem Material hergestellt)
Sowohl das Wartungs- als auch das Betriebspersonal sollten an der Änderung und Ergänzung einer Fehlermöglichkeits- und Auswirkungsanalyse beteiligt sein. Die Vielfalt der Perspektiven und Erfahrungen mit Geräten hilft, Lücken in Ihren FMEAs zu vermeiden.
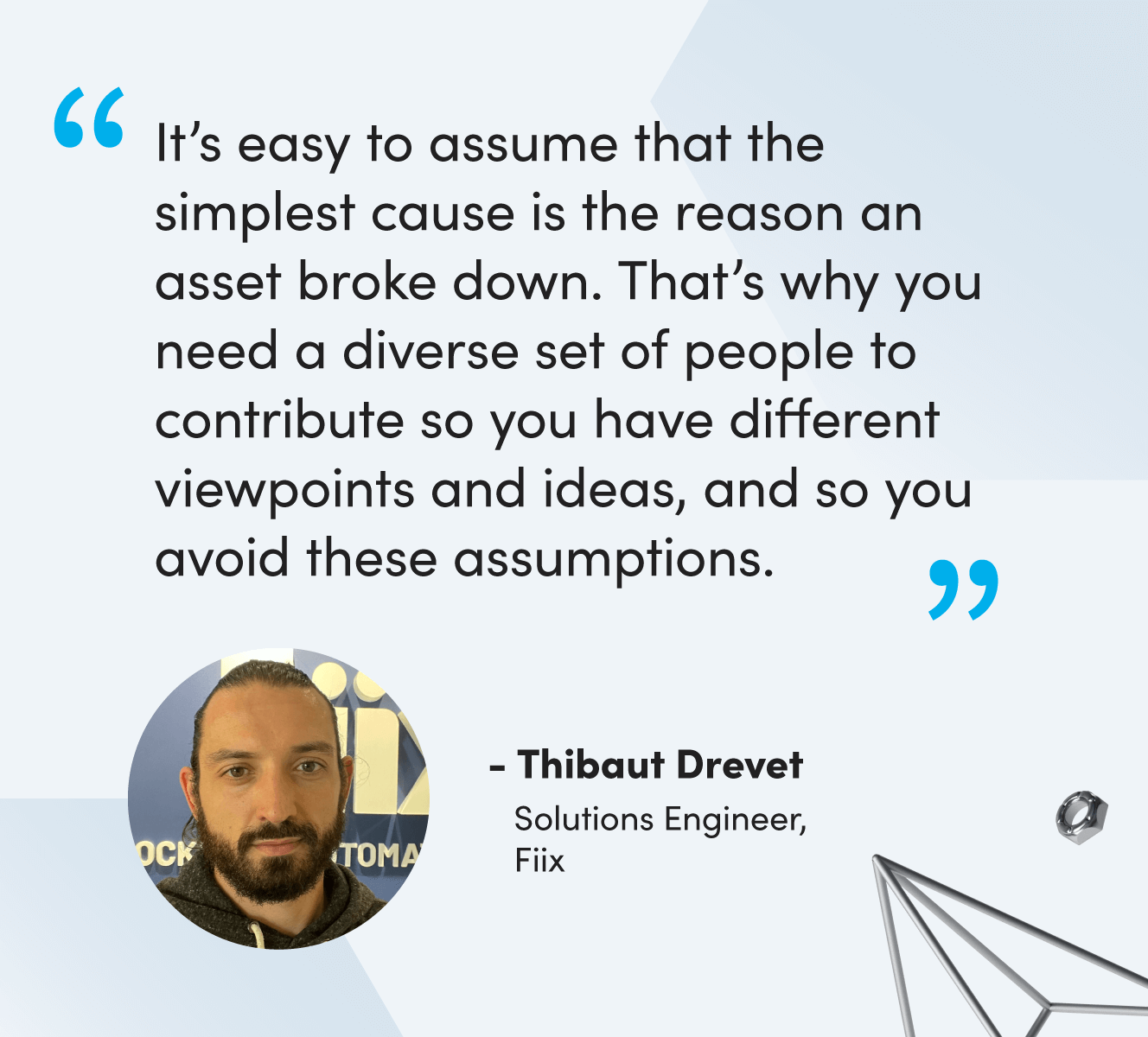
FMEAs sind eine langfristige Investition in den Erfolg
Eine Fehlermodus- und Auswirkungsanalyse ist kein Pflaster zur Fehlerbehebung oder ein Tool zur Fehlerbehebung. Es handelt sich um eine kontinuierliche Aktivität mit dem Ziel, Fehler nach Möglichkeit zu verhindern und deren Auswirkungen zu mildern, wenn dies nicht der Fall ist. Es ist eine Planungsressource und eine Absicherung gegen finanzielle Verluste und Sicherheitsrisiken.
Die Erstellung von FMEAs ist zwar mit einem erheblichen Zeitaufwand verbunden, zahlt sich jedoch langfristig aus, indem sie Ihnen hilft, vorauszuplanen, reaktive Wartungen zu verhindern und den Teamerfolg zu verfolgen.
Gerätewartung und Reparatur
- So halten Sie die Wartung in einem proaktiven Modus
- Kurzanleitung zur PM-Entwicklung und -Ausführung
- Beste Leistung bei Wartung und Zuverlässigkeit
- Details sind wichtig für Wartung und Zuverlässigkeit
- Halten Sie die Wartung einfach:Verwenden Sie Sinne und Sensibilität
- 5 Ursachen für Geräteausfälle (und was Sie dagegen tun können)
- Zeit ist Geld:Tipps zur Verwendung von Wartungssoftware, um Zeit zu sparen und effizienter zu investieren
- Fehlermeldung in der Wartung vereinfachen
- Ein Leitfaden zur Wartung und Ersatzteilen von Skiliften
- Ihr Leitfaden für Kranbetrieb und -wartung