Synergetischer Effekt von Graphen und MWCNTs auf die Mikrostruktur und die mechanischen Eigenschaften von Cu/Ti3SiC2/C-Nanokompositen
Zusammenfassung
Mehrwandige Kohlenstoffnanoröhren (MWCNTs) und Graphene wurden aufgrund ihrer einzigartigen Struktur und Leistung als neuartige Verstärkungen verwendet. MWCNTs oder Graphene verstärkte Kupfermatrix-Verbundwerkstoffe konnten jedoch aufgrund der Verstärkungsdispersion in der Metallmatrix, der Benetzbarkeit zur Metallmatrix und der Verbundmaterialgrenzfläche nicht den idealen Wert einholen. Unter Ausnutzung der überlegenen Eigenschaften von eindimensionalen MWCNTs und zweidimensionalen Graphenen werden komplementäre Leistung und Struktur konstruiert, um eine hohe Kontaktfläche zwischen MWCNTs und Graphenen zur Cu-Matrix zu schaffen. Mechanisches Legieren, Heißpressen und heißisostatische Presstechniken werden verwendet, um selbstschmierende Nanokomposite mit Cu-Matrix herzustellen. Auswirkungen von MWCNTs und Graphenen auf die mechanischen Eigenschaften und Mikrostrukturen von Cu/Ti3 SiC2 /C-Nanokomposite werden untersucht. Die Bruch- und Verstärkungsmechanismen von Cu/Ti3 SiC2 /C-Nanokomposite werden anhand der Struktur und Zusammensetzung von Cu/Ti3 . untersucht SiC2 /C-Nanokomposite mit Bildung und Funktion der Grenzfläche.
Hintergrund
Kupfer-Graphit-Verbundwerkstoff hat eine gute elektrische Leitfähigkeit, eine hohe Wärmeleitfähigkeit, eine gute Verschleißfestigkeit und andere Eigenschaften; , dass es eine Mischung aus den Vorteilen von Kupfer und Graphit ist, so dass es zunehmend in der Luft- und Raumfahrt, Elektronik, Automobilanwendung und anderen Bereichen verwendet wird [1, 2]. Ti3 SiC2 bietet Vorteile in Bezug auf Wärmeleitfähigkeit, hohe elektrische Leitfähigkeit, einfache Verarbeitung ähnlich wie Metalle, Oxidationsbeständigkeit, geringes Gewicht und hohe Temperaturbeständigkeit, was es zu einem nützlichen Material für vielfältige Anwendungen macht [3, 4]. Ohne die selbstschmierenden Eigenschaften und die Leitfähigkeit von Kupfergraphitlegierungen zu beeinträchtigen, kann Ti3 SiC2 kann die Festigkeit, Härte und Verschleißfestigkeit von Kupfer-Graphit-Verbundwerkstoffen verbessern [5]. Cu/Ti3 SiC2 /C-Verbundwerkstoffe sind ein neues vielversprechendes Materialsystem, das die Vorteile von Kupfer-Graphit-Verbundwerkstoffen und Ti3 . kombiniert SiC2 , aber die mechanischen Eigenschaften, die Verschleißfestigkeit und andere Leistungsparameter dieser Materialien bleiben unter bestimmten Bedingungen unzureichend [6].
Die Einführung gleichförmig dispergierter nanoskaliger Verstärkungspartikel in eine Metallmatrix führt zu Metallmatrix-Verbundwerkstoffen, die bessere mechanische Eigenschaften, elektrische Leitfähigkeit, Wärmeleitfähigkeit, Verschleißfestigkeit, Korrosionsbeständigkeit und Hochtemperatur- und Oxidationsbeständigkeit aufweisen können [7]. Eindimensionale mehrwandige Kohlenstoffnanoröhren (MWCNTs) und zweidimensionales Graphen sind aufgrund ihrer einzigartigen Struktur und Leistung attraktive Materialien für die Verbundverstärkung [8,9,10] und werden anstelle von Graphit zur Herstellung von Metallmatrix-Verbundwerkstoffen verwendet [ 11,12,13]. Dennoch bleiben die Leistungen von Kupfermatrix-Verbundwerkstoffen aus MWCNTs oder Graphen unzureichend. Es gibt viele Faktoren, die die Leistung dieser Materialien einschränken:Verteilung der Verstärkung in der Metallmatrix, Benetzbarkeit der Metallmatrix und die Grenzfläche der Metallmatrix.
Das Potenzial für die Integration zweidimensionaler Materialien in neue Heterostrukturen, die durch schwache Van-der-Waals-Wechselwirkungen gebunden sind, wurde durch eine zukunftsgerichtete Analyse demonstriert, in der die Möglichkeit der Kombination von Graphen mit anderen Strukturen untersucht wurde [14, 15] und deren Machbarkeit Ansatz nachgewiesen wurde [16]. Die meisten Studien zu synergistischen Verstärkungen durch MWCNTs und Graphen konzentrierten sich auf Polymermatrix-Verbundstoffe, in denen ein kontinuierliches, miteinander verbundenes Netzwerk durch synergistisch verstärkte Mechanismen erreicht werden kann [17,18,19]. Allerdings gibt es noch einige Schwierigkeiten bei der Verbesserung von Metallmatrix-Verbundwerkstoffen durch MWCNTs und Graphen. Es gibt Herausforderungen bei der Verwendung von eindimensionalen MWCNTs und zweidimensionalem Graphen, um die Eigenschaften eines dreidimensionalen geflochtenen Verbundmaterials zu erreichen, das synergistische kooperative und mehrskalige Verstärkungen erzeugen kann [20,21,22]. In dieser Arbeit wird Cu/Ti3 SiC2 /C-Komposite mit MWCNTs und Graphen wurden durch mechanisches Legieren, Vakuum-Heißpressen (VHP) und heißisostatisches Pressen (HIP) hergestellt. Oberflächenmodifikationen von MWCNTs und Graphen wurden durchgeführt, um ihre Dispersion zu verbessern. Mikrostruktur und mechanische Eigenschaften des hergestellten Cu/Ti3 SiC2 /C-Verbundstoffe wurden gemessen, um die Verstärkungseffekte zu bewerten. Basierend auf den experimentellen Ergebnissen wurden die Festigkeits- und Bruchmechanismen von Cu/Ti3 SiC2 /C-Kompositen werden diskutiert.
Methoden/Experimental
Unter Ausnutzung der überlegenen Eigenschaften von eindimensionalen Kohlenstoffnanoröhren und zweidimensionalem Graphen wurde eine synergistisch verstärkte Nanostruktur entwickelt, um Cu/Ti3 . herzustellen SiC2 /C-Nanokomposite durch einen mehrphasigen, synergistisch verstärkenden Prozess. Mechanisches Legieren, Heißpressen und HIP-Techniken wurden verwendet, um Cu/Ti3 . herzustellen SiC2 /C-Nanokomposite sowohl unter erhöhter Temperatur als auch unter hohem Druck. Die Eigenschaften der Rohmaterialpulver von MWCNTs, Graphen-Nanoplättchen (GNPs), elektrolytischem Kupferpulver, Graphitpulver und Ti3 SiC2 in diesem Experiment verwendete Pulver sind in Tabelle 1 aufgeführt. Dispersionen von MWCNTs und Graphen wurden durch Ultraschallschwingung unterstützt; Plasma- und chemische Oberflächenmodifikationen wurden unter Verwendung von Ar-NH3 . durchgeführt Plasma und 0,02 µg/ml Rutin oder 10 µg/ml Gallussäurelösung [23, 24]. Details der Zusammensetzungskonstruktion der Nanokomposite sind in Tabelle 2 aufgeführt. Die Materialien wurden durch Hochenergie-Kugelmahlen mit einer Achat-Mahlkugel gemischt, und das Nanocomposit-Pulver wurde in einem Massenverhältnis von 10:1 unter Verwendung von tert-Butylalkohol als Dispergiermedium verarbeitet. Die Mischpulver wurden nach dem Abbindeverfahren (Vakuum-Heißpressen:950 °C × 20 MPa × 2 h, heißisostatisches Pressen:900 °C × 100 MPa × 2 h) gesintert, um das Cu-Matrix-Nanokomposit zu erhalten [25] .Die relativen Dichten von Nanokompositmaterialien wurden durch Dichtemessung mit Flüssigkeitsdrainage basierend auf dem archimedischen Gesetz analysiert (Tabelle 3). Mikrostrukturen von Cu/Ti3 SiC2 /C-Nanokomposite wurden durch optische Mikroskopie (OM, AxioCam MRC5), Röntgenbeugungsanalyse (XRD, X'Pert Pro-MPD), Rasterelektronenmikroskop (REM, JEOL JSM-7001F bei 15 kV) mit einem energiedispersiven X . charakterisiert -Strahlenspektrometer (EDS) und Transmissionselektronenmikroskop (TEM, FEI Tecnai F20ST bei 200 kV). Die Härtemessung wurde unter Verwendung eines Vickers-Härtetesters (HV, HXD-1000TM) bestimmt. Zug-, Druck- und Scherversuche von Cu/Ti3 SiC2 /C-Nanokomposite wurden unter Verwendung einer mikrocomputergesteuerten elektronischen Universalprüfmaschine (WDW-3100) bei einer Belastungsgeschwindigkeit von 0,5 mm/min durchgeführt. Die Auswirkungen von MWCNTs und GNPs auf die Eigenschaften und Mikrostrukturen der hergestellten Cu-Matrix-Nanokomposite wurden bestimmt.
Ergebnisse und Diskussion
Pulvermikrostruktur- und Phasenidentifizierung
Mechanisches Legieren ist eine Technik, die eine Reihe physikalischer und chemischer Prozesse umfasst, wie wiederholte Verformung, Kaltschweißen und Brechen für Verbundpulver unter Verwendung von Hochenergie-Kugelmahlen. Die Pulver werden auf Mikrometer- oder sogar Nanogröße gemahlen. Sie werden gut gemischt, um Verbundpulver herzustellen. Es wird erwartet, dass dieses Mahlen die homogene Verteilung von GNPs/MWCNTs in der Kupfermatrix durch mechanisches Legieren verbessert und eine wünschenswerte Grenzflächenbindung durch Miniaturschmieden erreicht, wodurch die mechanischen Eigenschaften der resultierenden Materialien verbessert werden. Die REM-Bilder von Cu, Ti3 SiC2 , C, MWCNT und GNP-Pulver nach dem Kugelmahlen sind in Fig. 1 gezeigt. Die größeren Partikel sind Cu, und die kleineren Partikel, die gleichmäßig zwischen den Cu-Partikeln dispergiert sind, sind Ti3 . SiC2 und C. Bei einer höheren Vergrößerung waren der Brückenzustand von MWCNTs und der eingebettete Zustand von GNP-Pulvern, wie durch die Pfeile in Fig. 1 angezeigt, auf den peripheren Oberflächen der Cu-Partikel dispergiert. Durch Kaltschweißen kann die Kupfermatrix gut an GNPs/MWCNTs gebunden werden. BSP mit gewisser Transparenz und gewundene lineare MWCNTs wurden auf der Oberfläche oder im Inneren des Kupferpartikelagglomerats verteilt. Wie in Abb. 1a gezeigt, sind die meisten MWCNTs ungeordnet und auf der Oberfläche der Kupferpartikel verteilt. MWCNTs bildeten eine Brücke zwischen Kupferpartikel-Agglomeraten, wie im Inlay gezeigt und durch Pfeile angezeigt. Dies deutet darauf hin, dass das Kugelmahlverfahren die Grenzflächenbindung zwischen den verstärkenden MWCNTs und der Matrix fördert [26]. Wie in Abb. 1b gezeigt, waren Agglomerat-BSP auf der Oberfläche der Kupfermatrix verteilt. In BSP tritt Agglomeration auf, wie durch die Pfeile gezeigt. Die intrinsische extrem große spezifische Oberfläche von GNPs und das Vorhandensein der Van-der-Waals-Kraft erhöhten die Anfälligkeit für Agglomeration, verringerten die Dispersionsgleichförmigkeit und verringerten die Grenzflächenbindung. In 1c werden, wie durch die Pfeile gezeigt, kleine GNPs aufgrund der mechanischen Wirkung des Kugelmahlens, der Kollision und der Reibung zwischen Verbundpulverpartikeln und GNPs während des Kugelmahlens in die Matrix eingelegt, wodurch die Grenzflächenbindungsfestigkeit verbessert wird. Dennoch treten in GNPs viele Falten auf, wodurch die effektive Kontaktfläche zwischen GNP und der Matrix verringert wird. In Fig. 1d sind MWCNTs, wie durch die Pfeile angedeutet, in die Cu-Matrix eingelegt und auf der Oberfläche der Cu-Partikel ungeordnet verteilt. Im Allgemeinen ist der Mischprozess durch Kugelmühlen effizient, was zu einer effektiven Einlagerung einiger GNPs/MWCNTs in die Kupfermatrixpartikel führt. Trotzdem ist die Agglomeration von BSP/MWCNT immer noch sehr stark.
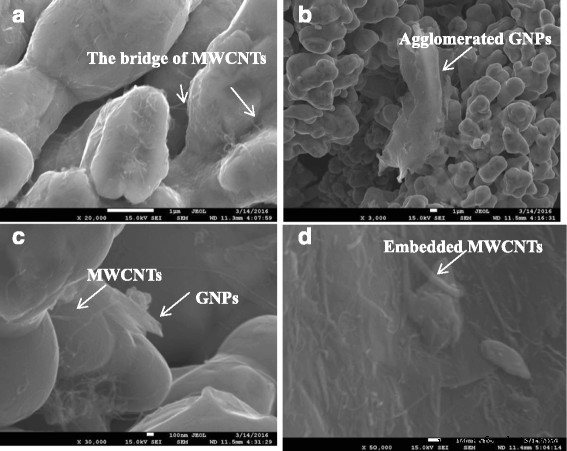
REM-Aufnahmen von Rohstoffen aus Cu, Ti3 SiC2 , C, MWCNT und Graphenpulver nach dem Kugelmahlen, aufgenommen bei geringer Vergrößerung (b ) und eine hohe Vergrößerung (a , c , d ). a –c Nanokomposite mit 0,5 Gew.-% Graphenen und 0,5 Gew.-% MWCNTs. d Nanokomposite mit 0,8 Gew. % Graphenen und 0,2 Gew. % MWCNTs
Die XRD-Ergebnisse von Rohstoffen einschließlich Cu, Ti3 SiC2 , C, MWCNTs und GNPs nach dem Kugelmahlen sind in Abb. 2 dargestellt. Die Ergebnisse zeigen Veränderungen in der neuen Phasenidentifikation vom Rohstoff zum mechanischen Legierungsprozess. Cu, Ti3 SiC2 , und Graphit wurden, wie in Fig. 2 gezeigt, nachgewiesen, was darauf hinweist, dass während des mechanischen Legierungsverfahrens keine Phasenidentifikation auftrat. Für CuO oder Cu2 . wurden keine Beugungspeaks beobachtet O, was darauf hinweist, dass das Kupferpulver nicht oxidiert wurde, die Zersetzungsreaktion für Ti3 . fand nicht statt SiC2 , und es trat keine chemische Reaktion auf.
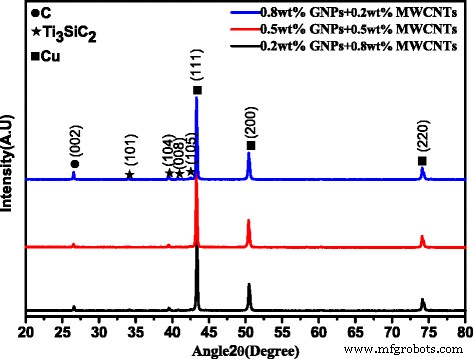
XRD-Muster von Rohstoffen nach dem Kugelmahlen. Nanokomposite mit 0,8 Gew. % Graphenen und 0,2 Gew. % MWCNTs, Nanokomposite mit 0,5 Gew. % Graphenen und 0,5 Gew. % MWCNTs und Nanokomposite mit 0,2 Gew. % Graphenen und 0,8 Gew. % MWCNTs
Nanokomposit-Phasen- und Mikrostruktur-Identifizierung
Die Kompaktheit von Nanokompositen, die mit 0,2 Gew. % Graphen und 0,8 Gew. % MWCNTs hergestellt wurden, entspricht ungefähr der Kompaktheit von Nanoverbunden, die mit 0,5 Gew. % Graphen und 0,5 Gew. % MWCNTs hergestellt wurden. Die Kompaktheit nahm jedoch auf 96,43 % ab, wenn die Zusammensetzung 0,8 Gew. % Graphen und 0,2 Ge % MWCNTs enthielt. Wie oben erwähnt, zeigt die Agglomeration der Verstärkungsphase mit zunehmendem Gehalt an GNP einen zunehmenden Trend und schwächt somit ihre Wirkung auf die Kornfeinung ab und behindert das Sintern und Binden, die Bildung und das Wachstum des Sinterhalses und die Lückenschließung zwischen Cu-Partikeln . Auf diese Weise können die GNPs Diffusion und Migration zwischen Cu-Atomen beeinflussen und die Porosität erhöhen. Daher nahm die Kompaktheit gesinterter Nanokomposite mit steigendem BSP ab. In dem Experiment war die Kompaktheit von Nanokompositen, die mit 0,2 Gew. % Graphen und 0,8 Gew. % MWCNTs hergestellt wurden, geringer als die von Nanoverbunden, die mit 0,5 Gew. % Graphen und 0,5 Gew. % MWCNTs hergestellt wurden, aber dieser Unterschied ist sehr gering. Folglich erhöhte die synergistische Verstärkung von GNP/MWCNT die Verstärkungsagglomeration und verringerte den Kornverfeinerungseffekt, wodurch das Sintern von Cu-Partikeln, die Bildung und das Wachstum von gesinterten Hälsen und der Spaltschlussprozess behindert werden. Insgesamt beeinflussten die GNPs/MWCNTs die Diffusion von Cu-Atomen zwischen der Matrix und den Verstärkungen, um die Grenzflächenbindung zu reduzieren und die Porosität des Nanokomposits zu erhöhen.
In den metallographischen Mikrostrukturinformationen in Fig. 3 ist die weiße Struktur die Cu-Matrix, die graue Struktur ist Ti3 . SiC2 , und der schwarze Teil ist C oder das Loch. Die Cu-Phasen sind im Wesentlichen verbunden, um die Matrix zu bilden, die eine diskontinuierliche netzwerkartige Struktur ist, die auf Ti3 . verteilt ist SiC2 oder TiC. Der Graphit wird jedoch vollständig isoliert verteilt, so dass der größte Teil des Graphits in der Cu-Matrix in einer kleineren, wurmähnlichen Form oder einer unregelmäßigen flockigen Form gleichmäßig verteilt ist, wodurch die Antifriktions-Schmiereigenschaften des gesinterten Nanokomposits verbessert werden. Beim Sintern der Nanokomposite interagieren Cu-Partikel nicht mit dem Ti3 SiC2 und das Graphitpulver. Die halbgeschmolzenen Cu-Partikel werden in die Kupfermatrix gesintert, nachdem sie miteinander in Kontakt gekommen sind, um eine Bindungsoberfläche zu bilden, die die Bildung und das Wachstum eines Sinterhalses und die Bildung geschlossener Poren ermöglicht. Der ursprüngliche mechanische Eingriff wandelt sich in eine interatomare metallurgische Verbindung um. Die Graphit- oder agglomerierten GNPs und MWCNTs werden in geschlossenen Poren zurückgehalten, um den schwarzen Bereich zu bilden, der in der metallographischen Mikrostruktur sichtbar ist. Die Ti3 SiC2 Pulver wird auch einem Sinterprozess mit Cu-Partikeln unterzogen, wodurch das graue Ti3 . gebildet wird SiC2 Bereich in der metallographischen Mikrostruktur. Laut dem Forschungsbericht zur XRD-Analyse ähnlicher gesinterter Nanokomposite sind die Unterschiede wie folgt:Ti3 SiC2 wird bei einer Sintertemperatur von 950 °C in Si und TiC zerlegt [27]. Si-Atome und die Kupfermatrix reagieren zu Cu9 Si, das die Grenzflächenbindung zwischen der Cu-Matrix und Ti3 . erhöht SiC2 [27].
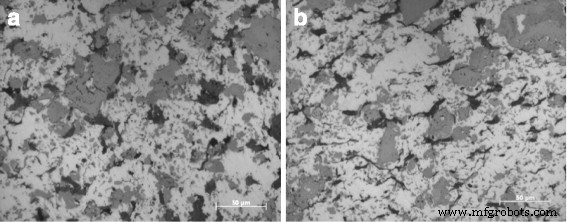
Metallographische Ergebnisse von gesinterten Nanokompositen mit 0,8 Gew. % Graphenen und 0,2 Ge % MWCNTs in verschiedenen Richtungen (a ist parallel zum Druck und b ist eine Senkrechte zum Druck)
Die metallurgische Phase von Nanokompositen ist in Fig. 3 in Längs- und Querrichtung relativ zur Heißpressrichtung dargestellt. Es gibt signifikante Unterschiede in der metallurgischen Phasenmikrostruktur senkrecht und parallel zur Heißpressrichtung. Der Graphit im schwarzen Bereich senkrecht zur Heißpressrichtung weist eine flockige Form auf, und der Graphit im schwarzen Bereich parallel zur Heißpressrichtung weist eine schlankere Form auf. Die Gründe für diesen Unterschied sind folgende:Das Heißpressen-Sinterverfahren ist ein einfachwirkendes Pressen. Auf das Verbundpulver wird in einer zylindrischen Graphitdüse vertikaler Druck ausgeübt. Es gibt erhebliche morphologische Unterschiede zwischen dem Graphit senkrecht zur Heißpressrichtung und dem Graphit parallel zur Heißpressrichtung, da der Graphit von Natur aus flauschig ist. Diese Unterschiede bleiben nach dem isostatischen Pressen erhalten, da die auf den Verbundgrünkörper aufgebrachten Drücke während des isostatischen Pressens nach dem Heißpress-Sinterschritt in jeder Richtung gleich sind. Somit bleiben die morphologischen Unterschiede, die beim Heißpresssintern entstanden sind, erhalten.
Um die Produkte weiter zu identifizieren, wurde die Nanokomposit-Mikrostruktur von EPMA für die Elementarkartierung analysiert. Wie in Fig. 4a gezeigt, zeigt das Rückstreubild (BS) Cu-Körner mit höherem Kontrast und Ti3 SiC2 und C befanden sich zwischen Cu-Körnern mit dunklerem Kontrast. Basierend auf der Cu-Verteilung in den in Fig. 4b gezeigten gesinterten Nanokompositen stellt der rote Bereich Cu dar und ist die Mehrheit des Materials. Die roten hellen Punkte in Fig. 4c repräsentieren das C-Element. Daraus lässt sich schließen, dass im Nanokohlenstoff Agglomeration auftritt. Basierend auf der Beobachtung der Verteilung von Ti in Fig. 4d ist der gelbe unregelmäßige helle Fleck, der über die gesamte Matrix verteilt ist, Ti, entsprechend der grauen Phase in Fig. 4a. In ähnlicher Weise repräsentieren die grünen hellen Punkte in Fig. 4e die Verteilung von Si in den gesinterten Nanokompositen. Basierend auf dieser Beobachtung wird Si gleichmäßig verteilt. La wird auch in den gesinterten Nanoverbundstoffen dispergiert, und die roten hellen Flecken in Fig. 4f stellen La dar. La wird hinzugefügt, um die Kompaktheit der gesinterten Nanoverbundstoffe zu erhöhen. Die beobachtete homogene Verteilung in den gesinterten Nanokompositen ist sehr wichtig für die resultierenden Eigenschaften der hergestellten Materialien.
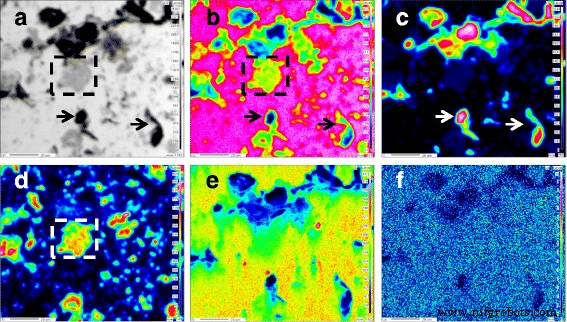
EPMA-Analysen von gesinterten Nanokompositen mit 0,2 Gew. % Graphenen und 0,8 Gew. % MWCNTs. a BS-Bild, b Cu-Karte, c C-Karte, d Ti-Karte, e Si-Karte und f La Karte
Hellgraue Flecken von Ti3 SiC2 wurden beobachtet und sind in der gestrichelten Box in Fig. 4a angegeben, und Cu und Ti sind in der gestrichelten Box in Fig. 4b, d vorhanden. Innerhalb des Kastens mit gestrichelten Linien in Fig. 4b ändert sich die Farbe von hellrot nach grün von der Matrix zur Mitte der hellen Flecken, was anzeigt, dass die Konzentration von Cu allmählich abnimmt. Innerhalb des gestrichelten Kastens in Fig. 4c ändert sich die Farbe von Ti von orange im Inneren zu grün im Äußeren. Daraus lässt sich schließen, dass die Konzentration von Ti3 SiC2 nimmt allmählich ab. Diese Ergebnisse legen nahe, dass die Cu-Phase und Ti3 SiC2 Phase sind eng gebunden und Cu und Ti3 SiC2 haben eine hohe Benetzbarkeit [27].
Basierend auf der Beobachtung und dem Vergleich der durch die Pfeile in Abb. 4a-c angezeigten Bereiche kann gefolgert werden, dass die schwarze kaulquappenartige Substanz hauptsächlich C umfasst. Wie in Abb. 4c gezeigt, ist das Zentrum von C hellrot, was darauf hinweist, dass die Konzentration von C hoch ist. Ein grüner Kreis um die leuchtend roten Punkte zeigt an, dass die Konzentration von C von der Mitte der hellen Punkte nach außen hin allmählich abnimmt. Wie durch die Pfeile in Fig. 4b angezeigt, ändert sich die Farbe von hellrot zu grün und dann ist die endgültige Farbe dunkelblau und bewegt sich von der Matrix in die Mitte der hellen Flecken. Die Farbänderungen zeigen an, dass die Konzentration von Cu allmählich abnimmt. Solche allmählichen Veränderungsprozesse der beiden Elemente bestätigen die gegenseitige Diffusion von C und Cu, was auf eine enge Bindung zwischen der C-Verstärkungsphase und der Cu-Matrix schließen lässt. Der Cu-Gehalt in der roten gestrichelten Linie ist hoch und stabil, und der entsprechende C-Gehalt ist niedrig, aber stabil, was darauf hindeutet, dass eine geringe Menge an C in Cu diffundiert. Cu und C würden unter den Versuchsbedingungen nicht zu neuen Stoffen reagieren. Diese Ergebnisse legen nahe, dass C teilweise in Cu diffundiert und die Cu- und C-Form gut gebunden sind.
Abbildung 5 zeigt die Ergebnisse des linearen Scans an einer zufälligen Position von Nanokompositen, die mit 0,2 Gew. % Graphen und 0,8 Gew. % MWCNTs hergestellt wurden. Abbildung 5a zeigt die Linienverteilung von Cu-Elementen und Fig. 5b ist die Linienverteilung des C-Elements. Der Cu-Elementgehalt ist am roten gestrichelten Kasten hoch und bleibt stabil. Der entsprechende C-Element-Gehalt ist gering und bleibt zudem stabil. Dies kann zumindest teilweise die Diffusion einer kleinen Menge C in Cu erklären, da Cu und C unter diesen experimentellen Bedingungen nicht reagieren, um eine neue Phase zu erzeugen. Daher stellen Cu und C eine gute Kombination dar, da Kohlenstoffatome in Kupferatome diffundieren können.
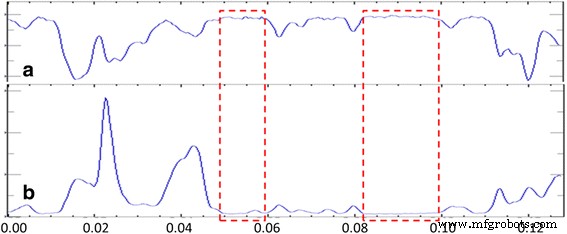
Elementverteilungslinienscannen von gesinterten Nanokompositen mit 0,2 Gew. % Graphenen und 0,8 Gew. % MWCNTs. a Cu und b C
Ein TEM-Bild der hergestellten Nanokomposite mit 0,5 Gew.-% Graphen und 0,5 Gew.-% MWCNTs ist in Fig. 6 gezeigt. 6a ist ein TEM-Bild, das eine Nanokohlenstoff-Mikrostruktur in einer Cu-Matrix zeigt, und Fig. 6b ist ein vergrößertes TEM-Bild von 6a. wobei die Mikrostruktur des Nanokohlenstoffs, die in dieser in Abb. 6a eingefügten Abbildung zu finden ist, die EDS-Spektren sind, die von den markierten Kreuzsymbolflecken 1 und 2 aufgenommen wurden. Abb. 6c, d ist eine hochauflösende TEM-Bildanalyse aus die markierten Kreuzsymbolpunkte 1 und 2 in Fig. 6a. In Verbindung mit den Ergebnissen der morphologischen und EDS, führt zu dem Schluss, dass Nano-Kohlenstoff stabförmig ist, seine Atomanordnung sich deutlich von der von Kupferatomen unterscheidet und gut kombiniert, während Beugungsringe in Abb. 6c, d GNPs und MWCNTs anzeigen ' Agglomeration ist ernst [28].
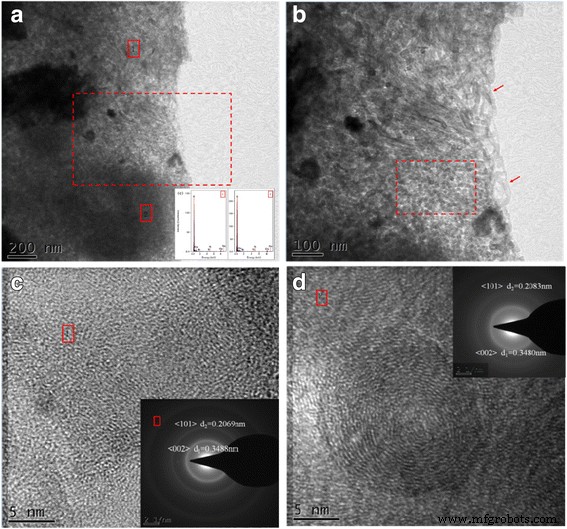
a –d TEM-Bild in gesinterten Nanokompositen mit 0,5 Gew. % Graphenen und 0,5 Gew. % MWCNTs. a TEM-Bild zeigt Nano-Kohlenstoff-Mikrostruktur in Cu; b Vergrößertes TEM-Bild von Fig. 6a; c Hochauflösende TEM-Bildanalyse, aufgenommen von den markierten Kreuzsymbolflecken 1 in Fig. 6a; d Hochauflösende TEM-Bildanalyse, aufgenommen von den markierten Kreuzsymbolflecken 2 in Fig. 6a. Eingefügt in a sind EDS-Spektren, die von den markierten Kreuzsymbol-Spots 1 und 2 aufgenommen wurden
Abbildung 7a ist das TEM-Bild von Graphen in den gesinterten Nanokompositen, die mit 0,5 Gew. % Graphen und 0,5 Gew. % MWCNTs hergestellt wurden. Aus Abb. 7a ist ersichtlich, dass Graphen in der Cu-Matrix vorhanden ist. Das in Fig. 7a eingefügte Ergebnis sind die EDS-Spektren aus Fig. 7a. Das Graphen erscheint durchscheinend, die Kanten sind gekräuselt und das Graphen befindet sich im Verbund immer noch größtenteils in einer Monoschicht mit gleichmäßiger Verteilung.
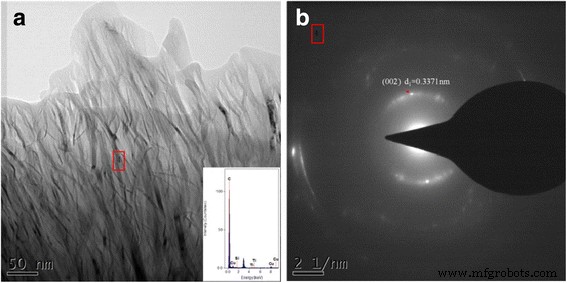
a TEM-Bild von Graphenen in gesinterten Nanokompositen mit 0,5 Gew. % Graphenen und 0,5 Gew. % MWCNTs. b Beugungsmuster aus Abb. 7a. In Abb. 7a eingefügt ist ein EDS-Spektrum aus Abb. 7a
Abbildung 8 zeigt die XRD-Muster der Nanokomposite, in denen TiC und Cu9 Si wurden nachgewiesen. Diese Ergebnisse ähneln den Ergebnissen in Abb. 2 der Nanokomposit-Pulver und drei Arten von Cu/Ti3 SiC2 /C/Graphen-Komposite. Die Ti3 SiC2 wird bei hoher Temperatur zersetzt, und die Zersetzungsprodukte und die Cu-Matrix reagieren, um Cu9 . zu erzeugen Si. Bei hoher Temperatur wird die spezielle Zwischenschicht schwach bindende Struktur von Ti3 SiC2 kann es dem Si-Atom leicht machen, die Zwangsbindung aufzubrechen, um Si frei zu bilden. Das zersetzte Si tritt in die Cu-Matrix ein, um eine Cu-Si-Mischkristalllösung zu bilden [27]. TiC ist ein Zersetzungsprodukt von Ti3 SiC2 beim Sintern als Si-Atome getrennt von Ti3 SiC2 [27]. TiC ist eine harte spröde Phase mit einem hohen Schmelzpunkt, hat also hohe Härteeigenschaften. Cu9 Si ist auch eine harte spröde Phase. Sowohl TiC als auch Cu9 Si kann eine Spannungskonzentration verursachen, die die Leistung der Nanokomposite verringern kann.
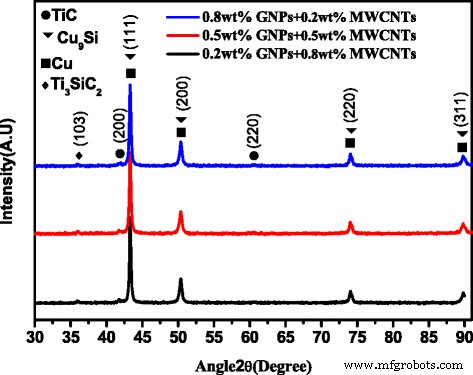
XRD-Muster von gesinterten Nanokompositen:Nanokomposite mit 0,8 Gew. % Graphen und 0,2 Gew. % MWCNT, Nanoverbunde mit 0,5 Gew. % Graphen und 0,5 Gew. % MWCNT und Nanoverbunde mit 0,2 Gew. % Graphen und 0,8 Gew. % MWCNTs
Die thermodynamische Analyse der möglichen Reaktionen kann durch die folgenden Reaktionen während des Sinterprozesses von Verbundwerkstoffen [11] analysiert werden:
$$ {\mathrm{Ti}}_3{\mathrm{SiC}}_2=3{\mathrm{Ti}\mathrm{C}}_{2/3}+\mathrm{Si} $$ (1) $ $ \mathrm{C}+\mathrm{Si}=\mathrm{SiC} $$ (2) $$ \mathrm{SiC}+9\mathrm{Cu}={\mathrm{Cu}}_9\mathrm{Si }+\mathrm{C} $$ (3) $$ \mathrm{Si}+9\mathrm{Cu}={\mathrm{Cu}}_9\mathrm{Si} $$ (4)Die freie Gibbs-Reaktionsenergie (1), in der Ti3 SiC2 zerlegt wird als:Δ r G m = ∑ ν B Δf G m = ‐ 106.52kJ/mol < 0, was darauf hinweist, dass die Reaktion ablaufen kann [11]. Für Reaktion (2) kann die freie Gibbs-Energie der Reaktion wie folgt berechnet werden:(4) − (3) = (2) und Δr Gm der Reaktion (2) beträgt – 66,99 kJ/mol. Somit tritt Reaktion (4) tendenziell häufiger auf als Reaktion (3), was mit der Abwesenheit von SiC-Verbindungen in der XRD-Phasenanalyse übereinstimmt.
Mechanische Eigenschaften und Zugbruchanalyse von Nanokompositmaterialien
Die Proben wurden mit einem Micro-Vickers-Härteprüfgerät getestet, bei dem die Verbundhärte als
. angegeben ist $$ \mathrm{HV}=\frac{0,102F}{A}=0,1891\frac{F}{d^2} $$ (5)wobei HV die Mikro-Vickers-Härte ist, F ist die Belastung (gf), A ist die Oberfläche von Vertiefungen (mm 2 ) und d ist der Resteindruck von zwei Diagonallängen, d = (d1 + d2)/2.
Die Ergebnisse der Mikro-Vickers-Härtetests für die Nanokomposite wurden ermittelt und sind in Tabelle 4 aufgeführt. Die Mikrohärte der gesinterten Nanokomposite zeigte einen leicht abnehmenden Trend und sank von 97,787 auf 96,859, wenn sich die Zusammensetzung von 0,5 Gew.-% Graphen und 0,5 Gew.-% änderte. MWCNTs bis 0,2 Gew. % Graphen und 0,8 Gew. % MWCNTs. Die Mikrohärte der gesinterten Nanokomposite nahm jedoch signifikant um 9,4 % ab und ging von 97,787 auf 88,626 zurück, als der Gehalt an GNP auf 0,8 Gew. % stieg. Insgesamt zeigte die Härte der gesinterten Nanokomposite mit steigendem GNP-Gehalt einen abnehmenden Trend. Wesentliche Ursachen für den Trend sind folgende:(1) Mit zunehmendem BSP-Gehalt kommt es eher zu einer Agglomeration in BSP als in MWCNTs, da BSP einen größeren Durchmesser haben. Schließlich kam es in der Verstärkungsphase zu einer Agglomeration, da BSP und MWCNT anstiegen. Die Agglomeration verringert somit die Zahl der kraftübertragenden Verstärkungsphasen und verringert die Härte der gesinterten Nanokomposite [11, 13, 22]. Das Sintern verringert die Bindung zwischen den Matrizen, erhöht den Hohlraumanteil und verringert die Kompaktheit und die Härte der gesinterten Nanokomposite [11, 13, 22]. (2) Mit steigendem BSP-Gehalt sinkt der entsprechende MWCNT-Gehalt.
Die gemessenen mechanischen Eigenschaften der Nanokomposite sind in Tabelle 4 aufgeführt. Wenn der weiche Spannungskoeffizient (α) des einachsigen Drucktests 2 beträgt, ist er weicher als der Zugspannungszustand und kann das mechanische Verhalten des spröden Materials in zeigen der plastische Zustand. Aus Tabelle 4 nahm die Druckfestigkeit der Nanokomposite mit steigendem GNP-Gehalt ab. Die Druckfestigkeitsunterschiede der Nanokomposite lagen bei den Nanokompositen, die mit 0,2 Gew.-% und 0,5 Gew.-% BSP hergestellt wurden, innerhalb von 2 %. Das mit 0,8 Gew. % BSP hergestellte Material zeigte eine Abnahme der Druckfestigkeit um 12 %. Ebenso sank die Zugfestigkeit der Nanokomposite um 12%. Bei Nanokompositen, die durch BSP und MWCNT synergistisch verstärkt werden, nimmt die Agglomeration von BSP und MWCNT mit steigender BSP-Menge zu, was zu einer ungleichmäßigen Verteilung von BSP und MWCNT in den Nanokompositen führen kann. Auch die Bildung von unregelmäßigen Mikrorissen nahm im Kompressionssinterprozess zu, und die Grenzflächenbindung mit der Kupfermatrix war aufgrund der Agglomeration schlecht, was schließlich zu einer verringerten Druck- und Zugfestigkeit der Nanokomposite führte [22].
Tabelle 4 zeigt auch die Scherfestigkeitsdaten der Nanokomposite. Wie oben gezeigt, scheint der allgemeine Trend mit steigendem BSP-Gehalt eine abnehmende Scherfestigkeit zu sein. Die Scherfestigkeitsunterschiede der Nanokomposite sind bei den Nanokompositen mit 0,2 Gew. % und 0,5 Gew. % BSP gering (nur bis zu 3,6 %). Für das 0,8 Gew. % BSP-Material nahm die Scherfestigkeit der Nanokomposite jedoch um 20,6 % ab. Der beobachtete Trend der Scherfestigkeitsänderung der Nanokomposite stimmt mit der Zug- und Druckfestigkeit der Nanokomposite überein. Dies liegt daran, dass die Scherfestigkeit die Materialkohäsion einschließlich der atomaren oder intermolekularen Verbindungskraft widerspiegelt, so dass die Scherfestigkeit als Indikator für die Grenzflächenbindungsstärke zwischen der Kupfermatrix und der Verstärkungsphase verwendet werden kann. Die BSP- und MWCNT-Agglomeration nahm mit der Zunahme des BSP-Gehalts zu, was zu einer ungleichmäßigen Verteilung von BSP und MWCNT in den Nanokompositen führen kann. Gleichzeitig ermöglichen die große spezifische Oberfläche und die geringe Dicke zwischen Graphen und der Kupfermatrix Grenzflächenhaftung und Scherfestigkeitsübertragung [29]. Thereby, a decline in the shear-lagging enhancement phase could result in a decrease of the shear strength of the nanocomposite material.
Tensile deformation curves of nanocomposites were determined and are shown in Fig. 9. The tensile strength of the sintered nanocomposites primarily depends on the compactness of sintered nanocomposites, homogeneous dispersion of the reinforcement phase, and interface bonding between the reinforcement phase and the matrix (or wettability). With increased content of GNPs, the tensile strength of the sintered nanocomposites exhibited a decreasing trend. There were minor differences in tensile strength between the sintered nanocomposites prepared with 0.2 wt% GNPs or 0.5 wt% GNPs. However, the tensile strength of the sintered nanocomposites decreased by 12% when the content of GNPs increased to 0.8 wt%. This is consistent with the variation trend of the compactness of the sintered nanocomposites. With the increase of the content of GNPs, the agglomeration of the reinforcement phase increases and the extent of heterogeneous distribution in the sintered nanocomposites increases, thus loosening the organization of the sintered nanocomposites [30]. Agglomeration of GNPs and MWCNTs prevents the effects of improved strength and reinforcement, thus decreasing the tensile strength of the sintered nanocomposites. If the extent of agglomeration of the reinforcement phase increases, the extent of irregular microcracks would also increase during the pressing-sintering process. This results in increased stress concentration and decreased effective bearing area of the stress. Finally, the tensile strength of the sintered nanocomposites decreases. Due to the non-wetting between the Cu matrix and GNPs and MWCNTs, the interface bonding is dominated by physical and mechanical bonding. The dispersion is much better and certain interface bonding occurs for low GNPs and MWCNTs. In this study of GNP/MWCNT synergistic action, with an increase of GNPs, the agglomeration extent of the reinforcement phase increased and the interface bonding was weak, thus decreasing the capacity of the reinforcement phase to transmit the load and finally decreasing the tensile strength of the sintered nanocomposites [22].
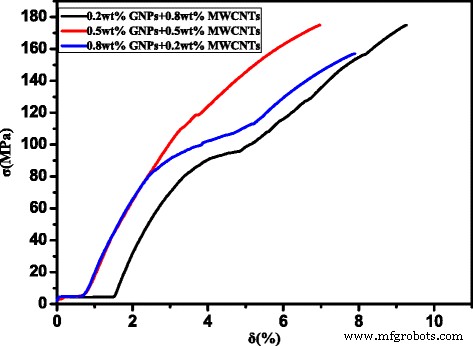
Tensile deformation curves of sintered nanocomposites:Nanocomposites with 0.8 wt% graphenes and 0.2 wt% MWCNTs, nanocomposites with 0.5 wt% graphenes and 0.5 wt% MWCNTs, and nanocomposites with 0.2 wt% graphenes and 0.8 wt% MWCNTs
In summary, co-operative enhancement effects of multi-phase reinforcements were significantly higher than single MWCNT enhancement effects or without GNP/MWCNT synergistic action for the mechanical properties of Cu/Ti3 SiC2 /C, Cu/Ti3 SiC2 /C/MWCNTs, and Cu/Ti3 SiC2 /C nanocomposites reinforced by MWCNTs and graphene. These enhancing effects include grain refinement strengthening, load transfer strengthening, Orowan mechanism strengthening, and large interface strengthening of GNPs.
Figure 10 presents SEM analyses of tensile fracture microscopic process of the nanocomposites. As shown in Figs. 10a, b, the fracture surface of the nanocomposites exhibits a typical dimple and cleavage fracture pattern. Simultaneously, due to non-wetting phenomenon between GNPs, MWCNTs, and the Cu matrix, or due to defects in the sintering process, cracks or holes were evident, as indicated by arrows 2 and 3. This is consistent with the absence of GNPs, MWCNTs, and Cu matrix in the TEM analysis. Stress concentration occurs at cracks or holes of nanocomposites, and microcracks can initiate in these regions to form cracks or holes that can propagate and lead to fracture. Graphene itself has a large specific surface area that increases the contact area with the Cu matrix to promote interface bonding, but also makes it more prone to agglomeration [13]. In Fig. 10c, graphene sheets are pulled out during the tensile test as indicated by arrows 2 and 3. The two arrows show interface bonding between graphene and the Cu matrix. The agglomerated graphene atoms are pulled out from the adjacent micro-cracks at arrow 2, because the agglomeration of graphene leads to the formation of cracks. The graphene is embedded in the Cu matrix because the interface bonding is good between the graphene and the Cu matrix. However, agglomerated graphene sheets can be seen in Fig. 10d and are not effectively transferred during loading in the matrix. Under tensile stress, agglomerations can form micro-cracks and extend sequentially into a crack or form a secondary crack [13, 22, 30]. Additionally, the unique fold structure of graphene can be seen as indicated by the arrow in Fig. 10d. The graphene atoms are first flattened and then rupture when subjected to stress, leading to a certain strengthening-toughening effect. As shown in Fig. 10e, MWCNTs have been embedded in the Cu matrix, explaining MWCNTs good loading transfer ability and the improved tensile strength of the nanocomposites [11]. Nevertheless, as shown in Fig. 10e, f, the disordered aggregation of MWCNTs is observed, and micropores or microcracks are formed in the agglomeration region, which decrease the strength of the nanocomposites.
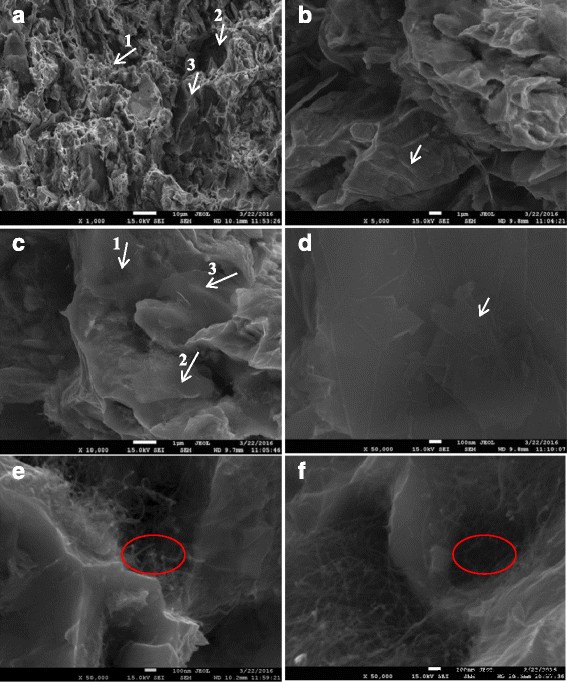
a −f SEM images of fractures of the sintered nanocomposites with 0.5 wt% graphenes and 0.5 wt% MWCNTs
Schlussfolgerungen
The following conclusions can be drawn based on microstructural and mechanical evaluation of Cu/Ti3 SiC2 /C nanocomposites reinforced with MWCNTs and graphene.
- 1.
Powder metallurgy techniques (vacuum hot-pressing and hot isostatic pressing) can successfully be applied to synthesize Cu/Ti3 SiC2 /C nanocomposites reinforced with MWCNTs and graphene.
- 2.
The synergetic effect of sintered nanocomposites primarily depends on the compactness of the sintered nanocomposites, the homogeneous dispersion of the reinforcement phase, and interface bonding between the reinforcement phase and the matrix.
- 3.
The optimum value of Cu/Ti3 SiC2 /C nanocomposites was reinforced with 0.8 wt% MWCNTs and 0.2wt% graphene. When GNPs and CNTs are used as the synergistically reinforced matrix, with the increase of GNPs content, reinforcement agglomeration increasingly affects the strengthening and fracture mechanism of the resulting materials.
- 4.
Enhanced properties of Cu/Ti3 SiC2 /C nanocomposites reinforced with MWCNTs and graphene include grain refinement strengthening, load transfer strengthening, Orowan mechanism strengthening, and large interface strengthening of GNPs.
Abkürzungen
- EDS:
-
Energy dispersive X-ray spectrometer
- HIP:
-
Hot isostatic pressing
- MWCNTs:
-
Multi-walled carbon nanotubes
- OM:
-
Optical microscopy
- SEM:
-
Rasterelektronenmikroskop
- TEM:
-
Transmission electron microscope
- VHP:
-
Vacuum hot-pressing
- XRD:
-
Röntgenbeugung
Nanomaterialien
- Doppelte Nichtlinearitätskontrolle von Moden- und Dispersionseigenschaften in graphen-dielektrischen plasmonischen Wellenleitern
- Mit Titanat-Nanoröhren dekorierte Graphenoxid-Nanokomposite:Vorbereitung, Flammhemmung und Photoabbau
- Auswirkung des Einschlusses auf die photophysikalischen Eigenschaften von P3HT-Ketten in einer PMMA-Matrix
- Die Wirkung von Kontakt-Nichtgleichgewichtsplasma auf die strukturellen und magnetischen Eigenschaften von Mn Х Fe3 − X О4 Spinellen
- Infraroteigenschaften und Terahertz-Wellenmodulation von Graphen/MnZn-Ferrit/p-Si-Heterojunctions
- Paramagnetische Eigenschaften von Fulleren-abgeleiteten Nanomaterialien und ihren Polymerverbundstoffen:Drastischer Pump-Out-Effekt
- Magnetische Poly(N-isopropylacrylamid)-Nanokomposite:Einfluss des Herstellungsverfahrens auf die antibakteriellen Eigenschaften
- Bewertung von Graphen/WO3- und Graphen/CeO x -Strukturen als Elektroden für Superkondensatoranwendungen
- Synergetische Wirkung von Dy2O3- und Ca-Co-Dotanden auf eine verbesserte Koerzitivfeldstärke von seltenen Erden reichlich vorhandenen RE-Fe-B-Magneten
- Eigenschaften technischer Werkstoffe:Allgemeines, Physikalisches und Mechanisches