Sinterverhalten von funkenplasmagesintertem SiC mit Si-SiC-Verbund-Nanopartikeln, die durch thermisches DC-Plasmaverfahren hergestellt wurden
Zusammenfassung
Das Si-beschichtete SiC (Si-SiC) Verbundnanopartikel wurde durch nicht übertragene Lichtbogen-Thermoplasmabearbeitung von festkörpersynthetisiertem SiC-Pulver hergestellt und als Sinteradditiv für die SiC-Keramikbildung verwendet. Gesinterte SiC-Pellets wurden durch Spark Plasma Sintering (SPS)-Verfahren hergestellt, und die Wirkung von Si-SiC-Verbundpartikeln in Nanogröße auf das Sinterverhalten von SiC-Pulver in Mikrometergröße wurde untersucht. Das Mischungsverhältnis von Si-SiC-Komposit-Nanopartikel zu mikrometergroßem SiC wurde auf 10 Gew.-% optimiert. Die Härte und relative Dichte von Vicker wurden mit steigender Sintertemperatur und Haltezeit erhöht. Die relative Dichte und die Vicker-Härte wurden durch Reaktionsbindung mit zusätzlicher Aktivkohle an die Mischung aus mikrometergroßem SiC und nanoskaligem Si-SiC weiter erhöht. Die maximale relative Dichte (97,1 %) und die Vicker-Härte (31,4 GPa) wurden bei 1800 °C Sintertemperatur für 1 min Haltezeit aufgezeichnet, wenn 0,2 Gew.-% zusätzliche Aktivkohle zu der Mischung aus SiC/Si-SiC hinzugefügt wurden.
Hintergrund
Keramiken aus Siliziumkarbid (SiC) haben aufgrund ihrer phänomenalen Eigenschaften, wie Hochtemperaturhärte, Verschleißfestigkeit, niedriger Wärmeausdehnungskoeffizient, hohe Wärmeleitfähigkeit, starke Korrosionsbeständigkeit und hohe Stabilität in aggressiver Umgebung, große Aufmerksamkeit auf sich gezogen für verschiedene Bereiche wie Turbinenschaufeln, Dieselmotorteile und Materialien für Luft- und Raumfahrt und Kernreaktoren [1,2,3,4,5,6]. Aufgrund der kovalenten Natur der Si-C-Bindung und des geringen Selbstdiffusionskoeffizienten ist es jedoch schwierig, SiC ohne Zusätze zu verdichten [7, 8]. Die Bulk-SiC-Materialien werden normalerweise entweder durch gesintertes Siliziumkarbid in festem Zustand (SSS-SiC) oder durch gesintertes Siliziumkarbid in flüssiger Phase (LPS-SiC) aus den Ausgangs-kristallinen SiC-Pulvern hergestellt [7, 8]. Im Fall von SSS-SiC wurden keine flüssigkeitsbildenden Zusätze wie Bor, Aluminium, Kohlenstoff oder deren Verbindungen zur Verdichtung von SiC durch die Reduzierung der Oberflächenenergie der Körner und die Reaktion zwischen auf der Oberfläche vorhandenem Siliciumdioxid und Kohlenstoff. Dieser Prozess erfordert jedoch zum Sintern eine Temperatur von über 2000 °C [7, 9, 10]. LPS-SiC wird durch die Flüssigphasenbildung des Metalloxidadditivs bei der Sintertemperatur bestimmt und diese Flüssigphase wirkt während des SiC-Sinterns als Stofftransportmedium [8, 11, 12]. Außer Magnesiumoxid und Aluminiumoxid werden hauptsächlich Yttriumoxid und andere Seltenerdoxide als Sinteradditive verwendet, und die Sintertemperatur kann bis auf 1850 °C gesenkt werden, abhängig von der verwendeten Kombination von Sinteradditiven [11, 12]. Die Anwesenheit der amorphen Silikatverbindung an den Korngrenzen und den Tripelpunkten führt jedoch im Vergleich zu SSS-SiC zu einer Abnahme der Härte und der Hochtemperatur-Kriechfestigkeit [12]. Die zur Verbesserung der Verarbeitung verwendeten Additive werden jedoch unweigerlich zu einer „schwachen“ Sekundärphase in der fertigen Keramik, die normalerweise ihre mechanischen Eigenschaften bei hoher Temperatur verringert [13]. Dieser nachteilige Effekt lässt darauf schließen, dass ein möglichst geringer Anteil an Additiven wünschenswert ist. Darüber hinaus hängt die Wirksamkeit der Additive stark von der Homogenität ihrer Verteilung ab [13]. Es gibt auch einen anderen Ansatz zur Herstellung von Bulk-SiC, der als reaktionsgebundenes Siliziumkarbid (RB-SiC) bezeichnet wird. Bei RB-SiC führt die Reaktion von geschmolzenem Silizium mit Kohlenstoffpulver zur Bildung von SiC [13,14,15,16]. Obwohl dieser Ansatz eine niedrigere Sintertemperatur erfordert und es keine Beschränkung der Produktform und -größe gibt, ist die geringe Dichte der Körper ein Nachteil [17, 18]. Die Absenkung der Sintertemperatur ist jedoch wesentlich, um Energie zu sparen. In letzter Zeit wird Energieeinsparung zur treibenden Kraft, um andere geeignete Verfahren für die Herstellung von SiC-Keramikmassen bei niedrigen Temperaturen zu finden.
Vor kurzem wurde SiC in Nanogröße umfassend untersucht, um ihre mechanischen, physikalischen und chemischen Eigenschaften zu untersuchen, die sich von denen in Bulk-Formen unterscheiden und oft nützlich sind [19,20,21]. Beispielsweise können Nanopulver vor allem aufgrund der höheren spezifischen Oberflächen und Oberflächenaktivitäten die Tieftemperatursinterfähigkeit von nanoskaligem SiC in der Konsolidierungsverarbeitung und die Verbesserung der mechanischen Eigenschaften durch die Ermöglichung hoher Dichten ermöglichen [22]. Daher haben wir derzeit eine neue Methode zur Herstellung von Si-beschichteten SiC (Si-SiC)-Nanopartikeln entwickelt, die als Sinteradditiv verwendet werden, indem nicht übertragene thermische DC-Plasmabearbeitung von festkörpersynthetisiertem SiC-Pulver verwendet wird [23].
In dieser Studie wurde das nanoskalige Si-SiC-Kompositteilchen als Sinteradditiv zur Herstellung von SiC-Keramikmassen durch das Spark-Plasma-Sinterverfahren (SPS) verwendet und die Wirkung der Zugabe des nanoskaligen Si-SiC-Kompositteilchens auf das Sintern Temperatur, relative Dichte und Vicker-Härte von gesinterter SiC-Keramik wurden untersucht. Um die relative Dichte und Härte von gesintertem SiC weiter zu erhöhen, wurde außerdem die Reaktionsbindung zwischen freiem Silizium von nanoskaligen Si-SiC-Partikeln und zusätzlich hinzugefügter Aktivkohle neu in den SiC-Sinterprozess eingeführt. Der Sintermechanismus der SiC-Keramik, die mit nanoskaligem Si-SiC-Kompositadditiv durch SPS-Prozess hergestellt wurde, wurde auch auf der Grundlage des Nanogrößeneffekts und des Reaktionsbindungseffekts diskutiert. Diese Studie bietet eine neue vielversprechende Strategie, um die SiC-Keramik mit hoher Dichte und Härte bei relativ niedriger Sintertemperatur herstellen zu können.
Experimentell
Abbildung 1 zeigt die Herstellungsverfahren für SiC-Pulver in Mikrometergröße durch Fest-Feststoff-Reaktion (Kalzinierung), SiC-Pulver in Nanogröße durch thermisches Plasmaverfahren mit nicht übertragenem Lichtbogen und gesinterte SiC-Pellets durch SPS-Verfahren. In dieser Arbeit wurden SiC-Pulver mit zwei verschiedenen Größen, mikrometergroßes SiC-Pulver (als Hauptsintermaterial) und nanoskaliges Si-SiC-Komposit-Nanopulver (als Sinteradditiv), durch Kalzinierung bzw. Plasmaverfahren hergestellt.
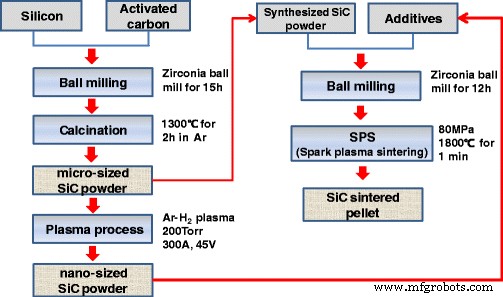
Experimentelles Verfahren zur Herstellung von mikrometergroßem SiC-Pulver durch Kalzinieren und nanoskaligem Si-SiC-Verbundpulver durch Plasma und zum Sintern von SiC-Keramiken durch SPS
Zubereitung von SiC-Pulver in Mikrometergröße
Das mikrometergroße SiC wurde unter Verwendung von Si-Pulvern mit einer durchschnittlichen Teilchengröße von 25 μm (99,9 %; Neoplant Co. LTD.) und Aktivkohle mit einer durchschnittlichen Teilchengröße von 32 μm (Sigma-Aldrich) synthetisiert. In einem typischen Verfahren wurde ein Molverhältnis von 1:1,5 von Si und Kohlenstoff unter Verwendung einer Kugelmühle für 15 h zusammengemischt. Das gemischte Pulver wurde in einen vertikalen Rohrofen gegeben und 2 h bei 1300 °C mit einer Heizrate von 10 °C/min in Gegenwart von Argongas (1 l/min) erhitzt. Nach Beendigung der Reaktion wurde das erhaltene Pulver zur weiteren Charakterisierung in Achatmörser gemahlen.
Plasmaverarbeitung von synthetisierten SiC-Pulvern
Die Plasmabearbeitung wurde durch einen thermischen Plasmareaktor mit nicht übertragenem Lichtbogen durchgeführt, wie in unserer früheren Arbeit berichtet [21, 23]. Das gemahlene SiC-Pulver wurde dem Plasmalichtbogen durch die interne Zuführungsleitung mit 2 mm Innendurchmesser im Plasmabrenner mit einem speziell konstruierten Pulverförderer zugeführt. Das Pulverfördersystem bestand aus einem Probenbehälter, einem Vibrator und einer Trägergasleitung. Die Pulver wurden durch eine Vibrationszuführung bei 70 V mit einer Zuführungsrate von 1 g/min zugeführt. Typische Syntheseexperimente wurden bei Systemdrücken von 200 Torr und mit Ar-Plasmagasflussraten von 30 l/min, H2 . durchgeführt Gasdurchflussraten von etwa 3 l/min und Gleichstrom von 300 A (bei 45 V). Nach der Plasmazündung wurde ein mikrometergroßes SiC-Pulver per Feeder zugeführt. Die synthetisierten Nanopulver wurden von der Reaktorwand und dem Boden des Plasmareaktorsystems gesammelt. Die Ausbeute betrug etwa 80–85 %.
Vorbereitung von gesinterten SiC-Pellet
Gesintertes SiC-Pellet wurde durch das SPS-Verfahren hergestellt (wie in 1 gezeigt). Beide SiC-Materialien, d. h. das durch Kalzinierungsverfahren synthetisierte mikrometergroße SiC-Pulver und das aus dem Plasmaprozess erhaltene nanoskalige Si-SiC-Pulver, wurden ohne zusätzliche Zusätze verwendet. Der Mischungsgehalt von Si-SiC-Nanopartikeln in mikrometergroßem SiC-Pulver wurde von 5 auf 15 Gew.-% geändert.
Die gemischten Pulver wurden in eine Graphitdüse (20 mm Durchmesser) gegeben und mit einem SPS-System in einer Vakuumatmosphäre (10 -2 Torr). Die Heizrate wurde auf 600 °C/min festgelegt und der angelegte Druck betrug 80 MPa. Die Sintertemperatur wurde von 1600 auf 1800 °C geändert. Die Haltezeit bei Zieltemperatur wurde von 0 bis 1 min bei 1800 °C variiert. Nach dem Sintern wurden die Probenoberflächen geschliffen, um die Graphitschicht zu entfernen, und dann mit einer Diamantpaste poliert. Die Dichte der gesinterten Proben wurde nach der Archimedes-Methode in entionisiertem Wasser als Immersionsmedium gemessen.
Probencharakterisierung
Die kristallographischen Strukturen der festen Proben wurden mit einem XRD (D/Max 2005 Rigaku) bestimmt, das mit graphitmonochromatisierter hochintensiver Cu-Kα1-Strahlung (λ = 1,5405 Å). Die XRD-Muster wurden von 20° bis 80° aufgezeichnet (2θ ) mit einer Scangeschwindigkeit von 0,04°/s. Partikelgröße und Morphologie wurden mit einem Rasterelektronenmikroskop (SEM; JSM-5900, JEOL) und einem Transmissionselektronenmikroskop (TEM; JEM-2010, JEOL) untersucht.
Ergebnisse und Diskussion
Abbildung 2 zeigt das XRD-Muster und das FESEM-Bild von SiC, das mit einer Festkörpermethode unter Verwendung einer Mischung aus Si und C in einem Molverhältnis von 1:1,5 synthetisiert wurde. Das XRD-Muster bestätigt die Bildung von β-SiC mit einer kleinen Menge von α-SiC, wie in Fig. 2a gezeigt. Es gab keine anderen Fremdphasen wie freies Silizium und SiO2 . Das FESEM-Bild zeigte die Bildung von mikrometergroßen SiC-Partikeln und die Partikelgröße variierte von 2 bis 5 μm, wie in Abb. 2b dargestellt.
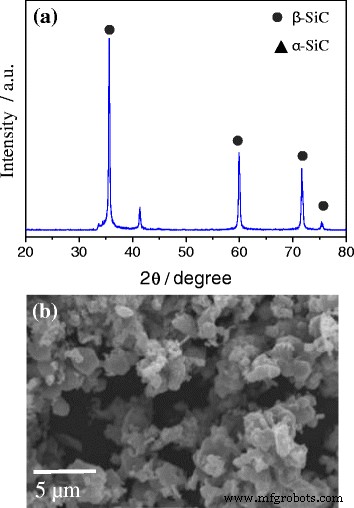
XRD-Profil (a ) und FESEM-Bild (b ) von mikrometergroßem SiC, synthetisiert durch die Festkörpermethode
SiC-Pulver in Nanogröße wurde aus diesem SiC-Pulver in Mikrometergröße unter Verwendung einer thermischen Plasmabearbeitung hergestellt, wie in Fig. 3 gezeigt. Fig. 3a, b war ein FESEM-Bild bzw. ein TEM-Bild. Diese Fotografien bestätigen die Bildung von Si-SiC-Partikeln in Nanogröße, und die Partikelgröße variierte zwischen 20 und 70 nm. Abbildung 3c ist ein HRTEM-Bild von Si-SiC-Partikeln in Nanogröße, das die Bildung von Si-SiC-Kompositpartikeln in Nanogröße bestätigt, da klare Gittersäume beider Materialien (Si und SiC) dargestellt werden. Die Oberfläche des nanoskaligen SiC-Pulvers betrug 69 m 2 . /g.
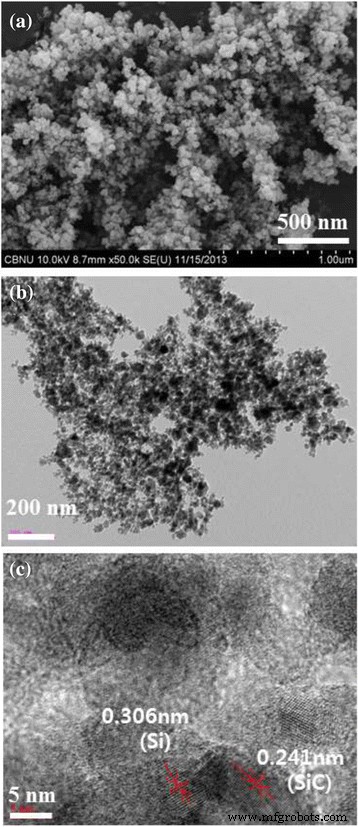
EM-Bilder von Si-SiC-Verbundpartikeln, hergestellt durch nicht übertragenes thermisches Lichtbogen-Plasmaverfahren:a FESEM, b TEM und c HR-TEM
Die Phase und Struktur von SiC-Partikeln in Nanogröße wurden durch XRD analysiert und in Abb. 4 gezeigt. Ähnlich wie bei SiC in Mikrometergröße zeigt es auch die Bildung von β-SiC mit einer geringen Menge an α-SiC. Allerdings zeigte SiC in Nanogröße freies Si und SiO2 Spitzen. Das Auftreten des Siliziumpeaks stand im Zusammenhang mit der teilweisen Zersetzung von SiC während der thermischen Plasmabearbeitung. Der Ursprung von SiO2 Peak war möglicherweise mit der partiellen Oxidation der SiC-Oberfläche während der Einwirkung von Luft nach der Plasmabearbeitung verbunden. Gesinterte SiC-Keramikpellets wurden aus diesen zwei Arten von SiCs hergestellt, d. h. aus den mikrometergroßen SiC- und den nanoskaligen Si-SiC-Verbundwerkstoffen. Die Mischung wurde durch ein SPS-Verfahren unter Verwendung verschiedener Zusammensetzungen von mikrometergroßem SiC und nanoskaligem Si-SiC gesintert, und die Sintertemperatur, die Haltezeit bei der Sintertemperatur und der komprimierte Druck wurden wie in Tabelle 1 gezeigt variiert.
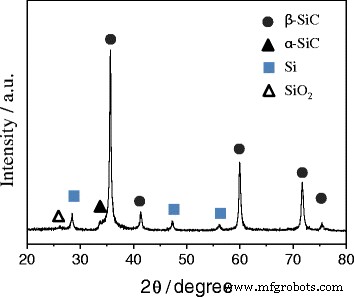
XRD-Profil von Si-SiC-Komposit-Nanopartikeln, hergestellt durch ein thermisches Plasmaverfahren mit nicht übertragenem Lichtbogen
Die Änderungen der relativen Dichte und der Vicker-Härte des gesinterten SiC entsprechend der Sintertemperatur und der Haltezeit bei der Zielsintertemperatur sind ebenfalls in Tabelle 1 angegeben. Die relative Dichte und Härte nimmt mit steigender Sintertemperatur zu und die höchste relative Dichte (87,4 %) und Härte (18,6 GPa) wurden bei 1800 °C aufgezeichnet. Die relative Dichte und Härte wurde weiter auf 88,2 % bzw. 21,2 GPa erhöht, wobei die Haltezeit von 0 auf 1 min bei einer Sintertemperatur von 1800 °C verlängert wurde. Es deutet darauf hin, dass die relative Dichte und Härte mit zunehmender Haltezeit zunimmt; leider konnte die Haltezeit bei 1800 °C aufgrund der Beschränkung des SPS-Systems nicht weiter erhöht werden.
Abbildung 5 zeigt die FESEM-Bilder einer gesinterten SiC-Oberfläche mit unterschiedlicher Sintertemperatur und Haltezeit. Die Korngröße von SiC wurde mit steigender Sintertemperatur erhöht, wie in Abb. 5a–c gezeigt. Form und Größe der mikrometergroßen SiC-Partikel wurden bis 1600 °C fast beibehalten (Abb. 5a), und das Kornwachstum von SiC begann ab 1700 °C, was zu einer Zunahme der relativen Dichte und Härte von bis zu 86,1 . führte % bzw. 14,8 GPa (Abb. 5b). Bei 1800 °C Sintertemperatur betrug die Korngröße von SiC 2–4 μm und die Kristalltextur war stärker verdichtet (Abb. 4c). Die relative Dichte und Härte bei 1800 °C betrugen 87,4 % bzw. 18,6 GPa. Das Kornwachstum wurde weiter aufgezeichnet, wenn die Probe 1 Minute lang bei 1800 °C Sintertemperatur gehalten wurde, was aus der Zunahme der relativen Dichte und Härte auf 88,2 % bzw. 21,2 GPa ersichtlich ist (Abb. 5d).
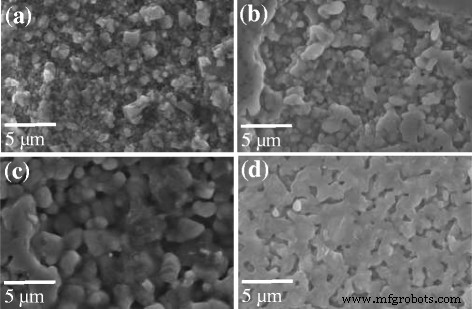
FESEM-Bilder des gesinterten SiC mit nanoskaligen Si-SiC-Kompositpartikeln durch SPS-Prozess bei a 1600 °C, b 1700 °C, c 1800 °C Sintertemperatur mit 0 min Haltezeit und d 1800 °C Sintertemperatur bei 1 min Haltezeit bei Zieltemperatur
Um die relative Dichte zu erhöhen, wurde die Zugabemenge an Si-SiC in Nanogröße in SiC-Pulver in Mikrometergröße von 5 auf 15 Gew.-% geändert. Darüber hinaus wurde dieser Mischung zusätzliche Aktivkohle zugesetzt, um die relative Dichte durch Reaktionsbindung (RB) mit freiem Silizium von nanoskaligem Si-SiC zu erhöhen. Die relative Dichte und Vickers-Härte von gesintertem SiC in Abhängigkeit von verschiedenen Zusammensetzungen von SiC in Mikrometergröße, Si-SiC in Nanogröße und Aktivkohle sind in Tabelle 2 zusammengefasst.
Sintertemperatur (1800 °C), Haltezeit (1 min) und Druck (80 MPa) wurden während des gesamten Experiments konstant gehalten. In Abwesenheit von zugesetztem Kohlenstoff nimmt die relative Dichte und Härte mit zunehmendem SiC-Gehalt in Nanogröße auf bis zu 10 Gew.-% zu und nimmt dann ab. Zum Beispiel betrug die relative Dichte und Härte 85,9 % und 21,1 GPa, wenn der Gehalt an Si-SiC in Nanogröße 5 Gew.-% betrug. Die relative Dichte und Härte stiegen auf 88,2 % bzw. 21,2 GPa bzw. 10 Gew.-% des nanoskaligen Si-SiC. Wenn der Gehalt hingegen 15 Gew. % betrug, nahm die Härte merklich auf 16,6 GPa ab, obwohl die relative Dichte immer noch 85,6 % betrug. Dies liegt hauptsächlich daran, dass die übermäßig zugesetzten nanoskaligen Si-SiC-Partikel eine große Menge an Poren in dem gesinterten SiC bereitstellen können. Zur weiteren Erhöhung der relativen Dichte und Härte wurde zusätzlich Aktivkohle zugesetzt. Die Zugabe von 0,1 Gew.-% Aktivkohle führte zu einem bemerkenswerten Anstieg der relativen Dichte (93,1 %) und der Härte (25,2 GPa). Die relative Dichte und Härte wurde weiter auf 97,1 % bzw. 31,4 GPa erhöht, wobei der Aktivkohlegehalt auf 0,2 Gew. % angehoben wurde. Eine XRD-Analyse dieser gesinterten SiC-Pellets mit unterschiedlichen Zusammensetzungen wurde durchgeführt und in Fig. 6 gezeigt. Es gab auch nach dem Sintern keine Veränderung der Kristallstruktur, mit Ausnahme eines schwachen Siliziumpeaks, der bei 29° aufgezeichnet wurde, der möglicherweise auf die Zugabe von . zurückzuführen ist Nano-Si-SiC-Verbundpartikel.
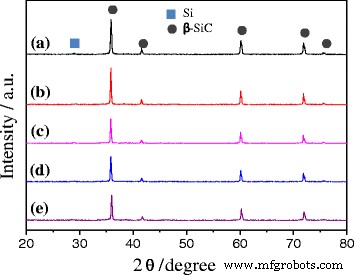
XRD-Profile von SiC-Pellets, die mit nanoskaligen Si-SiC-Verbundpartikeln und Aktivkohle durch das SPS-Verfahren gesintert wurden (Details zu a, b, c, d und e sind in Tabelle 2 angegeben)
Abbildung 7 zeigt FESEM-Bilder der Oberfläche der gesinterten SiC-Pellets mit unterschiedlichen mikrometergroßen SiC- und nanoskaligen Si-SiC-Zusammensetzungen. Die Korngröße von SiC betrug 2–3 μm mit größeren Poren, wenn der Gehalt an Si-SiC in Nanogröße 5 Gew.-% betrug (Abb. 7a). Die Korngröße wurde mit zunehmendem Gehalt an nanoskaligem Si-SiC erhöht, wie in Fig. 7b, c gezeigt. Die Korngröße von SiC-Pellets mit 10 und 15 Gew.-% Si-SiC betrug etwa 3–5 bzw. 4–6 μm. Abbildung 7d, e zeigt die FESEM-Bilder von gesinterten SiC-Pellets nach Zugabe von Aktivkohle. Wenn 0,1 Gew. % Aktivkohle hinzugefügt wurden, beginnen riesige Körner zu erscheinen, was darauf hindeutet, dass die Verdichtung der SiC-Textur durch die Reaktionsbindung zwischen Silizium und Aktivkohle vorangetrieben wurde. Ein weiterer Anstieg der Aktivkohle auf bis zu 0,2 Gew.-% führte zu einer vollständigen Verdichtung der SiC-Textur, wie in Abb. 7e gezeigt.
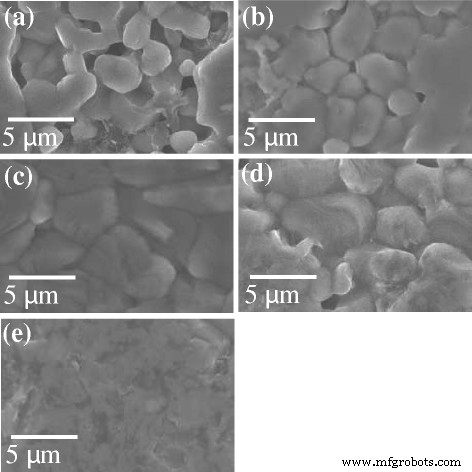
FESEM-Bilder von SiC-Pellets, die mit nanoskaligen Si-SiC-Komposit-Nanopartikeln und Aktivkohle durch einen SPS-Prozess gesintert wurden (Details von a , b , c , d , und e sind in Tabelle 2) aufgeführt.
Abbildung 8 zeigt die Schwindungsverschiebungen von gesinterten SiC-Proben mit unterschiedlichen Zusammensetzungen bei unterschiedlichen Sintertemperaturen. Bei allen Proben wurde eine Ausdehnung bis 1500 °C festgestellt, die hauptsächlich auf die Ausdehnung von Gasen im SiC-Gemisch zurückzuführen ist (Abb. 8a–e). Es kann auch an einer Erhöhung der Höhe der Graphitform mit SiC-Mischpulver um 1,0–1,28 mm nach dem Sintern im Vergleich zum anfänglichen Sinterschritt beobachtet werden. Ein weiterer Anstieg der Sintertemperatur führte zu einer Schrumpfung aller Proben aufgrund des Sintereffekts von nanoskaligen Si-SiC-Nanopartikeln. Die Verlängerung der Haltezeit der Probe bei der Sintertemperatur von 0 auf 1 min führte auch zu einer Zunahme der Schrumpfung der Probe. Die Zugabe von zusätzlicher Aktivkohle zu der Mischung aus SiC und Si-SiC zeigte nach 1500 °C eine höhere Schrumpfungsverschiebung im Vergleich zu SiC/Si-SiC-Mischungen ohne Aktivkohle (Abb. 8d, e). Außerdem nimmt die Schrumpfverdrängung mit zunehmender Zugabemenge an zusätzlicher Aktivkohle zu. Zum Beispiel wurde die Schrumpfungsverschiebung von 1,11 auf 1,61 mm erhöht, wenn die zugegebene Aktivkohlemenge von 0,1 auf 0,2 Gew.-% erhöht wurde, wie in 8d dargestellt, e. Dies ist auf den Reaktionsbindungseffekt von freiem Silizium von Si-SiC-Komposit-Nanopartikeln und Aktivkohle zurückzuführen. Die exotherme Natur dieser Reaktion führt während des Sinterns zu einem Anstieg der tatsächlichen Temperatur im Inneren des SiC-Pellets. Somit bestätigen diese Ergebnisse eindeutig, dass die Reaktionsbindungswirkung von Silizium und Aktivkohle die relative Dichte und Härte von SiC-Keramiken erhöhen kann.
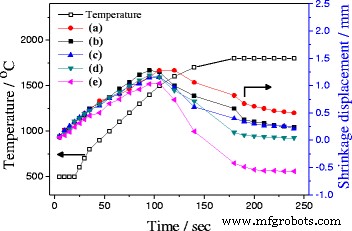
Änderung der Schrumpfverlagerung von SiC-Pellets, die mit nanoskaligen Si-SiC-Komposit-Nanopartikeln während des SPS-Prozesses gesintert wurden (Details zu a, b, c, d und e sind in Tabelle 2 angegeben)
Aus den obigen experimentellen Ergebnissen können wir einen Sintermechanismus von mikrometergroßem SiC-Pulver mit nanoskaligem Si-SiC-Verbundpulver und Aktivkohle wie folgt zusammenfassen. In Tabelle 1 wurde bestimmt, dass das Sintern von mikrometergroßem SiC-Pulver mit 10 Gew.-% an nanoskaligem Si-SiC-Verbundpulver bei 1600 °C begonnen wurde und die Sinterreaktion mit Erhöhung der Sintertemperatur und Haltezeit beschleunigt wurde. Aus diesem Ergebnis bestätigten wir den Nanogrößeneffekt von Si-SiC-Komposit-Nanopartikeln auf das Sintern des mikrometergroßen SiC-Pulvers. Wenn dabei Aktivkohle zu der Mischung aus mikrometergroßem SiC und nanoskaligem Si-SiC-Verbundpulver zugegeben wird, kann die Reaktionsbindung, die aus der exothermen Reaktion zwischen dem freien Silizium der Si-SiC-Verbundnanopartikel stammt, induziert werden den Sinterprozess wie in Abb. 9 schematisch dargestellt. Folglich konnte festgestellt werden, dass der Sintermechanismus von mikrometergroßem SiC-Pulver mit nanoskaligem Si-SiC-Verbundpulver und Aktivkohle als Sinteradditive auf beiden Effekten beruht, dem Nano- Größeneffekt und Reaktionsbindungseffekt, die aus dem nanoskaligen Si-SiC-Verbundpulver eingeführt wurden.
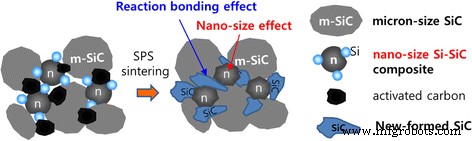
Schematische Darstellung des Sintermechanismus für mikrometergroßes SiC-Pulver mit nanoskaligem Si-SiC-Verbundpulver und Aktivkohle als Sinteradditive
Schlussfolgerungen
Mikrometergroßes SiC-Pulver (2–5 μm) wurde durch ein Festkörperverfahren unter Verwendung von Si-Pulver und Aktivkohlequellen synthetisiert. Si-SiC-Verbundpulver in Nanogröße mit einer Partikelgröße von 20–70 nm wurde durch ein thermisches Plasmaverfahren mit nicht übertragenem Lichtbogen hergestellt. Gesinterte SiC-Pellets wurden durch das SPS-Verfahren unter Verwendung der Mischung mit unterschiedlichen Verhältnissen von mikrometergroßem SiC-Pulver und nanoskaligen Si-SiC-Verbundpartikeln als Sinteradditiv hergestellt. Bei einem festen Verhältnis von mikrometergroßem SiC und nanoskaligem Si-SiC (90:10) nahmen die relative Dichte und die Vickers-Härte mit steigender Sintertemperatur und Haltezeit zu. Die maximale relative Dichte (88,2 %) und die Vicker-Härte (21,2) wurden bei 1800 °C Sintertemperatur für 1 min Haltezeit aufgezeichnet. Die relative Dichte und die Vicker-Härte wurden durch Zugabe von zusätzlicher Aktivkohle zu der Mischung aus mikrometergroßem SiC und nanoskaligem Si-SiC weiter erhöht. Die relative Dichte und die Vicker-Härte wurden auf 97,1 % bzw. 31,4 GPa erhöht, indem der SiC/Si-SiC-Mischung 0,2 Gew.-% zusätzliche Aktivkohle zugesetzt wurden. Es wurde festgestellt, dass der Nanogrößeneffekt der Si-SiC-Kompositpartikel und die exotherme Natur der Silizium-Kohlenstoff-Reaktionsbindung für die Zunahme der relativen Dichte und Härte verantwortlich sind. Daher wurde vorgeschlagen, dass die nanoskaligen Si-SiC-Verbundpartikel ein vielversprechendes Additiv zum Sintern von SiC-Keramiken sein könnten.
Nanomaterialien
- Sinterprozess für feuerfeste Legierungen
- Großartige Verbesserung der Wärmeleitfähigkeit von Silikonverbundstoffen mit ultralangen Kupfer-Nanodrähten
- Elektrogesponnene Polymer-Nanofasern, dekoriert mit Edelmetall-Nanopartikeln für die chemische Sensorik
- Verbundmembranen mit Nanopartikeln von anorganischen Ionenaustauschern für die elektrodialytische Entsalzung von Glycerin
- Einfache Synthese von farbigen und leitfähigen CuSCN-Kompositen, die mit CuS-Nanopartikeln beschichtet sind
- Zielgerichtete Endothelzellen mit multifunktionalen GaN/Fe-Nanopartikeln
- Elektrische Eigenschaften von Verbundmaterialien mit durch ein elektrisches Feld unterstützter Ausrichtung von Nanokohlenstoff-Füllstoffen
- Synergistische Effekte von Ag-Nanopartikeln/BiV1-xMoxO4 mit erhöhter photokatalytischer Aktivität
- Studie zum Effekt der Aufprallrichtung auf den nanometrischen Schleifprozess mit Molekulardynamik
- Toxizität von PEG-beschichteten CoFe2O4-Nanopartikeln mit Behandlungseffekt von Curcumin