Schneidbasierter Mechanismus zum Entfernen einzelner Atomschichten von monokristallinem Kupfer:Kantenradiuseffekt
Zusammenfassung
Das ultimative Ziel des mechanischen Schneidens besteht darin, die minimale Spandicke auf eine einzelne Atomlage zu reduzieren. In dieser Studie wird der schneidbasierte Mechanismus zur Entfernung einzelner Atomschichten auf monokristallinem Kupfer durch eine Reihe von molekulardynamischen Analysen untersucht. Die Forschungsergebnisse zeigen, dass, wenn die Schnitttiefe auf die atomare Skala abnimmt, die minimale Spandicke durch mechanisches Schneiden mit einem Werkzeug mit abgerundeten Kanten auf eine einzelne atomare Schicht herabgesetzt werden kann. Das Materialabtragsverhalten beim spanabhebenden Einzelatomschichtabtrag weist vier Charakteristika auf, darunter Spanbildung durch scherspannungsgetriebene Versetzungsbewegung, elastische Verformung auf der bearbeiteten Oberfläche, atomarer Größeneffekt und Schneidkantenradiuseffekt. Basierend auf diesem Verständnis wird ein neues Schneidmodell vorgeschlagen, um das Materialabtragsverhalten beim spanabhebenden Verfahren zum Abtragen einzelner Atomlagen zu untersuchen, das sich deutlich von denen beim Nanoschneiden und konventionellen Schneiden unterscheidet. Die Ergebnisse bieten theoretische Unterstützung für die Erforschung und Entwicklung der Herstellungstechnologie im atomaren und nah-atomaren Maßstab.
Einführung
Mechanisches Trennen als eines der wichtigsten subtraktiven Bearbeitungsverfahren wird zur Herstellung von Teilen mit hoher Oberflächengüte angewendet [1, 2]. Eine große Anzahl theoretischer und experimenteller Studien wurde durchgeführt, um den zugrunde liegenden Materialentfernungsmechanismus im Nanomaßstab aufzuklären, um die grundlegende Theorie des Nanoschneidens zu etablieren und zu bereichern [3,4,5,6]. Die Forschungsergebnisse tragen wesentlich zur Anwendung des nanometrischen Schneidens in Wissenschaft und Industrie bei und ermöglichen die Herstellung von Hochleistungsteilen, die eine komplexe Form und eine nanometrische Oberflächengüte erfordern [7, 8]. Es gibt jedoch immer noch keinen Bericht über den Mechanismus des Materialabtrags beim Schneiden im atomaren und nah-to-atomaren Maßstab (ACS), was den Fortschritt bei der Entwicklung der Fertigungstechnologie der nächsten Generation – der Fertigung im atomaren und nah-to-atomaren Maßstab – ernsthaft einschränkt ( ACSM), dh Fertigung III [9]. Darüber hinaus hat die fortschreitende Entwicklung von Geräten im atomaren Maßstab auch die Nachfrage nach verschiedenen Bearbeitungsprozessen betont, um ACSM zu erreichen [10].
Beim konventionellen makroskaligen Zerspanen ist die Schnitttiefe deutlich größer als der Schneidenradius, wobei der Materialabtrag durch materialscherungsgetriebene Spanbildung realisiert wird [11,12,13]. Da beim Mikro-/Nanoschneiden die Schnitttiefe vergleichbar oder kleiner als der Schneidenradius ist, dominiert allmählich die Spanbildung beim Strangpressen, wobei die Schnitttiefe bis in den Nanobereich abnimmt, was stark von den Schneidenradiuseffekten beeinflusst wird [14,15,16 ,17,18,19]. Da beim ACS-Schneiden die Schnitttiefe weiter auf eine nahe atomare Skala und sogar auf eine atomare Skala, die viel kleiner als der Schneidenradius ist, verringert wird, würde der Kantenradiuseffekt unweigerlich das Materialabtragsverhalten beeinflussen.
Darüber hinaus ist die Schnitttiefe beim ACS-Schneiden im Gegensatz zum konventionellen Schneiden und Mikro-/Nanoschneiden nicht nur deutlich geringer als der Schneidenradius, sondern auch vergleichbar oder sogar kleiner als der Radius der Werkstückatome. Das praktische Abtragsverhalten würde sich bei unterschiedlichen Verhältnissen von Schnitttiefe zu Atomradius des Werkstücks ändern, was als ein neuer Kalibriereffekt, d. h. Atomgrößeneffekt, erkannt wird [20]. Daher sollten beim ACS-Schneiden sowohl der Schneidenradiuseffekt als auch der Atomgrößeneffekt berücksichtigt werden. Es gibt jedoch keinen Bericht zu diesem kritisch wichtigen Thema in der Studie der ACS-Schneidtechnologie.
Aus diesen Gründen werden in der vorliegenden Studie der Atomgrößeneffekt und der Kantenradiuseffekt auf den schneidbasierten Einzelatomschicht-Abtragsmechanismus unter Verwendung von Molekulardynamik(MD)-Modellierung untersucht.
Dieses Papier ist in die folgenden Abschnitte gegliedert. Abschnitt 2 stellt die verwendete Methodik, einschließlich Modellierung und Protokoll, geeignete potenzielle Funktion vor. Abschnitt 3 präsentiert die Analyseergebnisse und die entsprechenden Diskussionen. Abschnitt 4 diskutiert den detaillierten schneidbasierten Mechanismus zum Entfernen einzelner Atomlagen unter dem gekoppelten Einfluss des Schneidkanteneffekts und des Atomgrößeneffekts. Die Studienergebnisse werden in Abschnitt 5 abgeschlossen.
Methode
Simulationsmodell und -protokoll
Da die Schnitttiefe auf den atomaren oder nahezu atomaren Maßstab abnimmt, ist es in der Tat eine Herausforderung, den Materialabtragsprozess in der Praxis erfahrungsgemäß zu beobachten. In dieser Studie wird eine Reihe von MD-Simulationen durchgeführt, um den schneidbasierten Mechanismus zum Entfernen einzelner Atomlagen zu analysieren, wobei der Atomgrößeneffekt des Werkstücks und der Schneidkantenradiuseffekt nachdrücklich fokussiert werden.
Abbildung 1 zeigt die Schnappschüsse für die atomare Konfiguration des Diamant-Kupfer-Schneidmodells, das aus einem einkristallinen Kupferwerkstück und einem Diamantschneidwerkzeug besteht. Die Simulationen werden auf der (111)-Ebene von einkristallinem Kupfer durchgeführt. Die Abmessungen des Werkstücks in x -[1 -1 0], y -[1 1 -2] und z -[1 1 1] Richtungen sind 27, 10 bzw. 5 nm. Während der MD-Simulationen werden die Werkstückatome in Grenzschichtatome, thermostatische Schichtatome bzw. Newtonsche Schichtatome unterteilt, wie in Abb. 1 gezeigt. Die beiden Schichten an der Unterseite des Werkstücks, nämlich die Grenzschicht, bleiben fest über die MD-Simulationen, um die mögliche spanabhebende Positionsverschiebung des Werkstücks zu eliminieren. Die drei Atomschichten neben der Grenzschicht sind Thermostatschichtatome. Die Temperatur der thermostatischen Schicht wird durch Verfahren zur Neuskalierung der Geschwindigkeit bei 298 K gehalten. Die restlichen Werkstückatome gehören zur Newtonschen Schicht. In den vorliegenden Simulationen beträgt der Span- und Freiwinkel des Schneidwerkzeugs 0° und 12°. Die detaillierten Modellparameter sind in Tabelle 1 zusammengefasst. Da das ACS-Schneiden vorzugsweise mit einer niedrigeren Schnittgeschwindigkeit durchgeführt wird, wird eine Schnittgeschwindigkeit von 25 m/s entlang der [-1 1 0]-Richtung verwendet, nachdem der Einfluss von Schnittgeschwindigkeit und Rechenzeit berücksichtigt wurde kosten.
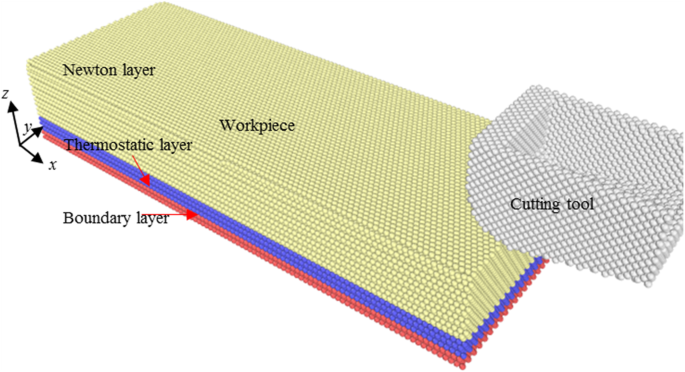
Simulationsmodell für Diamantschneidemodell
Potenzielle Funktion
Das Kupfer-Diamant-Schneidsystem umfasst hauptsächlich zwei Arten von Atomen, nämlich Kupfer- und Diamantatome. In den MD-Simulationen sollten die interatomaren Wechselwirkungen genau beschrieben werden, um die Rechengenauigkeit der Simulationsergebnisse sicherzustellen. Somit ist eine vernünftige Auswahl der potentiellen Funktion von entscheidender Bedeutung. In dieser Studie wird die häufig verwendete Potentialfunktion der Embedded-Atom-Methode (EAM) verwendet, um die interatomaren Wechselwirkungen zwischen Kupferatomen zu beschreiben [21]. Die Morsefunktion wird verwendet, um die Wechselwirkungen zwischen Kupferatomen und Diamantatomen (Cu-C) zu berechnen, hauptsächlich in Abhängigkeit von r.
$$ E={D}_0\left[{e}^{-2\alpha \left(r-{r}_0\right)}-2{e}^{\alpha \left(r-{r} _0\right)}\right] $$ (1)wo E und D 0 beziehen sich auf die potentielle Energie des Paares und die Kohäsionsenergie, α stellt eine Konstante dar, r 0 der Gleichgewichtsabstand ist und r ist der Abstand zwischen zwei Atomen. Für Cu-C-Wechselwirkungen D 0 ist 0,087ev, r 0 ist 0,205 nm [22] und α ist 51,40 nm −1 . Für die Wechselwirkungen zwischen Kohlenstoffatomen im Schneidwerkzeug (C-C) ist die deutlich stärkere Bindungsstärke zwischen Diamantatomen als Kupferatomen vernachlässigbar. Das Schneidwerkzeug wird bei der Analyse als starr angesehen.
Definition der Schnitttiefe
Schnitttiefe (a ) ist definiert als der Abstand zwischen dem obersten Punkt der Werkstückoberfläche und dem tiefsten Punkt des Schneidwerkzeugs. Die Größe eines Werkstückatoms wird normalerweise durch den Atomradius (r w ). Wie in Abb. 2 dargestellt, kann theoretisch die maximale Schnitttiefe wie folgt erreicht werden, wenn die oberste erste Atomschicht von der Werkstückoberfläche entfernt werden soll:
$$ {a}_{\mathrm{max}}={r}_w+0.5\ast {d}_{layer} $$ (2)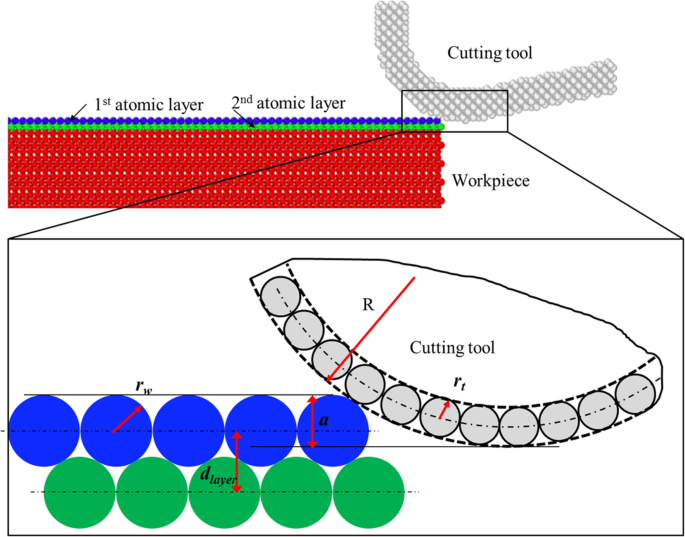
Schematische Darstellung der Schnitttiefendefinition beim Einzelatomschichtabtrag
Hier, d Ebene stellt den Abstand zwischen den obersten benachbarten Atomschichten auf der Werkstückoberfläche dar. In dieser Studie basieren alle Analysen auf der (111)-Oberfläche eines monokristallinen Kupferwerkstücks; daher die r w in Gl. (2) bezieht sich auf den Radius von Kupferatomen, nämlich 1,28 . Die d Ebene ist 2.087 Å. Wenn a ist größer als a max , kommt der tiefste Punkt des Schneidwerkzeugs in direkten Kontakt mit der zweiten Atomschicht und kann die Materialverformung und sogar den Abtrag bewirken. Daher sind in der vorliegenden Studie die verwendeten Schnitttiefen kleiner als a max (2,32 Å).
Basierend auf den Ergebnissen wird der grundlegende Mechanismus zum Entfernen einzelner Atomschichten auf der Grundlage des Schneidens bei verschiedenen Kombinationen der Verhältnisse von a . stark verändert zu R und a zu r w .
Ergebnisse und Diskussion
Laut MD-Ergebnissen haben sowohl der Atomgrößeneffekt als auch der Schneidkantenradiuseffekt den schneidbasierten Einzelatomschichtentfernungsprozess stark beeinflusst. Um in den folgenden Abschnitten den atomaren Größeneffekt und den Werkzeugschneidenradiuseffekt klar zu beschreiben, muss das Verhältnis der Schnitttiefe (a ) zum Atomradius des Werkstücks (r w ), a/r w , und die der Schnitttiefe(a ) zum Kantenradius(R ), a/R , beschäftigt sind. Die Analyseergebnisse werden systematisch unter den Aspekten Spanbildung, Oberflächenerzeugung, Untergrundverformung und atomares Verschiebungsverhalten untersucht. Die Ergebnisse liefern detaillierte Einblicke in die typischen Eigenschaften des schneidbasierten Einzelatomschicht-Abtragsmechanismus.
Chipbildung
Die Analyseergebnisse zeigen, dass es aufgrund des atomaren Sizing-Effekts des Werkstücks [20] zwei kritische Werte für das Verhältnis der Schnitttiefe gibt (a ) zum Atomradius des Werkstücks (r w ), nämlich kritischer Wert 1 (C1 ) und kritischer Wert 2 (C2 ), die das Spanbildungsverhalten in verschiedene Fälle unterteilt.
- a.
Das Verhältnis von a/r w kleiner als kritischer Wert 1 (C1 ).
Abbildung 3 zeigt die Ergebnisse der MD-Simulation bei verschiedenen Schneidenradien bei einer Schnitttiefe von etwa 1,1 Zoll. Hier ist das Verhältnis der Schnitttiefe (a ) zum Atomradius des Werkstücks (r w ) ist 0.781.
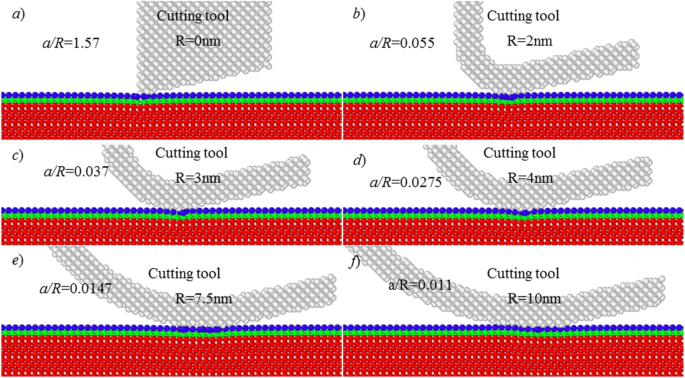
Simulationsergebnisse bei einer Schnitttiefe von 1,1 Å
Trotz des vergrößerten Schneidkantenradius tritt auf jeder bearbeiteten Cu-(111)-Oberfläche eine elastische Verformung auf. Es gibt keine Spanbildung und kein Materialabtrag während des Schneidprozesses. Die Studie zeigt, dass die Schnitttiefe größer als etwa 1,1 Å sein sollte, um Materialabtrag auf der Cu (111)-Oberfläche zu ermöglichen.
- b.
Das Verhältnis von a/r w ist größer als C1, aber kleiner als kritischer Wert 2 (C2 ).
Wenn die Schnitttiefe größer als etwa 1,1 Å ist, nämlich das Verhältnis von a/r w größer als 0,781 ist, findet auf der Werkstückoberfläche ein Materialabtrag statt. Wie in 4 gezeigt, wird ein Teil des Materials von der Werkstückoberfläche entfernt, aber eine größere Anzahl von Atomen innerhalb der obersten ersten Schicht bleibt auf der neuen bearbeiteten Oberfläche zurück, wodurch Oberflächenfehler entstehen. Wenn der Kantenradius auf 7,5 nm ansteigt, wird außerdem das Verhältnis von a/R ist 0,019. In einem solchen Fall wurde ein Teil der Atome in der ersten Atomschicht in die zweite Schicht und sogar in die dritte Atomschicht gepresst, wie in Fig. 4e gezeigt, was der Extrusionswirkung des Schneidwerkzeugs zugeschrieben werden sollte. Dies weist auch darauf hin, dass der Effekt des Werkzeugschneidenradius einen Einfluss auf den Materialabtragsprozess ausübt, obwohl kein kontinuierlicher Materialabtrag erzielt werden konnte.
- c.
Das Verhältnis von a/r w ist größer als C2 .
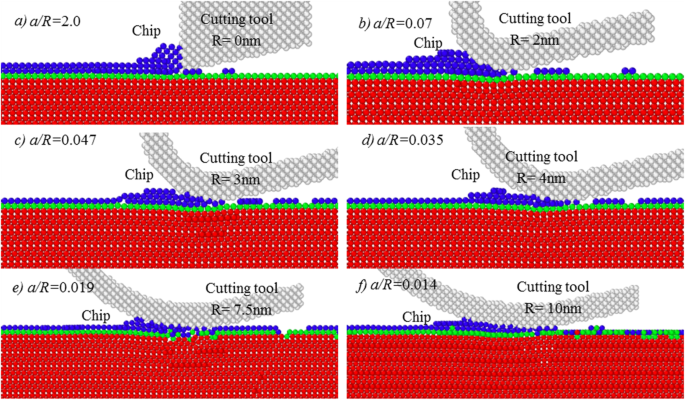
Simulationsergebnisse bei einer Schnitttiefe von 1,4 Å
Bild 5 zeigt die Spanbildung bei einer Schnitttiefe von ca. 2 Å. Hier ist das Verhältnis von a/r w =2 Å/1,28 Å =1,563. Im Vergleich zu Fig. 3 konnten bei einer Erhöhung der Schnitttiefe auf 2 Å die Atome innerhalb der anvisierten Atomschicht kontinuierlich und stabil durch Spanbildung abgetragen werden. Es zeigt an, dass die Schnitttiefe größer war als die minimale Spandicke von monokristallinem Kupfer, und die minimale Spandicke könnte bis zu einer einatomigen Schicht mit einer Schnitttiefe von etwa 2 Å betragen. Nach dem Schneiden wurden die Materialien innerhalb der ersten Atomschicht vollständig von der Werkstückoberfläche entfernt.
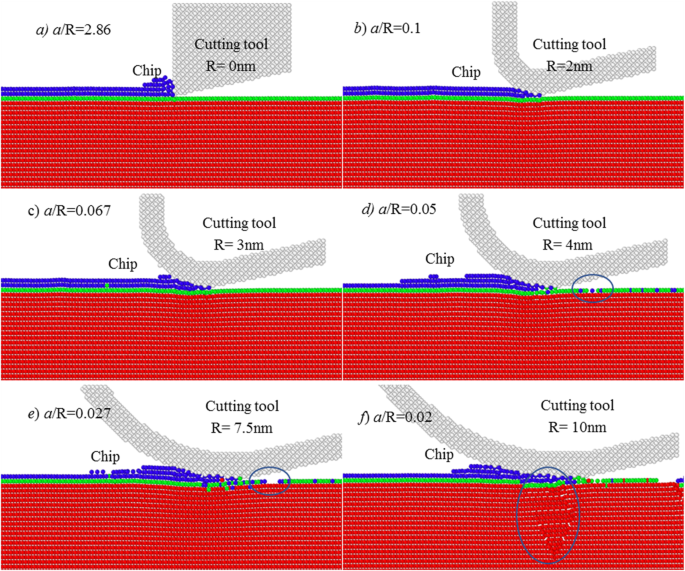
Simulationsergebnisse des ACS-Schneidens bei Schnitttiefe =2 Å
In Abb. 5 ist jedoch auch zu erkennen, dass aufgrund der Zunahme des Verhältnisses von a/R , durchlaufen die Atome in der ersten Atomschicht offensichtlich unterschiedliche Abtragsprozesse, insbesondere die spanabhebende Verformung an der bearbeiteten Oberfläche. Bei einer Schnitttiefe von 2 Å, wenn ein scharfes Schneidwerkzeug verwendet wird, nämlich das Verhältnis von a/R 5,70 beträgt, tritt auf der bearbeiteten Oberfläche nur eine geringe Verformung auf. Wenn der Schneidkantenradius auf 3 nm ansteigt, wird das Verhältnis von a/R 0,134 ist, wurde die Amplitude der elastischen Verformung offensichtlich erhöht.
Wenn der Werkzeugkantenradius auf 4 nm erhöht wird, wie in Fig. 5d gezeigt, wurden viele Atome innerhalb der angestrebten ersten Atomschicht in die zweite Atomschicht gepresst, wodurch die neue bearbeitete Oberfläche gebildet wird. Bei einem Werkzeugkantenradius von etwa 7,5 nm wird ein Teil der Atome in der ersten Schicht sogar in die dritte Atomschicht diffundiert. Wenn der Schneidenradius etwa 10 nm erreicht, tritt eine deutliche elastische und plastische Verformung auf, die auch im folgenden Abschnitt 3.3 bestimmt werden kann.
Daher hängt die schneidbasierte Entfernung einzelner Atomschichten nicht nur vom Verhältnis von a/r w , aber auch das Verhältnis von a/R . Um eine Einzelatomschichtentfernung durch mechanisches Schneiden zu erreichen, d. h. eine Materialentfernung auf atomarer Ebene, sollten sowohl Atomgrößeneffekte als auch Schneidkantenradiuseffekte berücksichtigt werden, die sich deutlich von Mikro-/Nanoschneiden und konventionellem Schneiden auf Makroebene unterscheiden.
Oberflächengenerierung
Ein Ziel der spanabhebenden Atomlagenentfernung ist es, die defektfreie bearbeitete Oberfläche mit idealer Kristallstruktur zu erhalten. Der Einfluss der atomaren Größe des Werkstücks auf die Oberflächenerzeugung beim ACS-Schneiden wurde kürzlich untersucht [20]. In der vorliegenden Studie werden die Oberflächentopographie und die Oberflächenzusammensetzung der neuen bearbeiteten Oberfläche wie folgt untersucht, um den Einfluss des Schneidkantenradius auf die Oberflächenerzeugung beim ACS-Schneiden deutlich zu machen.
Oberflächentopografie
Abbildung 6 zeigt die Oberflächentopographien der bearbeiteten Cu (111)-Oberfläche bei verschiedenen Kantenradien. Hier wird eine Schnitttiefe von 2 Å angenommen. Wie in Fig. 6a, b gezeigt, konnten die Cu-(111)-Oberflächen mit idealer kristalliner Struktur erhalten werden, wenn der Werkzeugkantenradius kleiner als 3 nm ist. Die Fehler an der linken Seite der Werkstückoberfläche sind auf die Verformung beim Schneiden des Werkzeugs zurückzuführen. Während des Schneidens in einer stationären Phase bildet sich kein Oberflächenfehler auf der bearbeiteten Oberfläche.
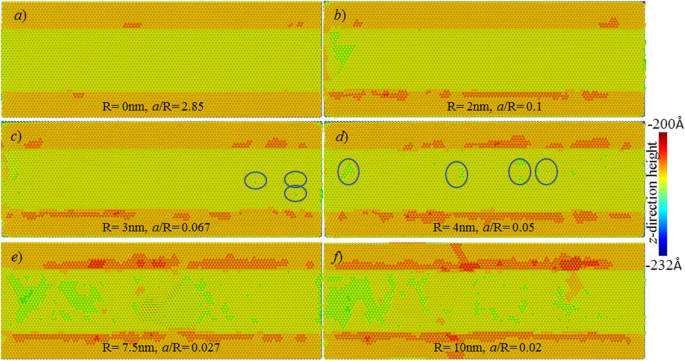
Auswirkungen des Schneidenradius auf Oberflächentopographien. Atome werden basierend auf ihren Höhen in z-Richtung gefärbt
Mit zunehmendem Werkzeugkantenradius bilden sich jedoch nach und nach viele Fehler auf der bearbeiteten Oberfläche. Bei einem Kantenradius von 4 nm bilden sich viele grubenartige Defekte auf der bearbeiteten Oberfläche, siehe Fig. 6d. Wenn der Werkzeugkantenradius gleich oder größer als 5 nm ist, wird eine große Anzahl von Oberflächendefekten gebildet, die die Oberflächenqualität ernsthaft verschlechtern. In einem solchen Fall wurde mehr als eine Atomschicht von der Werkstückoberfläche entfernt. Daher kann festgestellt werden, dass bei einer Schnitttiefe von 2 Å, wenn der Werkzeugkantenradius kleiner als 3 nm ist, eine Einzelatomschichtentfernung auf der Cu-(111)-Oberfläche erreicht werden könnte. Aufgrund des Schneidenradiuseffekts ist das Verhältnis der Schnitttiefe (a ) zum Kantenradius (R ) sollte größer als ein Schwellenwert sein, um eine defektfreie bearbeitete Oberfläche durch spanabhebende Einzelatomschichtentfernung zu erreichen. Hier ist der kritische Wert des Verhältnisses von a/R ist [0,05, 0,067].
Oberflächenzusammensetzung
Bild 7 zeigt die Zusammensetzung der bearbeiteten Oberflächen bei verschiedenen Schneidenradien und der Schnitttiefe von 2 Å. Hier sind grüne und blaue Atome diejenigen aus der ersten und zweiten Schicht, während die roten Atome diejenigen unter der zweiten Atomschicht sind. Wie in Abb. 7a gezeigt, ist bei Verwendung eines scharfen Schneidwerkzeugs das Verhältnis von a/R 2,85 beträgt, besteht die bearbeitete Oberfläche nur aus Atomen in der ersten Schicht. Dieses Ergebnis zeigt an, dass die angestrebte erste Atomschicht gründlich vom Werkstück entfernt wurde. Außerdem bedeutet dies, dass der Materialabtrag schichtweise erfolgt, bei dem das abgetragene Material nur aus der gezielten ersten Atomlage auf der Werkstückoberfläche stammt.
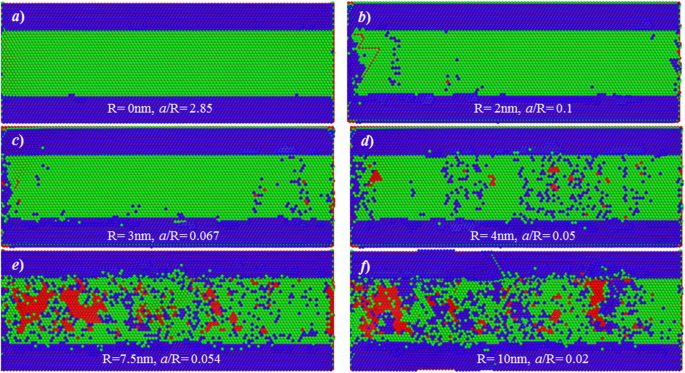
Oberflächenzusammensetzung der bearbeiteten Oberflächen. Atome werden basierend auf der Anzahl der Atomlagen gefärbt
Wenn der Werkzeugkantenradius jedoch 2 nm und 3 nm beträgt, wie in Fig. 7b, c gezeigt, werden die bearbeiteten Oberflächen aus zwei Atomschichten (blau und grün) zusammengesetzt. Es zeigt, dass, obwohl eine Einzelatomschichtentfernung erreicht wurde, der Oberflächenerzeugungsprozess mindestens 2 Atomschichten umfasst. Wenn der Werkzeugkantenradius größer als 4 nm ist, gibt es eine große Anzahl von Atomen der ersten Atomschicht auf der bearbeiteten Oberfläche, was darauf hinweist, dass viele Atome in der ersten Schicht gepresst wurden, um eine neue Oberfläche zu erzeugen.
Daher hat sich mit zunehmendem Schneidkantenradius die Oberflächenerzeugung stark verändert. Im Folgenden sind zwei Arten von beteiligten Oberflächenerzeugungsmechanismen zusammengefasst:
- 1.
Schicht für Schicht :Die anvisierte erste Atomschicht wird vollständig entfernt, um eine neue bearbeitete Oberfläche zu erzeugen. Beim Schneiden werden nur Atome innerhalb der ersten Schicht entfernt.
- 2.
Mehrschichtentfernung :Obwohl eine Einzelatomschichtentfernung realisiert werden konnte, unterliegen die Atome innerhalb der Zielatomschicht zwei typischen Verschiebungsverhalten. Ein Teil der Atome würde durch scherspannungsbedingte Versetzungsbewegungen zu Chips geformt, während andere unter der Wirkung eines Schneidwerkzeugs in die bearbeitete Oberfläche extrudiert würden. Der Materialentfernungsprozess umfasst mindestens zwei Atomschichten.
Deformationsmechanismus unter der Oberfläche
Beim Nanoschneiden kommt es während des Schneidprozesses zu einer elastischen und plastischen Verformung der bearbeiteten Oberfläche. Nach dem Überfahren der Werkstückoberfläche durch das Schneidwerkzeug federt der elastische Anteil zurück, während der plastisch verformte Teil zu einer bleibenden Verformung führen würde [1, 2]. Da die Schnitttiefe auf den atomaren Maßstab abnimmt, wird beim Schneiden in Richtung auf den einatomigen Schichtabtrag postuliert, dass nur eine elastische Verformung auf der bearbeiteten Oberfläche auftritt. Um dies zu überprüfen, werden die Verformungszustände des Werkstückuntergrunds während und nach dem Schneiden analysiert. Bild 8 zeigt die Fehlerstrukturen im Werkstückuntergrund bei verschiedenen Werkzeugschneidenradien. Hier werden die Atome basierend auf dem Zentrosymmetrieparameter (CSP) gefärbt, und die Atome mit einem CSP kleiner als 3 werden weggelassen, was diejenigen mit perfekter FCC-Struktur darstellt.
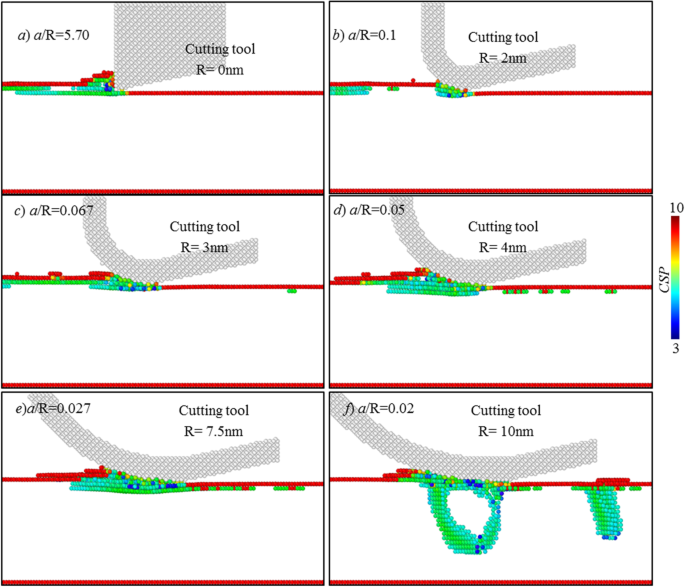
Oberflächenbeschaffenheit der bearbeiteten Oberflächen. Atome werden basierend auf ihren CSPs gefärbt
Wenn der Schneidkantenradius kleiner als 4 nm ist, wird kein Fehler unter der Oberfläche in der bearbeiteten Oberfläche gebildet. Beim Schneiden kommt es nur zu einer elastischen Verformung der bearbeiteten Oberfläche.
Wie in Fig. 8 gezeigt, werden, wenn der Schneidkantenradius gleich oder größer als 4 nm ist, Fehler unter der Oberfläche initialisiert. Darüber hinaus wird mit zunehmendem Schneidkantenradius die Anzahl von Fehlern unter der Oberfläche deutlich erhöht. Wenn der Kantenradius etwa 10 nm erreicht, wurde eine Versetzungsschleife gebildet, die nach dem Schneiden nicht verschwinden konnte, wie in Fig. 9e gezeigt. Es zeigt deutlich die plastische Verformung der bearbeiteten Oberfläche an.
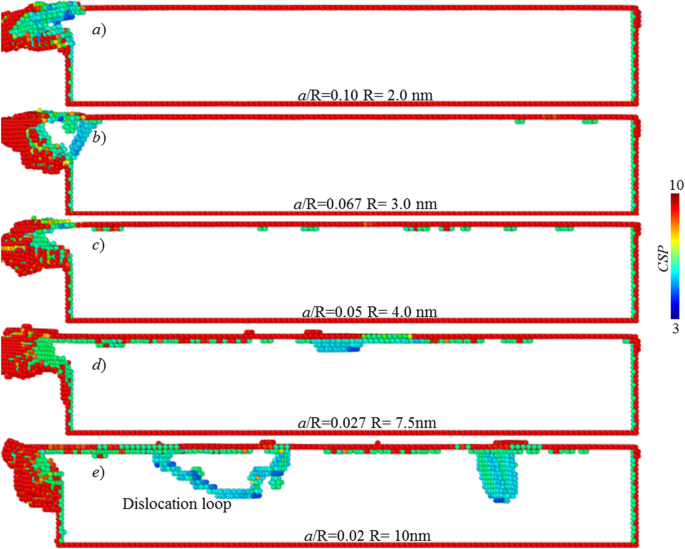
Fehler unter der Oberfläche an verschiedenen Werkzeugkantenradien. Atome werden basierend auf ihren CSPs gefärbt
Nach dem Überfahren des Werkzeugs über die Werkstückoberfläche würde der elastisch verformte Abschnitt zurückfedern; somit werden Teile von unterirdischen Defekten vernichtet. Wie in Abb. 9a–c dargestellt, liegt schließlich kein Fehler unter der Oberfläche vor, wenn der Schneidenradius 2 nm oder 3 nm beträgt.
Der plastisch verformte Abschnitt führt zu einer bleibenden Verformung. Wie in Fig. 9 gezeigt, verbleibt bei einem Werkzeugkantenradius von 7,5 nm eine kleine Anzahl von Fehlern unter der Oberfläche. Wenn der Schneidenradius 10 nm beträgt, sind die Versetzungsschleife und der Stapelfehler schließlich im Werkstückuntergrund vorhanden.
Basierend auf der obigen Analyse kann gefolgert werden, dass plastische Verformung vermieden werden sollte und nur elastische Verformung auf der bearbeiteten Oberfläche erlaubt ist, um eine schneidbasierte Einzelatomschichtentfernung zu ermöglichen. Es wird als ein charakteristisches Merkmal des schneidbasierten Verfahrens zum Entfernen einzelner Atomschichten angesehen.
Atomverschiebungsverhalten
Laut MD-Trajektoriendateien hat die Versetzungsbewegung den schneidbasierten Prozess zum Entfernen einzelner Atomschichten dominiert. Bild 10 zeigt die Simulationsergebnisse mit unterschiedlichen Schneidenradien. Bei einem Kantenradius von 2 nm wird unter der Wirkung des Schneidwerkzeugs nur die erste Atomschicht entlang der Schneidrichtung verschoben, um einen Span zu bilden, während andere immobilisiert bleiben. Es könnte als ein Querschnitt einer Kantenversetzung angesehen werden.
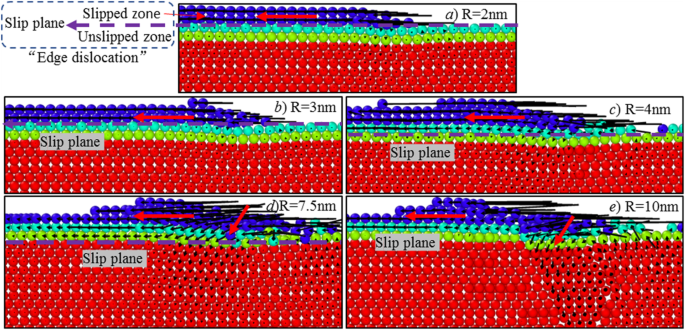
Atomares Verschiebungsverhalten bei verschiedenen Schneidenradien
Wenn der Werkzeugkantenradius zunimmt, wurde ein Teil des Materials innerhalb der ersten Atomschicht in die bearbeitete Oberfläche gepresst, was das Gleiten der Atomschichten unter der ersten Schicht bewirkt. Darüber hinaus besteht die Tendenz, dass mit zunehmendem Werkzeugkantenradius die Anzahl der Atomlagen, die einem Materialgleitprozess unterzogen werden, zunimmt. Wenn der Schneidenradius 4 nm beträgt, außer der ersten Atomlage, leitet die zweite Atomlage auch den Materialschlupf entlang der Schnittrichtung, wie in Abb. 10 dargestellt. Wenn der Schneidenradius 7,5 nm beträgt, werden beim Vorrücken des Schneidwerkzeugs die obersten drei Atomlagen auf der Werkstückoberfläche sind entlang der Schnittrichtung verrutscht. Wenn der Werkzeugkantenradius auf 10 nm erhöht wird, wurde eine große Anzahl von Materialien gepresst, um eine neue bearbeitete Oberfläche zu bilden; an der Werkstückoberfläche tritt eine plastische Verformung (siehe Abb. 10e) auf, die auch in Abb. 9 festgestellt werden kann.
Abbildung 11 zeigt den Gleitprozess der anvisierten Atomschicht entlang der Schnittrichtung. Der Bereich der Schlupfzone wird mit der Vorwärtsbewegung des Schneidwerkzeugs kontinuierlich vergrößert. Beim Schnittabstand von 17,5 nm hat die Gleitzone einen Maximalwert erreicht. Anschließend werden die Materialien innerhalb der Gleitzone kontinuierlich zu Chips geformt; das Chipvolumen wird ebenfalls erhöht.
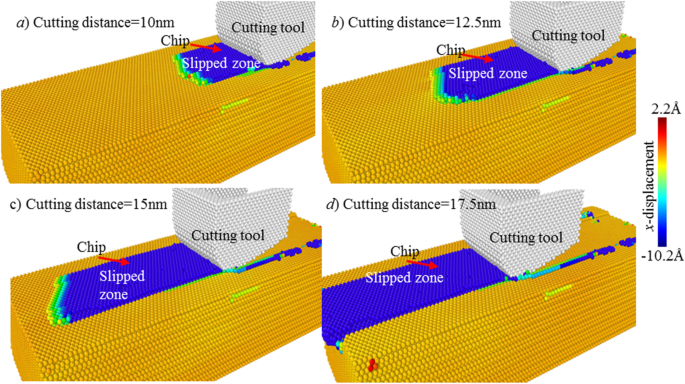
Gleitprozess der anvisierten Atomschicht bei einem Schneidkantenradius von 2 nm. Atome werden basierend auf ihren atomaren Verschiebungswerten in x-Richtung gefärbt
Insgesamt hat sich gemäß der Analyse in den Abschnitten 3.3 und 3.4 mit zunehmendem Schneidenradius sowohl der Mechanismus der Verformung unter der Oberfläche als auch das Verhalten der atomaren Verschiebung stark verändert. Bei unterschiedlichen Schneidenradien neigen unterschiedlich viele Atomlagen zum Gleiten entlang der Schnittrichtung, während auf der bearbeiteten Oberfläche unterschiedliche Verformungsregime auftreten, wie in Tabelle 2 zusammengefasst Prozess wird die Spanbildung durch eine scherspannungsgetriebene Versetzungsbewegung bestimmt, die sich deutlich von der Spanbildung beim konventionellen Schneiden und Nanoschneiden unterscheidet. Sie kann auch als ein charakteristisches Merkmal der spanabhebenden Einzelatomschichtentfernung angesehen werden
Schnittkraft
Einfluss des Kantenradiuseffekts
Abbildung 12 zeigt den Einfluss des Schneidenradius auf die gemittelten Schnittkräfte bei einer Schnitttiefe von 2 Å. Hier sind die Tangential- und Normalkomponenten der Schnittkräfte, nämlich F t und F n , verglichen werden. Wie dargestellt ist für ein scharfes Schneidwerkzeug das Verhältnis von a/R ist 2,85 und das F t von 16,4 nN ist offensichtlich kleiner als F n von 23,7 nN. Mit zunehmendem Schneidenradius werden beide von F t und F n werden erhöht. Die F n hat deutlich größere Wachstumsamplituden gezeigt als F t . Es zeigt deutlich, dass mit zunehmendem Schneidenradius die normale Schnittkraft einen größeren Einfluss auf den Materialabtragsprozess beim ACS-Schneidprozess haben würde. Wenn der Werkzeugkantenradius jedoch größer als etwa 3 nm ist, konnte die Entfernung einzelner Atomschichten nicht erreicht werden. Daher wäre eine größere normale Schneidkraft nicht hilfreich, um eine schneidbasierte Einzelatomschichtentfernung zu ermöglichen, und eine niedrigere normale Schneidkraft sollte vorzugsweise verwendet werden.
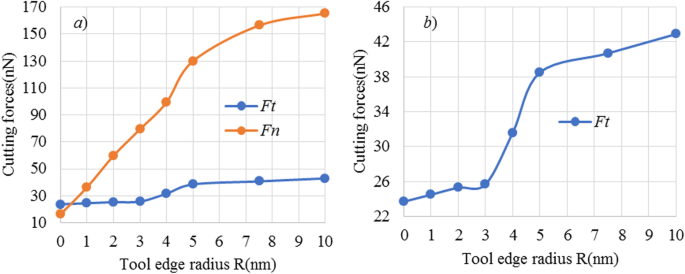
Verlauf der Schnittkräfte über dem Schneidenradius bei einer Schnitttiefe von 2 Å
Da die normalen Schnittkräfte die Druckspannung bereitstellen, um eine elastische und/oder plastische Verformung der bearbeiteten Oberfläche zu ermöglichen, würden die tangentialen Schnittkräfte die Scherspannung für die Spanbildung bereitstellen. Daher kann gefolgert werden, dass die Spanbildung bei der spanabhebenden Entfernung einzelner Atomschichten hauptsächlich durch die tangentiale Schneidkraft angetrieben werden sollte. In Abb. 12b ist auch zu sehen, dass die F t hat drei Arten von Veränderungen gezeigt, die weiter zu unterschiedlichen Oberflächentopographien führen (siehe Abb. 6), einschließlich der folgenden:
Wenn der Schneidenradius kleiner als etwa 3 nm ist, nämlich das Verhältnis von a/R ist 0,067, das F t bleibt annähernd unverändert und ist mit zunehmendem Kantenradius immer kleiner als 25 nN. In diesem Fall wird nur eine Atomschicht von der Werkstückoberfläche entfernt.
Wenn der Schneidenradius 3 nm und 5 nm beträgt, sind die Verhältnisse von a/R sind 0,04 und 0,067, während F t ist offensichtlich auf etwa 38,5 nN erhöht. Folglich wird mehr als eine atomare Schicht von der Werkstückoberfläche entfernt, aber es bildet sich eine kleine Anzahl von Oberflächendefekten.
Bei einem Kantenradius von mehr als 5 nm ist F t konvergiert ebenfalls allmählich zu einem konstanten Wert. In diesem Fall wird mehr als eine Atomschicht entfernt. Auf der Werkstückoberfläche und dem Untergrund bilden sich jedoch viele Oberflächenfehler.
Es kann gefolgert werden, dass eine sehr geringe tangentiale Schneidkraft ein schneidenbasiertes Entfernen einzelner Atomlagen bei einem vernünftigen Schneidkantenradius, wie z. B. 2 nm, ermöglichen könnte. Die Abtragung einzelner Atomlagen wiederum konnte trotz der größeren tangentialen Schnittkraft nicht realisiert werden.
Einfluss des atomaren Größeneffekts
Abbildung 13 zeigt außerdem die Auftragung der Schnittkräfte gegen die Schnitttiefe bei einem Schneidkantenradius von 2 nm. Es kann festgestellt werden, dass bei einem Schneidkantenradius von 2 nm mit zunehmender Schnitttiefe sowohl die normale Schnittkraft als auch die tangentialen Schnittkräfte dreistufige Änderungen gezeigt haben. Es gibt deutliche Änderungen bei der Schnitttiefe von etwa 1,1 Zoll und 1,6 Zoll. Das entsprechende Verhältnis der Schnitttiefe (a ) zum Atomradius des Werkstücks (r w ) sind 0,055 und 0,080, die oben genannten zwei kritischen Werte von a/r w , C1 und C2, wie in Abschnitt 3.1 dargestellt.
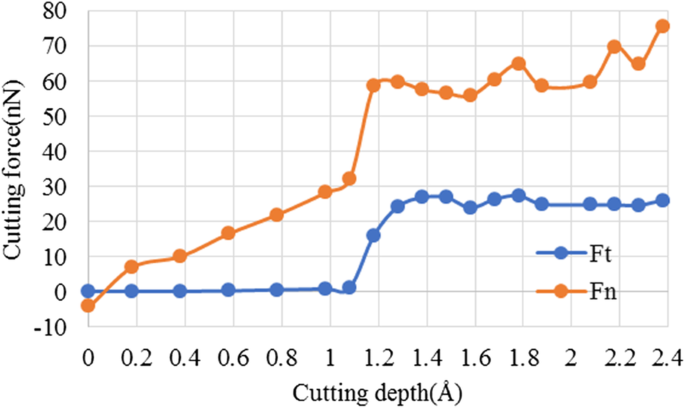
Diagramm der Schnittkräfte gegen die Schnitttiefe bei einem Kantenradius von 2 nm
When cutting depth is smaller than 1.1 Å, namely, the ratio of a/r w is less than 0.055, F t is always 0 nN, while F n is linearly increased to about 32 nN. However, the cutting forces could not enable plastic material deformation and removal on the workpiece surface. Consequently, there is only elastic deformation on workpiece surface, as shown in Fig. 3.
When the cutting depth is larger than 1.1 Å, but smaller than 1.6 Å, the ratio of a/r w is more than 0.055 but less than 0.080. If this case, F t has greatly increased from 0 nN to about 25 Nn, while F n further increased to about 58 nN. The cutting forces are larger enough to enable material removal on workpiece surface. At the cutting depth of 1.4 Å, there is chip formation and material removal on workpiece surface. But the stable and continuous material removal could not be realized and many defects are formed on the processed surface, as shown in Fig. 4.
When the cutting depth is larger than 1.6 Å, both F t und F n are large enough to enable continuous material removal on workpiece surface. Consequently, chip is stably formed over the workpiece surface, and the targeted atomic layer is continuously removed via chip formation, forming a new processed surface, as shown in Fig. 5b and Fig. 6b.
Overall, both cutting-edge radius effect and atomic sizing effect have an influence on cutting force in cutting-based single atomic layer removal process, thereby changing the material removal and surface generation process.
Discussions About Cutting-Based Single Atomic Layer Removal Mechanism
As per above analysis, both atomic sizing effect and cutting-edge radius effect have a great influence on the cutting-based single atomic layer removal mechanism. As summarized in Table 3, depending on the ratio of cutting depth to workpiece atomic radius(a/r w ) and the ratio of cutting depth to edge radius(a/R ), there are minimum 5 typical cases of material deformation and removal behaviours in cutting-based single atomic layer removal process. In this section, the fundamental material deformation and removal mechanism of each case is summarized.
In conventional machining, as cutting depth is significantly larger than the cutting-edge radius, the cutting-edge radius effect can be ignored. As the cutting depth is decreased to nanoscale, which is comparable or lower than the edge radius, the edge radius effect can be no longer ignored. In nanocutting, the material removal process is dominated by the extrusion deformation, which is greatly influenced by cutting-edge radius. As the cutting depth is further decreased to atomic scale, except for cutting-edge radius effect, a new sizing effect, atomic sizing effect [20] has a great influence on material removal.
As shown in Fig. 14, in the cutting-based single atomic layer removal process, there are two portions involving in cutting, i.e., nanometric cutting edge and the lowest cutting tool atoms (B ). Such two portions could be coupled to enable single atomic layer removal. The size of cutting edge, regarded as ‘nano-tool,’ is described by edge radius (R ). The cutting edge is the envelope curve of the outermost atoms in cutting tool. Regarding the lowest atoms, as ‘atomic-tool,’ it is described by workpiece atomic radius (r w ). The cutting-based single atomic layer removal is the results of the coupled actions of nano-tool and atomic-tool on workpiece material.
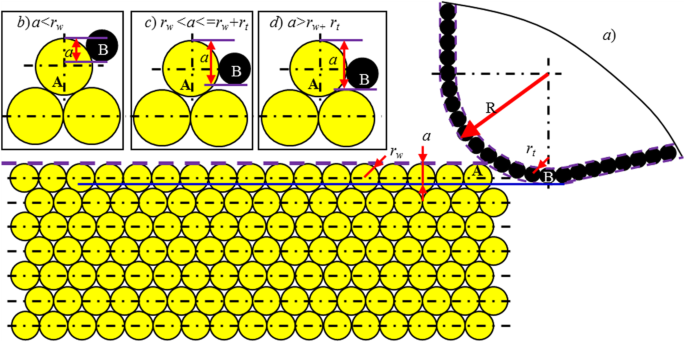
Schematic diagram for cutting-based single atomic layer removal
Firstly, depending on the ratio of cutting depth (a ) to the workpiece atomic radius (r w ), i.e., a/r , there are three kinds of material deformation behaviour in ACS cutting process.
- 1.
The ratio of a/r w is smaller than critical value 1(C1 ).
As shown in Fig. 15, chip formation does not occur, but elastic deformation does occur on the workpiece surface. During cutting process, after workpiece passes the lowest point of cutting tool, the elastically deformed part would recover completely. Consequently, no material deformation and removal occurred on the topmost surface. In such case, the tool edge effect could be ignored. This ratio could be affected by material properties (case 1).
- 2.
The ratio of a/r w is larger than C 1 , but smaller than critical value 2 (C2 ).
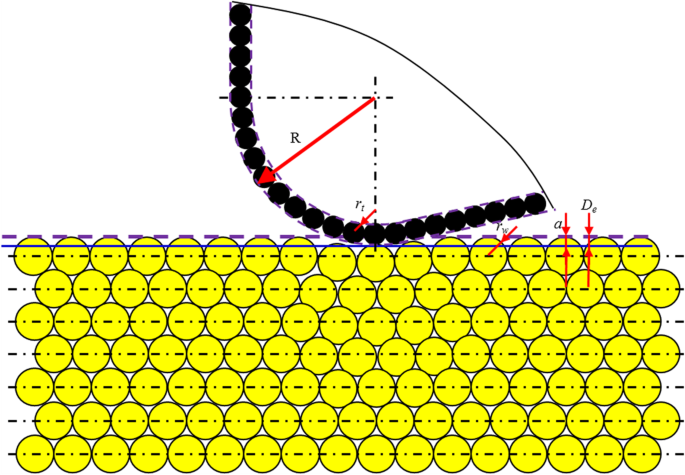
Schematic illustration of cutting-based single atomic layer removal at the ratio of a/rw smaller than C1
As the ratio of the cutting depth to atomic radius (a/r w ) increases to be larger than C1 but smaller than critical value 2(C2 ), there is material removal on the workpiece surface, but it is noncontinuous. In such case, only part of material within targeted atomic layer is formed into chip by shear stress-driven dislocation motion, while others are remained on the workpiece surface. When cutting tool passes over the workpiece surface, the surface quality of the processed surface is seriously deteriorated (case 2) (Fig. 16).
- 3.
The ratio of a/r w is larger than critical value 2 (C2 ).
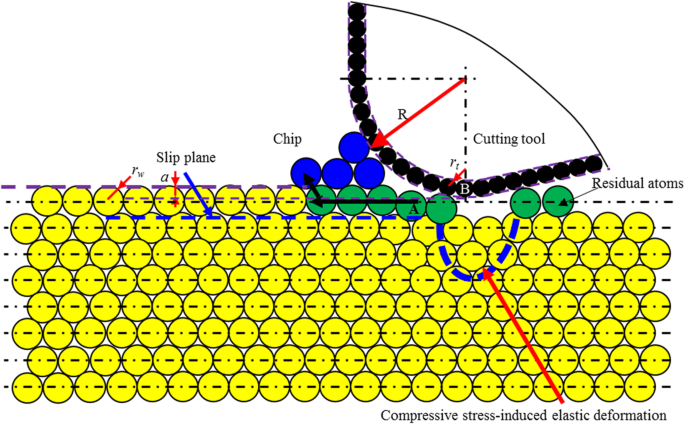
Schematic illustration of cutting-based single atomic layer removal at a/rw larger than C1 and smaller than C2
When the ratio of cutting depth to atomic radius (a/r w ) increases to be larger than critical value, there is a continuous material removal by chip formation during cutting process. In such case, the edge radius effects can no longer be ignored. For ACS cutting process, the maximum cutting depth is subnanometer order. At such extremely low cutting depth, regardless of the nominal rake angle, the effective rake angle is always largely negative. The negative rake face can produce the necessary shear stress to enable chip formation by dislocation motion and the compressive force to enable the elastic and/or plastic deformation on the processed surface.
Depending on the ratio of cutting depth (a ) to tool edge radius (R ), different kinds of elastic and/or plastic deformation process occur on the workpiece surface. There are two threshold values of a/R , namely, threshold value 1 (T 1 ) and threshold value 2 (T 2 ), leading to different material removal processes.
- a.
The ratio of a/R is larger than threshold (T 1 ).
As shown in Fig. 17, there is one atomic slip plane. The workpiece material below this plane would have an elastic deformation. As for the materials above this slip plane, it undergoes a plastic deformation by dislocation motion. A part of materials is also formed into chip by shearing stress-driven dislocation motion, while the other undergoes dislocation slip. After the workpiece passes the lowest point of the cutting tool, the elastically deformed part recovers completely (case 3).
- b.
The ratio of a/R is lower than threshold 1 (T 1 ), but larger than threshold 2 (T 2 ).
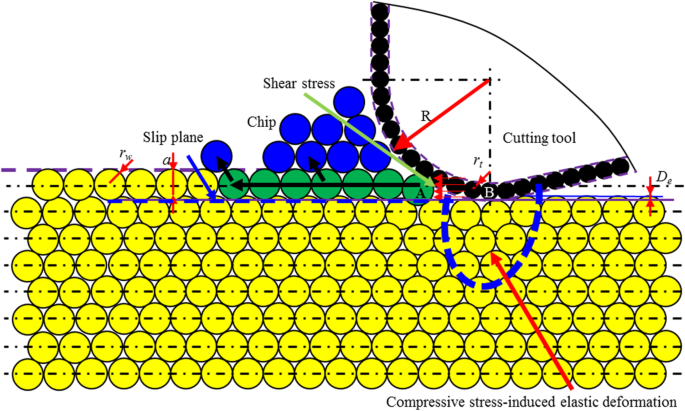
Schematic illustration of cutting-based single atomic layer removal at a/rw larger than C2 and a/R larger than T1
Under the action of cutting edge, minimum two atomic layers undergo dislocation slip, while elastic deformation occurs on the processed surface, as shown in Fig. 18. The cutting edge provides a force to generate the shear stress to enable chip formation by dislocation motion and compressive stress to induce elastic deformation on the processed surface. In such case, part of material within the targeted atomic layer is formed into chip by dislocation motion, while the other is extruded into other atomic layers to form new processed surface. It also drives the slip of other atomic layers on the workpiece surface, leading to the negative dislocation climb. After workpiece material passes the lowest point of the cutting tool, the elastic portion springs back (case 4).
- c.
The ratio of a/R is lower than threshold 2 (T 2 ).
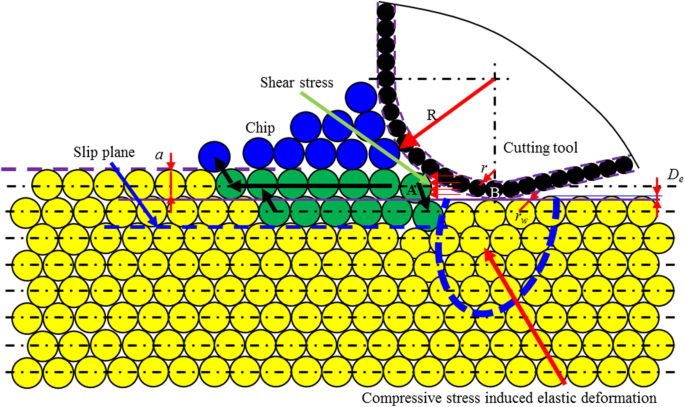
Schematic illustration of cutting-based single atomic layer removal at a/rw larger than C2 , a/R larger than T2 , smaller than T1
As the ratio of a/R decreases to lower than T 2 , there is either no chip formation or extremely small volume of chip formation, but elastic-plastic deformation occurs on the processed surface, as shown in Fig. 19. After workpiece material passes the lowest point of cutting edge, the elastic deformed part springs back. The plastic deformed part (Δ ) leads to lasting deformation. Such ratio is related with material properties, tool geometry and process conditions (case 5).
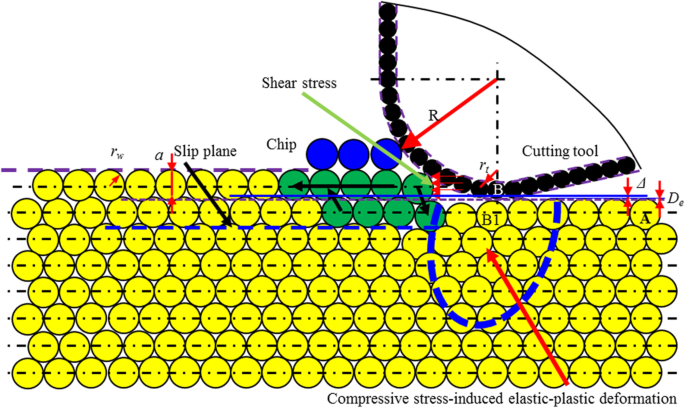
Schematic illustration of cutting-based single atomic layer removal at a/r larger than C2 and a/R lower than T2
Schlussfolgerungen
In the present study, both of atom sizing effect and cutting-edge radius effect are analysed to investigate their influence on chip formation, surface generation, subsurface deformation, and atomic displacement behaviour during the cutting of monocrystalline copper towards single atomic layer removal. The following conclusions can be drawn.
- 1.
A new model is proposed to describe the underlying material deformation and removal mechanism in the cutting-based single atomic layer removal process, which exhibits four characteristics, including chip formation by dislocation motion, elastic deformation occurring on the processed surface, atomic sizing effect, and cutting-edge radius effect.
- 2.
Both of atomic sizing effect and cutting-edge radius effect have a great influence on the material deformation and removal during the cutting process of monocrystalline copper towards single atomic layer removal. With a specific ratio of cutting depth to workpiece atom radius (a/r w ) and that of cutting depth to edge radius (a/R ), cutting-based single atomic layer removal could be achieved on Cu (111) surface.
- 3.
Chip formation is affected by the ratios of a/r w and a/R . There is a chip formation only when the ratio of a/r w is larger than one critical value (C1) and the ratio of a/R is smaller than one threshold value (T1). Moreover, chip formation is mainly dependent on the shear stress-driven dislocation motion, significantly different from the extrusion-dominated chip formation in nanocutting and shearing-dominated chip formation in conventional machining.
- 4.
Single atomic layer removal can be achieved via layer-by-layer removal and multi-layer removal. The former one refers to that the targeted atomic layer could be either fully removed from workpiece surface. The latter one means that the first atomic layer is partly removed while the remaining materials are pressed into other atomic layers, forming a new processed surface.
- 5.
There is only elastic deformation occurring on the processed surface during ACS cutting process, different from the elastic-plastic deformation in nanocutting. It can be regarded as one characteristic feature in ACS cutting.
- 6.
Depending on the combined effect of atom sizing effect and cutting-edge radius effect, there exist five cases of material deformation and removal processes during the cutting-based single atomic layer removal, i.e., no workpiece material is removed (case 1), workpiece materials are non-continuously removed (case 2), a part of materials is formed into chip while others undergoes material slip via dislocation motion (case 3), a part of materials within the targeted atomic layer is formed into chip while others are extruded into other atomic layers to form new processed surface (case 4), and the elastic deformed part springs back, while the plastic deformed part leads to a lasting deformation (case 5).
Verfügbarkeit von Daten und Materialien
Authors declare that the materials, data, and associated protocols are available to the readers, and all the data used for the analysis are included in this article.
Abkürzungen
- ACS:
-
Atomic and close-to-atomic scale
- ACSM:
-
Atomic and close-to-atomic scale manufacturing
- MD:
-
Molekulardynamik
Nanomaterialien
- Advanced Atomic Layer Deposition Technologies für Mikro-LEDs und VCSELs
- Synergistische photokatalytische Adsorptionsentfernung des basischen Magenta-Effekts von AgZnO/Polyoxometallaten-Nanokompositen
- Die antibakteriellen hierarchischen Polyamid-6-ZnO-Nanofasern, hergestellt durch Atomlagenabscheidung und hydrothermales Wachstum
- Photokatalytische Eigenschaften von Co3O4-beschichteten TiO2-Pulvern, hergestellt durch plasmaunterstützte Atomlagenabscheidung
- Fermi-Level-Tuning von ZnO-Filmen durch Supercycling-Atomschichtabscheidung
- Studie zum Effekt der Aufprallrichtung auf den nanometrischen Schleifprozess mit Molekulardynamik
- Dickenabhängigkeit von Grenzflächen- und elektrischen Eigenschaften in Atomlagen-abgeschiedenem AlN auf c-Ebenen-GaN
- Plasmaunterstützte Niedertemperatur-Atomschichtabscheidung von SiO2 mit Kohlendioxid
- Silizium-Nanodraht-Heterojunction-Solarzellen mit einem Al2O3-Passivierungsfilm, hergestellt durch Atomlagenabscheidung
- Einzelgehrungsschnitt im Vergleich zur Doppelgehrungssäge