Leonardo und CETMA:bahnbrechende Verbundwerkstoffe für geringere Kosten und geringere Umweltbelastung
Dieser Blog basiert auf meinem Interview mit Stefano Corvaglia, Werkstoffingenieur, Leiter Forschung &Entwicklung und IP-Manager der Leonardo Aerostructures Division (Grottaglie, Pomigliano, Foggia, Nola Produktionsstätten, Süditalien) und Dr. Silvio Pappadà, Forschungsingenieur und Leiter von Programmen mit Leonardo bei CETMA (Brindisi, Italien).
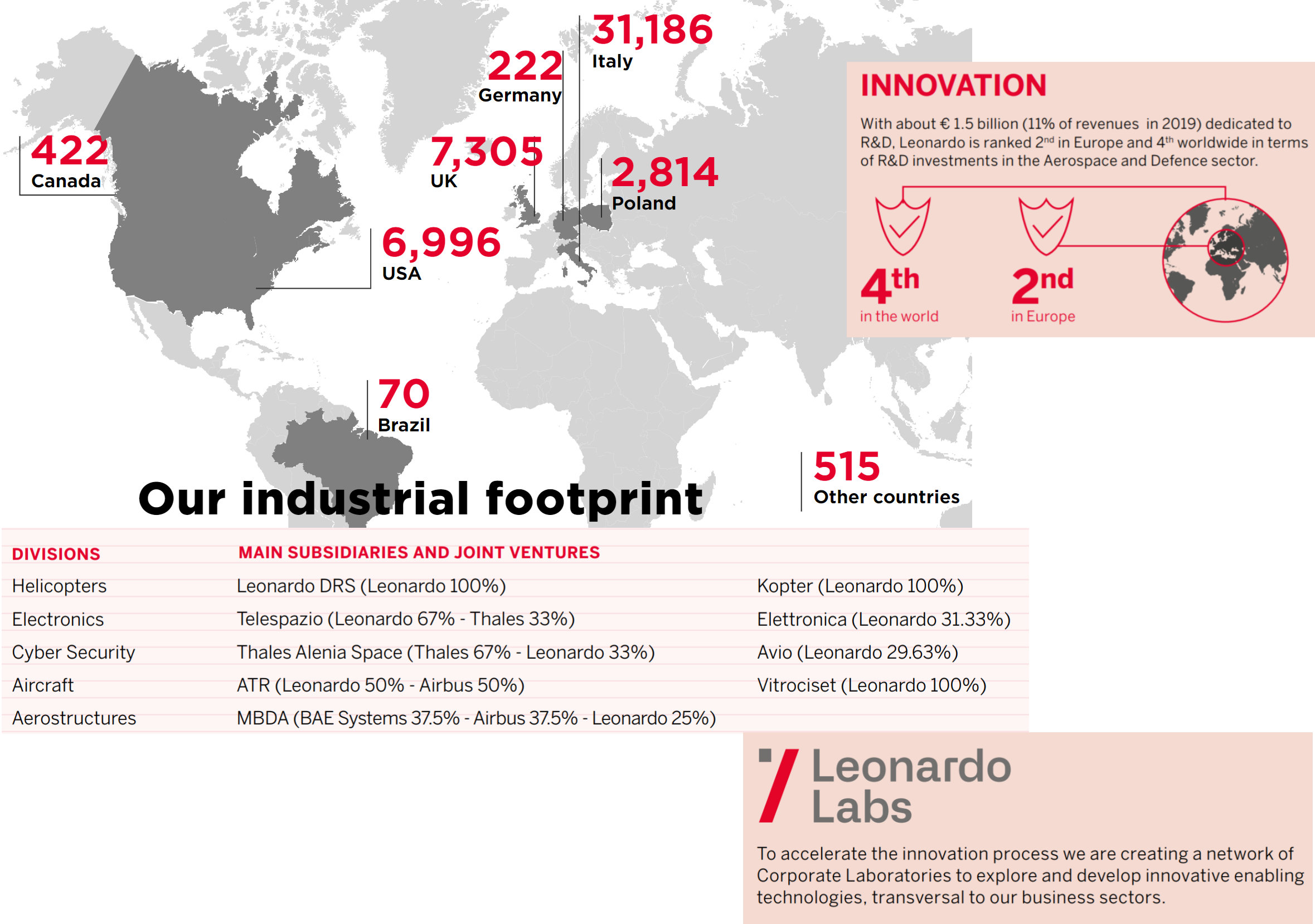
Leonardo (Rom, Italien) ist mit 13,8 Milliarden Euro Umsatz und mehr als 40.000 Mitarbeitern weltweit einer der weltweit größten Player in den Bereichen Luft- und Raumfahrt, Verteidigung und Sicherheit. Das Unternehmen bietet umfassende Lösungen auf globaler Ebene für Luft-, Land-, See-, Weltraum-, Cyber- und Sicherheitssysteme sowie unbemannte Systeme. Mit etwa 1,5 Milliarden Euro (11 % des Umsatzes im Jahr 2019) für Forschung und Entwicklung steht Leonardo in Europa auf Platz 2 und weltweit auf Platz 4 in Bezug auf Forschungsinvestitionen im Luft- und Raumfahrt- und Verteidigungssektor.
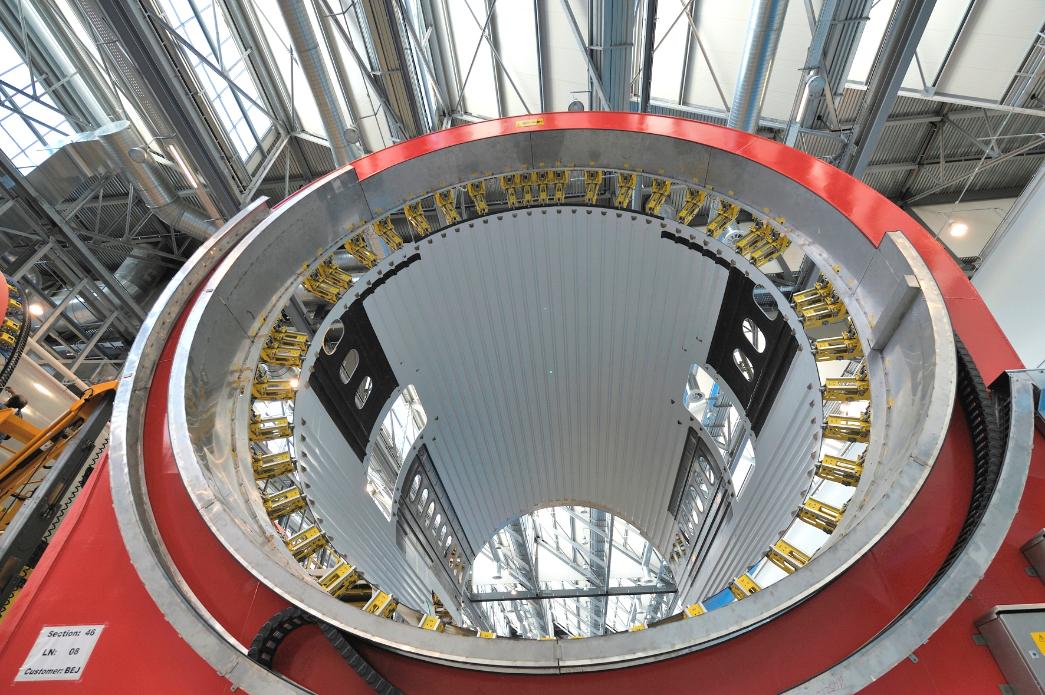
Über seine Aerostructures Division bietet Leonardo die Herstellung und Montage großer Strukturkomponenten, einschließlich Rümpfe und Leitwerke, aus Verbundwerkstoffen und traditionellen Materialien für die wichtigsten zivilen Flugzeugprogramme der Welt.
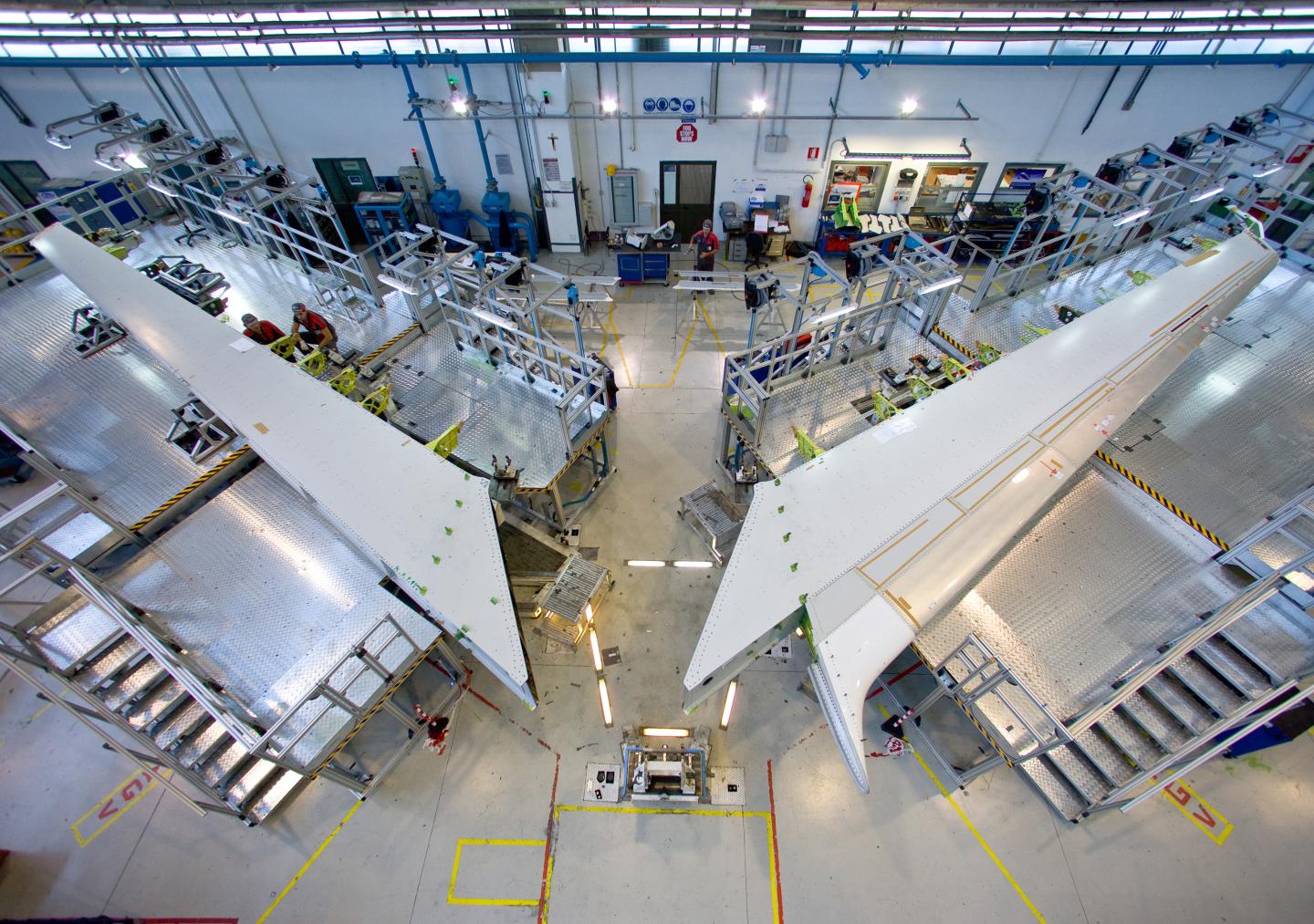
Im Bereich Verbundwerkstoffe produziert Leonardo Aerostructures Division „one-piece Barrels“ für die zentralen Rumpfsektionen 44 und 46 der Boeing 787 im Werk Grottaglie sowie die Höhenleitwerke im Werk Foggia – insgesamt rund 14 % der 787-Flugzeugzelle. Die weitere Produktion von Verbundstrukturen umfasst im Werk Foggia die Herstellung und Montage von Leitwerken für ATR- und Airbus A220-Verkehrsflugzeuge. Foggia produziert auch Verbundteile für die Boeing 767 und für Militärprogramme, darunter den Joint Strike Fighter F-35, den Eurofighter Typhoon-Kampfjet, den C-27J-Militärtransporter und den Falco Xplorer, das neueste Mitglied der Falco-Familie unbemannter Flugzeuge von Leonardo.
Zusammenarbeit mit CETMA
„Wir haben viele laufende Aktivitäten mit CETMA, zum Beispiel bei thermoplastischen Verbundwerkstoffen und Resin Transfer Moulding (RTM)“, sagt Corvaglia. „Unser Ziel ist es, die F&E-Aktivitäten in kürzester Zeit produktionsreif zu machen. In unserer Abteilung (F&E und IP-Management) suchen wir auch nach disruptiven Technologien mit einem niedrigeren TRL [Technologiebereitschaftsgrad – dh niedrigerer TRL ist im Entstehen und weiter von der Produktion entfernt], aber wir wollen wettbewerbsfähiger sein und unsere Kunden weltweit unterstützen .“
„Von Beginn unserer Zusammenarbeit an“, fügt Pappadà hinzu, „haben wir immer versucht, Kosten und Umweltbelastung gering zu halten. Wir haben festgestellt, dass thermoplastische Verbundwerkstoffe (TPC) beides gegenüber Duroplasten reduzieren.“
Corvaglia merkt an, dass „wir zusammen mit Silvios Team diese Technologien entwickelt und einige automatisierte Zellprototypen gebaut haben, um diese in der Produktion zu evaluieren.“
Kontinuierliches Formpressen (CCM)
„CCM ist ein gutes Beispiel für unsere Zusammenarbeit“, sagt Pappadà. „Leonardo hat einige Komponenten aus duroplastischen Verbundwerkstoffen identifiziert und gemeinsam haben wir Technologien erforscht, um diese in TPC bereitzustellen
„Wir brauchten eine neue Produktionstechnologie, die sich durch niedrige Kosten und hohe Geschwindigkeit auszeichnet“, fährt er fort. Er weist darauf hin, dass in der Vergangenheit einzelne TPC-Komponenten mit viel Abfall hergestellt wurden. „Deshalb produzieren wir Netzformen auf Basis des nicht-isothermen Formpressens, jedoch mit einigen Innovationen (Patente laufen noch), um Ausschuss zu reduzieren. Dafür haben wir eine vollautomatisierte Zelle konstruiert, die dann ein italienisches Unternehmen für uns gebaut hat.“
Diese Zelle ist in der Lage, die von Leonardo entworfenen Komponenten zu produzieren, sagt Pappadà, „mit einer Rate von einer Komponente alle 5 Minuten, 24 Stunden am Tag.“ Allerdings musste sich sein Team dann um die Herstellung des Preforms kümmern. „Am Anfang brauchten wir einen flachen Laminierprozess, denn das war damals der Flaschenhals“, erklärt er. „Unser Prozess beginnt also mit einem Rohling (flaches Laminat), erhitzt diesen in einem Infrarot-(IR)-Ofen und führt ihn dann zum Formen in eine Presse. Flachlaminate werden normalerweise mit großen Pressen hergestellt und benötigen 4-5 Stunden Zykluszeit. Wir beschlossen, ein neues Verfahren zu untersuchen, mit dem flache Laminate schneller hergestellt werden können. So haben wir bei CETMA mit Unterstützung der Leonardo-Ingenieure eine hochproduktive CCM-Linie entwickelt. Wir haben die Zykluszeit für ein 1 Meter mal 1 Meter großes Teil auf 15 Minuten reduziert. Wichtig ist, dass es sich um einen kontinuierlichen Prozess handelt, sodass wir unbegrenzte Längen produzieren können.“
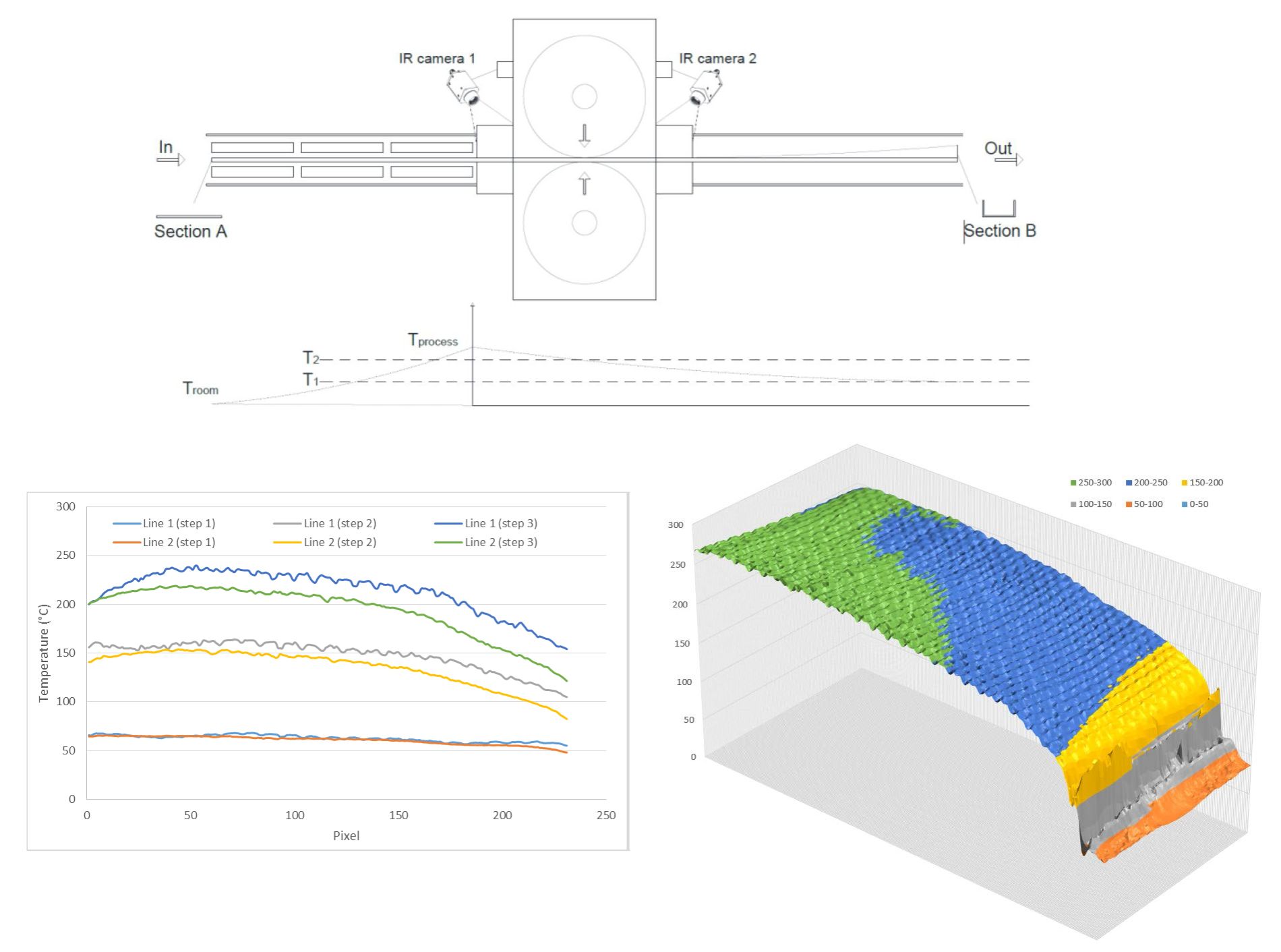
Aber wie ist diese Neuerung im Vergleich zu dem CCM, das seit über einem Jahrzehnt von Xperion, jetzt XELIS (Markdorf, Deutschland) verwendet wird? „Wir haben analytische und numerische Modelle entwickelt, die Defekte wie Hohlräume vorhersagen können“, sagt Pappadà. „Wir haben dies in Zusammenarbeit mit Leonardo und der Universität Salento (Lecce, Italien) getan, um Parameter und deren Einfluss auf die Qualität zu verstehen. Wir haben diese Modelle verwendet, um dieses neue CCM zu entwickeln, bei dem wir eine sehr hohe Dicke, aber auch eine hohe Qualität haben können. Dank dieser Modelle können wir Temperatur und Druck optimieren, aber auch wie diese angewendet werden. Es gibt viele technologische Aspekte, die Sie entwickeln können, um eine gleichmäßige Temperatur- und Druckverteilung zu erreichen; Wir mussten jedoch den Einfluss dieser auf die mechanische Leistung und das Wachstum von Defekten in Verbundstrukturen verstehen.“
Pappadà fährt fort:„Unsere Technologie ist flexibler. Auch CCM wurde vor 20 Jahren entwickelt, aber es gibt keine Informationen darüber, weil die wenigen Unternehmen, die es verwendeten, kein Wissen und Know-how teilten. Wir mussten also bei null anfangen, nur mit unserem Wissen über Verbundwerkstoffe und Verarbeitung.“
„Wir arbeiten jetzt über interne Programme und mit unseren Kunden zusammen, um Teile für diese neuen Technologien zu finden“, sagt Corvaglia. „Diese Teile können umgestaltet und neu qualifiziert werden, um die Produktion aufzunehmen.“ Wieso den? „Das Ziel ist ein möglichst leichtes, aber auch preislich wettbewerbsfähiges Flugzeug. Wir müssen also auch mit der Dicke optimieren. Aber wir könnten herausfinden, dass ein Teil noch leichter werden kann oder mehrere Teile mit einer ähnlichen Form identifizieren, was erhebliche Kosteneinsparungen ermöglichen könnte.“
Bis jetzt, bekräftigt er, sei diese Technologie in den Händen einiger weniger gewesen. „Aber wir haben alternative Technologien entwickelt, um diese Prozesse durch das Hinzufügen fortschrittlicherer Pressformen noch stärker zu automatisieren. Wir legen ein flaches Laminat ein und heraus kommt ein Teil, fertig. Wir befinden uns in der Phase der Neukonstruktion von Teilen und der Entwicklung von flachen versus geformten CCM.“
„Mit CETMA haben wir jetzt eine sehr flexible CCM-Linie“, sagt Pappadà, „wo wir je nach Bedarf unterschiedliche Drücke anwenden können, um komplexe Formen zu erreichen. Die Linie, die wir zusammen mit Leonardo entwickeln werden, wird sich stärker auf Komponenten konzentrieren, die den spezifischen Anforderungen entsprechen. Wir denken, wir könnten unterschiedliche CCM-Linien für Flachpaneele und L-Stringer im Vergleich zu komplexeren Formen haben. Auf diese Weise können wir die Ausrüstungskosten im Vergleich zu den großen Pressen senken, die derzeit zur Herstellung von TPC-Teilen mit komplexer Geometrie verwendet werden.“
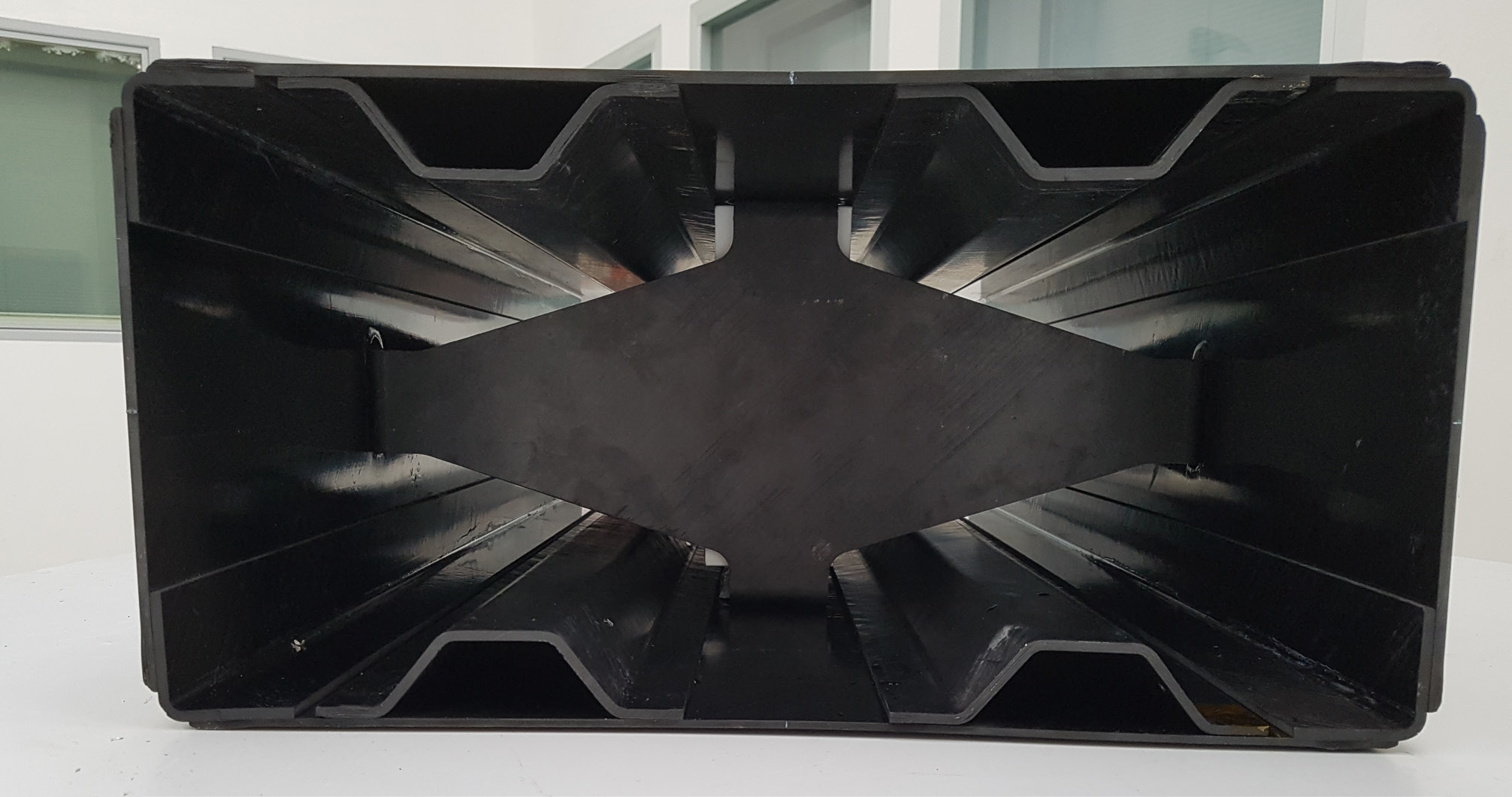
Induktionsschweißen zur in-situ-Konsolidierung
„Induktionsschweißen ist für Verbundwerkstoffe sehr interessant, weil es möglich ist, die Temperatur sehr gut abzustimmen und zu kontrollieren, sehr schnell zu erhitzen und sehr genau zu steuern“, bemerkt Pappadà. „Mit Leonardo haben wir das Induktionsschweißen zum Fügen von TPC-Komponenten entwickelt. Aber jetzt denken wir darüber nach, das Induktionsschweißen für die in-situ-Konsolidierung (ISC) von TPC-Bändern zu verwenden. Dazu haben wir ein neues Kohlefaserband entwickelt, das durch Induktionsschweißen mit einer speziellen Maschine sehr schnell erhitzt werden kann. Das Band verwendet die gleichen Matrixmaterialien wie kommerzielle Bänder, jedoch mit einer anderen Architektur, die die elektromagnetische Erwärmung verbessert. Wir optimieren die mechanische Leistung, denken aber auch an den Prozess und versuchen, unterschiedliche Anforderungen zu erfüllen, beispielsweise wie man mit Automatisierung kosteneffektiv verarbeitet.“
Er weist darauf hin, dass ISC mit TPC-Band bei guten Produktionsraten sehr schwer zu erreichen ist. „Um dies für die industrielle Produktion zu haben, muss man schneller heizen und kühlen und sehr kontrolliert Druck ausüben. Daher haben wir uns entschieden, Induktionsschweißen zu verwenden, um nur einen kleinen Bereich zu erwärmen, in dem wir das Material verfestigen, den Rest des Laminats jedoch kalt lassen.“ Induktionsschweißen für die Montage hat eine höhere TRL, sagt Pappadà. “
Die Verwendung von Induktionserwärmung für die In-situ-Konsolidierung scheint sehr störend zu sein – etwas, das derzeit kein anderer OEM oder Tierlieferant offen tut. „Ja, das ist möglicherweise eine disruptive Technologie“, sagt Corvaglia. „Wir haben die Maschine und die Materialien patentieren lassen. Wir streben nach etwas, das mit Duroplasten vergleichbar ist. Viele haben AFP (Automated Fiber Placement) mit TPC ausprobiert, müssen jedoch einen zweiten Schritt zur Konsolidierung durchführen. Dies ist eine große Einschränkung in Bezug auf Geometrie, Kosten, Zykluszeit und Größe der Teile. Wir könnten tatsächlich die Art und Weise ändern, wie Luftfahrtteile hergestellt werden.“
SQRTM
Neben Thermoplasten beschäftigt sich Leonardo weiterhin mit RTM-Technologien. „Auch hier haben wir mit CETMA zusammengearbeitet und neue Entwicklungen basierend auf einer älteren Technologie, in diesem Fall SQRTM, patentiert. Das gleiche qualifizierte Resin Transfer Moulding (SQRTM) wurde ursprünglich von Radius Engineering (Salt Lake City, Utah, USA) entwickelt. „Es ist wichtig, eine Methode außerhalb des Autoklaven (OOA) zu haben, die es uns ermöglicht, bereits qualifiziertes Material zu verwenden“, sagt Corvaglia. „Außerdem können wir Prepregs mit bekannten Eigenschaften und Qualität verwenden. Wir haben einen Flugzeugfensterrahmen mit dieser Technologie entwickelt, demonstriert und patentiert.“
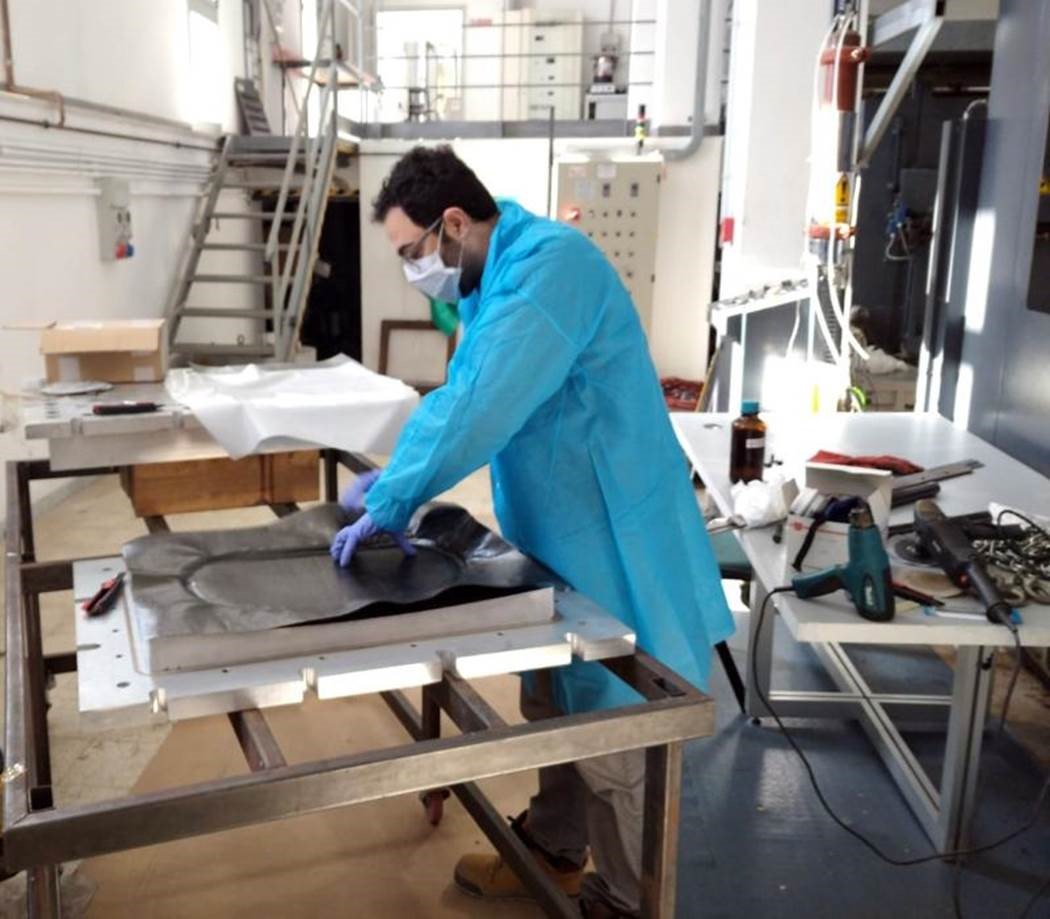
„Dies ist ebenfalls eine ältere Technologie, aber wenn Sie im Internet surfen, können Sie keine Informationen zu dieser Technik finden“, bemerkt Pappadà. „Wichtig ist, dass wir wiederum mit analytischen Modellen die Prozessparameter vorhersagen und optimieren. Mit dieser Technologie können wir eine gute Harzverteilung erzielen – ohne trockene Bereiche oder Harzansammlungen – und einen Hohlraumgehalt von nahezu null. Wir können eine hohe strukturelle Leistung erzielen, weil wir den Fasergehalt kontrollieren können, und diese Technologie kann verwendet werden, um komplexe Formen herzustellen. Wir verwenden dieselben Materialien, die für die Autoklavenhärtung geeignet sind, jedoch in einem OOA-Verfahren, aber Sie können auch schnell härtende Harze verwenden, um die Zykluszeit auf Minuten zu reduzieren.“
„Selbst mit dem aktuellen Prepreg haben wir die Aushärtezeit verkürzt“, bemerkt Corvaglia. „Im Vergleich zu einem normalen Autoklavenzyklus von 8-10 Stunden können wir beispielsweise mit SQRTM 3-4 Stunden für ein Teil wie einen Fensterrahmen erreichen. Hitze und Druck werden direkt auf das Teil aufgebracht, und die aufzuheizende Masse ist geringer. Außerdem ist das Erhitzen des flüssigen Harzes gegenüber der Luft in einem Autoklaven schneller und die Teilequalität ist hervorragend, was insbesondere bei komplexen Formen von Vorteil ist. Es gibt keine Nacharbeit, nahezu keine Hohlräume und eine hervorragende Oberflächenqualität, da das Werkzeug sie kontrolliert, kein Vakuumbeutel.“
Visionäre, technologiebasierte Zukunft
Leonardo produziert Innovationen in einer Vielzahl von Technologien. Aufgrund der schnellen technologischen Entwicklung werden Investitionen in risikoreiche Forschung und Entwicklung (niedrige TRL) als entscheidend angesehen, um die für zukünftige Produkte erforderlichen neuen Technologien zu entwickeln, die über die inkrementelle (kurzfristige) Entwicklung hinausgehen, die sie bereits bei aktuellen Produkten unterstützt. Eine solche Kombination aus kurz- und langfristigen Strategien wird im F&E-Masterplan 2030 von Leonardo kombiniert, einer einheitlichen Vision für ein nachhaltiges und wettbewerbsfähiges Unternehmen.
Als Teil dieses Plans startet es die Leonardo Labs, ein internationales Netzwerk von Forschungs- und Entwicklungslabors von Unternehmen, die sich der fortschrittlichen Forschung und technologischen Innovation widmen. Für 2020 wird das Unternehmen die Eröffnung der ersten sechs Leonardo Laboratories in den Gebieten Mailand, Turin, Genua, Rom, Neapel und Taranto fortsetzen und stellt 68 Forscher (Leonardo Research Fellows) mit Fähigkeiten in den folgenden Bereichen ein:36 Positionen im Bereich Künstliche Intelligenz und autonome intelligente Systeme, 15 in Big Data Analytics, 6 in High Performance Computing, 4 in Elektrifizierung von Luftfahrtplattformen, 5 in Materialien und Strukturen und 2 in Quantentechnologien. Leonardo Labs wird die Rolle von Innovations-Außenposten und Generatoren von Leonardos Zukunftstechnologien spielen.
Insbesondere können die Technologien, die Leonardo in Flugzeugen vermarktet, auch in seinen Land- und Seeabteilungen Anwendung finden. Bleiben Sie dran für weitere Updates zu Leonardo und seinen möglichen Auswirkungen auf Verbundwerkstoffe.
Harz
- Ultraleichte TPE-Verbundwerkstoffe für Schuhe
- Schaumstoff PP zur Verbesserung von Nachhaltigkeit und Kosten
- Graphen- und Polymerverbundstoffe für Superkondensatoranwendungen:ein Rückblick
- Anpassung von Ultraschallsensoren für die Optimierung und Steuerung von Verbundwerkstoffprozessen
- OTOMcomposite entwickelt Software für die Composites 4.0-Produktion mit lasergestützter Bandplatzierung und -wicklung
- Wiederaufbereitbare, reparierbare und recycelbare Epoxidharze für Verbundwerkstoffe
- Solvay-Verbundwerkstoffe für Rennkatamarane ausgewählt
- Konsortium für thermoplastische Verbundwerkstoffe strebt die Massenproduktion für die Automobil- und Luftfahrtindustrie an
- Umweltauswirkungen der Halbleiter- und Elektronikfertigung
- Tragbarer Gassensor für Gesundheits- und Umweltüberwachung