Medizinische Fertigung wird intelligenter
Die digitalisierte und automatisierte Fertigung macht Fortschritte in der Welt der medizinischen Fertigung, was durch die jüngsten Systeme belegt wird, die während der COVID-19-Pandemie in Produktionslinien eingebaut wurden.
Angesichts der strengen Standards, die die Herstellung medizinischer Geräte regeln, ist die datenzentrierte Industrie 4.0-Umgebung maßgeschneidert für Vertragshersteller, die versuchen, die Spezifikationen einzuhalten und gleichzeitig mit dem dramatischen Mangel an qualifizierten Bedienern fertig zu werden.
Nach wie vor werden Materialien anspruchsvoller und Teile immer kleiner, mit komplexeren Geometrien und engeren Toleranzanforderungen.
Im weitesten Sinne treiben Trends im Gesundheitswesen – alternde Bevölkerungen, der Trend zu mehr Ferndiagnosen und -therapien außerhalb der teuren Krankenhausumgebung, personalisiertere Therapien – die Entwicklung medizinischer Geräte voran. Und angesichts anhaltender pandemischer Unsicherheiten und der daraus resultierenden angeschlagenen Lieferketten ist die Schaffung von mehr Transparenz über die Arbeitsweise von Lieferanten und Anbietern Priorität Nr. 1.
Mit der Digitalisierung des Gesundheitswesens geht die Notwendigkeit einher, alle gesammelten Daten zu sichern. Zu diesem Zweck gibt es Initiativen wie das neue Center for Medical Device Cybersecurity der University of Minnesota, das am 9. September angekündigt wurde. Fünf Schwergewichte der Gesundheitsbranche haben sich zusammengeschlossen, um in dem neuen Zentrum zusammenzuarbeiten:Boston Scientific, Smiths Medical, Optum, Medtronic und Abbot Labore. Ihr Ziel ist es, Software-Schwachstellen in medizinischen Geräten zu beseitigen, die möglicherweise dazu verwendet werden könnten, Patienten zu schaden oder Gesundheitseinrichtungen zu stören.
Die Hightech-Zukunft des Gesundheitswesens bedeutet auch mehr Roboterdiagnostik und -verfahren, daher der Bedarf an mehr medizinischen Werkzeugen und Teilen, die für die Verwendung mit diesen Systemen bestimmt sind. Beispielsweise gab XACT Robotics in Hingham, Mass., der Entwickler des XACT ACE Robotic Systems, am 30. August bekannt, dass es die Patientenaufnahme in die erste US-Studie zur Bewertung von XACT ACE für die Verwendung bei perkutanen Lungeneingriffen erfolgreich abgeschlossen hat. Dazu gehören Biopsien, um das Vorhandensein von Krebs zu bestätigen. Das freihändige Robotersystem könnte Krebs früher und weniger invasiv erkennen.
Unterdessen prognostiziert iData Research, dass bis 2025 jährlich 3 Millionen robotergestützte chirurgische Eingriffe durchgeführt werden. Roboterarme an Geräten wie dem da Vinci-Chirurgiesystem werden viele der miniaturisierten Instrumente erfordern, die Ärzte steuern, um diese minimalinvasiven Operationen durchzuführen. Bei Roboteroperationen werden kleinere Einschnitte verwendet, was zu weniger Blutverlust und Narbenbildung, kürzeren Krankenhausaufenthalten und schnellerer Genesung führt.
Datengestützte KI wird auch bei der Verbesserung der Patientenergebnisse in den Vordergrund treten. Ein klarer Indikator für diesen Weg ist die Übernahme von Gauss Surgical aus Menlo Park, Kalifornien, durch Stryker. Gauss hat Triton entwickelt, eine Plattform mit künstlicher Intelligenz zur Überwachung des Blutverlusts während der Operation.
Die additive Fertigung wird auch ihre entscheidende Rolle bei der Herstellung patientenspezifischer Implantate, Werkzeuge und chirurgischer Trainingsmodelle weiter ausbauen. Das italienische Unternehmen Tsunami Medical beispielsweise begeistert die Branche mit dem Einsatz von Laser- und Elektronenstrahl-3D-Drucksystemen von GE Additive zur Herstellung einer Reihe hochkomplexer Wirbelsäulenimplantate.
Kleinteile, Herausforderungen beim Sortieren
Da sich die Materialien für medizinische Geräte weiterentwickeln und die Teile immer kleiner werden, kommen die Maschinen der L-Serie im Schweizer Stil von Marubeni Citizen-Cincom (MCC), Allendale, N.J., dem Ruf nach.
„Medical hat Materialien, von denen Sie noch nie zuvor gehört haben“, scherzte Präsident und COO Brian Such. Zähe Materialien können für einfache Teile oder komplexere Komponenten verwendet werden, die den Einsatz vieler Werkzeuge erfordern, um die verschiedenen Merkmale zu erzeugen.
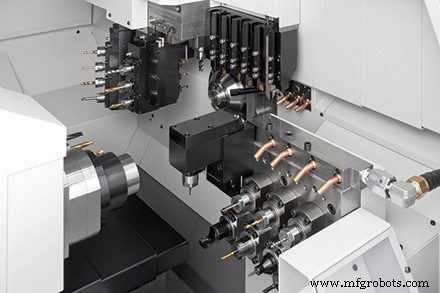
„Unsere Maschinen der L-Serie sind eine Gangmaschine mit Gegenspindel“, und ihr wesentlicher Vorteil für die medizinische Produktion besteht darin, dass sie modular aufgebaut sind, erklärte Such. „Mit einer Reihe von Tools, die jederzeit verfügbar sind, können wir einfach eines herausziehen und drei an derselben Stelle platzieren.“
Um die kleineren Durchmesser zu handhaben, die für aktuelle medizinische Bohrer und Fräser typisch sind, bietet MCC Speeder mit bis zu 4-facher Beschleunigung an. „Unsere angetriebenen Werkzeuge erreichen je nach Modell Drehzahlen von bis zu 6.000 oder 9.000 U/min, aber wir können einen anderen Werkzeughalter einschieben, und jetzt sind wir bei 36.000 U/min. Wenn das nicht ausreicht, können wir unsere Elektrospindeln nachrüsten, die bis zu 80.000 U/min erreichen können.“
Als Beispiel, so merkte Such an, könnte ein Kunde ein Achttausendstel-Loch bohren, „also brauchen Sie dafür etwas Geschwindigkeit – oder verwenden Sie einen 16-Tausendstel-Schaftfräser oder vielleicht sogar einen Achttausendstel-Schaftfräser, um sich irgendwo um eine Ecke zu lehnen . Mit unseren Elektrospindeln mit 80.000 U/min können wir in diese Taschen gleiten. Und dasselbe Werkzeug kann als Stirnwerkzeug, Kreuzwerkzeug oder nach hinten gerichtetes Werkzeug verwendet werden, es ist also sehr modular.“ MCC ist eine Partnerschaft mit dem Anbieter von Hochgeschwindigkeitsspindeln NSK eingegangen, um diese proprietären Spindeln zu entwickeln.
Vor etwa zwei Jahren erweiterte MCC die Funktionalität der B-Achse seiner Maschinen durch die Einführung der ATC-Version (automatischer Werkzeugwechsler) seiner L20-Maschine. „Jetzt haben wir die Fähigkeit von 13 Werkzeugen auf der B-Achse“, sagte Such, während eine B-Achse normalerweise nur vier Werkzeuge hat – und das „ziemlich heißes Zeug für den medizinischen Markt“ angesichts der engen Winkel der heutigen Teile. P>
Eine weitere MCC-Innovation, die etwa 2016 eingeführt wurde, ist das niederfrequente Vibrationsschneiden (LFV). Bei diesem Prozess „oszilliert die Werkzeugmaschine den Schnittpfad der Z- oder X-Achse und bewegt sich mit sehr hoher Geschwindigkeit hinein und heraus, um kleine Luftschnitte zu machen und die Späne während der Bearbeitung zu brechen“, sagte Such. „Der medizinische Bereich liebt die LFV-Technologie, und die meisten Kunden, die sie zum ersten Mal verwenden, sagen:‚Ich werde nie wieder eine Maschine ohne sie kaufen.‘“ Mit LFV „werden Sie zu 100 Prozent die Späne brechen; es gibt kein dazwischen. Sobald Sie den Prozess zum Laufen gebracht haben, ist er garantiert. Sie müssen Ihre Schneidwerkzeuge immer noch kennen, und Schneidwerkzeuge können immer noch ausfallen, aber das Problem der Späneumwicklung verschwindet.“
Die Kunden von MCC reichen von OEMs mit 300 oder 400 Maschinen bis hin zu kleineren Herstellern mit 10 Maschinen. Und diese Kunden „stellen alle unterschiedlichen Teile her“, von gewöhnlichen Knochenschrauben und Käfigen für die Wirbelsäulenchirurgie bis hin zu verschiedenen chirurgischen Werkzeugen wie Knochenreibahlen, die für Hüft- und Knieoperationen erforderlich sind. Es gibt winzige Knochenschrauben von etwa 4 mm Durchmesser mit Löchern für Nähte. „Neun verschiedene Werkzeuge kommen zum Einsatz, um die verschiedenen Formen zu schneiden“, sagte Such. „Diese kleine Knochenschraube hat viele Funktionen – sie ist nicht nur eine Schraube mit Kopf.“
Nachdem diese winzigen Teile hergestellt sind, wird das Sortieren zum Hauptproblem, fuhr Such fort. MCC stellt Automatisierungsgeräte her, die auf die Aufgabe zugeschnitten sind.
„Diese Teile sind so klein, dass, wenn sie in den Eimer fallen, dort 300 sein könnten. Wenn Sie versuchen, den letzten auszuwählen, um zu versuchen, ihn zu messen, welcher war das? Wir können ein Gerät haben, das verschiedene Fächer zum Zählen hat“, sagte Such.
Der Kunde kann 100 Teile in ein Tablett legen, dann, wenn sich das Tablett bewegt, eines in das nächste Tablett legen, 100 in das nächste Tablett, eines in das nächste Tablett und so weiter. Wenn es 10 Schalen gibt, kann es acht Stunden lang oder über Nacht unbeaufsichtigt laufen. Durch das Messen von Teilen in Intervallen können Kunden dank der Auffangwannen feststellen, ob vorherige Teile gut oder schlecht sind.
Der Sechs-Achsen-Vorteil
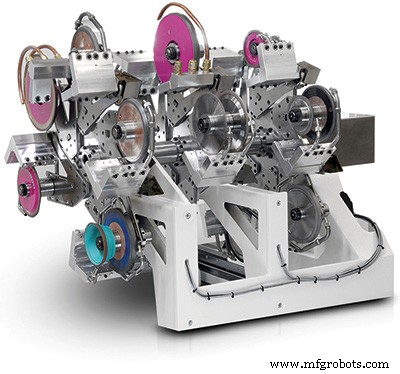
Die stetige Nachfrage nach den Schneidwerkzeug-Schleifmaschinen von Rollomatic USA Inc., Mundelein, Illinois, ist ein klarer Indikator für die Widerstandsfähigkeit der Medizingeräteherstellung, versichert Präsident Eric Schwarzenbach.
Unter den vielen Instrumenten, die Rollomatic-Maschinen von OEMs und Vertragsherstellern zur Herstellung anfordern, befinden sich verschiedene orthopädische Schneidwerkzeuge wie Raspeln, Knochenbohrer, Schädelperforatoren und arthroskopische Bohrer. Während der gesamten Pandemie haben „unsere Kunden wie zuvor investiert – nicht mehr und nicht weniger“, trotz der Verschiebung orthopädischer oder elektiver Operationen. „Es gab genug Geschäfte, um diese Unternehmen am Laufen zu halten und ihren Bedarf an Reinvestitionen aufrechtzuerhalten.“
In den letzten Jahren sei die Nachfrage nach verschiedenen Instrumenten für Roboteroperationen gestiegen. Aber diese Geräte stellen eine besondere Herausforderung dar.
„Ein Bohrer, den ein Chirurg mit einem Handstück zum Bohren in Knochen verwendet, unterscheidet sich von dem, was ein Roboter ausgibt“, erklärte er. „Roboter verwenden längere Bohrer als Chirurgen. Die Herstellung eines langen Bohrers ist naturgemäß schwieriger als bei einem kürzeren Bohrer. Zunächst werden chirurgische Werkzeugrohlinge auf einer Langdrehmaschine im weichen Zustand bearbeitet und anschließend gehärtet. Diese Prozesse verursachen inhärent ein Verziehen in diesen Rohlingen, und je länger sie sind, desto gebogener sind sie. Und wenn sie verbogen sind, haben wir Probleme, zuverlässig zu laden, zu schleifen und zu entladen. Wenn wir unseren Kunden unsere Maschine und Einrichtung beibringen, müssen wir sehr darauf achten, sie ausführlich zu unterrichten und sicherzustellen, dass sie die Funktionen verstehen, um einen gebogenen Rohling zu umgehen. Gebogene Rohlinge werden vom Hersteller oft gerichtet, aber auch dann sind sie nie perfekt – obwohl sie nicht perfekt sein müssen. Die Maschine ist in der Lage, eine kleine Verzerrung zu bewältigen.“
Je roboterhafter die Industrie wird, „desto mehr muss man sich auf den Bohrpunkt konzentrieren. Während ein Chirurg immer in Knochen bohren kann, weil er sehen, sehen, seine Hand und seinen Druck anpassen kann, damit der Punkt nicht weggeht, tut der Roboter dies nicht. Diese Punkte müssen also so gestaltet werden, dass sie selbstzentrierender sind. Wir helfen Medizingeräteherstellern, ihnen beizubringen, wie ein selbstzentrierender Punkt aussieht.“
Schwarzenbach bemerkte auch mehr Varianten in 17-4 Edelstahl für orthopädische Schneider. „Das Material ist weicher und weniger verhärtet geworden, was für uns eine Herausforderung ist, die richtigen Schleifscheiben zu finden, um sie zu schleifen. Je weicher das Material, desto schwieriger ist es bekanntlich zu schleifen.“ Um diesem Bedarf gerecht zu werden, hat sich Rollomatic mit Radherstellern in der Schweiz und den USA zusammengetan, um Räder zu beschaffen, die für weichere Materialien geeignet sind.
„Je weicher das Material ist, desto mehr Grat wirft es ab“, erklärt Schwarzenbach, „also ist die Gratentfernung ein Problem. Unsere Kunden verwenden im Allgemeinen Nylonbürsten, um Grate nach dem Schleifen zu entfernen, insbesondere bei weicheren Materialien. Aber kein Rad oder Prozess ist jemals perfekt; Es wird immer einen kleinen losen Grat geben, der mit irgendeiner Methode entfernt werden muss. Wir verwenden entweder Nylon- oder manchmal imprägnierte Bürsten mit Keramik oder Schleifmitteln darauf, um diese Grate zu entfernen.“
Schnellkupplungsgriffe für medizinische Instrumente seien ein weiterer Wachstumsbereich, fuhr er fort. Diese Werkzeuge können von einem Chirurgen in ein Handstück eingeklickt oder an einem Roboterarm befestigt werden. Solche Griffe „sind viel komplexer geworden, als wir es je gesehen haben. Für die meisten verwenden wir eine Schälmühle.“
Die Sechs-Achsen-Fähigkeit von Rollomatic ist der Wendepunkt für medizinische Hersteller, die mehr Flexibilität bei der Programmierung und eine einfachere Radeinrichtung benötigen, sagte Schwarzenbach.
„Sie müssen keine komplexen Räder verwenden; Sie können einfacher geformte Räder verwenden, insbesondere an den Bohrspitzen“, sagte er. „Man kann eine Bohrspitze einfacher herstellen als auf einer Fünf-Achs-Maschine. Und vergessen Sie nicht:Die Bohrpunkte sinken jetzt auf einschließlich 50 bis 60 Grad. Sie sind sehr steil, im Gegensatz zu einem Hartmetallbohrer in Metall mit 120 oder 130 Grad. Unsere sechsachsigen Maschinen helfen wirklich dabei, diese Bohrspitzen viel einfacher zu schleifen, als sich mit dem Einrichten einer fünfachsigen Maschine herumschlagen zu müssen.“
Und der Schnellradwechsler von Rollomatic biete noch mehr Vorteile, fügte er hinzu. „Wir haben viel mehr Radwechsler verkauft. Der Basis-Radwechsler hat sechs Stationen, sodass Sie sechs Radpakete einsetzen können, um die Flexibilität zu erhöhen, was für kürzere Chargen dient. Kürzere Chargen erfordern mehr Flexibilität durch häufiges Umrüsten. Radwechsler sind dafür sehr gut geeignet.“ Während etwa 80 Prozent der Maschinen, die Rollomatic an die medizinische Industrie verkauft, die Standardspindeln beibehalten, die vorne und hinten ein Paar Räder aufnehmen, „fangen einige Hersteller an, unsere neue Technologie anzunehmen“.
Die Rolle von Force-Tests
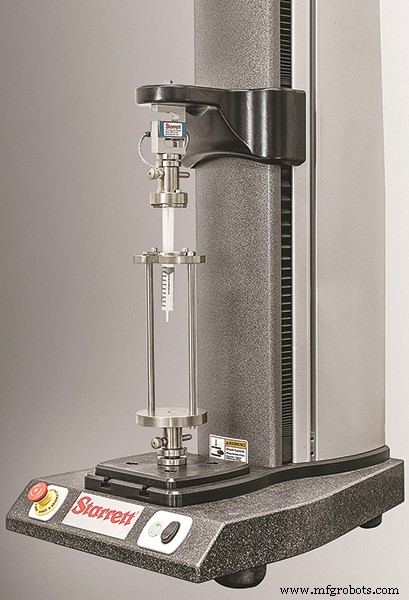
Von der Vorbereitung für die Fertigung bis nach der Herstellung des Teils erfüllen Kraftprüfgeräte und ihre integrierte Software wichtige Funktionen für Medizinprodukte – oft mit dem Ziel des Patientenkomforts.
Beispielsweise können die Konturen und die Beschichtung einer Nadel darauf getestet werden, wie leicht sie in die Haut eindringen, während Klebstoffe daraufhin bewertet werden können, wie gut sie auf der Haut haften oder wie leicht sie entfernt werden können.
Vor der Fertigung „können Sie Tests durchführen, um sicherzustellen, dass Ihre Ausrüstung so funktioniert, wie sie sollte, bevor Sie sie in der Fertigung einsetzen“, erklärt Jacob Morales, technischer Support-Ingenieur bei The L.S. Starrett Co., Athol, Massachusetts. Und bei Bandagen „können Sie den Klebstoff testen, bevor Sie ihn in Ihrer Fertigungslinie verwenden“, in Chargen, die beispielsweise von einer von 100 bis zu einer von 10.000 Proben reichen. „Nach der Verarbeitung können Sie diese Tests erneut ausführen, um die Konsistenz sicherzustellen.“
Solche Tests sind besonders wichtig bei der Fertigung gemäß ASTM- und ISO-Normen sowie für die Erstellung von Dokumentationen, die für die Rückverfolgbarkeit entscheidend sind, fügte Eric Perkins, Technologiemanager für Kraft- und Materialprüfungen bei Starrett, hinzu. Die Starrett-Software ermöglicht sowohl Kraft- als auch Materialeigenschaftentests, und durch einfaches Klicken auf das richtige Symbol kann die Software den entsprechenden Test starten. Die Kraftmessung deckt Go/No-Go-Szenarien ab, darunter Tests für Spitzenlast, Durchschnittslast, Kompressionstests und mehr. Spritzen, ein Paradebeispiel, das eine einachsige Kraftanwendung erfordert, können mit Probensubstanzen getestet werden, um die Injektionskraft für kontrollierte Injektionsraten zu bestimmen.
Während diese Tests Probeninformationen liefern, liefern sie nicht immer Daten, die spezifisch für das Material sind, aus dem die Probe besteht. Die Materialprüfung geht noch weiter und verwendet Materialeigenschaften, um beispielsweise Dehnung und Spannungs-Dehnung zu testen.
Starrett-Software kann in den Herstellungsprozess integriert werden, erklärte Morales.
„Wenn Sie ein Kraftsystem haben, das eine Probe testet, können Sie es mit einem Input-Output-System programmieren, sodass der Test ständig läuft. Die Fertigungsanlage bewegt eine Probe zur Maschine und sendet ein Signal; Die Maschine antwortet, indem sie den Test durchführt und eine Signalausgabe basierend auf den Testergebnissen bereitstellt. Der Rest Ihrer Produktionsanlagen kann entsprechend reagieren. Wenn Sie ein Ergebnis erhalten, das außerhalb der Toleranz liegt, kann das Signal einen Bediener warnen.“
Diese Flexibilität bedeutet, dass „Sie das Force-System an eine SPS anschließen und es in die Produktionsumgebung einbinden können, sodass Sie potenzielle Fehler bei der menschlichen Dateneingabe ausschließen können“, sagte Perkins. „Benutzer können ein Produkt jedes Mal automatisch testen lassen, wenn es in die Warteschlange gestellt wird.“
Von der grundlegenden L1-Force-Software von Starrett bis hin zu den fortschrittlicheren L2-, L2Plus- und L3-Optionen „geben wir unseren Kunden die Möglichkeit, genau so zu testen, wie es jeder Fertigungsstandard vorschreibt“, sagte Perkins. Und da die Starrett-Software plattformübergreifend kompatibel ist, entsteht durch das Hinzufügen optischer und optischer Systeme eine extrem breite Messlösung.
Dieses Maß an Anpassung hört jedoch nicht bei der Software auf. Starrett hat mit Herstellern zusammengearbeitet, um vollständig automatisierte Systeme zu entwickeln.
„Wir verwenden Roboter, um Teile in unser Kraftprüfsystem einzulegen“, sagte Perkins. „Wir verwenden pneumatische Greifer, um die Teile zu greifen.“ Mit einer ständig laufenden Testplattform, die mit diesem Automatisierungsgrad verbunden ist, „sagt unser System, ob Sie ein gutes oder schlechtes Teil haben, dann führt der Roboter das erforderliche Programm aus und legt diese Teile in den dafür vorgesehenen Behälter.“
Großbildansicht von GE
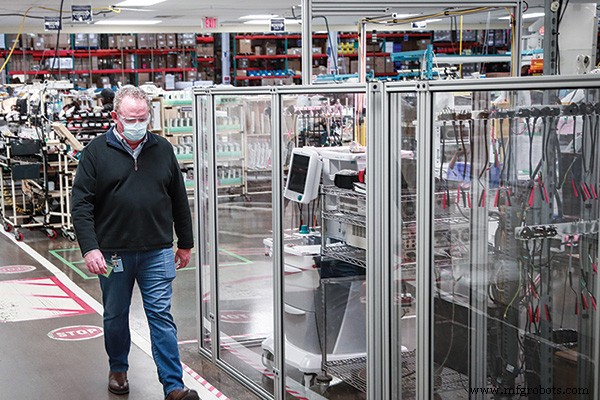
Die Verbesserung der Krankenhausabläufe und die Aufrechterhaltung der Ausfallsicherheit der Lieferkette standen für GE Healthcare während der Pandemie an erster Stelle.
„Wir sehen zunehmende Anfragen nach mehr Automatisierung – nicht nur aus typischer Produktivitätssicht, sondern auch in Bezug auf die Nutzung der Automatisierung, damit wir die Produktion an verschiedenen Standorten aufrechterhalten können“, sagte Jimmie Beacham, Executive Chief Engineer for Advanced Manufacturing bei GE Healthcare in Milwaukee. „Das ist einfacher, als eine neue oder wechselnde Belegschaft einarbeiten zu müssen. Es geht nicht unbedingt um die Arbeit, sondern um die Sicherheit der Lieferkette, bei der Automatisierung sinnvoll ist. Wenn ich die Produktion von einer Region in eine andere verlagern muss, ist es viel einfacher, wenn der Prozess bereits automatisiert ist.“
Ein wichtiger Teil dieser Philosophie sei die Fehlersicherheit, fügte er hinzu. „Wir würden Bediener schulen und schriftliche Verfahren haben“, erklärte Beacham. „Jetzt prüfen wir den Einsatz anderer Technologien, die digitalisieren, was die Bediener tun müssen, und die mit ihnen interagieren. Angenommen, Sie haben eine Drehmomentstation, an der Sie Schrauben festziehen, gefolgt von einer komplexen Montage und dann einem Cobot. Wir suchen nach Technologien, die all das digital verbinden – die im Gleichschritt mit dem Bediener arbeiten, sodass sie mit dieser Person interagieren und der Bediener sich nicht an alles erinnern muss. Das gibt uns viel Flexibilität, wenn wir dasselbe Produkt in drei Regionen auf der ganzen Welt herstellen. Wir haben jetzt einen Steuerungsprozess. Wir verlassen uns nicht darauf, dass sich die Bediener Papierverfahren merken, wenn sie mehrere komplexe Teile des Vorgangs durchlaufen müssen.“
Das ist von entscheidender Bedeutung für GE Healthcare, das eine Reihe intelligenter Diagnosegeräte herstellt. Die additive Fertigung spielt dabei eine große Rolle, und auch GE Healthcare hat seine Prozesse in dieser Hinsicht verfeinert.
„Als wir anfingen, investierten wir wahrscheinlich 80 bis 90 Prozent unserer Zeit in Forschung und Entwicklung, um herauszufinden, wie Additive funktionieren, wie man Materialien und Parameter entwickelt, um unsere technischen Anforderungen zu erfüllen“, sagte er. „Jetzt sind wir zu etwa 80 Prozent in der Ausführung, wo wir die Dinge in die Produktion bringen, und die anderen 20 Prozent unserer Zeit widmen wir der Entwicklung neuer Materialien für die neuen Trichter, die hereinkommen. Wir haben eine Produktionsstätte in Monterrey, Mexiko, und wir haben einen ziemlich aktiven Trichter von Dingen, die dort vor sich gehen. Dann haben wir einige andere Additivanwendungen, die wir am Point of Use ausführen.“
Obwohl sich die Pandemie als herausfordernd erwiesen hat, hat GE Healthcare den Sturm überstanden.
„Unsere große Herausforderung war die Versorgung, die Menschen sicher in die Anlage zu bringen“, sagte Beacham. „In einigen Fällen, wie bei Beatmungsgeräten, haben wir uns stark auf die Automatisierung verlassen, um eine beispiellose Nachfrage zu erfüllen. Wir haben viele Leute für die Arbeit hinzugezogen, aber wir mussten immer noch kreative Wege finden, um die Menge an Produkten herzustellen, die unsere Kunden dringend benötigten. Und wir haben gelernt, dass wir Dinge anders herstellen können; das hat noch mehr Ideen inspiriert.“
Automatisierungssteuerung System
- Bewertung der Auswirkungen von Industrie 4.0 auf die Fertigung
- 8 prominente Mythen der Metallherstellung entlarvt
- Technologien für eine effektivere Herstellung medizinischer Komponenten, gesehen auf der MD&M West 2018
- 6 Möglichkeiten, wie das IIoT die Fertigung effizienter macht
- Stratasys:Nachhaltiger sein mit 3D-Druck
- BERICHT:2016 wird ein "Wendepunkt" für die Fertigungstechnologie
- Die britische Fertigung intelligenter machen:Erwartungen für 2018
- Überbrückung der Qualifikationslücke in der Automobilherstellung
- Stora Enso:Die Zukunft der Fertigung ist jetzt intelligenter
- Aufbau einer widerstandsfähigen Lieferkette in der Fertigung