Spritzgussteil-Design Teil 4:Warp
Wir haben über verschiedene Herausforderungen und Fehler gesprochen, die bei Spritzgussteilen auftreten können, die kosmetische Mängel, innere Spannungen in diesen Teilen und Verzögerungen bei der Markteinführung verursachen können, und wie man Spritzgussteile entwickelt, um diese Probleme zu vermeiden. Ein Bereich, den wir erwähnt, aber nicht angesprochen haben, ist die Verwerfung von Spritzgussteilen nach dem Spritzzyklus. Dies wird durch die unterschiedliche Kühlung des Kunststoffs im frisch geformten Teil verursacht und kann auf unterschiedliche Materialdicken, innere Merkmale oder Wandverbindungen, Teile-Seitenverhältnisse und den Spritzgussprozess zurückzuführen sein.
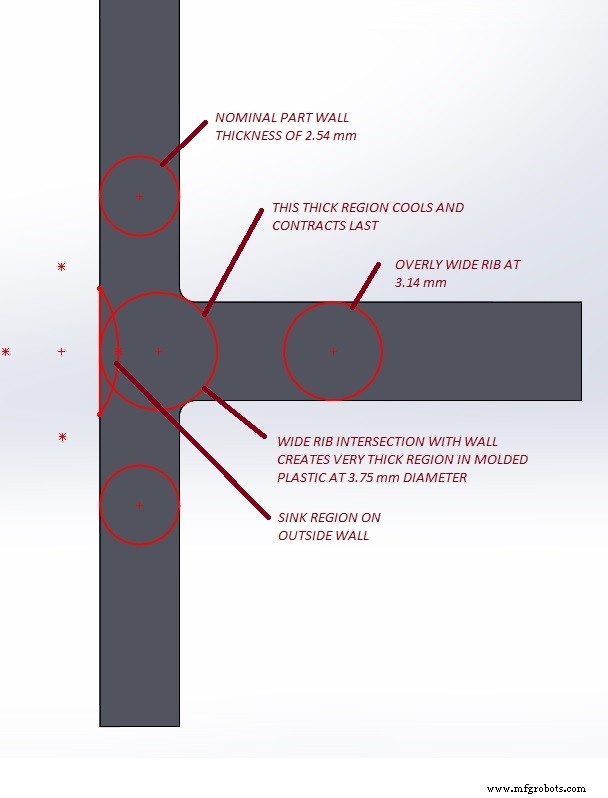
Der Verzug von Spritzguss-Kunststoffteilen ist wirklich eine eigene Herausforderung und kann eine kleine Überraschung sein. Obwohl die Formflussanalyse mithilfe von 3D-Konstruktions-CAD-Dateien helfen kann, dies vorherzusagen, gibt es mehrere Parameter, die die Verwerfung beeinflussen, nicht nur die Teilegeometrie, sodass Vorhersagen nicht genau sind. Oftmals können kleine Mengen der vorhergesagten Verwerfung schwerwiegender sein, da die inneren Spannungen im Kunststoffteil und der Kaltfluss des Kunststoffmaterials nach der Teileherstellung zu mehr Biegung führen können, die beim Zusammenbau des Produkts nicht unbemerkt bleibt. Obwohl viele Passungs-, Form- und Funktionsaspekte eines neuen Kunststoffteiledesigns während der Prototypenphase anhand von bearbeiteten oder gedruckten Teilen bestätigt werden können, wird sich hier nicht unbedingt ein Verzug manifestieren.

Aus diesen Gründen ist es wichtig, mehrere allgemeine Richtlinien zu befolgen, um relativ konstante Wandstärken von Kunststoffteilen mit allmählichen Übergängen beizubehalten, und die Empfehlungen für Rippen- und Nabengrößen zu befolgen, die wir kürzlich besprochen haben. Dies ist jedoch nicht immer ausreichend. Einige Produktdesigns können aufgrund ihrer erforderlichen Funktionen oder Stile immer noch erhebliche Herausforderungen hinsichtlich der Vermeidung von Verzug in den Spritzgussteilen aufweisen. Scharfe Ecken, sehr große flache Seiten und nicht symmetrische oder offene Teileformen können alle Probleme mit der Beibehaltung der beabsichtigten Form und Passform haben.
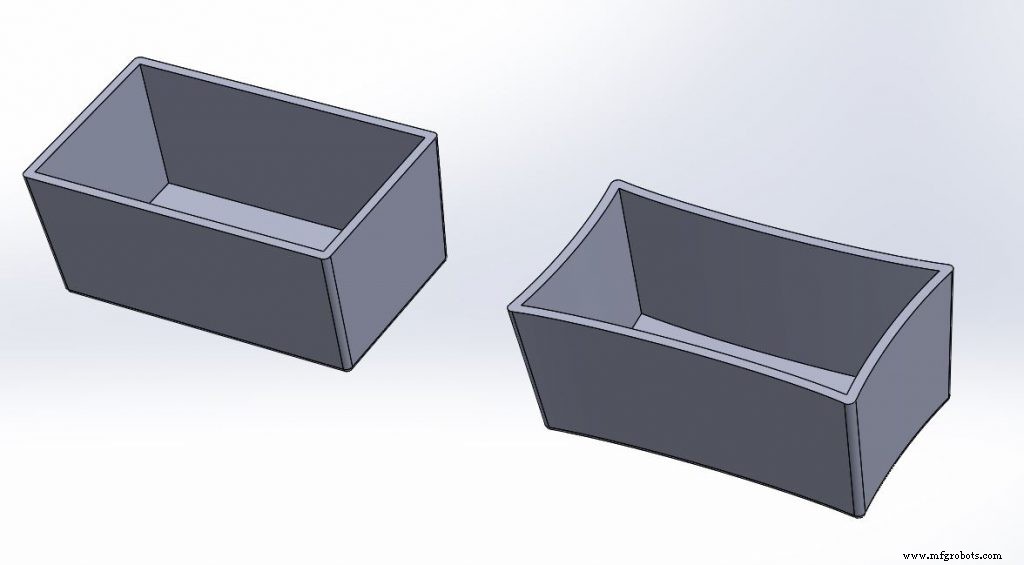
Ein klassischer Kettfehler ist ein 5-seitiges Gehäuseteil mit nach innen verformten Seitenwänden. Obwohl das Teil auf allen 5 Seiten des Gehäuses eine relativ konstante Wandstärke hat, können die Ecken dickere Abschnitte darstellen, die langsamer abkühlen und schrumpfen können und an der Innenseite der Teilwände stärker ziehen als an den Außenseiten.
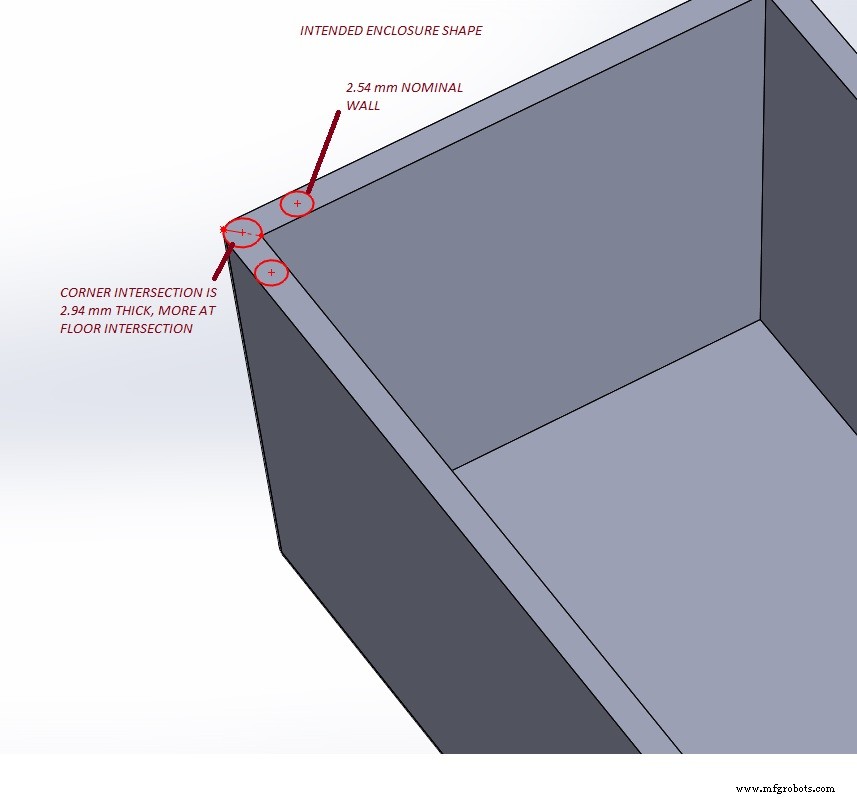
In diesen Ecken ist auf die Dicke zu achten oder Entkernungsreliefs hinzuzufügen. Eine Möglichkeit besteht darin, die Eckenradien an der Außenseite des Teils zu vergrößern und eine gemeinsame Wandstärke zu den Radien der Innenrundung beizubehalten.
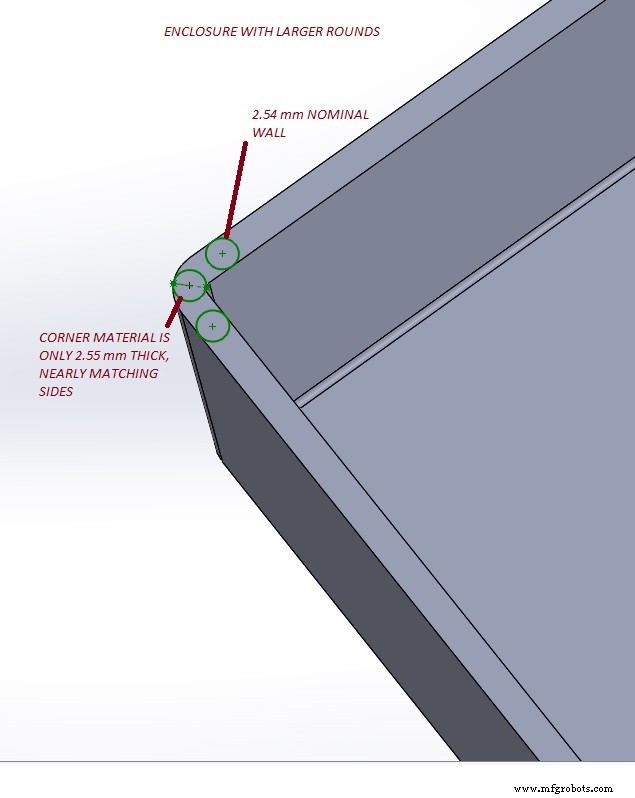
Wenn alternativ ein schärferes kantiges Aussehen an der Außenseite des Produkts erforderlich ist, können entkernte Innenecken die Dicke lokal durch die scharfen Innenecken verringern.
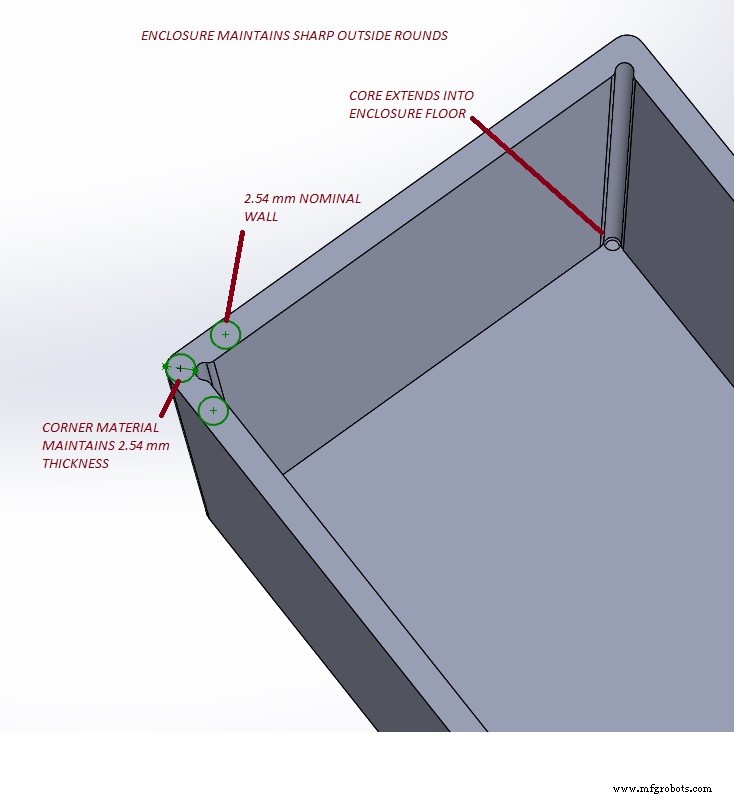
Wie bereits erwähnt, gilt dieser Kernansatz auch für den Schnittpunkt von Seitenwänden und der Bodenwand.
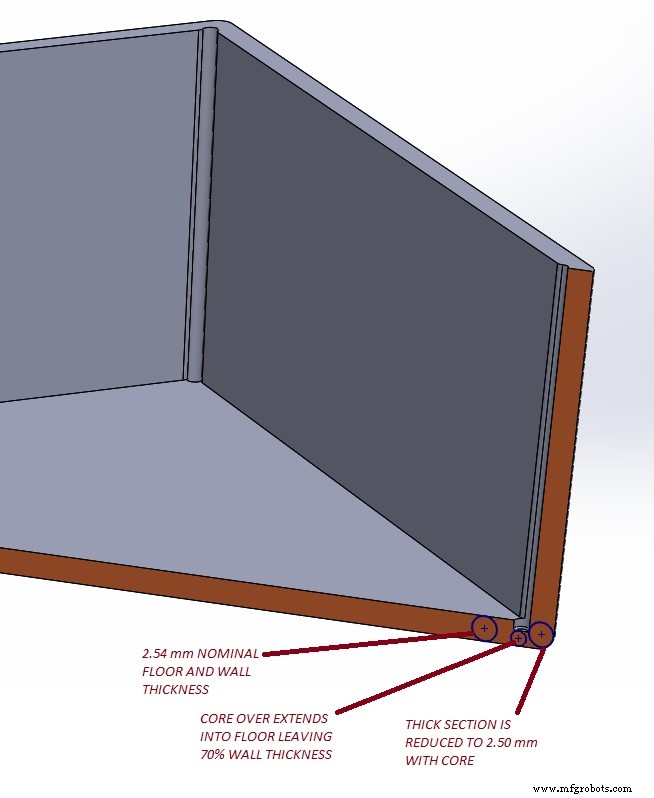
Produkte, die mit großen flachen Flächen entworfen wurden, haben ein klares, modernes Erscheinungsbild für Unternehmen, die häufig ihr Image neu gestalten und sich von Mitbewerbern abheben möchten. Aber Kunststoffteile wie diese haben ihre eigene Herausforderung, die Ebenheit auf größeren Flächen zu erhalten.
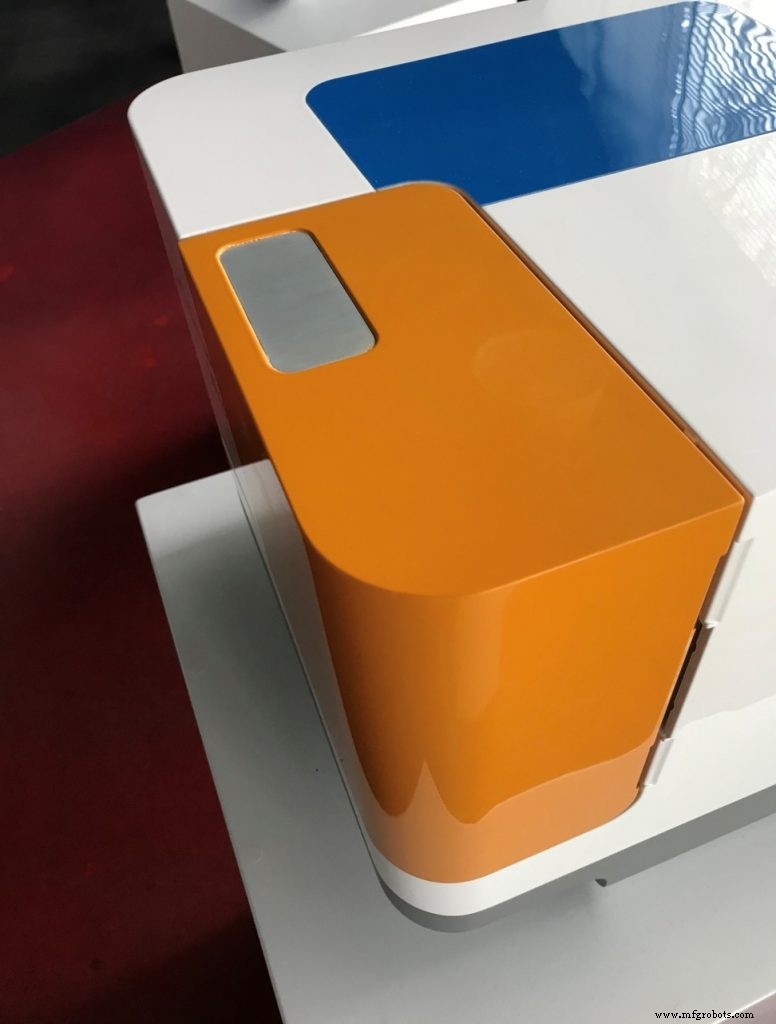
Mit einem glänzenden Finish werden alle Durchhänge, Vertiefungen oder Fehlausrichtungen hervorgehoben und sind sehr auffällig. Fischaugen von reflektiertem Licht können Oberflächen seltsam aussehen lassen. Die Teile für die Protein-Simple-Laborgeräte, gezeigtes WES-Modell, hatten nicht einmal einen Entwurf, um das gewünschte orthogonale Aussehen zu optimieren. Obwohl diese Teile aus strukturellem Schaumkunststoff geformt wurden, lindert dieses Verfahren nur einige der Bedenken hinsichtlich Senken und Verziehen. Der Schlüssel zu perfekten Teilen lag darin, sie mit minimalen abrupten Wanddickenänderungen zu konstruieren und eng mit dem Spritzgussteam zusammenzuarbeiten, um die erforderliche Ebenheit zu kommunizieren und bei der Entwicklung von Vorrichtungen nach dem Einspritzen zu helfen, um ein Verziehen während des Abkühlens zu verhindern.
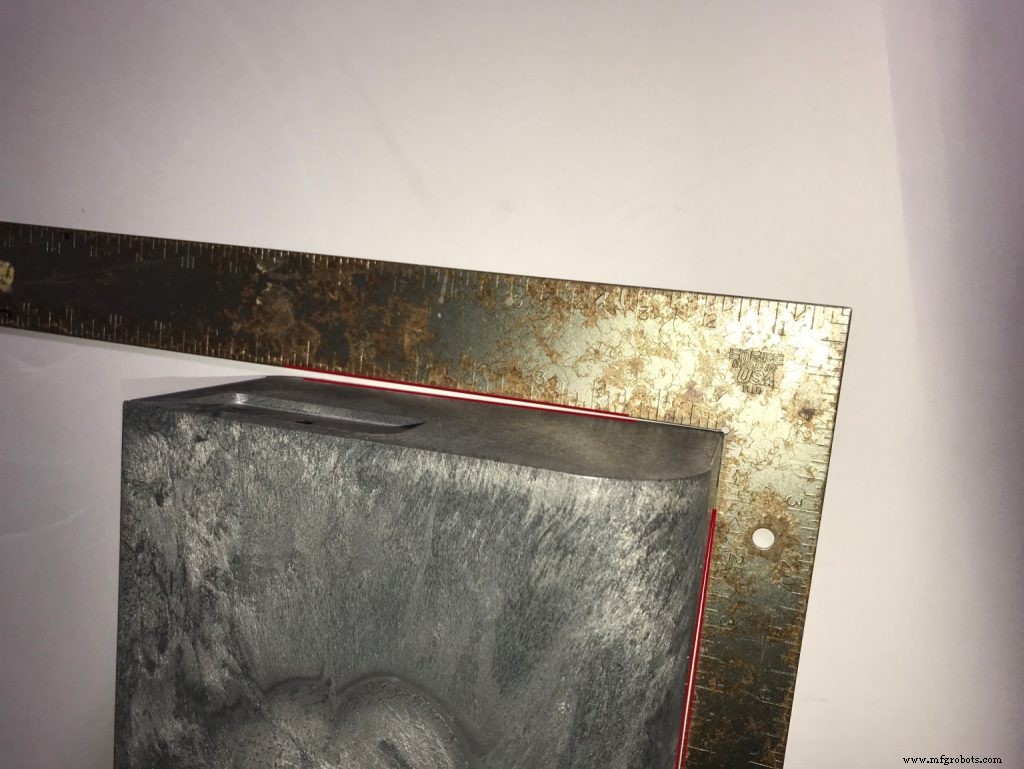
Da die Teile in geringerer Stückzahl produziert wurden, waren die Vorrichtungen eine praktikable Option, mussten jedoch so konstruiert werden, dass die gewünschten Ergebnisse erzielt werden. In vielen Fällen entwirft ein Spritzgießer seine eigenen Vorrichtungen, um die Toleranzen einzuhalten und Beschriftungen in den technischen Zeichnungen zu bilden. Diese Vorrichtungen wurden gemeinsam vom Produktdesignteam von StudioRed und dem Formenbau entwickelt.
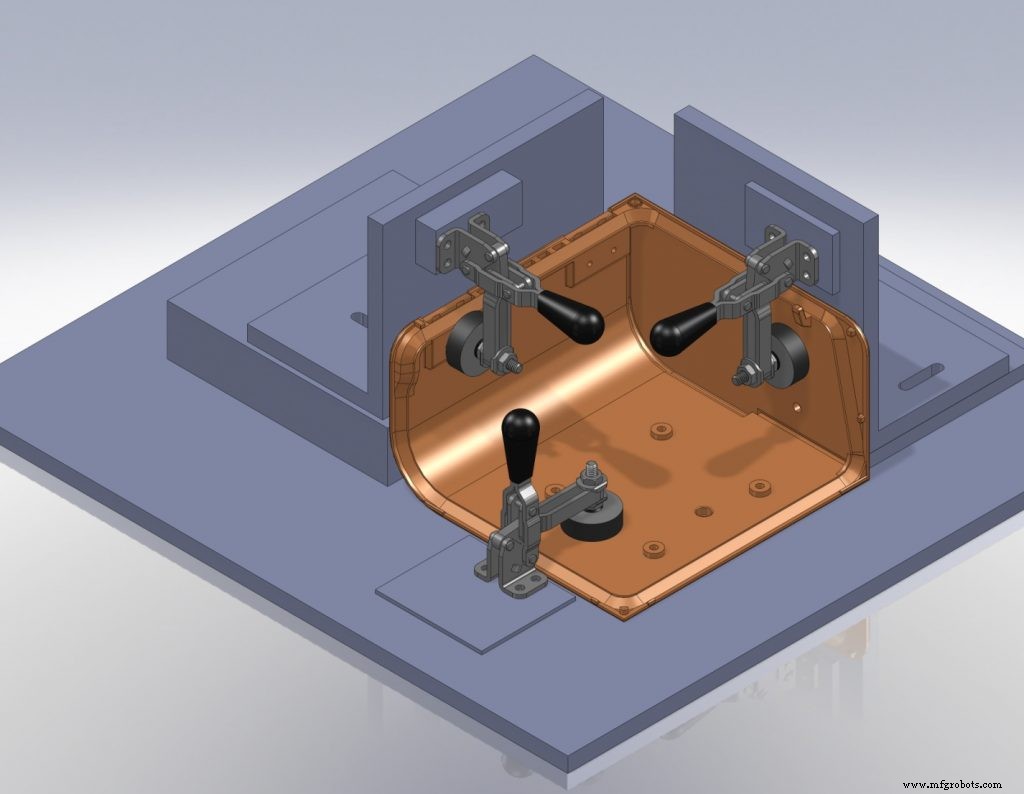
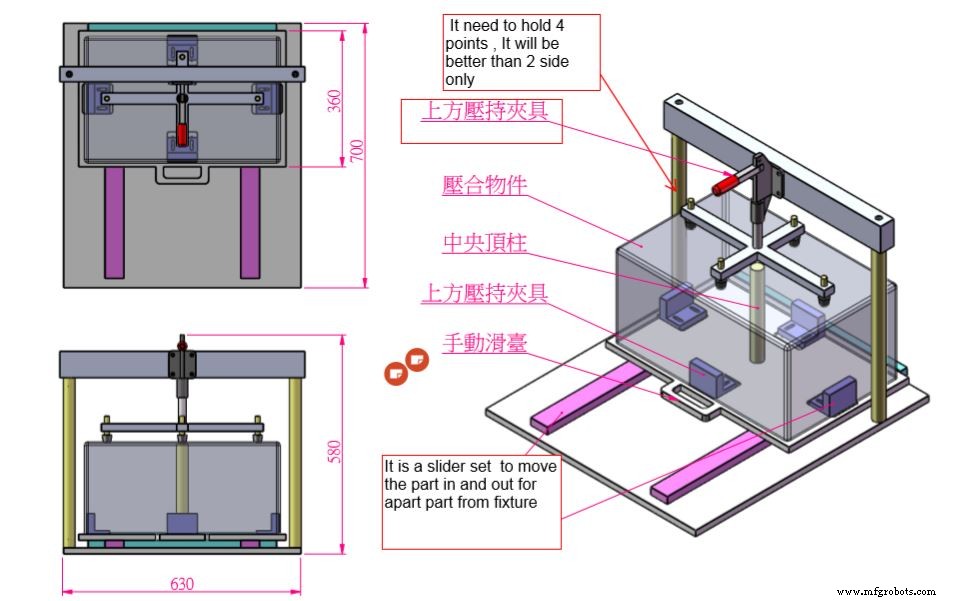
Der zusätzliche Aufwand im Engineering und die Verwendung von Vorrichtungen führten zu den gewünschten Ergebnissen für das neue Produktdesign von Protein Simple und zu geringeren Kosten als bei der zusätzlichen manuellen Nachbearbeitung verzogener Teile. Der neue Look wurde nicht nur mit einem Designpreis ausgezeichnet, sondern brachte die beabsichtigte Markenbotschaft auf den Markt, und der Umsatz reagierte mit einer 6-fachen Steigerung im ersten Monat.
Wir haben uns gerade die Herausforderungen des Kunststoffspritzgießens angesehen, bei denen Ebenheit und Ausrichtung entscheidend sind und wie dicke Abschnitte die beabsichtigte Form verzerren können. Es gibt auch Situationen, in denen ein spritzgegossenes Kunststoffteil so konstruiert sein kann, dass es große Öffnungen oder fehlende Bereiche aufweist, die durch Montage, Teilezerfall oder andere funktionale Anforderungen wie Belüftung verursacht werden. Diese asymmetrischen Formen und dünnen Kunststoffspannweiten können zu Verwerfungen führen. Dies ist häufig die Herausforderung bei Blendendesigns für Rack-Server, Switches und Speicherprodukte.
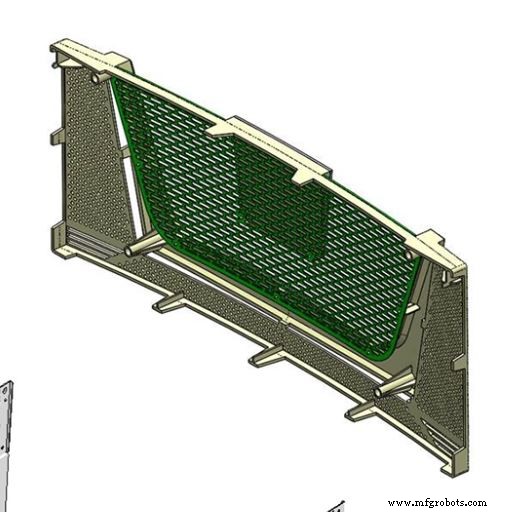
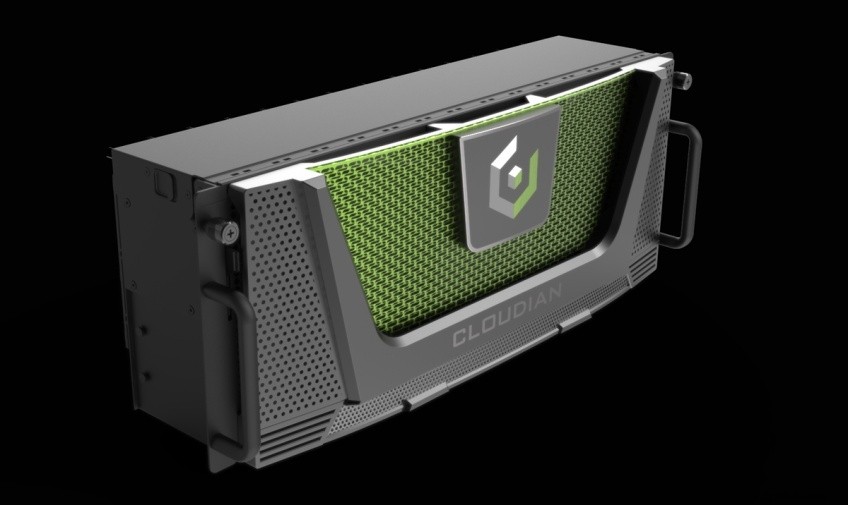
Die Blende kann der Schlüssel zum Branding des Rack-montierten Produkts sein und es über ein allgemeines Metallgehäuse heben. Sowie für einige Sicherheit sorgen und Hardwareplattformen von OEM-Anbietern darunter verbergen.
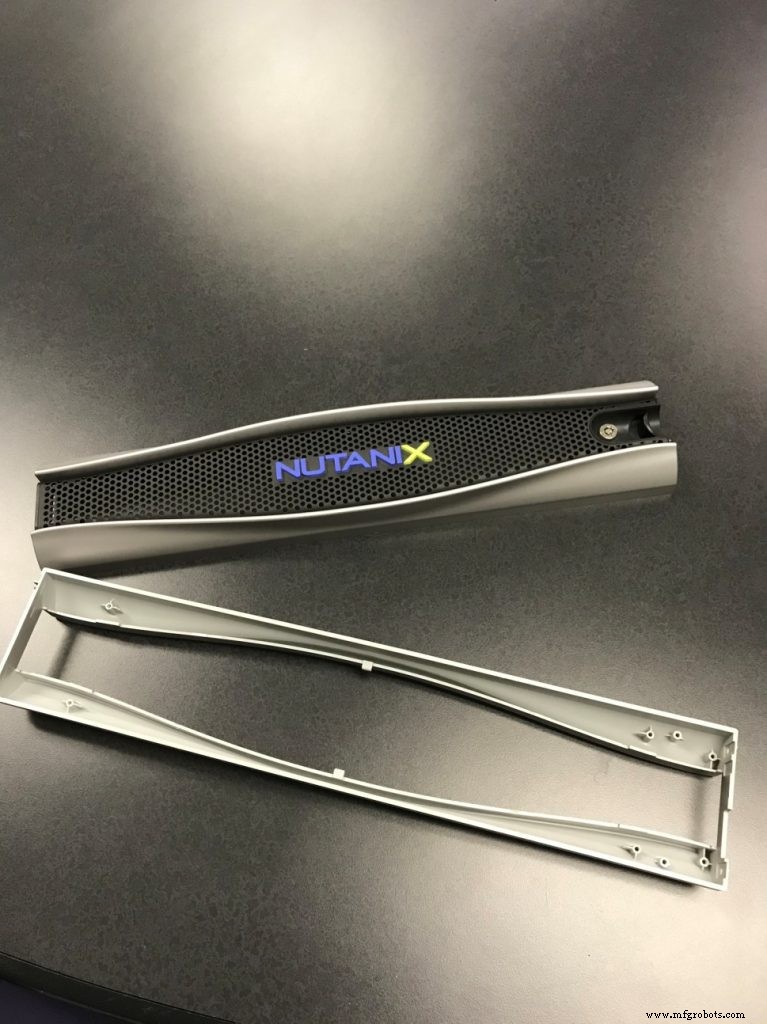
Wenn der spritzgegossene Teil der Blende zu spindeldürr wird oder sehr große Öffnungen überbrücken muss, um den offenen Belüftungsbereich, den Zugang und andere Anpassungsanforderungen des Teils zu erfüllen, dann kann sich das Teil leicht über die Überbrückungsabschnitte hinweg verziehen.
Das Verziehen des Teils zeigt sich möglicherweise erst dann, wenn die Kunststoffteile des zweiten Artikels geschossen werden, während der Formprozess weiter eingestellt wird. Aber Anpassungsprobleme am Chassis des Computerprodukts können Durchhänge und Biegungen sehr sichtbar telegrafieren.
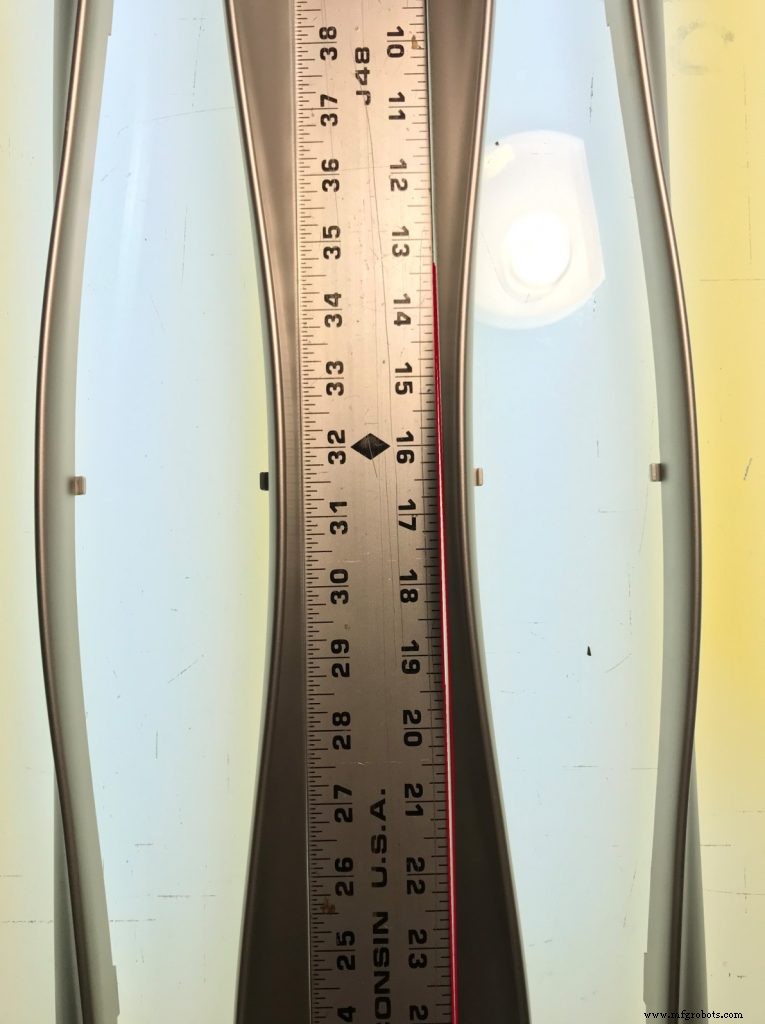
Oft kann man sich nicht auf zusätzliche strukturelle Unterstützung durch andere Teile, wie Metallperforationssiebe, verlassen, da sie entfernbar sein können oder aufgrund von Material- und Kostenvorgaben nicht sehr genau geformt werden können.
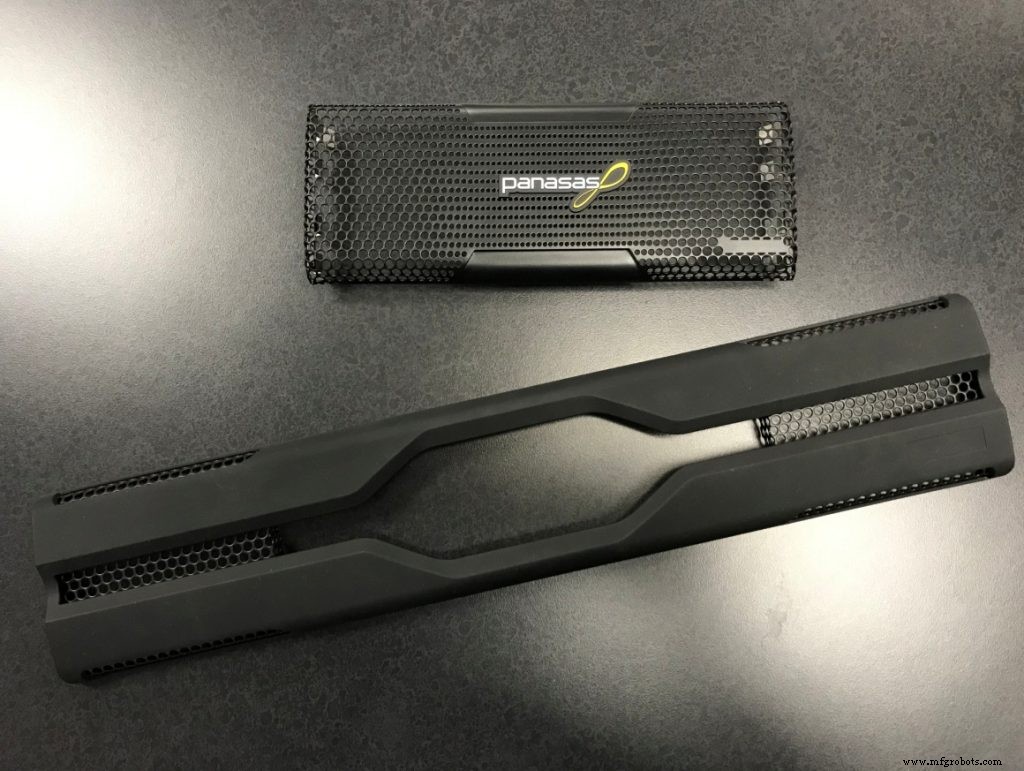
Diese Herausforderungen bei spritzgegossenen Blendenteilen mit großen offenen Bereichen durch die Teile oder exzentrischen Querschnitten wurden durch genaue Überprüfung der Materialstärken und Übergänge im gesamten Teil, enge Zusammenarbeit mit dem Spritzgussteam, Anpassung von Prozess- und Abkühlzeiten sowie durch Hinzufügen von Nacheinspritzungen gelöst Vorrichtungen, um die Kunststoffteile nach dem Formen in den extremeren Fällen in Form zu halten.
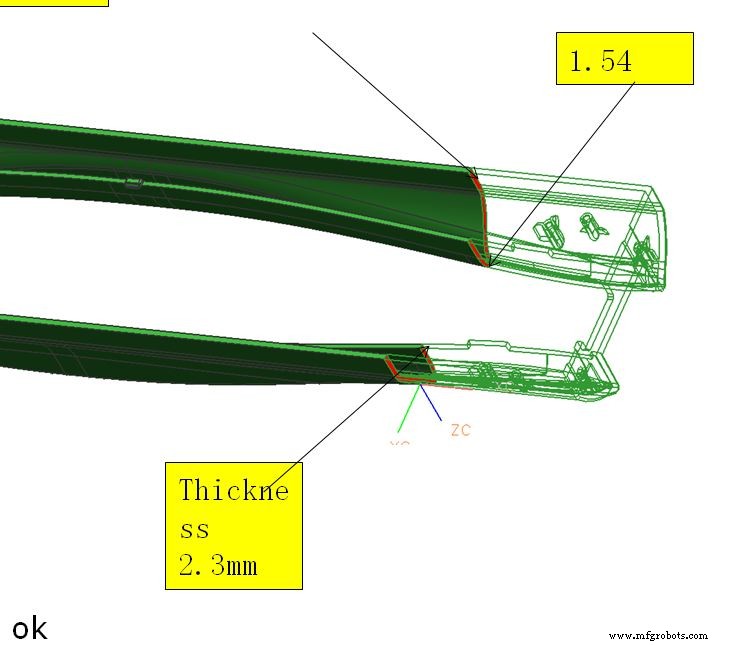
Das Ergebnis waren hochwertige Komponenten, die gut zu verschiedenen Chassis passen und Markendefinitionen für Unternehmen lieferten, die sich differenzieren wollten.
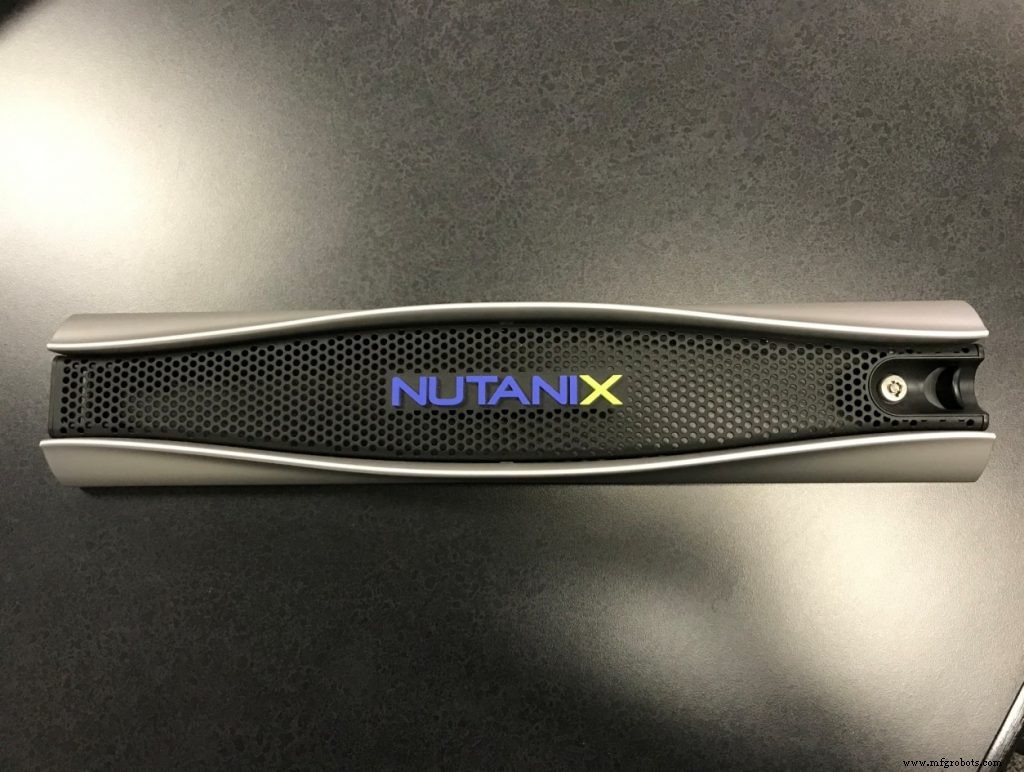
Obwohl die Verwerfung für einige Teilekonstruktionen eine Herausforderung sein kann, sogar eine Überraschung bei den ersten Spritzgussformen, können die Befolgung grundlegender Konstruktionsrichtlinien zu Teiledicken und die Zusammenarbeit mit dem Spritzgussteam Probleme schnell lösen, um hochwertige Produktkonstruktionen zu erzielen, die wie beabsichtigt aussehen und funktionieren erforderlich.
Mehr sehen wie folgt:Hinterschneidungen, Einfallstellen, Bosse
Herstellungsprozess
- Spritzgussteil-Design Teil 6:Teams und Auftragsfertiger leiten
- Spritzgussteil-Design Teil 5:Entwurf
- Spritzgussteil-Design Teil 3:Bosse
- Spritzgussteil-Design Teil 2:Einfallstellen
- 6 wichtige Designüberlegungen für den 3D-Metalldruck
- So entwerfen Sie ein Duroplast-Verbundteil [Infografik]
- Design for Manufacturability-Richtlinien – Teil 2
- Design for Manufacturability-Richtlinien – Teil 1
- Was ist die beste SPI-Oberflächengüte für Ihr Spritzgussteil?
- Designtipps für Spritzguss