Kernherstellung in der Gießerei
Kerne unterstützen die Komplexität im Sandguss
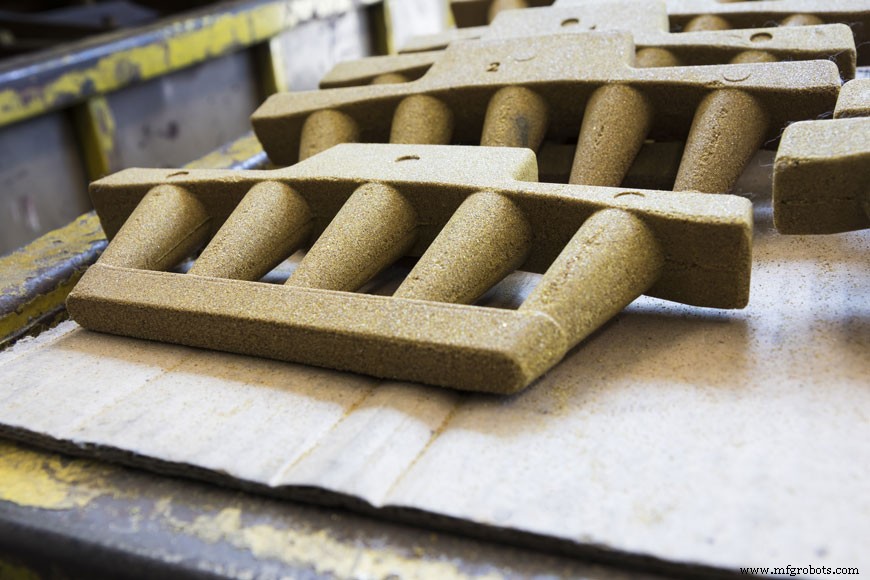
Was ist ein Kern beim Metallguss?
Ein Kern ist ein Sand- oder Metalleinsatz, der verwendet wird, um einen beliebigen Teil eines Gussstücks zu formen, der nicht durch das primäre entfernbare Modell geformt werden kann. Wenn ein Muster in Sand gepresst und dann herausgezogen wird, hinterlässt es einen konkaven Eindruck. Flüssiges Metall füllt diesen Hohlraum und kühlt ab. Kerne werden erstellt, um mehr Komplexität im Design zu ermöglichen. Gut konstruierte Kerne erzeugen Löcher oder Kammern in einem Gussteil. Formen für Automotoren können bis zu fünf Kerne enthalten, um die für den Betrieb eines Verbrennungsmotors notwendigen Kammern zu schaffen.
Kerne können auch dabei helfen, Winkel zu erzeugen, die mit einem Muster unmöglich wären. Jeder Überhang über einem leeren Raum würde es unmöglich machen, das Muster zurückzuziehen, ohne den Überhang zu brechen. In diesen Fällen kann ein Kern verwendet werden.
Gussteile mit inneren Kernen haben normalerweise eine Öffnung in der Außenhülle des Formteils, um den Kern nach dem Gießen herauszuziehen, obwohl diese Öffnung während der Endbearbeitung mechanisch verstopft werden kann.
Kerne aus Sand sind so konzipiert, dass sie zerfallen; Innenkerne werden am Ende des Prozesses buchstäblich aus dem Guss herausgeschüttelt. Hilfreich für die Platzierung des Kerns ist auch die „shakeout“-Öffnung. Jede Stelle, an der der Kern die Form berührt, ist eine Stelle, an der geschmolzenes Metall nicht fließen kann. Um eine gleichmäßige Metalldicke zu erhalten, muss ein Kern den zu füllenden Raum „überbrücken“, ohne irgendwelche Seiten zu berühren. Um dies zu erreichen, ist der Kern normalerweise länger als das Gussteil und wird durch Aussparungen im Sand außerhalb des Gussmusters an Ort und Stelle gehalten.
Chaplets für Kernunterstützung
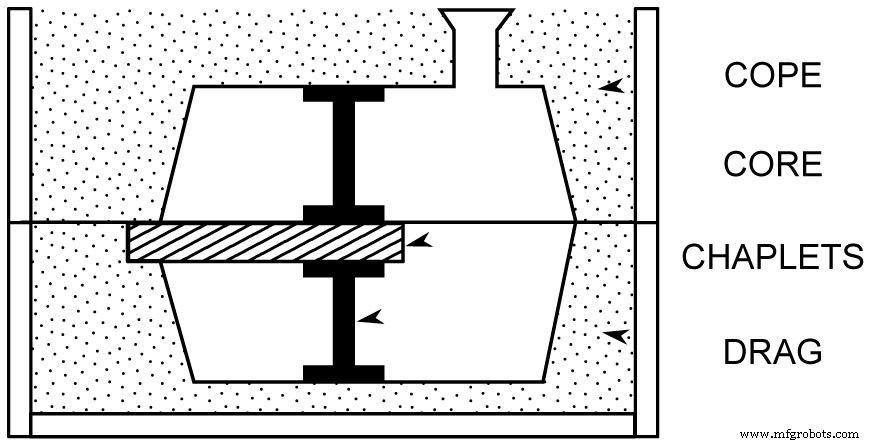
Wenn der Kern sehr lang ist oder nur eine Kante aus der Form herausragen kann, dann Kränze werden verwendet, um den Kern an Ort und Stelle zu verankern. Kränze bestehen oft aus demselben Metall wie der Guss, da ein Teil des Kranzmetalls in den Guss selbst eingearbeitet wird. Um sich sicher mit dem Rest des Gussstücks zu verbinden, muss die Oberfläche des Kranzes schmelzen – aber zuerst muss sie die Aufgabe übernehmen, den Kern zu stützen. Das Design von Kränzen ist daher ein kniffliger metallurgischer Prozess, der nach Möglichkeit vermieden wird, da bei der Verwendung von Kränzen immer die Möglichkeit besteht, Schwächen oder Gussfehler einzuführen.
Allerdings sind Kränze manchmal die einzige Möglichkeit, bestimmte Strukturen innerhalb eines Gussteils zu erzeugen. Sandkerne neigen dazu, auf dem flüssigen Metall zu schwimmen, und steigen manchmal so hoch, dass sie brechen. Oben und unten platzierte Kränze können helfen, den Kern in der richtigen Position zu halten. Der obere Kranz muss stärker sein, um dem Druck von Metall und Gas entgegenzuwirken, der in der Form nach oben drückt.
Mit Kraft Sand erzeugen
Die Tendenz des Kerns zum Aufschwimmen ist ein Grund dafür, dass ein genaues Verständnis der mechanischen Festigkeit des Kernsands wichtig ist. Tests der Scher- und Zugfestigkeit werden an Kernsanden durchgeführt und ähneln den Tests, die in unserem Artikel zu Gießereisand untersucht wurden. Wenn die Scherfestigkeit des Sandes geringer ist als der Druck, der durch das flüssige Metall erzeugt wird, das die Form füllt, kann der Kern brechen und eine Verformung des Gusskörpers verursachen.
Bindemittel sind ein großer Teil des Kernsandherstellungsprozesses. Grüne Sandkerne werden aus handelsüblichen feuchten Formsandmischungen und einem Bindemittel wie Dextrin hergestellt. Kerne dieses Typs sind sehr zerbrechlich und können mit einem Dorn oder Innendrähten hergestellt werden, um die Handhabung zu erleichtern. Trockene Sandkerne enthalten kein Wasser. Sie bestehen aus Quarzsand und einem Bindemittel zur Härtung der Oberfläche.
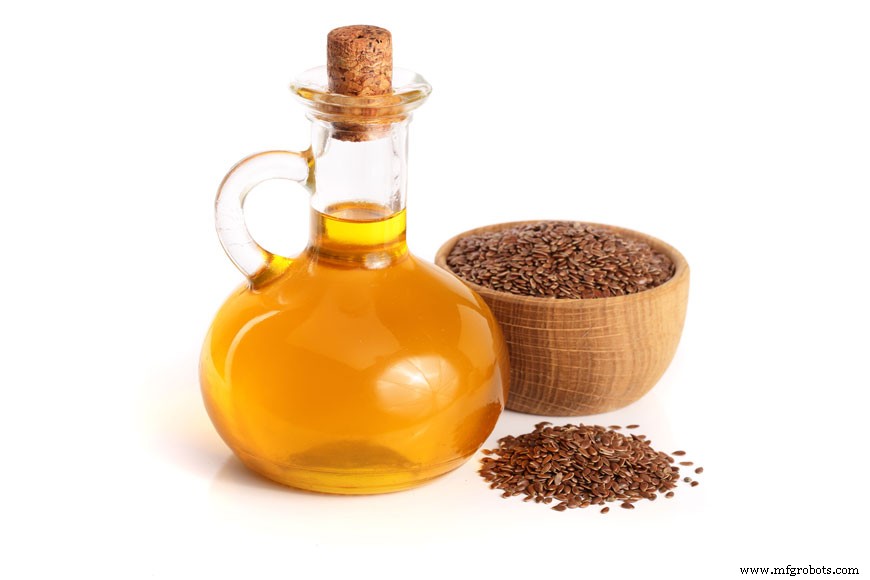
Ab den 1980er Jahren fand ein Übergang in der Kernbindemitteltechnologie statt. Seit Hunderten von Jahren Kernöl war das traditionelle Kernbindemittel – und wird teilweise noch verwendet. Leinöl, gemischt mit kleineren Mengen Harz und einem Verdünner, wie z. B. hochwertigem Kerosin, würde trockenem Gießereisand zugesetzt, um Kernsand zu erzeugen. Zusatzstoffe wie Maismehl, Dextrin, Nebenprodukte der Papierfabrik oder Proteinbindemittel kann hinzugefügt werden, um den Kern zu stärken. Diese würden normalerweise in der hohen Hitze des Gießens verbrennen, wodurch der Kern zusammenbrechen und leicht herausgeschüttelt werden könnte. Andere traditionelle Bindemittel waren Kohlenteerpech und Erdölpech, besonders stabil für große Kerne. Holz und Gummikolophonium wurde traditionell auch verwendet, um die Kollabierbarkeit des Kerns zu verbessern, obwohl diese Harze dazu neigen, bei Hitze und Feuchtigkeit zusammenzubacken. Viele dieser traditionellen Verbindungen wurden durch synthetische Optionen ersetzt, sodass die wünschenswerten Eigenschaften beibehalten, aber die Herausforderungen beseitigt wurden.
Moderne Gießereien verfügen daher über saubere Kernherstellungsprozesse, die eine bessere Luftqualität unterstützen und auf dem Gießereiboden einfacher umzusetzen sind. Diese synthetischen „chemisch gehärteten“ Kerne bieten mehrere Vorteile, darunter Backen bei niedriger Temperatur, leichtes Kollabieren während des Ausschüttelns und weniger Ausgasung während des Kernherstellungsprozesses.
Die heute am häufigsten verwendeten Kernbindemittel sind Kunststoffe aus dem Harnstoff - und Phenol-Formaldehyd Gruppen und Furanharze . Es gibt drei Kategorien von Harzbindeverfahren: Kalthärten , Coldbox/gasgehärtet und Heißhärten Methoden.
Kalthärtend Prozesse beginnen sich zu verfestigen, nachdem der letzte Zusatzstoff in den Sand eingerührt wurde, wie es bei Zement der Fall ist. Sie sind chemisch selbsthärtende Prozesse. Gängige Beispiele sind Furanharze und Phenol-Formaldehyd-Harze, die säurekatalysiert sind. Sie beginnen auszuhärten, nachdem Sulfonsäure in den Sand eingerührt wurde. Das Timing ist für diese Prozesse wichtig – der Sand kann nicht so langsam abbinden, dass er die Produktion stört, und auch nicht so schnell, dass es schwierig ist, die Reaktion zu steuern.
Cold-Box- oder gasgehärtete Prozesse ein Gas in den Kernkasten einleiten, das chemisch reagiert, um das Kernbindemittel zu härten. Beispielsweise können mit Furanharzen oder Epoxiden angereicherte Sande durch Einbringen von SO2 gehärtet werden . Wasserglas oder Natriumsilikat können mit CO2 gehärtet werden verarbeiten.
Heißhärtend Verfahren beruhen auf der Einführung von Wärme, um die Kernsande zu verfestigen. Leinkernöl , das traditionelle Kernbindemittel, wird durch einen Heißhärtungsprozess fixiert. Im Shell-Prozess , braucht die Gießerei keine Chemie:Sand kommt vorgemischt oder beschichtet vom Händler und die Chemikalien im Sand bewirken, dass er beim Backen eine harte Schale bildet. Normalerweise müssen diese nicht vollständig aushärten. Hot-Box und warm-box Verfahren verwenden Furan- oder Phenolharze und einen Säure-Salz-Katalysator, der beim Erhitzen des Kernkastens aushärtet. (Sie unterscheiden sich nur in der Art des Harzes und der zum Aushärten erforderlichen Temperatur.)
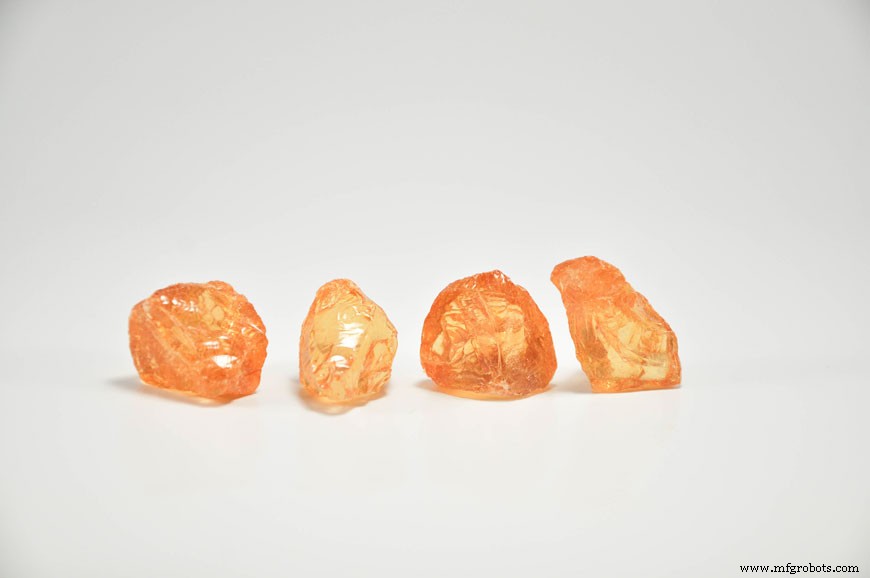
Kernherstellungsverfahren
Kerne werden nach vielen der gleichen Methoden hergestellt, die für Sandformen verwendet werden. Außerdem Kerngebläse und Schneckenmaschinen verwendet werden.
Kerngebläse Pressen Sie Sand mit Druckluft mit etwa 100 lb/in 2 in den Kernkasten . Sie können zur Herstellung aller Arten von kleinen und mittleren Hülsen verwendet werden. Die hergestellten Kerne sind sehr gleichmäßig und es werden hohe Produktionsraten erreicht.
Schraubenvorschub Maschinen werden verwendet, um glatte Kerne zu extrudieren, normalerweise zylindrisch. Der Kernsand wird durch eine Matrize auf eine Kernplatte gedrückt. Der Einsatz dieser Maschinen beschränkt sich auf die Herstellung von Vorratskernen:Der lange, extrudierte Zylinder, der von der Maschine erzeugt wird, wird gebacken und dann auf die gewünschte Länge geschnitten.
Kerntrockner sind wie Kuchenformen, da sie die Form eines Kerns unterstützen, während er sich im Kernofen befindet Backen. Dies sind normalerweise leichte Skeletteisen- oder Aluminiumkästen, deren innere Form sich eng an den oberen Teil des Kerns anpasst. Kerne, die zerbröckeln oder Teile abbrechen würden, wenn sie auf eine flache Platte gelegt werden, durchlaufen den Ofen in einem Kerntrockner.
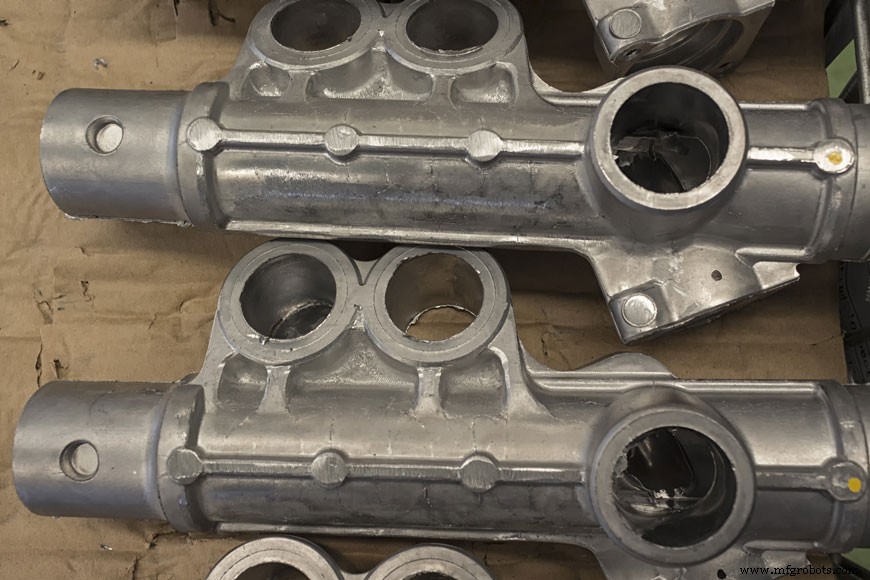
Kern platzieren
Nachdem ein Kern fertig ausgehärtet ist, wird er oft von Hand fertiggestellt. Entlang der Trennlinien des Kernkastens können „Finnen“ gefeilt werden. Manchmal werden Kerne in mehreren Teilen hergestellt, wenn die benötigte Form größer ist als die vorhandenen Kernkästen und Öfen. Nach der Härtungsstufe wird ein segmentierter Kern zusammengesetzt. Wenn die Kerne glatt und verbunden sind, werden sie in Gestelle gelegt, um auf die Verwendung in der Form zu warten.
Kerne werden fast immer sorgfältig von Gießereiarbeitern platziert und nicht von einer Maschine eingesetzt. Rosenkränze, falls vorhanden, gehen zuerst in die Schleppe, und dann wird der Kern platziert. Der Gießer achtet darauf, dass der Kern richtig in der Form sitzt und frei von Fehlstellen ist. Alle benötigten Kränze werden auf den Cope gelegt, und wenn alles gut aussieht, wird der Cope über die Schleppe gelegt und festgeklemmt.
Kerne schaffen Flexibilität im Sandguss
Die Fähigkeit, Sandkerne herzustellen und zu platzieren, ist ein wesentlicher Bestandteil des Gießprozesses.
In einigen Fällen ist der Kern für die Nützlichkeit des endgültigen Teils erforderlich:Rohre, Motoren und andere mechanische Geräte müssen oft hohl sein, um zu funktionieren. Bei Dekorationsartikeln können Kerne auch die Gesamtkosten für Metall senken. Besonders beim Gießen in Eisen können Kerne das Gewicht eines Endprodukts erheblich reduzieren. Wenn die mechanische Festigkeit von massivem Stahl benötigt wird, kann dies ungeeignet sein. Unter anderen Umständen ist ein Kern jedoch eine gute Designüberlegung, auch wenn er für die Funktion des Produkts nicht erforderlich ist.
Vorheriger Beitrag:Gießerei-SandMetall-GießverfahrenNächster Beitrag:Schmelzen und Gießen
Herstellungsprozess
- Die Bedeutung von Kernkompetenzen
- Die Grundlagen der Statorkernlaminierung in Ihrer Ausrüstung
- Cyber-Physical Systems:Der Kern von Industrie 4.0
- Welche Arten von Sandstrahlsand gibt es?
- Sandgussanwendungen für den Schwermaschinenmarkt
- Sandguss vs. Druckguss:Was sind die Unterschiede?
- Sandgussanwendungen für den Automobilmarkt
- Wann das Harz-Sandgussverfahren gewählt werden sollte
- Die Funktionsweise eines Heizkerns verstehen
- Lake Erie Brecher – Die Zukunft von Sand und Kies