Alcoa strebt hervorragende Zuverlässigkeit an
Wenn Sie die Hitze nicht ertragen können, suchen Sie besser keine Anstellung im Alcoa Primary Metals Werk im Süden von Indiana.
Feuerspeiende Topfleitungen und mit geschmolzenem Metall gefüllte Tiegel können die Umgebungstemperatur der Produktionshalle in den dreistelligen Bereich anheben. Hitze strahlt sichtbar von Maschinen ab. Schweißrinne rinnt den Arbeitern über Wangen und Rücken. Häufige Pausen für Wasser und Gatorade sind eine Notwendigkeit.
Es ist eine körperlich anstrengende Umgebung, aber die im ersten Absatz erwähnte tatsächliche Wärme bezieht sich eher auf die Position dieses speziellen Werks in der Aluminiumschmelzindustrie. Dieser Standort, Teil von Alcoas massivem Warrick Operations, wurde in den späten 1950er Jahren gebaut und begann in den frühen 1960er Jahren mit der Produktion von Rohaluminium für die Dosenblechindustrie.
Es ist ein altes Werk in einer alters- und technologiesensiblen Branche. 1980 waren in den USA 33 Schmelzwerke in Betrieb. Heute sind es 13. Nur noch 6 Prozent der weltweiten Aluminiumkapazität werden in diesem Jahr in über 50 Jahre alten Schmelzhütten produziert. Die Uhr tickt.
Fügen Sie zu diesem Zustand Folgendes hinzu:
-
25 Prozent der Belegschaft des Werks haben derzeit aufgrund des Alters oder der Dienstjahre Anspruch auf Rente;
-
die vom Werk gezahlten Löhne gehören zu den höchsten in der Branche; und,
-
Vor einigen Jahren waren die Wartungskosten dieser Schmelze pro produzierter Tonne Aluminium die zweithöchsten im globalen Alcoa-System.
Kannst du die Hitze spüren? Jeder Mitarbeiter in diesem Werk tut es. Aber anstatt auf einen drohenden Untergang zu warten, sind Wartungs- und Betriebspersonal vorgetreten und haben Maßnahmen ergriffen.
„Wir müssen anpacken, wenn wir diesen Lebensstandard halten und diese Anlage am Leben erhalten wollen“, sagt Mark Keneipp, Manager für das schmelzende Alcoa Business System. „Das ist die neue Realität. Du musst nur damit klarkommen.“
Es beginnt mit einem Blick in den Spiegel.
„Unsere Herausforderung war und ist es, trotz unseres hohen Alters wettbewerbsfähig zu bleiben“, sagt Keneipp. „Wir stehen nicht mehr an der Spitze der Alterskurve. Wir müssen einen Horizont von 15 bis 20 Jahren haben, um Kapital bei Alcoa anzuziehen. Wenn es 25 bis 30 Jahre sind, wäre das toll. Dazu müssen wir uns kontinuierlich als schlankes, wettbewerbsfähiges, stabiles und effizientes Werk beweisen.“
Dies ist keine Umgebung für die Schwachen. Aber für harte Arbeit und Ausdauer gibt es reichlich Belohnungen.
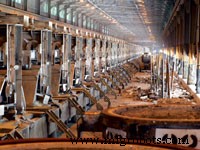
Anrufzeitüberschreitung
Die Bemühungen, die Präsenz von Alcoa Primary Metals in der Fertigungsgemeinschaft im Süden von Indiana aufrechtzuerhalten, begannen auf Unternehmensebene.
1997 begann Alcoa-CEO Alain Belda, die Prinzipien des Toyota Production System (TPS) an die 250 weltweiten Standorte seines Unternehmens zu übertragen.
Produktionsleiter der Aluminiumanlage Rodney Cunningham (links), Prozesskoordinator Larry York und Senior Der Prozessingenieur Brian Audie steht in einem leeren Aluminiumoxidtank auf dem Gelände von Alcoas Warrick Operations. Der Standort verwendete traditionell vier solcher Tanks als Auffanggefäße für Aluminiumoxid, einen Schlüsselbestandteil des Aluminiumschmelzprozesses. Initiativen zur schlanken Produktion und kritisches Denken führten dazu, dass das Werk auf zwei Tanks verkleinert wurde, wodurch dem Unternehmen eine große Summe Geld gespart wurde.
TPS ist eine schlanke Fertigungsphilosophie, die auf „Just-in-Time“-Produktion, Abfallvermeidung und schneller Problemlösung basiert. Bei der Implementierung des Systems machte die Hütte in Indiana jedoch eine wichtige Entdeckung.
„TPS und Flow und Lean funktionieren nicht, wenn Sie eine instabile, unberechenbare Ausrüstung haben“, sagt Keneipp.
Effiziente, optimierte und kostengünstige Anlagenwartung und Maschinenzuverlässigkeit müssen an erster Stelle stehen.
Um seinen Standpunkt zu veranschaulichen, bietet Keneipp ein Diagramm namens „der Wartungseisberg“ an. Über dem Wasser liegen direkte Wartungskosten in Verbindung mit Material, Arbeit, Überstunden, Vertragsleistungen sowie Gemeinkosten und Sozialleistungen. Unter der Oberfläche lauern indirekte Kosten im Zusammenhang mit Ausfallzeiten, Einrichtung und Inbetriebnahme, verpassten Zeitplänen, Überbeständen, Krisenmanagement, Notkäufen und einer allgemeinen Auswirkung auf die Produktion.
„Die indirekten Komponenten werden von den instabilen Anlagen und Prozessen einer Anlage gefangen gehalten“, sagt er.
All dieser Abfall belastet das System und treibt sowohl die Betriebs- als auch die Wartungskosten in die Höhe.
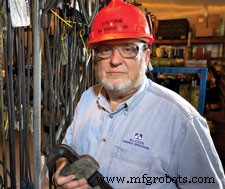
Im Jahr 2002 hatte diese Schmelzanlage Gesamtwartungskosten von über 35 Millionen US-Dollar. Seine „schmerzlich hohe“ Quote von mehr als 137 US-Dollar an Wartungskosten für jede produzierte Tonne Aluminium (siehe „Nur die Fakten“ für die Jahrestonnage) platzierte es an zweiter Stelle unter den Alcoa-Schmelzwerken weltweit. Der weltweite Durchschnitt lag im Jahr 2002 bei 90 USD pro Tonne.
Dieses Alcoa-Werk und seine Führer hatten zwei Möglichkeiten.
„Der Werksleiter Royce Haws sagte, wir würden unsere Kosten senken. Es war keine Option, dort zu bleiben, wo wir waren. Es würde passieren“, sagt Keneipp. „Wir könnten es entweder klug oder kurzsichtig machen. Wenn Sie kurzsichtig sind, sind das beängstigende Tage. Es ist schwierig, Kapital in die Anlage zu locken, um die Dinge zu erledigen, die getan werden müssen, wenn Sie nur die Wartung verschieben. Niemand fühlt sich bei diesem Ansatz gut. Das ist Motivation für die Leute, nach etwas Besserem zu suchen.“
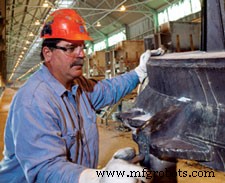
Die Wellen fangen
Wenn Sie es noch nicht erraten haben, hat sich das Werk von Alcoa für den intelligenten Ansatz entschieden, um die Wartungskosten zu senken. Instandhaltungsleiter haben sich Anfang 2003 mit Beratern von Life Cycle Engineering (LCE) und der Ron Moore Group zusammengetan, um einen Ansatz namens Reliability Excellence Process zu entwickeln, der in drei „Wellen“ umgesetzt wurde. Der Prozess basiert auf der Überzeugung, dass eine formalisierte, klar definierte Partnerschaft zwischen Wartung und Betrieb unerlässlich ist. Bei dieser Partnerschaft besitzt der Betrieb die Ausrüstung und hat einen primären Anteil an der Zuverlässigkeit. Maintenance ist ein gleichberechtigter Partner, der sich dafür einsetzt, zeitnahe und effektive Methoden, Fähigkeiten, Fachwissen und Unterstützung bereitzustellen.
„Das ist eine große Veränderung“, sagt der Leiter der Zuverlässigkeitstechnik, Joseph Motz. „Früher war es eine Siloumgebung mit vielen Fingerzeigen.“
In der Barrenabteilung von . wird geschmolzenes Metall aus einem Tiegel gegossen
die Alcoa-Pflanze.
Einige Beispiele:
Ein Bediener hat ein potenzielles Problem bemerkt. Es wurde kein Fix geplant oder durchgeführt. Die Maschine ist kaputt gegangen. Wer war schuld?
Oder die Wartung erschien zu einer zweistündigen vorbeugenden Wartung. Während es in der Maschine war, stellte es zusätzliche Probleme fest und beendete den PM-Job acht Stunden später, was sich auf die Leistung auswirkte. Wer war schuld?
Die Antwort in diesen Fällen war sowohl Wartung als auch Betrieb.
„Wir mussten feststellen, dass wir alle im selben Team sind“, sagt Motz. „Wir sind alle hier, um Aluminium herzustellen. Wenn wir in verschiedene Richtungen gehen und nicht zusammenarbeiten, funktioniert der Prozess nicht.“
Welle 1 des Drei-Wellen-Ansatzes begann im Juni 2003.
„Welle 1 war Ron Moore“, sagt Keneipp. „Wir haben ihn eingeladen, um mit wichtigen Werksleitern zu sprechen. Er forderte die uralten Paradigmen heraus. „Du musst mehr von einer Asset-Owner-Philosophie ausgehen.“ „Du verschwendest Geld.“ Er mischt die Dinge auf und öffnet die Augen.“
Welle 2 kam im August mit einer vollständigen Reliability Excellence-Bewertung durch LCE. Über einen Zeitraum von zwei Wochen führte das Unternehmen langwierige Interviews mit 90 Betriebs- und Wartungsmitarbeitern (Stundenlohn und Gehalt) sowie dem Anlagencontroller.
Die Informationen führten zu:
-
eine Finanzanalyse, die den geschätzten Wert bei der Schließung der Lücken in Bezug auf hervorragende Zuverlässigkeit im Vergleich zu den Implementierungskosten detailliert beschreibt (dargestellt als Return-on-Investment-Berechnung);
- ein vorläufiger Masterplan, der die Prozesse und Methoden skizziert, die erforderlich sind, um die Lücken zu schließen.
„Wir wollten unseren Ist-Zustand betrachten und einen Soll-Zustand ermitteln“, sagt Keneipp. „Die Kluft zwischen diesen beiden ist dein Schmerz oder dein Gewinn. Lohnt es sich, die Lücke zu schließen? Das mussten wir der Geschäftsleitung beweisen. Wir mussten beweisen, dass es sinnvoll war, Geld in die alte Anlage zu investieren.
„Angesichts der Tatsachen war es ratsam, so schnell wie möglich Gelder zu genehmigen, um fortzufahren.“
Welle 3 begann im September. Betriebs- und Wartungsleiter:
-
den Masterplan umgesetzt
-
schulte alle Mitarbeiter in ihren neuen Rollen und Verantwortlichkeiten im Zusammenhang mit der Erhöhung der Anlagenzuverlässigkeit
-
Workshops zu geeigneten Techniken zur Verbesserung der Zuverlässigkeit durchgeführt
-
etablierte definierte Prozesse und wirksame Fortschrittsmaßstäbe
„Das ist nicht einfach. Nichts von alledem ist es“, sagt Rodney Cunningham, Produktionsleiter des Potrooms. „Aber mit Engagement des Managements und einer Partnerschaft zwischen Instandhaltung und Betrieb steigen Ihre Erfolgschancen. Ohne diese Dinge wirst du es nicht schaffen.“
Die Messlatte höher legen
Die Festlegung von Definitionen in einer Vielzahl von Bereichen hat dazu beigetragen, Verbesserungen anzustoßen. Ein Hauptaugenmerk lag auf der Definition von „Was ist möglich?“. und „Was ist Fortschritt?“
Eine Antwort bestand darin, die Gesamtanlageneffektivität (OEE) als wichtige anlagenweite Kennzahl zu akzeptieren. OEE verfolgt Quellen von Betriebsverlusten, einschließlich Geräteverfügbarkeit, Leistung und Qualität, und wird als Prozentsatz der optimalen Leistung ausgedrückt.
„Im Grunde wird es durch einige der besten Leistungen der Vergangenheit definiert“, sagt Tom Svoboda, Leiter der Elektrodenproduktion. „Du hast gesehen, wie es passiert ist. Es war weder fiktiv noch hypothetisch. Ob die Geräte in diesem Monat außergewöhnlich liefen oder Sie den Prozess wirklich im Griff hatten, es passierte. Die Frage ist, wenn Sie es in diesem einen Zeitraum getan haben, warum können Sie es dann nicht die ganze Zeit tun?“
Unter Verwendung einer Sportanalogie, um die Bedeutung von 100 Prozent OEE zu veranschaulichen, wenn ein Hochspringer normalerweise 6 Fuß 6 Zoll springt, aber eine persönliche Bestleistung von 2,7 Fuß aufstellt, was speziell zu dieser 100-prozentigen Spitzenleistung führte. Hat er anders trainiert? Hat er vor dem Treffen seine Ernährung umgestellt? Hat er andere Schuhe getragen? Er hat die Messlatte buchstäblich höher gelegt. Was kann man lernen und was kann man tun, um diese Marke immer wieder zu erreichen?
Wartung und Betrieb arbeiteten zusammen, um Spitzenleistungen für Anlagenfunktionen (z. B. Anodenmontage), Prozesse (Erzentladung), Ergebnisse (Schrott) und einzelne Ausrüstungsteile (Ringofen) zu definieren. Bei der Zusammenstellung dieser Informationen wurde festgestellt, dass durch das Erreichen der OEE-Ziele jährliche Kosteneinsparungen in Höhe von 8,3 Millionen US-Dollar möglich sind.
Mit den Hintergrundinformationen wurden Ist-Zustände definiert und Soll-Bedingungen festgelegt. Aktivitäten – Arbeitsprojekte mit Lean-Manufacturing-Tools wie Kaizen und Continuous Improvement – fanden statt. Der Fortschritt wurde gemessen und analysiert. Und es wurden greifbare Vorteile berechnet.
Im Jahr 2004 waren Verbesserungen in Höhe von 2,4 Millionen US-Dollar mit OEE-Gewinnungen verbunden.
Ein genauer Blick und das Ergreifen von Maßnahmen führte auch zu geringeren Wartungskosten in der Schmelzanlage. Im ersten Jahr nach Beginn der Zuverlässigkeitsinitiative sanken die Ausgaben um 1,9 Millionen US-Dollar, von 32 Millionen US-Dollar auf 30,1 Millionen US-Dollar. Im Jahr 2004 sank die Zahl um weitere 700.000 US-Dollar. Auch die Wartungskostenquote pro produzierter Tonne sank 2004 auf 109 US-Dollar.
Der Plan zu „Geplant“
Es wurden auch große Anstrengungen unternommen, um Elemente der Instandhaltung besser zu definieren. Insbesondere in diesem bedienergeführten Zuverlässigkeitssystem:„Wie wird die Arbeit geplant?“ und „Wie wird Arbeit erledigt?“
„Rückblickend täuschten wir uns vor, wir seien gesund“, sagt Wartungsleiter Danny Reyes. „Viele unserer alten Metriken waren außer Reichweite. Wir dachten, unser ‚Prozentsatz geplanter und geplanter Arbeit‘ liege bei 85 Prozent und unser ‚Prozentsatz PM-Erledigung‘ bei 90 Prozent.“
LCE hat dem Werk mitgeteilt, dass es die falschen Definitionen verwendet.
„Der ‚Prozentsatz geplanter und geplanter Arbeit‘ war eigentlich nur ‚Prozentsatz geplant‘. Die Planung war sehr begrenzt“, sagt Reyes. „Es war die Einhaltung des Zeitplans. Wahrscheinlich waren 10 Prozent dieser Jobs geplant.“
Ein 35-zu-1-Verhältnis von Handwerkern (140) zu Planern (vier) war der Kern des Problems.
„Es hat nicht sehr gut funktioniert“, sagt Wartungsplaner Larry McCubbins. „Es war sehr wenig Zeit für die Planung. Du bist ein Planer geworden, und noch dazu kein sehr guter.“
Eine reaktive Umgebung gedeiht in dieser Umgebung. „Wir machten den ‚Home Maintenance-Ansatz‘“, sagt Keneipp. „So gehen Sie und ich an einem Samstagmorgen Projekte an. Es ist wirklich ungeplant und ineffizient.“
Das Werk hat seitdem drei Planer für insgesamt sieben hinzugefügt, was ein überschaubareres Verhältnis von 20 zu 1 bietet.
„Das ermöglicht es diesen Leuten, die Arbeit einzurichten, zu organisieren, zu planen, mit Produktionszentren abzustimmen, sicherzustellen, dass alle Teile vorhanden sind, sicherzustellen, dass die Ausrüstung ausfällt und die Zeit zugewiesen ist“, sagt der Instandhaltungsleiter der Schmelze Scott Deon.
Andere Schlüssel für eine bessere Planung:
-
Ein formelles Dokument skizziert nun die Komponenten eines geplanten Jobs (siehe Seitenleiste auf Seite 14). „Die armen vier Planer, die wir versuchten, alles zu machen, haben die Dinge nicht gleich gemacht“, sagt Deon. „Dieses neue Format standardisiert jetzt, wie die Arbeit ausgeführt wird.“
-
Ein formeller, sicherer Bereich wird nun von den Planern für das Job-Kitting genutzt. In der Vergangenheit wurden benötigte Teile und Materialien stückweise an eine Baustelle geliefert. Der Stapel kann wochenlang liegen, bis alle Artikel angekommen sind. Während der Wartezeit kam es nicht selten vor, dass Teile oder Werkzeuge verschoben, verloren oder für einen anderen Auftrag verwendet wurden.
„Da der Planer den Auftrag plant, bestellt er alle Materialien und lässt sie hierher liefern “, sagt McCubbins. „Wenn alles für den Job da ist, sammeln wir es auf ein oder zwei Paletten. Die Handwerker kommen dann und bringen es zur Baustelle und führen die Arbeit aus.“ -
Effektive Kommunikation.
„Früher dachte ich, ich wüsste, was die Leute wollen. Dieser Prozess hat mich gelehrt, dass ich es nicht getan habe“, sagt McCubbins. „Ich wusste nicht, was sie wollten und was für sie richtig war. Früher habe ich den Job geplant und keine Fragen gestellt.“
Fügt Deon hinzu:„Durch die gemeinsame Verantwortung mit der Produktion wissen wir jetzt, welcher Job zuerst kommt. Die Person, die die Ausrüstung besitzt, sollte wissen, was das Wichtigste ist. Ich glaube nicht, dass wir vorher geahnt haben. Aber waren wir 100 Prozent? Wahrscheinlich nicht.“ -
Konzentrierte, effektive wöchentliche Meetings.
„Vermögenseigentümer leiten die Sitzungen und Planer/Planer für die Bereichswartung sind Vermittler“, sagt Keneipp. „Wenn es sich um ein Planungstreffen handelt, besprechen wir, wie wir das machen. Wenn es sich um ein geplantes Meeting handelt, legen wir den Zeitplan fest.“
Auch im Hinblick auf die Art und Weise, wie die Arbeiten ausgeführt werden, hat das Werk Schritte unternommen, um die Gerätehistorie zu dokumentieren und die Anweisungen für Wartungsaufgaben zu standardisieren.
„Früher konnte man Aufzeichnungen bekommen, aber dann hörte die Dokumentation auf“, sagt Dan Decastra, Energieingenieur der Gleichrichterstation. „Also haben wir einen Standort auf dem Server erstellt und mit der Dokumentation begonnen. Für diese Station haben wir eine „Bad Boy“-Liste erstellt. Wir haben uns die großen Themen herausgesucht und dort angefangen. Jetzt können Sie bis ins Jahr 2001 zurückgehen und eine Historie der Luftschalter, Kontakte, Transformatoren und Kufen einsehen.“
Zuverlässigkeitsingenieur Jonathan Fulton fügt hinzu:„Vielleicht könnte ein Drittel unserer Wartungsmitarbeiter morgen in Rente gehen, wenn sie wollten. Das ist eine große potenzielle Belastung für uns. Und es ist schwer, von außen einen guten Handwerker zu bekommen. Dafür standardisieren wir Arbeitsabläufe und entwickeln die Gerätehistorie. Auf diese Weise können wir schnell Leute mit technischem Know-how auf den neuesten Stand bringen.“
Krippennotizen
Ein letztes Verbesserungsbeispiel ist, wie das Werk besser definierte, wer Wartungsprodukte kauft und wie Geld für Werkzeuge und Verbrauchsmaterialien ausgegeben wird.
In der Vergangenheit kaufte verschiedenes Wartungspersonal im Schmelzwerk die Handwerkzeuge, Elektrowerkzeuge, Sicherheitsprodukte, Reinigungsmittel, Fördermittel und hundert andere benötigte Artikel. Gekaufte Produkte wurden in dezentralen Werkzeuglagern in der gesamten Einrichtung und in einer Vielzahl nicht offizieller Aufbewahrungsorte (Schließfächer, Truhen und Ablagefächer) untergebracht.
„Im Zuge der ständigen Erweiterung des Werks kamen weitere Flächen hinzu. Sie hatten eine kleine Gruppe und jemand hat die Bestellung gemacht und hier und da ihre Vorräte gesammelt“, sagt Generalmechaniker Dick Day. „Wir haben viel Geld ausgegeben, um diese Satellitenkrippen zu ernähren. Sie wurden nicht verwaltet. Die Leute haben Sachen gekauft, aber sie waren nicht wirklich zugänglich.“
Wenn ein Mechaniker ein bestimmtes Werkzeug brauchte, würde er danach suchen. Es war irgendwo herum. Wenn er es nicht finden konnte, würde er eines bestellen. Das gekaufte Werkzeug könnte verschwinden, bevor es ihn erreicht. Dies führte zu verschwenderischen und überflüssigen Ausgaben.
Um dies zu beheben, wurde eine zentrale Krippe gebaut und alle Satelliten-Krippen und Ablagefächer wurden in diesen sicheren, umzäunten Bereich gebracht.
Das Wertlose kam herein.
„Wir haben festgestellt, dass wir viel veraltetes Zeug haben – etwas für ein Gerät, das wir vielleicht vor 10 Jahren herausgenommen haben“, sagt Keneipp.
Und da kam das Wertvolle.
„Es war erstaunlich, was alles aus den Holzarbeiten herauskam. Jemand brachte einen Schrank mit Pumpen und Buchsen im Wert von mehr als 38.000 US-Dollar herüber“, sagt Day, der zum Hauptwärter der zentralen Krippe wurde. „Wir haben angefangen, das zu verwenden, was wir hatten. Bei manchen Materialien mussten wir ein Jahr lang nichts bestellen.“
Heute ist Day für den Einkauf dieser wartungsrelevanten Produkte verantwortlich. Er nimmt die Einkäufe entgegen, lagert die Artikel und gibt sie nach Bedarf aus.
„Wir wissen, was wir haben und wo es sich befindet“, sagt er.
Day hat außerdem ein Minimum-/Maximum-System für eine Vielzahl von Produkten entwickelt und sich bemüht, Marken von Elektrowerkzeugen und Schweißzubehör zu standardisieren.
„Bei Elektrowerkzeugen haben wir uns größtenteils auf DeWalt standardisiert, und wir steigen stark in ihre schnurlosen Werkzeuge ein“, sagt er. „Für Schweißzubehör haben wir unsere Drahtvorschubzangen und die Ersatzteile für diese Zangen standardisiert.“
Er macht seine Hausaufgaben und findet innovative Wege, um Kosten zu sparen.
Einige Beispiele sind:
Handschuhe :„Früher kauften wir Handschuhe mit einer kleinen Lasche für 12 Dollar pro Paar. Das musste jeder haben“, sagt er. „Sie könnten die gleichen Handschuhe mit einem kleinen Gummiband für 2,67 US-Dollar pro Paar kaufen. Die Leute mochten sie.“
Hydrauliköl :„Wir haben es in Gallone für 8 Dollar pro Pop gekauft. Wenn wir es in großen Mengen kaufen, sparen wir jetzt 3 US-Dollar pro Gallone. Ich gieße das Öl in wiederverwendbare Krüge, die 57 Cent pro Stück kosten.“
Acetylenschlauch :„Früher haben wir es vorverpackt in einer Spule gekauft. Jetzt kaufen wir es auf einer 150-Fuß-Rolle und schneiden ab, was die Person braucht. Wir sparen 25 Prozent.“
Day sagt, das ist alles gesunder Menschenverstand.
„Ich betrachte es als mein Geld“, sagt er. „Wenn das mein Geschäft ist, würde ich es so führen.“
Bringt sie zum Schwitzen
Durch harte Arbeit, Partnerschaft, Eigenverantwortung und innovatives Denken ist diese Alcoa-Schmelzanlage stabiler, schlanker, berechenbarer, zuverlässiger und wettbewerbsfähiger geworden.
Die OEE-Kostenvorteile belaufen sich auf das Jahr 2005 auf Jahresbasis hochgerechnet auf 4,4 Millionen US-Dollar im Vergleich zum Ausgangswert von 2003.
Die Wartungskosten für das Jahr 2005 betragen jährlich 27,1 Millionen US-Dollar und spiegeln einen Rückgang um 4,9 Millionen US-Dollar gegenüber dem Ausgangswert von 2003 wider.
Die Wartungskosten für das zweite Quartal 2005 betrugen 96 US-Dollar pro produzierter Tonne, und in naher Zukunft sollen 87 US-Dollar erreicht werden.
Eine LCE-Folgebewertung hat das Werk in die Kategorie „proaktive Bedingungen“ eingestuft und es wird daran gearbeitet, in die Kategorie „Exzellenz“ aufzusteigen.
Es herrscht Optimismus und Dynamik.
„Als ich vor 15 Jahren eingestellt wurde, sagten wir:‚Wir sind alte Technologie. Wir können mit einigen der moderneren Einrichtungen nicht mithalten“, sagt Fulton. „Für mich besteht die Belohnung darin, dass wir konkurrenzfähig sind und eine höhere Effizienz haben. Wir produzieren mit unserer 40 oder 50 Jahre alten Technologie besser als an Standorten, die vor 10 oder 20 Jahren gebaut wurden.“
Auch wenn die Hitze dieser Pflanze nie ganz verschwinden wird, tut sie alles, um die Konkurrenz ins Schwitzen zu bringen.
Was sind die Merkmale eines geplanten Jobs?
-
Es gibt eine genaue Zeitschätzung für den Job, so dass der Vorgesetzte vernünftigerweise erwarten kann, wann er oder sie die Aufgabe zuweisen kann.
-
Es gibt eine genaue Schätzung der benötigten Ressourcen in Bezug auf Handwerkspersonal, Reparatur-/Ersatzteile, Werkzeuge, Hilfsausrüstung usw.
-
Alle notwendigen Informationen (Blaupausen, Genehmigungen, sicherheitsrelevant, etc.) werden eingeholt.
-
Arbeitsschrittfolge, Verfahren und Anweisungen zur Ausführung der Arbeit sind festgelegt.
-
Alle benötigten Teile und Materialien sind montiert.
-
Besprechen Sie als eingebaute Überprüfung, um eine geplante Qualität der Arbeit zu gewährleisten, regelmäßig die Art der Arbeit mit einem Vorgesetzten und/oder dem mit der Ausführung der Arbeit beauftragten Handwerker. Stellen Sie sicher, dass Sie den Umfang der Arbeit vollständig verstehen und das Jobpaket vollständig ist.
Gerätewartung und Reparatur
- Was ist Zuverlässigkeitskultur?
- Welche Rolle spielt der Zuverlässigkeitsingenieur?
- Eine Revolution der Whirlpool-Zuverlässigkeit
- Beste Leistung bei Wartung und Zuverlässigkeit
- Der Schlüssel zum Erfolg bei Zuverlässigkeit
- Wie beschleunigt Exzellenz der Zuverlässigkeit die Vorteile von Lean?
- Familienorientierte Zuverlässigkeit
- Supply Chain Management:Mehr als nur hervorragende Zuverlässigkeit
- Warum hervorragende Zuverlässigkeit für die Sicherheit unerlässlich ist
- Zuverlässigkeit ist eine grüne Initiative