Hybrid, großformatige additive Werkzeuge:Leichtere, schnellere und kostengünstigere Formen für große Teile
Seit mehr als drei Jahrzehnten setzt die kommerzielle Luftfahrt verstärkt auf Verbundwerkstoffe. Tatsächlich sind heute mehr als die Hälfte der kritischen Strukturkomponenten mehrerer Modelle großer Verkehrsflugzeuge Verbundwerkstoffe. Da die Verwendung dieser Materialien sowohl in Bezug auf das Volumen als auch die Größe der Teile zugenommen hat, wurde es immer schwieriger, Werkzeuge – insbesondere kostengünstige Werkzeuge – zu bauen, um diese Teile schneller als Prototypen herzustellen und herzustellen. Die Tragflächen der A350 XWB von Airbus SE (Leiden, Niederlande) sind beispielsweise jeweils 32 Meter lang und 6 Meter breit und stellen einige der größten jemals produzierten Verbundstrukturen für die Luftfahrt dar.
„Es gibt mittlerweile so bahnbrechende Fertigungstechnologien auf dem Markt, dass wir große Fortschritte in der Werkzeugentwicklung erwarten können, die uns helfen, die Herausforderungen zu meistern, denen wir bei der Entwicklung von Verbundwerkstoff-Flugzeugkomponenten gegenüberstehen“, sagt M. Pilar Muñoz Lopez, Composite Manufacturing Engineer bei Airbus-Werk in Illescas, Spanien:„Für uns ist es von entscheidender Bedeutung, diese Technologien, Fähigkeiten und Einschränkungen zu untersuchen, damit wir für die Zukunft gerüstet sind.“
Da Werkzeuge einen erheblichen Anteil an den Gesamtprogrammkosten für Flugzeugstrukturteile ausmachen und angesichts der zunehmenden Größe dieser Teile werden neue Werkzeugoptionen mit geringeren Kosten und Vorlaufzeiten benötigt. Airbus, Northrop Grumman Aeronautics Systems – Aerospace Structures Business Unit (Clearfield, Utah, USA) und die Universität haben kürzlich eine interessante Studie zu hybriden, großformatigen, additiv gefertigten (LFAM) Werkzeugen für Prototypen- und Kleinserien-Flugzeugstrukturteile abgeschlossen des Dayton Research Institute (UDRI, Dayton, Ohio, USA) mit ermutigenden Ergebnissen.
Zähmung von Problemen mit der Wärmeausdehnung
Ein Großteil der Flugzeugstrukturen aus kohlenstofffaserverstärktem Kunststoff (CFK) wird aus Prepreg mit Epoxidmatrix hergestellt. Um solche Teile zu formen, müssen die Werkzeuge Ofen- oder Autoklaven-Härtungstemperaturen von bis zu 180 °C/356 °F überstehen. Angesichts des sehr niedrigen (linearen) thermischen Ausdehnungskoeffizienten von CFK (CLTE oder CTE) ist es außerdem entscheidend, dass Werkzeug- und Formmaterial-CLTEs bei Raum- und erhöhten Temperaturen so genau wie möglich übereinstimmen. Dadurch wird sichergestellt, dass die Formen ihre Abmessungen beibehalten, sodass die resultierenden Teile auch die dimensionalen Anforderungen erfüllen. Um Verzerrungen oder Spannungen in den endgültigen Strukturen zu vermeiden, ist es auch wichtig, ein Werkzeugmaterial zu vermeiden, das schneller abkühlt als das Teilematerial. Infolgedessen werden die am häufigsten verwendeten Werkzeuge zum Formen großer CFK-Flugzeugstrukturen entweder aus CFK selbst oder Invar hergestellt, einer Eisenlegierung aus Nickel und Eisen, die für ihren niedrigen CLTE bekannt ist. Beides ist kostspielig und kann erhebliche Vorlaufzeiten haben. Darüber hinaus ist Invar schwierig und zeitintensiv zu bearbeiten und schwer zu versenden. Während Stahl- oder Aluminiumwerkzeuge die Kosten senken können, schränken ihre relativ höheren CLTE-Werte den Einsatz in vielen Anwendungen ein – insbesondere beim Formen großer oder langer Teile.
Viele öffentliche und private Studien haben additiv gefertigte Werkzeuge bewertet, die aus thermoplastischen Materialien gedruckt sind, und kamen zu dem Schluss, dass sie potenzielle Vorteile bieten, darunter niedrigere Kosten und kürzere Vorlaufzeiten für die Herstellung von duroplastischen Laminatverbundwerkstoffen. Leider weisen LFAM-Werkzeuge auf Polymerbasis Probleme wie die Werkzeugporosität auf, die zu einem erheblichen Vakuumverlust bei Härtungstemperaturen/-drücken führen kann. Um dies zu beheben, sind zusätzliche Nacharbeiten der Werkzeugfüllung und Oberflächenbeschichtungen erforderlich. Eine noch größere Herausforderung sind die stark anisotropen CLTE-Werte aufgrund der Ausrichtung des Füllmaterials in der Ebene während des Extrudierens/Druckens, was zu 5-10-mal größeren Dehnungs-/Kontraktionsunterschieden in der Z-Achse als in den X- und Y-Druckachsen führen kann. Das macht es zu einer Herausforderung, maßgenaue Teile wiederholbar und reproduzierbar zu erhalten – insbesondere wenn Teile groß sind, ein hohes Seitenverhältnis aufweisen und/oder komplexe Oberflächen aufweisen.
„Jeder, der sich für additive Werkzeuge interessiert, ist mit den gleichen Problemen wie Porosität und unkontrollierte Wärmeausdehnung konfrontiert und es gibt nur wenige wirksame Möglichkeiten, diese Probleme anzugehen“, erklärt Scott Huelskamp, UDRI-Teamleiter, Entwicklung fortschrittlicher Herstellungsverfahren, Division Structural Materials. „Es gibt viele Leute, die AM-Tools verwenden möchten, aber sie warten darauf, dass jemand diese Probleme löst.“
Angesichts des Potenzials von AM zur Reduzierung von Werkzeugkosten und Vorlaufzeiten hat die Branche erhebliche Anstrengungen unternommen, um Erweiterungsprobleme durch die Erforschung neuer druckbarer Materialien, Modifikationen der Druckerhardware und innovativer Modellierungsansätze anzugehen. Einige Gruppen haben beispielsweise einen „Kompensationswert“ für die Entwicklung von AM-Tools entwickelt, um CLTE-Unterschiede zu beheben. Huelskamp merkt jedoch an, dass die Bestimmung welche Der zu verwendende Kompensationswert ist schwierig und fehleranfällig. Außerdem waren solche Ansätze bei Werkzeugen mit weiblicher Kavität und Werkzeugen mit Einfangmerkmalen entlang ihrer Länge, die Formverriegelungsbedingungen erzeugen, die Teile während der thermischen Zyklen im Werkzeug beschädigen können, wirkungslos.
„Es gibt keinen Kompensationsfaktor, der diese Art von Problem lösen würde“, fügt er hinzu. „Bisher hat keine AM-Tooling-Studie den Bedarf an niedrigen isotropen CTE-Werten bei erhöhter Temperatur vollständig berücksichtigt. Ohne diese Eigenschaft sind Werkzeuggrößen und -geometrien immer begrenzt, und größere Werkzeuge werden bei Härtungstemperaturen unter größeren Maßfehlern leiden.“
Um neue Ansätze zur Lösung von LFAM-Werkzeugherausforderungen auszuprobieren, wurde ein 18-monatiges Projekt von mehreren Mitgliedsunternehmen unter der Schirmherrschaft des Institute for Advanced Composites Manufacturing Innovation (IACMI, Knoxville, Tennessee, USA) durchgeführt und von den USA unterstützt Department of Energy and JobsOhio (Columbus, Ohio). Das Team wurde von UDRI geleitet und umfasste Airbus und Northrop Grumman. Diese Organisationen hatten zuvor sowohl innerhalb als auch außerhalb der IACMI an anderen Forschungsarbeiten zusammengearbeitet und waren daher mit den Fähigkeiten der anderen vertraut.
„Brute-Force“-Ansatz
UDRI verfügte bereits über beträchtliche Erfahrung mit Studien zu AM-Werkzeugen und ist aktives Mitglied von America Makes (Youngstown, Ohio, USA), dem US-amerikanischen AM-Konsortium. Darüber hinaus hat das Institut für die US-Luftwaffe Forschung zu AM-Strukturen mit metallischen Trägern durchgeführt und mit Cincinnati Inc. (Harrison, Ohio, USA), Hersteller von Big Area Additive Manufacturing (BAAM)-Druckern, an reinen AM-Werkzeugen zusammengearbeitet.
„Wir hatten auch mit kundenspezifischen Compoundern an neuen Rohstoffen für 3D-Drucker gearbeitet, aber nichts, was wir taten, schien große Fortschritte zu machen, und wir wussten nicht, dass jemand mehr Erfolg hatte als wir“, erinnert sich Huelskamp. „Da kam uns die Idee, das Problem anders anzugehen. Wenn wir das Verhalten von AM-Materialien nicht ändern oder dieses Verhalten direkt vorhersagen könnten , dann könnten wir sie vielleicht zwingen, sich indirekt so zu verhalten, wie wir es wollten .“ Unter Anwendung eines von Huelskamp als „Brute-Force“-Ansatz bezeichneten Ansatzes schlug UDRI eine hybride LFAM-Studie vor, die unter Anwendung von herkömmlichen . Flugzeugstrukturwerkzeugen produzieren würde CFK-Gesichtshäute zu Thermoplast-Verbund AM-Kerne.
Die Ziele des Projekts waren einfach:eine kostengünstigere und schnellere Methode zur Herstellung großer Werkzeuge für Flugzeugstrukturen zu finden. Das Team suchte nach einer Option, die die Kosten um 50 % senkte und mindestens 10 akzeptable Prototypen- oder Kleinserienteile für spätere Tests produzierte
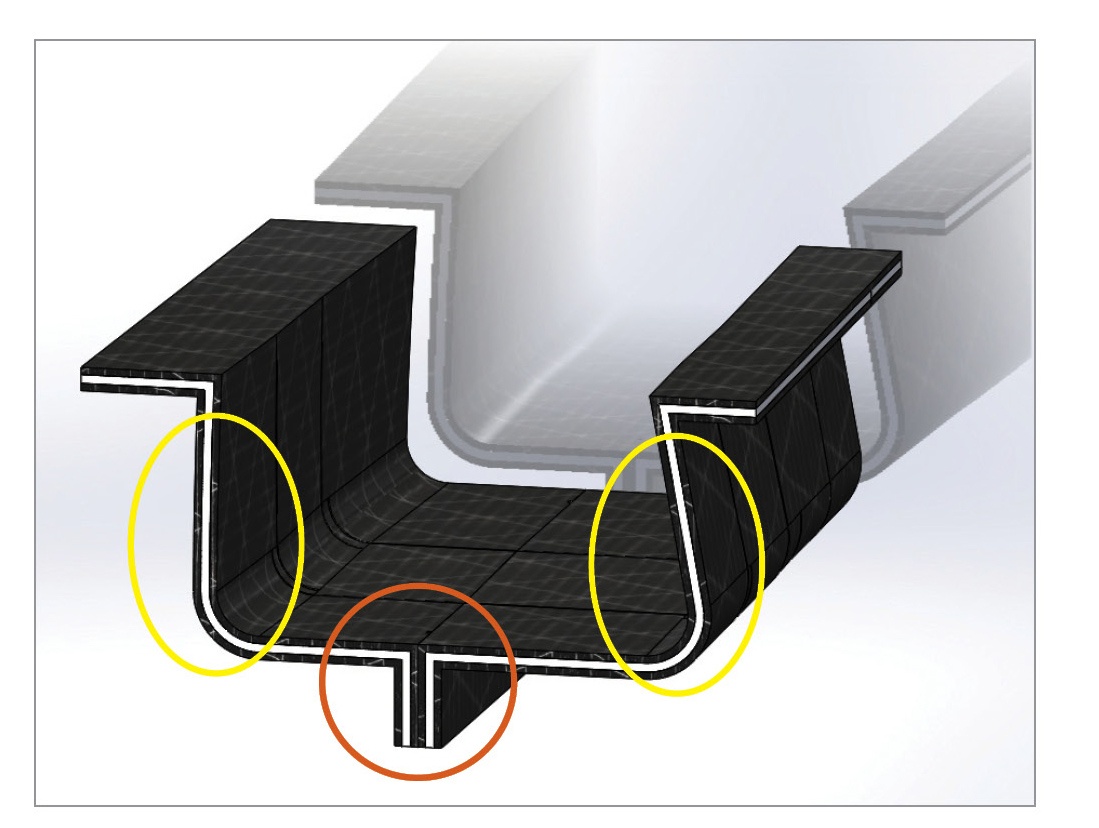
Das Team entschied sich, eine Sandwichstruktur zu verwenden, um einseitige Werkzeuge für einen Abschnitt eines generischen Flügelholms mit Werkzeugdaten von Airbus herzustellen. Abgesehen von der Herstellung von Werkzeugen, um nur einen Abschnitt des C-Holms in Originalgröße zu formen – aufgrund von Platzbeschränkungen in der UDRI-Anlage – wurden keine größeren Designänderungen vorgenommen.
Eine Matrize wurde entwickelt, um sicherzustellen, dass kritische Teilegeometrien mit hart bearbeiteten Oberflächen geformt werden. Dieses Holmkappenwerkzeug hatte einen leichten Einwärtswinkel, der eine negative Formschräge und einen Zustand der Formverriegelung erzeugte, da es sich um ein einteiliges Werkzeug handelte. Dies führte dazu, dass die Forscher das Design zu einem geteilten Werkzeug modifizierten, das mit Dichtungen/Cordmaterial abgedichtet wurde. Um das Risiko zu mindern, begann das Team mit einem 0,6-Meter/2,0-Fuß-Subskalen-Tool, um das Konzept zu beweisen. Nachdem der Werkzeugentwicklungsprozess und die mit diesem Werkzeug hergestellten Prototypenteile getestet und für funktionsfähig befunden worden waren, baute das Team ein größeres, 3,3 Meter langes Werkzeug, um einen größeren Abschnitt des Holms für Prototypentests zu formen.
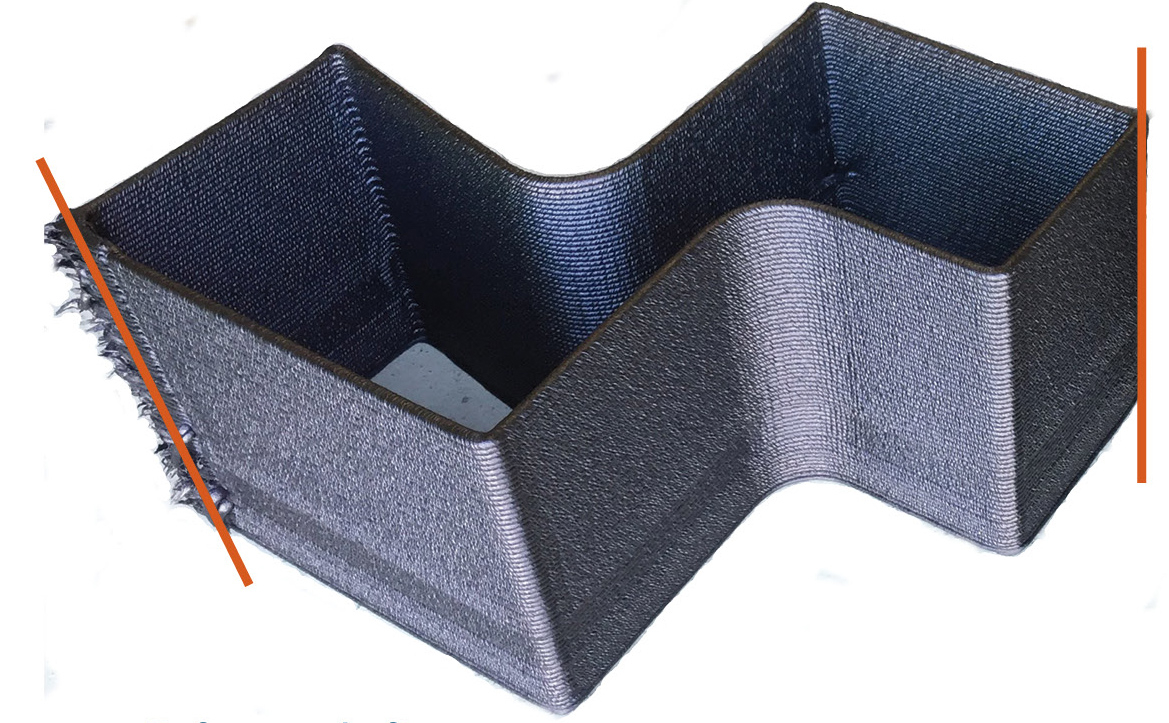
Da CFK-Werkzeuge einen so niedrigen CLTE-Wert aufweisen, leichter als Invar sind und das Werkzeug für Prototypen-/Kleinserienteile gedacht war, entschied sich das Team, CFK-Deckschalen zu verwenden, um den AM-Kern einzuschränken. Die Häute wurden mit Hextool M81 Epoxy Tooling Prepreg von Hexcel (Corp., Stamford, Connecticut, USA) hergestellt.
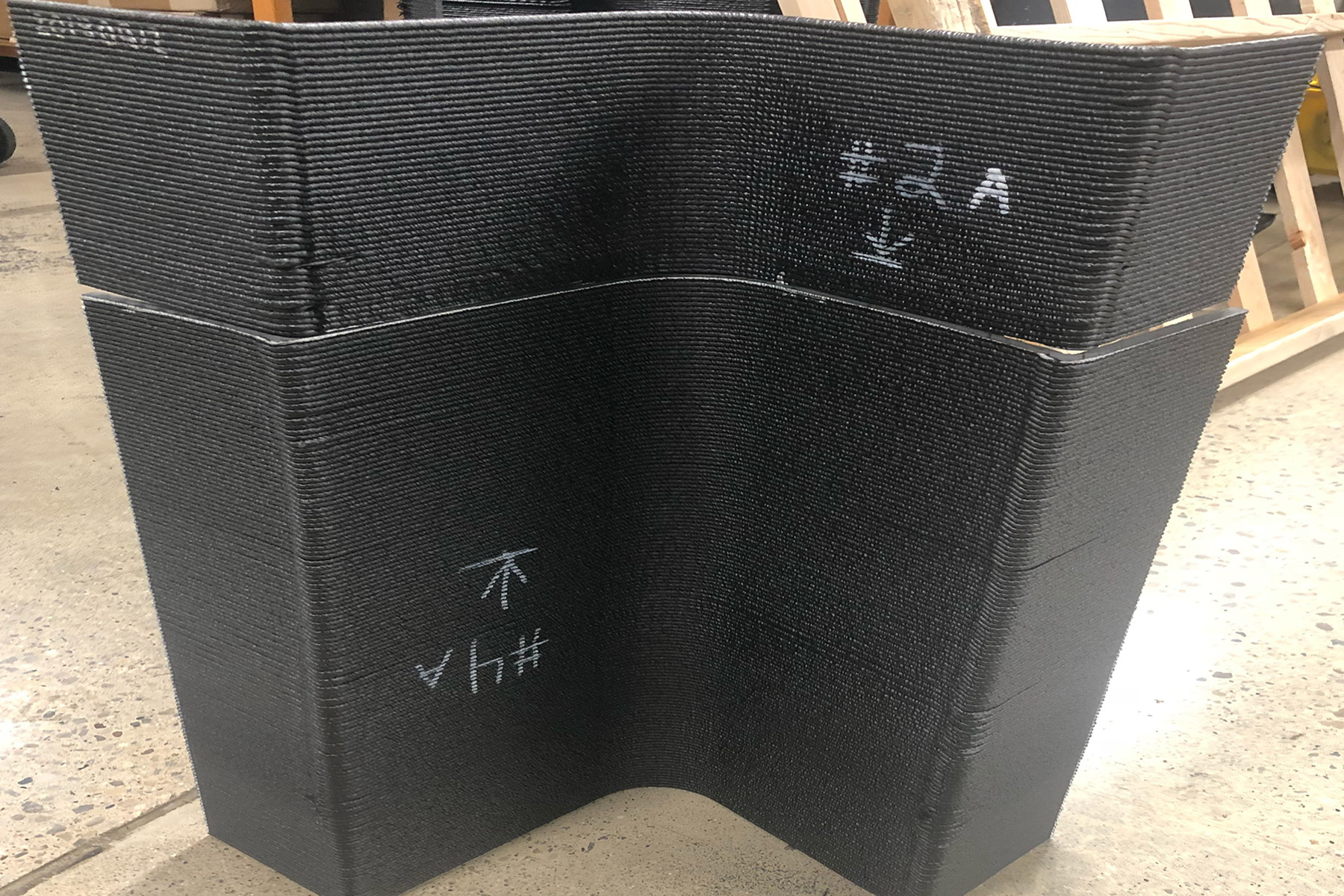
Das obere Bild zeigt einen Ausschnitt der rechten Hälfte des Subscale, BAAM-gedruckten Werkzeugs mit roten Linien, die Schnittlinien nach dem Drucken kennzeichnen. Das untere Bild zeigt die rechte Werkzeughälfte, nachdem die Abschnitte miteinander verbunden wurden. Bildnachweis:University of Dayton Research Institute.
Das Materialformat war eine 2.000-Gramm-pro-Quadratmeter/59-Unzen-pro-Quadratyard-Matte aus gehackter Kohlefaser, die mit Hexcels 8552 gehärtetem Epoxid imprägniert war. Dieses Material wird aufgrund seiner nahezu isotropen Eigenschaften häufig für Verbundwerkzeuge verwendet, die eine Nachbearbeitung ohne Werkzeugbewegungen ermöglichen, die ansonsten durch Eigenspannungsrelaxation verursacht werden könnten.
Angesichts der Tatsache, dass der Kern auf einem BAAM 1000-Drucker von Cincinnati Inc. bei Additive Engineering Solutions (Akron, Ohio, USA) gedruckt werden würde und da UDRI und Cincinnati über beträchtliche Erfahrung bei der Arbeit mit dem thermoplastischen Hochtemperatur-Polyetherimid (PEI) verfügten, wählten sie 20 % kurzes kohlenstofffaserverstärktes PEI (Thermocomp EX004EXAR1 Ultem) von SABIC, (Riyadh, Saudi-Arabien) zum Drucken eines endkonturnahen Kerns. (Das Vorhandensein von Kohlefasern stabilisiert das Polymer während des Drucks und verhindert ein Absacken; in der fertigen Struktur reduzieren die Fasern CLTE in Druckrichtung.) Um die Kosten niedrig zu halten, wurde der Kern als Werkzeugmaster und Deckschichten direkt laminiert zum Kern ohne Klebstoff, aber mit einigen Modifikationen an der Kernoberfläche, die unter während des Projekts entwickeltes geistiges Eigentum (IP) fallen. Dieser Ansatz war effektiv, auch nach mehreren thermischen Zyklen gab es keine Delamination.
Kondensierte Herstellung
Bei der konventionellen Fertigung von Flugzeugstruktur-CFK-Werkzeugen wird zunächst ein kostengünstiger Master erstellt. Dies beinhaltet normalerweise das Zusammenkleben von Werkzeugplattenblöcken in einem Ofen oder Autoklaven und das anschließende Bearbeiten der monolithischen Struktur auf die gewünschte Teilegeometrie. Das Werkzeugmaterial wird dann aufgelegt, verpackt und auf dem Master in einem Autoklaven ausgehärtet. Nach der Entformung und Reinigung wird eine Trägerstruktur mit dem Werkzeug verbunden und die Werkzeugoberfläche wird erneut bearbeitet, um eine gute geometrische Toleranz und Oberflächengüte zu gewährleisten.
Mit hybriden AM-Werkzeugen entwickelte das Team einen komprimierten Fertigungsprozess, um Durchlaufzeiten und Kosten zu reduzieren. Zunächst wurde ein endkonturnaher Kern (Toolmaster) 3D-gedruckt (in Kurzkohlefaser/PEI). Als nächstes wurde CFK-Werkzeug-Prepreg direkt auf beide Seiten des Kerns laminiert (mit heißen Debulks zwischen den Lagen eins, vier und sieben gemäß den Empfehlungen des Lieferanten). Die gesamte Struktur wurde dann vakuumverpackt und autoklaviert.
Kondensierter Herstellungsprozess für C-Holm-Werkzeug im Untermaßstab.
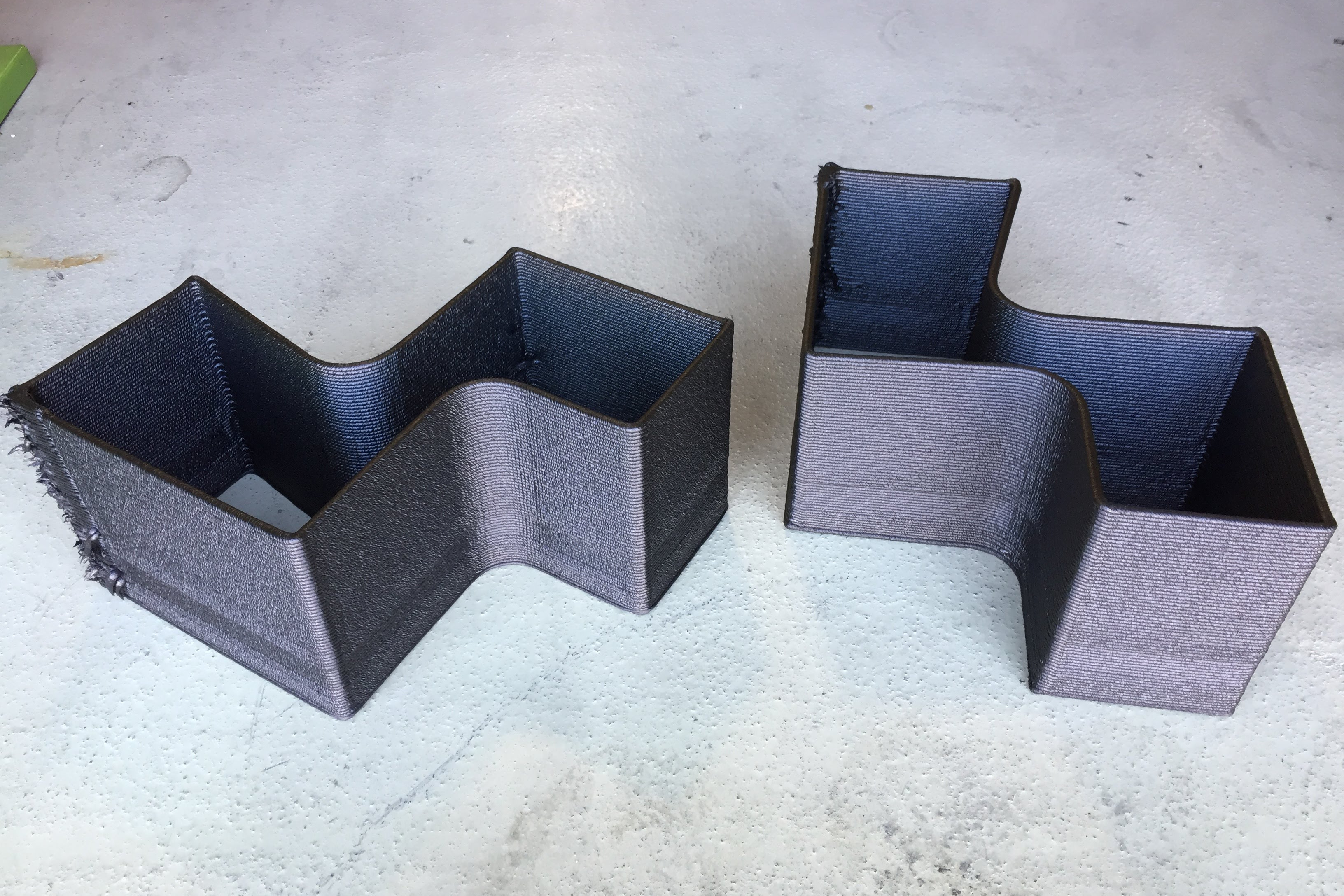
Schritt 2:Schneiden Sie den BAAM-Druck in der Mitte und in die linke und rechte Hälfte.
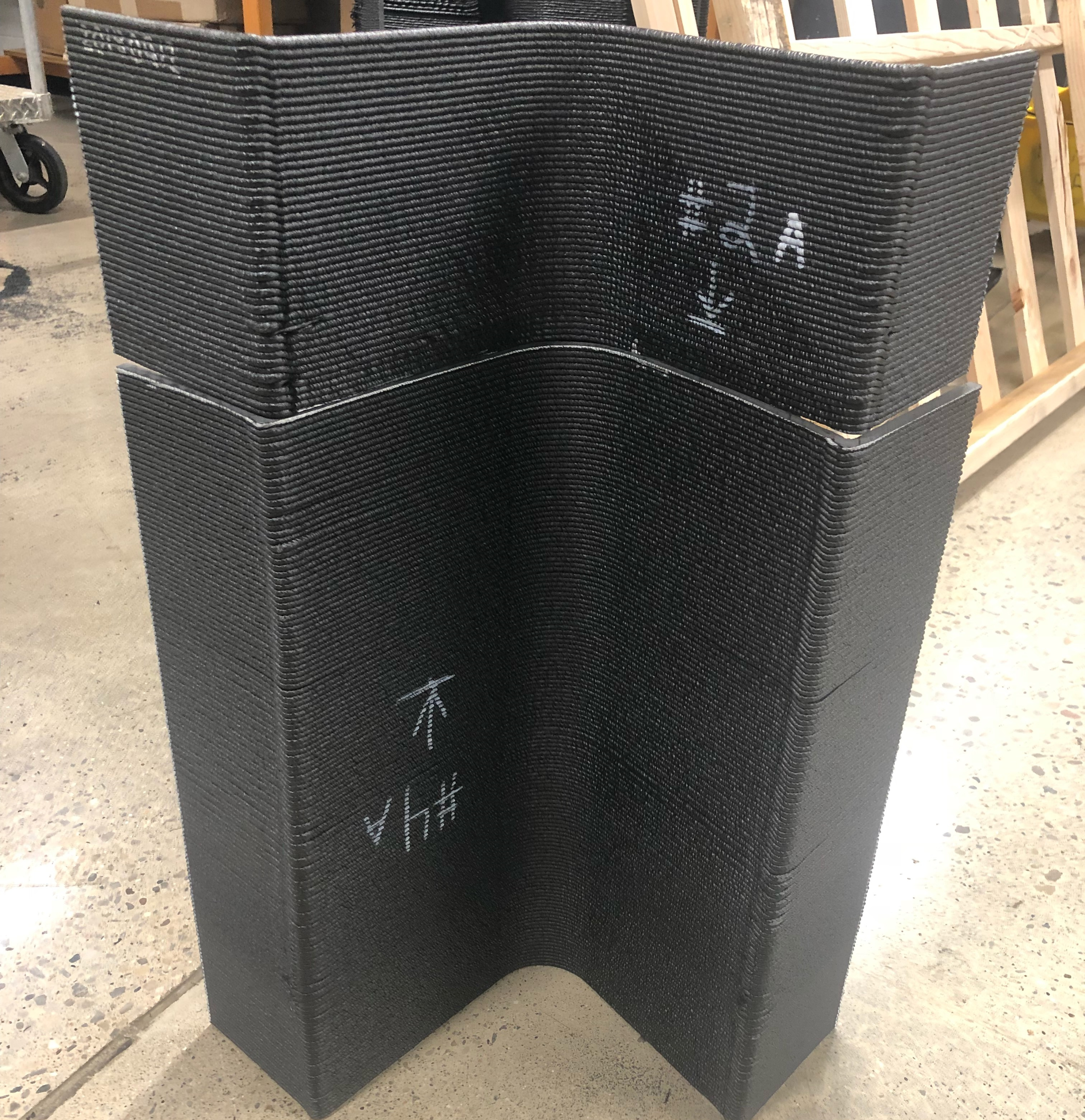
Schritt 3:BAAM-Druck aufkleben, um die gewünschte Länge zu erreichen und aushärten lassen.
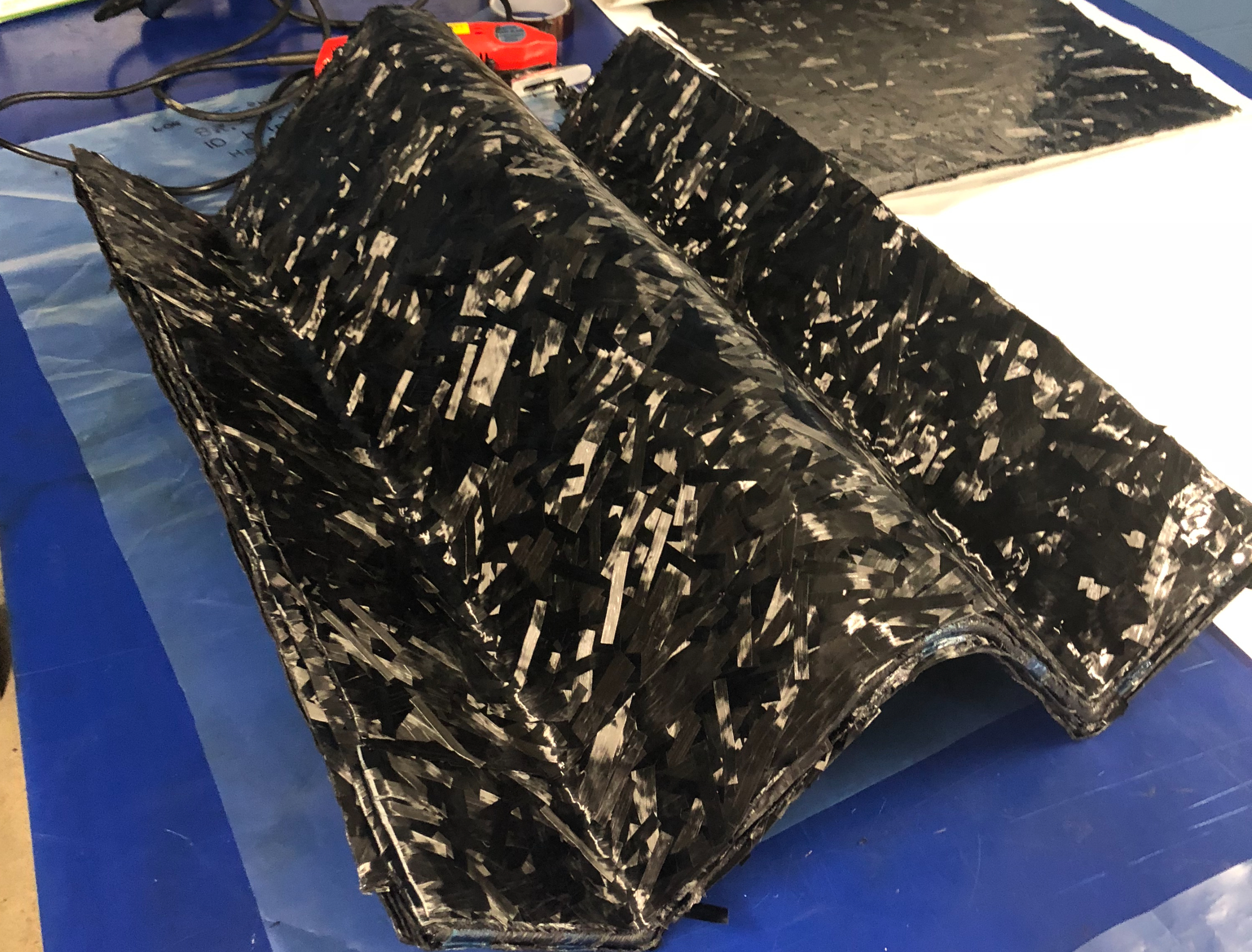
Schritt 4:Laminieren Sie das Werkzeug-Prepreg mit heißen Debulks gemäß den Anweisungen des Herstellers auf beide Seiten des Kerns.
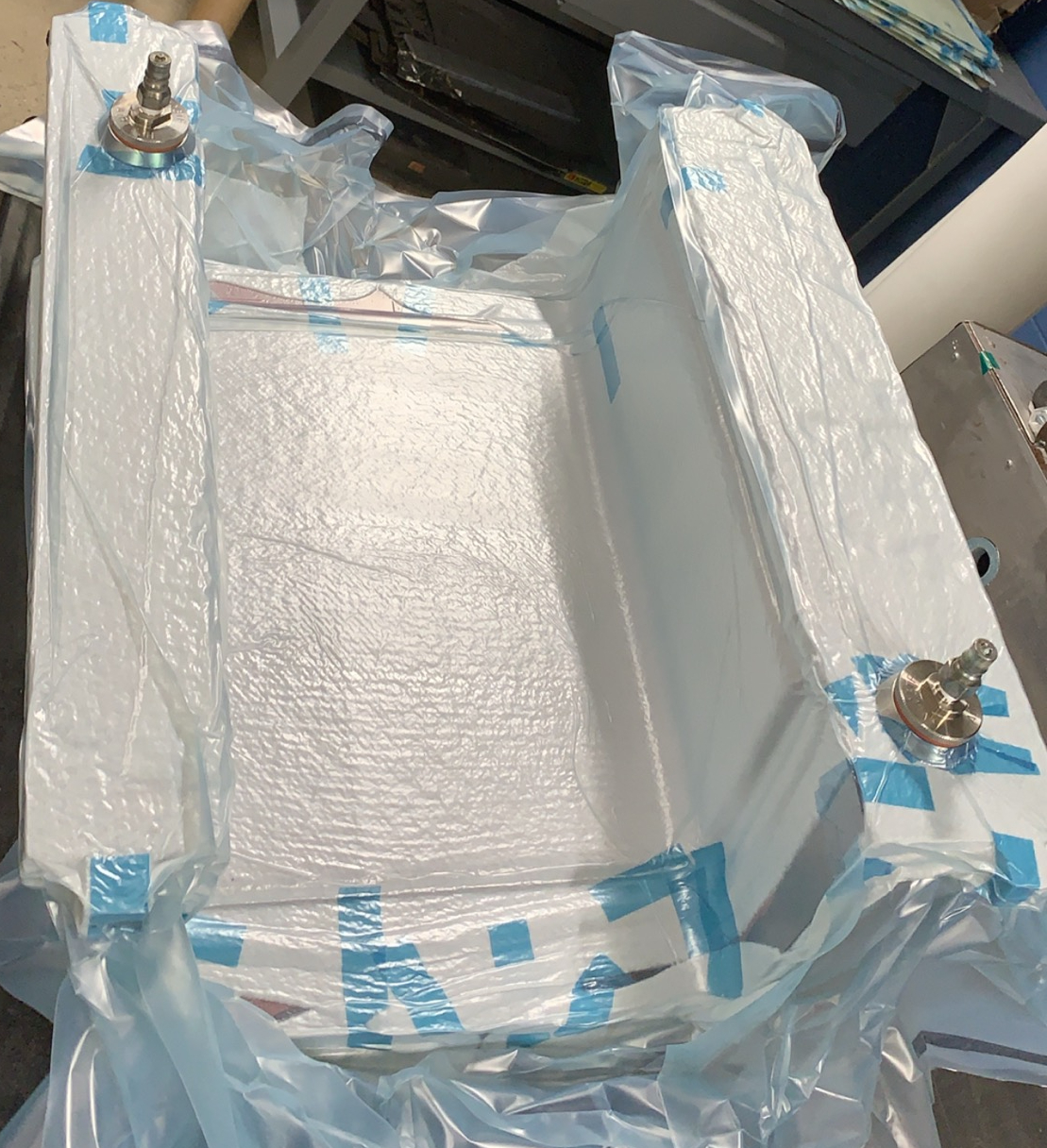
Schritt 5:Beutel vakuumieren und im Autoklaven aushärten.
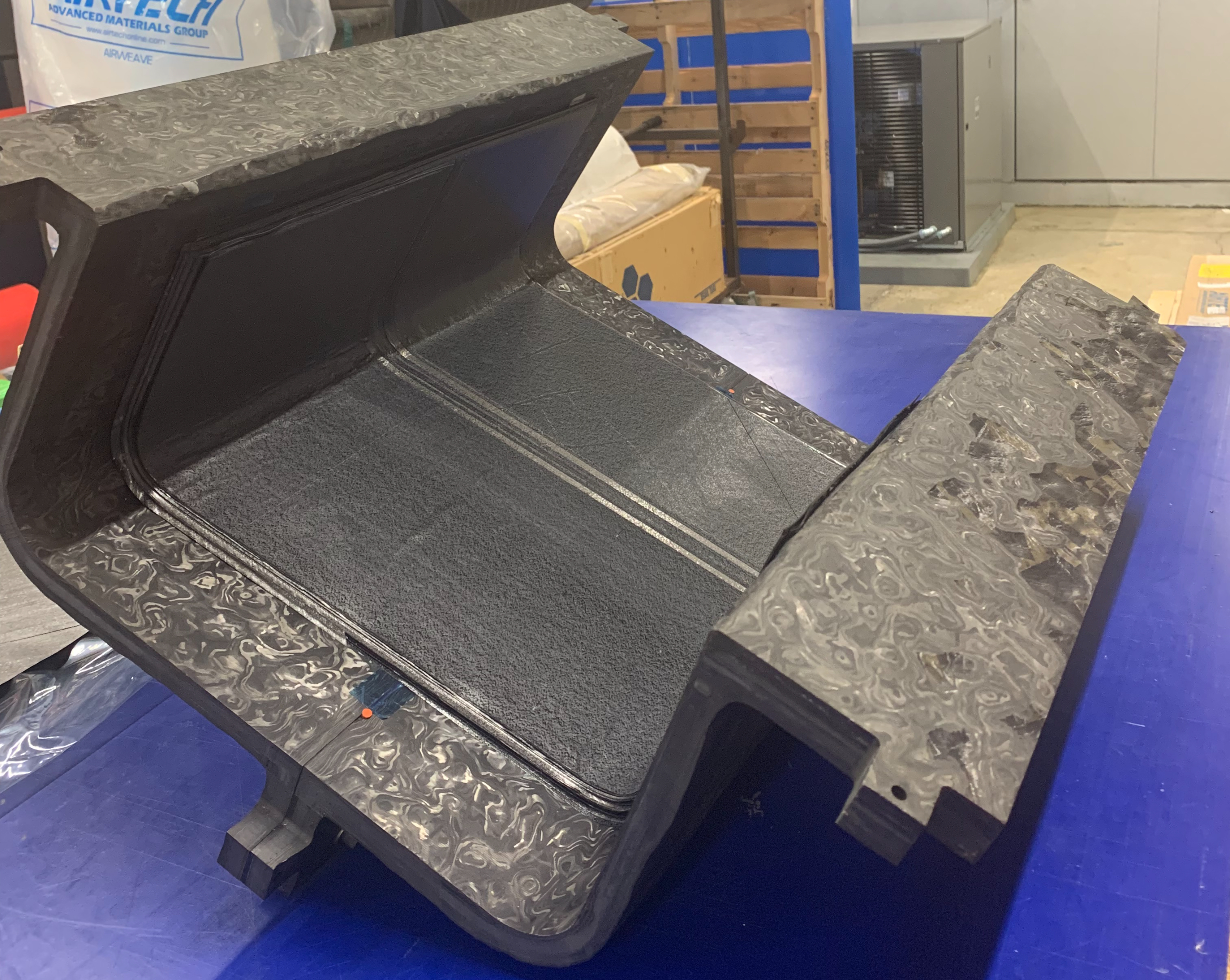
Schritt 6:Maschinengehärtetes Werkzeug, um die endgültigen Abmessungen und die Oberflächengüte zu erreichen.
Vorherige NächsteWährend der Laminathärtung wurde eine gute Haftung zwischen dem PEI-Kern und den Epoxidhäuten erreicht, sodass kein Klebstoff erforderlich war. Die CFK-Häute sind nicht nur porenfrei und haltbarer als der AM-Kern, sie schränken aufgrund ihrer viel niedrigeren CLTE-Werte auch die Bewegung des Kerns bei Temperaturschwankungen physikalisch ein. Nur eine einzige Aushärtung und ein einziger Bearbeitungsvorgang – beides große Kosten bei der traditionellen Werkzeugherstellung — wurden benötigt, um Endmaße und Oberflächengüte zu erreichen. Außerdem war aufgrund der Sandwichstruktur und Werkzeugform, die Rücklaufflansche an der Oberseite der Form für seitliche Steifigkeit und eine Schraubverbindung in der Mitte der Form für vertikale Steifigkeit umfasste, keine Unterlage erforderlich, wodurch ein Klebevorgang überflüssig wurde.
Erste Herausforderungen
Die Forscher standen bei dem neuen Verfahren vor mehreren überschaubaren Herausforderungen.
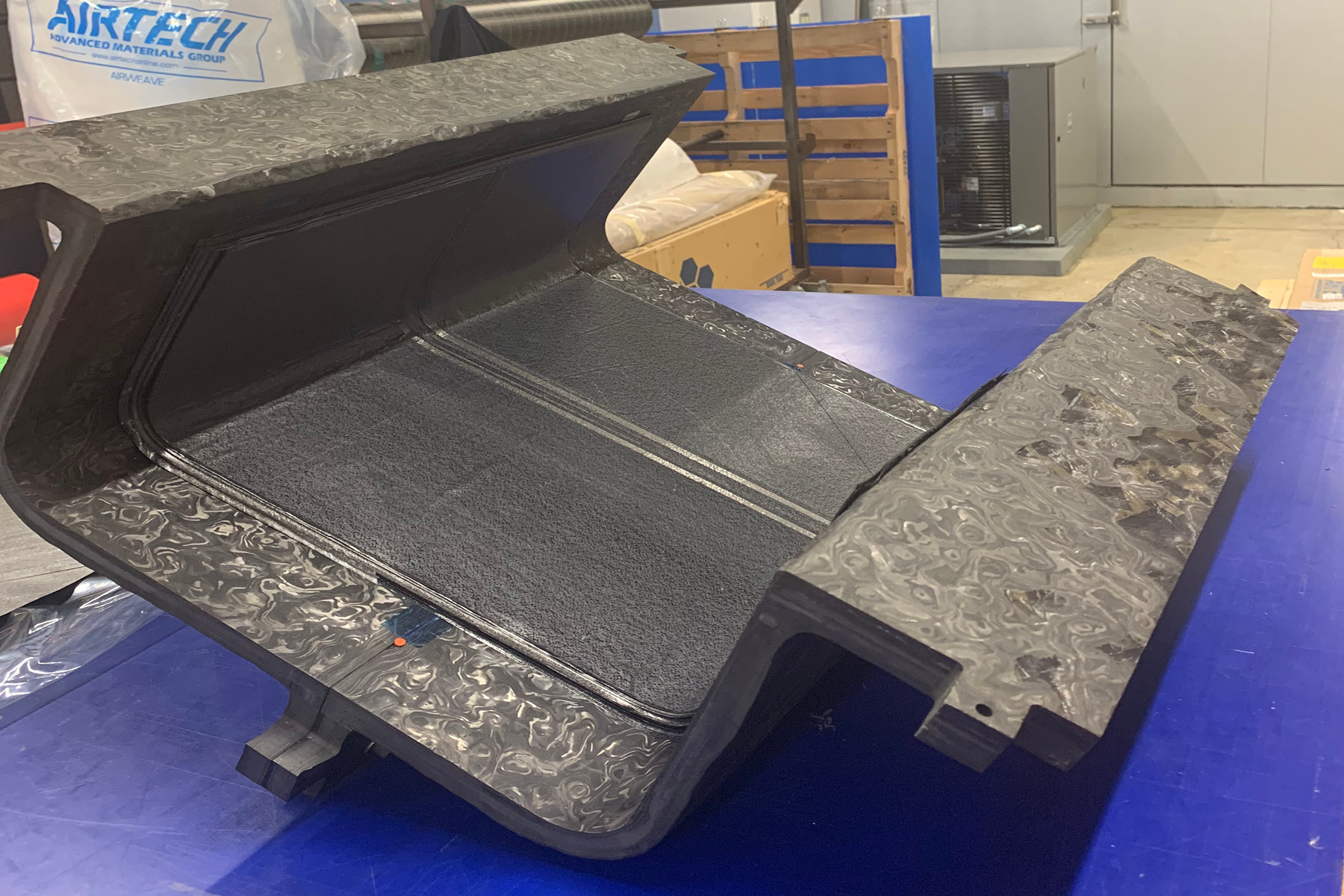
Um die Herstellung auf dem BAAM zu vereinfachen, war die bevorzugte Herstellungsrichtung für den Kern das Drucken des Querschnitts als vertikaler Aufbau. Für das 0,6-Meter-Gerät war das kein Problem; Das größere Werkzeug war jedoch mit 3,3 Metern höher, als der BAAM 1000 vertikal drucken konnte. Aufgrund der Z-Achsen-Druckraumbeschränkungen des Druckers entschieden sich die Forscher, beide Subscale-Werkzeuge entlang ihrer Länge zu halbieren und sie dann wieder in einen linken und einen rechten Abschnitt aufzuteilen (um Probleme mit der Holmkappenhinterschneidung zu beheben und das Entformen zu erleichtern).
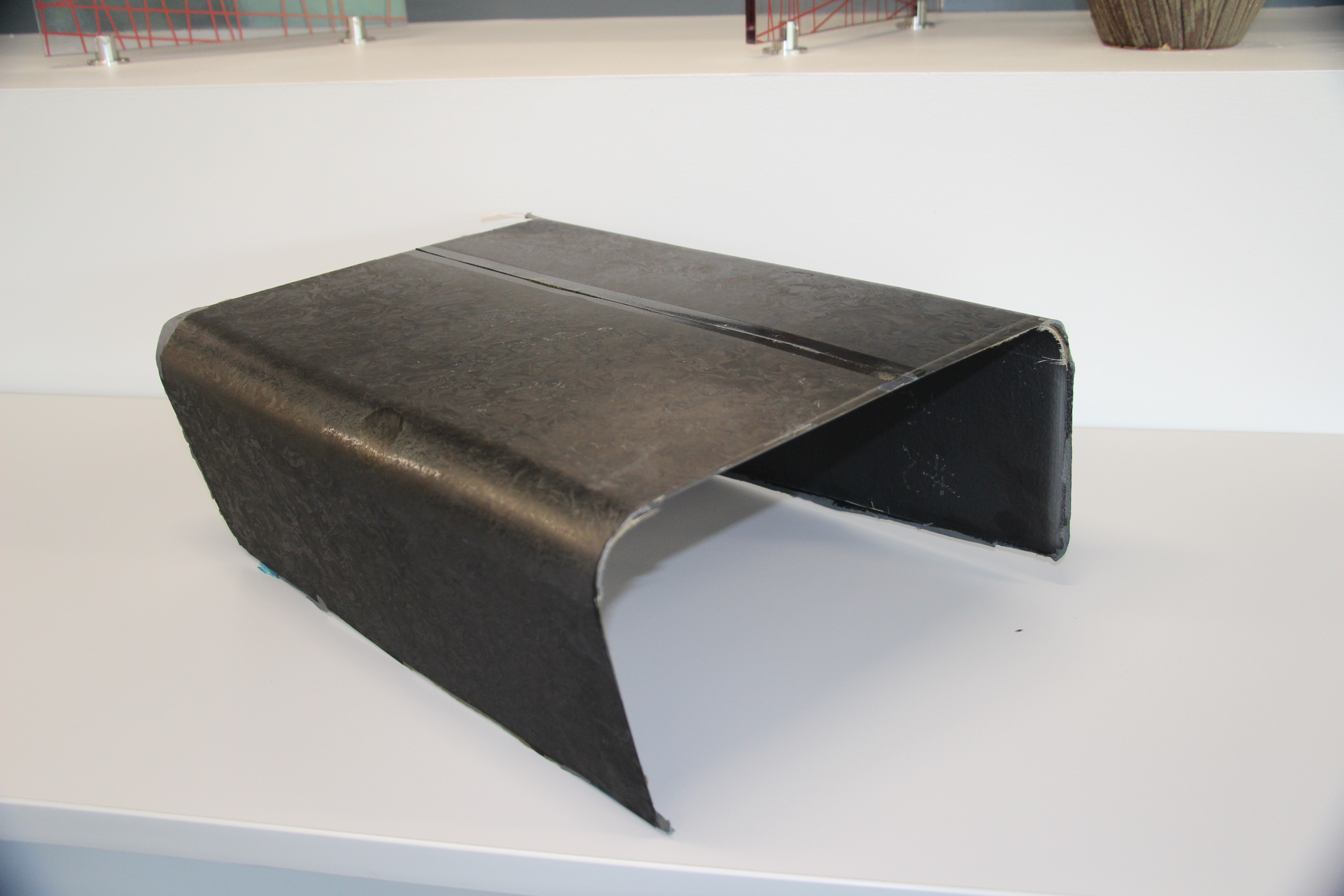
Um die Druckeffizienz zu erhöhen, wurden Werkzeugabschnitte Rücken an Rücken gedruckt und dann in rechte und linke Teile geschnitten. Um die Länge von 3,3 Metern zu erreichen, wurden die beiden rechten Abschnitte miteinander verbunden, gefolgt von den beiden linken Abschnitten mit dem Epoxidklebstoff Loctite EA9394 von Henkel Corp. (Rocky Hill, Connecticut, USA). Das Team ließ den AM-Kern unbearbeitet und war der Meinung, dass dies entscheidend war, um niedrige Werkzeugkosten und kurze Durchlaufzeiten zu erzielen sowie eine mechanische Verriegelung zwischen dem AM-Kern und den CFK-Hüllen auf jeder Seite herzustellen. Die Rückseite jeder Werkzeughälfte wurde mit fünf Lagen Prepreg laminiert, während die Vorderseite mit neun Lagen laminiert wurde, um zusätzliches Material bereitzustellen, das während der Nachhärtungsbearbeitung entfernt werden konnte.
Vorläufige Ergebnisse
Zusätzlich zur Kontrolle des CLTE des AM-Kerns bot das Prepreg eine grubenfreie Oberfläche, die die Vakuumintegrität ohne Versiegelung/Beschichtung beibehielt. Dieser Ansatz war so erfolgreich, dass er die Verwendung eines mehrteiligen Werkzeugdesigns ermöglichte, das mit einer Dichtung abgedichtet ist, was nach Ansicht der Forscher zuvor bei AM-Werkzeugen, die bei hohen Temperaturen verwendet werden, nicht nachgewiesen wurde. Außerdem wurde die Werkzeugmasse deutlich reduziert; das Subscale-Tool wies ein Drittel des Gewichts auf, das für ein vergleichbares Invar-Design berechnet wurde. Leichtere CFK-Werkzeuge sind nicht nur einfacher zu handhaben und auf Gestellen zu lagern, sondern erfordern auch kürzere Aufheiz-/Abkühlzyklen im Autoklaven. Bei einem Werkzeug zum Formen des C-Holms in Originalgröße könnte dieser Gewichtsvorteil in einigen Fertigungsbereichen den Unterschied ausmachen, ob die Gewichtsgrenzen für Portal/Kran unter- oder überschritten werden.
Wichtig ist, dass die Kosten für das 0,6-Meter-Hybridwerkzeug während der Herstellung mit branchenüblichen Arbeitssätzen auf 24.136 USD berechnet wurden, wobei sich die Bearbeitungskosten und die Druck-/Laminierkosten ungefähr 50/50 aufteilten. Im Gegensatz dazu wurde ein identisches Invar-Tool mit 46.775 USD angegeben – eine Ersparnis von fast 50 %. Die Kosten für das 3,3-Meter-Werkzeug sind nicht vollständig, aber es wird erwartet, dass sie auf Kosten-/Einheitslängenbasis etwa 30 % einsparen, da die Material-/Druckkosten linear skalieren, die Bearbeitungskosten jedoch einen Skaleneffekt haben, der ihre Auswirkungen reduziert. Der hybride Ansatz führte zu Werkzeugen, die die betrieblichen Leistungsanforderungen von Airbus und Northrop Grumman erfüllten und als praktikable Alternative zu Invar für Rapid-Prototyp- oder Low-Use-Werkzeuge gelten. Die Untersuchung der Werkzeugstandzeit war nicht Teil dieser Studie, würde aber wahrscheinlich deutlich über die 12 nachgewiesenen Zyklen hinausgehen.
Das Programm wurde von 18 auf 30 Monate verlängert, aber es gibt immer noch Bereiche, in denen weitere Untersuchungen erforderlich sind, wie zum Beispiel das Verständnis, wie sich die endgültige Geometrie des gedruckten Kerns von der in CAE-Modellen vorhergesagten unterscheidet. Das Team möchte auch die Vorhersagegenauigkeit verbessern, damit in kritischen Bereichen genügend Lagen hinzugefügt werden, um sicherzustellen, dass es während der Bearbeitung nicht zu Durchschlägen kommt. Dennoch betrachtete das Team dies als erfolgreiches Projekt mit beträchtlichen Möglichkeiten für zukünftige LFAM-Werkzeuge.
„Northrop Grumman freut sich darauf, ein 3 Meter langes Holm-Demonstrationsteil mit dem 3,3 Meter langen Hybridwerkzeug von UDRI und unserem eigenen automatisierten Versteifungsformungsprozess (ASF) zu bauen, um die Haltbarkeit und Dimensionsstabilität des Werkzeugs zu bewerten“, fügte hinzu Vern Benson, technischer Mitarbeiter von Northrop Grumman.
Harz
- Evonik entwickelt additive Lösungen zur Entwicklung von 3D-Druckmaterialien für den STEP-Prozess
- Henkel bietet Werkstoffplattform für die additive Fertigung
- Essentium und Lehvoss kooperieren bei der Entwicklung von Materialien für die additive Fertigung
- Neuartiges hitzestabilisiertes Nylon 6 für Hybrid- und Elektroantriebe
- Trelleborg gibt neuen Distributor für Werkzeugmaterialien an
- UAMMI, Impossible Objects bauen Verbundteile für die US Air Force
- Victrex- und Bond-Partner für den 3D-Druck von PAEK-Teilen
- AeroLas erforscht neue Spinntechnologie für thermoplastisches Hybridgarn
- Tipps für 3D-Druckformen
- Minimierung der Durchlaufzeiten für große Teile