Composites 4.0:Digitale Transformation, adaptive Produktion, neue Paradigmen
Composites 4.0 ist eine kleine Galaxie im Universum von Industrie 4.0, der digitalen Transformation, wie Waren und Dienstleistungen entworfen, produziert, geliefert, betrieben, gewartet und außer Betrieb genommen werden. Bei der Herstellung von Verbundwerkstoffen besteht das Ziel darin, Automatisierung, Sensoren und Daten, 5G-Kommunikation, Software und andere sich ständig weiterentwickelnde digitale Technologien zu nutzen, um Produkte und Prozesse effizienter, intelligenter und anpassungsfähiger zu machen.
Die Hersteller von Verbundwerkstoffen durchlaufen diese digitale Transformation entlang eines Spektrums. Zu den ersten Schritten gehören Inline-Inspektion und optimierte Prozesse, die Ausschuss und Kosten reduzieren und gleichzeitig die Teilequalität und den Ertrag steigern. Fortschrittlichere Lösungen arbeiten an einer intelligenten, autonomen Produktion, die nicht nur agil ist, sondern auf sie reagiert und sogar vorausschaut sich ändernde Märkte und Kundenanforderungen.
„Composite 4.0 ist kein Zweck, sondern ein Werkzeug“, erklärt Dr. Michael Emonts, Geschäftsführer des AZL Aachen Center for Integrative Lightweight Production an der RWTH Aachen (Aachen), dessen iComposite 4.0-Projekt eine adaptive Prozesskette mit Potenzial, die Kosten für Fahrzeugbodenbleche um 50–64 % zu senken.
„Es gibt einen Unterschied zwischen der reinen Digitalisierung und der digitalen Transformation, die tatsächlich die Prozesse hinter Ihrem Geschäft verändert und neue Möglichkeiten und Geschäftsmodelle eröffnet“, sagt Christian Koppenberg, Geschäftsführer des Composite-Teile-Herstellers Dynexa (Laudenbach, Deutschland).
„Composites 4.0 setzt nicht nur Roboter ein“, sagt Dr. Michael Kupke, Leiter des Zentrums für Leichtbauproduktionstechnik (ZLP, Augsburg) des Deutschen Zentrums für Luft- und Raumfahrt (DLR), das eine mit künstlicher Intelligenz [KI] ausgestattete Arbeitszelle entwickelt hat wo kollaborative Roboter ohne Umprogrammierung oder Umschulung von der Herstellung von hinteren Druckschotts aus Verbundwerkstoff zu Rumpfpaneelen wechseln können. „Es ist die Technologie, die dafür sorgt, dass Sie den Robotern nicht beibringen müssen, denn dafür gibt es keinen Business Case. Composites 4.0 ist mehr als nur Effizienzsteigerung und Kostensenkung. Es ist eine Veränderung in der Art und Weise, wie Unternehmen über die Produktion denken und sie herangehen, die bestimmen wird, welche Unternehmen überleben und welche nicht.“
Adaptive Preforming, RTM
„Die Idee des iComposite 4.0-Projekts bestand darin, Preforms aus kostengünstigen Rovings und Tows herzustellen, indem trockene, lange Glasfasern (25-30 Millimeter) gespritzt und anschließend über eine automatisierte Faserplatzierung mit einem Gitter aus unidirektionalen (UD) Carbonfasern verstärkt werden (AFP)“, erklärt Emonts. „Der gewählte Demonstrator, eine Heckpartie unter dem Fahrzeugboden, wurde zuvor aus teureren Textilien hergestellt, die auch mehr als 60 % Abfall produzierten.“
Die Transformation von Composites 4.0 erforderte die Integration der Prozesse Faserspritzen, Faserabscheidung und anschließendes Resin Transfer Moulding (RTM), damit sie aufeinander reagierten und sich an die zwischen den Schritten gemessene Teilequalität anpassten (Abb. 1). „Wir haben ein Bildverarbeitungssystem der Apodius GmbH [Aachen] mit optischem Lasersensor und Kameramodul verwendet, um die Oberflächentopologie des gespritzten Preforms zu charakterisieren“, sagt Emonts. „Apodius hat die Software angepasst, um den Faseranteil in jeder Richtung zu analysieren. Die iComposite 4.0-Reihe verglich dies mit dem digitalen Design und entschied, ob es die mechanischen Anforderungen erfüllt. Wenn ja, wurde das Standard-UD-Gitter für die Bewehrung angewendet. Wenn nein, hat es entschieden, wo zusätzliche UD-Faserschichten platziert werden.“
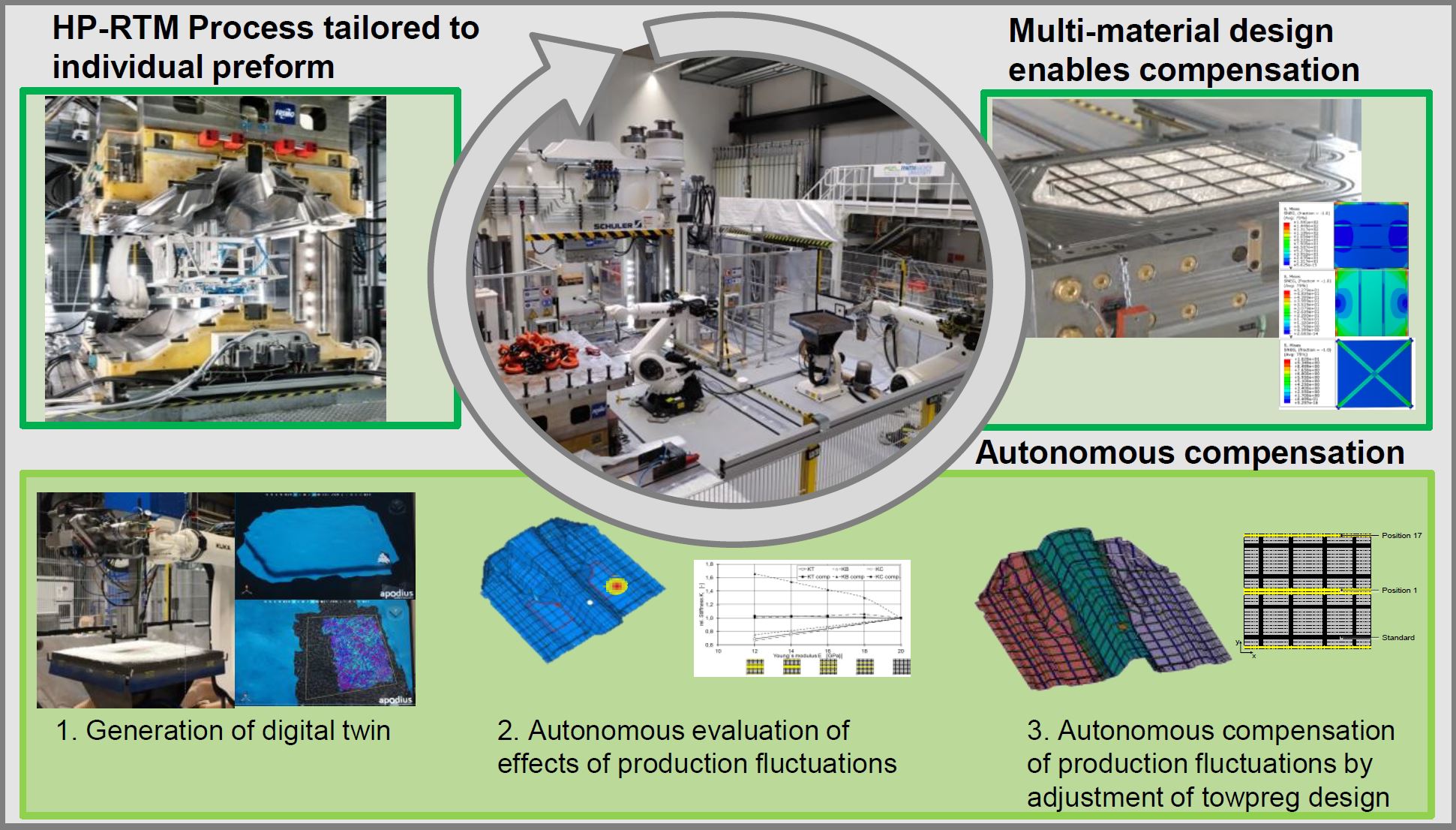
Diese zusätzlichen UD-Schichten können jedoch dazu führen, dass die Teiledicke und -geometrie die Toleranzen überschreitet. „Deshalb“, erklärt er, „kombinierten wir die Preforming-Linie mit einem adaptiven RTM-Verfahren, das bei Bedarf die Teiledicke durch Erhöhung des Drucks auf bestimmte Teile der Presse anpasste.“ Auch dies wurde automatisiert, um den Eingriff des Linienbedieners zu ersetzen, erforderte jedoch eine Simulation der Teileleistung mit Messdaten und Standard-FEA-Software.
„Derzeit wird die Simulation der mechanischen Eigenschaften des Teils offline durchgeführt“, sagt Emonts. „Wir haben eine Datenbank mit Prozess- und Teilevariationen erstellt, Algorithmen erstellt, um auf jede Variation zu reagieren, und diese über FEA validiert. Auf der Grundlage der von der Leitung gemessenen Variationen weisen die Algorithmen sie daher an, eine geeignete Abschwächung durchzuführen. Um die Linie in-situ adaptiv zu machen, wäre der nächste Schritt das Hinzufügen von maschinellem Lernen.“ Inzwischen verfolgt AZL zahlreiche Composite 4.0-Projekte, darunter die selbstoptimierte Produktion von hybriden thermoplastischen Verbundwerkstoffen und Spritzgussteilen mit integrierter Versteifung von Tape-basierten Tailored Blanks.
Fehlerfreie CFK-Wingskins
Das ZAero-Projekt (siehe „Null-Fehler-Fertigung von Verbundbauteilen“) ist ein weiteres wichtiges Composites 4.0-Projekt, das 2016 gestartet wurde. Es zielte darauf ab, die Produktivität für große kohlenstofffaserverstärkte Kunststoff (CFK)-Strukturen wie Wingskins zu steigern. Defekte würden durch die Verwendung einer automatisierten Inline-Inspektion mit entweder Prepreg AFP oder Danobats (Elgoibar, Spanien) automatisierter Trockenmaterialplatzierung (ADMP, siehe „Nachweis der Lebensfähigkeit von Trockengeweben, Infusion für große Flugzeugstrukturen“) reduziert. Die Prozessüberwachung während der Harzinfusion oder der Prepreg-Härtung würde den Härtungszustand vorhersagen und die Zykluszeit verkürzen. Gesammelte Prozess- und Fehlerdaten wurden mit FEA verwendet, um die Teileleistung vorherzusagen. Dies wurde dann in ein Entscheidungsunterstützungstool eingegeben, um zu ermitteln, wie identifizierte Fehler behoben werden können. Es wurde eine Teilestromsimulation für CFK-Wingskins entwickelt, die, eingespeist in dieses Tool, zur Optimierung einer Nacharbeitsstrategie beiträgt (Bild 2). Heutzutage werden viele dieser Teile während der Fertigung nachbearbeitet, aber erst nach NDI. Frühere Nacharbeit und verbesserte Prozesskontrolle waren tatsächlich Ziele des ZAero-Projekts sowie Voraussetzungen für die angestrebte Produktionssteigerung um 15 %, die Reduzierung der Produktionsrate um 15-20 % Produktionskosten und 50% weniger Abfall.
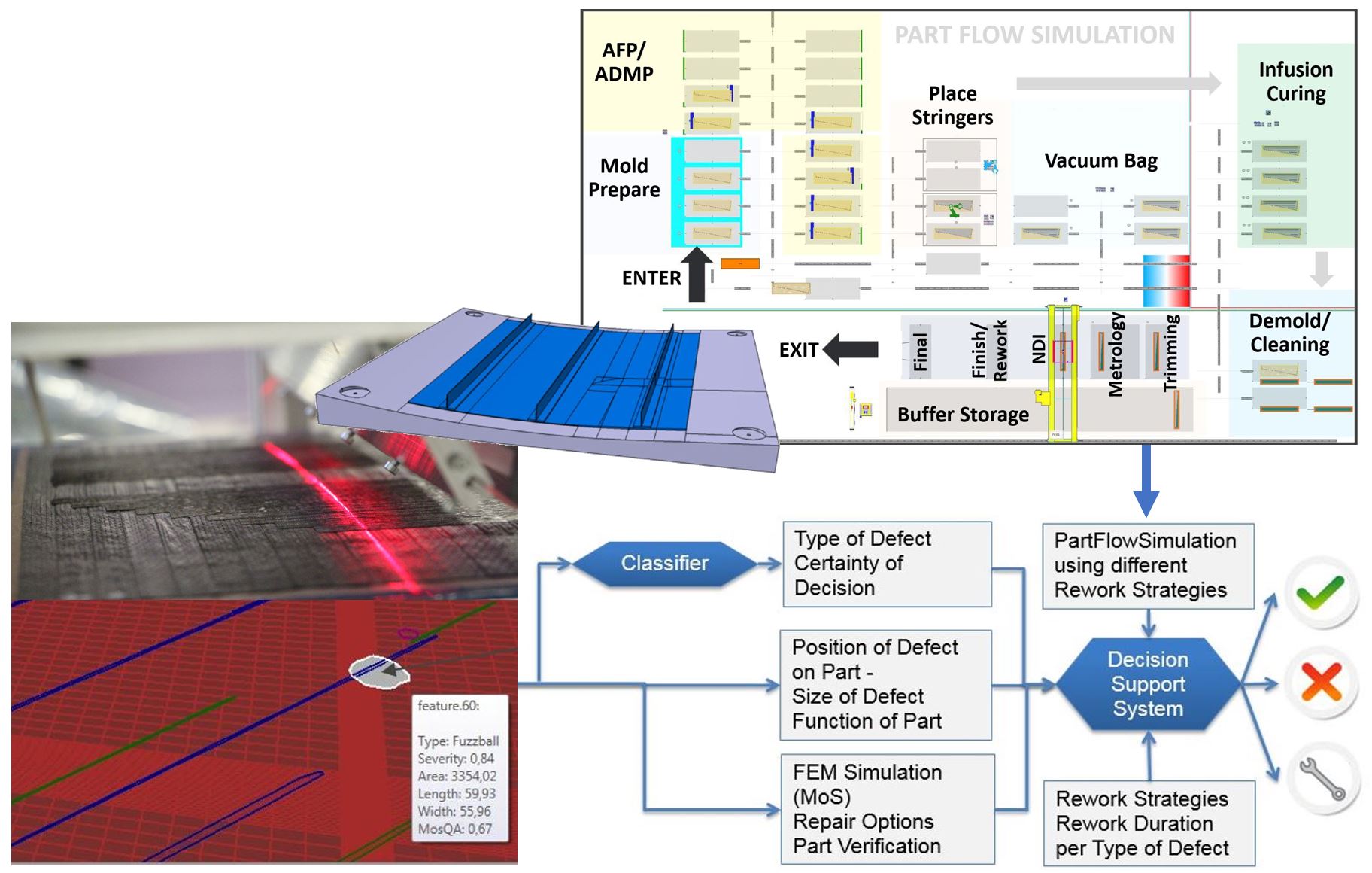
Bis zur Abschlussprüfung im September 2019 erreichte der von Projektleiter Profactor (Steyr, Österreich) entwickelte Prepreg-AFP-Sensor nicht nur eine automatisierte Inline-Inspektion, sondern könnte auch zur Vor-Ort-Korrektur von Teilen eingesetzt werden. „Dieser Sensor kann die Standardfehler wie Lücken, Überlappungen, FOD, Fuzzballs und Twisted Tows sowie den frühen und späten Schnitt jedes Tows erkennen“, sagt Dr. Christian Eitzinger, Leiter Machine Vision bei Profactor. Ein fehlendes Schleppseil kann automatisch korrigiert werden, indem ein zusätzliches Schleppseil genau dort platziert wird, wo es ausgelassen wurde. Die Maschine muss jedoch gestoppt werden, um Fuzzballs oder ein verdrehtes Schleppseil zu entfernen. „Eine Datenbank, die mit 3D Experience von Dassault Systèmes (Paris, Frankreich) für CATIA erstellt wurde, ermöglicht es uns, die Auswirkungen auf die Leistung des Teils basierend auf Größe, Form und Art des Fehlers zu berechnen. Die Verarbeitung aller Fehler in einer Lage dauert nur Sekunden. Der Maschinenbediener entscheidet dann, welche Mängel belassen werden dürfen und was nachgearbeitet werden muss.“
Für die Überwachung und Steuerung des Infusionsprozesses hat Airbus (Toulouse, Frankreich) über die Tochtergesellschaft InFactory Solutions (Taufkirchen, Deutschland) drei Sensoren entwickelt, die Temperatur, Aushärtungszustand und Harzflussfront messen (siehe „Sensoren zur Überwachung der Harzinfusionsflussfront“. ) „Wir haben diese mit CATIA 3D Experience integriert und gezeigt, dass die Daten zuverlässig erfasst und dem digitalen Faden jedes Teils hinzugefügt werden können“, sagt Eitzinger. (Siehe Online-Seitenleiste „Composites 4.0:Digitaler Thread vs. digitaler Zwilling“.)
Der letzte von drei Teildemonstratoren war ein Unterabschnitt der oberen Flügelabdeckung mit drei Stringern (siehe Online-Sidebar „ZAero-Projektupdate“). Für diesen Teil wurde das Entscheidungsunterstützungstool von Profactor live beim Partner FIDAMC (Madrid, Spanien) demonstriert, verbunden mit der Teileflusssimulation – basierend auf der Siemens PLM (Plano, Texas, USA) Tecnomatix Plant Simulation Software – die auf dem Server von Profactor in Österreich läuft. Neben dem Aufbau einer Fehlerdatenbank führte ZAero auch Experimente mit maschinellem Lernen durch. Manuell entworfene, generative Computermodelle in Kombination mit tiefen neuronalen Netzen, die Defekte erkannt und klassifiziert haben, erreichen eine zu 95 % korrekte Klassifizierung verschiedener Regionen (Lücke, Überlappung, Tow, Fuzzball) in echten ADMP-Überwachungsdaten, selbst wenn künstlich erzeugte Fehlerdaten wurden für das Tiefennetzwerktraining verwendet (analog wie Ultraschallprüfsysteme auf eine Reihe von absichtlichen Fehlern kalibriert werden).
„Wir werden auf jeden Fall eine Art nächste Phase verfolgen“, sagt Eitzinger. Inzwischen vermarktet Profactor modulare Sensoren für Faserorientierung und Defekte während des automatisierten Layups. InFactory Solutions bietet auch seine AFP- und Harzinfusionssensoren an, und die Faserplatzierungspartner Danobat und MTorres (Torres de Elorz, Navarra, Spanien) verkaufen jetzt ihre Geräte mit integrierter Inline-Inspektion.
Die digitale Transformation von Dynexa
Dynexa ist ein Hersteller von Verbundteilen, der sich auf CFK-Rohre und -Wellen spezialisiert hat. „Wir hatten immer versucht, alles zu digitalisieren“, sagt Geschäftsführer Koppenberg. „Wir haben uns bereits von manuellen und analogen Prozessen befreit und alles größtenteils in unser ERP-System [Enterprise Resource Planning] integriert. Aber wie machen wir das in der Fertigung? Wir haben verstanden, dass alles, was wir in ein Arbeitsprotokoll oder eine Arbeitsprozedur einbringen, ein Code ist, und dies ist eine Grundlage für die digitale Transformation. Aber wo wird es gespeichert? Auf einem lokalen Server, in der Cloud oder innerhalb der Maschine? Wir fragten fünf Leute und bekamen sieben Antworten, was wir tun sollten.“ (Siehe Online-Seitenleiste „Composites 4.0:Wo soll ich anfangen?“)
Glücklicherweise hatte die Bundesregierung ein Programm für Hochschulen aufgelegt, um kleine und mittlere Unternehmen (KMU) kostenlos zu Industrie 4.0-Beratung zu beraten. Dynexa hat die Zusammenarbeit mit dem Darmstädter Kompetenzzentrum Mittelstand 4.0 aufgenommen. „Sie sagten, man solle sich keine Sorgen um die digitale Architektur machen, sondern mehr darauf achten, was man messen muss und wie man das macht“, erinnert sich Koppenberg. „Wir haben uns für einen Prozess entschieden, der erhebliche manuelle Messungen beinhaltete, bei dem wir wussten, dass wir Qualitäts-, Zeit- und Kostenprobleme hatten.“
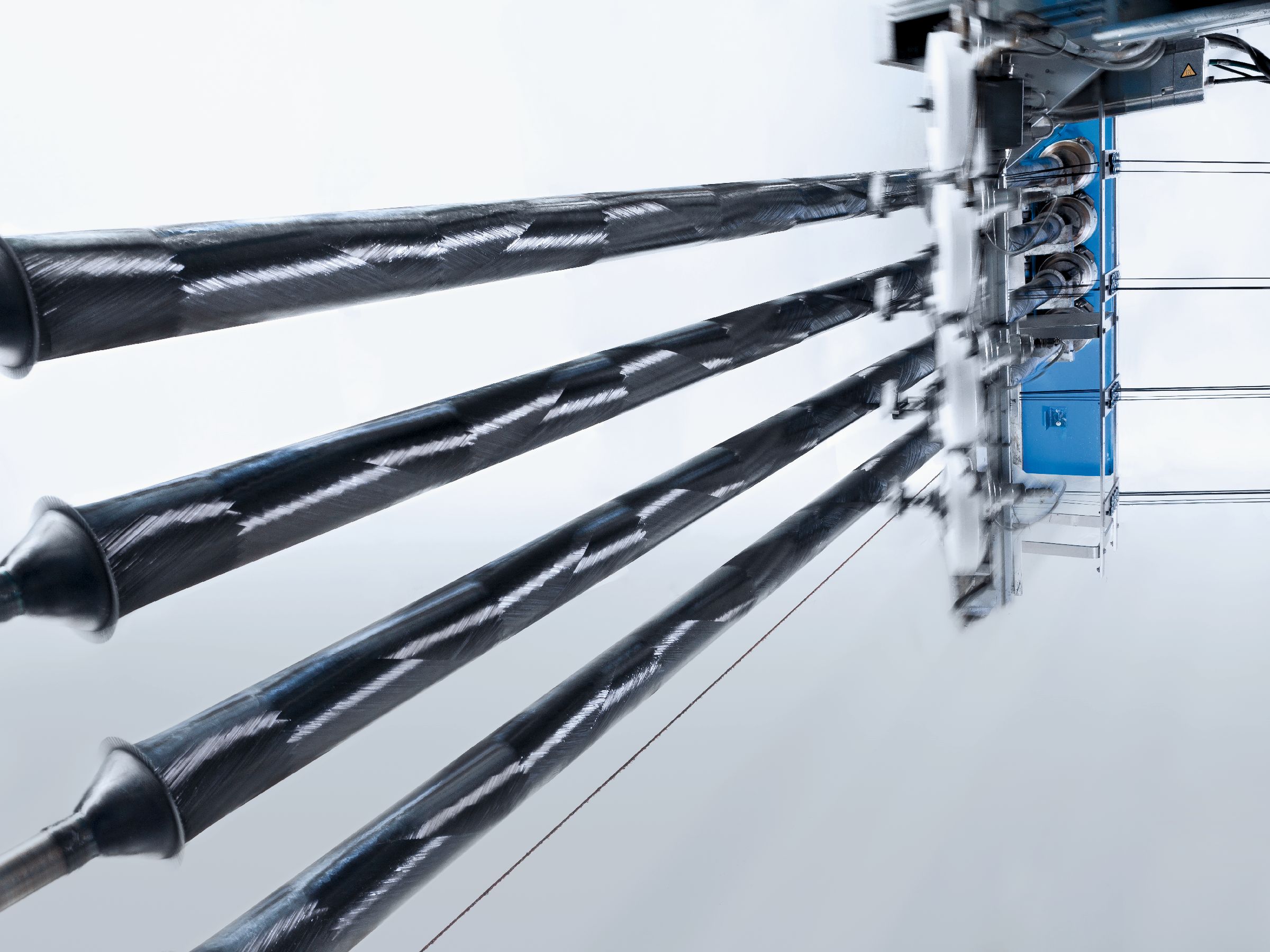
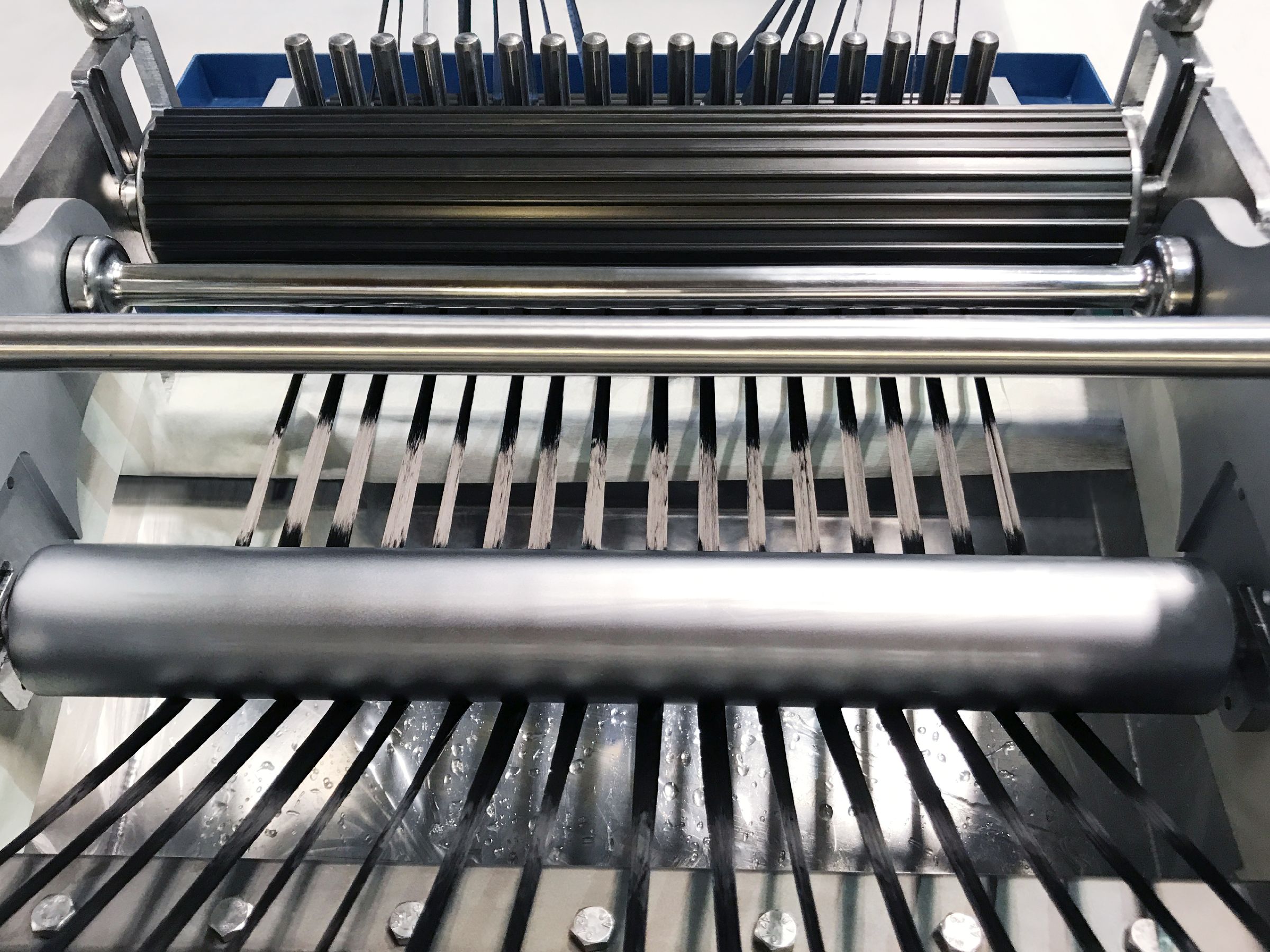
Dynexa verwendet ein Nass-Filament-Wicking-Verfahren. (Siehe „Verbundstoff-Abtriebswelle bereit für den Automobiltest.)“ Ein wichtiger Schritt ist die Harzaufnahme, bei der die trockene Faser auf eine Verdichtungswalze geleitet wird, die aus dem Harzbad aufrollt. An der Verdichtungswalze sitzt ein Rakel, der die Harzmenge bestimmt, die mit dem trockenen Filament vor dem Aufwickeln verbunden wird. „Wenn wir zu viel Harz aufnehmen, können wir den angegebenen Rohrdurchmesser überschreiten“, sagt Koppenberg, „aber bei zu wenig Harz riskieren wir, den zulässigen Mindestdurchmesser zu unterschreiten.“
„Ohne Messung kennt man den endgültigen Durchmesser erst nach dem Aushärten, wenn der gesamte Wert investiert ist“, betont er. „Der Bediener muss also die Maschine stoppen, das Teil messen, aufschreiben und dann wieder starten. Aus jahrelanger Erfahrung wissen wir, welche Laminatdicke in jedem Wickelschritt sein sollte. Daher vergleicht der Bediener die Messung und passt die Rakel an, um die Harzaufnahme nach Bedarf zu korrigieren, aber dies ist sehr manuell und hängt von den Fähigkeiten und der Erfahrung des Bedieners ab.“
Um dies zu digitalisieren, hat Dynexa mit unzähligen Laser- und Kameraherstellern gesprochen. „Sie sagten:‚Wir haben die Lösung‘, aber dann schaffte es keiner“, sagt Koppenberg. Das Team der Universität Darmstadt ermöglichte jedoch den Einsatz einer Kamera, indem es die Korrekturen ermittelte, die aufgrund bestimmter physikalischer Faktoren wie Lichtreflexion von der nassen Oberfläche erforderlich sind. „Jetzt haben wir die Wickelmaschine an das Messgerät angeschlossen, das sehr standardisiert arbeitet“, fügt er hinzu.
Das Team entwickelte eine Datenbank mit Korrekturtabellen und Entscheidungsalgorithmen, die es der Filamentwickelmaschine ermöglichen, zu wissen, was das Ziel für jede Stufe des spezifischen zu wickelnden Rohres sein muss. „Wenn die Eingabe des Messgeräts anzeigt, dass die Harzaufnahme nicht dort ist, wo sie sein sollte“, erklärt Koppenberg, „reagiert die Fadenwickelmaschine, indem sie die Rakel so anpasst, dass sie wieder in die Spezifikation zurückkehrt, ohne das Aufwickeln zur Messung anzuhalten.“
Jede Spulmaschine hat jetzt das digitale Messsystem, und eine Ethernet-Karte. „Der teuerste Teil war die Installation und Verlegung der Kabel zum Server“, witzelt Koppenberg, „aber jetzt können wir mit jeder Maschine sprechen und alle Daten sammeln.“ Und es gibt noch einen weiteren Vorteil. „Früher haben Bediener an den Maschinen programmiert, aber sobald wir sie mit dem Server verbunden haben, können wir an jedem Desktop- oder Laptop-Computer programmieren. Dadurch wurden Ausfallzeiten weiter reduziert und ein weiterer Produktionsengpass beseitigt.“
Dieser erste digitale Schritt hat es Dynexa ermöglicht, seine Prozesskontrolle, Qualität und Effizienz zu verbessern und so kosteneffektiver zu werden. Es hat auch eine weitere Transformation vorangetrieben.
Paradigmenwechsel bei Verbundwerkstoffen
„Wir sind dabei, unseren Kunden schrittweise ein neues Ökosystem bereitzustellen“, sagt Matthias Bruckhoff, Vertriebs- und Marketingleiter von Dynexa. Er nennt ein Beispiel:„Bei Amazon sieht man, was man wann gekauft hat, sowie neue Produktvorschläge. Früher haben wir Kundenanforderungen aufgenommen und dann innerhalb weniger Tage mit unseren Berechnungs- und Engineering-Tools reagiert. Nun wird dies online sein. Unsere Kunden werden sich die Produkte ansehen und in wenigen Minuten ihren Bedarf, ihre Kosten und ihre Lieferung berechnen. Das ist nicht neu, aber ist für unsere Branche. Genauso wie wir unseren Maschinenbedienern die Freiheit gegeben haben, sich auf mehr Maschinen und übergeordnete Aufgaben zu konzentrieren, werden wir jetzt unser Engineering-Team freigeben, um sich auf spezialisiertere und anspruchsvollere Produkte zu konzentrieren.“
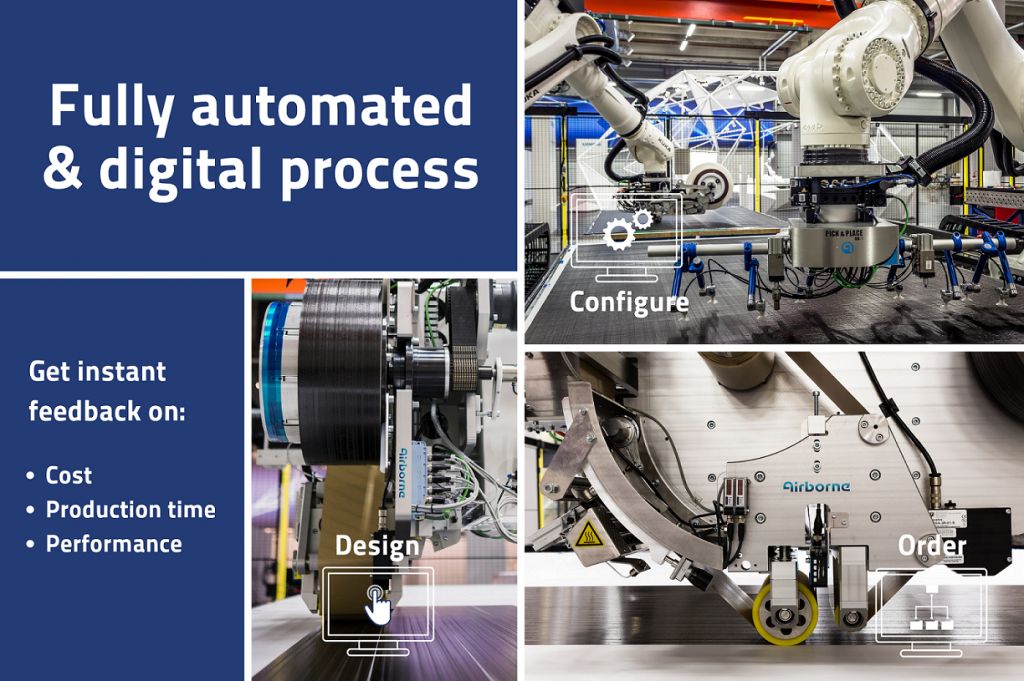
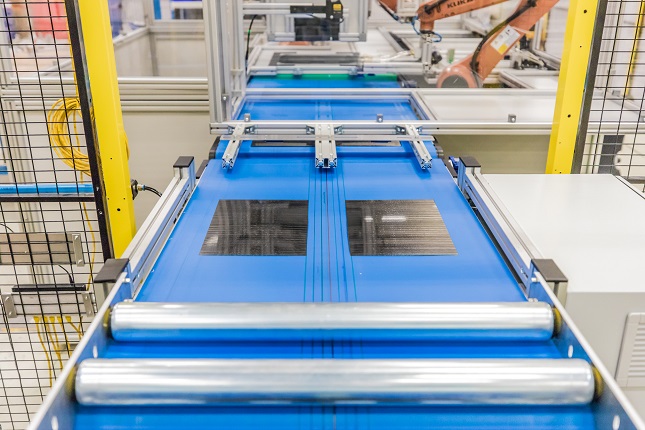
Airborne (Den Haag, Niederlande) hat im September 2019 sein On-Demand-Fertigungsportal für die automatisierte Herstellung von Verbundwerkstoffen eingeführt (siehe „Airborne startet Verbunddruckportal“). Mit diesem Tool geben Kunden Designs in die webbasierte Plattform ein. Das System erstellt dann im laufenden Betrieb den Maschinencode und ermittelt die Produktionsdauer und -kosten. Produkte können dann individualisiert und nach der Bestellung in einer automatisierten Fertigungszelle produziert werden. Das Portal wurde mit der Automated Laminating Cell (ALC) von Airborne gestartet, um duroplastisches Prepreg zu verarbeiten. Sie wird auf andere Prozesse ausgeweitet, beispielsweise auf die High-Volume-Produktionslinie für thermoplastische Verbundwerkstoffe (TPC), die für den Geschäftsbereich Specialties von SABIC (Riad, Saudi-Arabien) entwickelt wurde.
„Dieses Portal ist ein wichtiger Baustein dafür, wie wir die digitale Zukunft der Composite-Fertigung sehen“, sagt Marcus Kremers, Chief Technology Officer bei Airborne. „Vor fünf Jahren haben wir uns von einem Geschäftsmodell der Teilefertigung zu einer Unterstützung der Kunden bei der Automatisierung und Digitalisierung entwickelt. Wir entwickeln ein Portfolio von Lösungen, die es unseren Kunden leicht machen, mit Verbundwerkstoffen zu bauen.“ Dieses Portfolio umfasst ALC, automatisiertes Honeycomb-Potting, automatisiertes Ply-Kitting und die High-Volume-Linie mit TPC-Bändern, die von SABIC als Digital Composites Manufacturing Line (DCML) und von Airborne Falcon bezeichnet wird. Letzteres ist ein Beispiel für die maßgeschneiderten Lösungen von Airborne. „Wir betten unser Wissen über Verbundwerkstoffe und Teilefertigung in diese automatisierten Systeme ein, damit die Kunden keine Spezialisten sein müssen“, sagt Kremers.
Airborne hat drei Geschäftsmodelle:Automatisierung kaufen, mieten oder Airborne überlassen, um sie über Manufacturing as a Service (MaaS) zu betreiben. Luftgestützte automatisierte Zellen verfügen über Sensoren und Inline-Inspektionssysteme, die Warnungen basierend auf einer vom Kunden definierten Fehler- und Toleranzdatenbank generieren. „Die Falcon-Linie hat sehr geringe Toleranzen für optische Qualitätsmängel“, bemerkt Kremers, „aber unsere Automatisierung für die Luft- und Raumfahrt wird stärker von strukturellen Toleranzen bestimmt. Wir entwickeln auch unsere Technologien kontinuierlich weiter, um selbstlernend und selbstanpassend zu sein. Zum Beispiel wird unsere nächste Softwareversion für das ALC-Tapelegen in der Lage sein, Fehler zu erkennen und das Produktionsprogramm im laufenden Betrieb zu ändern.“
Längerfristig besteht die Vision darin, das On-Demand-Portal zu erweitern, um Produktionskapazitäten für Verbundteile zu sammeln, die über mehrere Unternehmen und Regionen verteilt sind. Kremers nennt Protolabs (Maple Plains, Minnesota, USA), das spritzgegossene, aus Blech gefertigte, CNC-gefräste oder 3D-gedruckte Prototypen auf Abruf in nur einem Tag bereitstellt. In ähnlicher Weise bietet die Online-App von Plyable (Oxford, Großbritannien) Formen zur Herstellung von Verbundwerkstoffen und bietet Materialien von Polyurethanplatten bis hin zu Stahl, einschließlich Verbundwerkstoffen und 3D-gedruckten Werkzeugen. „Das ist eine andere Art, die Wertschöpfungskette zu organisieren“, sagt Kremers. „Wir stellen die Maschinen und die Software her, die dies für Verbundteile ermöglichen.“
Dieses Ziel verfolgt das AZL Aachen auch mit seiner Ultra-Fast Consolidator Machine, die entwickelt wurde, um mehrschichtige TPC-Laminate in weniger als fünf Sekunden herzustellen. Es wurde 2019 kommerzialisiert und verwendet robotische, laserunterstützte AFP-Applikatoren von Conbility (Aachen, Deutschland) und 25 Millimeter breite UD-Bänder sowie ein Stückflussprinzip – Stand der Technik in der Hochgeschwindigkeitsdruckindustrie – zur Herstellung von TPC-Laminaten, einfach geheftet oder vollverfestigt, in verschiedenen Dicken, mit lokalen Verstärkungen. „Unsere Vision ist es, skalierbare Maschinen bereitzustellen, die Online-Plattformen ermöglichen“, sagt Emonts. „Linien können mehrere Stationen haben, jede mit mehreren AFP-Applikatoren. Der Kunde gibt die Anforderungen ein und erhält Optionen für Slybook, Kosten und Lieferung. Nach der Fertigstellung kommunizieren die Applikatoren miteinander, um die Produktion zu organisieren, nicht mit dem Bediener. Das ist eine völlig intelligente Produktion von maßgeschneiderten Verbundwerkstoffen.“
Automatisierung der Automatisierung
Der Schwerpunkt des ZLP liegt auf der automatisierten Fertigung von CFK-Strukturen. „Eine Automatisierung für nur ein Teil oder Programm ist schwer zu rechtfertigen“, sagt Florian Krebs, ZLP-Teamleiter für flexible Automatisierung. „Wenn Sie jedoch über aufgabenspezifische Maschinen hinaus zu einer Automatisierungsplattform wechseln, die fast ohne zusätzliche Einrichtung rekonfigurierbar ist, haben Sie jetzt eine Geschäftslösung. Je flexibler die Plattform, desto schneller der Return on Investment.“
Die in den Anfangsbildern gezeigte Arbeitszelle wurde im Rahmen des ZLP-Projekts PROTEC NSR zum Aufbau einer Teilefamilie konzipiert, die dem gleichen Prozessweg folgt:Pick-and-Place-Layup trockener Gelege und Harzinfusion (siehe Online-Sidebar „No Business Case für das Lehren von Robotern“). „Dieser Prozess wurde für das hintere Druckschott des Airbus A350 entwickelt, aber man könnte auf dieser Linie auch eine Rumpfplatte oder eine Flügelabdeckung herstellen, da die Schritte ähnlich sind“, sagt Krebs.
„Um flexible Automatisierungsplattformen zu realisieren, sind bestimmte Technologiebausteine erforderlich, darunter Algorithmen für die Roboter sowie Sensoren und das Verständnis der von ihnen erzeugten Daten“, sagt Kupke. „Zum Beispiel ist die PROTEC NSR-Produktionslinie auf maximale Modularität ausgelegt – alle Module sind miteinander verbunden, um ein selbstkonfigurierendes Korrektur- und Optimierungssystem zu demonstrieren, das in Größe und Komplexität skalierbar ist.“
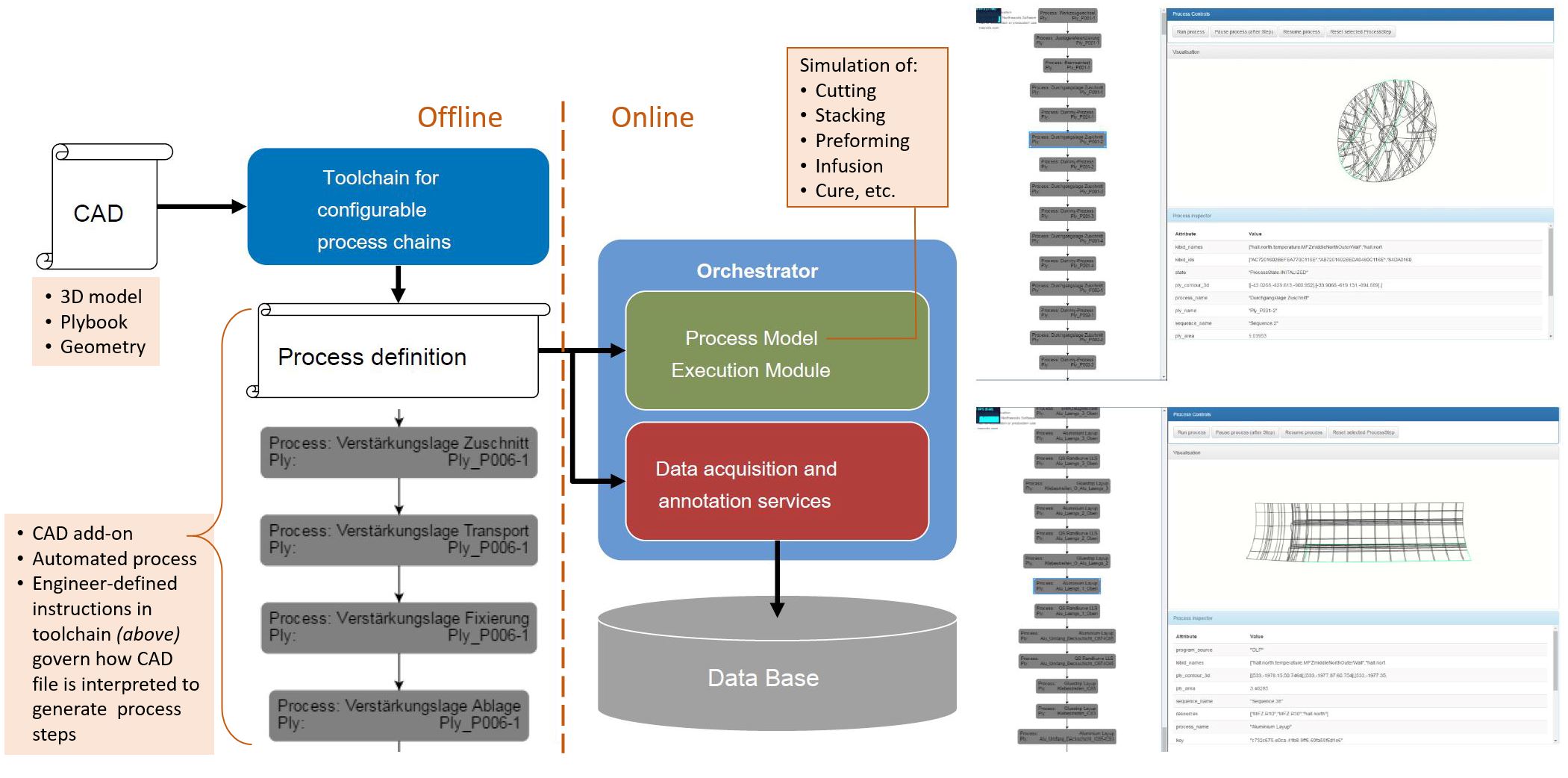
Er erklärt die Module wie in Abb. 5 gezeigt, darunter CAD-Modell, Prozessdefinition, Prozessmodell, das die Simulation und Ausführung des Prozesses ermöglicht, Fertigungsausführungsmodul, Sensoren zum Erfassen von Daten, Software zum Kommentieren der Daten und Datenbank zur Speicherung.
„Auf der linken Seite dieses Diagramms machen Sie einen Plan. Das Ausführungsmodul setzt diesen Plan dann um“, sagt Kupke. „Während der Prozessschritte erfassen wir Daten von allen beteiligten Maschinen und Prozessen, zum Beispiel dem Cutter, den Robotern, dem Gebäude (Temperatur, Druck, Luftfeuchtigkeit), den Kameras beim Pick-and-Place etc. Wir analysieren die Daten in Echtzeit während des Prozesses und annotieren die gesammelten Daten zusätzlich automatisch mit Metadaten, um sie in die Datenbank einzuspeisen, die die Grundlage für den digitalen Zwilling des Prozesses bildet. Der wichtigste Punkt des digitalen Zwillings ist ein zentrales Repository, eine Quelle der Wahrheit. Das CAD-Modell und die Prozessdefinition jedes Teils sind Teil seiner Single Source of Truth.“
Mit diesen Modulen arbeitet die Linie autark auf Knopfdruck. Aus CAD-Modell, Fertigungsplan und Kameras leiten die Roboter ab, welches Teil als nächstes kommt und suchen es auf dem Tisch (z. B. aus 100 anderen Zuschnitten). „Sie entscheiden, wie die Greifer konfiguriert werden, um es aufzunehmen und in das Werkzeug zu legen, und wissen, wo es platziert werden muss.“ Basierend auf dem Produktionsplan bestimmen die Roboter jeden Start-/Endpfad für alle Prozessschritte und wissen, wann jeder fertig ist. „Normalerweise werden diese Wege von einem Menschen gelehrt“, sagt Kupke. „Aber in unserem System wird jeder Pfad automatisch, kollisionsfrei und in Echtzeit definiert. Wenn Sie das CAD-Modell oder die Prozessdefinition ändern, passen sich die Roboter ohne zusätzlichen Teach-Aufwand an. Aber was ist, wenn Sie das Teil komplett ändern? Mit dieser Art der Automatisierung könnten Sie diese Änderung sehr schnell vornehmen. Dies ist der Weg zur flexiblen Produktion. Unsere Rolle bei ZLP besteht darin, diesen Weg zu ebnen, indem wir Technologiebausteine entwickeln und diese miteinander verbinden.“
Gelegenheit und Ontologie
Die COVID-19-Pandemie hat den Wert einer flexiblen Produktion deutlich gemacht. Es hat auch ein zunehmend unberechenbares Geschäftsumfeld geschaffen. „In den letzten zwei bis drei Jahren ist alles volatiler geworden“, sagt Bruckhoff von Dynexa. „Unsere Kunden wollen sehr schnelle Antworten, um auf ihre Kunden eingehen zu können. Indem wir unser neues Online-Ökosystem anbieten, machen wir die gesamte Lieferkette wettbewerbsfähiger.“
Dies ist in der Luftfahrtindustrie allgemein anerkannt. „Wir brauchen eine digitale Basis für Produktionslinien und ganze Standorte, die sowohl eine horizontale als auch eine vertikale Integration ermöglicht“, sagt Marc Fette, Vorsitzender des Fachbereichs Luft- und Raumfahrttechnik des VDI – Verband Deutscher Ingenieure und COO Composite Technology Center (CTC). Stade, Deutschland), einer F&T-Tochter von Airbus. CTC-Projekte in Composites 4.0 umfassen Material- und Asset-Tracking, kollaborative Roboter, fortschrittliche Prozessketten und mehr. Fette betont jedoch die Notwendigkeit einer Ontologie – einer Terminologie und eines gemeinsamen Protokolls für die digitale Kommunikation und den Datenaustausch. (Siehe die Online-Seitenleiste „Composites 4.0-Architektur und Ontologie“.)
„Man braucht eine ganzheitliche Vernetzung aller Maschinen und Produktionssysteme einer Anlage“, erklärt er, „dies muss sich aber auch auf die gesamte Wertschöpfungskette erstrecken, einschließlich Disziplinen wie Engineering, Beschaffung, Logistik und Material- und Prozesszertifizierung.“ , einerseits. Andererseits müssen alle Stakeholder, wie zum Beispiel Lieferanten, berücksichtigt und in diesen Veränderungsprozess eingebunden werden. Wir sehen viele Pilotprojekte, aber im Detail fehlt noch die Strategie für einen ganzheitlichen Ansatz pro Unternehmen oder Produktionskette.“
Er fährt fort:„Wir haben ein sehr großes, globales Lieferantennetzwerk und diese haben die gleichen Anforderungen, um als digital vernetzte Lieferkette zu agieren. Die meisten unserer Lieferanten sind mittelständische Unternehmen, die für die beiden Flugzeughersteller Airbus und Boeing arbeiten. Gibt es keine Diskussion über einen gemeinsamen Standard, dann geben Sie diese Herausforderungen an die Lieferanten weiter. Sie können es sich höchstwahrscheinlich nicht leisten, für alle ihre Maschinen zwei unterschiedliche Standards einzuhalten, einschließlich Dokumentation, Bewertung von Daten, Cybersicherheit usw.“
Fette räumt ein, dass dies große Ideen sind und sagt, dass Flugzeug-OEMs Pläne entwickeln, um diese Herausforderungen anzugehen. „Aber es gibt viele Hindernisse wie diese, und es ist wirklich komplex, was nicht nur Technologie, sondern auch soziale, wirtschaftliche, ergonomische und rechtliche Aspekte betrifft – es ist ein mentaler Veränderungsprozess. Wir stehen erst am Anfang. Aber um erfolgreich zu sein, müssen wir verstehen, dass diese neuen Systeme auf Menschen angewiesen sind und diese Menschen an Bord sein müssen, nicht nur bei den OEMs, sondern im gesamten globalen Netzwerk.“
“Markets are becoming more fragmented across all industries and everyone is facing a paradigm shift,” notes ZLP’s Krebs. “Many people don’t see that as an opportunity,” adds Kupke, also of ZLP. But those who do see that opportunity envision democratized access to composites enabled by Composites 4.0, and with that, a much broader market, including applications that we are only beginning to conceive.
Harz
- Optimierung der digitalen Transformation in der CPG-Herstellung
- Strategie für die digitale Transformation erfordert neue Talente
- Datengesteuerte digitale Transformation bringt Airbus in neue Höhen
- Wie verändert das neue Zeitalter der digitalen Transformation den Versorgungssektor?
- Evonik baut neue Produktionsstätte für PA12
- Planen Sie den Erfolg bei der digitalen Transformation
- Was ist digitale Transformation in der Fertigung?
- 7 Treiber der digitalen Transformation
- Herausforderungen der digitalen Transformation in der Fertigung
- Digitale Fertigungstransformation:Ein Vorsatz für das neue Jahr