Die Nachfrage nach längeren Spritzgestängen ermöglicht Verbundwerkstoffe in landwirtschaftlichen Geräten
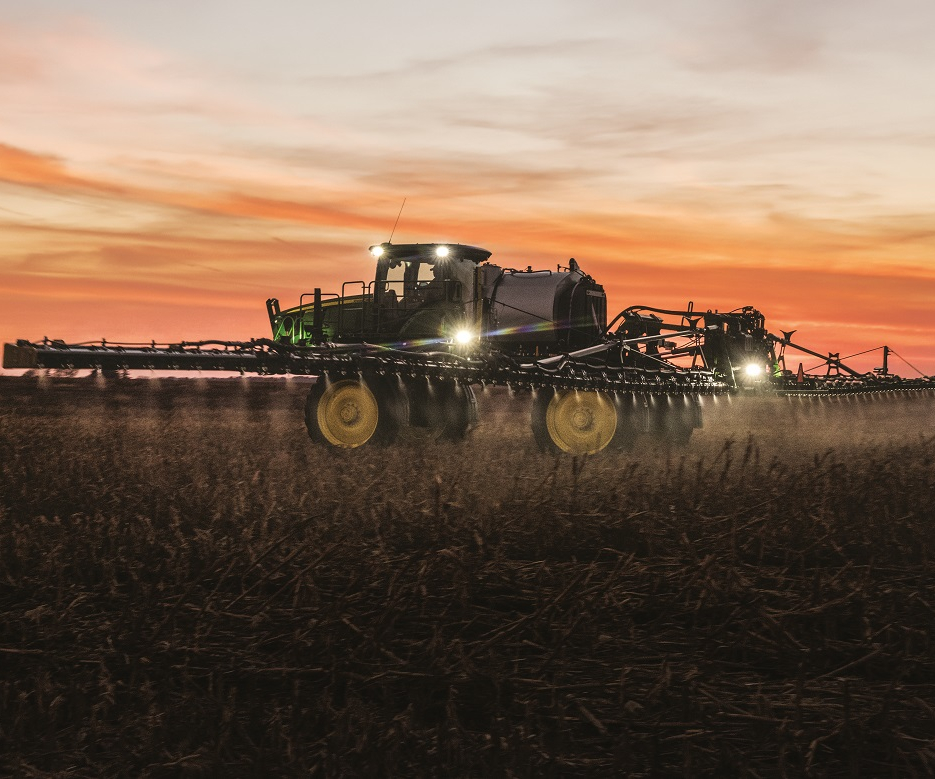
Erfüllung der landwirtschaftlichen Nachfrage. Eine wachsende Anwendung von Verbundwerkstoffen auf dem Landmaschinenmarkt sind Auslegerarme für selbstfahrende Spritzgeräte, die zum Auftragen flüssiger Chemikalien auf Pflanzen verwendet werden. Quelle | Deere &Co.
Da zusammenhängende landwirtschaftliche Felder in Gebieten wie Nordamerika, Argentinien und Brasilien dank der Konsolidierung größer geworden sind und die Direktsaat in bestimmten Regionen zunimmt, möchten Landwirte Sprühsysteme mit längeren Auslegerarmen, um die Anzahl der für die Bearbeitung erforderlichen Übergänge zu reduzieren größere Felder. Dadurch wird auch die Bodenverdichtung reduziert, die Produktivität und die Ernteerträge erhöht.
Um diesem Bedarf gerecht zu werden, nutzte der argentinische Zweig der King Marine SA (Valencia, Spanien), dessen Kerngeschäft ironischerweise die Herstellung von Bootsteilen aus Verbundwerkstoffen aus kohlenstofffaserverstärktem Kunststoff (CFK) in Luft- und Raumfahrtqualität war, seine Verbundwerkstoffkompetenz in anderen Märkten neue Spritzgestänge für selbstfahrende Spritzgeräte zu entwickeln. Im Gebrauch entfalten sich die Auslegerarme und erstrecken sich senkrecht zur Hauptachse von Traktoren und ermöglichen es Landwirten, flüssige Chemikalien (z. B. Insektizide, Herbizide und Düngemittel) auf Feldfrüchte aufzubringen. Nach Gebrauch lassen sie sich wieder zusammenfalten und entlang des Traktorkörpers verstauen, um ein Verheddern mit Zaunpfosten zu vermeiden und den Landwirten das Befahren von Straßen zu ermöglichen.
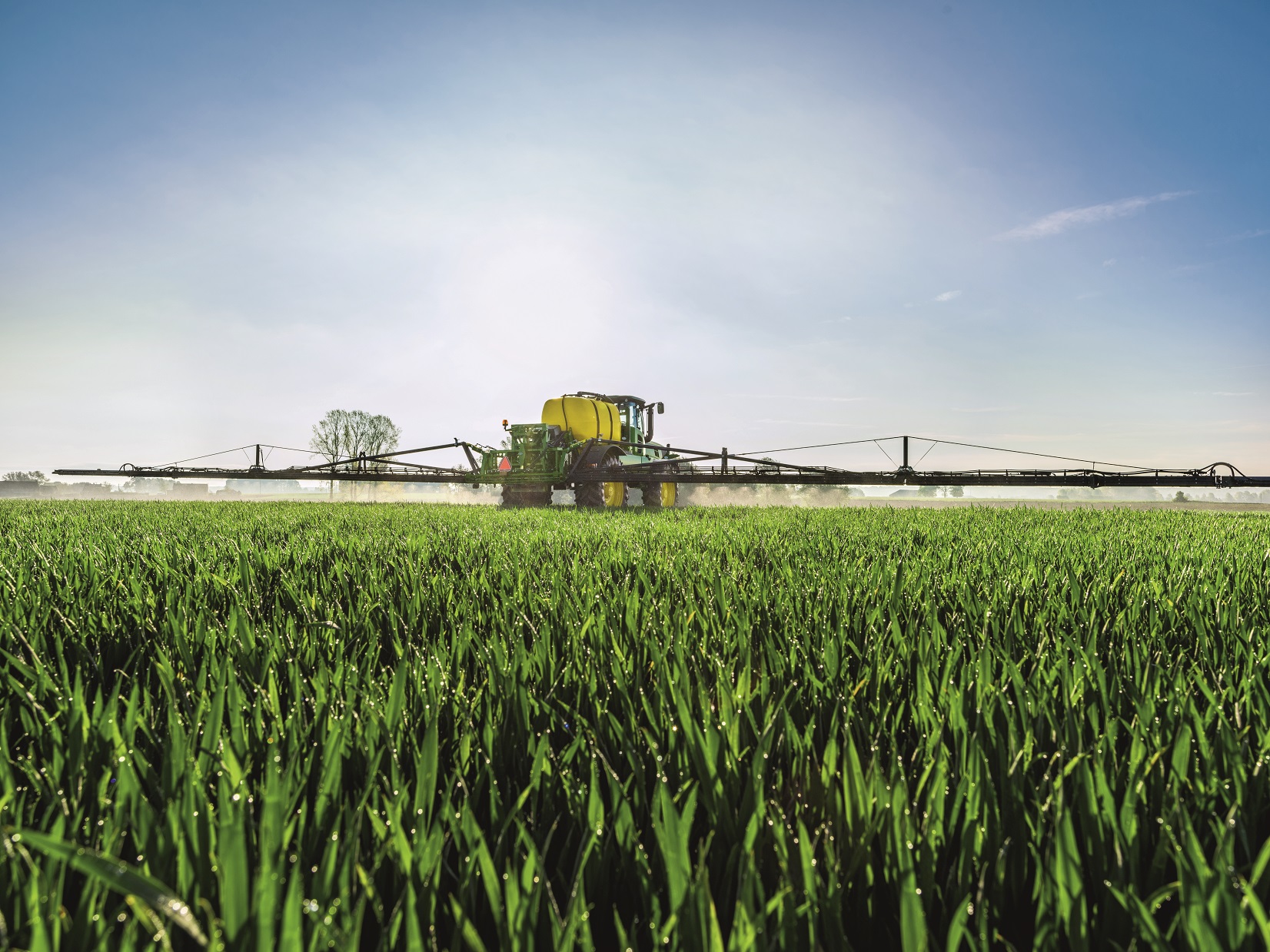
Die Grenzen von Metall. Traditionell aus Stahl gefertigt, hatten die Spritzgestängearme aufgrund der großen Stützstrukturen, die erforderlich waren, um ein Verbiegen der Arme unter Torsions- und Ermüdungsbelastungen zu verhindern, ihre praktischen Grenzen in Bezug auf Struktur und Breite erreicht. Quelle | Hirsch &Co
Ausleger werden seit langem aus Stahl hergestellt, aber mit zunehmender Länge waren größere Stützstrukturen erforderlich, um zu verhindern, dass sich die Arme unter Torsions- und Ermüdungsbelastungen und bei unbeabsichtigten Aufprallen auf Zäune, Bäume und andere Strukturen verbiegen. (Hohe Ermüdungsbelastungen sind der Grund, warum Ausleger nie auf Aluminium umgestellt wurden.) Im Gegenzug erforderten längere Ausleger mit größeren Stützstrukturen, dass Landwirte größere Traktoren kauften, um schwerere Spritzgeräte und größere Tanks mit größeren Flüssigkeitsmengen zu transportieren; Bei der Lösung eines Problems führt die schwerere Ausrüstung jedoch zu einer erhöhten Bodenverdichtung und infolgedessen zu geringeren Ernteerträgen. Außerdem korrodieren viele landwirtschaftliche Chemikalien Metalle und längere Ausleger erfordern aufwendigere Klappmechanismen zum Verstauen des Auslegers. Schließlich erreichten Stahlausleger eine praktische Grenze von ungefähr 36 Metern (120 Fuß) von Seite zu Seite. Dennoch wollte der Markt – insbesondere in Amerika – längere Booms.
Rezession bietet Chancen
Die Große Rezession von 2008 war sowohl für Einzelpersonen als auch für Unternehmen katastrophal. Das zwanzig Jahre alte, in Familienbesitz befindliche King Marine mit Produktionsstätten in Picassent, Spanien, und Campana, Argentinien, startete 2008 mit einem boomenden Geschäft, das CFK-Komponenten – insbesondere Masten – für Hochleistungsyachten herstellte.
„Damit begann die weltweite Wirtschaftsrezession und der Markt für Luxusschiffe erlitt einen gewaltigen Einbruch“, erinnert sich Natalia Dacko, Leiterin der europäischen Verwaltung und interne Revision bei King Marine. „Unsere Verkäufe gingen dramatisch zurück und wir hörten auf, Boote zu bauen. Wir waren im Krisenmodus, weil unser Unternehmen in Gefahr war. Wir hatten einen großen Stab von Technikern, Ingenieuren und Spezialisten – allesamt Experten für Kohlefaser [Verbundwerkstoffe]. Die große Frage war:‚Was machen wir jetzt?‘“ King Composite S.L. wurde entwickelt, um nicht-marine CFK-Anwendungen zu erforschen.
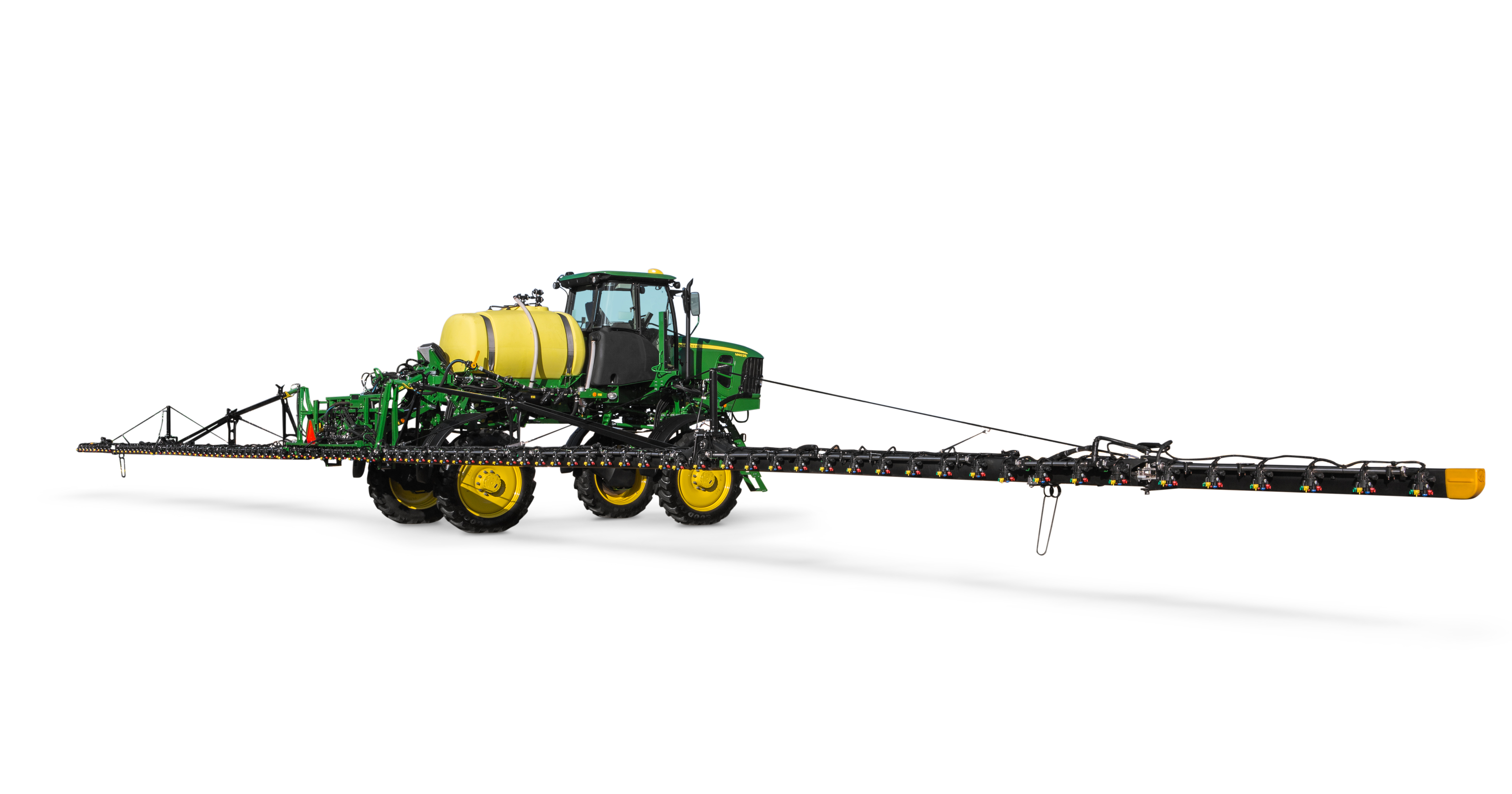
Länger denn je. Verbundausleger können für eine einfache Verwendung auf- und ausgefahren werden. Quelle | Deere &Co.
Eine unerwartete Lösung für die Bedenken des Unternehmens kam 2009 von einem Argentinier, dessen eigenes Unternehmen landwirtschaftliche Sprühsysteme herstellte. Der Mann war frustriert über die Probleme mit seinen Metallbooms. „Er hat uns gesagt, dass er leichter, länger, ermüdungsfreier, korrosionsbeständiger und reparaturfreundlicher sein möchte“, erinnert sich Dacko. Obwohl King Composite noch keine Erfahrung mit Landmaschinen hatte, baute ein Team einen CFK-Prototyp, und das argentinische Unternehmen liebte ihn, was das wachsende Geschäft von King Composite mit Landmaschinen-OEMs in Argentinien ankurbelte. King Composites würde schließlich in King Agro SL umbenannt.
Als das Geschäft mit Spritzgestängen aus Verbundwerkstoffen wuchs, wurde King Agro für seine innovativen und qualitativ hochwertigen Produkte bekannt. Nach einigen Jahren wurde der Erfolg von einem führenden Landmaschinenführer bemerkt, der seine eigenen Schlachten mit Spritzgestänge bekämpfte. Mitglieder des Engineering-Teams von Deere &Co. (Moline, Illinois, USA) trafen sich 2015 mit King Agro, um Möglichkeiten zu besprechen, und bald produzierte und vertrieb King Agro CFK-Ausleger für die Marke John Deere.
Neue Generationen, neue Permutationen
„Wir begannen mit den Designs und Empfehlungen von King Agro sowie dem, was Deere entwickelt hatte, und fanden sie ziemlich anwendbar“, erklärt Phillip Ferree, General Manager von King Agro. „Zunächst hat unser gemeinsames Team einige Änderungen vorgenommen, um die Zuverlässigkeit und Haltbarkeit für den südamerikanischen Markt zu verbessern, und diese Produkte im Jahr 2015 auf den Markt gebracht. Gleichzeitig begannen wir mit der Entwicklung von Produkten der zweiten Generation für Nordamerika und Europa. Um die lokalen Vorschriften zu erfüllen, brauchten wir unterschiedliche Funktionen in Bezug auf Haltbarkeit und Schlagfestigkeit, was die Umsetzung von Metallspezifikationen in Verbundkonstruktionen erforderte.“ Diese Produkte wurden 2017 kommerzialisiert.
„Bei unserem ersten Treffen haben wir drei Stunden damit verbracht, nur die unterschiedlichen Eigenschaften von Spritzen in Nord- und Südamerika zu diskutieren“, erinnert sich Thomas Bartlett, Produktentwicklungsleiter bei Deere Spritzen. „Sie verwenden nicht nur unterschiedliche Faltmuster – je nach Markt und Vorschriften gibt es 20 verschiedene Möglichkeiten, diese Systeme zu falten –, sondern auch die landwirtschaftlichen Bedingungen sind unterschiedlich. In Brasilien wird Direktsaat angebaut. In Nordamerika ist es mit unterschiedlichen Anbaumethoden und mehr Regulierungen begrenzter. Europa hat weitere Unterschiede und viel kleinere Betriebe. Sie halten ihre Chemikalien zentral, sodass Sprühgeräte zum Nachfüllen ins Depot gebracht werden, anstatt Chemikalien zum Nachfüllen auf die Felder zu bringen, wie wir es in Amerika tun.“ Darüber hinaus transportierten Rohrleitungen in einigen Regionen Flüssigkeiten vom Tank zu Düsen durch die Arme, aber an anderen Orten verliefen Rohrleitungen unter den Armen. Eine weitere Herausforderung bestand darin, wie lange die Ausleger ausgefahren werden sollten, da das Hinzufügen eines weiteren Meters hier oder da nicht unbedingt eine praktikable Lösung darstellen würde. Stattdessen mussten die Ingenieure berücksichtigen, wie die Pflanzen in den einzelnen Regionen angebaut wurden und die Abstände zwischen und innerhalb der Reihen.
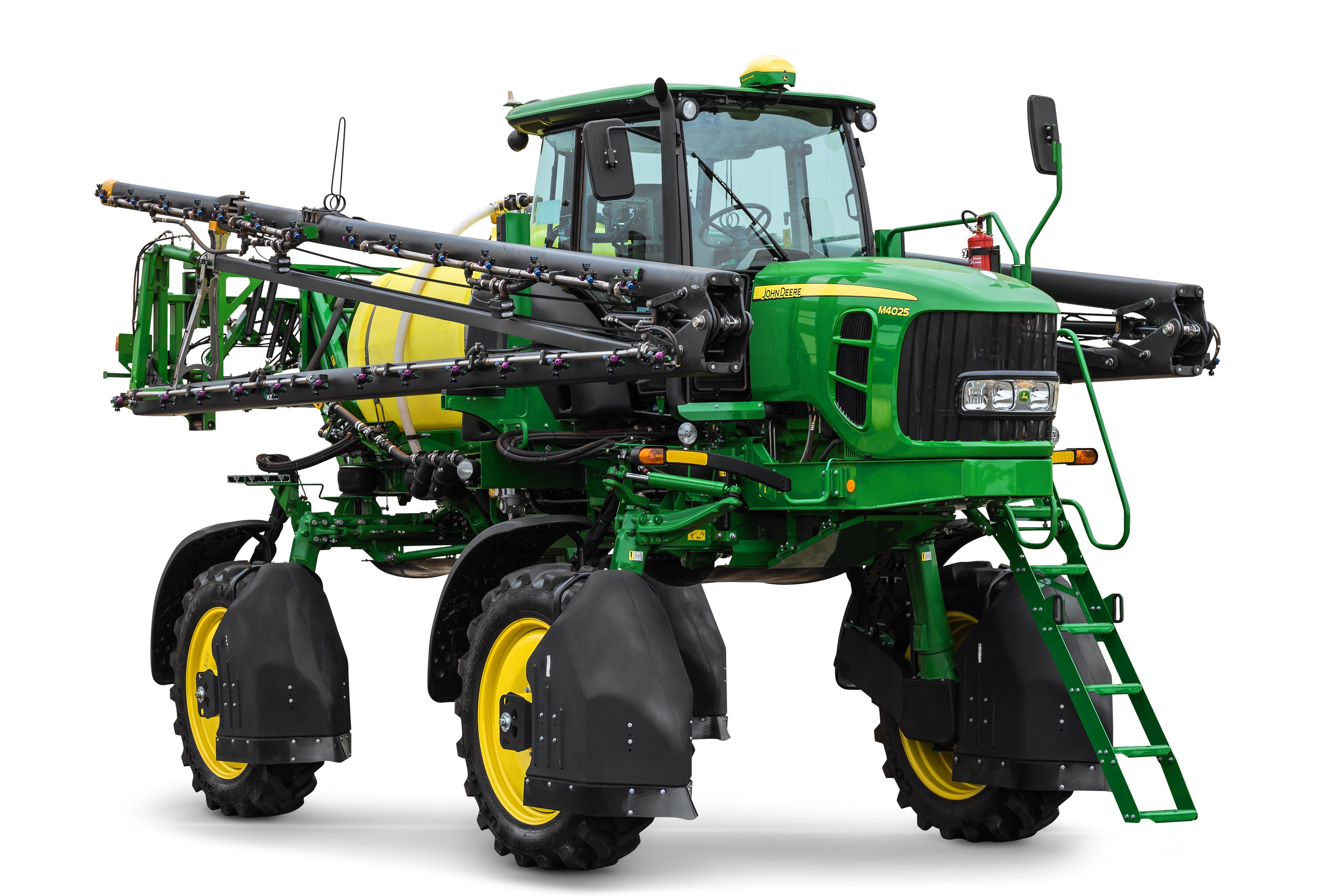
Gefaltet zur einfachen Aufbewahrung. Die Auslegerarme lassen sich verstauen, um das Reisen zwischen Feldern und Ausrüstungslagerung zu erleichtern. Quelle | Deere &Co.
Die Ausleger verfügen über mehrere Verbundrohrstrukturen mit quadratischem Querschnitt, die wiederum über spezielle „Enden“ verbunden sind, die mit den Flüssigkeitszufuhrsystemen verbunden sind. Speziell entwickelte Merkmale, die in die Hauptstrukturen eingeformt sind, bieten Komponenten mit der erforderlichen Funktionalität zum hydraulischen Öffnen/Schließen und zum Transportieren von Flüssigkeiten unter hohem Druck. „Mit der Hydraulik konnten wir viele Funktionen integrieren, die wir brauchten, um die Dinge zusammenzufügen und insgesamt ein einfacheres Design zu schaffen“, fügt Bartlett hinzu. Deere verlangt, dass die Ausleger in weniger als 1 Minute ausfahren/verstauen und die Flüssigkeit innerhalb von zwei Sekunden nach dem Starten der Pumpe abgegeben wird.
Alle Verbundwerkstoffe verwenden eine Epoxidmatrix und sind vakuumverpackt und autoklaviert. Je nachdem, ob Bauteile eine höhere Festigkeit oder eine höhere Schlagzähigkeit benötigen, kommt eine Kombination aus Carbon- und Glasverstärkung zum Einsatz. Der größte Teil der Kohlefaser ist 24K-Tow, jedoch in einer Vielzahl von Formaten, die von unidirektionaler bis Köperbindung für äußere Erscheinungsschichten mit Klarlack-Finish reichen. In Verbindungen und an Stellen, an denen Hydraulik zusammenwirkt, wo mehr Festigkeit und Steifigkeit benötigt werden, werden schwerere Strukturen mit mehr Lagen verwendet. Je nach Modell und Markt reichen die Produktionsmengen von 100 bis 1.000 Systemen pro Jahr. King Agro schätzt, dass der weltweite Markt für selbstfahrende Spritzen im Jahr 2017 14.000 Einheiten/Jahr betrug.
„Unser Ziel für dieses Programm war es, das Gestänge auf 40 Meter zu verlängern, aber bei einer um 30 % geringeren Masse, da das Gewicht sehr wichtig war“, bemerkt Jonathan Nelson, Deere-Konstrukteur für Verbundspritzgestänge. „Wenn Sie eine große Masse an der Vorder- oder Rückseite einer Maschine hängen, kämpfen Sie mit der Trägheit, daher ist es viel schwieriger, die Lasten zwischen Vorder- und Hinterachse zu verteilen. Wir wollten auch die Korrosionsbeständigkeit verbessern, mussten aber auch galvanische Korrosion in Gegenwart von Kohlefasern berücksichtigen. Eine weitere Anforderung war eine höhere Wirkung, da man einfach nie ein Spritzgerät sieht, das nicht etwas getroffen hat . Wir haben für Metalle entwickelte standardisierte Tests durchgeführt, bei denen Ausleger über mehrere hundert Zyklen in Zaunpfosten gefahren werden.“ Die Arbeitsbelastung und die Ermüdung der Teile sind überraschend hoch, da die Ausrüstung mit 24 bis 30 Stundenkilometern [15 bis 19 Meilen pro Stunde] fährt und die Rohrleitungen Spritzdrücke von 276 bis 414 kPa [40 bis 60 psi] aufweisen.
Leichter, besser, schneller
Nach drei Jahren erwies sich die Zusammenarbeit als so fruchtbar, dass Deere 2018 King Agro erwarb, das heute Ausleger in seinen Werken baut und sie zur Endmontage an John Deere-Werke in Des Moines, Iowa, USA, und Horst, Niederlande, liefert. Der Deal ermöglicht es King Agro Berichten zufolge, seinen Markennamen, seine Marke und seine Handelsbeziehungen beizubehalten.
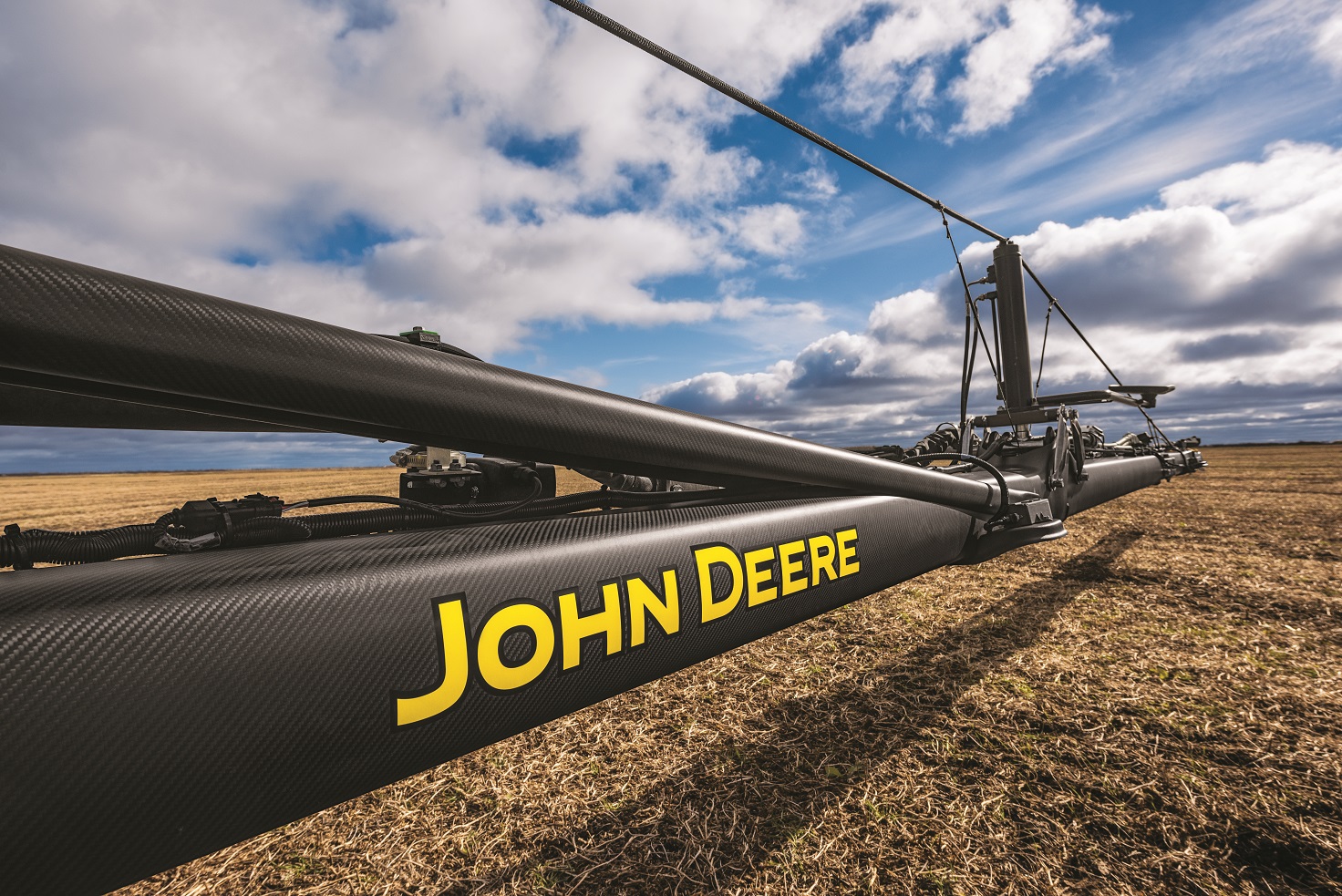
Die Vorteile leichterer Ausleger. Leichtere Ausleger bedeuten geringeren Kraftstoffverbrauch, geringeren Wartungsaufwand, größere Arbeitsbreite, längere Lebensdauer, niedrigere Betriebskosten, einfachere Reparierbarkeit auf dem Feld und bessere Effizienz mit weniger Maschinenwegen für ein größeres Erntevolumen. Quelle | Deere &Co.
Durch die Umstellung auf Verbundwerkstoffe konnten die Ausleger über 36 Meter (120 Fuß) bis 40 Meter (132 Fuß) ausfahren. Im Vergleich zu Stahl ist CFK sechsmal stärker, 5,5mal leichter, schlagfester und korrodiert nicht. Leichtere Ausleger bedeuten weniger Kraftstoffverbrauch, weniger Wartung, größere Arbeitsbreite, längere Lebensdauer, niedrigere Betriebskosten und bessere Effizienz mit weniger Maschinenwegen für mehr Erntevolumen. Ein weiterer Vorteil ist die Reparierbarkeit. „Unsere Händler können einen katastrophalen Ausfall hinnehmen, die Komponente halbieren, etwas Harz hinzufügen, einspannen und aushärten lassen, und sie können loslegen“, fügt Nelson hinzu. „Es ist tatsächlich einfacher zu reparieren als Stahl zu schweißen.“
„Das Beste daran ist der Kundennutzen“, ergänzt Bartlett. „Mit Kohlefaserprodukten können sie produktiver sein. Sie können ohne Gewichtsverlust breiter werden, mehr Hektar bedecken, eine geringere Bodenverdichtung erfahren und die Verringerung des Bodendrucks wirkt sich positiv auf den Ertrag aus.“
Ferree stimmt dem zu:„Aus gestalterischer Sicht ermöglichen uns Verbundwerkstoffe, Dinge zu tun, die wir mit aktuellen Materialien nicht tun konnten, die an ihre strukturellen und Breitengrenzen gestoßen waren“, erklärt er. „Wir haben einen soliden Übergang von unserem Stahlangebot zu unseren Premium-CFK-Angeboten – insbesondere in Nord- und Südamerika –, weil wir eine höhere Produktivität erzielen, die in diesem Segment eine größere Breite bedeutet. Bei kleineren, kostengünstigeren Traktoren können leichtere, breitere Ausleger montiert werden. Oder es kann mehr Flüssigkeit auf einem bestimmten Traktor transportiert werden, während die gleiche Masse beibehalten wird. In jedem Fall wird die Lastverteilung zwischen Vorder- und Hinterachse verbessert und der Massenschwerpunkt liegt näher an der Maschinenmitte, was die Fahrt für den Fahrer verbessert.“
„Wir sehen Anwendungen für Kohlefaser in anderen Produkten“, prognostiziert Aaron Wetzel, Vice President der Deere ag &Turf Crop Care Platform. „In den kommenden Jahren werden wir zusätzliche Möglichkeiten erkunden, bei denen das geringe Gewicht und die Stärke als Stahl unseren Produkten einen Mehrwert für unsere Kunden bieten.“
Harz
- Ultraleichte TPE-Verbundwerkstoffe für Schuhe
- Sind die Preise für Rohstoffharze stabil?
- EV-Heckklappen zur Steigerung der Nachfrage nach LFT-PP
- RS Electric Boats wählt Norco für die Herstellung von Verbundwerkstoffen
- PEEKSense Hochtemperatur-Thermoelement für die Aushärtung von PEEK-Verbundwerkstoffen
- Solvay-Verbundwerkstoffe für Rennkatamarane ausgewählt
- Die Vorteile nutzen:Der Einsatz von Verbundwerkstoffen in landwirtschaftlichen Geräten nimmt zu
- Arbeitsausrüstung:Ist es Zeit für ein Upgrade?
- Vorbereitung der Ausrüstung für den Überseeversand
- Ihre landwirtschaftliche Ausrüstung kennen