Experteninterview:Dr. Johannes Homa, CEO von Lithoz zum Stand des keramischen 3D-Drucks
Keramik-3D-Druck ist noch eine relativ neue additive Fertigungstechnologie. Trotz seiner Neuheit findet der keramische 3D-Druck jedoch seinen Weg in viele Branchen, von der Medizin und Zahnmedizin über die Luft- und Raumfahrt bis hin zu Luxusgütern.
Derzeit entwickeln nur eine Handvoll Unternehmen 3D-Drucktechnologien für Keramik. Ein solches Unternehmen ist der österreichische Hersteller Lithoz.
Wir haben uns mit dem CEO und Gründer von Lithoz, Dr. Johannes Homa, getroffen, um den aktuellen Stand des keramischen 3D-Drucks, einige seiner spannenden Anwendungen und die Vorteile des 3D-Drucks als digitale Fertigungstechnologie zu besprechen.
Können Sie uns etwas über Lithoz und Ihre Mission als Unternehmen erzählen?
Lithoz ist ein Technologieanbieter für den 3D-Druck von Hochleistungskeramik, das heißt, wir entwickeln und vertreiben Maschinen, Software und Materialien für den 3D-Druck von Keramik.
Wir sind in diesem Bereich eindeutig Weltmarkt- und Technologieführer.
Neben der Technologieentwicklung unterstützen wir unsere Kunden auch im Bereich der Anwendungsentwicklung.
Weder die AM-Community noch die Keramikindustrie waren an den 3D-Druck von Keramik gewöhnt. Wir unterstützen beide Seiten so gut wir können.
Wie sind Sie zur Gründung von Lithoz gekommen?
Die Technologie wurde bereits 2006 an der TU Wien in Zusammenarbeit mit dem Dentalunternehmen Ivoclar Vivadent AG entwickelt.
2010 gelang uns dann der Durchbruch:Wir konnten Keramiken mit den gleichen Materialeigenschaften wie in der konventionellen Umformtechnik im 3D-Druck drucken. Dieser Meilenstein hat uns ermutigt, Lithoz als Unternehmen für den 3D-Druck von Hochleistungskeramiken auszugliedern.
Können Sie die von Lithoz entwickelte Technologie ein wenig erläutern?
Unsere Technologie basiert auf einem Photopolymerisationsverfahren, das der konventionellen Stereolithographie sehr ähnlich ist. Der Unterschied besteht darin, dass bei unserer Technologie die Keramikpartikel in einem lichtempfindlichen Harz dispergiert werden.
Während des Druckprozesses wird dieser Verbundwerkstoff Schicht für Schicht durch Licht verfestigt. Das Teil, das aus unserem 3D-Drucker kommt, wird als Grünkörper bezeichnet, was bedeutet, dass es noch kein fertiges Produkt ist.
Der Grünling muss einer Wärmebehandlung unterzogen werden, bei der ein Teil in einem speziellen Ofen gebrannt wird. Technisch entbindern und sintern wir das Teil, um die gewünschten Eigenschaften eines Keramikteils zu erreichen.
Beim Entbindern brennt man den Binder ab und sintert dann die Keramik bis zur vollen Dichte. Das Teil unterliegt einer Schrumpfung, dies ist jedoch ein normales Phänomen bei keramischen Umformprozessen.
Können Sie einige Beispiele für Anwendungen nennen, die mit Ihrer Technologie erreicht wurden?
Wir sind in drei verschiedenen Branchen tätig. Der erste ist medizinisch, wo wir resorbierbare und nicht resorbierbare Implantate und Medizinprodukte anbieten. Resorbierbare Implantate sind beispielsweise seit 2017 im Einsatz. Nicht resorbierbare Implantate sind dagegen bioinert, dh sie reagieren nicht mit dem menschlichen Körper.
Außerdem ist die Wärmeleitfähigkeit von Keramik eher gering. Ein weiterer Vorteil von Keramikimplantaten im Vergleich zu Metallimplantaten besteht darin, dass Menschen bei direkter Sonneneinstrahlung oder beim Duschen keine Schmerzen verspüren.
Die dritte medizinische Anwendung sind Medizinprodukte, bei denen einige isolierende, nicht magnetische Eigenschaften der Keramik benötigt werden. Keramiken sind ideal für die medizinische Industrie, da sie bioinert sind und keine allergischen Reaktionen hervorrufen, wie dies bei Metallen oder Kunststoffen der Fall sein kann.
Ein weiterer Bereich, auf den wir uns konzentrieren, ist das Gießen von Kernen für Turbinenschaufeln. Turbinenschaufeln verfügen über ein internes Kühlsystem, um die Schaufel während des Betriebs abzukühlen. Mit dem zunehmenden Trend zur Effizienzsteigerung durch Temperaturerhöhung wurden die Konstruktionen solcher Kühlsysteme immer ausgefeilter.
Der Grad an Raffinesse bedeutet, dass die Designs nicht mehr spritzgegossen werden können und einen neuen Herstellungsansatz erfordern, um sie produzieren zu können. Die additive Fertigung erweist sich für diese Kerne als ideale Lösung.
Ein weiterer Schwerpunkt für uns ist die Technische Keramik. Dies sind hochentwickelte Keramikmaterialien, die in allem verwendet werden, von Satellitenkomponenten wie Spiegelhaltern und Hochfrequenzkomponenten bis hin zu Maschinenbauteilen, beispielsweise für Textilmaschinen und Halbleitermaschinen.
Das bedeutet, dass es für unsere Technologie ein breites Anwendungsspektrum bis hin zu Luxusgütern gibt.
Kann diese Technologie auch bei Metallen eingesetzt werden?
Das ist eine großartige Frage.
Unsere Philosophie ist, dass wir unsere Technologie dem Pulver anpassen und nicht umgekehrt.
Das bedeutet, dass wir unsere Technologie an Metalle anpassen konnten. Wir waren so erfolgreich, dass wir sogar einen Spin aus dem Unternehmen gemacht haben.
Jetzt gibt es ein Unternehmen namens Incus, das 3D-Metalldruck mit einem Photopolymerisationsansatz durchführt. Mit dieser Technologie können hohe Auflösungen, gute mechanische Eigenschaften und hohe Präzision erreicht werden, wodurch Teile vergleichbar mit Metallspritzgussteilen werden.
Wie ist der aktuelle Stand des keramischen 3D-Drucks in Bezug auf das Verständnis der Technologie?
Keramischer 3D-Druck ist eine der jüngsten Technologien im 3D-Druck, daher ist die Wissensbasis noch nicht so weit entwickelt.
Trotzdem erhielt ich gerade heute eine E-Mail von einem Kunden, der ein Treffen mit seinem C-Level-Manager hatte und der überrascht war, dass das Potenzial für den 3D-Druck von Keramikteilen in seinem Unternehmen größer ist als für Metallteile .
Wir sehen, dass es viele Anwendungen gibt, aber keramisches AM ist in der 3D-Druckindustrie noch nicht so bekannt.
Dies beginnt sich jedoch zu ändern. Die Leute haben gesehen, dass es bei Kunststoffen und Metallen Einschränkungen gibt, die durch Keramik überwunden werden können.
Wie würden Sie einem Unternehmen raten, das das Potenzial des keramischen 3D-Drucks oder des 3D-Drucks untersucht? allgemeiner, aber Sie wissen nicht, wo Sie mit der Einführung der Technologie anfangen sollen?
Das ist eine sehr schwierige Frage, denn der Business Case liegt meist nicht direkt auf Ihrem Schreibtisch. Der einfachste Weg, um loszulegen, besteht darin, den 3D-Druck für Prototypen zu erkunden. Auf diese Weise können Sie mit dem Erlernen der Technologie beginnen.
Dann beginnen Sie, mit Kunden zu sprechen und Ihr Portfolio zu durchsuchen, um herauszufinden, welche Teile für den 3D-Druck sinnvoll sind. Die größte Herausforderung besteht darin, ein für die additive Fertigung geeignetes Teil zu finden. Aus gestalterischer Sicht sollte dieses Teil sehr anspruchsvoll sein und im Idealfall nicht mit anderen Technologien hergestellt werden.
Wenn Sie es gefunden haben, haben Sie einen Wettbewerbsvorteil. Zusammenfassend lässt sich sagen, dass Sie nicht nur nach niedrig hängenden Früchten suchen, sondern ein Projekt, das Sie in Ihrem Unternehmen aufbauen. Und zwar eher von oben nach unten und nicht von unten nach oben.
Am Anfang kann es schwierig sein, das volle Potenzial von AM zu erkennen. Jedes Unternehmen, das den 3D-Druck einführt, muss einige Anstrengungen unternehmen, um dieses Potenzial auszuschöpfen. Aber wenn Sie einen geeigneten Anwendungsfall gefunden haben, öffnet er Ihnen viele Türen.
Welche Herausforderungen gibt es beim 3D-Druck von Keramik?
Ein Problem, mit dem wir oft konfrontiert sind, ist, dass Menschen 3D-Druckteile wünschen, die in konventionellen Umformtechnologien bereits etabliert sind. Daher sind sie überrascht, dass die additive Fertigung tendenziell teurer ist als konventionellere Technologien.
Es muss verstanden werden, dass die Reproduktion eines traditionell hergestellten Teils mit Hilfe des 3D-Drucks es in den meisten Fällen nicht billiger macht.
Eine weitere Herausforderung besteht darin, dass wir materialwissenschaftliche Probleme mit Hilfe der additiven Fertigung nicht lösen können. AM ist nur eine Umformtechnologie. Es überwindet keine Probleme beim Sintern, das für die Keramikverarbeitung obligatorisch ist.
Zum Beispiel ist es einfach, Keramikteile aus mehreren Materialien in 3D zu drucken. Aber es wäre dann eine Herausforderung, diese Materialien gemeinsam zu sintern. Ich denke, solche Überlegungen werden manchmal unterschätzt.
Ein aktueller Bericht von SmarTech Analysis Staaten dass das Wachstum des keramischen 3D-Drucks weitgehend von der Endteilfertigung getrieben wird. Was sagst du dazu?
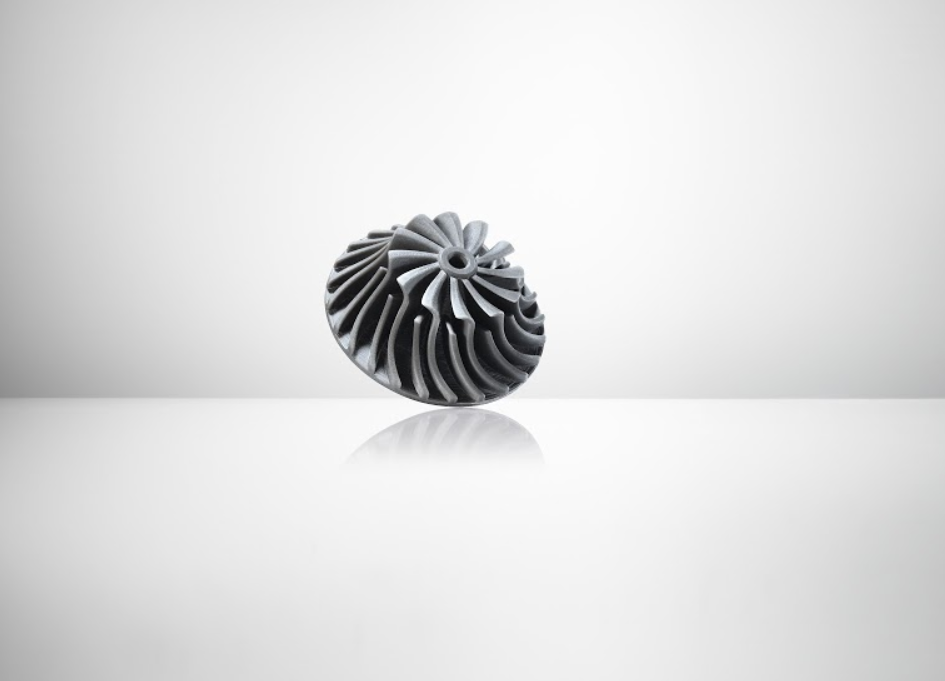
Ich stimme voll und ganz zu. Als wir vor 10 Jahren anfingen, hatte niemand eine Idee von Hochleistungskeramik-3D-Druck. Und jetzt sehen wir so viele Anwendungen, von denen selbst wir nichts wussten.
Ich bin fest davon überzeugt, dass Keramik die Materialien der Zukunft sind und wir erst am Anfang dieser Reise stehen. In den letzten 10 Jahren mussten wir zeigen und beweisen, dass 3D-Druck auch mit Keramik möglich ist, und jetzt beginnen die Leute, diese Technologie zu nutzen.
Was die Leute meiner Meinung nach auch sind Jetzt wird langsam klar, dass digitale Technologien wie AM eine Lösung für Sperren sein können, dank digitaler Inventarisierungen, die mit der Technologie möglich sind.
Können Sie ein wenig näher darauf eingehen, wie digitale Technologien? und 3D-Druck Unternehmen unterstützen können?
Während der COVID-19-Krise kam es zu einer Sperrung bestimmter Lieferanten. Im Spritzguss hat zum Beispiel ein Lieferant das Werkzeug und wenn Sie ein Teil erneut produzieren möchten, gehen Sie zu Ihrem Lieferanten und bitten ihn, weitere Teile für Sie zu fertigen und er wird dies in einer normalen Umgebung tun.
Aber die Situation mit COVID-19 macht die globale Lieferkette jetzt viel anfälliger und gestörter. Viele Unternehmen können ihre Lieferanten nicht erreichen oder die Lieferanten können keine Teile produzieren.
Auf der anderen Seite ist bei der additiven Fertigung das einzige Werkzeug, das Sie verwenden, die Maschine selbst. Die Maschine kann hier in Europa oder den USA, in Asien, im Grunde an jedem Ort stehen, und Sie müssen nur die Daten auf die Maschine übertragen und das Teil sofort ohne Werkzeug drucken.
Natürlich müssen Sie das Teil für AM qualifizieren, aber insgesamt bietet Ihnen die Technologie viel mehr Flexibilität.
Ein weiterer Punkt ist, dass die digitale Natur von AM es Ihnen ermöglicht, Konstruktionsdateien in einem virtuellen Speicher statt in einem physischen Inventar zu speichern und sie bei Bedarf auszudrucken.
Wie sehen Sie die Entwicklung des Keramik-3D-Drucks in den nächsten Jahren?
Ich denke, es liegt großes Potenzial vor uns. Allerdings muss keramisches AM im Gegensatz zu anderen AM-Technologien von Anfang an die Anforderungen an ein hochwertiges Bauteil erfüllen.
Denn wenn Sie ein Keramikteil benötigen, muss es die gleichen Materialeigenschaften aufweisen wie in der konventionellen Fertigung, auch wenn es nur ein Prototyp ist. Dies liegt daran, dass Sie es in einer rauen Umgebung wie hohen Temperaturen oder einer korrosiven Umgebung verwenden würden.
Wenn Sie einen visuellen Prototyp haben möchten, würden Sie ihn nicht aus Keramik, sondern aus Kunststoff herstellen. Sie wollen mit Ceramics AM immer einen funktionalen Prototypenbau haben, deshalb haben wir von Anfang an die Produktion der Losgröße eins gemacht.
Was hält das kommende Jahr für Lithoz bereit?
Wir sehen zwei unterschiedliche Folgen der Pandemie für unser Geschäft.
Erstens haben wir gesehen, dass eine kleinere Gruppe unserer Kunden eine Pause in der additiven Fertigung eingelegt und sich auf andere Dinge konzentriert hat.
In einer anderen Gruppe sehen wir, dass jetzt mehr Unternehmen auf der Suche sind aufgrund der Vorteile digitaler Produktionstechnologien, wie der digitalen Lagerhaltung und der Möglichkeit, ihre Lieferkette zu stabilisieren, viel mehr in die additive Fertigung.
Während die aktuelle Lage schlecht für die Weltwirtschaft ist, sehe ich, dass Unternehmen jetzt das Potenzial der additiven Fertigung erkennen, weil die Menschen anfangen, anders zu denken und digitale Produktionstechnologien als Mittel zur Überwindung dieser Probleme in Betracht ziehen.
Für Lithoz glauben wir nicht, dass diese Krise große Auswirkungen auf unseren Umsatz und Umsatz haben wird. Die Zukunft sieht für uns sehr rosig aus.
Wir haben viele Projekte am Laufen, die wir derzeit noch nicht veröffentlichen können. Sie werden in Zukunft auftauchen und die Leute werden sehr überrascht sein, was mit dem keramischen 3D-Druck bereits möglich ist.
3d Drucken
- Interview mit einem Experten:Dr. Bastian Rapp von NeptunLab
- Experteninterview:Felix Ewald, CEO von DyeMansion
- Experteninterview:Duncan McCallum, CEO von Digital Alloys, über den Joule-Druck und die Zukunft des 3D-Metalldrucks
- Experteninterview:Nanoe CEO Guillaume de Calan über die Zukunft des keramischen 3D-Drucks
- Experteninterview:Ultimaker-Präsident John Kawola über die Zukunft des 3D-Drucks
- Experteninterview:Nano Dimension-Mitbegründer Simon Fried über den Aufstieg des 3D-Drucks für die Elektronik
- Experteninterview:CEO von PostProcess Technologies zur Lösung des Post-Processing-Engpasses für die additive Fertigung
- Experteninterview:Jabils Rush LaSelle zur Zukunft der additiven Fertigung
- Experteninterview:MELD Manufacturing CEO Nanci Hardwick über die Ausschöpfung des Potenzials der additiven Metallfertigung
- Experteninterview:Andy Kalambi, CEO von RIZE über die nachhaltige und skalierbare Gestaltung des industriellen 3D-Drucks