4 Wege zur Sicherstellung einer konsistenten Schnitttiefe
4 Möglichkeiten, um eine konsistente Schnitttiefe sicherzustellen (selbst auf Oberflächen, die alles andere als flach sind): Was Ihre CNC anbelangt, ist die Welt voller Sonnenschein und Rosen:Ihr Schneidwerkzeug biegt oder verschleißt nie, Ihre Vorrichtung ist starr und vibrationsfrei, und die Oberfläche Ihres Werkstücks ist perfekt eben. Diejenigen von uns mit grauen Zellen hier in der realen Welt wissen jedoch, dass die Wahrheit der Situation alles andere als perfekt ist – Werkzeuge verschleißen, Vorrichtungen biegen sich, und die Oberfläche, die Sie schneiden werden, ist ungefähr so flach wie die gute Erde selbst .
Das obige Video erklärt alles!
Video mit freundlicher Genehmigung von #rapiddtm – besuchen Sie sie auf Facebook!
Wenn Sie unserem Blog folgen, wissen Sie bereits, dass wir darüber gesprochen haben, wie man sich mit der Werkzeugablenkung auseinandersetzt, und einige Tipps zu Best Practices für die Werkstückspannung gegeben haben. Heute werden wir einige Tricks behandeln, mit denen Sie beim Gravieren, Markieren oder Fräsen von Oberflächen, die nicht gerade das Aushängeschild für Ebenheit sind, eine konsistente Schnitttiefe beibehalten können.
Ebenheit definieren:
Einfach ausgedrückt wird mit dem Begriff „Ebenheit“ ein Bereich zwischen zwei parallelen Linien bezeichnet, innerhalb dessen eine Fläche liegen muss. Diese Spezifikation funktioniert oft in Verbindung mit anderen dimensionalen Beschriftungen auf dem Druck, um den Bereich möglicher Positionen einer bestimmten Oberfläche zu beschreiben:
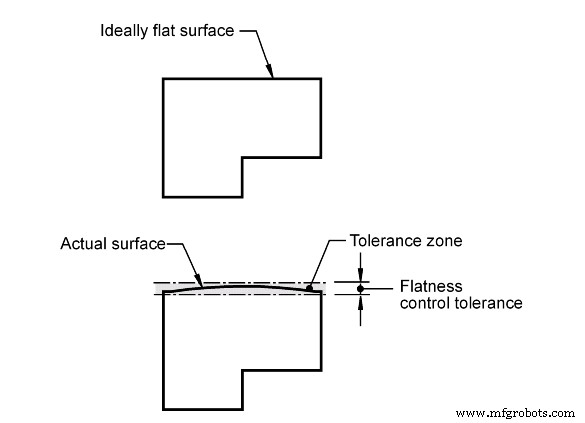
Bildnachweis:http://www.engineeringessentials.com/gdt/flatness/flatness.htm
Wie Sie vielleicht schon bemerkt haben oder auch nicht, ist keine Oberfläche perfekt eben – tatsächlich kommen nur sehr wenige Oberflächen einer perfekten Ebenheit nahe – und wenn es um gefertigte Teile geht, kostet Ebenheit Geld. Wenn es also nicht flach sein muss oder der Druck es nicht als flach definiert, müssen Sie davon ausgehen, dass es wirklich nicht flach ist. Je nachdem, was Sie mit einer bestimmten Oberfläche machen müssen, muss ihre Ebenheit (oder deren Fehlen) eine Schlüsselrolle in Ihrer Frässtrategie spielen.
Konsistente Schnitttiefe Methode 1:Qualifizieren Sie die Oberfläche
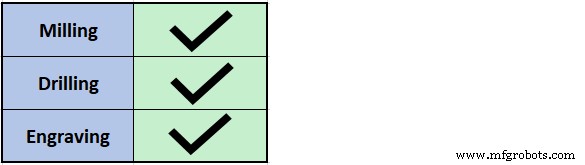
Wenn Sie dazu in der Lage sind, ist die Qualifizierung der Oberfläche bei weitem der einfachste und sicherste Weg, um sicherzustellen, dass die Oberfläche, auf der Sie arbeiten werden, einigermaßen eben und richtig ist. Das Qualifizieren einer Oberfläche ist nur ein ausgefallenes Maschinistengespräch für das Planfräsen der gesamten Oberfläche, wobei jeweils ein paar Tausendstel abgenommen werden, bis die gesamte Oberfläche in Bezug auf die Ebenheit einigermaßen gleichmäßig ist. Ein Qualifizierungspass ist oft der erste Schritt, den Sie sehen werden, wenn Sie einen Fräsprozess in einer Werkstatt oder online verfolgen, und dies aus mehreren Gründen, nicht zuletzt um die Ebenheit der betreffenden Oberfläche sicherzustellen.
Wenn Sie mit einem Stück Knüppel oder Rohmaterial beginnen, ist das Qualifizieren einer Oberfläche fast immer eine Option und im Allgemeinen nur eine gute Maschinistenpraxis. Manchmal ist die Qualifizierung der Oberfläche jedoch einfach keine Option – beispielsweise bei der Arbeit mit Druckgussmaterial, einem Schmiedestück oder mit anderweitig fertiggestellten Teilen, die lediglich gekennzeichnet oder serialisiert werden müssen. In diesen Fällen muss eine andere Strategie angewendet werden, um ein gutes Ergebnis zu erzielen.
Konsistente Schnitttiefe Methode 2:Verwendung eines federbelasteten Gravierwerkzeugs
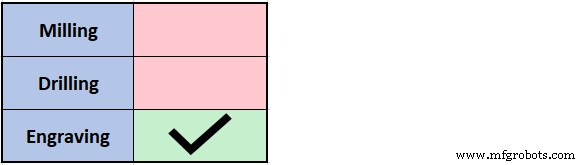
Wenn alles, was Sie tun müssen, ein einfacher Gravur- oder Teilemarkierungsprozess ist und Ihre Oberfläche ein wenig „überall auf der Karte“ ist, ist ein federbelastetes Gravierwerkzeug möglicherweise genau das, was der Arzt verordnet hat. Federbelastete Werkzeuge gibt es in einigen verschiedenen Varianten, wobei die beliebtesten Versionen eine federbelastete Version eines traditionellen Gravierwerkzeugs mit geteiltem Schaft und ein federbelasteter „Schleppgravur-Bit“, auch als „Anreißer“ bekannt, sind.
Federbelastetes Gravurwerkzeug:Mit diesem Werkzeug bleiben Sie bei einfachen Gravurarbeiten auf dem Laufenden.
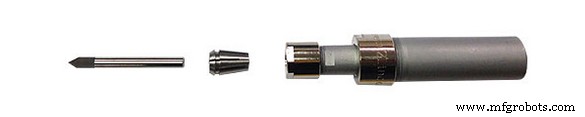
Federbelastete Gravierwerkzeuge enthalten ein zusammendrückbares mechanisches System zwischen der Spindelschnittstelle und dem Schneidwerkzeug. Diese Werkzeugbaugruppen haben normalerweise einen Federweg von 0,20 Zoll bis 0,40 Zoll, sodass sie eine ziemlich dramatische Änderung der Z-Höhe absorbieren können, während sie dennoch einen konstanten Abwärtsdruck auf das Werkstück ausüben. Gefederte Graviereinsätze verwenden ein spitzes Gravierwerkzeug mit geteiltem Schaft und können daher eine Vielzahl von Gravurbreiten und -tiefen erzeugen. Schleppgravier- oder Ritzwerkzeuge werden buchstäblich nur über eine Oberfläche gezogen und sind nicht dafür ausgelegt, ein Rotationselement in den Prozess einzubauen. Infolgedessen eignen sich Ritzwerkzeuge wirklich nur gut für sehr flache Teilemarkierungen.
Während diese Werkzeuge bei Fräs- oder Bohranwendungen nicht sehr hilfreich sind, eignen sie sich sehr gut zum Markieren von Teilen mit geringer bis mittlerer Tiefe. Diese Art von Werkzeug hat jedoch einige Nachteile:Eine übliche Schaftgröße für diese Werkzeuge ist ¾ Zoll, was für einige Spindeln zu groß sein kann. Da es sich bei diesen Werkzeugen um eine mechanische Baugruppe handelt, sind sie normalerweise auf maximal 10.000 U / min begrenzt. Diese Einschränkung kann Sie dazu zwingen, Ihre Vorschubgeschwindigkeit zu verlangsamen und Ihre Zykluszeit zu verlängern.
Wenn Sie also Werkzeuge für die Serialisierung von tausend Aluminiumgussteilen benötigen, wird ein federbelastetes Werkzeug wahrscheinlich die Arbeit erledigen. Wenn Sie jedoch vorhaben, einen Fräs- oder Bohrprozess durchzuführen, oder wenn die Arbeit eine tiefe, breite oder komplizierte/hochwertige Gravur erfordert, müssen Sie möglicherweise auf andere Methoden zurückgreifen, um die Arbeit zu erledigen.
Konsistente Schnitttiefe Methode 3:Verwenden eines Touch-Probing-Systems zur Kartierung einer unregelmäßigen Oberfläche
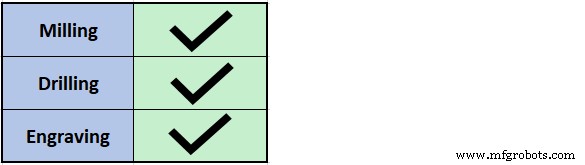
Bei der Oberflächenkartierung durch Berührungsantasten müssen Sie der Maschine normalerweise einige grundlegende Details darüber geben, was Sie antasten möchten:Größe des Antastbereichs, Abstand des Antastgitters und so weiter. Von dort berührt die Maschine das Werkstück so oft wie nötig, um den angegebenen Bereich mit dem gewünschten Rasterabstand zu prüfen. Sobald der Messzyklus abgeschlossen ist, nimmt die Maschinensteuerung die Schnittdatei, die zum Schneiden auf einer flachen 2D-Oberfläche programmiert wurde, und modifiziert sie mit der Z-Variation des Werkstücks, die während des Messzyklus gefunden wurde. Auf diese Weise variiert die Tiefe beim Fräsen oder Gravieren der Oberfläche automatisch, sodass Sie unabhängig von der Variation der Z-Höhe der Oberfläche eine konsistente Schnitttiefe erhalten.
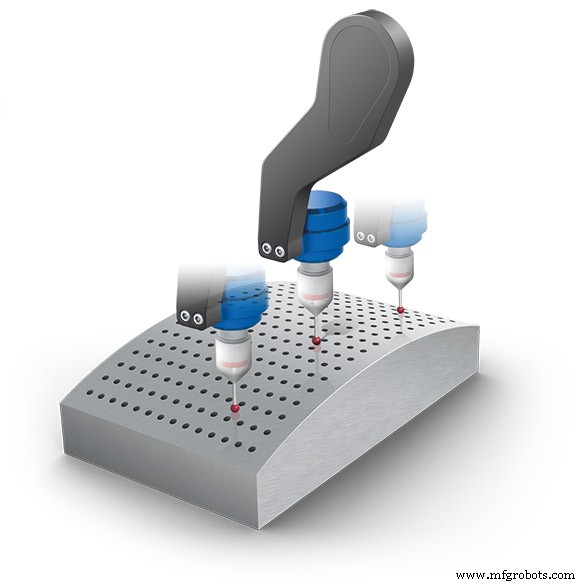
Nicht alle CNC-Maschinen bieten Berührungstastung an, und Oberflächenkartierung ist nicht immer eine Option, wenn dies der Fall ist. Aber wenn Ihre Maschine über Sondierung und Oberflächenkartierung verfügt, ist es keine schlechte Idee, sich damit vertraut zu machen – man weiß nie, wann es nützlich sein könnte.
Konsistente Schnitttiefe Methode 4:KMG-Oberflächenkartierung und Bildprojektion in Kamera
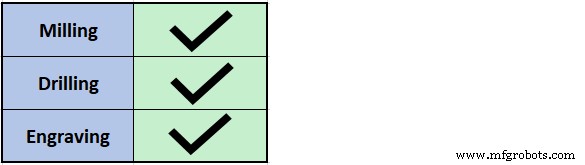
Wenn alles andere fehlschlägt … wenn Sie die Oberfläche nicht qualifizieren können, wenn ein federbelastetes Werkzeug nicht das tut, was Sie brauchen, und Ihre CNC-Maschine kein Tastsystem hat, wenn Sie ein einsatzbereites KMG herumliegen haben und es Ihnen nichts ausmacht, ein paar CAM-Arbeiten zu erledigen, es gibt eine Option als letzten Ausweg.
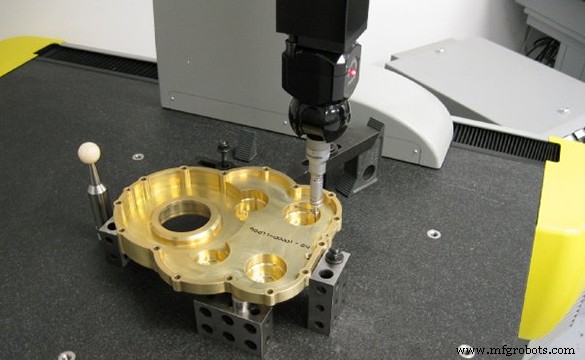
Foto oben mit freundlicher Genehmigung von #rapiddtm – besuchen Sie sie auf Facebook!
Die Verwendung eines KMG zum Abbilden einer Oberfläche zum Ausgleichen von Höhenunregelmäßigkeiten ist der Durchführung auf der CNC-Maschine selbst sehr ähnlich – jedoch wird der Prozess ohne den Luxus, Mapping, Fräsen und NC in einem Gerät integriert zu haben, viel arbeitsintensiver.
Dieser Prozess ist so aufwendig, dass allein dafür leicht ein ganzer Artikel geschrieben werden könnte. Um mich kurz zu fassen, reduziere ich es auf eine Schritt-für-Schritt-Zusammenfassung:
- 1. Laden Sie das Werkstück auf das KMG
- 2. Messen Sie manuell so viele Punkte wie nötig, um die volle Oberflächenvariabilität innerhalb des Arbeitsbereichs zu realisieren
- 3. Exportieren Sie die resultierende Punktwolke in Ihre CAD-Software
- 4. Erstellen Sie Splines, die die gemessenen Punkte verbinden, um eine 3D-Oberflächenkarte zu erstellen
- 5. Exportieren Sie die 3D-Oberflächenkarte in die CAM-Software
- 6. Projizieren Sie Grafiken / Fräsungen auf die 3D-Oberfläche
- 7. Generieren Sie benötigte Werkzeugwege und senden Sie die Schnittdatei an Ihre CNC
- 8. Laden Sie das Werkstück in die CNC und führen Sie das Teil aus
Um es klar zu sagen: Dieser Vorgang müsste für jeden Teillauf zu 100 % wiederholt werden. Wie Sie wahrscheinlich erkennen können, könnte die Verwendung dieser Methode eine Arbeit, die mit dem Tastsystem in der Maschine in etwa einem Tag von Anfang bis Ende erledigt wäre, leicht auf mehrere Tage ausdehnen – einfach aufgrund der mühsamen Natur der Notwendigkeit, ein KMG zur Kartierung der Oberfläche zu verwenden.
Nichts auf dieser Welt ist perfekt – aber die Fähigkeit, mit Unvollkommenheiten umzugehen, um ein gutes Ergebnis zu erzielen, egal was, ist eines der Dinge, die gute Maschinisten von großen unterscheiden. Ich hoffe, die in diesem Beitrag beschriebenen Methoden verschaffen Ihnen einen Vorteil, wenn Sie das nächste Mal mit einem Werkstück konfrontiert werden, das eher wie ein Kartoffelchip als wie ein Pfannkuchen aussieht.
CNC-Maschine
- Sechs Möglichkeiten zur Emissionsreduzierung bei Lagerung und Vertrieb
- Drei Möglichkeiten, wie E-Tailer die Versandkosten für Käufer senken können
- 8 Möglichkeiten, wie Sie Ihren Schaftfräser töten
- Eintauchen in die Schnitttiefe:Umfangs-, Schlitz- und HEM-Ansätze
- So stellen Sie Genauigkeit und Präzision beim CNC-Fräsen sicher
- 5 Wege zur Verlängerung der Werkzeuglebensdauer und Steigerung der Produktivität
- Wasserstrahl:Das vielseitigste Werkzeug im Shop
- Möglichkeiten zur Steigerung der Schlaglebensdauer
- 5 effektive Möglichkeiten zur Verlängerung der Standzeit von Stanzwerkzeugen
- Erläuterung der vollständigen Steuerung des G76-Gewindezyklus Anzahl der Durchgänge und der Schnitttiefe