Herstellung und Charakterisierung eines neuen anodischen Tio2-Kohlenstoff-Nanofaser-Verbundkatalysators für eine Direkt-Methanol-Brennstoffzelle mittels Elektrospinnverfahren
Zusammenfassung
Platin (Pt) ist der übliche Katalysator, der in einer Direkt-Methanol-Brennstoffzelle (DMFC) verwendet wird. Pt kann jedoch zu einer Katalysatorvergiftung durch kohlenstoffhaltige Spezies führen und verringert somit die Leistung von DMFC. Daher konzentriert sich diese Studie auf die Herstellung eines neuen zusammengesetzten TiO2 Anodischer Katalysatorträger aus Kohlenstoff-Nanofasern für Direkt-Methanol-Brennstoffzellen (DMFCs) mittels Elektrospinntechnik. Als Einflussparameter in der Elektrospinntechnik wurden der Abstand zwischen Spitze und Kollektor (DTC) und die Flussrate untersucht. Um sicherzustellen, dass das beste katalytische Material hergestellt wird, wurde die Nanofaser mehreren Charakterisierungen und elektrochemischen Tests unterzogen, darunter FTIR, XRD, FESEM, TEM und zyklische Voltammetrie. Die Ergebnisse zeigen, dass D18, hergestellt mit einer Flussrate von 0,1 mlh −1 und DTC von 18 cm, ist eine ultrafeine Nanofaser mit dem kleinsten durchschnittlichen Durchmesser von 136,73 ± 39,56 nm. Es zeigte die höchste Katalysatoraktivität und den höchsten elektrochemischen aktiven Oberflächenwert von 274,72 mAmg −1 . und 226,75 m 2 g −1 PtRu , bzw. verglichen mit den anderen Proben.
Hintergrund
Die Direkt-Methanol-Brennstoffzelle (DMFC) ist eines der erneuerbaren Stromerzeugungssysteme der Zukunft und sehr umweltfreundlich. Das System erzeugt elektrische Energie direkt aus einem flüssigen Brennstoff (Methanol) ohne zusätzliche Geräte oder Verbrennungsprozesse. Die Vorteile von DMFCs sind ihre Einfachheit, hohe spezifische Energie, niedrige Betriebstemperatur und einfache Inbetriebnahme mit sofortiger Betankung [1]. DMFC-Systeme leiden jedoch immer noch unter mehreren Einschränkungen, wie Katalysatorvergiftung und langsamer Reaktionskinetik, die zu einer geringen Leistung und Leistungsabgabe des Systems führen [2]. Beide Einschränkungen sind auf den Katalysator und das Material zurückzuführen, das in diesem System verwendet wird.
Platin (Pt) ist der übliche Katalysator, der in DMFC verwendet wird. Pt kann jedoch zu einer Katalysatorvergiftung durch kohlenstoffhaltige Spezies führen und verringert somit die Leistung von DMFC. Später wird Platin-Ruthenium (PtRu) eingeführt, um die Reaktionsgeschwindigkeit zu erhöhen, aber der kinetische Parameter des Katalysators ist immer noch eines der Hauptprobleme bei DMFC. Daher beginnt die Umstellung auf diesen bimetallischen Katalysator im Bereich der DMFC-Katalysatoren. Einer der attraktivsten Ansätze unter Forschern ist die Einführung von Metalloxiden und Nanomaterialien als Nebenkatalysatorkomponente. Titandioxid (TiO2 .) ) ist ein Metalloxid, das von Forschungsentwicklern viel Aufmerksamkeit erregt. TiO2 hat verschiedene vorteilhafte Eigenschaften, die nicht toxisch, nicht brennbar und sehr korrosionsbeständig sind [1], die elektrochemische und thermische Stabilität erhöhen [3] und die elektronischen Eigenschaften und den bifunktionellen Mechanismus von Verbundkatalysatoren beeinflussen können [4]. Ito et al. [5] entwickelte PtRu/TiO2 -Embedded Carbon Nanofiber (CNF) (PtRu/TECNF) und Ercelik et al. [6] präsentierte das PtRu/C-TiO2 als Elektrokatalysator in DMFC-Anwendungen, und das Ergebnis zeigt, dass die Leistung dieses neuen Verbundelektrokatalysators höher ist als die des PtRu-Katalysators.
Nanomaterial ist eine der Nanotechnologien, die in einem breiten Anwendungsbereich, einschließlich der Energieumwandlung, fasziniert hat. Auf dem Gebiet der Energieumwandlung gibt es zahlreiche Arten von Nanomaterialien, nämlich Nanofasern, Nanoröhren, Nanodrähte, Nanostäbe und andere. Dieses Material wird zur Hauptattraktion in der Energiematerialforschung aufgrund der Dimensionsreduktion auf die Nanometerskala, die viele elementare Schritte beeinflussen kann, einschließlich Ladungstransfer und molekulare Umlagerung, sowie die Oberflächeneigenschaften, die hohe Grenzflächenvolumenanteile und verbesserte Reaktionsgeschwindigkeiten bieten [ 7]. Diese Studie konzentriert sich auf Nanofaserstrukturen für beide Materialien, TiO2 Metalloxid und Kohlenstoff. Dies ist auf die besonderen Eigenschaften von Nanofasern zurückzuführen, die ein hohes Oberflächen-/Volumen- und Aspektverhältnis [7], eine hohe elektrische Leitfähigkeit, eine gute mechanische Festigkeit und eine gleichmäßige Dispersion des Katalysators bieten können, was die elektrokatalytische Aktivität erhöhen kann [8].
Nanofasern können durch verschiedene Verfahren hergestellt werden, darunter Schmelzblasen, Grenzflächenpolymerisation, Elektrospinnen und durch Antilösungsmittel induzierte Polymerfällung [9]. In letzter Zeit ist das Elektrospinnen aufgrund des großen Vorteils der Herstellung ultrafeiner Nanofaserstrukturen die erste Wahl unter Forschern. Elektrospinnen ist ein einzigartiges Verfahren zur Bildung von Fasern mit submikrometergroßen Durchmessern (im Nanometer- bis Mikrometerbereich) unter Verwendung polymerbasierter Lösungen oder Schmelzen durch elektrostatische Kräfte [10]. Es gibt drei Hauptkomponenten für das Elektrospinnen:eine Hochspannungsversorgung (mehrere zehn kV), die Spinndüse (Spritze mit einer Nadel) und einen geerdeten Kollektor (z. B. Platte oder rotierender Kollektor) [11, 12]. Abbildung 1 veranschaulicht den Gesamtprozess und die Einrichtung für den Elektrospinnprozess. Daher ist das Elektrospinnen aufgrund seines einfachen Verfahrens, seiner Vielseitigkeit, seiner hohen Ausbeute, seiner Effektivität und seines wirtschaftlicheren Verfahrens beliebt [7, 13].
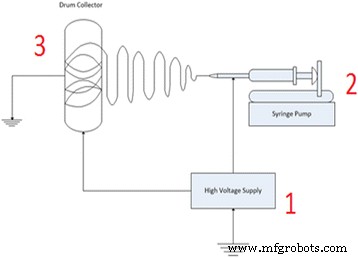
Elektrospinning-Setup für alle Hauptkomponenten
Dieser Prozess hat mehrere Parameter, die abgestimmt werden können, um die optimalen Nanofaserstrukturen entweder für Durchmesser oder Oberflächenmorphologie zu erhalten, und die Einflussparameter sind für jedes Material unterschiedlich. Die Parameter können in drei Hauptkategorien unterteilt werden:Lösungs-, Umgebungs- und Prozessparameter. Diese Studie konzentriert sich auf Prozessparameter, und die Lösungsflussrate und der Abstand zwischen der Nadelspitze und dem Kollektor (DTC) wurden als die wichtigsten Einflussparameter gewählt, um den kleinsten Durchmesser zu erhalten. Dies liegt an der geringen Menge an Forschung, die sich auf diese Parameter konzentrierte [14], obwohl sie als Hauptvariablen für die Gewinnung ultrafeiner Nanofasern angesehen wurden [15,16,17,18].
Daher präsentiert diese Studie das zusammengesetzte TiO2 Kohlenstoffnanofaser als Katalysatorträger auf der Anodenelektrode. Von dieser Kombination des Verbundstoffs wird erwartet, dass sie die elektrokatalytische Aktivität erhöht und die Katalysatorvergiftung verringert, um die Gesamtleistung von DMFC zu steigern. Die Hauptziele dieser Studie sind die Herstellung des kleinstmöglichen Nanofaserdurchmessers, um die Oberfläche zu vergrößern und einen aktiveren Punkt für die katalytische Reaktion bereitzustellen und die DMFC-Leistung zu verbessern. Die Herstellung von Nanofasern umfasst mehrere Schritte, darunter Sol-Gel-, Elektrospinnen-, Stabilisierungs- und Karbonisierungsprozesse. Um Nanofasern mit dem kleinsten Durchmesser zu erhalten, werden die Elektrospinnparameter Durchflussrate und DTC als Hauptvariablen in dieser Studie verwendet. Die präparierten Nanofasern werden durch Fourier-Transform-Infrarot-(FTIR)-Spektroskopie, Röntgenbeugung (XRD) und Rasterelektronenmikroskopie (FESEM) charakterisiert. Alle Katalysatorträger mit unterschiedlichen Elektrospinnparametern werden auf PtRu (PtRu/TiO2 -CNF) und bewertet durch elektrochemische Analyse der aktiven Oberfläche (ECSA) und Cyclovoltammetrie (CV), um die Leistung zu bewerten und ihr Potenzial als Katalysatorträger in DMFCs zu bestimmen. Die experimentellen Ergebnisse zeigen den Einfluss der Elektrospinnparameter auf den Nanofaserdurchmesser sowie deren Potenzial in DMFC-Anwendungen.
Methoden/Experimental
Materialien
Es wurden Poly(vinylacetat) (PVAc, Mw = 500.000), Dimethylformamid (DMF, 99,8%), Titanisopropoxid (TiPP, 97% Gehalt), Essigsäure (99,7%) und Ru-Vorstufe (45–55% Gehalt) erhalten von Sigma-Aldrich Co., Ltd., während Pt-Vorläufer (40% Gehalt) und Ethanol (99,8%) von Merck, Deutschland bzw. R&M Chemical Reagents bezogen wurden. Alle Chemikalien wurden ohne weitere Reinigung verwendet. Das Hauptgerät, die Elektrospinnmaschine, trägt die Marke Nfiber N1000, Progene Link Sdn. Bhd., und der Ultraschall-Zellbrecher INS-650Y stammt von INS Equipments Trading Co., Ltd., China.
Vorbereitung von TiO2 -CNF-Nanofasern
Das Sol-Gel-Verfahren beginnt mit der Herstellung einer Polymerlösung, bei der PVAc (11,5 Gew.-%) als Kohlenstoffquelle in dem Lösungsmittel DMF gelöst wurde. Die Polymerlösung wurde 1 h bei 60 °C gerührt und dann über Nacht bei Raumtemperatur gerührt. Das TiO2 Precursor, TiPP und Polymerlösung wurden im Verhältnis 1:1 gemischt und der Polymerlösung wurde eine kleine Menge Essigsäure und Ethanol zugesetzt. Die Mischung wurde 60 s lang mit einem Ultraschall-Zellbrecher homogenisiert. Dann wurde die Lösung zur Injektion in eine Nanofaser-Elektrospinneinheit in eine Spritze überführt. Die angelegte Spannung betrug 16 kV, während die Flussrate und der DTC im Bereich von 0,1–0,9 mLh –1 . manipuliert wurden und 14–18 cm. Die Flussrate wurde auf 0,1, 0,5 , . eingestellt und 0,9 mLh −1 , bezeichnet mit F0.1, F0.5 bzw. F0.9. Die Proben mit DTC-Werten von 14, 16 und 18 cm werden als D14, D16 bzw. D18 bezeichnet. Die hergestellte Nanofaser wurde 5 h bei Raumtemperatur ruhen lassen, bevor sie 8 h bei 130 °C stabilisiert wurde. Die stabilisierte Nanofaser wurde bei 600 °C 2 h lang unter Stickstoffatmosphäre in einem Röhrenofen karbonisiert und dann vor der weiteren Verwendung in dieser Studie 5 Minuten lang mit Mörser und Stößel zerkleinert. Die Massenbeladung für alle Proben ist gleich und beträgt 6,67 mg −1 .
Ablagerung des Katalysators
Das TiO2 -CNF-Nanofasern wurden in eine Mischung aus Isopropylalkohol (IPA) und entionisiertem Wasser (DI-Wasser) gegeben und 20 Minuten lang in einem Ultraschallbad beschallt. Die Vorstufe des Platin- und Rutheniumkatalysators (20 Gew.-% im Verhältnis 1:1) wurde in die Lösung eingemischt und 20 Minuten gerührt. Dann wurde der pH-Wert der gemischten Lösung mit NaOH-Lösung eingestellt, bis pH 8 erreicht wurde. Die Temperatur wurde auf 80 °C erhöht, und 25 ml 0,2 M NaBH4 wurde tropfenweise in die gemischte Lösung gegeben. Die Lösung wurde noch 1 h gerührt. Die Mischung wurde dann abgekühlt, filtriert und wiederholt gewaschen. Das Katalysatorpulver wurde 3 h bei 120 °C getrocknet und schließlich mit Mörser und Stößel zerkleinert, um ein feines Katalysatorpulver zu erhalten, das für die Leistungstests einsatzbereit war.
Charakterisierung des Katalysators
Die chemische Verbindung im Katalysatorträger wurde mittels Fourier-Transform-Infrarotspektroskopie (FTIR, PerkinElmer) und Röntgenbeugung (XRD, D8 Advance/Bruker AXS, Deutschland) identifiziert, um das Muster und die Kristallstruktur der Proben zu analysieren. Die Morphologie und Größenverteilung der Proben wurden durch Feldemissions-Rasterelektronenmikroskopie (FESEM, SUPRA 55VP) analysiert. Mithilfe von Transmissionselektronenmikroskopie (TEM, Tecnai G2 F20 X-Twin) wurde die detaillierte Struktur und Elementverteilung der Nanofasern beobachtet.
Auswertung der elektrochemischen Messung
Die Leistung wurde für alle Katalysatoren gemessen, die mit unterschiedlichen Parametern hergestellt wurden. Der PtRu-Katalysator wurde auf dem TiO2 . abgeschieden -CNF-Katalysatorträger zur Auswertung durch elektrochemische Messungen. Diese Messungen wurden unter Verwendung eines Drei-Elektroden-Zellsystems durchgeführt, das zyklische Voltammetrie (CV) verwendet, um die Katalysatoraktivität in der Methanoloxidationsreaktion (MOR) unter Verwendung einer elektrochemischen Workstation von Autolab zu untersuchen. Das Drei-Elektroden-Zellsystem wurde bei Raumtemperatur betrieben und umfasste eine Pt-, Silber/Silberchlorid- (Ag/AgCl) und Glaskohlenstoffelektrode (GCE, 3 mm Durchmesser) als Gegen-, Referenz- und Arbeitselektrode. Vor Beginn der Messung wurde der GCE mit Aluminiumoxid und Polierpapier gereinigt, wobei mehrmals ein abgerundetes Muster gezeichnet wurde, das der Zahl „acht“ ähnelte. Dann wurde das GCE mit DI-Wasser gespült und vor der Verwendung 30 s lang beschallt. Die Katalysatortinte für die GCE wurde hergestellt, indem 15 mg Katalysator in einer Mischung aus 400 μl DI-Wasser, 400 μl IPA und 125 μl Nafion-Lösung (5 Gew.-%) 30 Minuten lang dispergiert wurden. Dann wurden 2,5 μl Katalysatortinte mit einer Mikropipette auf die GCE aufgetragen und 1 h bei Raumtemperatur getrocknet, bevor sie weitere 30 Minuten auf 80 °C erhitzt wurde. Der Elektrolyt war eine Lösung von 0,5 M H2 . SO4 in 2 M Methanol, und es wurde 20 Minuten lang mit Stickstoffgas geperlt, um jeglichen Sauerstoff zu entfernen. Die CV-Messung wurde über einen Potenzialbereich von − 0,1–1,1 V vs. Ag/AgCl bei einer Abtastrate von 50 mVs −1 . durchgeführt .
Ergebnisse und Diskussion
Strukturelle Charakterisierung
Auswirkung der Flussrate
Am TiO2 . wurde FTIR-Spektroskopie durchgeführt -CNF-Proben zur Identifizierung der vorliegenden chemischen Verbindungen. Die IR-Spektren der Proben, die bei verschiedenen Flussraten hergestellt wurden, sind in Abb. 2 gezeigt. Die Spektren zeigten chemische Bindungssignale, die für TiO2 . repräsentativ sind und Kohlenstoff. Die mittleren und breiten Peaks bei 3200–3600 cm −1 stellen funktionelle O-H-Gruppen dar, während die scharfe und starke C=O-Absorptionsbande im Bereich von 1550–1850 cm −1 . lag [19]. Peaks für Alkane (C-H-Gruppen) sind schwach und breit und liegen im Bereich von 1300–1450 cm −1 . C-C-Gruppen treten jedoch angeblich bei sehr niedrigen Wellenzahlen auf, unter 500 cm −1 [19] und sind in den Spektren aufgrund des kleinen Wellenzahlbereichs (4000 cm −1 .) nicht vorhanden < wavenumber > 50 cm −1 ) durch das Spektrum erzeugen. Die mittleren und scharfen Bänder im Bereich von 650–900 cm −1 gehören zu Ti-O-Gruppen, wie von Ding et al. [20]. Die IR-Spektren zeigen alle funktionellen Gruppen des TiO2 -CNF-Proben. Alle Proben haben ähnliche Wellenzahlen und Peaks, was darauf hindeutet, dass die Flussrate der Polymerlösung während des Elektrospinnens die chemischen Verbindungen in der Probe nicht beeinflusst.
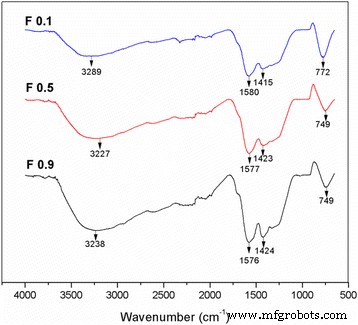
Die IR-Spektren für das TiO2 -CNF-Probe mit unterschiedlichen Durchflussparametern im Bereich von 650 bis 4000 cm −1 Wellenzahl
Das TiO2 -CNF-Proben, die mit Durchflussraten von 0,1, 0,5 , . hergestellt wurden und 0,9 mlh −1 werden mit F0.1, F0.5 bzw. F0.9 bezeichnet. Abbildung 3 zeigt die XRD-Muster von TiO2 -CNF-Katalysatorträger mit unterschiedlichen Durchflussraten hergestellt. Abbildung 3a ist eine einzelne Probe für den Katalysatorträger, bei der es sich um eine F0.1-Probe handelt, um das XRD-Muster in Nahaufnahme mit dem gesamten Peakmaterial in TiO2 . zu betrachten -CNF, während Abb. 3b die gesamte betroffene Flussratenprobe darstellt. Die Existenz von TiO2 und Kohlenstoff in der Probe ist gekennzeichnet. Das TiO2 besteht aus zwei Strukturen, Anatas und Rutil, da die Karbonisierungstemperatur eine kleine Menge Anatas TiO2 . umwandelt in Rutil-TiO2 . Die Beugungspeaks für Anatas TiO2 sind 25° (101), 38° (112), 48° (200), 53,9° (105), 62° (213) und 68° (116), während die für Rutil, TiO2 sind 27° (110), 36° (101), 41° (111) und 54° (211). Die Kohlenstoffquelle wird durch mehrere Beugungspeaks angezeigt, einschließlich derjenigen bei 30° (110) und 55° (211). Anatas und Rutil TiO2 bildete eine tetragonale Struktur, während sich Kohlenstoff in der kubisch-flächenzentrierten kristallographischen Struktur befand.
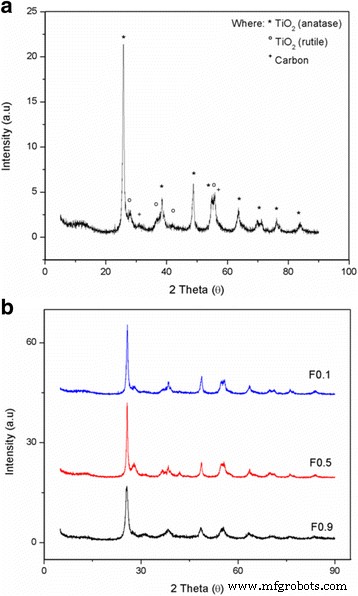
Röntgenbeugungsmuster von a einzelnes TiO2 -CNF-Probe und b Beispiel für verschiedene Durchflussraten
Es wurde festgestellt, dass die Flussrate bei der Elektrospinntechnik den Nanofaserdurchmesser beeinflusst, der mit FESEM-Analyse berechnet wurde. Das FESEM-Bild ist in Abb. 4 dargestellt, während die Ergebnisse der Größenverteilung und des Durchmessers in Abb. 5 und Tabelle 1 gezeigt sind. Das Bild bestätigt, dass die Nanofaserstruktur bei allen untersuchten Flussraten gebildet wurde. Die F0.1-Nanofasern zeigten aufgrund der langsameren Fließgeschwindigkeit eine glatte Morphologie, die dem Lösungsmittel genügend Zeit zum Verdunsten gibt, was zur Bildung der glatten Struktur beiträgt. Der mittlere Nanofaserdurchmesser aus 100 Messungen beträgt 161,18 ± 26,08 nm, was der kleinste Durchmesser unter den Proben ist, die bei unterschiedlichen Flussraten hergestellt wurden. Das FESEM-Bild von F0.5 zeigt jedoch die Bildung von flachen Bändern auf den Nanofasern aufgrund der fehlenden Verdunstung aus dem Kern, dh das Lösungsmittel wird im Kern eingeschlossen und diffundiert in die Umgebungsatmosphäre, um die flache Bandstruktur zu verursachen [ 21]. F0.9 zeigt rauere Nanofasern mit ungleichmäßigen Durchmessern und mehrere Kügelchen, die auf der Nanofasermorphologie gebildet wurden. Dies tritt auf, wenn die Durchflussmenge viel höher als der optimale Wert ist, wodurch die Trocknungszeit verkürzt wird, bevor die Faser den Kollektor erreicht. Die mittleren Nanofaserdurchmesser von F0.5 und F0.9 waren höher als die von F0.1, die 220,28 ± 38,01 bzw. 286,33 ± 50,83 nm betrugen. Das FESEM-Bild zeigt, dass der Durchmesser der Nanofasern mit zunehmender Flussrate während des Elektrospinnens zunimmt. F0.1 mit einer Durchflussrate von 0,1 mLhr –1 , wurde zur weiteren Analyse der Wirkung von DTC auf den Nanofaserdurchmesser verwendet.
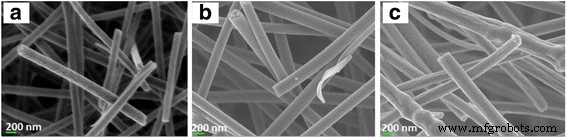
FESEM-Bild von a TiO2 -CNF (F0.1), b TiO2 -CNF (F0.5) und c TiO2 -CNF (F0.9) bei 30.000-facher Vergrößerung
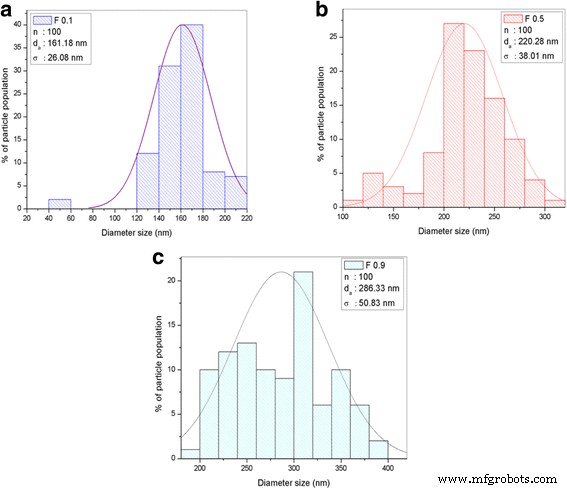
Histogrammdaten der Durchmessergrößenverteilung mit dem Parameter n, da , und . a TiO2 -CNF (F0.1). b TiO2 -CNF (F0.5). c TiO2 -CNF (F0.9)
Auswirkung des Abstands zwischen Spitze und Kollektor
Das synthetisierte TiO2 -CNF-Katalysatorträger wurden durch FTIR analysiert, um die chemische Bindung in den Proben zu bewerten, und die IR-Spektren der Proben sind in Abb. 6 dargestellt. Die IR-Spektren zeigen drei Proben mit unterschiedlichen DTC-Parametern nach dem Carbonisierungsprozess. Alle synthetisierten Proben zeigen die Existenz von O-Ti-O- und Carbonationen-Bindungen, wobei die Peaks und Wellenzahlen in den Spektren im gleichen Bereich lagen wie bei den Proben F0.1, F0.5 und F0.9 in den Vorherige Sektion. Die Wellenzahlen waren nahe genug, um die Ähnlichkeit der Proben anzuzeigen, einschließlich der Proben, die bei unterschiedlichen Durchflussraten in Abb. 2 erzeugt wurden. Probe D14 zeigt jedoch ein neues Maximum bei 2300–2400 cm −1 , die die N-H-Streckschwingungen anzeigen. Dieser Peak kann als Peak der tertiären Aminsalze kategorisiert werden, bei dem die N-H-Bindung schwach ist und keinen praktischen Wert hat, der vernachlässigt werden kann [19]. Das Vorhandensein dieser Bindung könnte auf die unvollständige Entfernung der Lösungsmittelverbindung während des Carbonisierungsprozesses zurückzuführen sein. Diese Beobachtung zeigt, dass die Elektrospinnparameter Durchflussrate und DTC die chemische Bindung in den Proben nicht beeinflussen.
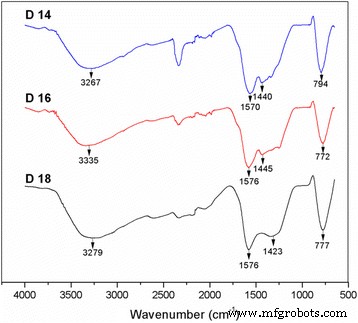
Das IR-Spektrum für das TiO2 -CNF-Probe mit unterschiedlichem DTC-Parameter im Bereich von 650 bis 4000 cm −1 Wellenzahl
Die Kristallinität von TiO2 -CNF-Katalysatorträger wurden analysiert. Die XRD-Muster sind in Abb. 7a für eine einzelne Probe und in Abb. 7b für DTC gezeigt. Die einzelne Probe in Abb. 7a zeigt das Nahaufnahme-XRD-Muster für DTC 18 an, um den Existenzpeak für alle beteiligten Materialien zu sehen. Die am Katalysatorträger beteiligten Materialien, TiO2 und Kohlenstoff, in jeder Probe nachgewiesen werden. Die Beugungspeaks wurden über einen 2θ-Bereich von 5° bis 90° untersucht, und die Peaks bei 31° (110) und 55° (211) zeigen an, dass Kohlenstoff mit einer kristallographischen FCC-Struktur im Katalysatorträger vorhanden ist. Der scharfe Beugungspeak bei 25° (101) wurde TiO2 . zugeschrieben in Anatas-Form, und es gibt mehrere andere Peaks für Anatas-TiO2 , einschließlich der bei 38 ° (004), 48 ° (200), 53 ° (105), 55 ° (211), 63 ° (204) und 69 ° (116). Die anderen vier Beugungspeaks bei 27° (110), 36° (101), 41° (111) und 54° (211) gehören zu Rutil-TiO2 . Sowohl Anatas als auch Rutil-TiO2 haben eine tetragonale kristallographische Struktur.
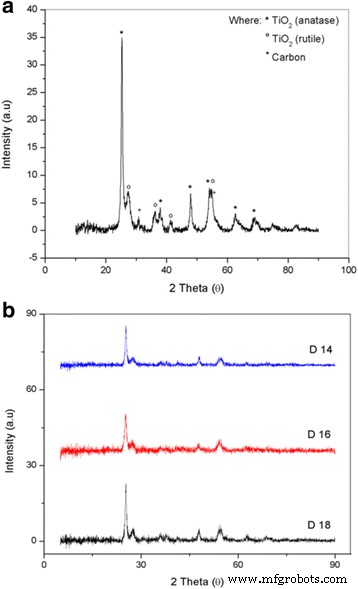
Röntgenbeugungsmuster von a einzelnes TiO2 -CNF-Probe und b anderes DTC-Beispiel
TiO2 -CNF-Nanofasern wurden durch Elektrospinnen mit verschiedenen DTC-Werten hergestellt, die als D14, D16 und D18 bezeichnet werden. Der DTC wurde auf 14, 16 und 18 cm geändert. Der Durchmesser der Nanofaser wurde mittels FESEM-Analyse berechnet. Abbildung 8 zeigt die FESEM-Bilder der Proben mit unterschiedlichen DTC-Werten bei einer Vergrößerung von 30.000 ×. Die Auswirkung der Variation des DTC auf den Durchmesser der Nanofasern wurde unter Verwendung der Partikelgrößenverteilung (Durchmesser) abgeschätzt, wie in Fig. 9 dargestellt, und die Werte sind in Tabelle 2 tabellarisch aufgeführt. Die Durchmesserverteilung umfasst mehrere Parameter, n (Nanopartikel Bevölkerung), da (arithmetische mittlere Partikelgröße) und σ (Standardabweichung) [22].
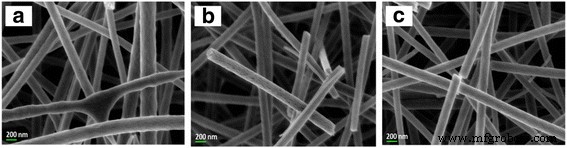
FESEM-Bild von a TiO2 -CNF (D14), b TiO2 -CNF (D16) und c TiO2 -CNF (D18) bei 30.000-facher Vergrößerung
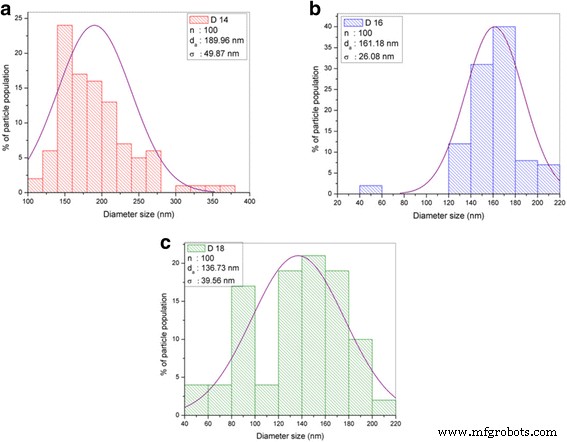
Histogrammdaten der Durchmessergrößenverteilung mit dem Parameter n, da , und . a TiO2 -CNF (D14). b TiO2 -CNF (D16). c TiO2 -CNF (D18)
Der kleinste mittlere Durchmesser betrug 136,73 ± 39,56 nm (90–170 nm) und gehörte zu D18, gefolgt von D16 und D14 mit Durchmessern von 161,18 ± 26,08 bzw. 189,96 ± 49,87 nm. Je länger die Spitzen-Kollektor-Abstände sind, desto kleiner ist der Nanofaser-Durchmesser. Dieses Verhalten ist auf die Abscheidungszeit und das Schlag-Instabilitätsintervall während des Elektrospinnverfahrens zurückzuführen. Der längere Abstand führt zu einer längeren Abscheidungszeit, und während dieser Zeit tritt das Phänomen der Peitscheninstabilität auf, das auch als Ausdünnungs- und Spaltmechanismus bekannt ist. Dieses Phänomen tritt aufgrund von Wechselwirkungen zwischen geladenen Ionen und dem elektrischen Feld auf [17]. Wenn die auf die Düsenspitze ausgeübte elektrische Kraft einen kritischen Wert erreicht, spalten die hoch geladene Dichte und die viskoelastische Kraft die Strahlen in kleinere Strahlen, wodurch ein gebogener, gewundener und spiralförmiger Pfad zum Kollektor entsteht. Wenn der DTC länger ist, tritt wiederholt eine Strahlaufspaltung auf, was zu ultrafeinen Fasern mit kleinerem Durchmesser führt. Daher gehört der kleinste Durchmesser zu Probe D18 mit einer Flussrate von 0,1 mLh −1 und DTC von 18.
Der Durchmesser der hergestellten Nanofasern, TiO2 -CNF, wird mit der vorherigen Untersuchung des Nanofaserdurchmessers für TiO2 . verglichen -basierte Nanofasern, und dieser Vergleich ist in Tabelle 3 dargestellt. Die Ergebnisse zeigen, dass das TiO2 -CNF hat mit 136,73 ± 39,56 nm den kleinsten Nanofaserdurchmesser. Dies ist auf den optimalen Parameter zurückzuführen, der während des Elektrospinnverfahrens verwendet wird; die eine niedrige Durchflussrate und einen hohen DTC-Wert hat. Somit wird bei kleinerer Flussrate und höherem DTC-Wert der kleinere Durchmesser einer Nanofaser erzeugt. Dies zeigt, dass die Elektrospinnparameter den größten Einfluss auf den Durchmesser der Nanofaser haben. Auch wenn ein längerer DTC und eine kleinere Durchflussmenge vorzuziehen sind, gibt es für diese Parameter optimale Werte, da diese Parameter zu Gewichtsverlust führen können. Dies geschieht aufgrund von Überverdampfung, bei der sich die Nanofaser bildet, bevor sie den Kollektor erreicht, wodurch die Nanofaser ungehindert in unerwünschte Bereiche wandern kann.
Die D18-Probe mit einer Flussrate von 0,1 mLh –1 und DTC von 18 wurde für die TEM-Analyse ausgewählt, um die Morphologie zu untersuchen und die Durchmessergröße zu erhalten. Das TEM-Bild und die Elementarkartierung des TiO2 -CNF-Katalysatorträger sind in Abb. 10 dargestellt. Das TEM-Bild zeigt, dass TiO2 -CNF ergibt glatte und seidige Nanofasern mit einem Durchmesser von 135,38 nm. Der Durchmesser liegt im gleichen Bereich (90–170 nm) wie bei der FESEM-Analyse. Die Kartierung wird verwendet, um die Verteilung von TiO2 . zu untersuchen und Kohlenstoff auf Nanofaser. Die Ergebnisse spiegeln wider, dass TiO2 und Kohlenstoff gleichmäßig in der Nanofaserstruktur gebildet, aufgrund der homogenen Verteilung der Polymerlösung und des TiO2 Vorläufer beim Sol-Gel-Verfahren. Dieses Mapping zeigt auch die Lage der Materialien, in denen TiO2 und Kohlenstoff befinden sich entlang der gesamten Nanofaseroberfläche, was der Bildung aktiver Reaktionsbereiche während der Katalyse zugute kommt. Es wird erwartet, dass die anderen Nanofaserproben dieselbe gleichmäßige Verteilung von TiO2 . aufweisen und Kohlenstoff. Die Partikelgröße von TiO2 und Kohlenstoff in den Nanofaserproben und ihre Wirkung auf MOR wird im nächsten Abschnitt diskutiert.
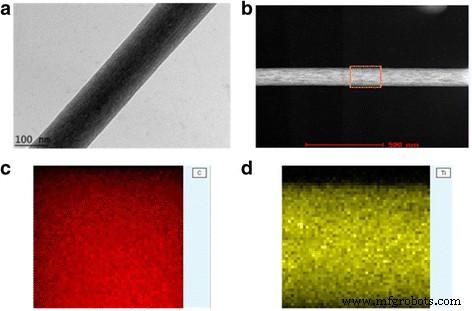
TiO2 -CNF-Katalysatorunterstützung a TEM-Bild (Maßstab 100 nm), b TEM-Bild für TiO2 und C-Nanofaser-Mapping, c Mapping für C-Nanofasern und d Kartierung für TiO2 Nanofaser
Elektrochemische Charakterisierung der Methanol-Oxidationsreaktion
Die elektrochemische Charakterisierung umfasst drei Hauptschritte, nämlich die Charakterisierung der elektrochemischen Aktivität, der elektrokatalytischen Leistung sowie der Langzeitstabilität und Haltbarkeit. Die elektrochemische Aktivität und die elektrokatalytische Leistung wurden mittels CV unter Verwendung eines Drei-Elektroden-Systems analysiert, um qualitative und quantitative Informationen über die beteiligte Reaktion zu erhalten [23]. Abbildung 11a, b zeigen das TEM-Bild des PtRu-Katalysators, der auf der Oberfläche von F0.1 und D18 TiO2 . abgeschieden wurde -CNF unterstützt bzw. Der PtRu-Katalysator war sowohl in F0.1 als auch in D18 gleichmäßig auf der Oberfläche der Nanofasern verteilt. Abbildung 11c zeigt das XRD-Muster von D18 PtRu/TiO2 -CNF, während Tabelle 4 die Daten für den Nanofaserdurchmesser, erhalten von FESEM, und Kristallitgröße der Partikel in den Proben, erhalten von XRD, enthält. Tabelle 4 zeigt, dass die Proben der F-Serie (F0.1, F0.5 und F0.9) mit hinzugefügtem Katalysator einen TiO2 . aufweisen (Anatas) Kristallitgröße von etwa 20 bis 22 nm. Die Änderung des Nanofaserdurchmessers hat wenig Einfluss auf die Kristallitgröße von TiO2 , während sich die Kristallitgröße von Kohlenstoff mit zunehmendem Nanofaserdurchmesser von 15,9 nm in F0,1 auf 25,8 nm in F0,9 ändert. Die Kristallitgröße von Pt neigt auch dazu, mit der Kohlenstoffkristallitgröße zuzunehmen. Die Kristallitgröße von Pt auf F0.1, F0.5 und F0.9 beträgt 5,67, 8,04 bzw. 9,75 nm. Die Veränderungen der Pt-Kristallitgröße sind auf die Oberflächeneigenschaften der Nanofaser zurückzuführen. Tabelle 4 zeigt auch die Kristallitgröße von PtRu, das von Proben der D-Serie getragen wird. Der Nanofaserdurchmesser nimmt von D14 über D16 bis D18 ab. Im Gegensatz zu den Proben der F-Serie ist die Kristallitgröße von TiO2 (Anatas) in den Proben der D-Serie nimmt mit abnehmendem Nanofaserdurchmesser ab. Das TiO2 Die Kristallitgröße beträgt 23,40, 21,50 und 18,60 nm für D14, D16 bzw. D18. Die Kristallitgröße von Kohlenstoff und Pt nimmt auch mit einer Abnahme des Nanofaserdurchmessers ab. Die Kohlenstoffkristallitgröße nimmt von 17,3 nm in D14 auf 14,4 nm in D18 ab, während die auf D14, D16 und D18 unterstützte Pt-Kristallitgröße 5,44, 5,67 bzw. 4,64 nm beträgt. Aus diesen Daten können die Veränderungen der Kristallitgrößen von TiO2 und Kohlenstoff in der Nanofaser führen zu Veränderungen der Oberflächeneigenschaften der Nanofaser, was zu Veränderungen der Kristallitgröße der auf der Oberfläche der Nanofaser abgeschiedenen Pt-Partikel führt.
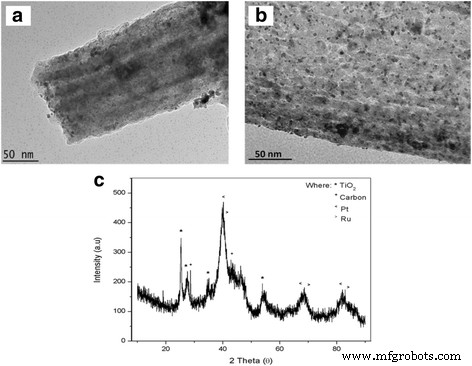
Bild von auf TiO2 . abgeschiedenem PtRu -CNF a TEM-Aufnahme von PtRu/TiO2 -CNF in F0.1, b TEM-Aufnahme von PtRu/TiO2 -CNF in D18 und c XRD-Muster von PtRu/TiO2 -CNF von D18
Abbildung 12 zeigt die CV-Profile von PtRu/TiO2 -CNF electrocatalysts with different catalyst supports in 0.5 M H2 SO4 solution. The CV curve for F0.1, F0.5, and F0.9 are shown in Fig. 12a, while D14, D16, and D18 are shown in Fig. 12b. Hydrogen adsorption-desorption by Pt occurs around − 0.2 to 0.1 V vs. Ag/AgCl. The mass loading for all the electrocatalyst in this profile is the same that as 0.57 mgcm −2 . The PtRu/TiO2 -CNF supported on D18 exhibits a steep current peak for hydrogen adsorption in comparison in the other D series samples, while F0.1 has a steep peak in comparison with the F series samples. The peak indicates that the active surface area on the PtRu/TiO2 -CNF electrocatalyst and the ECSA can be calculated from the equation:ECSA = Q /(Γ .W Pt ). Where, Q is the integral of the hydrogen adsorption area, Γ is the constant for the charge required to reduce the proton monolayer on the Pt (2.1 CmPt −2 ), and W Pt is the mass loading of Pt. Table 5 shows the ECSA of all the catalyst samples in units of m 2 g −1 with mass loadings according to the mass of PtRu. From Table 5, the ECSA for PtRu supported on F0.1, F0.5, and F0.9 is 131.29, 65.05, and 25.03 m 2 g −1 , respectively. The ECSA value decreases with increasing Pt crystallite size in the catalyst samples. The catalyst supported on D14, D16, and D18 has an ECSA value of 21.48, 131.29, and 226.75 m 2 g −1 , respectively. As shown previously, the value of the Pt crystallite size in the D series samples decreases from D14 to D18, and thus, the ECSA increases according to Pt crystallite size. Smaller size particles lead to an increase in the active surface area of the catalyst. Overall, the electrospinning parameters clearly show big influence towards the diameter and surface properties (surface morphology) of nanofibers.
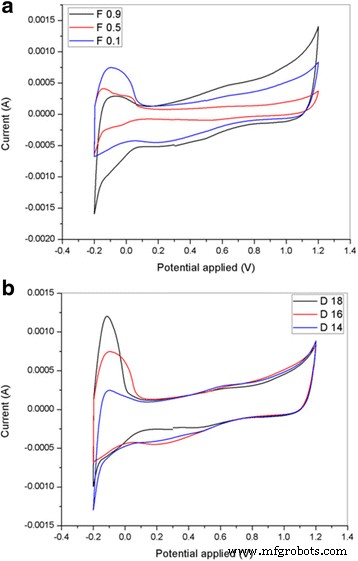
Cyclic voltammetry profiles of the PtRu/TiO2 -CNF with a different flow rate, F0.1, F0.5, F0.9, and b different DTC, D14, D16, and D18, in 0.5 M H2 SO4 solution at the scan rate of 50 mVs −1
The electrocatalytic performance of PtRu supported on the different F and D series nanofibers is tabulated and plotted in Table 5 and Fig. 13. The CV curve was measured in 2 M methanol and 0.5 M H2 SO4 solution saturated with N2 gas at room temperature. The mass loading for all the electrocatalyst is the same which is 0.57 mgcm −2 . Figure 13 shows multiple CV curves over a potential range of − 0.1 to 1.1 V vs. Ag/AgCl. Figure 13a shows the CV graphs for PtRu supported on the F series nanofiber samples. As the diameter of the nanofiber decreases from sample F0.9 to F0.1, the current density in MOR increases, and the oxidation peak and onset potential of MOR shift towards positive values. On the other hand, in the D series nanofiber samples, the oxidation peak potential of the catalyst supported on D14, D16, and D18 is 0.754, 0.771, and 0.732 V (vs. Ag/AgCl), respectively. There is no pattern in the oxidation peak potential in the D series samples, and the onset potential is almost the same for each sample, at 0.36 V vs. Ag/AgCl. However, the peak current density at the oxidation peak potential of MOR increases in accordance to the catalyst support on D14, D16, and D18. The peak current density for D14, D16, and D18 is 201.45, 249.58, and 274.72 mAmg −1 PtRu , respectively. It can be clearly seen that the increase in the current density matches the patterns in the diameter, from FESEM analysis, and ECSA value. This shows that a smaller diameter size produces high surface area and increases the number of active sites on the electrocatalyst surface. The higher peak current for the composite electrocatalyst may result from the supporting material (TiO2 -CNF), where changes in the structure and the combination of materials can be very effective in producing positive effects on the metal-support interaction [5, 24].
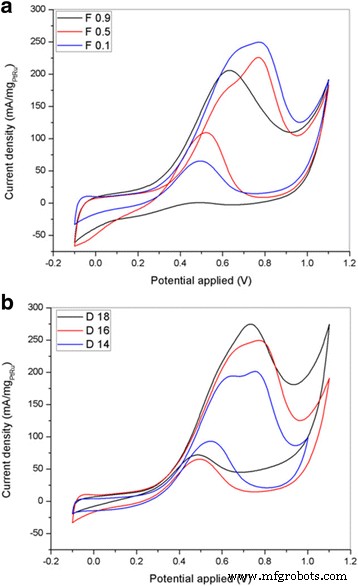
Cyclic voltammograms for PtRu/TiO2 -CNF with different a flow rate and b DTC of the catalyst support in 2 M methanol and 0.5 M H2 SO4 at the scan rate of 50 mVs −1
The reverse scan in the CV curve shows a small oxidation peak at a potential of approximately 0.49–0.55 V vs. Ag/AgCl. This second oxidation peak appeared due to the incomplete removal of oxidized carbonaceous species in the forward scan [25]. However, the ratio between the forward (If ) and reversed (Ib ) oxidation peak for PtRu/TiO2 -CNF (D18) exceeded 3.8, which means that the electrocatalyst has high tolerance towards carbonaceous species, reducing the potential for catalyst poisoning. This result shows that the combination of metal oxide and carbon nanofibers has a good potential for use in fuel cell applications.
Conclusion
TiO2 -CNF nanofibers can be fabricated via electrospinning, which is the main technique, and several other methods. The nanofibers are influenced by the flow rate and the DTC, which were examined as electrospinning process parameters, with three different samples for each parameter, denoted F0.1, F0.5, F0.9, D14, D16, and D18. The results showed that the TiO2 -CNF (D18) sample produced the smallest average diameter of 136.73 ± 39.56 nm. TiO2 -CNF was mixed with PtRu to form the composite catalyst, and its CV performance was examined. The current density of the PtRu/TiO2 -CNF (D18) sample is 1.4 times higher than that of PtRu/TiO2 -CNF (D14), while the ECSA of PtRu/TiO2 -CNF (D18) is 10 times higher than that of the other samples. Thus, the flow rate and DTC highly affect the diameter, morphology, and performance of the nanofibers. The nanofiber performance increased with decreasing nanofiber diameter, which shows the capability of the composite nanofiber catalyst to be an upcoming anode catalyst for DMFCs.
Nanomaterialien
- Herstellungsverfahren für künstliche Moleküle gewinnt den besten Posterpreis
- Graphen- und Polymerverbundstoffe für Superkondensatoranwendungen:ein Rückblick
- Entwerfen von sauberen und zusammengesetzten Kohlenstoff-Nanoröhrchen-Materialien durch porosimetrische Charakterisierung
- Verbesserte Leistung eines neuartigen anodischen PdAu/VGCNF-Katalysators für die Elektrooxidation in einer Glycerin-Brennstoffzelle
- Herstellung, Charakterisierung und Zytotoxizität von kugelförmigen, konjugierten Gold-Cockle-Shell-abgeleiteten Calciumcarbonat-Nanopartikeln für biomedizinische Anwendungen
- Polyanilin-beschichtetes Aktivkohle-Aerogel/Schwefel-Komposit für Hochleistungs-Lithium-Schwefel-Batterien
- Herstellung und Charakterisierung von ZnO-Nano-Clips durch das Polyol-vermittelte Verfahren
- Neuartige anodische Katalysatorunterstützung für Direktmethanol-Brennstoffzelle:Charakterisierungen und Einzelzellleistung
- Eine einfache Methode zum Laden von CeO2-Nanopartikeln auf anodische TiO2-Nanoröhren-Arrays
- Platinbasierte Katalysatoren auf verschiedenen Kohlenstoffträgern und leitfähigen Polymeren für Direktmethanol-Brennstoffzellenanwendungen:eine Übersicht