Entwicklung von AFP für die nächste Generation
Wenn Automatisiertes Fiber Placement (AFP) und Automated Tape Laying (ATL) die Herstellungsverfahren waren, die eine breite Anwendung von Verbundwerkstoffen in der Boeing 787 und dem Airbus A350 ermöglichten, dann wird es auch AFP/ATL sein, die den Weg für die nächste Generation kommerzieller Flugzeuge, jetzt auf Reißbrettern. Der Unterschied diesmal? Bewerten.
Boeing schätzt, dass bis 2037 weltweit mehr als 31.000 neue Single-Aisle-Flugzeuge benötigt werden, um die Passagiernachfrage zu decken. Airbus prognostiziert bis 2037 einen Bedarf von mehr als 28.000 Single-Aisle-Flugzeugen. Beide Unternehmen erwägen den Austausch ihrer Single-Aisle-Stars – der 737 (Boeing) und der A320 (Airbus). Von beiden Unternehmen wird erwartet, dass sie bei allen neuen Flugzeugen, die sie entwickeln, in großem Umfang Verbundwerkstoffe einsetzen. Beide Unternehmen sagen ihren Lieferketten, dass sie für diese Flugzeuge Produktionsraten von 60-100 Flugzeugen pro Monat erwarten, wobei der Schwerpunkt auf 100 liegt. Die Single-Aisle-Kategorie stellt für beide Unternehmen etwa zwei Drittel der weltweiten Gesamtnachfrage dar, was bedeutet, dass die Die für Single-Aisle-Flugzeuge entwickelte Fertigungsumgebung wird auf absehbare Zeit zur Standard-Fertigungsumgebung für Aerocomposites.
All dies bedeutet, dass die Automatisierungstechnik jetzt entwickelt werden muss, wenn sie mit den Anforderungen an Qualität und Produktionsrate von Flugzeugen der nächsten Generation Schritt halten will. Nichts davon geht dem leitenden Ingenieur von Electroimpact (EI, Mukilteo, Washington, USA) Todd Rudberg verloren. Rudberg und EI traten 2004 in die Welt der Verbundwerkstoffe ein, als das Unternehmen die AFP-Technologie zur Herstellung des vorderen Rumpfabschnitts der 787 Section 41 entwickelte, der von Spirit AeroSystems (Wichita, Kan., USA) hergestellt wurde. In der Folge produzierte EI AFP- und ATL-Systeme zur Herstellung anderer 787-Strukturen, A350-Strukturen, Triebwerksstrukturen und zuletzt Boeing 777X-Flügelholme. Jetzt blickt Rudberg in die Zukunft des Flugzeugbaus der nächsten Generation und sieht Verbesserungsmöglichkeiten für AFP. Im Wesentlichen.
Die Chancen, sagt Rudberg, seien beim Blick auf die Daten offensichtlich. Tatsächlich hat EI mehrere Metriken entwickelt, die dem Unternehmen helfen zu verstehen, was seine Maschinen gut machen und was es verbessern kann. Erstens sieht Rudberg bei einem Blick auf die AFP-Landschaft 2019 unzählige Bedrohungen für die aktuelle AFP-Technologie, einschließlich ATL, Handlaminierung, Flachladungen von gewebten Stoffen und natürlich Aluminium.
Die von Rudberg entwickelten AFP-Metriken stammen aus einem Full Production Demonstrator (FPD)-Projekt, für das EI vier Vorserien-Builds durchführte. Daten aus einem dieser Builds, die im Februar 2019 mit „Standard“-EI-AFP-Technologie erstellt wurden, zeigten eine erhebliche Herausforderung bei der Maschinennutzung, wobei die Maschinennutzungszeit in einen von sieben Kategorien fällt:
- Laserprojektion:30 %
- Lauf:27 %
- Inspektion:22 %
- Pause:10 %
- Bedienerinduzierter Stopp:6 %
- Fehlerbehebung:3 %
- Bild:2 %
Anders betrachtet gibt es bei der aktuellen Technologie einen wertschöpfenden Betrieb in AFP (Run), wobei alle anderen als nicht wertschöpfenden Betrieb angesehen werden. Somit beträgt das Verhältnis von Wert- zu Nicht-Wert-Operationen 1:3. „Die Branche will wirklich 3:1, und ich auch“, sagt Rudberg, „und das möchte ich gerne vor meiner Pensionierung erledigen.“ Das Ziel besteht einfach darin, den Zeitaufwand für nicht wertschöpfende Vorgänge zu reduzieren.
Es gibt auch eine übergreifende AFP-Metrik, die einer Erklärung bedarf:Mean Strips Before Failure (MSBF). Dies ist die durchschnittliche Anzahl von Faserkabeln, die zwischen Platzierungsfehlern platziert werden. Je größer diese Zahl ist, desto zuverlässiger ist natürlich die Maschine und der Prozess. Der FPD-Build vom Februar hatte laut Rudberg 5.365 MSBF.
Die Ziele
Bei genauerer Betrachtung des AFP-Betriebs hat EI, so Rudberg, die direkte Kontrolle über nur drei Vorgänge:Lauf, Fehlerbehebung und Inspektion. Und genau hier setzt das Unternehmen an. Rudberg weist jedoch darauf hin, dass auch die Flugzeugzelle eine Rolle spielt, insbesondere bei der Reduzierung von Qualitätsprüfungen, Pausen und betreiberbedingten Stopps. „Wir müssen feststellen, dass die Laufzeiten sehr kurz geworden sind, weil die Maschinen sehr schnell sind“, sagt er, „und alles, was nicht wertschöpfend ist, hat einen massiven Einfluss auf Ihre Auslastung. Es stellt sich also heraus, dass dies ein Mannschaftssport ist. Nicht nur der OEM – ich – muss es besser machen, der Flugzeughersteller trägt auch eine gewisse Verantwortung.“
Für den Flugzeugbau der nächsten Generation möchte Rudberg die MSBF auf>20.000 erhöhen, die Laufzeit auf 77% erhöhen und Laserprojektion, bedienerinduzierte Stopps und Bilder vollständig eliminieren. Wie? Rudberg identifiziert drei Technologiebereiche, die diesen Übergang erleichtern können:servogetriebene Spulengatter, 100 % Inprozesskontrolle und Datenmanagement oder EI 4.0.
Alle drei wurden von EI in einer Reihe von jüngsten FPD-Projekt-Builds nach diesem ersten Februar-Build bewertet. Daten aus dem FPD-Projekt selbst belegen, dass EI auf dem richtigen Weg ist. Rudberg sagt, dass das verwendete AFP-System – genannt MuSCLE – eine Spitzenleistung von 1.500 PS, eine Beschleunigung/Verzögerung von 0,5 G, eine Ablegerate von 4.000 Zoll/Minute, eine Kopfdrehzeit von 1 Sekunde, eine Holm-Kurvengeschwindigkeit von 120 Grad/Sekunde und 6.000 MSBF . erreichte (in Produktion erreicht).
Die Umstellung auf servomotorische Gatter und weg von servopneumatischen Gattern, sagt Rudberg, wurde durchgeführt, um die Geschwindigkeit der Kabelplatzierung, die Genauigkeit der Kabelplatzierung, die Steuerung der Kabelspannung und die allgemeine Bauzuverlässigkeit zu erhöhen. Das Unternehmen hat in den letzten zwei Jahren an einem kompakten Servoverstärker gearbeitet, der auf dem EI-Modulkopf installiert werden kann. Die bisherigen Ergebnisse der Technologie sind vielversprechend; Tests zeigen:15.000 MSBF, 87% schnellere Addiergeschwindigkeit, 36% schnellere Schnittgeschwindigkeit, bessere Endplatzierungsgenauigkeit. Darüber hinaus bewies EI, dass das Gattersystem mit Servomotor verwendet werden kann, um trockene Kohlefasern zu platzieren.
Der Schlüssel für die Inspektion ist der „in-Prozess“-Teil. EI verfügt bereits über eine Inspektionstechnologie, die mit Aligned Vision (Chelmsford, Massachusetts, USA) entwickelt und in der 777X-Flügelfertigungslinie eingesetzt wurde, die Laser- und Visionstechnologie verwendet, um Überlappungen, Lücken, Falten, Endplatzierungsfehler und Fremdkörperablagerungen zu überprüfen ( FOD). Dieses System existiert jedoch unabhängig vom AFP-System und erfordert ein klares Sichtfeld, um zu funktionieren – was bedeutet, dass der AFP-Kopf bewegt werden muss. Rudberg und EI haben ein neues Inspektionssystem namens RIPIT entwickelt, das in den AFP-Kopf integriert ist und die Faserplatzierung sofort überprüft.
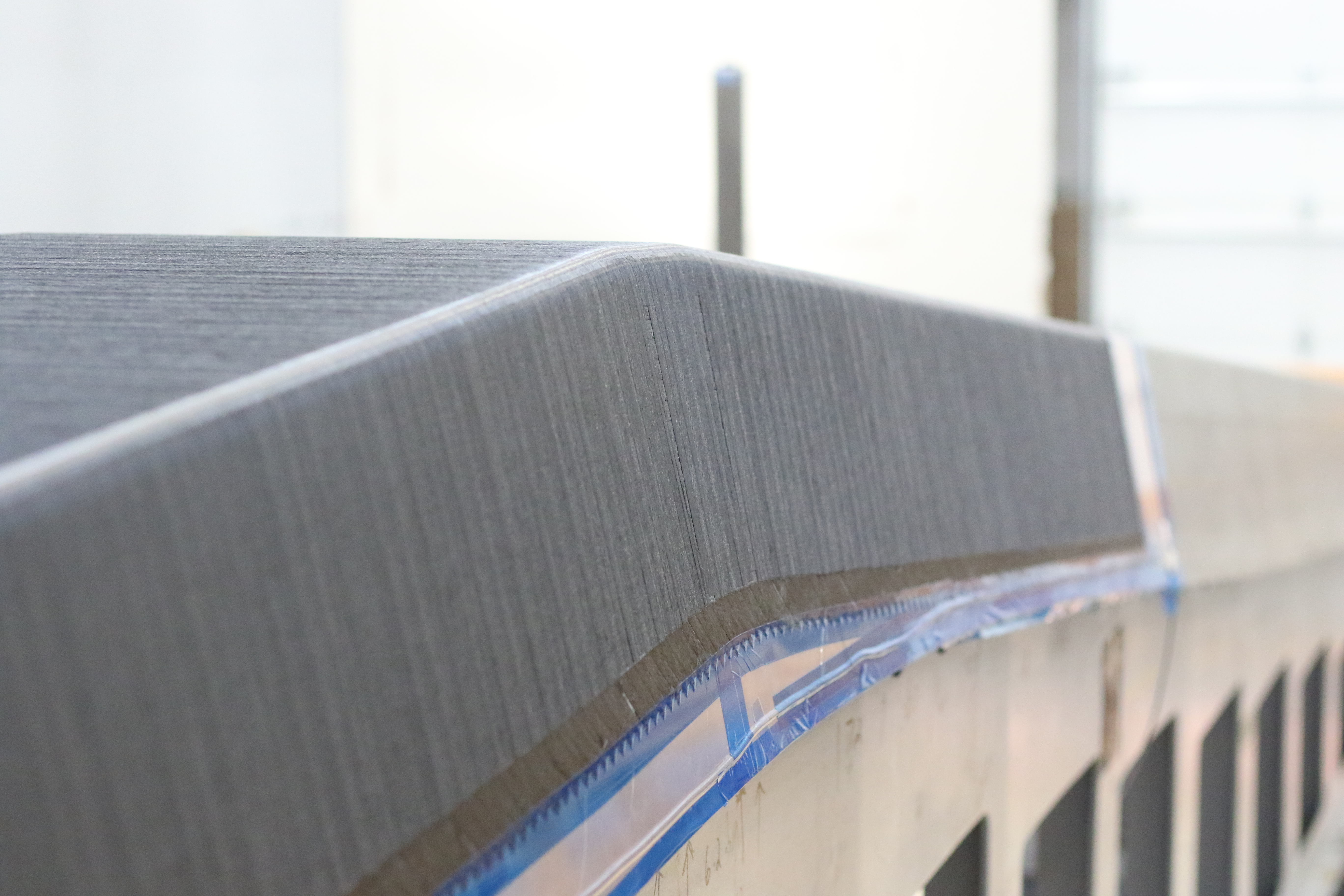
Da Boeing und Airbus Herstellungsverfahren für Verbundwerkstoffe außerhalb des Autoklaven in Betracht ziehen, wird die Fähigkeit von AFP-Systemen, trockene Kohlefasern effizient zu platzieren, von entscheidender Bedeutung sein. Dieser Demonstratorholm zeigt trockene Fasern, die von einem Electroimpact-System platziert wurden. Quelle | Elektroschock
EI wird die Natur der Technologie hinter RIPIT nicht preisgeben, außer zu sagen, dass sie nicht laser- oder visionsbasiert ist. Rudberg sagt auf jeden Fall, dass Tests des Systems zeigen, dass es in der Lage ist, Schleppschlupf bis ±0,030 Zoll in Echtzeit zu erkennen, die Platzierung auf ±0,050 Zoll zu erhöhen und die Schnittplatzierung auf ±0,050 Zoll zu erhöhen. Darüber hinaus sagt Rudberg:„Wir haben viele Versuche durchgeführt, um RIPIT-Daten mit dem bestehenden Boeing-qualifizierten Vision-System [Aligned Vision System, das auf 777X verwendet wird] zu korrelieren, und wir erhalten eine Korrelation.“
Der Wert des Datenmanagements liegt laut Rudberg in der Fähigkeit der EI-Systeme, Herstellern zu helfen, klarer zu erkennen, wie gut der AFP-Prozess funktioniert. Zu diesem Zweck hat EI eine Datenvisualisierungssoftware – EI 4.0 – entwickelt, die nicht nur Einblicke in die Leistung einer bestimmten Maschine (basierend auf MSBF) während eines bestimmten Baus bietet, sondern auch darüber, wie einzelne Schleppen und Sequenzen abliefen. Grundsätzlich hilft die Software dem Bediener, genau zu sehen, wo im AFP-Kopf das Problem liegt. „Also werden wir diese EI 4.0 verwenden, um anzuzeigen, wo sie [Bediener] hingehen müssen, um im AFP-Kopf nachzusehen, um Änderungen vorzunehmen“, sagt Rudberg.
Mit dieser Software ist es möglich, MSBF für eine Vielzahl von Maschinenfunktionen grafisch darzustellen und problematische Faserkabel und besonders anspruchsvolle Abläufe zu identifizieren. Die Software misst und meldet auch andere Maschinenaktivitäten, die die Auslastung beeinträchtigen könnten. Mit diesen Datenmanagement-Tools konnte EI die Build-Zeit für das OPS von über 50 Minuten auf knapp unter 40 Minuten optimieren und reduzieren. Andere Tools umfassen Vergleiche der Schaltleistung und Lagenwinkelvergleiche.
„Ich halte eine Auslastung von 75 % für ein realistisches Ziel oder eine realistische Erwartung“, sagt Rudberg. „Aber dazu braucht es Teamwork, organisatorische Initiative und Nachverfolgung durch den Flugzeughersteller, unsere verbesserte Technologie, bessere vorbeugende Wartung und vorausschauende Wartung sowie bessere Tools zur Analyse der Zellennutzung und Maschinenleistung.“
Harz
- Industrie 4.0 und das IoT:Markttrends für die nächsten Jahre
- Augmented Reality – Das nächste große Ding für die Personalabteilung?
- DARPA arbeitet an Materialien der nächsten Generation für Hyperschallfahrzeuge
- Neue Kristalle für Displaytechnologien der nächsten Generation
- Wie man sich auf die nächste Unterbrechung der Lieferkette vorbereitet
- Fünf Regeln für die nächste Lieferkettenkrise
- Merchandising in der Cloud ist das nächste Muss für den Einzelhandel
- Material für die nächste Generation intelligenter Sensoren
- COVID-19:Nachfrage nach Smart Factory der nächsten Generation
- Wie geht es weiter mit der Automatisierungsrevolution?