Ein Leitfaden zum Aufbau und zur Messung einer schlanken Wartungsstrategie
Professioneller Rennsport ist eine Meisterklasse in Sachen Effizienz. Teams mögen Verschwendung nicht nur nicht – sie hassen sie.
Jede Millisekunde eines Boxenstopps hat einen Sinn. Jede Komponente eines Autos wird analysiert, um sicherzustellen, dass es optimal funktioniert. Strategien sind darauf ausgelegt, so schnell wie möglich von Punkt A nach Punkt B zu gelangen.
Wenn Sie diese Denkweise auf den Shopfloor übertragen, erreichen Sie eine schlanke Wartungsstrategie. Lean Maintenance ist die gnadenlose Reduzierung und Eliminierung von Verschwendung in jeder Phase Ihres Wartungsprogramms, damit Sie schneller vorankommen und weniger Geld ausgeben können.
Dieser Leitfaden beschreibt die Grundlagen für den Aufbau und die Messung einer Lean-Maintenance-Strategie, einschließlich:
- Was ist Lean Maintenance?
- Die Abfallarten bei der Instandhaltung
- Eine Formel zum Erstellen einer schlanken Wartungsstrategie
- Messwerte zur Verfolgung des Erfolgs von Lean Maintenance
Was ist Lean Maintenance?
Wie Lean Manufacturing ist Lean Maintenance der kontinuierliche Prozess der Identifizierung, Reduzierung und Beseitigung von Verschwendung bei Wartungsaktivitäten. Als Abfall wird alles angesehen, was die Leistung nicht steigert, die Kosten senkt oder die Produktivität auf andere Weise steigert.
Es gibt viele Beispiele für Verschwendung bei der Wartung, darunter:
- Geld, das für ein Teil ausgegeben wird, das vor der Verwendung veraltet
- Zeitaufwand für die Klärung der Details einer Wartungsanfrage
- Aufwendiger Aufwand zum Sammeln von Wartungsdaten, die Sie nie verwenden
Es ist oft schwierig, Verschwendung in Ihrem Wartungsprogramm zu erkennen. Deshalb kann eine Lean-Maintenance-Strategie ohne Iteration nicht funktionieren. Iteration ist die Praxis, im Laufe der Zeit kleine Änderungen vorzunehmen, um den besten Weg zum Einrichten von Prozessen und Aktivitäten zu finden. Mit anderen Worten, Lean Maintenance ist kein einmaliges Projekt. Es ist eine Denk- und Handlungsweise, deren Aufbau Jahre dauert.
Was sind die Vorteile von Lean Maintenance?
Wahrscheinlich haben Sie in den letzten Wochen die Worte „Was für eine Zeitverschwendung“ oder „Was für eine Geldverschwendung“ gesagt. Lean Maintenance eliminiert diese Momente. Und obwohl Sie sich auf tausend Dinge beziehen könnten, lassen sich die meisten in diese vier Hauptvorteile einteilen:
1. Kosteneinsparungen
Eine schlanke Wartungsstrategie reduziert direkte Kosten (Arbeit und Ressourcen) und indirekte Kosten (das Geld, das Sie durch Ausfallzeiten oder Produktionsausfälle verlieren). Sie könnten beispielsweise feststellen, dass Sie die routinemäßige Wartung einer Anlage von einmal pro Woche auf einmal im Monat reduzieren und dabei die Arbeitskosten um 75 % senken können.
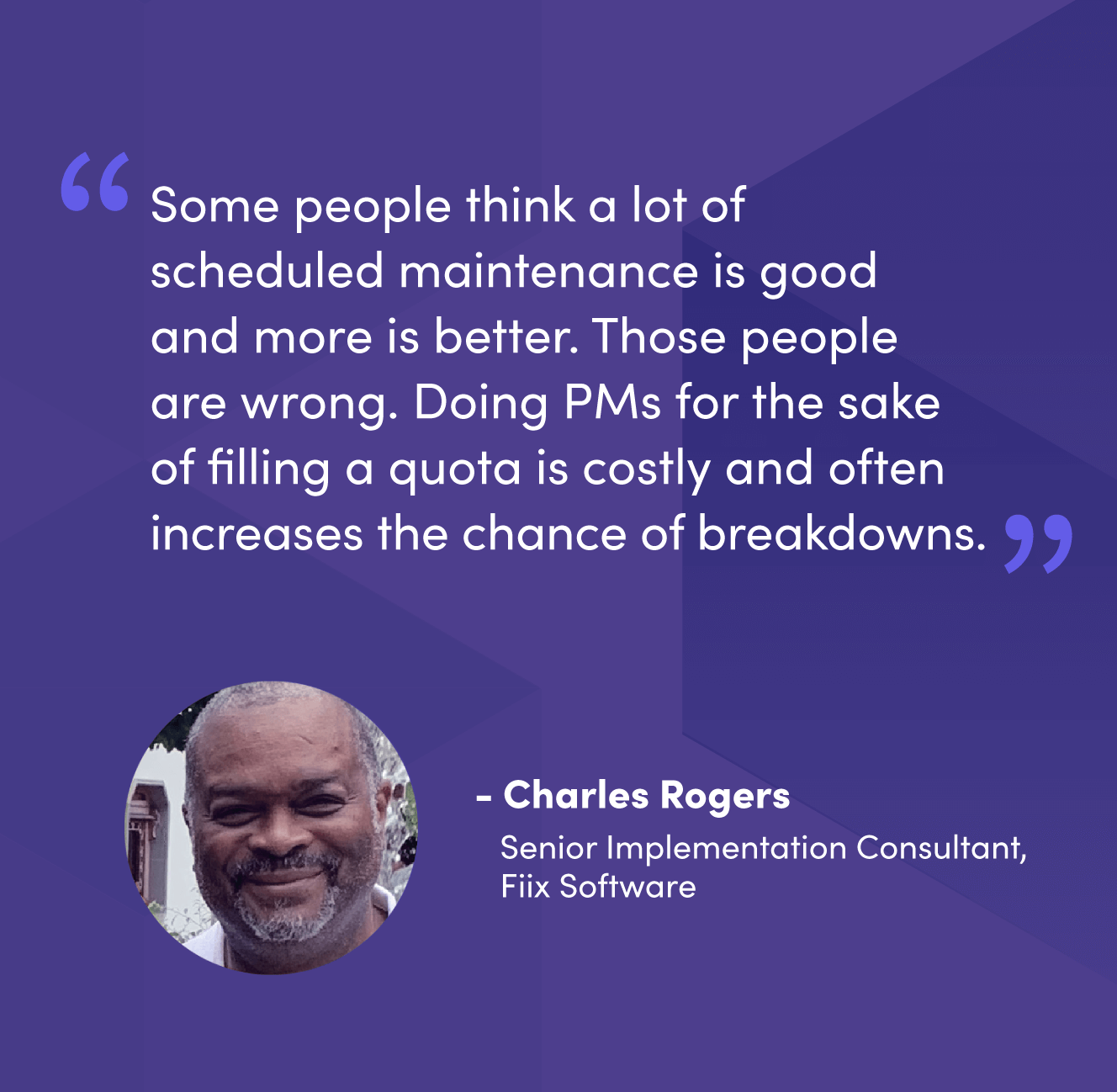
2. Effizienzgewinne
Effizienz ist ein anderes Wort für mehr Leistung in kürzerer Zeit. Lean-Maintenance-Strategien helfen Ihnen, Aktivitäten und Prozesse zu finden, die zu viel Zeit in Anspruch nehmen, sodass Sie diese ändern oder eliminieren können. Das Wartungsteam von Voltalia ist ein großartiges Beispiel für diesen Vorteil in der Praxis. Das Unternehmen stellte fest, dass eines seiner Serviceteams 40 Stunden pro Woche damit verbrachte, vom Büro zu einer externen Einrichtung zu fahren. Die Lösung bestand darin, ein Satellitenbüro in der Nähe der externen Einrichtung zu errichten, um Zeit zu sparen.
Lesen Sie mehr darüber, wie Voltalia die datengesteuerte Wartung erreicht hat
3. Maximales Potenzial
Wenn Maschinen und Menschen nicht durch unnötige Aufgaben behindert werden, können sie ihre volle Leistung erbringen und ihr Bestes geben. Das Wartungsteam von Tom Dufton ist ein perfektes Beispiel dafür. Tom, ein Wartungsmanager, stellte fest, dass seine erfahrenen Wartungstechniker viel Zeit damit verbrachten, die Produktion zu unterstützen. Er nutzte diese Daten, um für zusätzliche Bediener zu werben, damit sein Team sich wieder der Wartung der Geräte widmen konnte.
4. Mitarbeiterengagement
Das Entfernen unnötiger Arbeit und administrativer Aufgaben hilft den Mitarbeitern, sich mehr mit ihrer Arbeit zu beschäftigen. Es gibt ihnen auch Zeit, sich weiterzubilden und hochwertige Arbeit zu leisten. Dies lässt sich unter anderem mit einer neuen Wartungssoftware in die Realität umsetzen. Wenn Techniker keine Zeit haben, das System zu erlernen, könnte Ihre große Investition in Technologie umsonst sein. Wenn Sie zusätzliche Aufgaben an anderer Stelle eliminieren, bleibt Ihrem Team Zeit, zu lernen, Fragen zu stellen und sich an neue Technologien zu gewöhnen.
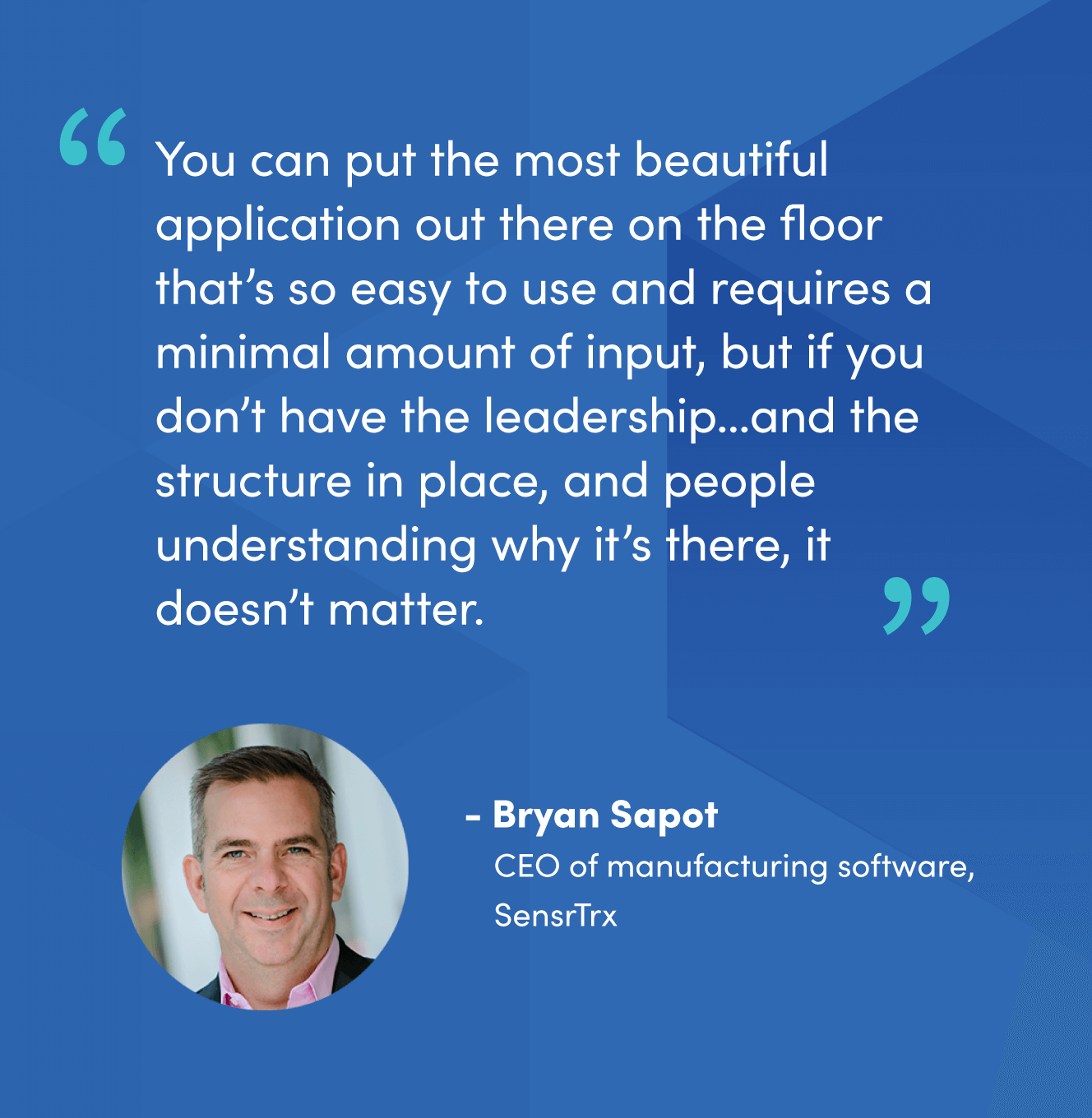
Die drei Abfallarten in der Instandhaltung
Der erste Schritt zur Beseitigung von Abfällen besteht darin, sie zu finden. Es gibt drei Hauptbereiche in einem Wartungsbetrieb, in denen Abfall anfällt:Umwelt-, Finanz- und Humanpotenzial.
Umweltmüll
Umweltverschwendung entsteht, wenn Rohstoffe ineffizient verwendet oder aufgrund ineffizienter Wartungsaktivitäten entsorgt werden.
Beispiele für Umweltabfälle bei der Wartung sind:
- Zunahme von Ausschuss oder Nacharbeit nach Gerätewartung
- Überverbrauch von Kraftstoff durch unsachgemäß gewartete Fahrzeuge oder unnötige Transporte zu und von einer Baustelle
- Überbestand an Teilen für die Wartung aufgrund eines veralteten Einkaufsplans für Lagerbestände
Die Auswirkungen von Umweltabfällen aus der Wartung umfassen:
- Mehr Umweltverschmutzung und Müll
- Höhere CO2-Emissionen
- Produkte von geringer Qualität
- Erhöhte Sicherheitsrisiken
Einige Strategien zur Reduzierung von Umweltverschwendung bei der Wartung sind:
- Häufige Bestandszählungen und Just-in-Time-Käufe, um sicherzustellen, dass Ihr Lager nicht mit ungenutztem Inventar überschwemmt wird
- Gruppieren geplanter Wartungsarbeiten in einem Zeitraum, um Reisen zu reduzieren
- Eine obligatorische Überprüfung durch einen zweiten Techniker nach Reparaturen oder Austausch vor der Produktion, um sicherzustellen, dass Inbetriebnahmen nicht zu Ausschuss oder Nacharbeit führen
Sehen Sie, wie Ihr Wartungsteam die Nachhaltigkeit in Ihrem Unternehmen steigern kann
Finanzverschwendung
Finanzielle Verschwendung bezieht sich auf die zusätzlichen Kosten durch ineffiziente Wartung. Dazu gehören auch Produktionsausfälle durch unnötige Ausfallzeiten.
Beispiele für finanzielle Verschwendung bei der Wartung sind:
- Hohe Arbeits- und Teilekosten durch zu häufig durchgeführte vorbeugende Wartungsaufgaben
- Defekte Produkte aus einer Anlage, die falsch zusammengebaut oder umgebaut wurde
- Wartungsverzögerung, weil Techniker warten mussten, bis ein Teil repariert wurde
Zu den Auswirkungen finanzieller Verschwendung gehören:
- Höhere Arbeits- und Teilekosten
- Mehr Investitionen
- Einkommensverlust
- Verpasste Gelegenheiten, das Geschäft auszubauen
Zu den Strategien, um schlanker zu werden, gehören:
- Identifizieren von Aufgaben in Ihrem vorbeugenden Wartungsplan, die eliminiert oder weniger häufig durchgeführt werden können
- Reduzierung von Ausfallzeiten, indem Wartungsarbeiten gefunden werden, die während des Betriebs einer Anlage abgeschlossen werden können
- Aufbau eines FRACAS, um Ausfälle kritischer Geräte zu beheben und zu verhindern
- Erstellen von Teilesätzen für kritische Geräte, um Reparaturen zu beschleunigen und Fehlbestände zu vermeiden
- Einrichten eines regelmäßigen Treffens mit dem Produktionspersonal, um die Wartung mit dem Betrieb abzustimmen und Updates für Geräteänderungen zu erhalten
Verschwendetes menschliches Potenzial
Administrative Tätigkeiten und unnötige Aufgaben belasten die Mitarbeiter und nehmen sie von spezialisierten Aufgaben ab, die nur sie selbst erledigen können. Burnout, schlechte Moral und Fluktuation nehmen zu, was zu noch mehr Verschwendung führt.
Beispiele für verschwendetes menschliches Potenzial bei der Wartung sind:
- Verbringen täglich Stunden damit, Arbeitsaufträge zu schreiben, zu überprüfen und zu sortieren
- Das gleiche Bauteil immer wieder reparieren
- Inspektion nicht kritischer Geräte mit geringen oder nicht vorhandenen Ausfallraten
- Produktion mehr als ab und zu unterstützen
- Suche nach Teilen und Verbrauchsmaterialien in Ihrem Lagerraum
Die Auswirkungen des verschwendeten menschlichen Potenzials umfassen:
- Hohe Mitarbeiterfluktuation und Verlust von Organisationswissen
- Kurze Schraubenschlüsselzeit und große Rückstände
- Verringertes Mitarbeiterengagement und geringe Akzeptanz neuer Systeme
- Mehr Bleistiftschläge und weniger genaue Daten
Zu den Strategien, um schlanker zu werden, gehören:
- Führen Sie häufige Besprechungen des Wartungsteams durch, um Herausforderungen zu besprechen und Lösungen zu finden
- Automatisieren Sie häufig ausgeführte Aktivitäten wie das Erstellen von Arbeitsaufträgen oder Berichten
- Eliminieren oder reduzieren Sie geplante Wartungsarbeiten mit geringen Folgearbeiten
- Schulen Sie Maschinenbediener für Routinewartungsaufgaben
Hol dir Tipps zur Reduzierung der Fluktuation in deinem Wartungsteam
Erstellung einer schlanken Wartungshaltung
Der erste Schritt bei der Entwicklung einer Lean-Maintenance-Strategie besteht darin, die richtigen Fragen zu stellen, die Art und Weise, wie Sie Dinge tun, zu hinterfragen und bereit zu sein, sich zu ändern. Dies ist eine Lean-Maintenance-Mentalität und es ist wichtig, dass Lean-Maintenance-Strategien langfristig funktionieren.
Es gibt vier Änderungen, die Ihnen beim Übergang zu einer schlanken Wartungshaltung helfen:
1. Von kleinen Details → Großes Bild
Es wird immer Tage geben, an denen Ihr Team auf alles reagiert – Feuer löschen, Anfragen in letzter Minute erhalten und den Rückstand aufholen.
Aber eine Lean-Maintenance-Mentalität verhindert, dass dies zur Norm wird. Es ermöglicht Ihnen, Wartungsaktivitäten rund um die Geschäfts- und Produktionsziele aufzubauen und Arbeiten, die nicht mit diesen Zielen in Verbindung stehen, zu priorisieren oder zu eliminieren.
Sie können beispielsweise jede Woche eine Stunde damit verbringen, einen Bericht zu erstellen. Aber wenn dieser Bericht Ihnen nicht hilft, Verschwendung zu vermeiden, wird diese Zeit selbst zu Verschwendung. Sie können entweder Zeit damit verbringen, nützlichere Berichte zu erstellen oder andere abfallvermeidende Arbeiten erledigen.
Laden Sie diese Vorlage herunter, um Ihre Wartungsziele mit Geschäftszielen zu verbinden
2. Vom Erledigen → Sammeln von Daten im Laufe der Zeit
Viele Wartungsteams arbeiten im Überlebensmodus. Schließen Sie die Aufgabe ab und fahren Sie mit der nächsten fort. Keine Zeit für zusätzliche Schritte.
Aber eine schlanke Wartungsstrategie hängt von Daten ab und nimmt sich die Zeit, sie zu sammeln. Diese fünf zusätzlichen Minuten, die zum Ausfüllen zusätzlicher Felder in einem Arbeitsauftrag benötigt werden, summieren sich. Eine schlanke Wartungsmentalität bedeutet, einen Puffer in Ihrem Zeitplan zu schaffen, um dies zu berücksichtigen. Es bedeutet auch, dass jeder die Bedeutung dieser zusätzlichen Schritte kennt und nicht unter Druck gesetzt wird, die Zahlen zu verfälschen, um die verlorene Zeit auszugleichen.
3. Von großen Änderungen → iterative Verbesserungen
Jeder möchte so schnell wie möglich große Gewinne sehen. Unser Gehirn sehnt sich nach einer Ziellinie und greifbaren Ergebnissen.
Aber so funktioniert Lean Maintenance nicht. Stattdessen kommt es darauf an, kleine, konsequente Verbesserungen vorzunehmen. Wenn es richtig gemacht wird, ist es ein Prozess, der nie wirklich abgeschlossen ist. Der beste Weg, diesen Wandel zu bewältigen, besteht darin, sich und Ihrem Team kleine Ziele und Meilensteine zu setzen, Fortschritte zu verfolgen und Erfolge zu feiern.
Beispielsweise möchten Sie möglicherweise unnötige Schritte bei Ihrer geplanten Wartung aussparen. Bei der Lean Maintenance überprüfen Sie Ihre Arbeitsaufträge einmal im Monat, um Verzögerungen zu reduzieren und die Schraubenschlüsselzeit über das ganze Jahr um 10 bis 15 % zu erhöhen. Es ist wichtig, den Fortschritt zu verfolgen, ihn mit Ihrem Team zu feiern und Vorschläge von Technikern zu erhalten, wie Sie weiterhin gewinnen können. Techniker fühlen sich dieser Kennzahl verpflichtet und werden in den Fortschritt investiert.
4. Von „so ist das“ → „Ist das nötig?“
Es ist einfach, den Status Quo zu akzeptieren. Es ist unangenehm, sich zu ändern. Und es erfordert viel Arbeit.
Aber bei Lean Maintenance geht es vor allem darum, das Geschäft wie gewohnt herauszufordern. Sie müssen alles, was Ihr Team tut, kritisch betrachten und Änderungen vornehmen, wenn etwas keinen Sinn mehr macht. Dies erfordert eine Win-or-Learn-Mentalität anstelle einer Win-or-Fail-Mentalität. Ihr Team wird in der Lage sein, Dinge ohne Schuldzuweisungen oder Bestrafung in Frage zu stellen.
Zum Beispiel könnten Sie ein Jahrzehnt lang im gleichen Intervall eine PM gemacht haben. Aber in dieser Zeit hat sich alles verändert, von der Ausrüstung bis zum Techniker, der die Arbeit verrichtet. Sie müssen auch hinterfragen, wie die PM gemacht wird. Soll es mehr oder weniger gemacht werden? Ist es überhaupt noch nötig?
Aufbau einer schlanken Wartungsstrategie
Der Aufbau einer schlanken Wartungsstrategie folgt einer dreistufigen Formel:
- Verstehen Sie, was Sie gerade tun und wie Sie es tun
- Suchen Sie nach Abfallbereichen und beseitigen Sie sie
- Erstellen Sie Prozesse, mit denen Sie die Schritte eins und zwei immer wieder ausführen können
Schritt 1:Ihren Wartungsprozess abbilden
In diesem Schritt geht es darum, zu wissen, wie Ihr Team derzeit arbeitet, damit Sie die Arbeit finden können, von der Sie zu viel tun, und die Arbeit, von der Sie nicht genug tun. In dieser Phase müssen Sie Ihre Wartungsprozesse dokumentieren, einschließlich:
- Schlüsselinformationen zu Geräten wie Kritikalität und Fehlermodi (diese FMEA-Vorlage kann Ihnen bei der Erfassung dieser Daten helfen)
- Welche Inspektionen und Reparaturen werden wie oft durchgeführt
- Wie ein Notfall aussieht und wie Ihr Team reagiert
- Wie Folge- oder Korrekturwartungen erstellt, zugewiesen und verfolgt werden
- Teammeetings und was in jedem passiert
- Zielsetzung, Erstellung von Messwerten, Berichterstellung und Datenerfassung
- Gesundheits-, Sicherheits- und Compliance-Aktivitäten
- Einkauf von Teilen und Lagerverwaltung
Denken Sie dann an die geschäftlichen Anforderungen:
- Produktionsstufen nach Saison
- Zeiträume mit hohen und niedrigen Verkaufszahlen
- Reaktionsbedarf bei früheren Notfällen
- Organisationsziele und Ressourcen
Schritt 2:Identifizieren Sie Verbesserungsmöglichkeiten, auf die Sie jetzt reagieren können
Der nächste Schritt besteht darin, herauszufinden, wo Sie zu viel Zeit, Geld oder Energie aufwenden. Hier sind einige Möglichkeiten, wie Sie Verschwendung in Ihren Prozessen erkennen können:
-
Betrachten Sie spezifische Prozesse mit Mitgliedern Ihres Wartungsteams. Fragen Sie sie, welcher Teil des Prozesses die meiste Zeit in Anspruch nimmt oder wo sie bei der Erledigung der Arbeit mit Herausforderungen konfrontiert sind. Nutzen Sie diese Erkenntnisse, um Aktivitäten zu vereinfachen und Hindernisse zu beseitigen.
Beispielsweise kann eine so kleine Fehlidentifikation der Schmierung zu Zeitverschwendung, Ausfällen, Produktionsausfällen und dem Kauf von zu vielen Verbrauchsmaterialien führen. Farbcodierung von Schmierung und Lagern kann diese Verschwendung vollständig vermeiden.
-
Identifizieren Sie Aufgaben, die ständig mehr Zeit oder Geld kosten als geplant, und führen Sie eine Ursachenanalyse durch, um herauszufinden, warum. Dies ist hilfreicher als Kostensenkungen, die mehr schaden als nützen können und den wahren Grund für die Verschwendung nicht angehen.
Die Arbeitskosten für einen wöchentlichen Arbeitsauftrag sind beispielsweise doppelt so hoch wie geplant. Ein RCA stellt möglicherweise fest, dass die Reparaturzeiten länger als erwartet sind, da andere Techniker die Arbeit erledigen. Sie können den Zeitplan anpassen, um denselben Techniker mit der Arbeit zu beauftragen, damit sie sich mit der Arbeit vertraut machen und sie schneller erledigen können.
Laden Sie Ihre eigene Vorlage für die Ursachenanalyse herunter
-
Auditieren Sie Ihre geplanten Wartungsarbeiten, um sie effizienter zu gestalten. Wir haben die Schritte zum Auditieren Ihrer PMs in einem separaten Artikel beschrieben, aber die wichtigste Erkenntnis besteht darin, die Notwendigkeit aller regelmäßigen Wartungsarbeiten sowie die Häufigkeit, den Zeitpunkt und die Ressourcen für jede Aufgabe zu hinterfragen.
Beispielsweise kann alle 10 Tage eine PM ausgelöst werden, unabhängig davon, wie viel das Asset verwendet wird. Das kann Zeit- und Geldverschwendung sein. Versuchen Sie in dieser Situation, die Wartung basierend auf der Nutzung auszulösen, z. B. alle 100 Produktionsstunden.
-
Entwickeln Sie KPIs und Metriken rund um das Wachstum und den Erfolg Ihres Teams. Anhand dieser Daten können Sie ungenutztes Potenzial in Ihrem Wartungsteam erkennen.
Sie können beispielsweise Fluktuationsraten oder Möglichkeiten zum Wissensaustausch in Ihrem Team verfolgen. Diese Statistiken können komplexe Prozesse oder Bereiche mit geringer Produktivität aufdecken, die Sie korrigieren können. Das Endergebnis ist eine bessere Moral und ein leistungsfähigeres Wartungsteam.
Schritt 3:Erstellen Sie eine langfristige Vision
Die Kernvision Ihrer Lean-Maintenance-Strategie wird immer darin bestehen, die Instandhaltung Stück für Stück zu verbessern, um die Geschäftsziele zu unterstützen. Aber diese Ziele können sich ändern, ebenso wie die Dinge, die Sie verbessern müssen.
In diesem Schritt geht es darum, zu dokumentieren, worüber Sie iteriert haben, die Auswirkungen von Änderungen und was als nächstes kommen könnte.
Wenn Ihre Iterationen zu einem negativen Ergebnis geführt haben, kehren Sie nicht sofort zum alten Zustand zurück. Denken Sie stattdessen darüber nach, was das negative Ergebnis verursacht hat, und prüfen Sie, ob es eine weitere iterative Verbesserung gibt. Es kann einige Versuche dauern, bis es richtig ist.
Auswahl von Metriken für eine schlanke Wartungsstrategie und Verfolgung des Erfolgs
Obwohl jedes Projekt basierend auf Ihren gewünschten Ergebnissen unterschiedliche KPIs und Metriken hat, sind hier einige Best-Practice-Metriken für den Anfang:
Dies ist zwar kein umfassender Blick auf die Lean-Maintenance-Metriken, bietet Ihnen jedoch eine gute Grundlage. Und Sie müssen nicht jede Metrik verfolgen, messen und verbessern. Wählen Sie Metriken aus, die Sie realistisch erfassen können und die mit Produktions- und Geschäftszielen in Verbindung stehen.
Es gibt zwei Möglichkeiten, Erfolgspläne für jede Kennzahl zu erstellen und Ihre Lean-Maintenance-Strategie voranzutreiben. Die erste ist, klein zu werden. Wählen Sie einige Kennzahlen aus und konzentrieren Sie sich auf die Verbesserung bestimmter Bereiche Ihres Wartungsbetriebs. Wenn Sie beispielsweise die Wartungskosten senken möchten, wählen Sie Ihre 10 teuersten Aufgaben aus. Konzentrieren Sie sich auf die Reduzierung von Abfall bei diesen Aktivitäten.
Die andere Methode ist, breit zu gehen. Streben Sie ein Ziel an, das die Verbesserung mehrerer Metriken umfasst. Das ultimative Ziel könnte beispielsweise darin bestehen, die Effizienz durch eine bessere Standardisierung über die Standorte hinweg zu steigern. Im Rahmen dieses Projekts können Sie die Prozesse für Arbeitsanfragen, Reporting und Teilebeschaffung standardisieren. Es gibt mehrere Metriken, die Sie verwenden können, um Ihr Projekt aufzubauen und seinen Erfolg zu verfolgen. Dazu gehören die Anzahl der Schritte in einem Wartungsprozess, die für Verwaltungsaufgaben aufgewendete Zeit, die Reaktionsraten bei Störungen und der Rohstoffverbrauch.
Es ist wichtig, Ihre Gewinne zu teilen, unabhängig von Ihrem Ansatz. Der Sinn von Lean Maintenance besteht darin, kleine Gewinne zu erzielen, die sich im Laufe der Zeit zu großen summieren. Wenn Sie Ihren Erfolg unter Beweis stellen, halten Sie die Dynamik hoch, erhöhen die Akzeptanz und helfen Ihnen, sich für mehr Ressourcen einzusetzen, um Ihr Lean-Maintenance-Programm zu erweitern.
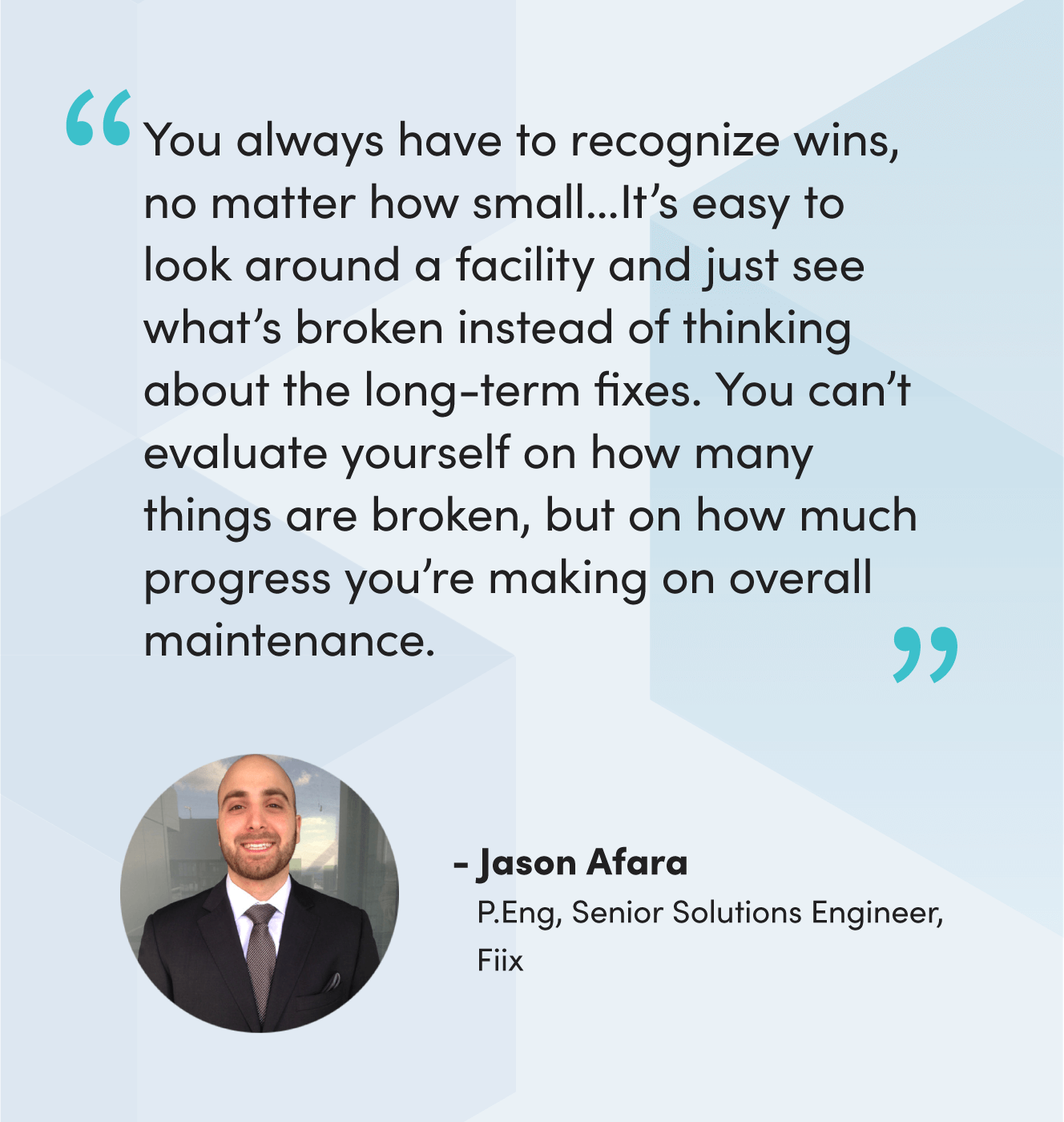
Lean Maintenance läuft
Im Kern geht es bei Lean Maintenance darum, die Wartungspraktiken an die Geschäftsanforderungen zu binden. Dies wird wahrscheinlich die Federn zerzausen, aber es ist ein entscheidender Schritt, um die Wartung von einer Kostenstelle zu einem Werttreiber zu verlagern. Und wenn Sie das tun, öffnet sich die Welt für das Wartungsteam, um als echter Geschäftspartner wahrgenommen zu werden.
Gerätewartung und Reparatur
- Schritt-für-Schritt-Anleitung zum Aufbau einer intelligenten Fabrik
- Eine fehlerhafte Wartungsstrategie beheben:PM-Optimierung und FMEA
- Der grundlegende Leitfaden zur Auswahl einer Wartungsstrategie für Ihre Anlagen
- Lean Manufacturing:Was ist das und was hat Wartung damit zu tun?
- Lassen Sie Risiko und Ihre Ausrüstung Ihre Wartungsstrategie bestimmen
- Strategie und Lösungen der Armee für zustandsorientierte Instandhaltung
- Messen der Wartungseffektivität
- Über die Wartung
- TOTAL entwickelt Wartungs- und Inspektionsstrategie
- Leitfaden zum Verständnis von Lean und Six Sigma für die Fertigung