Die geheime Mechanik von Schaftfräsern mit hohem Vorschub
Ein High-Feed-Schaftfräser ist eine Art High-Efficiency Milling (HEM)-Werkzeug mit einem speziellen Endprofil, das es dem Werkzeug ermöglicht, die Spanverdünnung zu nutzen, um dramatisch erhöhte Vorschubraten zu erzielen. Diese Werkzeuge sollen mit einer extrem geringen axialen Tiefe arbeiten, so dass der Schneidvorgang entlang der gekrümmten Kante des Bodenprofils stattfindet. Dadurch können einige unterschiedliche Phänomene auftreten:
- Durch den geringen Einstellwinkel wird der Großteil der Schnittkraft axial zurück in die Spindel übertragen. Dies führt zu einer geringeren Durchbiegung, da viel weniger radiale Kräfte den Fräser aus seiner Mittelachse drücken.
- Das erweiterte gekrümmte Profil der Unterkante bewirkt einen Spanverdünnungseffekt, der aggressive Vorschübe ermöglicht.
Der niedrige Einstellwinkel eines High-Feed-Schaftfräsers
Wie in Abbildung 1 unten zu sehen ist, überträgt der niedrige Einstellwinkel, kombiniert mit einer geringen axialen Schnitttiefe, den größten Teil der Schnittkraft nach oben entlang der Mittelachse des Werkzeugs, wenn ein Hochvorschub-Schaftfräser richtig in ein Werkstück eingreift. Eine geringe Radialkraft ermöglicht die Verwendung größerer Reichweiten ohne die nachteiligen Auswirkungen von Rattern, was zu einem Werkzeugversagen führen würde. Dies ist vorteilhaft für Anwendungen, die eine geringe Radialkraft erfordern, wie z. B. das Bearbeiten dünner Wände oder das Konturieren tiefer Taschen.
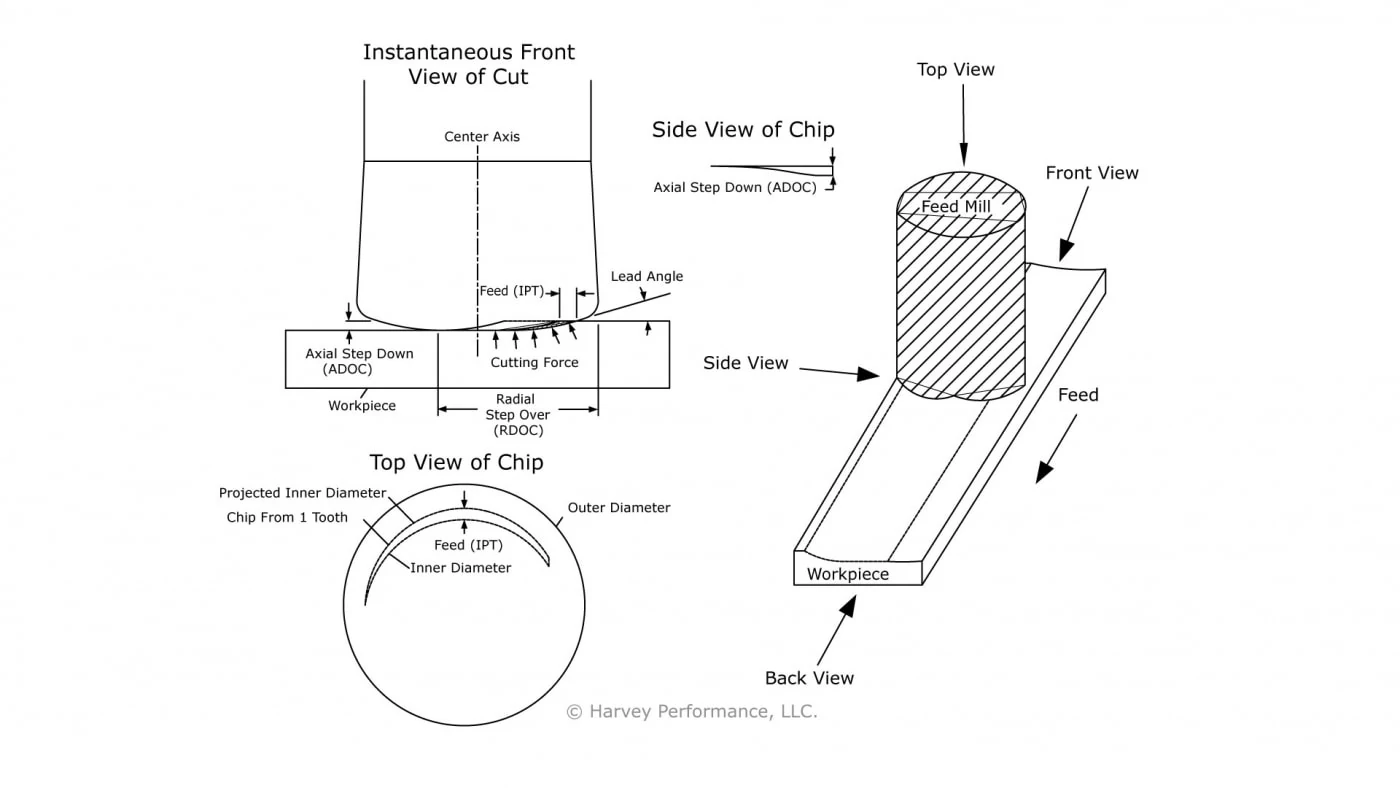
Futtermühlen haben aggressive Futterraten
Fig. 1 zeigt auch eine momentane Momentaufnahme des sich bildenden Spans, wenn er in einen geeigneten Weg des Schruppwerkzeugs eingreift. Beachten Sie, wie der Span (markiert durch diagonale Linien) dünner wird, wenn er sich der Mittelachse des Werkzeugs nähert. Dies liegt an der gekrümmten Geometrie der Unterkante. Aufgrund dieses Späneverdünnungsphänomens muss der Vorschub des Werkzeugs erhöht werden, damit das Werkzeug aktiv mit dem Schneiden beschäftigt ist und nicht am Werkstück reibt. Reiben erhöht die Reibung, was wiederum die Hitze um die Schneidzone erhöht und vorzeitigen Werkzeugverschleiß verursacht. Da dieses Werkzeug eine erhöhte Spanlast erfordert, um eine funktionsfähige Schneidkante beizubehalten, wurde dem Werkzeug der Name „Hochvorschubfräser“ gegeben.
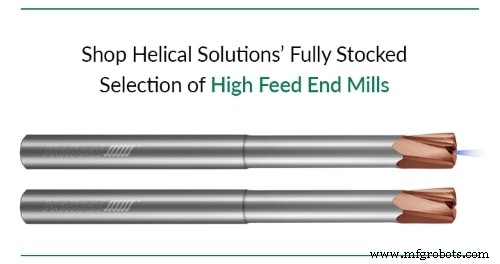
Andere Phänomene aufgrund der gekrümmten Geometrie der Unterkante
Die geschwungene Geometrie der Unterkante lässt auch die folgenden Aktionen zu:
- Ein programmierbarer Radius, der einem CAM-Werkzeugweg hinzugefügt wird
- Muscheln, die sich während der Planbearbeitung bilden
- Unterschiedlich geformte Späne, die beim Schlitzen erzeugt werden, im Vergleich zum HEM-Schruppen
Programmierbarer Radius
Die Hochvorschub-Schaftfräser von Helical Solutions haben eine Unterkante mit doppeltem Radius. Aus diesem Grund kann das exakte Profil von einigen CAM-Programmen nicht einfach programmiert werden. Daher wird ein theoretischer Radius verwendet, um eine einfache Integration zu ermöglichen. Programmieren Sie einfach einen abgerundeten Werkzeugweg und verwenden Sie den theoretischen Radius (siehe unten in Abbildung 2) aus der Maßtabelle als Eckenradius.
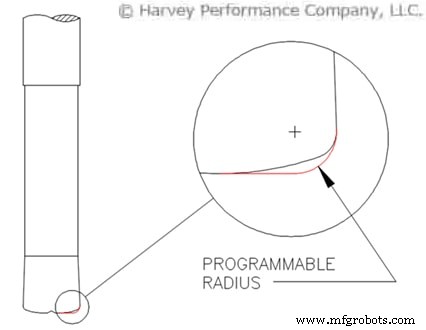
Muscheln verwalten
Eine Jakobsmuschel ist eine Materialspitze, die von Schneidwerkzeugen mit gekrümmten Profilen zurückgelassen wird. Drei Hauptfaktoren, die die Höhe und Breite von Jakobsmuscheln bestimmen, sind:
- Axiale Schnitttiefe
- Radiale Schnitttiefe
- Krümmung der Unterkante oder Führungswinkel
Abbildung 3 unten ist eine Darstellung des Muschelprofils eines typischen Schruppschnitts mit 65 % radialer Zustellung und 4 % axialer Schnitttiefe. Der schattierte Bereich stellt die Muschel dar, die nach 2 Schruppdurchgängen zurückbleibt und parallel zur Werkzeugbahn verläuft.
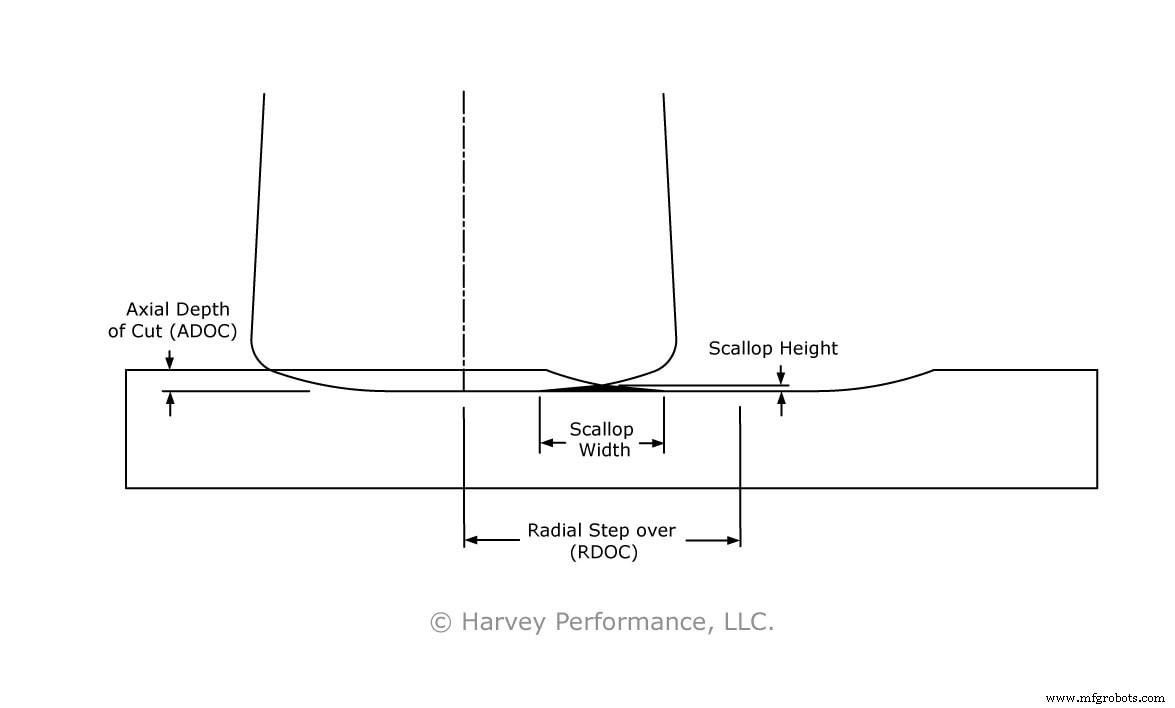
Die Abbildungen 4 und 5 zeigen die Auswirkungen der radialen und axialen Schnitttiefe auf die Höhe und Breite von Muscheln. Diese Zahlen sollten im Zusammenhang mit Abbildung 3 betrachtet werden. Es wird der Prozentsatz pro Durchmesser anstelle von Standardmaßeinheiten verwendet, um zu zeigen, dass dieser Effekt bei jeder Werkzeuggröße vorhergesagt werden kann. Abbildung 4 zeigt, dass sich ein Bogen zu bilden beginnt, wenn das Werkzeug so programmiert ist, dass es eine radiale Schrittweite zwischen 35 % und 40 % aufweist. Die Höhe nimmt exponentiell zu, bis sie bei der axialen Schnittiefe maximiert ist. Abbildung 5 zeigt, dass es eine lineare Beziehung zwischen der radialen Schrittweite und der Bogenbreite gibt. Zwischen der Bogenbreite und der axialen Schnitttiefe besteht kein Zusammenhang, solange ADOC und der Krümmungsradius der unteren Schneidkante gleich bleiben.
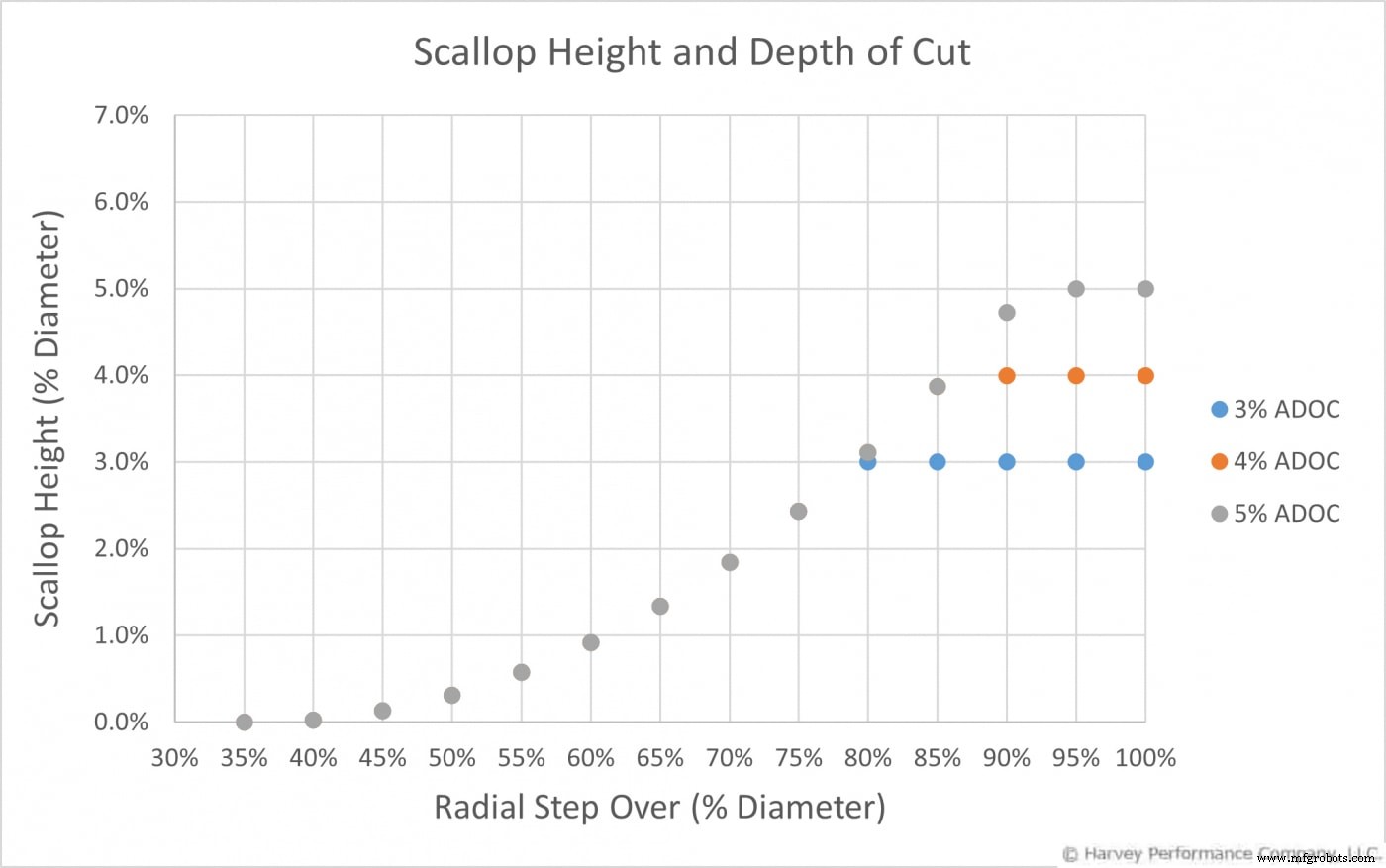
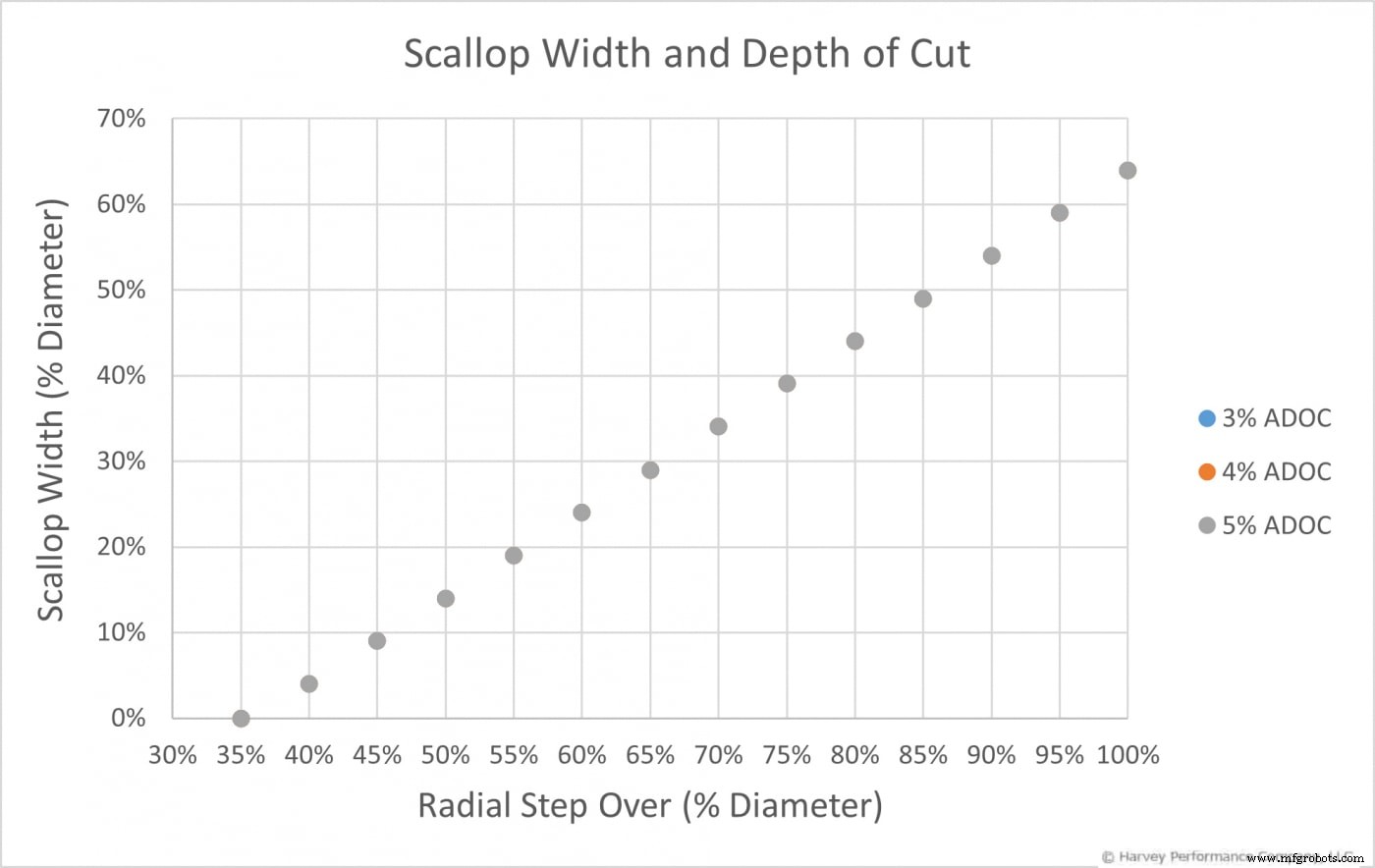
Aus den Diagrammen in den Abbildungen 4 und 5 erhalten wir die folgenden Gleichungen für Bogenmaße.
Hinweise zu diesen Gleichungen:
- Diese Gleichungen gelten nur für Hochvorschub-Schaftfräser von Helical Solutions
- Diese Gleichungen sind Annäherungen
- Die Gleichung für die Muschelhöhe ist nach Erreichen der axialen Schnitttiefe ungenau
- RDOC wird in Prozent des Durchmessers angegeben (0,55 x Durchmesser, 0,65 x Durchmesser usw.)
Krümmung der Unterkante von Hochvorschub-Schaftfräsern
Je kleiner der Krümmungsradius, desto größer die Höhe des Bogens. Beispielsweise hinterlässt der große Teilradius der unteren Schneidkante des Hochvorschub-Schaftfräsers von Helical Solutions im Vergleich zu einem Kugelstirnfräser, der mit derselben Werkzeugbahn programmiert ist, eine kleinere Auskehlung. Abbildung 6 zeigt einen direkten Vergleich eines Kugelkopffräsers und eines Hochvorschubfräsers mit der gleichen radialen und axialen Schnittiefe. Die Bogenbreite und -höhe sind beim Kugelkopffräser deutlich größer, da er einen kleineren Krümmungsradius hat.
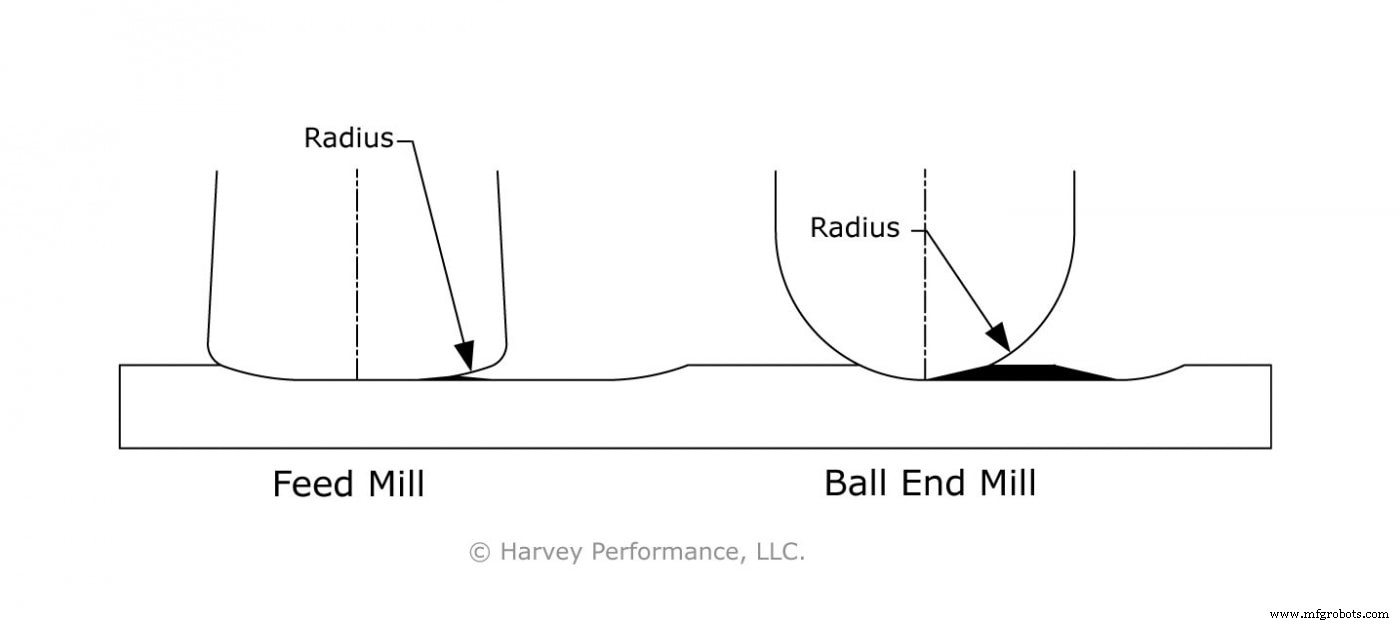
Vollständiges Schlitzen
Beim Schlitzen sollte die Vorschubgeschwindigkeit im Vergleich zum Schruppen stark reduziert werden, da ein größerer Teil der unteren Schneidkante im Eingriff ist. Wie in Fig. 7 gezeigt, entspricht die axiale Untersetzung nicht dem axialen Eingriff. Sobald er in einen vollen Schlitz eingreift, nimmt der Chip eine komplexe Form an. Wenn Sie den Span von der Seite betrachten, können Sie sehen, dass das Werkzeug nicht zu einem bestimmten Zeitpunkt den gesamten axialen Eingriff schneidet. Der Span folgt der Kontur am Schlitzschnitt in Form der Werkzeugunterkante. Aufgrund dieses Phänomens taucht der Span bis zum tiefsten Punkt des Schlitzes ein und dann wieder bis zum höchsten Punkt des axialen Eingriffs entlang der Seite. Dadurch entsteht ein langer, dünner Span, der die kleinen Rillentäler des Werkzeugs verstopfen kann, was zu einem vorzeitigen Werkzeugausfall führt. Dies kann gelöst werden, indem die Vorschubgeschwindigkeit verringert und die Kühlmittelmenge erhöht wird, die bei der Operation verwendet wird.
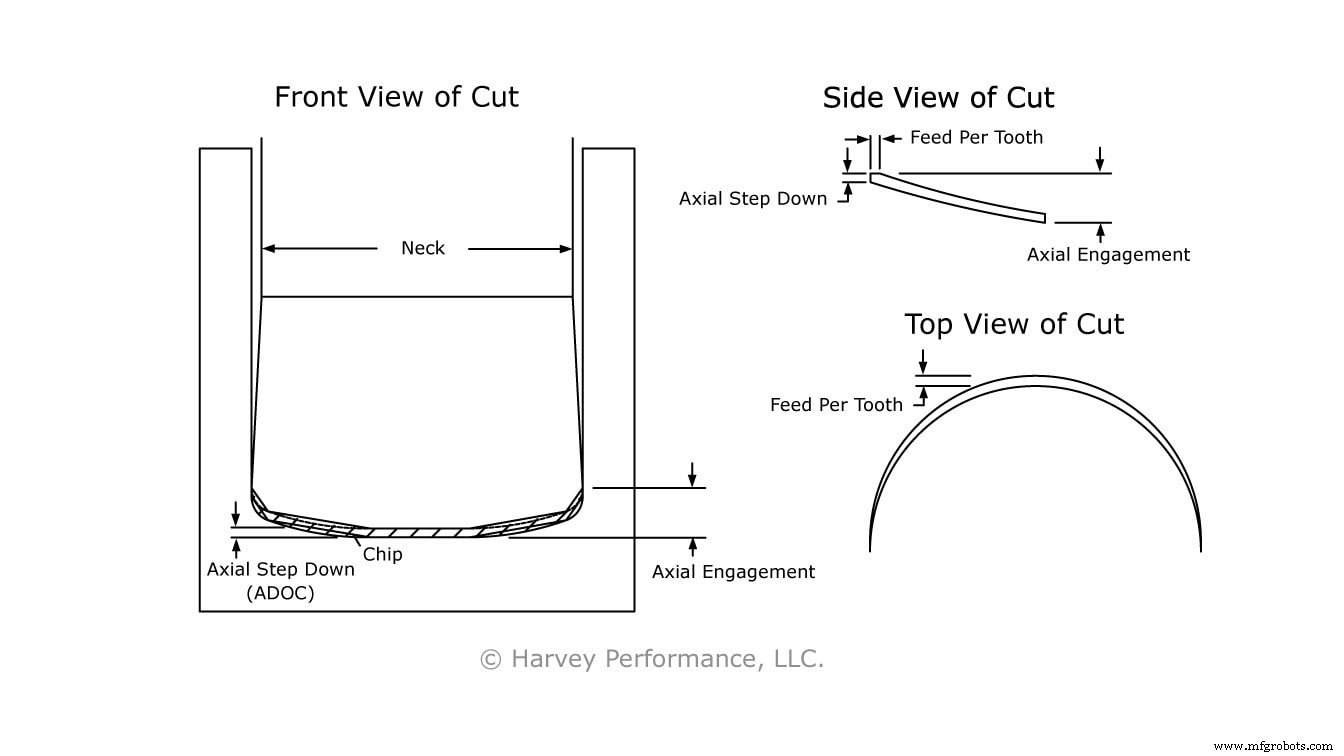
Zusammenfassend lässt sich sagen, dass das gekrümmte Profil der Unterkante des Werkzeugs höhere Vorschübe beim Fräsen mit hohem Vorschub ermöglicht, da es mit seinem geringen Einstellwinkel einen Spanverdünnungseffekt erzeugt. Dieser geringe Einstellwinkel verteilt auch die Schnittkräfte axial statt radial und reduziert so das Rattern, das ein normaler Schaftfräser unter den gleichen Bedingungen erfahren könnte. Maschinisten müssen jedoch vorsichtig sein, da die gekrümmte untere Kante auch die Bildung von Muscheln ermöglicht, einen programmierbaren Radius erfordert, wenn einige CAM-Pakete verwendet werden, und das Schlitzen nicht annähernd so produktiv macht wie Schruppoperationen.
CNC-Maschine
- um das Brechen von Schaftfräsern zu stoppen
- Was ist das beste Werkzeug zum Schneiden von Blech?
- Die Geschichte der Bohrwerke
- Vespel®:Das Luft- und Raumfahrtmaterial
- Leitfaden zur Fehlerbehebung für Schaftfräser und Fräser
- Einführung in das hocheffiziente Mahlen
- Optimierung der Ergebnisse bei der Bearbeitung mit Miniatur-Schaftfräsern
- So verlängern Sie die Lebensdauer Ihres Schaftfräsers
- So maximieren Sie Schaftfräser mit hoher Balance
- Was Sie über den Wendeschneidplattenfräser wissen müssen