Auf dem Weg zur digitalen Herstellung intelligenter Multimaterialfasern
Zusammenfassung
Fasern sind allgegenwärtig und in der Regel passiv. In einer Faser realisierte Optoelektronik könnte mehrere Anwendungsbereiche revolutionieren, darunter biosynthetische und tragbare Elektronik, Umweltsensorik und Energy Harvesting. Die Realisierung von Hochleistungselektronik in einer Faser bleibt jedoch eine anspruchsvolle Herausforderung, da eine Materialverarbeitungsstrategie schwer zu fassen ist, die es ermöglichen würde, aus kristallinen Halbleitern wie Silizium hergestellte Bauelemente in einer geordneten, adressierbaren, und skalierbare Weise. Aktuelle Ansätze zur Herstellung von Fasersensoren sind entweder nicht skalierbar oder beschränken die Auswahl an Halbleitern auf amorphe, wie Chalkogenidgläser, die in ihrer elektronischen Leistung Silizium unterlegen sind, was zu einer begrenzten Bandbreite und Empfindlichkeit solcher Sensoren im Vergleich zu einem Standardsilizium führt Fotodiode. Unsere Gruppe begründet eine universelle In-Fiber-Fertigung von Logikschaltkreisen und sensorischen Systemen analog zur sehr großen Integration (VLSI), die die Entstehung des modernen Mikroprozessors ermöglichte. Wir entwickeln eine vielseitige Hybridfertigungsmethodik, die In-Faser-Materialarchitekturen aufbaut, die typisch für integrierte mikroelektronische Geräte und Systeme in Siliziumdioxid, Silizium und Hochtemperaturmetallen sind. Diese Methodik, die als „VLSI for Fibers“ oder „VLSI-Fi“ bezeichnet wird, kombiniert den 3D-Druck von Preforms, ein thermisches Ziehen von Fasern und die Montage von fasereingebetteten integrierten Bauteilen nach dem Ziehen durch materialselektive, räumlich kohärente Kapillartrennung der Faserkerne. Wir glauben, dass diese Methode eine neue Klasse von langlebigen, kostengünstigen, durchdringenden Fasergeräten und Sensoren liefern wird, die die Integration von Stoffen mit von Menschenhand geschaffenen Objekten wie Möbeln und Kleidung in das Internet der Dinge (IoT) ermöglichen. Darüber hinaus wird es die Innovation im 3D-Druck fördern und den digitalen Fertigungsansatz auf den Bereich der Nanoelektronik ausdehnen.
Einführung
Obwohl glasgezogene Fasern bis in die Römerzeit zurückreichen, wurden 1792 die ersten funktionstüchtigen optischen Fasern von den französischen Brüdern Chappe für Kommunikationszwecke hergestellt [1]. 1842 zeigte der Schweizer Physiker Jean-Daniel Colladon, dass Licht durch einen Wasserstrahl nach innen geleitet werden kann [2]. Diese beiden Entdeckungen führten zu jahrzehntelangen optischen und materialtechnischen Verbesserungen, die zu den heutigen effizienten Glasfasern führten, die Hochgeschwindigkeits-Telekommunikation und Datenspeicherung über Kilometer Entfernung auf der ganzen Welt ermöglichen, wie das 25.000 km lange transpazifische Unterwasserkabel (TPC) fertiggestellt 1996 [3, 4]. Darüber hinaus werden faseroptische Sensoren (FOS) für eine Vielzahl von biomedizinischen, Öl- und Gas-, Schiffs-, Architektur-, Chemie- und Luft- und Raumfahrtanwendungen eingesetzt [5, 6].
Die 1996 von Philip Russel entwickelte Kontrolle und verbesserte Leistung der Lichtausbreitung mit photonischen Kristallfasern (PCF) öffnete die Türen für die Erforschung komplexerer faserinterner Funktionsstrukturen [7,8,9]. Neue Mikrostrukturen begrüßten auch die Integration von Materialvielfalt in ihre Konstitution [10, 11], um intelligente Fasern für die Elektronik [12], Optoelektronik [11], In-Faser-Synthese [13], Mikrofluidik [14], mikroelektromechanische Systeme [15, 16] und biosynthetische Schnittstellen [17]. Intelligente Fasern unterscheiden sich von herkömmlichen Fasern dadurch, dass sie eine nicht-traditionelle Funktion beinhalten, die über die optische Kommunikation und die typische Verwendung von Fasern in kommerziellen Stoffen hinausgeht. Smart Fibers können für die Ästhetik in elektronischen Textilien verwendet werden, indem das farbige Erscheinungsbild der Fasern durch optische Interferenzen in ihrer Mikrostruktur kontrolliert wird [18] oder zur Leistungssteigerung, beispielsweise im Fall von herkömmlichen Lichtwellenleitern und dielektrischer Spiegelbeschichtung, die eine Lichtlenkung ermöglichen durch Luft [19, 20].
Um eine Faser funktionsfähig zu machen, sollte sie aus Materialien mit unterschiedlichen elektronischen Eigenschaften bestehen, ihre Architektur sollte speziell auf eine bestimmte Funktion ausgelegt sein und ihre inneren Eigenschaften sollten auf die Nanoskala reduziert werden, um Größenordnungen kleiner als der Kern der heutigen Telekommunikation Fasern. Fasern werden typischerweise durch Verfahren zur Herstellung optischer Fasern hergestellt, d. h. durch thermisches Ziehen aus makroskopischen zylindrischen oder quaderförmigen Stäben, die als "Vorformen" bezeichnet werden. Der Herstellungsprozess beginnt mit einer Auswahl geeigneter Kern- und Mantelmaterialien wie Metalle, Isolatoren und Halbleiter. Beispielsweise wurde 2004 die erste Faser mit Metall-Isolator-Halbleiter-Strukturen für die Photodetektion entwickelt [21]. Materialien für die Vorform werden so ausgewählt, dass ihre Viskositäten μ , sind bei Ziehtemperatur vergleichbar und fallen ungefähr in das Fenster von 4 < log(μ )[Poise] < 6 Dies ist erforderlich, um Scherströmungen und Kapillarinstabilitäten zu verhindern, die andernfalls die Geometrie der Faservorrichtung verzerren. Materialien, für die diese Anforderung nicht erreichbar ist, wie Metalle oder kristalline Halbleiter, die während des Faserziehens in ihrer flüssigen Form sehr dünn sind, müssen auf Kanäle mit einem niedrigen Aspektverhältnis mit einer Geometrie nahe dem Gleichgewicht beschränkt werden.
Der Vorformling, der im Wesentlichen eine verkleinerte Version der Faser ist, kann mit einer Vielzahl von Techniken hergestellt werden, wie z (I) und in diesem Review diskutiert und dann durch ein Vakuumsintern konsolidiert. Der Vorformling wird dann in einem Ofen erhitzt und zu einer Faser wie eine Karamell- oder Toffee gedehnt (siehe Ziehkegel in Abb. 1a (II)), während seine Querschnittsanordnung basierend auf den gegebenen thermomechanischen Eigenschaften des Konstrukts wie Viskositäten, Grenzflächen erhalten bleibt Energien, gegenseitige Adhäsion und unterschiedliche Wärmeausdehnung (Abb. 1a (III)) [22]. Dieser Vorgang ist für den Fall eines 3D-gedruckten Vorformlings in Abb. 1a schematisch dargestellt. Ein typischer Zug kann kilometerlange Fasern mit sehr feinen nanoskaligen Querschnittsdurchmessern von etwa 5 nm ergeben [23, 24].
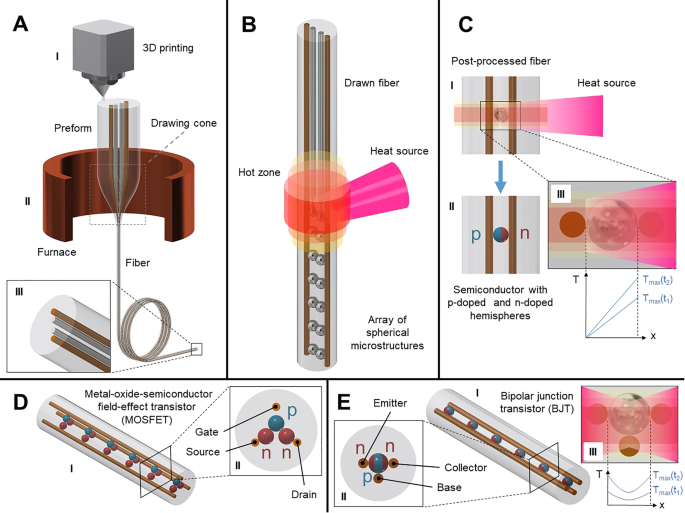
VLSI-Fi:Konzeptionelle schematische Darstellungen der VLSI-Fi-Technik, die den „2D + 1D + 0D”-Ansatz repräsentiert ein Der 3D-gedruckte Vorformling a (I) wird thermisch gezogen a (II) zu einer langen, dünnen Faser, die die Querschnittsgeometrie des Vorformlings (2D) beibehält. b Axiale Strukturierung der Faser durch räumlich kohärentes, materialselektives Kapillaraufbrechen (+1D), was zur Anordnung von anfänglich kontinuierlichen, separaten Kernen zu Arrays von diskreten Bauelementen führt, die parallel kontaktiert werden. c Segregationsgesteuerte Kontrolle der Dotierung in halbleitenden Partikeln nach dem Aufbrechen, die die Kontrolle der internen Architektur eines einzelnen Bauelements ermöglicht c (II) über den thermischen Gradienten c (III). d (I) Schematische Darstellung eines Metall-Oxid-Halbleiter-Feldeffekttransistors (MOSFET) durch VLSI-Fi, wobei die Halbleiter vom p-Typ und vom n-Typ in Blau bzw. Rot dargestellt sind. Die in eine Quarzfaser eingebetteten goldenen Endlosstäbe fungieren als Gate, Source und Drain. Der resultierende Faserquerschnitt ist in d . dargestellt (II). Ebenso e (I) zeigt ein schematisches Bild eines durch VLSI-Fi realisierten Bipolartransistors (BJT), der mit auftreffenden Wärmequellen sowohl von der Emitter- als auch von der Kollektorseite erreicht wird. Der Faserquerschnitt e (II) zeigt Emitter, Kollektor und Basis des BJT (in die Faser eingebettete kontinuierliche Stäbe), wobei die p- und n-Halbleiter des n-p-n-Übergangs blau bzw. rot dargestellt sind
In einem Nachziehschritt, der auf kapillare Instabilitäten ausspielt, kann die Faser durch Erhitzen wieder verflüssigt werden, um das Aufbrechen der Kerne in einer räumlich zusammenhängenden, materialselektiven Weise zu ermöglichen, was eine axiale Kontrolle über die in die Faser eingebetteten Strukturen ermöglicht [25,26, 27] wie in Abb. 1b dargestellt. Alternative Techniken zum axialen Strukturieren der Kerne umfassen UV-Belichtung durch Photomasken in photopolymeren Kernen, was zu nicht trivial geformten Mikropartikeln führt [28]. Andere Hybridfunktionalisierungstechniken umfassen das Beschichten der Faseroberflächen mit funktionellen Materialien [10, 29] und das Einschließen eines Fasermantels durch Ziehen [12] auf ein Array optoelektronischer Bauelemente, die durch standardmäßige komplementäre Metalloxid-Halbleiter (CMOS)-Fertigung hergestellt werden.
Fasern können zu Geweben oder Netzen verwebt werden, um eine kollektive Funktionalität zu erreichen, die die einer einzelnen Faser übertrifft [30]. Durch Biomimikry entworfen, können Fasern gemäß den nützlichen Eigenschaften der Natur geformt werden, um die Funktionalität des Gewebes zu verbessern, wie z. B. Hydrophobie [31]. Die Fasern können auch als Syntheseplattformen für eine kostengünstige Materialherstellung wie die Umwandlung von Aluminiumkernen in Silizium in silikaummantelten Fasern [13] oder die thermisch induzierte Herstellung poröser Strukturen durch Phasentrennung [32] gedacht werden. Fasern können auch der dezentralen und verteilten Signalerkennung dienen, wie z. B. der umweltchemischen Erfassung gefährlicher flüchtiger Stoffe [29]. Die Flexibilität des Faserdesigns ist so groß, dass für komplexe Anwendungen wie die tiefe spinokortikale Stimulation und das Monitoring bei Mäusen für die Erforschung neurodegenerativer Erkrankungen mehrere funktionelle Modalitäten in einer Faser integriert werden können [33]. Diese Beispiele zeigen einige der vielfältigen Bereiche, in denen intelligente Fasern die natürliche Lösung sind.
Motivation
Obwohl Fasern allgegenwärtig sind, bleibt die Integration leistungsfähiger mikroelektronischer Systeme innerhalb einer dünnen Faser eine große Herausforderung [11, 12]. Es wurden verschiedene Ansätze zur Bewältigung dieser Herausforderung vorgeschlagen, wobei sich die Bemühungen hauptsächlich auf Niedertemperaturmaterialien konzentrierten. Beispielsweise wurde die chemische Hochdruckdampfabscheidung (HPCVD) verwendet, um Verbindungshalbleiter in mikrostrukturierte optische Fasern (MOFs) zu integrieren [34] sowie um flexible Silizium-p-i-n-Übergangsfasern zu erzeugen [35]. Alternativ ein CO2 Laser wurde für die Rekristallisation des SiGe-Kerns in Siliziumdioxidfasern verwendet, um deren elektronische Eigenschaften zu verändern [36]. Solche Ansätze führen entweder zu Geräten mit begrenzter elektronischer Bandbreite, wie dies bei Chalkogenidmaterialien der Fall ist, die von Natur aus amorph oder von Natur aus nicht skalierbar sind.
Als solches hat das Fibers and Additive Manufacturing Enabled Systems Laboratory (FAMES Lab) eine Technik zur Steuerung der 3D-Architektur von Fasern entwickelt und implementiert diese derzeit, die in diesem Review beschrieben wird. Da die Kompliziertheit der endgültigen Faser mit der Komplexität des Querschnitts der Vorform korreliert, ermöglicht die Freiformherstellung von Vorformen Funktionalitäten von Faservorrichtungen, die sonst unerreichbar wären. Darüber hinaus ist der 3D-Druck weit verbreitet, was ihn zu einer kostengünstigen und anwenderfreundlichen technologischen Alternative zu traditionell eingesetzten Verfahren macht und eine breite Palette von Materialien ermöglicht, von Thermoplasten über Hochtemperaturmaterialien bis hin zu Biomaterialien [37].
Darüber hinaus verfügt das FAMES-Labor über die Möglichkeit, neben der eher traditionellen Verwendung von Thermoplasten in der additiven Fertigung auch Hochtemperaturmaterialien zu verarbeiten, wodurch wir auch Eigenschaften wie die hohe Elektronenmobilität in Si/Ge [38] nutzen können als zukünftige Verwendung von Bleizirkonattitanat (PZT)/BaTiO3 Verbundwerkstoffe für piezoelektrische Anwendungen mit großen piezoelektrischen Koeffizienten im Vergleich zu Polymeren [39, 40] und einer höheren akustischen Bandbreite [41].
Angesichts dieser Herausforderungen schlagen wir Optimierungslösungen durch additive Fertigung vor, um eine schnellere und komplexere Preform-Herstellung zu erreichen, Simulationen des Kapillarbruchs zur Optimierung der axialen Kontrolle der Faser und Kombinationen unserer Fasern mit Tissue Engineering. Diese Strategien ermöglichen die Schaffung realistischer biomedizinischer Plattformen mit Biosensorik- und Biofunktionalisierungsfähigkeiten für die in vitro-Medikamenten- und Behandlungsanalyse als eine der vielversprechenden Anwendungen für Fasergeräte.
Konzept
Um funktionale Fasern zu realisieren, lassen wir uns von der sehr großen Integration (VLSI) inspirieren – einer digitalen Konstruktions- und Fertigungstechnik, aus der in den 1970er Jahren der moderne Mikroprozessor hervorging. Diese Technik verwendet Photolithographie und chemische/thermische Behandlung belichteter Bereiche des Halbleitersubstratwafers, um die Merkmale der integrierten Schaltung in dieser Schicht (2D) zu definieren, während die Herstellung einer vollständigen Schaltung durch Stapeln solcher Einzelschichten in der Richtung senkrecht zu fortschreitet die Waferoberfläche (+1D). Zusätzlich kann die elektronische Dotierung einzelner Komponenten der Schaltung (+0D) durch Implantation und thermische Aktivierung kontrolliert werden [42]. Unser Ansatz für Fasern, genannt „VLSI for Fibers“ oder „VLSI-Fi“, ist analog:Erstens definieren additive Fertigung und thermisches Ziehen einer Vorform die Querschnittsgeometrie der Faservorrichtung (2D); zweitens kann die resultierende Faser später axial gemustert werden (+1D), was den Zusammenbau von Arrays integrierter diskreter Vorrichtungen aus anfänglich kontinuierlichen, aber getrennten Kernen ermöglicht; und drittens kann eine segregationsgesteuerte Strukturierung einzelner in die Faser eingebetteter Vorrichtungen (0D) durchgeführt werden. Tabelle 1 zeigt einen Vergleich zwischen den beiden Techniken, wobei die Übereinstimmung zwischen jedem Grad der Geometriekontrolle hervorgehoben wird, der durch jede Technik ermöglicht wird („2D + 1D + 0D“). Die Schemata der beschriebenen Schritte sind im Detail in Fig. 1 gezeigt, wo Beispiele für mögliche in die Faser eingebettete Vorrichtungen unter Verwendung der VLSI-Fi-Technik realisiert werden könnten.
Experimenteller Abschnitt
In diesem Abschnitt beschreiben wir zunächst unsere Arbeit zum 3D-Druck von Polycarbonat-Preforms, gefolgt von den jüngsten Fortschritten im Glas-3D-Druck mit Stereolithographie. Dann nähern wir uns der axialen Strukturierung der Fasern durch eine räumlich kohärente, materialselektive Kapillaraufspaltung, die den Zusammenbau von anfänglich kontinuierlichen, separaten Kernen zu Arrays von diskreten Bauelementen ermöglicht, die parallel kontaktiert werden. Schließlich schlagen wir die Anwendung unserer Biointerfacing-Fasern in Kombination mit Tissue Engineering vor, um das lebensfähige Gewebewachstum in vitro zu überwachen. Funktionen werden durch die Verwendung von mikrofluidischen Kanälen in der Faser ermöglicht, um Zellen und Signalbiochemikalien und Drähte aus einer Legierung mit Formgedächtnis zur Bewegungssteuerung zu transportieren, sowie piezoelektrische Elemente, um die Umgebung durch Ultraschallwellen abzubilden.
Zeichnung von 3D-gedruckten Vorformlingen
Wie bereits erwähnt, sind konventionelle Verfahren zur Herstellung von Vorformlingen, wie Dünnschichtwalzen und Stapeln und Rohen [10], bei der Herstellung komplexer geometrischer Strukturen begrenzt, nehmen viel Zeit im Faserziehprozess in Anspruch und erfordern Fachkenntnisse Arbeitskraft und teure Ausrüstung. Der 3D-Druck adressiert diese Probleme mit Hilfe von löslichem Trägermaterial und seinem teilautomatisierten und anwenderfreundlichen Verfahren. Dies ermöglicht das einfache Drucken sehr komplexer Geometrien in relativ kurzer Zeit.
Um den Einfluss des Druckwinkels von Polycarbonat (Hatchbox 3D)-Preforms zu beurteilen, wurden zylindrische und quadratische Stäbe mit einem Prusa i3 MK2 FDM-Drucker mit einem Kopf gedruckt. Die Extruder- und Druckbetttemperaturen wurden auf 235 °C bzw. 105 °C eingestellt, und der Drucker wurde so eingestellt, dass er mit einer 0,35-mm-Düse 100 % Infill-Preforms produzierte. Die Ausrichtung der Schichten im Vorformling hängt von der horizontalen Ausrichtung des Teils in Bezug auf das Druckbett ab, und wenn der Vorformling während des thermischen Ziehens in den Ofen eingeführt wird, wird der Wärmefluss durch die Schichtorientierung beeinflusst. Um zu testen, welche Orientierung für das Thermoziehen am besten geeignet ist, wurden Vorformlinge mit 0°, 15°, 30°, 45° und 90° Orientierung gedruckt. Alle Winkel wurden zwischen der Längsachse des Vorformlings und der Horizontalachse gemessen. Die 3D-gedruckten Preforms durchliefen den thermischen Ziehprozess in einem Ofen mit drei Temperaturzonen von 90°C, 100°C und 200°C. Bei den zylindrischen Vorformlingen war das thermische Ziehen bei den Winkeln 0° und 45° erfolgreich. Die 90° Preform-Ziehungen scheitern immer aufgrund von Schichtablösung.
Wir konnten auch erfolgreich Nichtgleichgewichtsstrukturen wie einen quadratischen Stab mit einem improvisierten Füllmuster zeichnen, wie in Abb. 2a (I) gezeigt, wobei anstelle des geradlinigen Füllmusters auch die Füllung so eingestellt wurde, dass sie den Perimetern folgt und drucken in geordneter Struktur. Das Ziehen des Vorformlings auf 0°-Quadratbasis war erfolgreich, und obwohl er sich leicht verformte, war die Faser immer noch in der Lage, die Form des Vorformlings beizubehalten. Fasern mit Abmessungen von nur 40 &mgr;m × 60 &mgr;m wurden erfolgreich gezogen und sind in Fig. 2a ohne Schichtablösung gezeigt. Außerdem wurden alle Schichten richtig konsolidiert. Ein Beispiel für einen Faserquerschnitt ist in Abb. 2a (IV) gezeigt, und Bilder einer Faser vor und nach dem Glühen sind in Abb. 2a (V) bzw. 2a (VI) gezeigt, wo wir sehen, dass die geglühte Faser erreicht optische Transparenz, die in zukünftigen Arbeiten geprägt sein wird. Aus diesen Experimenten schließen wir, dass die erfolgreichsten Preforms diejenigen sind, die bei 0° gedruckt wurden, während 90° während des Ziehprozesses immer delaminieren. Die Konsolidierung der Schichten in den thermisch gezogenen Fasern verbesserte sich mit abnehmendem Orientierungswinkel des 3D-gedruckten Vorformlings.
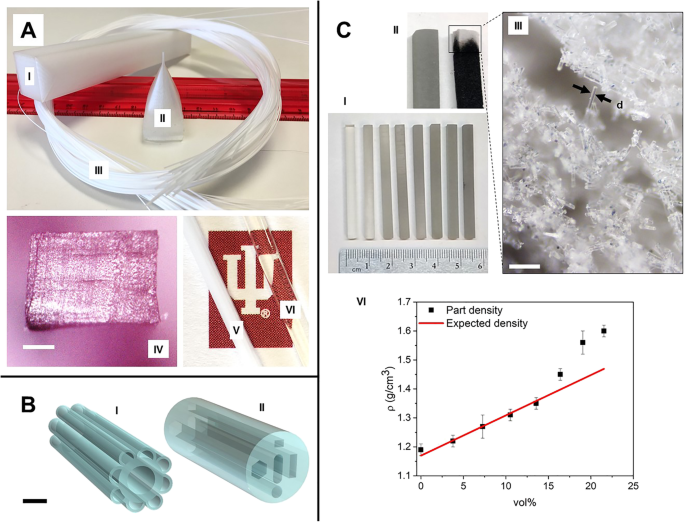
3D-gedruckte Preforms:a (I) 3D-gedruckte Polycarbonat-Vorform mit quadratischer Basis. a (II) Ziehkegel. a (III) Erhaltene Polycarbonatfaser nach dem thermischen Ziehen. a (IV) Faserquerschnitt nach dem Ziehprozess, ohne Schichtablösung. Der Querschnitt ist aufgrund der nicht isotropen Porosität des Füllmusters (Maßstab 200 μm) rechteckig. a (V) Gezogene Faser vor dem Glühen. a (VI) Gezogene Faser nach dem Tempern mit scheinbarer optischer Transparenz. b CAD-Modelle von Glas-Preforms, erfolgreich in Kalknatronglas mit hochpräzisem 3D-Druck auf Extrusionsbasis realisiert. b (I) Struktur ahmt blaues Tarantelhaar nach. b (II) Vorformmodell mit Nichtgleichgewichts-Querschnittsgeometrie (Maßstab 1 cm). c (I) Quadratische Glasproben mit zunehmender Glasfüllung (von links nach rechts), bedruckt mit SLA-Technik. c (II) Detail einer Glasprobe vor dem Einbrennen (links) und während des Einbrennens (rechts). Bei letzterem kann man die schwarze Färbung sehen, die von den karbonisierten Harzresten herrührt, während die Spitze eine weiße Färbung aufweist, nachdem diese Reste ausgewaschen wurden. c (III) Mikroskopische Aufnahme des ausgewaschenen Schnitts (Maßstab 200 μm), wobei die Weißfärbung durch die Eigenfarbe der verdichteten gemahlenen Fasern in einer zusammenhängenden porösen Struktur entsteht. Außerdem korreliert die Nennweite der Glasfaser, im Bild mit d gekennzeichnet, mit den erwarteten Werten von 16 μm (#38 Fiber Glast). c (IV) Ein Diagramm der Dichten der gedruckten Glasvorformlinge (ρ ) als Funktion des Volumenanteils der mit Harz vermischten Glasfasern zusammen mit der durchschnittlichen Dichte des Druckmaterials
3D-Druck von Glasvorformen
Über Thermoplaste hinaus haben Gläser einschließlich Quarzglas bedeutende wissenschaftliche und technische Anwendungen in der Optik, Kommunikation und Elektronik [43]. Strukturierte Siliziumdioxidfasern könnten für mehrere Anwendungen von Nutzen sein, beispielsweise für die farbstofffreie Färbung von Stoffen für Mode, photonische Kristallfasern für die optisch-chemische Detektion oder Singlemode-Fasern für die Telekommunikation und die enge Fokussierung von Licht. Diese Fasern werden im Allgemeinen durch einen zweistufigen Prozess hergestellt:die Vorformherstellung und das thermische Ziehen der Vorformlinge zu einer Faser. Während der Ziehprozess relativ einfach und billig ist, erfordert die Vorformherstellung an dieser Stelle eine Einzelfallbehandlung und für jede spezifische Vorformkonfiguration muss eine separate Technologie entwickelt und angewendet werden.
Abbildung 2b zeigt Computer-Aided-Design (CAD)-Modelle für Kalknatronglas-Preforms, die mit hoher Präzision erfolgreich in der extrusionsbasierten Drucktechnologie realisiert wurden, ähnlich den von der Firma Micron3DP beschriebenen Produkten [44]. Dieses Material weist insbesondere bei langen Wellenlängen wie IR vielversprechende optische Eigenschaften auf [45], was es zu einem interessanten Kandidaten für die Herstellung von Fasern mit neuartigen optischen Funktionalitäten macht. Das in Abb. 2b (I) gezeigte Preform-Modell ahmt die Struktur des blauen Tarantelhaares nach, ähnlich der in [46] dargestellten Struktur, und in Abb. 2b (II) enthält der Preform-Querschnitt Nichtgleichgewichtsgeometrien und ist daher anfällig für Umformungen aufgrund der Minimierung der Oberflächenspannung. Diese Modelle wurden entworfen und realisiert, um die Möglichkeit zu verifizieren, komplexe, nicht im Gleichgewicht befindliche Vorformquerschnitte zu erreichen.
Da die Mantelstruktur der Faser während des Ziehprozesses mechanische Integrität verleiht – da sie aus dem viskosesten Material besteht – haben sich unsere Bemühungen bisher auf diese Komponente der Faser konzentriert, wobei wir letztendlich auf die Erhaltung der Querschnittsgeometrie abzielen des Vorformlings. Langfristig streben wir die Entwicklung von Multimaterial-Extrusionstechniken an, die es uns ermöglichen, mehrere Materialien monolithisch in denselben Druck zu integrieren. Alternativ ist es möglich, die Struktur mit pulverförmigen Materialien wie Si oder Ge zu füllen. Anschließend kann die gefüllte Struktur gesintert werden, um den Vorformling zu erhalten. Gumenniket al. haben einen ähnlichen Ansatz beschrieben [47].
Wenn Interesse an der Herstellung einer Faser mit Natronkalkglas als Kernmaterial besteht, besteht ein einfacher Ansatz darin, eine Vorform mit hängendem Kern zu drucken. Fasern mit suspendiertem Kern sind für verschiedene Anwendungen von Interesse, darunter Sensorik [48] und verlustarme Terahertz-Führung [49], und werden typischerweise mit Polymeren realisiert [49]. Bei dieser Art der Fasergeometrie wird der Kern von Streben getragen, die ihn mit der Außenschicht verbinden. Nach dem Ziehen werden diese Strukturen auf Abmessungen in der Größenordnung der interessierenden Wellenlänge reduziert, so dass für das geführte Licht die Wirkung eines schwebenden Kerns entsteht. Monroet al. haben über Fasern mit suspendiertem Kern in verschiedenen Materialien wie Siliziumdioxid und Wismutglas berichtet [48]. Sie bieten auch eine Reihe von Beispielen für Sensoranwendungen dieser Fasern, insbesondere in der biologischen und chemischen Sensorik, die die Realisierbarkeit dieser Fasergeometrien bestätigen.
Neue Ansätze für den Stereolithographie-basierten 3D-Druck von Glas mit kundenspezifischen Harzen wurden unter Verwendung von photohärtbarem Siliziumdioxid-Nanokomposit entwickelt [50]. Hier schlagen wir ein Verfahren vor, bei dem Glasfaser-Preforms durch 3D-Druck auf der Grundlage von handelsüblichen Harzen hergestellt werden, was es zu einer kostengünstigeren und einfacheren Methode macht, 3D-gedruckte Glasteile mit Stereolithographie (SLA) herzustellen. Der SLA-Drucker (Form 2 von Formlabs) arbeitet mit einem Laser mit einer Wellenlänge von 405 nm, um das Harz durch den Boden des Bottichs zu vernetzen, während die gebaute Plattform schrittweise Schicht für Schicht ansteigt.
Um Glasdrucke zu erhalten, verwenden wir für den Druckprozess eine Mischung aus handelsüblichem klarem Harz (Formlabs FLGPCL04 Clear) mit 0,79 mm (1/32") Borosilikatglasfasern (#38 Fiber Glast). Dies ermöglicht eine hervorragende Kontrolle der endgültige Zusammensetzung des Druckmaterials und Flexibilität bei der Erzielung der gewünschten Fasereigenschaften Die Glasfasern wurden mit einem Magnetrührer in klares Harz dispergiert. Das Glas wird in kleinen Schritten zugegeben und nach jeder Zugabe für ca. 3 min homogenisiert. Für den Druckprozess Der Drucker wurde auf den offenen Modus eingestellt, um die Verwendung unseres benutzerdefinierten Harzes zu ermöglichen. Quaderförmige Vorformlinge mit den Abmessungen 4 "× 4" x 50" mm wurden in einer 90°-Ausrichtung gedruckt. Nach dem Drucken wurden die Teile 10 Minuten lang in Isopropanol getaucht, um überschüssiges Harz zu entfernen , und nachgehärtet mit UV-Licht für 30 Minuten bei 60 ° C. Ausgehärtete Glasvorformlinge mit zunehmendem Volumenverhältnis von Glasfasern, die in das Druckharz eingemischt sind (von links nach rechts), sind in Abb. 2c (I) gezeigt.
Die Preforms werden dann nachbearbeitet, um das restliche Harz zu entbinden und die Glaspartikel zu sintern, wodurch ein Teil vollständig aus Glas besteht. Die Auswirkungen dieser Prozesse auf den Preform sind in Abb. 2c (II) dargestellt, wo wir einen Preform nach dem Aushärten (links) und nach dem Backprozess (rechts) sehen. Bei letzterem ist die Schwarzfärbung durch das Brennen im Veraschungsofen zu sehen, während die Spitze nach dem Entbindern eine Weißfärbung aufweist. Fig. 2c (III) zeigt eine mikroskopische Aufnahme eines Vorformlings vor dem Sintern, wobei zu sehen ist, dass das gesamte Harz tatsächlich aus dem Teil ausgebrannt ist, was zu einer verbundenen Struktur führt, die nur durch die Glasfasern gebildet wird. Mehrere Parameter müssen kontrolliert werden, wie zum Beispiel die Einbrenntemperatur und das Heizprofil, um chemische Reaktionen und Schrumpfung zu kontrollieren. Die thermische Entbinderung des Bindemittels erfolgte mit einem Veraschungsofen. Die resultierenden braunen Teile wurden in einem Hochtemperatur-Rohrofen gesintert. Das Sintern wurde bei einer Temperatur von 1300°C und einem Druck von 5 × 10 –2 . durchgeführt mbar, nach dem vorgeschriebenen Protokoll in [51]. Eine Haltephase bei 800 °C wurde eingestellt, um molekular gebundenes Wasser und oberflächengebundene Silanolgruppen zu verdampfen. Das Sintern unter Vakuum verbessert die optische Transparenz, da es das Einschließen von Luft innerhalb des gesinterten Glasteils reduziert [52].
Nach der Nachbearbeitung werden Volumen und Gewicht der Teile gemessen, um die Dichte zu erhalten. Diese wird dann mit der durchschnittlichen Dichte des Druckmaterials – bestehend aus der Mischung aus härtbarem Harz und Glasfaser – verglichen, die durch ρ . berechnet wird Durchschn. = ρ Harz (1 − χ v ) + ρ Glas (χ v ), wobei ρ Harz = 1,17 g/cm 3 ist die Dichte des ausgehärteten klaren Harzes, ρ Glas = 2,55 g/cm 3 die Dichte der gemahlenen Glasfasern ist und χ v ist das Volumenverhältnis der in das Harz eingemischten Glasfasern.
Die Ergebnisse sind in Tabelle 2 und graphisch in Abb. 2c (IV) dargestellt, wo wir die Dichte der gedruckten Teile für verschiedene Volumenanteile von Glasfasern im Harz im Vergleich zur durchschnittlichen Dichte des Druckmaterials darstellen. Wir beobachten, dass bei geringeren Volumenverhältnissen von Glas, das in das Harz eingemischt wird, die erhaltenen Ergebnisse innerhalb des erwarteten Bereichs liegen. Bei höheren Glaskonzentrationen sehen wir jedoch eine Abweichung vom linearen Verhalten der idealen Dichte. Dies kann auf die Sedimentation während des Drucks zurückgeführt werden, die bei diesen Volumenverhältnissen signifikant wird, wodurch effektiv höhere Glaskonzentrationen in diesen Drucken erzeugt werden. Der Druckvorgang findet am Boden des Tanks statt, wo die Glaskonzentration durch Sedimentation während des Druckvorgangs ständig ansteigt. Sie beginnt bei (und darüber) der anfänglichen einheitlichen Konzentration, die auf die berechnete Kurve fallen sollte.
Aus Tabelle 2 können wir sehen, dass bei 21,54 Vol.-% gemahlenen Glasfasern in Füllteilen die gemessene Dichte 1,61 g/cm 3 . betrug , was bedeutet, dass der tatsächliche Volumenanteil 31,88 vol% beträgt. Während des Versuchsprozesses erhielten wir eine Probe mit tatsächlich 34,78 vol% gemahlenen Glasfasern als Füllung. Dieses Ergebnis war nicht weit von der 37,5 Vol.% Silica-Füllung entfernt, die von Kotz et al. [53], wo ein kundenspezifisches Harz entwickelt wurde, im Gegensatz zu dem kommerziellen Harz, das wir in dieser Arbeit verwenden. Zukünftige Richtungen für diese Arbeit umfassen Wärmebehandlungsverfahren, das Sintern von Teilen und die Untersuchung der mechanischen und optischen Eigenschaften der resultierenden Teile.
Kohärentes materialselektives Kapillaraufbrechen und Dopingkontrolle
Sobald ein Vorformling thermisch gezogen wird, ist das Ergebnis eine lange, dünne Faser, bei der der Querschnitt erhalten bleibt, wie in Fig. 1a (III) gezeigt. Im Falle einer Faser mit einem oder mehreren Kernen können diese durch einen räumlich kohärenten, materialselektiven Kapillaraufschlussprozess [26] axial gemustert werden, wie in Abb. 3 gezeigt. Während das Tomotika-Modell die Bildung periodischer Instabilitäten in einem unendlicher, gleichmäßig erhitzter Flüssigkeitszylinder, der die Auswirkungen der umgebenden Flüssigkeit berücksichtigt [55], sich ausbreitende Rayleigh-Instabilitäten führt das Konzept der Frontausbreitung ein [56]. Obwohl in der Literatur mehrere Beispiele für mathematische Behandlungen von Kapillarinstabilitäten zu finden sind, beispielsweise in Liang et al. [57] konzentrieren sich diese Arbeiten hauptsächlich auf isotherme Therapien, die in unserem Fall nicht anwendbar sind. Darüber hinaus hat unser Fall eine zusätzliche Komplikation des sich ausbreitenden thermischen Gradienten und somit des Viskositätsgradienten. Als solches ist es wahrscheinlich näher am kriteriumsgetriebenen Prozess der marginalen Instabilität, wie in Powers et al. [56]. Durch die Kombination unserer rechnerischen und experimentellen Ergebnisse wollen wir ein mathematisches Modell für den Faserbruch über axiale thermische Gradientenphänomene erstellen.
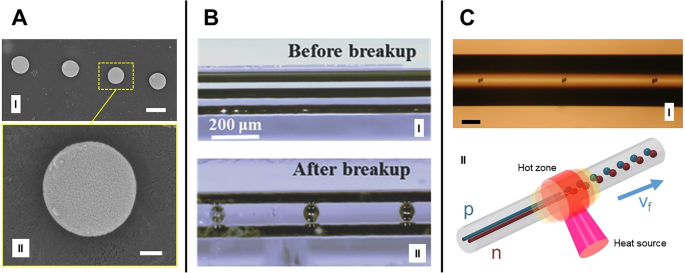
Kapillartrennung:a (I) Faserschnitt, der Si-Kugeln zeigt, die durch kapillares Aufbrechen gebildet wurden (Maßstab 0,5 µm). a (II) Einzelkugelbild zur Darstellung der Formqualität (Maßstab 100 nm), von Gumennik et al. [26]. b (I) Beispiel einer Metall-Halbleiter-Metall-Photodetektorvorrichtung in einer einzelnen Quarzglasfaser vor b (I) und nach b (II) Aufbruchverfahren, von Wei et al. [54]. c (I) Aufbrechen einer Doppelkernfaser in bisphärische Cluster (Maßstab 100 μm), von Gumennik et al. [26]. c (II) Schematische Darstellung des in c gezeigten Prozesses (I), mit p- und n-Typ-Kernen in blau bzw. rot dargestellt
Die gegenwärtige Phase der Kapillarzerfallssimulation konzentriert sich auf den stationären Bereich. Wir interessieren uns dafür zu analysieren, wie sich Instabilitäten in einer anfänglich stationären Faser entwickeln, die einem thermischen Gradienten ausgesetzt ist. Dieser Prozess ist analog zum Anfangsschritt der Kapillar-Aufbruch-Experimente von Gumennik et al. [26], bei dem eine Quarzfaser mit einem 4 μm dicken Si-Kern mit Durchflüssen von 0.3 bzw. 0.1 L/min durch die heiße Zone einer Wasserstoff-Sauerstoff-Flamme geführt wird. Obwohl die mit diesem Brennertyp erreichbare Höchsttemperatur bis zu 2800 °C betragen kann, muss die maximale Temperatur der Faser unter dem Siedepunkt von Silica von 2230 °C liegen.
Considering that the flame width is between 3 and 3.5 mm and that the fiber has a diameter of about 300 μm, it is easy to understand why it is not feasible to experimentally measure the temperature gradient to which the fiber is exposed. Furthermore, the dynamic nature of the breakup process and the fact that it involves multiple materials with varying emissivities further adds to the complexity of the problem, while the fiber’s high aspect ratio and sharp viscosity ratios render the numerical simulation of the full Navier-Stokes equations computationally challenging.
In our simulations (using COMSOL Multiphysics® 5.3a, with its Microfluidics and Heat Transfer modules) shown in Fig. 4a, we assume an axisymmetric fiber with radius r fiber = 140 μm, composed of a thin Silicon core (r core = 2 μm) enclosed in a Silica cladding. Initial heat-transfer simulations showed that a fiber length of 15 mm is sufficient to ensure that the fiber extremities remain at room temperature, thus avoiding influence from the boundaries to the breakup process. Through the sweep of different parameters such as heat source length and distance to the fiber surface, as well as power, we can observe the changes produced in the breakup behavior, thus collecting information about the temperature gradient. Also of importance are the breakup period and speed, parameters which can be compared to experimental results and used for the refinement of the simulations.
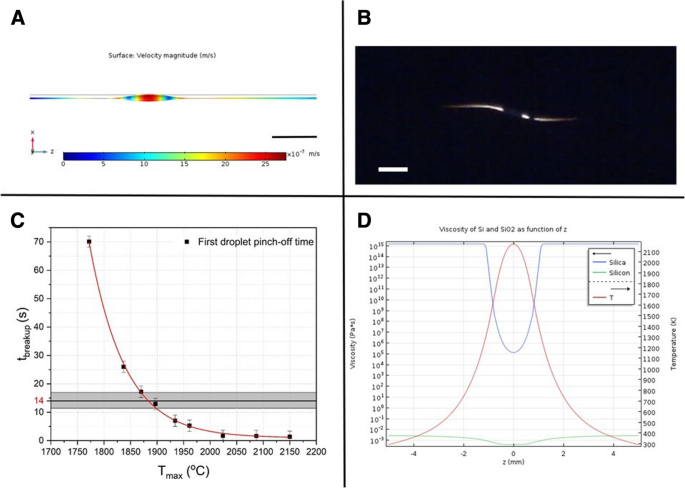
Capillary breakup simulations:a Image of the simulated Si core during the first droplet formation, right before the pinch-off for T max = 1900 °C. Color scale represents surface velocity (scale bar = 50 μm). b Snapshot of fiber breakup experiment recording just after the first droplet pinch-off, indicating a breakup time of 14 ± 3 s (scale bar = 60 μm). c Breakup time t breakup for different values of T max . The exponential dependence of t breakup on T max is evident, a behavior that is expected due to the dependence of t breakup on the core’s viscosity, which in turn depends exponentially on the temperature. The shaded rectangle encompasses the temperature range compatible with this breakup time-scale. d Si core and SiO2 cladding viscosities as a function of axial position, with temperature pro le over-imposed, for T max = 1900 °C
The simulations are performed in two steps:first, the steady-state temperature profile is calculated for different heat source powers, in order to achieve the desired maximum temperature T max . The results are then exported to a time-dependent fluid-flow simulation, where the Navier-Stokes equation is solved with time steps of 0.05 s, from 0 s until the first droplet pinch-off (t breakup ), which is dependent on T max , as can be seen in Fig. 4c, where t breakup is plotted for different values of T max . It is possible to observe that t breakup has an exponential dependence on T max , which is expected since t breakup is proportional to the core’s viscosity, which in turn is exponentially dependent on the temperature.
The relevant parameters used in these simulations are listed in Table 3. Preliminary simulations indicate that the phase transition of the Si core has no significant influence on the steady-state temperature pro le obtained, neither on the subsequent fluid-flow simulations since, in the entire region where the capillary instabilities occur, the temperature is higher than the melting point of Si. Therefore, in order to maintain the model as less computationally intensive, we simulate a core of liquid Si as a first approximation. Moreover, although a fully coupled heat-transfer and fluid-flow simulation is preferable, we consider that the effects of coupling bring second-order corrections to the solution and thus can be neglected at this stage. An image of the simulated core during the first droplet formation, right before the pinch-off, is shown in Fig. 4a, for T max = 1900 °C. A plot of the densities of silica and silicon, as a function of the axial position (in the simulation, the z-axis) for this particular simulation, is presented in Fig. 4d, with the temperature profile over-imposed.
Our results allow us to define the ranges of viscosities for which the time scales for breakup are comparable to those observed experimentally, thus assessing qualitatively the temperature profile imposed on the fiber. Fig. 4b shows a snapshot of a fiber breakup experiment recording just after the first droplet pinch-off, at the frame corresponding to t = 39 s. Since the resolution of the images before this frame is not ideal, judging on the basis of the symmetry of the breakup behavior, it is possible to assess that the pinch-off of the first droplet occurs at t = 35 ± 3 s, which translates to a breakup time after the temperature steady-state regime is achieved, of 14 ± 3 s. The shaded rectangle in Fig. 4c encompasses the temperature range compatible with this breakup time-scale, from which we can infer that the maximum temperature to which the fiber is exposed is 1885 ± 15 °C. With the collection of statistics on the breakup behavior in the future, we aim to develop a procedure for the temperature measurement of the process, which is otherwise unattainable by conventional means [26, 58, 59].
Moreover, segregation-driven control of doping in post-breakup semiconducting particles is attainable, allowing to control an individual device’s internal architecture. It is possible to control the structure of a single sphere, as was demonstrated by Gumennik et al. [47] shown in Fig. 5. When the droplet is exiting the flame, it experiences a thermal gradient:it is colder on the end distant from the flame, and consequently, it is expected to solidify laterally, starting from the colder side. If the sphere is doped with a material that is more soluble in a liquid than in a solid, this dopant will be repelled into the liquid as the solidi cation front propagates, collecting predominantly on the hot side. This effect is shown schematically in Fig. 1c and can be used to synthesize structured particles, composed for example of Ge-rich Si, (as shown in Fig. 5):Starting with 50:50 Si-Ge mixture in the fiber core, after the breakup the sphere will solidify, such that the Ge is extruded into the melt as the solidi cation evolves, leading to anisotropic distribution and resulting in axially oriented Janus particle heterojunctions [47]. This method can be extremely useful in assembling complex fiber-embedded devices such as heterojunctions, as shown in Fig. 1d and e.
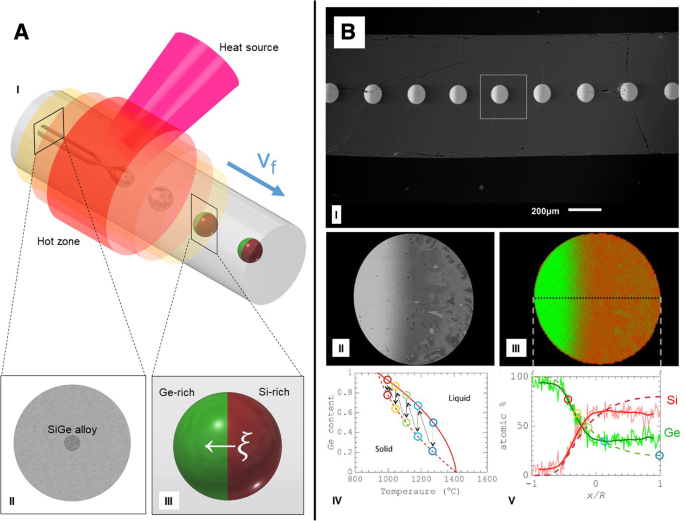
Segregation control of doping:a (I) Schematic illustration of the segregation-driven control of doping in post-breakup semiconducting particles. Details:cross section of a Ge-rich Silicon continuous core in silica fiber a (II) and post-breakup schematic drawing of doping-segregated sphere, or Janus particle, with the Ge-rich side indicated in green a (III). b (I) Scanning Electron Microscope image in backscattered mode of the fiber, polished along its axis, showing an array of Janus particles. b (II) Detail of single Janus particle cross section. b (III) Energy-dispersive X-ray spectroscopy (EDS) map of Janus particle, indicating non-homogeneous distribution of Ge along the cross section, from overlaid maps of Si (in red) and Ge (in green). b (IV) Si-Ge equilibrium phase diagram, liquidus (solid line), and solidus (dashed line). b (V) SiGe atomic content distribution along the dashed line in b (III). (From Gumennik et al. [47])
Biomedical Application
Fiber technology is frequently utilized in various biomedical applications as chemical, biological, and physical sensors. Fiber-embedded sensors have been designed to monitor physical parameters such as stresses, temperature, pressure, and humidity or chemical parameters such as pH level, oxygen concentrations, and carbon dioxide concentrations [60]. Fiber bundles are beneficial to embed multiple sensors together in a single system and in increasing signal reception levels, resulting in higher signal-to-noise ratios. Lightness, flexibility, and unique optical properties are the main characteristics that lead the demand for fiber sensors in biomedical studies. To meet clinical usage requirements, preforms must be fabricated from biocompatible, non-toxic, and chemically inert materials to prevent immune reaction from the patient. Examples of smart fiber development include a neural fiber probe composed of a polymer and metal core composition that enables flexibility and bending stiffness of the neural probe as it provides in vivo optogenetic stimulation and delivers drugs as an input in order to record feedback electrical and physiological output signals [33]. Another example is a fiber integrating microfluidic principles with complex cross-sectional geometries and meter-long microchannels which analyzes cell separation by dielectrophoresis (DEP). Live and dead cells are separated by inertial and dielectrophoretic forces by sheathless, high-throughput microfluidic cell separator which contains conductive materials in the microchannels [14]. The following strategies show a new array of possibilities where smart fibers can be used in biological interfacing.
Consider an artificial gut that can serve as a bioactivity testing platform at the microscale and at the macroscale. With today’s progress in tissue engineering, a variety of functionalities can be integrated in bioink-coated fibers co-extruded using a bioprinter for tissue fabrication, as shown in Fig. 6(I). Traditionally, bioprinting research aims at creating tissue grafts for regenerative medical practice and does so by carefully designing the hydrogel (Fig. 6(II)) with the appropriate nutrition and signaling molecules for the type of cells required based on the application (Fig. 6(III)). Tissue engineering is very challenging to study as the whole biology of the system completely changes microseconds after the experiment has been launched. Monitoring and regularly tuning a tissue’s maturation remains very complex.
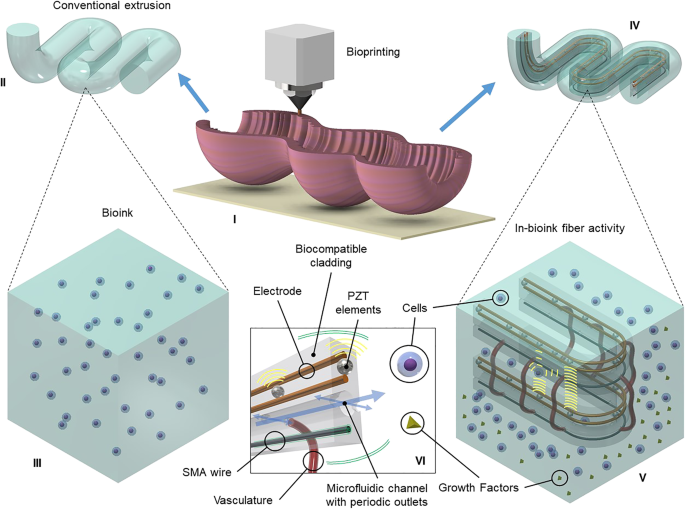
Biological interfacing. (I) Three-dimensional bioprinting of a tissue. (II) Standard microextrusion of bioink. (III) Conventional bioink with cells suspended in hydrogel. (IV) Novel coaxial microextrusion of biointerfacing fiber coated in bioink. (V) Close-up view of fiber where biointerfacing occurs:epithelial cells and vascular epithelial growth factors are excreted from different microchannels and result in cellular self-assembled vasculature between two orifices; piezoelectric elements measure surrounding cell density by ultrasound; and shape memory alloy wires provide peristaltic motion in the tissue. (VI) Visualization of biointerfacing fiber and its components
We propose here a solution by introducing smart fibers in the design (Fig. 6(IV)) to provide a better understanding of the climate and environmental growth. The embedded fiber holds multiple functionalities (Fig. 6(VI)) such as inducing vasculogenesis, ultrasonic imaging, peristaltic movement, and microfluidic flow. Control of the microenvironment takes place via the fiber hooked to syringe pumps and wired to an analytical software. The features of this application (Fig. 6(V)), including pilot experimental data, are detailed in the next subsections.
The Extracellular Matrix and Vasculature
Tissue engineering is widely explored with the increase of artificial tissue needs [61, 62], and the ability to bioprint realistic tissue has an important role to play in tomorrow’s drug and treatment development [63, 64]. One of the biggest challenges is the design of the extracellular matrix (ECM), composed of proteins, growth factors, and other biomolecules, that guide the cell’s contribution to the tissue [65]. Naturally, the ECM gives purpose and structure to the cells, and its extraction typically works by decellularizing tissue and recycling or reusing the ECM for a new cellular construct. The ECM comes in the form of solvents, hydrogels, biopolymers, bioceramics, aerogels, or foams to provide biodegradable or resorbable structure to the tissue [66]. Due to tissue engineering’s high complexity in defining the specifics of the biosystem—mechanical properties, scaffold dissolvability or absorption rates, initial cell types, nutrition, density and ratios, growth factors introduction, and its resulting bioactivity and tissue self-assembly—it is vital to assess the behavior of different types of naturally produced ECM or artificially developed biomaterials in the presence of interacting cells. Moreover, viable tissue requires an organized vascular system that supplies nutrition and oxygen to the tissue for the health and growth of cells. Vascularization provides the natural microfluidic feed of biochemicals to initiate proliferation, specialization, interactions, and motion. The vascular network is formed by vasculogenesis, arteriogenesis, and angiogenesis. Vasculogenesis develops its network through the differentiation and division of endothelial stem cell [67]. Angiogenesis forms new sprouts from existing vessels that are formed in the early embryonic vasculogenesis stage [68].
In-Fiber Microfluidic Feed
Microfluidic conduits with periodic microchannels for content delivery can be used to weave microfluids to specific locations in tissue constructs. The liquefaction front at the boundary of the hot zone defines the droplets’ pinch-off location as described previously. Multiple cores can therefore be broken up in a spatially coherent manner. For example, a silica fiber including a platinum and a silicon core can become a fiber tube with multiple outlets, by inducing the silicon core into an array of spheres and then thinning the fiber using hydrogen fluoride, etching the silicon spheres with potassium hydroxide and etching the platinum core with regal water. An example of the result is shown in Fig. 6(V). The flexibility of fibers allows the microfluidic feed to be integrated in multiple ways in tissue construct. In Fig. 6(IV), the microfluidic channels are used to provide the necessary cell type and growth factors to initiate vascularization and angiogenesis as the tissue reaches maturity.
Biomaterial and Biochemical Testing
In parallel to fiber development, a new testing platform (Fig. 7a (I)) was designed to analyze vascularization and cell-to-cell interactions in the presence of growth factors (Fig. 7a (II)). The platforms were printed in high resolution at an orientation of 30 from biocompatible resin by stereolithography (Formlabs’ Form 2 and Dental LT Clear resin). The print result, shown in Fig. 7a (III), was assembled with two glass capillary tubes with outer diameters of 1.8 mm and 1.0 mm where biological agents are fed. Initial trials will assess diffusion parameters of biochemicals and the growth of cellular colonies in various biocompatible materials. These platforms are designed to be single-use. In 2 h, 24 testing wells can be printed at a relatively low cost. The distance between each capillary outlet of two parallel fibers can be adjusted between 100 and 400 m to investigate the optimum vasculogenesis range that is accepted around 200 m [67]. The medium of interaction in the well’s chamber will first host commercial bioinks (Cellink, USA), one containing sodium alginate and nanofibrillar cellulose and the other containing gelatin methacryloyl, before developing our own in-house biomaterials. The glass capillary tubes shown in Fig. 7a (I) will eventually be replaced by the microfluidic fiber shown in Fig. 6a (V) which will be discussed in the next section.
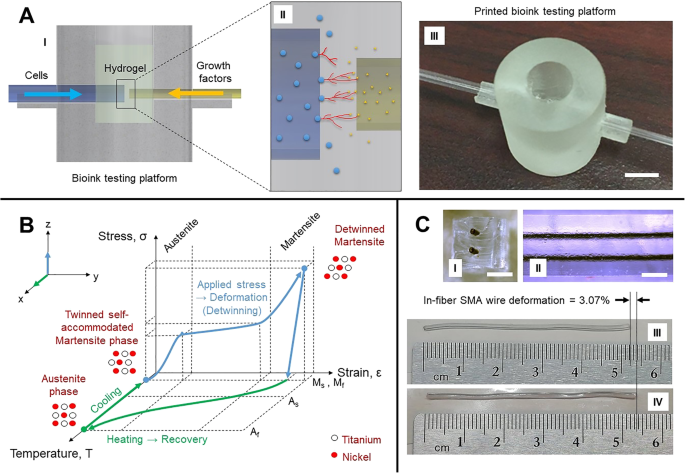
Pilot experiments for biointerfacing:a (I) Cross section of biotesting well showing fluidic feed. a (II) Example of the interaction of epithelial cells (blue circles on the left) with vascular endothelial growth factors (yellow dots on the right) resulting in vasculogenesis excreted by the cells (red lines in the center). a (III) Printed testing platform in biocompatible resin (scale bar = 5 mm). b Temperature-stress-strain graph of the shape memory effect. c (I) Cross section of in-fiber SMA wires (scale bar = 1 mm). c (II) Side view of in-fiber SMA wires (scale bar = 1 mm). c (III) 5.2-mm segment of an in-fiber SMA wire in contraction after being heated at 80 °C. c (IV) 5.36-mm segment of extended in-fiber SMA wire at room temperature
Peristaltic Motion
Shape memory alloy (SMA) wires are lightweight, non-corrosive, and cost-efficient actuating materials for refined applications in a variety of applications such as prosthetic biomimicry [69], self-expandable surgical implants [70], and aerospace engineering [71].
SMAs are metal compounds known for their shape memory effect and pseudoelasticity. Although such properties are typically found in nickel-titanium, these properties can be found in a range of different other metal alloys. Figure 7(b) shows the shape memory effect in terms of temperature, stress, and strain. As shown, at low temperatures, the SMA in its martensite solid state can be deformed by mechanical force, and when thermally induced, goes through a non-diffusive molecular reordering, converting to an austenite solid state. When cooled, the material will return to its initial martensite form, hence the shape memory effect. This thermal cycle is defined by four temperatures, the starting and finishing martensite and austenite temperatures (M s, M f , A s , und A f ), which specifies the start and end of transition periods between states. When the SMA is deformed in as martensite, the molecular de-ordering is defined as detwinning, and it allows the material to experience elongation, which is particularly useful for actuation applications. Essentially, the shape memory effect cycle can occur hundreds of times for an average elongation of 6% and contraction [72], hence its nickname “muscle wire” for its close similarity to muscular myofibrils.
This unique characteristic was first reported by Alden Greninger and Victor Mooradian in 1938 [73], can also be triggered by magnetic field energy [74], namely ferromagnetic shape memory alloys (FSMA), and can be found in polymers (SMP) as well [75]. Today, SMA’s mechanical fatigue and fracture, elasticity, and thermodynamics have been characterized well experimentally [76] and mathematically [77], and its behavior has been modeled [78].
Although the shape memory effect allows for nice contraction behavior of a material, for appropriate robotic applications, the motion needs to be reversable. Typically, an SMA is set in tandem with an opposite mechanism, such as springs, electric drives, elastic bands, or simply another SMA wire. Furthermore, the assembly changes whether it is a linear or rotatory actuation and if the opposing contractions of the actuation are equal. Although wires are thin and weak alone, they can be bundled together to reach the desired force and keep its shape memory effect response time. SMA wires can also be coiled around a capstan to provide greater elongation over shorter distances. Various strategies have been reviewed and chosen for specific applications [79]. The thermal induction is typically best controlled by powering the SMA wire and varying the input current of the order of hundreds of milliamperes. Cooling can be done naturally or by including heat sinks and ventilation.
Fiber drawing technology allows us to play on different material characteristics and to provide to an SMA wire an elastic coating that helps preserve the disorder state of the SMA fiber. As shown in Fig. 7c (I) and c (II), a fiber can be drawn with multiple embedded SMA wires. Styrene-ethylene-butylene-styrene (SEBS) was chosen as the surrounding structure to the SMA wires. SEBS is a copolymer elastomer that can withstand the drawing temperature of 80 °C. While preliminary results show that the actuation can work but with lower efficiency than bare SMA wires, the back-and-forth motion through heating (Fig. 7c (III)) and cooling (Fig. 7c (IV)) cycles is observed for a deformation of approximately 3.07%. More research is required to optimize the setup, but this early stage of experimentation in-fiber SMA actuation shows promising outlooks. The wires were physically pulled and heated using a hot plate to prove the concept. Heating by current would allow speeding up the shape memory effect and controlling better the heat’s diffusion through the fiber. The 5.35-mm wire was measured to have a diameter of 0.11 mm and a resistance of 18.2 was recorded across the fiber segment. To provide a frame of reference, according to SMA wire manufacturers (Dynalloy, Inc.), a 0.1-mm-thick wire made of nickel and titanium requires approximately 200 mA of current for a 1 s contraction. Controlling each wire individually would allow for directional movement, and adding more SMA wires to the design would allow multi-directional motion and greater contraction strength. Moreover, if ferromagnetic SMA wires were used, the control of the motion could become locally controllable via tuning of the interacting magnetic field. Additionally, the FAMES Lab’s drawing tower having the ability to rotate a preform as it is drawing into a fiber enables the possibility to manufacture spring-like structures of SMA wires in the fiber which allows for greater deformation, similar to commercially available SMA springs. Clearly, varieties of strategies are enabled with in-fiber SMA wires.
Biosensing
Biosensors are developed in a wide variety of ways. They can be designed label-based or label-free to detect specific expressions from biological elements such as cells, bacteria, hormones, proteins, DNA, and more [80, 81], from sampling blood, urine, saliva, sweat, or tears. Psychophysiological conditions can be observed from real-time biofeedback such as blood pressure, electrodermal activity, skin conductance, respiration and heart rates, and more [82, 83]. Bioimaging has been done by optical imaging, ultrasound, magnetic resonance frequency, computed tomography, near-infrared spectroscopy, quantum dot probing, and by many more techniques [84].
In optical fiber research, previous biosensing fibers have been fabricated relying on silicon photonic crystal detection of biological radiation [85]. Photonic crystal technology has been used before to monitor in label-free real-time cellular morphology and survival [86]. Such progress in biophotonics has led to hollow-core microstructured fibers visible under magnetic resonance imaging (MRI) [87]. The hollow core allows the propagation of the optical radiations along the fiber over very long distances. The geometry of the hollow fibers varies to tune the photonic bandgaps and dispersion of different detected wavelengths. The inner walls of these hollow tubes are coated with oppositely charged polyelectrolytes and magnetite nanoparticles which are used as contrast agents for MRI. Such design therefore enables new biomedical precision diagnosis opportunities, for example, in the observations of neural activity in vivo [87, 88].
Ultrasonography technology enables us to observe density of cells in liquid or gel in a non-intrusive manner [89, 90]. Ultrasonic probes typically function according to the piezoelectric effect (generation of electricity from applied stress), which was first discovered by Jacques and Pierre Curie in 1880 [91]. The inverse piezoelectric effect (deformation of a piezoelectric crystal from an applied electric field) was induced mathematically by Gabriel Lippmann in 1881 [92] and later in 1916, Chilowsky Constantin and Paul Langevin developed ultrasonic submarine detection for World War I military applications [93]. Thereon, sonar applications have been diverse, such as underwater imaging and fish-finding [94, 95] and energy harvesting [96, 97].
The piezoelectric elements convert electrical energy to and from mechanical energy and transmit sound waves between each other. All frequency and bandwidth parameters require precise regulation, and good energy transmission requires good acoustic and damping matching impedances. Two fibers with integrated piezoelectric elements, designed as pulsing emitter and receiver, can create an ultrasonic waveguide between each other to measure density over the wave’s trajectory. This fiber enables us to sense the microstructures of the environment as the tissue reaches maturation. The piezoelectric elements are created by capillary breakup from a PZT core for example. PZT elements have an acoustic impedance of 33.7 × 10 6 kg/m 2 s with a resonance frequency below 25 MHz. The produced spheres are lined with conductive electrodes to a transducer. This setup provides the feedback in a control system to better adjust microfluidic and motion feed. The in-fiber ultrasonic imaging of the microenvironment clearly helps understand how the tissue environment behaves over time.
Schlussfolgerungen
We have formulated the concept of VLSI for fibers (VLSI-Fi)—a combination of liquid-phase processing techniques in microelectronic materials forming a toolbox for fabrication of high-performance devices and systems in fibers and textiles. Our experimental work focuses on a set of demonstrations substantiating our control over narrower aspects of VLSI-Fi, such as preform 3D printing, in-fiber circuit assembly by material-selective spatially coherent capillary instability, and segregation-driven doping control at the level of an individual fiber-embedded device. We envision that VLSI-Fi will enable realization of product in multiple technological areas, one of which is fabrication of active biomimetic scaffolds for engineered tissues with realistic microstructures.
Verfügbarkeit von Daten und Materialien
Nicht zutreffend.
Abkürzungen
- BJT:
-
Bipolar junction transistor
- CAD:
-
Computer-aided design
- CMOS:
-
Komplementärer Metalloxid-Halbleiter
- DEP:
-
Dielectrophoresis
- ECM:
-
Extracellular matrix
- EDS:
-
Energiedispersive Röntgenspektroskopie
- FAMES Lab:
-
Fibers and Additive Manufacturing Enabled Systems Laboratory
- FOS:
-
Fiber optic sensors
- FSMA:
-
Ferromagnetic shape memory alloys
- HPCVD:
-
High-pressure chemical vapor deposition
- IoT:
-
Internet of Things
- MOF:
-
Microstructured optical fibers
- MOSFET:
-
Metal-oxide-semiconductor field-effect transistor
- MRT:
-
Magnetresonanztomographie
- PCF:
-
Photonic crystal fiber
- PZT:
-
Lead zirconate titanate
- SEBS:
-
Styrene-ethylene-butylene-styrene
- SLA:
-
Stereolithography
- SMA:
-
Shape memory alloy
- SMP:
-
Shape memory polymers
- TPC:
-
Trans-Pacific undersea cable
- UV:
-
Ultraviolett
- VLSI:
-
Very large-scale integration
- VLSI-Fi:
-
Very large-scale integration for fibers
Nanomaterialien
- Optimierung der digitalen Transformation in der CPG-Herstellung
- GE eröffnet Smart Plant in Alabama
- Der digitale Faden in der intelligenten Fertigung wird erwachsen
- Herausforderungen der datengesteuerten Fertigung
- Was ist digitale Transformation in der Fertigung?
- Nutzung digitaler Technologie in der Fertigung
- Die digitale Fabrik:Smart Manufacturing treibt Industrie 4.0 voran
- GE Digital:Transformation der Fertigung mit Smart MES
- Autodesk Intelligente Fertigung
- Digitale Fertigung:Die Industrie von morgen