3D-gedruckte Verbundwerkstoffe mit 60 % Fasern, weniger als 1 % Hohlräume
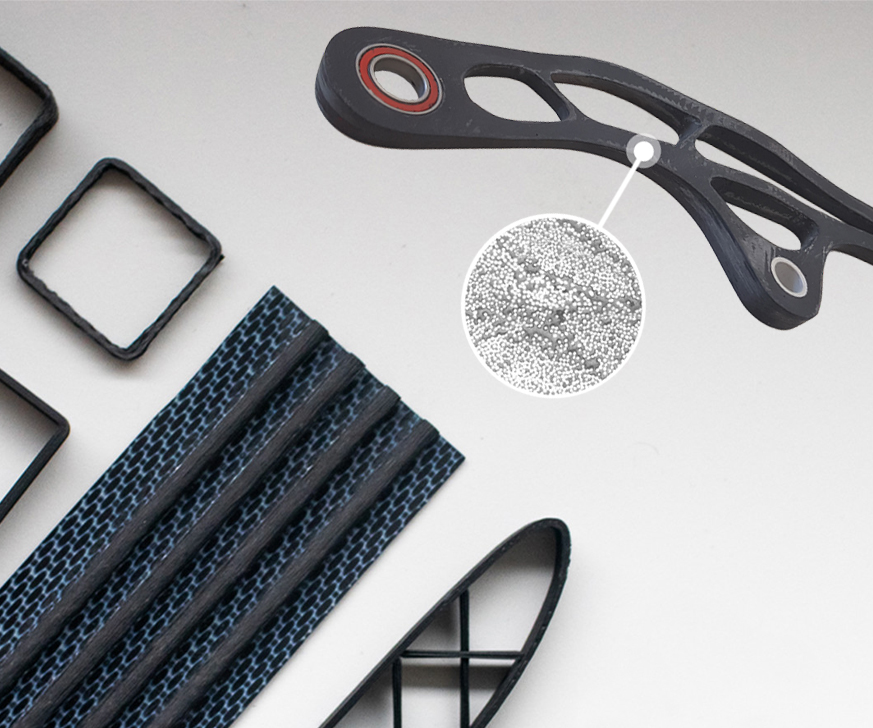
„Unser Hauptziel ist die Herstellung von strukturellen Endlosfaserverbundwerkstoffen für die Industrie“, sagt Giovanni Cavolina, Mitbegründer von 9T Labs (Zürich, Schweiz). „Wenn man mit Leuten spricht, die CFK-Teile (kohlenstofffaserverstärktes Polymer) herstellen, glauben die meisten nicht, dass es möglich ist, mit Endlosfaser-3D-Druck einen extrem niedrigen Hohlraumgehalt oder eine gute interlaminare Scherfestigkeit (ILSS) zwischen Schichten zu erreichen.“ 9T Labs hat jedoch einen patentierten Nachbearbeitungsprozess entwickelt, der Hohlräume eliminiert. „Wir können jetzt Endlosfaserverbundwerkstoffe mit hervorragender Haftung zwischen den Schichten und einem Hohlraumgehalt von unter 1 Prozent in 3D drucken, was mit herkömmlich hergestellten Verbundwerkstoffen konkurriert.“
Anfang an der ETH Zürich
9T Labs startete mit einem Forschungsprojekt im Laboratory of Composite Materials and Adaptive Structures (CMAS) der Eidgenössischen Technischen Hochschule Zürich (ETH Zürich). Cavolina und 9T Labs Mitbegründer Martin Eichenhofer und Chester Houwink hatte einen Druckkopf aus Verbundwerkstoffen entwickelt, „den wir auf einem Roboterarm montierten und Gitterkerne für ultraleichte Sandwichstrukturen für Luft- und Raumfahrtanwendungen herstellten“, erklärt Cavolina.
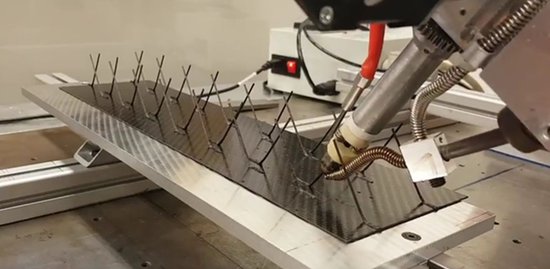
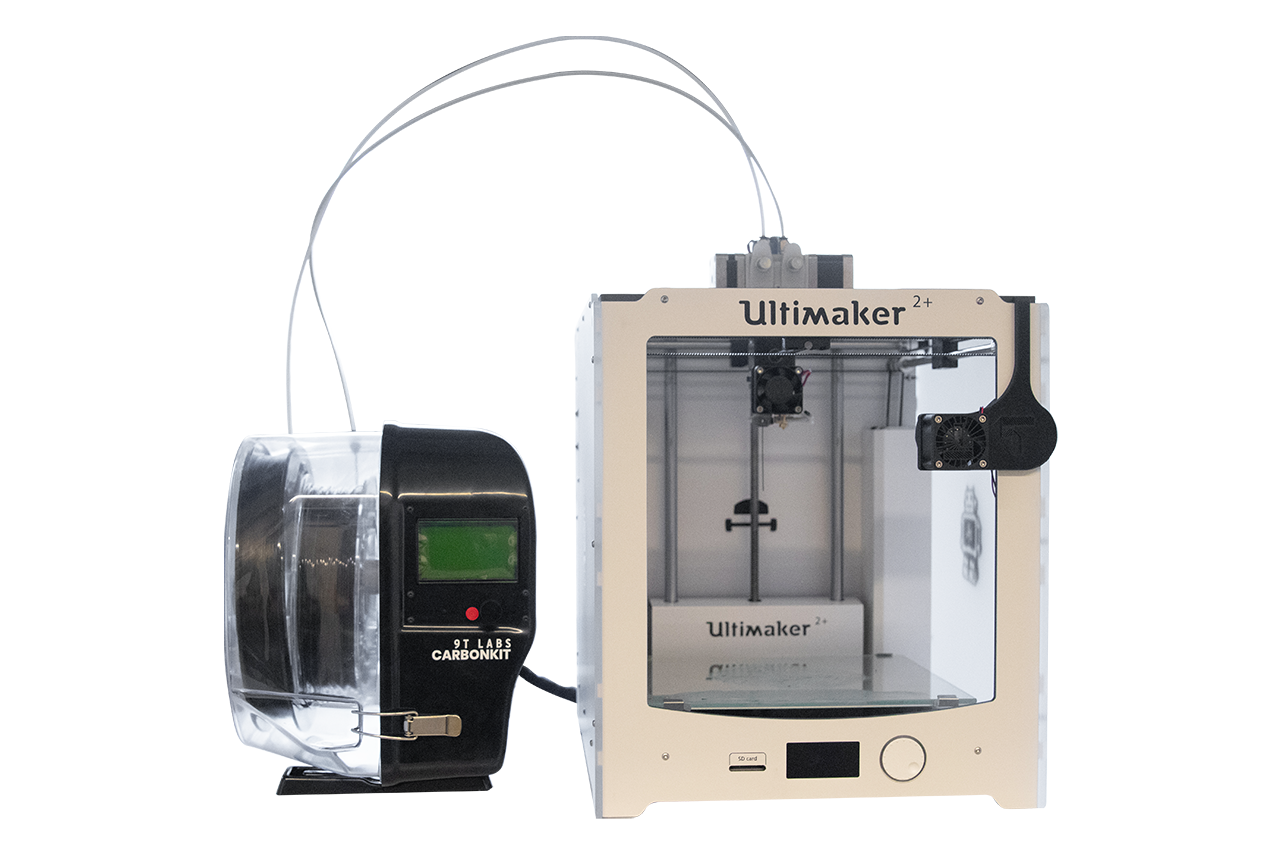
CarbonKit war ein Produkt mit begrenzter Freigabe, das es Standard-FDM-Druckern ermöglichte, Endlos-Carbonfasern zu verwenden, aber noch nicht die richtige Lösung für die Herstellung kostengünstiger CFK-Strukturteile für die Industrie war. QUELLE | 9T Labs.
CarbonKit
So wurde Anfang 2018 9T Labs gegründet, um das Konzept des 3D-Drucks monolithischer CFK-Laminate zu beweisen, das potenzielle Kundenanforderungen erfüllen könnte. „Unser nächster Schritt war das CarbonKit“, sagt Cavolina. Dies ist das Produkt, das in CW . vorgestellt wird 's Artikel vom März 2019 „Einführung des Endlosfaser-3D-Drucks in die Produktion“. Das CarbonKit verwandelt Ultimaker oder Prusa 3D-Drucker in ein System, das mit Endlos-Kohlefasern drucken kann. „Sie können Ihre vorhandenen Drucker in Kombination mit unserem Druckkopf, Filamenten und Software verwenden, um Endlosfasern je nach Lastfall mit 50 Prozent Kohlefaservolumenanteil zu platzieren – nicht 30 Prozent, wie es beim CFK-3D-Druck üblich war “, fügt er hinzu.
Cavolina erklärt, dass, obwohl das Interesse an diesem Produkt recht groß war, „wir nur 25 Kunden belieferten. Wir haben dieses Produkt limitiert, weil wir erkannt haben, dass es mit nur einem einstufigen FDM-Prozess (Fused Deposition Modeling) nicht möglich ist, strukturelle Endverbrauchsteile für industrielle Luft- und Raumfahrtanwendungen zu erzielen, die auch mit aktuellen Technologien wettbewerbsfähig sind.“
Durch das CarbonKit hat 9T Labs jedoch wertvolle Kundenbeziehungen aufgebaut. „Wir konnten lernen, was Unternehmen erwartet und brauchen, obwohl diese Teile mit dem CarbonKit eigentlich nicht herstellbar waren“, erklärt er. „In-situ-Konsolidierung ist mit FDM zwar möglich, aber dafür wären viel komplexere Maschinen erforderlich, die nicht teuer sind. Also haben wir einen 2-Stufen-Prozess mit einer Post-Print-Konsolidierung erstellt.“
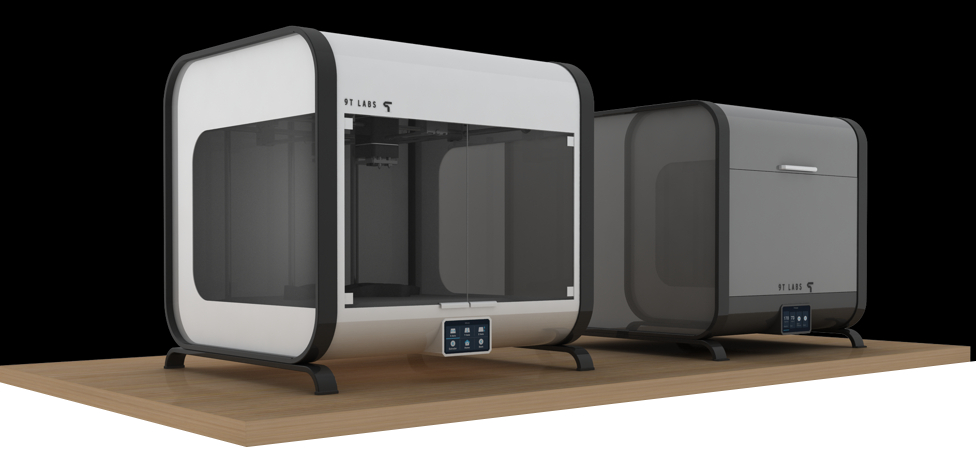
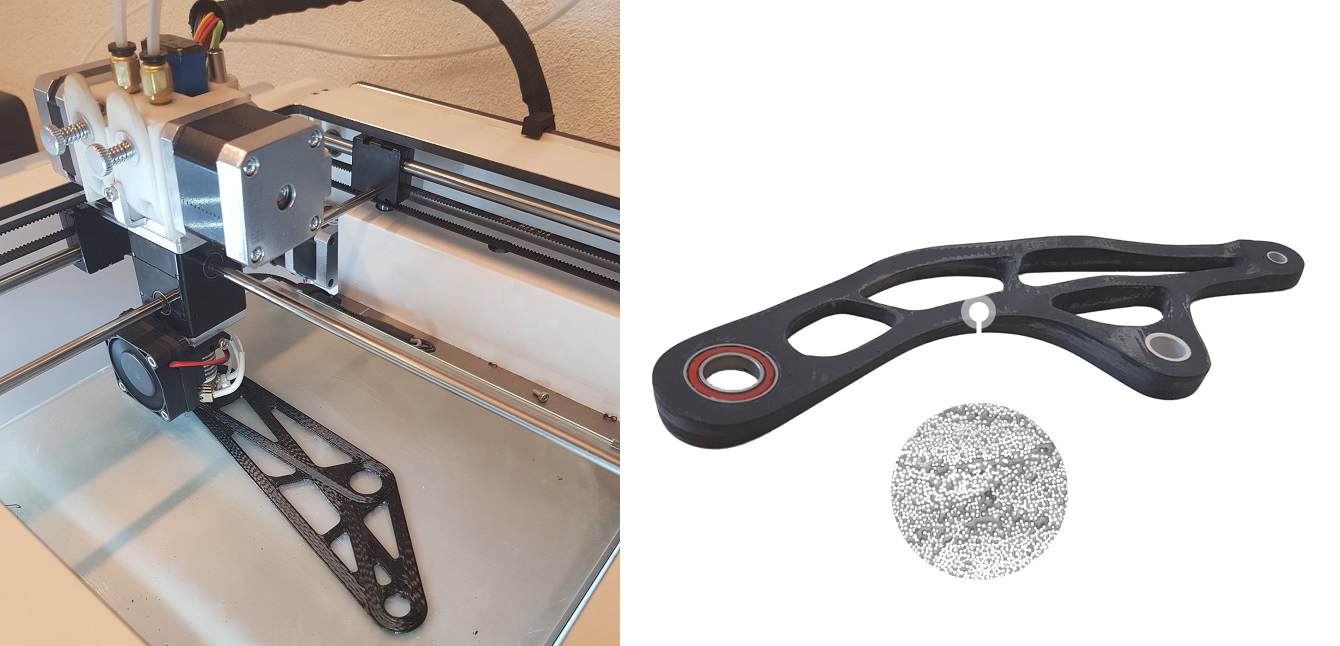
Mit der Red Series hat 9T Labs 3D-gedruckte CFK-Strukturen mit>50 % Faservolumen und <1 % Hohlräumen zu einem erschwinglichen Preis im Vergleich zu aktuellen Herstellungsverfahren für Verbundwerkstoffe erreicht. QUELLE | 9T Labs.
Rote Serie, zweistufiger Prozess
Das bringt uns dahin, wo 9T Labs heute ist. „Wir vermarkten die Red Series, die aus zwei Einheiten besteht:einer klassischen FDM-Druckeinheit mit patentiertem Druckkopf und einer angrenzenden Fusion Unit für die Nachbearbeitung“, erklärt Cavolina. „Wir erreichen keine vollständige in-situ-Konsolidierung während des Druckens, sondern drucken und konsolidieren dann in einem zweiten Prozess. Im Wesentlichen drucken wir einen Vorformling, der in der Fusionseinheit zur Nachverfestigung mit hoher Temperatur und hohem Druck platziert wird, um einen Faservolumengehalt von mehr als 50 Prozent mit weniger als 1 Prozent Hohlräumen zu erreichen. Dieser zweistufige Prozess erreicht Luft- und Raumfahrtqualität zu einem erschwinglichen Preis.“
Die Red Series verwendet vorerst thermoplastische Materialien. „Wir bedrucken Kohlefaser mit PEI, PEKK, PA (Nylon) und haben auch Erfahrung mit PP“, sagt Cavolina. Ist die Red Series ein offenes Materialsystem? „Der einzige Weg, um wettbewerbsfähig zu sein, besteht darin, vorhandene Materialien mit einem neuen Herstellungsverfahren zu verwenden“, erklärt er. „Wenn man von Grund auf sein eigenes Material entwickelt, schließt man eine Serienfertigung aus. Aus Gründen der Lieferkettensicherheit und Zuverlässigkeit verlassen sich Serienhersteller bei ihren Materialien nicht auf ein kleines Unternehmen. Daher lassen wir unsere Kunden ihre vorhandene Materialversorgung nutzen, indem wir sicherstellen, dass die Materialien in unserem System funktionieren.“ Er erklärt, dass 9T Labs die Materialien testet, um sicherzustellen, dass der Rohstoff bestimmte Anforderungen erfüllt und die besten Parameter für den Druck bestimmt.
Was ist mit offener Software? „Unsere Drucksoftware wird mit einer Struktursimulationssoftware kombiniert“, sagt Cavolina. „Als Ingenieur ist es großartig, Fasern dort zu platzieren, wo sie benötigt werden, aber wie können Sie sicher sein, dass sie dort tatsächlich platziert werden sollten? Unsere Software bietet die Freiheit zu entwerfen und dann mit einer strukturellen Simulation zu überprüfen. Die andere Richtung besteht darin, in einer Struktursimulation ein faserorientiertes Layup zu definieren und dann in unserer Software in einen Druckpfad umzuwandeln. Für die im Hintergrund laufende FEA nutzen wir einen bestehenden, bewährten und bekannten Partner. Sie können ein Teil auch direkt in CAD konstruieren und diese Datei dann in unser Programm hochladen. Dort entscheiden Sie, wo Sie die Kohlefaser haben möchten und wo reines Polymer ausreicht.“
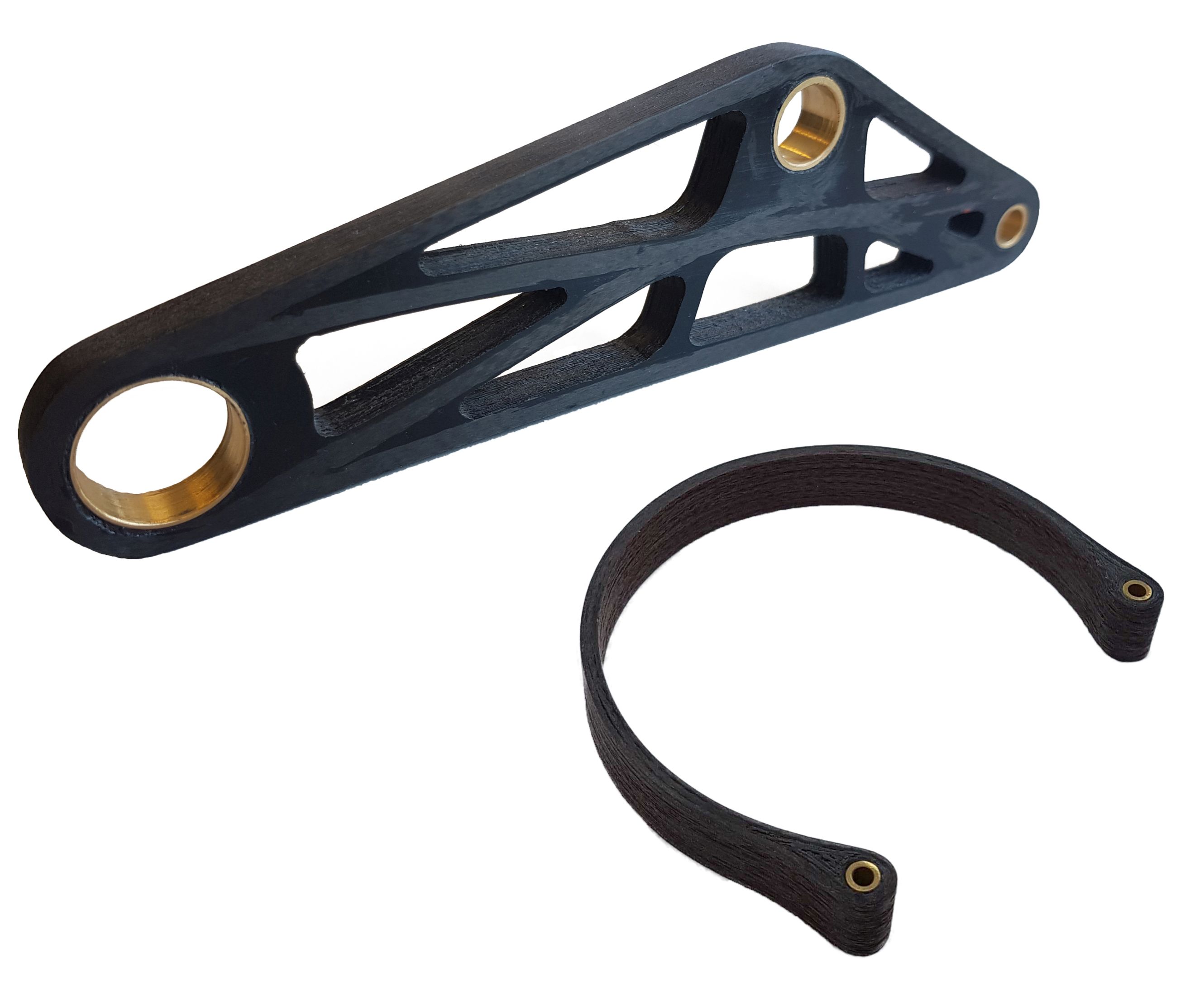
Dieser CFK-Halter und Kipphebel für Anwendungen außerhalb der Luft- und Raumfahrt erfüllt tatsächlich die Anforderungen an Laminate in der Luft- und Raumfahrt und verfügt über mehr als 40 Lagen – jede Lage mit einer anderen Faserorientierung, um Anisotropie auszunutzen und Strukturteile zu optimieren, die bisher nicht möglich waren. QUELLE | 9T Labs.
Anwendungen
9T Labs verfolgt Luft- und Raumfahrt (vorerst Interieur), biomedizinische und industrielle Automatisierung (z. B. Verpackungsmaschinen) sowie Freizeit/Luxus (z. B. Motorsport, Sportschuhe, Brillen). Dieser letzte Markt, sagt Cavolina, „ist dort, wo Strukturverbundwerkstoffe benötigt werden, aber die Anforderungen sind nicht so streng wie in der Luft- und Raumfahrt.“ Er zitiert den oben gezeigten Kipphebel. „Dies ist eine Halterung für eine Nicht-Luftfahrt-Struktur, die eine strukturelle Anwendung darstellt, die Sie mit unserer Technologie optimiert herstellen können“, erklärt er. „Es stammt aus einem Aluminiumteil, das topologieoptimiert wurde, um Gewicht zu sparen, indem die Carbonfasern entsprechend dem Lastfall ausgerichtet werden. Sie können Kosten sparen, da Sie die Menge der verwendeten Kohlefasern im Vergleich zu anderen Verbundwerkstoffverfahren reduzieren können. Auf andere Weise ist es nicht möglich, weil es mit anderen Methoden nicht möglich ist, jede Faser in hoher Auflösung so auszurichten, wie Sie es benötigen.“
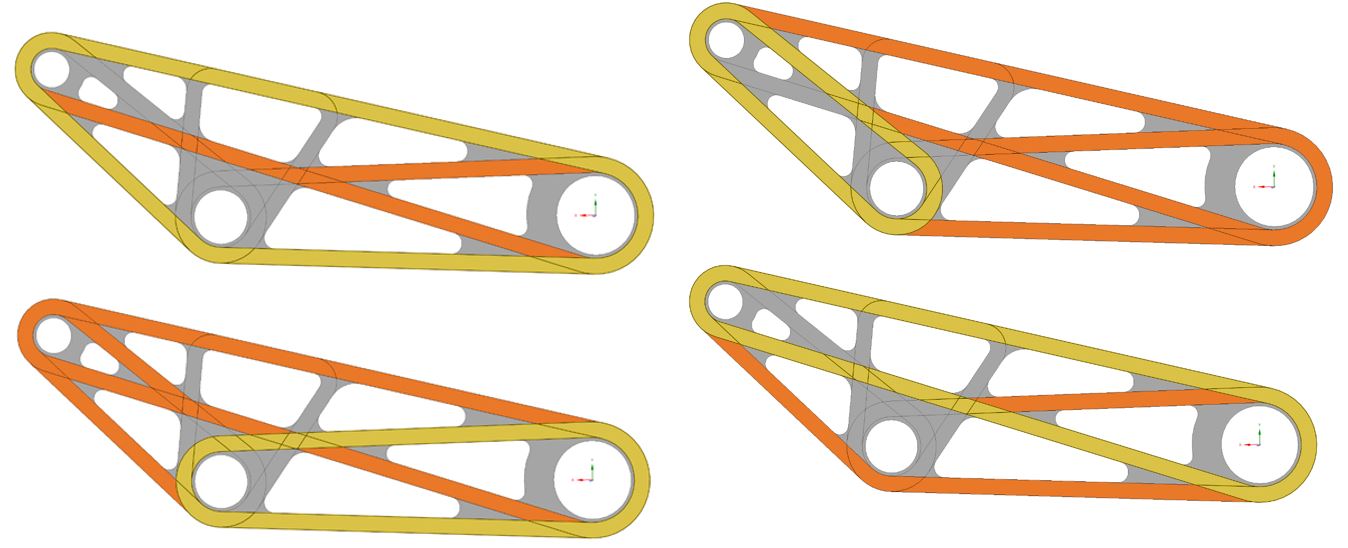
Vier verschiedene kontinuierliche Kohlefaser-Layups wechseln sich über die gesamte Dicke der mit 9T Labs Red Series bedruckten CFK-Halterung ab. QUELLE | 9T Labs.
Cavolina merkt an, dass dieser Kipphebel mehr als 40 Schichten aus Fasern und Polymer umfasst, „und wir können in jeder Schicht eine andere Faserorientierung haben. Wir haben vier verschiedene Layups ausprobiert, die nicht auf quasi-isotrop beschränkt sind. Diese Freiheit ermöglicht es uns, die Anisotropie von Verbundwerkstoffen auszunutzen, um die Endanwendungsstruktur weiter zu optimieren. Dies wäre mit anderen aktuellen Herstellungsverfahren nicht möglich.“
Er weist auch darauf hin, dass der 3D-Druck von CFK im Vergleich zum Handlaminieren ein automatisierter Prozess ist. „Unsere Technologie reduziert die manuelle Arbeit durch automatisiertes Layup drastisch“, sagt Cavolina. „Mit unserer Technologie drucken Sie einfach, konsolidieren und fertig.“
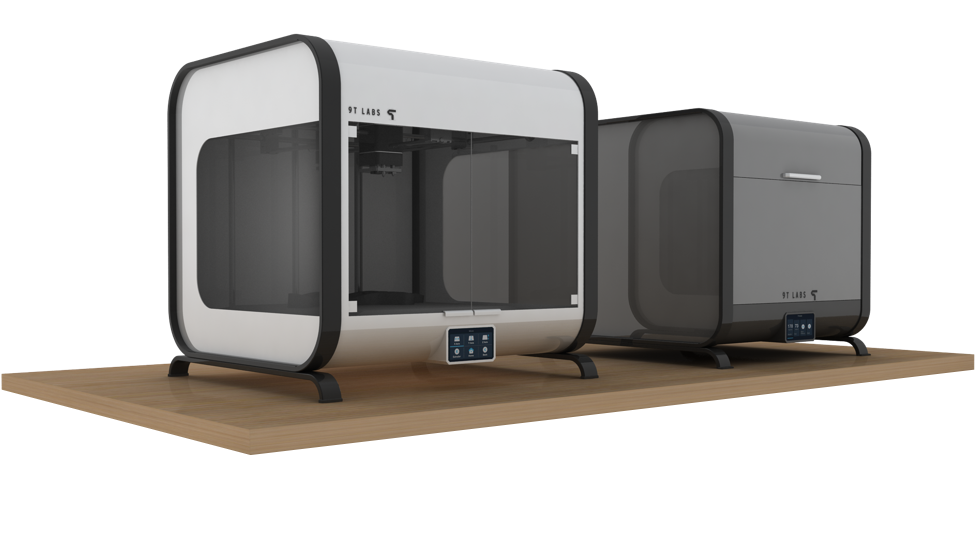
Die Red Series druckt kleinere, komplexe, monolithische CFK-Preforms, die in einem zweiten Schritt für eine skalierbare industrielle Serienfertigung konsolidiert werden. QUELLE | 9T Labs.
Druckgröße, Geschwindigkeit und vollständige Einführung der Roten Serie
Die Red Series richtet sich an kleinere, monolithische Teile für die Serienfertigung innerhalb eines Druckbereichs von 350 Millimeter mal 300 Millimeter. „hier sehen wir derzeit den höchsten Mehrwert für unsere Kunden“, erklärt Cavolina.
Wie sieht es mit der Druckgeschwindigkeit aus? „Wir sprechen ganz konkret davon, in den nächsten 1-2 Jahren 4.000 bis 8.000 Teile pro Jahr für verschiedene Kunden zu produzieren, was mit den Twin-Einheiten der Red Series erreicht wird“, sagt Cavolina. „Da wir die Produktion komplexer, detaillierter Preforms von der Konsolidierung entkoppelt haben, ist es jetzt möglich, das Produktionsvolumen schnell hochzufahren.“
„Wir haben viel Zeit damit verbracht, die Kostenstruktur unseres Prozesses zu analysieren, einschließlich der Ausrüstungs-, Arbeits- und Materialkosten“, antwortet er. „Wir haben eine erschwingliche Kostenstruktur für die Ausrüstung und haben den Preforming-Prozess automatisiert. Wir verwenden die günstigsten und effizientesten Materialien und reduzieren dann den Materialbedarf, indem wir die Fasern je nach Lastfall ausrichten und eine Strukturoptimierung anwenden. Wir arbeiten eng mit unseren Partnern in der Struktur- und Prozesssimulation zusammen und sehen, dass es als großer Teil des Produktionsziels, die digitale Zwillingstechnologie zu verwenden, um Plug-and-Play mit 4.0-Produktionslinien und -zellen zu ermöglichen, weiter wachsen wird.“
Die Red Series wird 2020 auf den Markt kommen. „Jetzt evaluieren wir sie durch unsere Kooperationsprogramme mit Produktionspartnern. Wir zertifizieren die Teile und Prozesse mit ihnen, damit sie die ersten Plätze für Red Series-Maschinen reserviert haben und diese zur Herstellung ihrer Endprodukte verwenden.“
Harz
- Verstärkung von 3D-gedruckten Teilen mit effizienter Faserführung:Teil 1
- Ein Teil der Woche – 3D-gedrucktes Stativ mit durchgehend kohlefaserverstärkten Beinen
- Recycling:Endlosfaserverstärkte thermoplastische Verbundwerkstoffe mit recyceltem Polycarbonat
- Kurze Kohlefaser-Compounds erweitern die Reichweite thermoplastischer Verbundwerkstoffe
- TxV Aero Composites erfüllt die AS9100-Standards
- Hexcel arbeitet mit Lavoisier Composites, Arkema zusammen
- Verbundstoffrecycling – keine Ausreden mehr
- Covestro bringt Maezio Endlosfaser-Thermoplaste auf den Markt
- Kontinuierliche Faserherstellung (CFM) mit Moi-Verbundwerkstoffen
- 3D-Druckverbundwerkstoffe mit Endlosfasern