Die Grundlagen des Design for Assembly (DFA)
Die Begriffe „Design for Manufacturing and Assembly“ (DFMA) und „Design for Assembly“ (DFA) beziehen sich auf eine Reihe von Praktiken und Prinzipien, die darauf abzielen, die Konzept- und Designphasen der Produktentwicklung an die gegebene Fertigungsmethode und in eine solche anzupassen Weg, der eine einfache und kostengünstige Produktion und Montage gewährleistet.
DFA-Frameworks haben im Laufe der Jahrzehnte eine Reihe verschiedener Formen angenommen, beginnend ernsthaft in den 1970er Jahren. Eine bahnbrechende Entwicklung war Hitachis Assembly Evaluation Method (AEM), die einen Punktverluststandard verwendete, um die Leichtigkeit der Montage für ein bestimmtes Produkt (insbesondere für die automatische Montage) zu bewerten. Das Konzept des „Design for Assembly“, wie wir es heute kennen, wurde 1977 geprägt und legte Kriterien und Strategien fest, um zu bestimmen, ob ein bestimmtes Produkt ein geeigneter Kandidat für die automatisierte Montage ist, sowie das ideale Montagesystem und den Automatisierungsgrad.
Das Entwerfen eines Teils für die Montage kann mit der Verbesserung seiner Funktionalität, Qualität und Konsistenz einhergehen. Darüber hinaus kann die Einhaltung der Design-for-Assembly-Prinzipien dazu beitragen, die erforderliche Produktionsausrüstung und den Teilebestand zu reduzieren (in vielen Fällen werden diese sekundären Vorteile tatsächlich zu einem bedeutenderen Verkaufsargument als die reduzierten Montagekosten). Die Befolgung der DFA-Richtlinien kann auch dazu beitragen, potenzielle Designprobleme früh im Produktzyklus aufzuzeigen – was dazu beitragen kann, den Prototyping-Prozess zu rationalisieren und die Produktionskosten weiter zu senken.
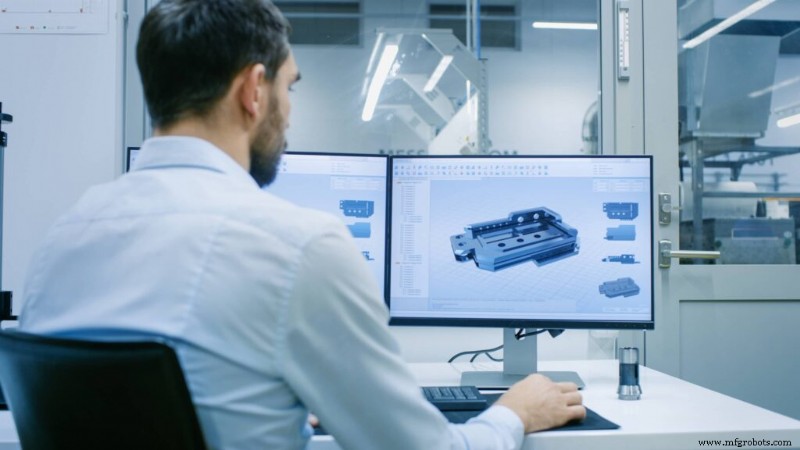
Hier ist eine kurze Einführung, wie Sie mit der Integration der DFA-Prinzipien in Ihre Produktentwicklungsprozesse beginnen können:
Teileanzahl minimieren
Die wichtigste Regel von DFA? Kombinieren Sie Teile wann immer möglich, solange dies die Lebensfähigkeit des Teils nicht beeinträchtigt. Weniger Teile können zu einer schnelleren Endmontage führen.
Das Minimieren der Teileanzahl ist jedoch nicht dasselbe wie das Entfernen von Merkmalen aus dem Teil. Ganz im Gegenteil – diese Vorgehensweise kann hilfreich sein, um die Anzahl der benötigten Befestigungselemente zu reduzieren und unnötige Arbeitskosten zu vermeiden.
Bauen Sie Verbindungselemente in die Teilekonstruktion ein
Eine spezielle Möglichkeit, die Anzahl der Teile zu reduzieren, besteht darin, Befestigungselemente direkt in das Teil selbst einzubauen (anstatt Schrauben, Bolzen oder andere zusätzliche Komponenten zu benötigen). Schnappverschlüsse und bewegliche Scharniere sind zwei gängige Konstruktionen für Montagevorlagen für Befestigungselemente, für deren Konstruktion keine zusätzlichen Werkzeuge oder Spezialgeräte erforderlich sind. Schrauben und Befestigungselemente können für bestimmte Teile und Anwendungen eine Notwendigkeit sein, aber im Allgemeinen sollten sie nach Möglichkeit eliminiert werden.
Achten Sie auf Symmetrie
Eine allgemeine Richtlinie in Bezug auf Symmetrie und Montage:Teile sollten entweder symmetrisch sein, damit sie während des Montageprozesses leicht ausgerichtet werden können, oder sie sollten sichtbar asymmetrisch sein, damit sie leicht ausgewählt und ausgerichtet werden können.
Vermeiden Sie die Konstruktion links- oder rechtsgängiger Teile (da dies Ihren Werkzeugbedarf im Wesentlichen verdoppeln könnte), selbst wenn dies zu veralteten oder unnötigen Merkmalen führt, die die Funktion des Teils ansonsten nicht beeinträchtigen.
Machen Sie es unmöglich, Teile falsch zu installieren
Das Einschließen von selbstausrichtenden Merkmalen zwischen den Teilen, die verhindern, dass verschiedene Komponenten falsch angebracht werden, ist eine weitere Möglichkeit, die Effizienz des Montageprozesses zu steigern.
Befestigungselemente sind dafür bekannt, dass sie erhebliche Montagearbeit erfordern. Daher ist es entscheidend, dass die Ausrichtung jedes Teils leicht zu bestimmen ist, um die Montage schnell und kostengünstig zu halten. Sogar etwas so Einfaches wie eine Kerbe an einem runden Teil kann viel dazu beitragen, den Prozess zu rationalisieren.
Optimieren Sie Ihre Toleranzen
Moderne Bearbeitungs- und Werkzeugmaschinen sind in der Lage, unglaublich enge Toleranzen zu erreichen. Allerdings wird nicht jedes Produkt von solch strengen Standards profitieren – die Kosten für die Bearbeitung von Teilen und Werkzeugen mit solch präzisen Toleranzen können schnell unglaublich teuer und zeitaufwändig werden und jeden Kosten- oder Effizienzvorteil zunichte machen.
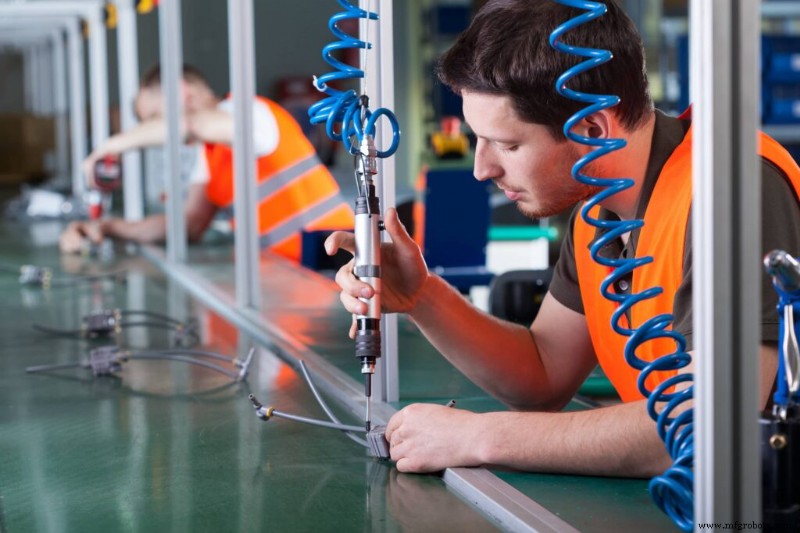
Baugruppen mit mehreren Teilen, die mit extrem engen Toleranzen bearbeitet werden, erhöhen auch das Risiko von Leistungsproblemen, wenn eine oder mehrere der Komponenten nicht den Spezifikationen entsprechen. Wenn Sie Ihre Toleranzen ein wenig lockern, können Sie oft Kosten senken und gleichzeitig die Widerstandsfähigkeit Ihrer Designs verbessern.
Design mit COTS-Teilen
Kommerzielle Standardteile (COTS) sind, wie der Name schon sagt, Teile, die Sie von einem Lieferanten kaufen können, anstatt sie selbst herzustellen. Übliche COTS-Teile umfassen Komponenten wie Gehäuse, Federn, Zahnräder, Stifte, Sensoren und mehr. Diese Teile sind ziemlich standardisiert, und die meisten Montagearbeiter und automatisierten Montagelösungen verstehen, was zu ihrer Verwendung und Montage erforderlich ist.
Indem Sie Ihre kundenspezifischen Bearbeitungs- und Fertigungsanforderungen auf ein Minimum beschränken, können Sie den Designprozess rationalisieren und gleichzeitig Hindernisse für die Beschaffung angemessener Lagerbestände und Rohstoffe oder Komponenten verringern. Dieser Vorteil ist besonders wertvoll für Teile, die in Zukunft einen Nachfrageschub erfahren könnten.
Verwenden Sie die gleichen Tools für alle Assemblys
Die Verwendung eines einzigen Werkzeugs für die gesamte Montage – oder noch besser, die gesamte Produktlinie – kann die Energie-, Arbeits- und Kosteneffizienz sowohl bei der Montage als auch bei der Demontage verbessern.
Wenn eine Baugruppe in verschiedenen Abschnitten unterschiedliche Schrauben- oder Befestigungstypen verwendet, erfordert jeder zusätzliche Befestigungstyp während des Montagevorgangs ein zusätzliches Werkzeug. Mischen Sie keine Innensechskantköpfe mit Sechskantköpfen, wenn der eine oder andere ausreicht.
Entdecken Sie den todsicheren Weg, um sicherzustellen, dass Ihre Teile den DFA-Richtlinien entsprechen
Die effektive Anwendung von Konstruktionsprinzipien für Fertigung und Montage ist in der heutigen On-Demand-Welt von entscheidender Bedeutung. Um jedoch die Vorteile der DFMA-Richtlinien in vollem Umfang nutzen zu können, müssen häufig viele Faktoren berücksichtigt werden – darunter die Auswahl und Verwendung von Designsoftware, die technischen Anforderungen einer Anwendung, Umweltaspekte, Materialauswahl und -beschaffung, Budgetbeschränkungen, enge Zeitvorgaben und mehr.
Die Partnerschaft mit einem On-Demand-Hersteller mit umfassendem Design- und Engineering-Know-how ist der Schlüssel, um auf dem heutigen wettbewerbsintensiven Markt voranzukommen. Hier kommt Fast Radius ins Spiel. Wir sind stolz darauf, neue Dinge möglich zu machen und die neuesten und besten Technologien zu nutzen, um bewährte Legacy-Komponenten mit verbesserter Effizienz neu zu gestalten. Wir bieten auch eine Reihe von Produktberatungsdiensten an, um Sie bei der Entwicklung und Vorbereitung Ihrer Teile für die Produktion zu unterstützen. Kontaktieren Sie uns noch heute, um mehr zu erfahren.
Industrietechnik
- Wie bereite ich meine Leiterplatte für die Fertigung vor? Beschleunigung der Leiterplattenbestückung mit Design Best Practices
- Die Bedeutung des Designs für die Fertigung
- Design for Manufacturability-Richtlinien – Teil 2
- Zurück zu den Grundlagen:Der ultimative CMMS-Leitfaden, Teil 1
- Zurück zu den Grundlagen:Der ultimative CMMS-Leitfaden, Teil 4
- Zurück zu den Grundlagen:Der ultimative CMMS-Leitfaden, Teil 3
- Ultiboard – Der ultimative Leitfaden für das Beste für Anfänger
- Wichtige Überlegungen zur Leiterplattenbestückung
- Wichtige Designrichtlinien für die Herstellung und Bestückung von Leiterplatten – Teil I
- Wichtige Designrichtlinien für die Herstellung und Bestückung von Leiterplatten – Teil II