Kenntnis und Auswahl gängiger Werkzeuge in der CNC-Bearbeitung
Obwohl die CNC-Bearbeitung immer noch zur Kategorie der spanenden Bearbeitung gehört, hat sie ihre eigenen Eigenschaften. Es wird hauptsächlich als ein hoher Automatisierungsgrad, ein langer kontinuierlicher Bearbeitungsprozess realisiert, und der Zeitaufwand für die Werkzeugeinstellung ist komplizierter und zeitaufwändiger als die herkömmliche Bearbeitung. Daher gibt es viele Fragen, über die es sich lohnt, bei der Werkzeugauswahl nachzudenken. Dieser Artikel vermittelt Ihnen das relevante Wissen über häufig verwendete CNC-Werkzeuge. Ich glaube, dass ein gutes Werkzeug der erste Schritt zur Verbesserung der Effizienz der CNC-Bearbeitung ist.
Werkzeugmaterial und -beschichtung
Verschiedene derzeit verwendete Werkzeugmaterialien haben ihre Eigenschaften, um unterschiedlichen Verarbeitungsanforderungen gerecht zu werden. Zu den notwendigen Eigenschaften allgemeiner Werkzeugmaterialien gehören niedriger Reibungskoeffizient, hohe Präzision, gute Wärmeleitfähigkeit, ausreichende Zähigkeit und Schlagzähigkeit.
Die gängigen Werkzeugmaterialien herkömmlicher CNC-Werkzeugmaschinen sind Schnellarbeitsstahl und Hartmetall. Einige besondere Anlässe wie Hochgeschwindigkeitsschneiden, Trockenschneiden, Schneiden von schwer zu bearbeitenden Materialien und Drehen anstelle von Schleifen erfordern jedoch die Verwendung von superharten Materialien, einschließlich Keramik, CBN, PCBN, Diamant usw. Der Preis von Diese superharten Materialien sind relativ hoch, und der Schneidprozess und die Parameter sind nicht leicht zu beherrschen, und sie stellen bestimmte Anforderungen an die Steifigkeit der Werkzeugmaschine, und es gibt nicht viele Anwendungen in der konventionellen Verarbeitung.
Werkzeug aus superhartem Material
Die Oberflächenbeschichtung von Werkzeugen ist eine der wichtigsten Methoden zur Verbesserung der Werkzeugleistung, die in den letzten Jahren weit verbreitet war. Die Standzeit mit Beschichtung ist zehnmal höher als die der Werkzeuge ohne Beschichtung. Übliche Beschichtungen umfassen Titannitrid TIN, Titancarbidnitrid TICN und Aluminiumoxid. Die folgende Abbildung zeigt, dass die Schnittgeschwindigkeit von Schnellarbeitsstahl und Hartmetall um das Hundertfache verkürzt wurde, während die Verwendung von beschichteten Werkzeugen die Bearbeitungszeit um das Vierfache verkürzte.
Werkzeugklassifizierung
Häufig verwendete CNC-Werkzeuge werden nach ihrer Form in drei Typen eingeteilt:Schaftfräser, Rundkopffräser und Kugelfräser. Jedes Tool hat seine spezifische Rolle.
Schaftfräser
Die Schaftfräser von CNC-Bearbeitungszentren werden auch Flachbodenfräser genannt, die von Hauptschneiden umgeben sind und unten eine Nebenschneide bilden. Die äußere Kante und die untere Fläche des Schaftfräsers haben Fräszähne, um die Schneidkante zu bilden, sodass er zum Fräsen der vertikalen Oberfläche des Werkstücks verwendet werden kann. Die Formänderung des Schaftfräsers ist sehr kompliziert und eignet sich für alle Arten von Bearbeitungen wie Fräsen von Ebenen, Nuten, Konturflächen usw. Man kann sagen, dass er der am weitesten verbreitete Fräser ist.
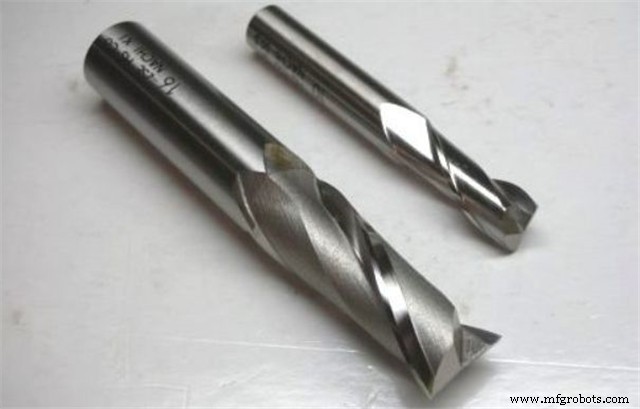
Da beim Fräsen eines 2D-förmigen Werkstücks der Kontaktbereich mit dem Werkstück die Außenkante und die Bodenfläche ist, ist es möglich, äußerst effiziente Werte sowohl für die Werkzeugsteigung als auch für die Schnitttiefe zu verwenden. Beim Schneiden der Form eines 3D-Werkstücks befindet sich die Kontaktfläche mit dem Werkstück jedoch fast immer in der Nähe der scharfen Spitze. Daher muss der Abstand zwischen den Werkzeugen oder die Schnitttiefe verringert werden, was die Bearbeitungseffizienz verringert.
Kurz gesagt, Schaftfräser sind für 2D-geformte Werkstücke geeignet, aber nicht für 3D-geformte Werkstücke.
Ballmesser
Die Klinge mit kugelförmiger Unterklinge ist ein Kugelmesser, auch R-Messer genannt. Im Gegensatz zu Schaftfräsern sind Kugelfräser unverzichtbare Werkzeuge zum Fräsen von 3D-Werkstücken. Da die Unterseite des Kugelmessers keine scharfe Spitze wie ein Schaftfräser hat, sondern eine Klinge mit einem R-Winkel, ist die Klinge des Kugelmessers stabiler und bricht nicht so leicht zusammen.
In der Formenbearbeitung werden Kugelfräser meist zum Fräsen von 3D-Formen eingesetzt, insbesondere beim Schlichten und Verputzen von Ecken. Die Kontaktfläche zwischen dem Kugelfräser und dem Werkstück ist jedoch gering und der Abstand kann nicht vergrößert werden, sodass er nicht zum Fräsen relativ flacher Bereiche geeignet ist.
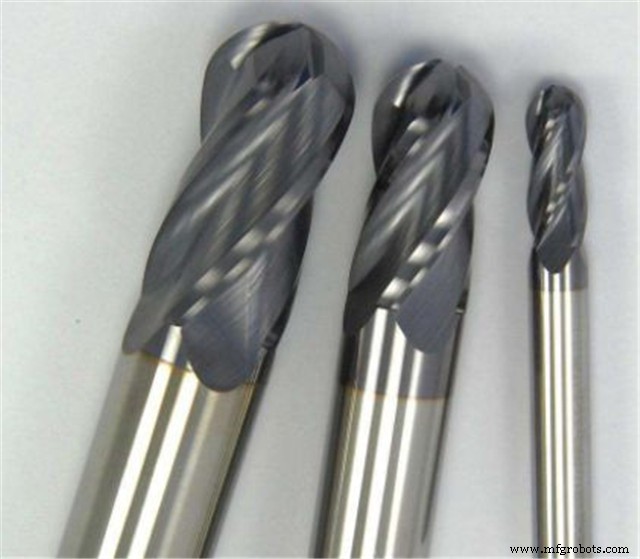
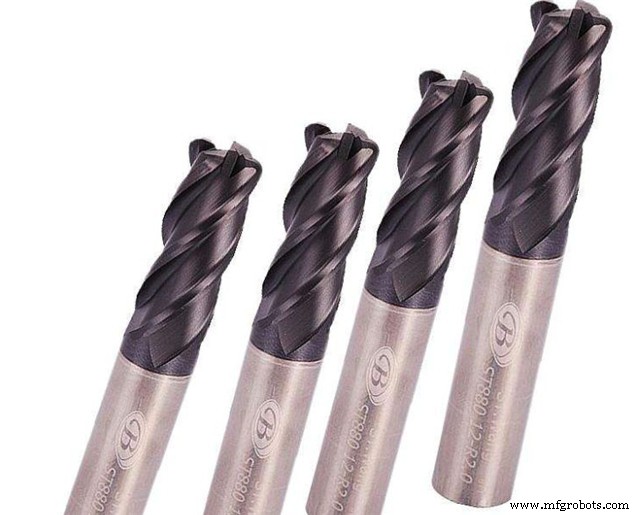
Rundnasenmesser
Das Rundnasenmesser des CNC-Bearbeitungszentrums wird auch als R-Messer mit flachem Boden bezeichnet, das zum Schruppen, flachen glatten Messer und glatten Messer mit gekrümmter Oberflächenkontur verwendet werden kann. Im Vergleich zu Schaftfräsern und Kugelfräsern kombinieren Rundkopffräser die Vorteile beider und haben eine bessere Arbeitseffizienz. Der horizontale Messerabstand des Rundmessers kann größer sein als der des Kugelmessers und hat beim Schlichten die gleichen Vorteile wie das Kugelmesser. Daher ist das Rundmesser eine gute Wahl zum Schruppen oder Schlichten.
Wenn das Werkstück groß ist, die Oberflächenänderung gering ist, der schmale vertiefte Bereich klein und der relativ flache Bereich groß ist, verwenden Sie am besten ein Rundmesser zur Bearbeitung und verwenden Sie dann die sekundäre Schruppmethode, um den Bereich zu finden das bedarf einer Nachbearbeitung. Aber gegenüber einigen vertieften Bereichen hat das Messer mit runder Nase einen blinden Bereich der Klinge, und das Phänomen der „Oberkante“ wird gefunden.
Häufige Probleme und Lösungen
Im tatsächlichen Betrieb wird es immer verschiedene Probleme geben. Hier sind einige allgemeine Probleme und Lösungen für alle. Ich glaube, dass mit der Lösung dieser Probleme die Verarbeitungseffizienz von Werkzeugmaschinen verbessert wird.
Werkzeugvibration
Da immer mehr schwer zu verarbeitende Materialien verwendet werden, ist die Vibration zu einem der Hindernisse für die Verbesserung der Verarbeitungseffizienz geworden. Das Auftreten von Vibrationen wirkt sich direkt auf die Bearbeitungsgenauigkeit und Oberflächenrauheit aus, beschleunigt den Werkzeugverschleiß, wirkt sich stark auf die Lebensdauer des Werkzeugs aus und in schweren Fällen kann die Schneidarbeit nicht fortgesetzt werden.
Die Werkzeugvibration erfordert drei Bedingungen, die gleichzeitig vorhanden sind. Das Prozesssystem einschließlich des Werkzeugs ist nicht ausreichend steif, was zu einer niedrigen Eigenfrequenz führt. Beim Schneiden wird eine ausreichend große äußere Anregungskraft erzeugt. Die Frequenz der externen Anregungskraft ist die gleiche wie die Eigenfrequenz des Prozesssystems. Resonanz.
Die Idee zur Lösung von Werkzeugvibrationen ist in drei Teile gegliedert. Die erste besteht darin, die Schneidkraft auf ein Minimum zu reduzieren. Um die Schnittkraft zu reduzieren, verwenden Sie den kleinstmöglichen Kopfbogen. Erhöhen Sie den Spanwinkel des Werkzeugs. Gepresste Klingen durch geschliffene Klingen ersetzen. Reduzieren Sie die Schnitttiefe, Drehzahl und erhöhen Sie den Vorschub. Verwenden Sie für die verlängerte Welle einen Eintrittswinkel von 90 Grad. Bei Fräsern mit schlanken Stäben sind runde Wendeschneidplatten am förderlichsten für die Vibrationsreduzierung.
Die zweite besteht darin, die statische Steifigkeit des Werkzeugsystems oder der Vorrichtung und des Werkstücks zu maximieren.
Die dritte besteht darin, eine weitere Vibration innerhalb der Werkzeugstange zu erzeugen, um die Vibrationsfrequenz der extern erregten Schneidkraft zu unterbrechen und dadurch die Werkzeugvibration zu eliminieren.
Klingenverschleiß
Während des Bearbeitungsprozesses verschleißen die vorderen und hinteren Werkzeugflächen oft zu schnell. Darunter sollte es unterschiedliche Reaktionsmethoden entsprechend unterschiedlichen Blattschadensbedingungen geben.
1. Übermäßiger Verschleiß der Flankenfläche führt zu rauer Oberfläche und schlechten Bearbeitungsmaßen
Gründe für dieses Szenario sind eine hohe Schnittgeschwindigkeit oder eine schlechte Verschleißfestigkeit der Klinge. Zu den Lösungen gehören verbesserte Methoden zur Reduzierung der Schnittgeschwindigkeit bei gleichzeitiger schrittweiser Erhöhung der Schnittmenge, die Verwendung von verschleißfesteren Klingenmaterialien oder -beschichtungen und der Versuch, Gleichlauffräsen anstelle von Gegenlauffräsen zu verwenden.
2. Kerbverschleiß
Nachdem die Messernut geschliffen wurde, kann sie beschädigt werden und Oberflächenrauheit und Abplatzungen verursachen. Die Gründe umfassen eine zu geringe Vorschubgeschwindigkeit; das Mahlgut neigt zur Kaltverfestigung; die Oberfläche des Werkstücks weist Oxidablagerungen usw. auf. Angesichts dieser Situation ist es notwendig, den Rillenverschleiß der Klinge häufig mit einem Nagel zu überprüfen.
3. Aufbauschneide beim Fräsen von Edelstahl und hitzebeständigen Legierungen
Das Fräsen von klebrigen Fräsern wird auch als Aufbauschneide bezeichnet, wodurch die bearbeitete Oberfläche rau und gratig wird. Das Abfallen der Aufbauschneide führt dazu, dass die Spanfläche der Klinge abfällt und die Klingenkante zusammenbricht, und das sekundäre Abplatzen von Werkstücken aus hitzebeständiger Legierung bewirkt, dass die Kante schnell zusammenbricht. Die Gründe für diese Art von Situation sind nichts anderes als eine stumpfe Schneidkante, ein negativer Spanwinkel, eine niedrige Schnittgeschwindigkeit, eine zu geringe Spandicke und eine schlechte Spanabfuhr.
Die Methode zur Lösung des aufgebauten Tumors basiert grob auf „sechs Schritten“. Der erste Schritt besteht darin, die Schnittgeschwindigkeit für Edelstahl und Aluminiumlegierungen zu erhöhen. Der zweite Schritt besteht darin, physikalisch beschichtete Klingen oder nicht beschichtete Klingen zu verwenden. Der dritte Schritt besteht darin, die Schnittmenge schrittweise zu erhöhen, um die beste Spandicke zu erreichen. Der vierte Schritt:Bereiten Sie ausreichend Hochdruck-Kühlmittel oder Luft vor, um sekundäre Späne zu vermeiden. Der fünfte Schritt besteht darin, Gleichlauffräsen anstelle von Gegenlauffräsen zu verwenden. Der sechste Schritt ist die Verwendung von reinem Mineralöl, um den Schnittbereich bei niedriger Geschwindigkeit für hitzebeständige Titanlegierungen und ausscheidungshärtenden Edelstahl zu waschen.
4 . Klinge bricht oder trifft ein Messer
Es gibt viele Gründe für diese Art von Kantenausbrüchen. Das Klingenmaterial ist zu hart, die Klingengeometrie ist zu schwach und die verwendete Schnittgeschwindigkeit ist zu niedrig, was die Schneidkante quetschen kann, was zu ungleichmäßigem Werkstückmaterial oder unterbrochenem Schnitt führt.
Überprüfen Sie in Anbetracht dieser Situation zunächst, ob die Unterlegscheibe gebrochen ist und ob die Messerschraube verformt ist und ersetzt werden muss; zweitens sollte der Vibrationsfaktor eliminiert werden und das Klingenmaterial mit besserer Zähigkeit sollte verwendet werden und die Klinge mit starker Kante sollte geändert werden; Schließlich sollte die Schnittgeschwindigkeit erhöht werden, um die Kante zu beseitigen. Der Mund kann gequetscht werden. (Verwandter Beitrag:Zusammenfassung von Bearbeitungsverschleißproblemen und -lösungen)
Herstellungsprozess
- Werkzeugdurchbiegung in der CNC-Bearbeitung
- Grundkenntnisse der Auswahl von CNC-Fräsern und Vorsichtsmaßnahmen für den Betrieb
- Tipps und Tricks zur CNC-Bearbeitung
- Wissen über Verrundungen in der CNC-Bearbeitung
- Vorteile und Anwendung von Flachauslegerwerkzeugen für die CNC-Bearbeitung
- Die 5 wichtigsten Anzeichen für ein abgenutztes CNC-Bearbeitungswerkzeug
- Identifizieren häufiger CNC-Bearbeitungsfehler und Kontrollmaßnahmen
- Was ist Werkzeugdurchbiegung bei der CNC-Bearbeitung und wie kann man sie reduzieren?
- CNC HMC-Bearbeitung und Bearbeitungszentren
- Leitfaden zur Auswahl von Fräswerkzeugen