Optimierung der Ergebnisse bei der Bearbeitung mit Miniatur-Schaftfräsern
Die Bearbeitungsindustrie betrachtet im Allgemeinen alle Schaftfräser mit einem Durchmesser von weniger als 1/8 Zoll als Mikrobearbeitungs- und Miniatur-Schaftfräser. Dies ist auch oft der Punkt, an dem Toleranzen in einem engeren Fenster gehalten werden müssen. Da der Durchmesser eines Werkzeugs direkt mit der Festigkeit eines Werkzeugs zusammenhängt, sind Miniatur-Schaftfräser erheblich schwächer als ihre größeren Gegenstücke, und daher muss bei der Mikrobearbeitung ein Mangel an Festigkeit berücksichtigt werden. Wenn Sie diese Tools in einer sich wiederholenden Anwendung verwenden, ist die Optimierung dieses Prozesses entscheidend.
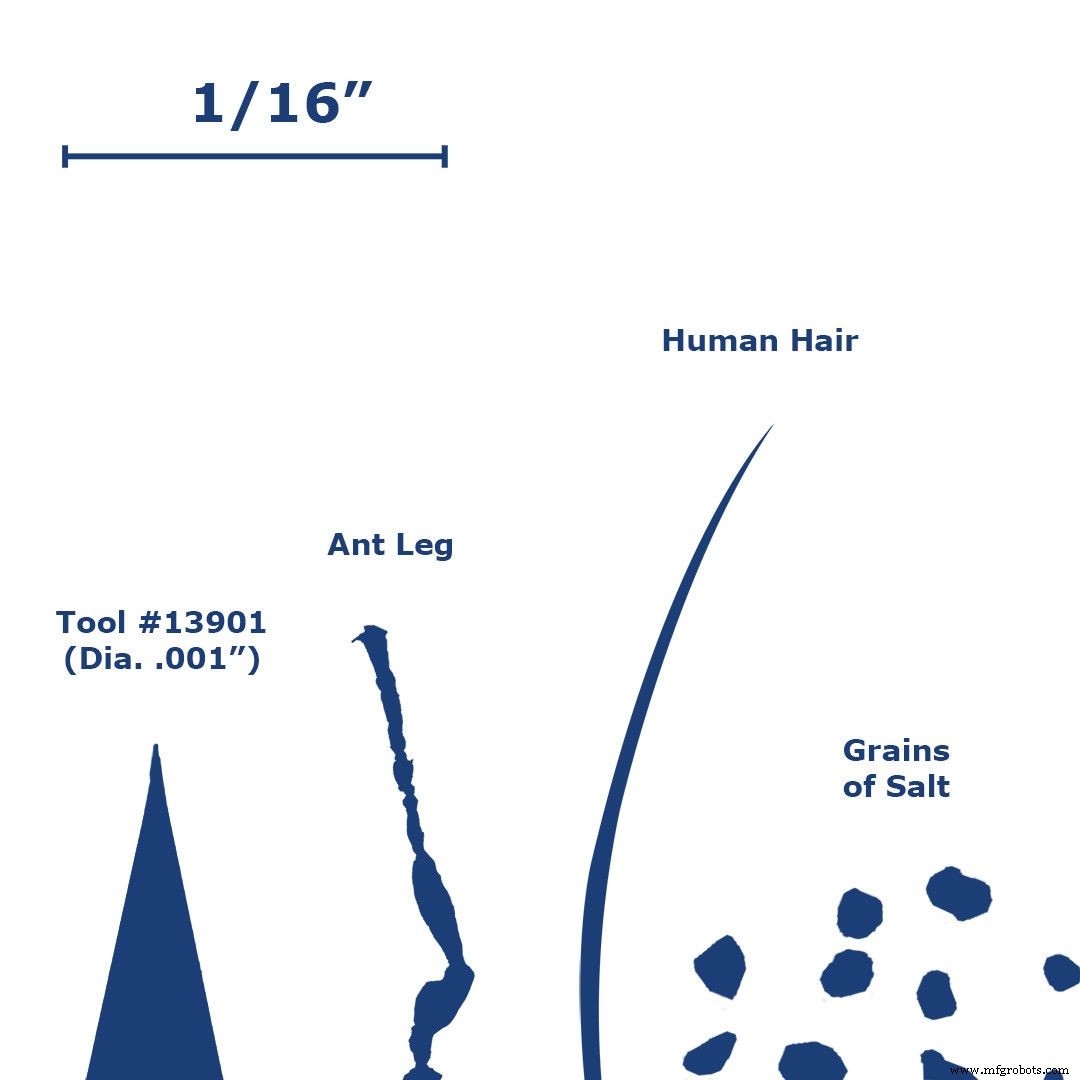
Wichtige Schnittunterschiede zwischen konventionellen und Miniatur-Schaftfräsern
Auslauf
Unrundheit während einer Operation hat einen viel größeren Einfluss auf Miniaturwerkzeuge, da selbst ein sehr kleiner Betrag einen großen Einfluss auf den Werkzeugeingriff und die Schnittkräfte haben kann. Unrundheit führt dazu, dass die Schneidkräfte aufgrund des ungleichmäßigen Eingriffs der Spannuten zunehmen, was dazu führt, dass einige Spannuten bei herkömmlichen Werkzeugen schneller verschleißen als andere und bei Miniaturwerkzeugen brechen. Werkzeugvibrationen wirken sich auch auf die Lebensdauer des Werkzeugs aus, da die intermittierenden Stöße dazu führen können, dass das Werkzeug absplittert oder, im Fall von Miniaturwerkzeugen, bricht. Es ist äußerst wichtig, den Rundlauf einer Einrichtung zu überprüfen, bevor Sie mit dem Betrieb beginnen. Das folgende Beispiel zeigt, wie groß der Unterschied von 0,001 Zoll im Rundlauf zwischen einem Werkzeug mit einem Durchmesser von 0,500 Zoll und einem Werkzeug mit einem Durchmesser von 0,031 Zoll ist.
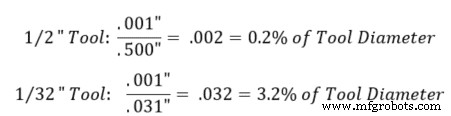
Chipdicke
Das Verhältnis zwischen Spandicke und Kantenradius (Schneidenpräparation) ist bei Miniaturwerkzeugen viel kleiner. Dieses Phänomen wird manchmal als „Größeneffekt“ bezeichnet und führt oft zu einem Fehler bei der Vorhersage der Schnittkräfte. Wenn das Verhältnis von Spandicke zu Kantenradius kleiner ist, pflügt der Fräser das Material mehr oder weniger, anstatt es zu scheren. Dieser Pflugeffekt ist im Wesentlichen auf den negativen Spanwinkel zurückzuführen, der durch den Kantenradius beim Schneiden eines Spans mit geringer Dicke entsteht.
Unterschreitet diese Dicke einen bestimmten Wert (dieser Wert hängt vom verwendeten Werkzeug ab), drückt sich das Material unter dem Werkzeug hindurch. Sobald das Werkzeug passiert und keine Spanbildung auftritt, stellt sich ein Teil des gepflügten Materials elastisch zurück. Diese elastische Erholung verursacht höhere Schnittkräfte und Reibung aufgrund der vergrößerten Kontaktfläche zwischen Werkzeug und Werkstück. Diese beiden Faktoren führen letztendlich zu einem größeren Werkzeugverschleiß und einer höheren Oberflächenrauheit.
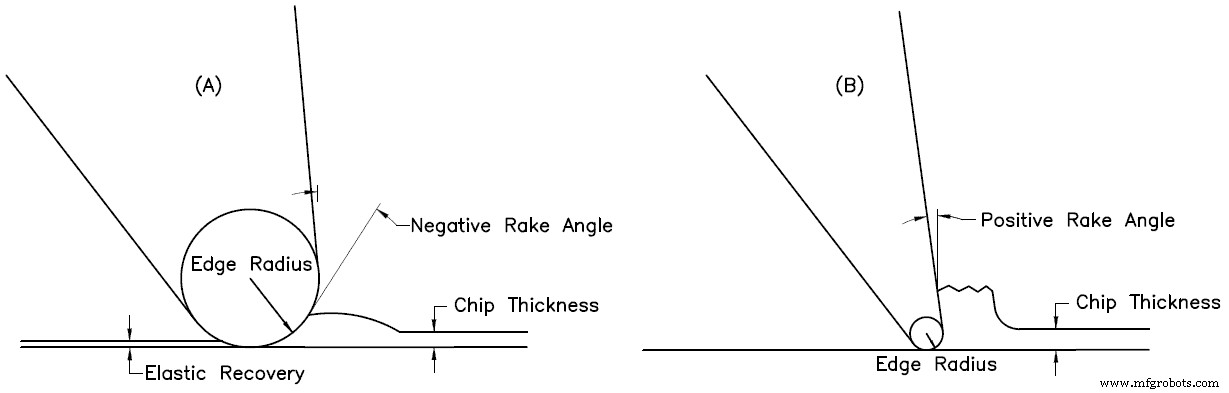
Werkzeugdurchbiegung in konventionellen vs. Mikrobearbeitungsanwendungen
Die Werkzeugablenkung hat einen viel größeren Einfluss auf die Bildung von Spänen und die Genauigkeit des Vorgangs bei Mikrobearbeitungsvorgängen im Vergleich zu herkömmlichen Vorgängen. An der Seite des Werkzeugs konzentrierte Schnittkräfte bewirken, dass es sich entgegen der Vorschubrichtung verbiegt. Die Größe dieser Durchbiegung hängt von der Steifigkeit des Werkzeugs und seinem Abstand von der Spindel ab. Werkzeuge mit kleinem Durchmesser sind im Vergleich zu Werkzeugen mit größerem Durchmesser von Natur aus weniger steif, da sie viel weniger Material haben, das sie während des Vorgangs an Ort und Stelle hält. Theoretisch führt eine Verdoppelung der Länge, die aus dem Halter herausragt, zu einer 8-mal größeren Durchbiegung. Die Verdoppelung des Durchmessers eines Schaftfräsers führt zu einer 16-mal geringeren Durchbiegung. Wenn ein Miniatur-Schneidwerkzeug beim ersten Durchgang bricht, liegt dies höchstwahrscheinlich daran, dass die Biegekraft die Festigkeit des Hartmetalls überwindet. Hier sind einige Möglichkeiten, wie Sie die Werkzeugablenkung minimieren können.
Werkstückhomogenität
Die Werkstückhomogenität wird mit abnehmendem Werkzeugdurchmesser zu einem fragwürdigen Faktor. Dies bedeutet, dass ein Material aufgrund einer Reihe von Faktoren, wie z. B. Behälteroberflächen, unlöslichen Verunreinigungen, Korngrenzen und Versetzungen, in einem außergewöhnlich kleinen Maßstab möglicherweise keine einheitlichen Eigenschaften aufweist. Diese Annahme wird im Allgemeinen für Werkzeuge mit einem Schneidendurchmesser von weniger als .020 Zoll gespeichert, da das Schneidsystem extrem klein sein muss, damit die Homogenität der Mikrostruktur des Materials in Frage gestellt wird.
Oberflächenbeschaffenheit
Die Mikrobearbeitung kann im Vergleich zur herkömmlichen Bearbeitung zu einer erhöhten Menge an Graten und Oberflächenrauheit führen. Beim Fräsen nimmt der Grat mit zunehmendem Vorschub zu und mit zunehmender Drehzahl ab. Während eines Bearbeitungsvorgangs werden Späne durch das Komprimieren und Scheren des Werkstückmaterials entlang der primären Scherzone erzeugt. Diese Scherzone ist in Abbildung 2 unten zu sehen. Wie bereits erwähnt, ist das Verhältnis von Spandicke zu Kantenradius bei Miniaturanwendungen viel höher. Daher entstehen beim Schneiden plastische und elastische Verformungszonen, die sich neben der primären Scherzone befinden (Abbildung 2a). Befindet sich also die Schneidkante nahe am Rand des Werkstücks, erreicht die elastische Zone auch diesen Rand (Bild 2b). Die plastische Verformung breitet sich mit fortschreitender Schneidkante in diesen Bereich aus, und an der Grenze bildet sich aufgrund der verbindenden elastischen Verformungszonen eine weitere plastische Verformung (Abbildung 2c). Ein dauerhafter Grat beginnt sich zu bilden, wenn sich die plastischen Verformungszonen verbinden (Abbildung 2d) und erweitert sich, sobald ein Span entlang der Gleitlinie reißt (Abbildung 2e). Wenn die Späne schließlich von der Werkstückkante abbrechen, bleibt ein Grat zurück (Bild 2f).
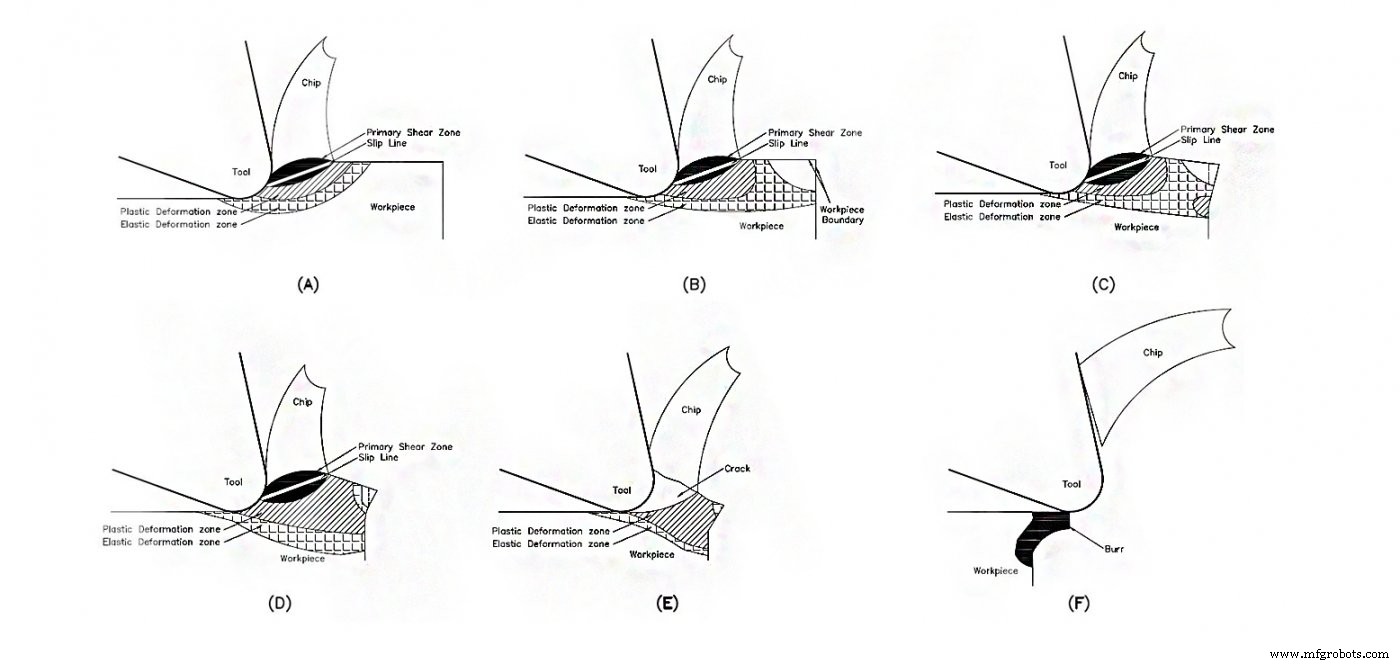
Best Practices für den Werkzeugweg für Miniatur-Schaftfräser
Aufgrund der Zerbrechlichkeit von Miniaturwerkzeugen muss der Werkzeugweg so programmiert werden, dass eine plötzliche Höhe der Schnittkraft vermieden wird und die Verteilung der Schnittkräfte auf mehrere Achsen ermöglicht wird. Aus diesen Gründen sollten beim Schreiben eines Programms für einen Miniatur-Werkzeugweg die folgenden Vorgehensweisen berücksichtigt werden:
Rampen in einen Teil
Das kreisförmige Eintauchen ist die beste Methode, um sich axial in ein Teil hineinzubewegen, da es die Schnittkräfte gleichmäßig entlang der x-, y- und z-Ebenen verteilt. Wenn Sie sich bei einer bestimmten Schnittiefe radial in ein Teil bewegen müssen, ziehen Sie einen bogenförmigen Werkzeugpfad in Betracht, da dies die Schnittkräfte allmählich und nicht auf einmal auf das Werkzeug überträgt.
Mikrobearbeitung in Kreisbahnen
Sie sollten für eine kreisförmige Bahn nicht die gleichen Geschwindigkeiten und Vorschübe verwenden wie für eine lineare Bahn. Dies liegt an einem Effekt, der zusammengesetzte Winkelgeschwindigkeit genannt wird. Jeder Zahn an einem Schneidwerkzeug hat seine eigene Winkelgeschwindigkeit, wenn er in der Spindel aktiv ist. Wenn eine kreisförmige Werkzeugbahn verwendet wird, wird dem System eine weitere Winkelgeschwindigkeitskomponente hinzugefügt, und daher bewegen sich die Zähne auf dem äußeren Abschnitt der Werkzeugbahn mit einer wesentlich anderen Geschwindigkeit als erwartet. Je nachdem, ob es sich um eine Innen- oder Außenrundbearbeitung handelt, muss der Vorschub des Werkzeugs angepasst werden. Um herauszufinden, wie Sie Ihren Feed anpassen können, lesen Sie diesen Artikel über das Laufen im Kreis.
Schlitzfräsen mit einem Miniatur-Schaftfräser
Nähern Sie sich einem Mini-Slot nicht auf die gleiche Weise wie einem größeren Slot. Bei einem Miniaturschlitz wünscht man sich möglichst viele Spannuten am Werkzeug, da dies durch einen größeren Kern die Steifigkeit des Werkzeugs erhöht. Dies verringert die Wahrscheinlichkeit, dass das Werkzeug aufgrund von Durchbiegung bricht. Da bei einer höheren Anzahl von Spannuten weniger Platz für die Spanabfuhr vorhanden ist, muss der axiale Eingriff verringert werden. Bei Werkzeugen mit größerem Durchmesser können Sie 50 % – 100 % des Werkzeugdurchmessers unterschreiten. Aber wenn Sie Miniatur-Schaftfräser mit einer höheren Schneidenzahl verwenden, reduzieren Sie nur zwischen 5 % – 15 %, abhängig von der Größe des Durchmessers und dem Risiko einer Durchbiegung. Die Vorschubgeschwindigkeit sollte erhöht werden, um den verringerten axialen Eingriff auszugleichen. Der Vorschub kann sogar hoch erhöht werden, wenn ein Kugelkopffräser verwendet wird, da die Spanausdünnung bei diesen geringen Schnitttiefen auftritt und sich wie ein Fräser mit hohem Vorschub zu verhalten beginnt.
Den Feed um Ecken verlangsamen
Ecken eines Teils erzeugen eine zusätzliche Menge an Schnittkräften, wenn mehr von dem Werkzeug mit dem Teil in Eingriff kommt. Aus diesem Grund ist es vorteilhaft, beim Bearbeiten um Ecken den Vorschub zu verlangsamen, um das Werkzeug allmählich an diese Kräfte heranzuführen.
Climb Milling vs. konventionelles Fräsen in Mikrobearbeitungsanwendungen
Dies ist eine etwas schwierig zu beantwortende Frage, wenn es um die Mikrobearbeitung geht. Gleichlauffräsen sollte immer dann eingesetzt werden, wenn eine hochwertige Oberflächengüte auf dem Teildruck erforderlich ist. Diese Art von Werkzeugweg führt letztendlich zu besser vorhersagbaren/geringeren Schnittkräften und damit zu einer hochwertigeren Oberflächengüte. Beim Gleichlauffräsen greift der Fräser zu Beginn des Schnitts in die maximale Spandicke ein, wodurch er die Tendenz hat, sich vom Werkstück wegzudrücken. Dies kann möglicherweise zu Chatter-Problemen führen, wenn das Setup nicht ausreichend starr ist. Beim konventionellen Fräsen zieht sich der Fräser beim Zurückdrehen in den Schnitt selbst in das Material und erhöht die Schnittkräfte. Konventionelles Fräsen sollte für Teile mit langen, dünnen Wänden sowie für heikle Operationen verwendet werden.
Kombinierte Schrupp- und Schlichtoperationen
Diese Operationen sollten bei der Mikrobearbeitung von hohen, dünnwandigen Teilen berücksichtigt werden, da in einigen Fällen das Teil für einen Endbearbeitungsdurchgang nicht ausreichend gestützt wird.
Hilfreiche Tipps für erfolgreiche Mikrobearbeitungsvorgänge mit Miniatur-Schaftfräsern
Versuchen Sie, Unrundheit und Durchbiegung zu minimieren so viel wie möglich bei der Mikrobearbeitung mit Miniatur-Schaftfräsern. Dies kann durch die Verwendung eines Schrumpf- oder Einpresswerkzeughalters erreicht werden. Maximieren Sie den Schaftkontakt mit der Spannzange und minimieren Sie gleichzeitig das Herausragen während einer Operation. Überprüfen Sie Ihren Druck noch einmal und vergewissern Sie sich, dass Sie den größtmöglichen Schaftfräser haben, da größere Werkzeuge weniger Durchbiegung bedeuten.
- Wählen Sie eine geeignete Schnitttiefe damit das Verhältnis von Spandicke zu Kantenradius nicht zu klein ist, da dies zu einem Pflugeffekt führt.
- Wenn möglich, prüfen Sie die Härte des Werkstücks vor der Bearbeitung, um die mechanischen Eigenschaften des vom Verkäufer beworbenen Materials zu bestätigen. Dies gibt dem Bediener einen Eindruck von der Qualität des Materials.
- Verwenden Sie ein beschichtetes Werkzeug wenn möglich, wenn in Eisenwerkstoffen gearbeitet wird, da bei der Bearbeitung dieser Metallarten übermäßig viel Wärme entsteht. Werkzeugbeschichtungen können die Werkzeuglebensdauer um 30 % bis 200 % verlängern und ermöglichen höhere Geschwindigkeiten, was bei der Mikrobearbeitung von entscheidender Bedeutung ist.
- Erwägen Sie die Verwendung eines Stützmaterials um das Auftreten von Graten während einer Mikrobearbeitungsanwendung zu kontrollieren. Das Stützmaterial wird auf der Werkstückoberfläche abgelagert, um eine zusätzliche Stützkraft bereitzustellen sowie die Steifigkeit der ursprünglichen Kante des Werkstücks zu erhöhen. Während des Vorgangs gratet und verformt sich eher das Trägermaterial als das Werkstück.
- Flutkühlmittel verwenden zu niedrigeren Schnittkräften und einer höheren Oberflächengüte.
- Untersuchen Sie den Werkzeugweg Das ist anzuwenden, da ein paar Anpassungen die Lebensdauer eines Miniaturwerkzeugs erheblich verlängern können.
- Werkzeuggeometrie doppelt prüfen um sicherzustellen, dass es für das zu bearbeitende Material geeignet ist. Wenn verfügbar, verwenden Sie Werkzeuge mit variabler Steigung und variabler Spirale, da dies Oberschwingungen bei den außergewöhnlich hohen Drehzahlen reduziert, mit denen Miniaturwerkzeuge normalerweise betrieben werden.
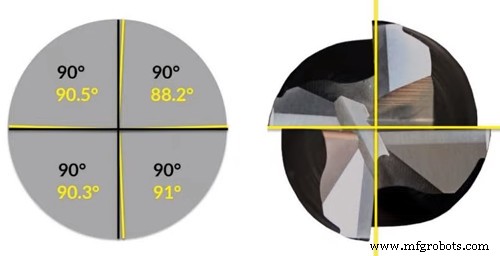
CNC-Maschine
- Wie benutzt man eine Holzdrehmaschine für Anfänger?
- Wie bedient man einen CNC-Router mit NC Studio?
- So senken Sie die CNC-Bearbeitungskosten mit gebrauchten Maschinen
- So verlängern Sie die Lebensdauer Ihres Schaftfräsers
- So maximieren Sie Schaftfräser mit hoher Balance
- Wie man CNC-Bearbeitungsteile mit engen Toleranzen herstellt
- Die geheime Mechanik von Schaftfräsern mit hohem Vorschub
- Wie die Schaftfräser TuffCut XT von M.A. Ford Ihnen helfen, die Produktivität zu steigern
- Abstechen mit Y-Achsen-Bearbeitung
- Was ist Standzeit? Werkzeugoptimierung mit Maschinendaten