Tiefbohren erfordert eine präzise Kühlmittelkontrolle
Kühlmittel ist für den Tieflochbohrprozess so entscheidend, dass die heutigen hochmodernen Tieflochbohrsysteme es ähnlich steuern wie die Spindel oder die Achsen einer Maschine. Ein sorgfältiges Management von Kühlmitteldruck, Filtration, Temperatur und Durchflussrate ist der Schlüssel zur Optimierung von Tieflochbohrprozessen. Dies erfordert eine programmierbare, stufenlose strömungsbasierte Steuerungsfähigkeit, die in die Tieflochbohrmaschine selbst integriert ist. Das Ergebnis ist ein System mit der erforderlichen Einstellbarkeit, um sicherzustellen, dass im Kühlmittelsystem nie mehr Druck herrscht, als für eine effektive Spanabfuhr und präzises Bohren erforderlich ist.
Viele Jahre lang waren Kühlmittelsysteme durch die Spindel/durch das Werkzeug das fortschrittlichste Kühlmittelzufuhrsystem neben den Fluttypen. Dann veränderte das Aufkommen von Hochdruck-Kühlmittelsystemen, die bei über 1.000 psi arbeiten, die Landschaft der Kühlmitteltechnologie mit einer besonders effektiven Werkzeugkühlung sowie einer effizienten Spanabfuhr für die meisten konventionellen Bearbeitungsvorgänge. Bohranwendungen, hauptsächlich solche mit Spiralbohrern, waren ein Hauptantrieb für die Entwicklung von Hochdruckkühlsystemen, insbesondere Tieflochbohranwendungen, bei denen das Verhältnis von Tiefe zu Durchmesser typischerweise 10:1 und mehr beträgt.
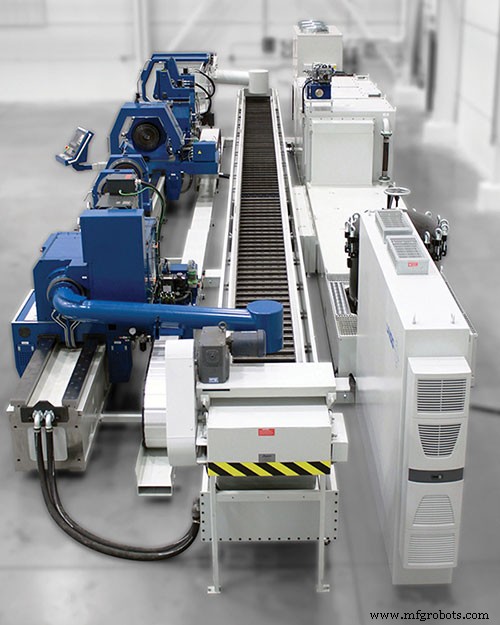
Mit zunehmendem Kühlmitteldruck steigt jedoch auch die Notwendigkeit einer ordnungsgemäßen Filtration und Temperaturregelung. Bei Systemen mit mehr als 1.000 psi ist eine 20- bis 50-stufige Filtration erforderlich, um einen Ausfall der Pumpen zu verhindern, und in den meisten Fällen benötigen Hochdruck-Kühlmittelsysteme einen Kühler, um die Kühlmitteltemperatur zu regulieren. Während die meisten Betriebe mit diesen Systemen aufhören, können Filtration und Kühlmittel selbst bei anspruchsvollen Bohranwendungen eine der wichtigsten Variablen bei der Verwendung von Hochdruck-Kühlmitteln nicht ansprechen, nämlich die Durchflussrate.
Werkstätten haben oft keine Ahnung, wie viel Kühlmittel ihr System liefert oder liefern sollte. Typische Hochwasser-Kühlmittelsysteme liefern zum Beispiel je nach System etwa 10-gpm bis etwa 40-gpm-Durchflussraten. Es werden jedoch viel größere Volumina benötigt, um Späne bei Bohrvorgängen abzuleiten, wenn die Löcher im Durchmesser größer und/oder tiefer werden. Bei der Verwendung größerer Einlippenbohrer oder BTA-Werkzeuge kann der erforderliche Kühlmittelfluss beispielsweise von 50 gpm bis zu 75 bis 350 gpm aufwärts für Lochdurchmesser von 10 bis 12 Zoll (25,4 bis 30,5 cm) reichen. Umgekehrt sind die Durchflussraten für kleine -Durchmessertiefe Löcher müssen möglicherweise nur 2 gpm betragen, aber mit viel höheren Druckniveaus. Ein Loch mit einem Durchmesser von 0,040 Zoll (1,016 mm) beispielsweise kann einen Kühlmitteldruck von bis zu 3.000 psi erfordern.
Da ein exponentieller Faktor beteiligt ist, steigt die Fläche/Metallabtragung erheblich an, wenn der Lochdurchmesser leicht zunimmt. Betrachten Sie den Unterschied zwischen einem Loch mit einem Durchmesser von 1 Zoll (25,4 mm) und einem Loch mit einem Durchmesser von 1,5 Zoll (38,1 mm) – eine 50-prozentige Vergrößerung des Durchmessers. Die resultierende Fläche beträgt 0,79 Zoll3 (12,95 cm3) für das 1-Zoll-Loch gegenüber 1,77 Zoll3 (29,01 cm3) für das 1,5-Zoll-Loch, eine 100-prozentige Zunahme. Die Verdoppelung des Lochdurchmessers von 1 auf 2 Zoll entspricht einer viermal größeren Fläche und viermal mehr Material, das aus dem Loch evakuiert werden muss. Mit anderen Worten, Werkstätten sollten davon ausgehen, dass selbst eine geringfügige Vergrößerung des Lochdurchmessers eine Änderung der Kühlmittelparameter rechtfertigt .
Trotzdem bieten die meisten Kühlmittelsysteme sehr wenig Flexibilität. Flutkühlsysteme haben beispielsweise überhaupt keine Flexibilität – das Kühlmittel ist entweder ein- oder ausgeschaltet. Kühlmittelsysteme durch die Spindel können Entlastungseinstellungen oder M-Codes enthalten, die Einstellungen für niedrigen, mittleren und hohen Druck bieten, aber diese sind unzureichend für Werkstätten, die eine wirklich optimierte Kühlmittelzufuhr benötigen.
Geben Sie die stufenlose Kühlmittelsteuerung ein. Diese Technologie ermöglicht es den Werkstätten, ein Loch bei etwa 400 psi zu beginnen, und dann, wenn der Bohrer tiefer vordringt, diesen Wert auf das Niveau zu erhöhen, das erforderlich ist, um die Durchflussrate für eine effektive Späneabfuhr aufrechtzuerhalten. Dies ist jedoch ein schwieriger Prozess, um sich manuell einzuwählen. Wenn die Durchflussrate zu niedrig ist, bleiben Späne im Loch und könnten schließlich den Bohrer beschädigen. Zu viel Durchfluss kann übermäßigen Druck erzeugen, der wiederum unerwünschte Kräfte erzeugt, die die Bohrgenauigkeit beeinträchtigen können.
Für eine erfolgreiche und konsistente Leistung werden Tiefbohrmaschinen-OEMs wie UNISIG Kühlmittelsysteme und Steuerungen von Anfang an in das tatsächliche Design einer Maschine integrieren, um eine vollständige Integration zu gewährleisten. Dadurch können die Steuerungen ein sofortiges In-Prozess-Feedback für extrem granulare Einstellmöglichkeiten des Kühlmittels liefern, die jederzeit genau die richtige Kühlmittelmenge an die Schneide bringen.
Das System funktioniert, indem es eine Prozessrückmeldung in das Steuersystem implementiert, das sofortige Kühlmittelanpassungen vornimmt, um einen Werkzeugbruch zu verhindern. Das Feedback von der Steuerung hilft den Bedienern auch bei der Optimierung des Kühlmittelflusses und -drucks beim Tieflochbohren, und sobald diese Parameter bestimmt sind, können sie verwendet werden, um den Prozess immer wieder zu wiederholen.
Zusätzlich werden der Kühlmitteldruck und die Durchflussrückmeldung aus dem Prozess selbst verwendet, um gebrochene Werkzeuge zu erkennen. Wenn zum Beispiel der Kühlmitteldruck der Anwendung plötzlich abfällt, kann das auf einen Werkzeugbruch hindeuten. Und genau in diesem Moment kann der Prozess gestoppt und das Werkzeug ausgetauscht werden. Dies ist besonders nützlich beim Bohren von Löchern mit extrem kleinem Durchmesser, bei denen die geringeren Bohrlasten selbst eine geringfügige Änderung der Kraft schwer zu erkennen machen. Durch die Überwachung des Kühlmittels können Bediener jedoch den Zustand des Werkzeugs feststellen und feststellen, ob Späne abgeführt werden oder nicht. Und es kann helfen, Parameter wie Vorschübe und Geschwindigkeiten für eine bessere Spankontrolle in diesen Fällen weiter zu optimieren.
Neben Kühlmittelsystemen und -steuerungen werden auch Kühlmittelbehälter speziell für Tieflochbohrmaschinen von OEMs wie UNISIG entwickelt. Während Flut- und Spindel-Kühlmittelsysteme für Bearbeitungszentren 20- bis 50-Gallonen-Kühlmittelreservoirs haben können, werden diejenigen mit Tieflochbohrsystemen variieren, um die Geschwindigkeit und den Fluss des Kühlmittels aufzunehmen. Abhängig von der Größe der Tieflochbohrmaschine können die Kühlmittelbehälterkapazitäten bis zu 3.000 Gallonen betragen und mit einer Filtereinheit mit einer Kapazität von 350 gpm kombiniert werden.
Flut-, Durchspindel- und Hochdruck-Kühlschmierstoffsysteme machen auf konventionellen Bearbeitungszentren gelegentliche Hochleistungs-Bohroperationen möglich. Wenn jedoch täglich Bohrarbeiten durchgeführt werden und viel tiefere Löcher mit einem Verhältnis von 10, 20 oder sogar 40:1 und darüber hinaus erforderlich sind, wird eine spezielle Tieflochbohrmaschine benötigt. Und die besten Typen sind diejenigen, die mit dem Kühlmittelsystem als Erweiterung der Maschine konstruiert sind, ähnlich wie eine Spindel oder Achse Teil der Maschine ist. Hochentwickelte Kühlmittelsysteme und Steuerungen von OEMs wie UNISIG ermöglichen Werkstätten, täglich Tausende von Löchern zuverlässig und genau zu bohren – und das bei Tiefen-zu-Durchmesser-Verhältnissen von über 100:1 – mit minimalem Bedienereingriff, wenn überhaupt.
Automatisierungssteuerung System
- Vorteile der industriellen Steuerungskonvergenz
- Industrielle Schalttafeln verstehen
- 8 wichtige Tipps zur Verbesserung der Spankontrolle beim Bohren
- Werkzeugstabilitätslösung für Tieflochbohren
- Was Sie über das Erodieren von Löchern wissen müssen
- Prinzipien des Lochbohrens EDM
- Was ist so schwer am Tieflochbohren?
- Allgemeine Tipps für die Bohrbearbeitung
- SPS vs. DCS
- Verschiedene Arten des Bohrmaschinenbetriebs