AMRs zeigen ihr Zeug während einer Pandemie, über
hinaus
Hersteller fordern Vielseitigkeit bei sich ändernden Anforderungen
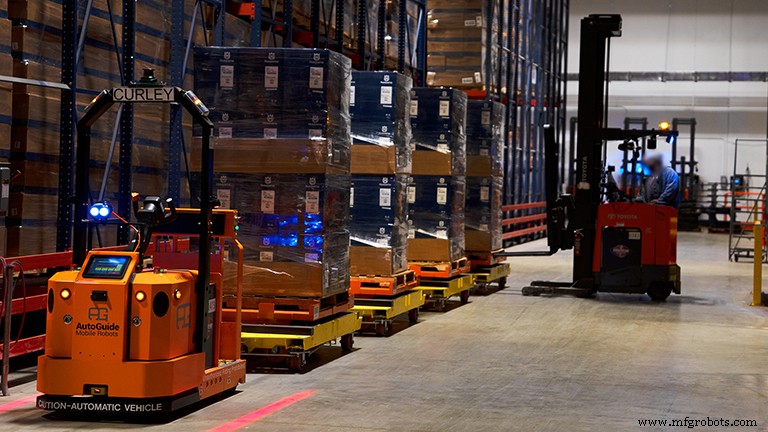
Im August hatte Rob Sullivan eine Installation für zwei seiner autonomen mobilen Roboter im Innovationszentrum von Deutsche Post DHL Group in Troisdorf, Deutschland, geplant. Aufgrund der Reisebeschränkungen von den USA nach Europa aufgrund der Coronavirus-Pandemie konnte Sullivans Installationstechniker jedoch nicht nach Deutschland fliegen, um bei der Arbeit zu helfen.
In einer Lösung des 21. Jahrhunderts führte Sullivans Team bei AutoGuide Mobile Robots die Installation also virtuell durch.
„Nach reiflicher Überlegung entschieden wir, dass die beste Vorgehensweise darin bestand, unseren lokalen (deutschen) Systemintegrator ST-IR (ST Integration &Robots) mit einem tragbaren Headset von RealWear zu schulen“, schrieb Sullivan, CEO von AutoGuide Mobile Robots auf LinkedIn, ein Beitrag, den Smart Manufacturing verifiziert hat. „In virtueller Zusammenarbeit mit ST-IR installierten wir einen AutoGuide MAX-N Pallet Stacker und MAX-N Tugger in der ST-IR-Anlage, um sie in der Implementierung zu schulen.“
Die Leute von ST-IR brachten dann das Wissen, das sie von AutoGuide und den beiden autonomen mobilen Robotern (AMRs) erworben hatten, zu DHL, wo die deutschen Integratoren den Schlepper und den Palettenstapler erfolgreich installieren konnten – mit virtueller Unterstützung durch AutoGuide-Techniker aus den USA Das ST-IR-Team konnte die Installation in wenigen Tagen durchführen, ohne den Zeitplan des Projekts zu beeinträchtigen.
Sullivan und sein Team erhielten auch virtuelles Feedback.
„Ich kann absolut bestätigen, dass wir seitens ST-IR glücklich und stolz auf die Installation sind und eine tolle Zeit bei DHL hatten“, Christoph Leutner, General Manager of Operations bei ST-IR, einem Full-Service-Integrator für Produktions- basierter Robotik, hat Sullivans LinkedIn-Beitrag kommentiert.
Während AutoGuide einen Integrator für die Remote-Installation im Ausland einsetzte, können die Techniker von AutoGuide Hersteller in den USA direkt unterstützen.
Michael Fleming, ein Systemintegrator mit jahrzehntelanger Erfahrung, sagte, dass ein Systemintegrator optional ist, da AMRs so konzipiert und konstruiert sind, dass sie einfach und schnell zu installieren und praktisch zu rekonfigurieren sind, wenn sich die Anforderungen einer Industrieanlage ändern.
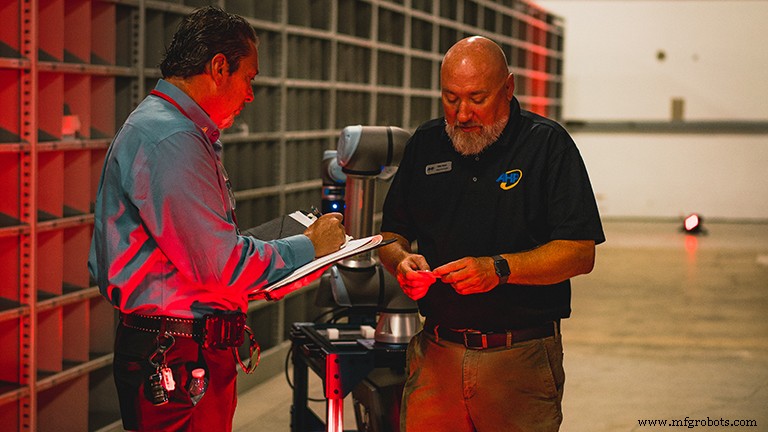
„AMRs konzentrieren sich darauf, dass der Benutzer/Eigentümer sie selbst programmieren, anpassen und integrieren kann, während die Hersteller von AGVs (Automated Guided Vehicles) dies in der Regel für den Kunden tun“, sagte Fleming, globaler Produktmanager für AMRs und AGVs für Systemintegrator MHS.
Während AMRs und AGVs einige der gleichen Aufgaben erledigen können, von denen sich viele darauf konzentrieren, Material von einem Ort zum anderen zu bewegen, gibt es andere Unterschiede zwischen den beiden Technologien.
„Der größte Unterschied besteht in der Denkweise, dass der AMR dezentralisiert ist und keinen Flottenmanager benötigt“, fügte er hinzu. „Innerhalb der letzten zwei Jahre haben AMR-Hersteller damit begonnen, einen Flottenmanager anzubieten, genau aus dem Grund, aus dem AGVs schon immer einen Flottenmanager hatten.“
Das hat mit der Anzahl autonomer Fahrzeuge zu tun, die an einem Ort unterwegs sind. Mit zunehmender Zahl verfügt das Unternehmen schließlich über eine Flotte, und die Verwaltung dieser Flotte wird zu einer Notwendigkeit.
„Da die Flottengröße wächst und die anvisierten Aufgaben deterministischer Natur sind [die Aufgaben müssen innerhalb eines bestimmten Zeitrahmens konsequent den ganzen Tag über ausgeführt werden], wird die Notwendigkeit eines effizienten Verkehrsmanagements und Auftragszuweisungsmanagements von den AMR-Herstellern erkannt“, so Fleming gesagt.
Es gibt weitere Unterschiede zwischen AGVs, die erstmals in den 1950er Jahren erfunden wurden, und AMRs, die es seit etwa einem Jahrzehnt gibt, sagte er.
„AMRs neigen dazu, ihre Steuerungen im Fahrzeug selbst zu dezentralisieren, was sie oft teurer macht“, sagte Fleming. Mit anderen Worten:„Es gibt viel mehr Intelligenz im Fahrzeug selbst.“
Diese Intelligenz manifestiert sich auf viele Arten, einschließlich der Navigation. Wenn ein AGV auf ein Hindernis trifft, bleibt es normalerweise stehen, bis jemand das Objekt aus dem Weg räumt. Ein AMR hingegen navigiert um ein Hindernis herum oder wählt einen anderen Weg, um dorthin zu gelangen, wo er hin muss.
Der Bedarf an dieser Art von Flexibilität veranlasste eine Unternehmerin, vor mehr als sechs Jahren ihr AMR-Unternehmen zu gründen.
Programmiere den Roboter per Drag-and-Drop
„Wir haben das Unternehmen gegründet, das sich auf Probleme des Arbeitskräftemangels und Flexibilitätsprobleme mit der aktuellen Automatisierungstechnologie konzentrierte“, sagte Melonee Wise, CEO von Fetch Robotics. „Das Problem, auf dessen Lösung wir uns konzentrierten, war die Bereitstellung flexibler Warenbewegungen, sei es eine Lieferung am Band oder eine Just-in-Time-Lieferung oder von Arbeitsstation zu Arbeitsstation.

„Eines der Dinge, die wir von Fertigungsingenieuren oder Verfahrenstechnikern gehört haben, ist, dass die Einrichtung eines Großteils der vorhandenen Automatisierungstechnik sehr lange gedauert hat. Es war sehr wartungsintensiv. Es hat viel Installation gekostet. Und es war sehr schwer, sich zu ändern“, sagte sie.
„Als sie also die Linie aufgrund von Saisonalität oder was auch immer ändern wollten, war es sehr schwierig, all diese Änderungen vorzunehmen, und es erforderte auch viel IT-Support vor Ort.“
Fetch macht:eine Reihe von Robotern für die automatisierte Materialhandhabung und automatisierte Datenerfassung; Plattformen für Robotikforschung; eine Plattform für kommerzielle Roboter; und Partner-Desinfektionsroboter, die die AMR-Basis von Fetch mit der Desinfektionstechnologie eines Industriepartners verwenden.
Nachdem ein Fetch-Kunde seinen AMR ausgepackt hat, fährt er damit durch seine Einrichtung, um eine Karte zu erstellen. Dann zeichnet er die Wege, die der Roboter nehmen soll, auf die Karte. Er programmiert den Roboter mit einem Drag-and-Drop-Menü mit Arbeitsablaufanweisungen. Alle diese Schritte werden aufgrund der Pandemie von einem Fetch-Anwendungstechniker aus der Ferne unterstützt.
Nachfolgende Interaktionen mit dem AMR erfolgen über Touchscreen, Tablet oder Scan-Pistole.
„Wir haben viele Komponenten gebaut, die die Integration in die Fabrik sehr … einfach in die feste Automatisierung zu integrieren machen, weil wir [nur] ein Teil der Automatisierungsgeschichte sind“, sagte Wise. „Wir verbinden und integrieren mit Management-Execution-Systemen, mit der physischen Automatisierung und mit SPS. Wir verbinden uns mit Handscannern, manchmal mit Sprachsystemen, je nachdem, was der Kunde von uns integrieren möchte.“
Wises Blick auf die gesamte Automatisierung in einer Fabrik und die Aufgabe, einen Teil dieses Gesamtbildes zu integrieren, stammen möglicherweise aus ihrer früheren Arbeit als eine der Kernentwicklerinnen für ROS oder Robot Operating System, ein Betriebssystem mit einer zusätzlichen Ebene für Visualisierung und Simulation .
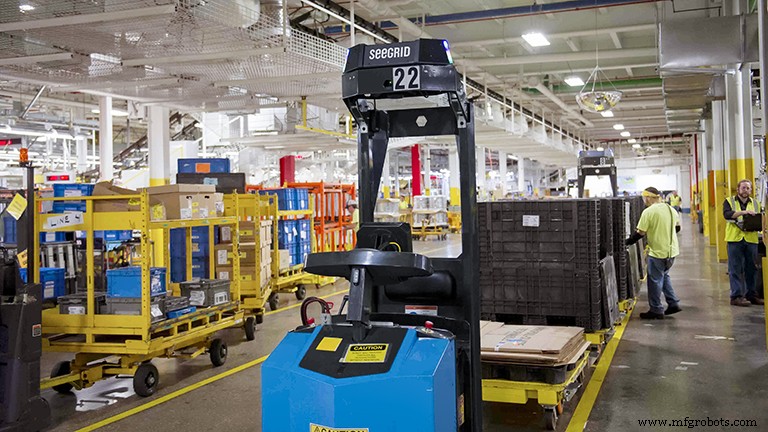
Abrufroboter verwenden einige ROS, haben aber ein Linux-basiertes Betriebssystem.
Für das Flottenmanagement befindet sich die FetchCore-Robotiksoftware in der Cloud und bietet Analysen, Planung, Roboterkonfiguration sowie Aufgaben- und Workflow-Management.
Zu den Aufgaben, die die AMRs von Fetch in Industrieanlagen erledigen, gehören:
- Bewegen von teilweise zusammengebauten Geschirrspülern zu einem Montageband zur Fertigstellung;
- Lieferung von gekitten Bootsmotorteilen;
- Versenden elektronischer Geräte in einer Rücknahmeeinrichtung von der Reparaturstation zum Standort des Qualitätssicherungstechnikers;
- Bestandsaufnahme von RFID-Tags aus Stahl- und Aluminiumrohren über ein mit Lesegeräten ausgestattetes AMR und
- Schieben montierter Elektronikeinheiten auf ein Förderband zum Verpacken.
Große Räume erfordern AMRs
Die AutoGuide-Roboter von Sullivan bestehen aus einem Basis-AMR mit kundenspezifischen Adaptern, einschließlich Schlepper, Palettenstapler und Hochregalstapler.
„Genau wie ein Roboter, an dem man einen Endeffektor hat“, sagte er in einem Interview mit Smart Manufacturing. „Sie würden einen Roboter nicht nur für eine Anwendung bauen. Sie bauen einen Roboter und setzen verschiedene Endeffektoren darauf. So haben wir das gebaut. Ein Roboter mit Adaptern, die Endeffektoren entsprechen.“
Ein Schlepper, den er an einen Konsumgüterhersteller in Arkansas verkauft hat, arbeitet in einer 800.000 Quadratfuß großen Fabrik und einem Lagerhaus mit einer 4-prozentigen Steigung zwischen den Fertigungs- und Lagerbereichen.
Es befördert jeden Tag 200.000 Pfund Waren.
„Aufgrund der Entfernungen und der Kosten, die für den Einbau dieser magnetisierten Struktur erforderlich sind, wollten sie kein herkömmliches AGV verwenden“, sagte Sullivan. Neuere AGVs verwenden anstelle von eingebetteten Drähten, wie frühere Modelle verwendet wurden, Magnetbänder auf Böden, um zu navigieren.
„Jede große Einrichtung – ob ein Distributionszentrum oder ein mit der Fertigung verbundenes Lagerhaus – würde teure und zeitaufwändige Infrastrukturänderungen erfordern, um die dauerhaften Drähte, Magnetstreifen oder im Boden eingebetteten Sensoren zu installieren“, sagte er.
„Wenn sich die Prozesse eines Unternehmens ändern, muss die Anlage erneut aktualisiert werden. Sie sind einfach nicht praktisch oder kosteneffektiv in Einrichtungen jeder Größe.“
Navigieren mit 3D-Vision
Die Roboter von Seegrid unterscheiden sich durch ihren Namen – Vision-Guided Robots (VGVs) vs. AMRs – und durch ihre Navigation.
„Wir verwenden ganz einzigartig auf dem Markt Kameras für unsere Navigation, und wir haben festgestellt, dass dies die zuverlässigste Navigation im AMR-Bereich ist“, sagte Jeff Christensen, VP of Product.
Die 10 Kameras der beiden VGV-Modelle von Seegrid – ein Schlepper und ein Hubwagen – arbeiten in fünf stereoskopischen Paaren und erfassen hemisphärische Sichtdaten. Die Software des VGV findet dann heraus, worauf es in der Umgebung ankommt.
Diese große Menge an Daten macht Routenänderungen möglich, während die Produktion weiterläuft, „und das kann sonst niemand“, beteuert Christensen.
„Fertigung, Lagerhaltung und Vertrieb sind hochdynamische Umgebungen, und um unter solchen realen Bedingungen zuverlässig zu navigieren, ist es viel besser, weit mehr Daten zu sammeln, als Sie möglicherweise verarbeiten können, und dann die Software herausfinden zu lassen, was wichtig ist die Umgebung um Sie herum, anstatt Ihre Sicht einzuschränken und dann zu versuchen, von dort nach oben zu extrapolieren und zu erraten, was sich um Sie herum befindet“, sagte er beim Vergleich echter 3D-Vision-Navigation mit laserbasierter Führung mit LiDAR.
Die häufigste Aufgabe für die Roboter von Seegrid in der Fertigung ist die Lieferung von Teilen an eine Linie, und ihr wahres Wertversprechen kommt in Werken zum Tragen, die mit der Nachfrage nach ihrem Produkt nicht Schritt halten können.
Raus aus den Kohleminen und rein in die Fabriken
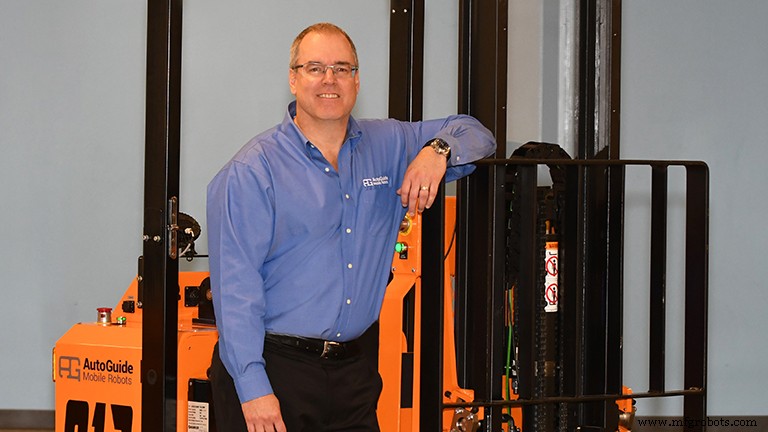
Während Roboter häufig dafür verantwortlich gemacht werden, amerikanische Jobs zu übernehmen, hat AutoGuide Mobile Robots nicht nur Jobs geschaffen, um ihre Roboter zu installieren und zu warten, sondern einige dieser Jobs auch mit umgeschulten Bergleuten besetzt.
AutoGuide und sein führender Integrationspartner Heartland Automation stellten 25 ehemalige Kohlebergleute ein, die am Haas eKentucky Advanced Manufacturing Institute (eKAMI) ausgebildet wurden.
eKAMI befindet sich nur wenige Kilometer von den Produktionsstätten der Unternehmen in Kentucky entfernt und wurde 2017 eingeführt.
eKAMI-Studenten nehmen an beschleunigten Programmen für computergestützte numerische Steuerungsmaschinen für die Robotik, Luft- und Raumfahrt, Medizin und andere fortgeschrittene Fertigungsindustrien teil.
„Die Suche nach qualifiziertem Personal für Fertigung und Installation kann äußerst schwierig sein, daher waren wir begeistert, eine Ressource wie eKAMI zu finden“, sagte Rob Sullivan, CEO von AutoGuide. „Wir bekommen nicht nur fleißige und hochqualifizierte Techniker, sondern sie bekommen Jobs, von denen sie wahrscheinlich nicht einmal wussten, dass sie für sie möglich sind, während sie in den Kohleminen arbeiten.“
Automatisierungssteuerung System
- Hubschrauber
- Sieben Möglichkeiten, Mitarbeiter in der Lieferkette während der Pandemie zu rekrutieren
- Wie die Automatisierung von Kundenaufträgen während der Pandemie für Stabilität sorgen kann
- Wie Lieferketten die nächste Pandemiewelle überstehen können
- Wie eine große Lebensmittellieferkette während der Pandemie die Kontrolle übernahm
- Fünf Möglichkeiten, während der Pandemie in Wachstum zu investieren
- Vier Schritte zum Schutz von Vertragsangestellten während der Pandemie
- Fünf Möglichkeiten, während des Cyber-Wochenendes mit großen Einzelhändlern zu konkurrieren
- Aufbau der Widerstandsfähigkeit der Lebensmittelindustrie über die Pandemie hinaus
- Kontinuierliche Verbesserung für Mitarbeiterbindung und Wachstum während eines Arbeitskräftemangels