Schwefeldotiertes alkyliertes Graphenoxid als Hochleistungsschmieradditiv
Zusammenfassung
Schwefeldotiertes Graphenoxid (SA-GO), hergestellt durch Sulfurierung und Alkylierung von Graphenoxid, wird als effizientes grünes Antiverschleißadditiv für raue Betriebsbedingungen von Motoren eingesetzt. Eine Röntgenphotoelektronenspektroskopie-Analyse zeigt, dass der Schwefelgehalt von Octadecylamin-modifiziertem SA-GO (Sulfurierung folgt Alkylierung) um das 79-fache im Vergleich zu dem umgekehrten Prozess, bei dem die Alkylierung auf die Sulfurierung folgt, erhöht ist, was darauf hindeutet, dass der Herstellungsweg ein Schlüsselfaktor des Sulfurierungsprozesses ist. Der höhere Schwefelgehalt und die –C–S–C–-Schwefelbindungskonstitution führen zu einer besseren Schmierwirkung, während die Untersuchung der Kettenlänge der Alkylierungsmodifikation und der Konzentration des alkylierten Schwefel-dotierten Graphenoxids darauf hindeutet, dass das Octylamin-modifizierte SA-GO einen kleineren Durchmesser aufweist der Abnutzungsnarbe im Konzentrationsbereich zwischen 1 × 10 −4 und 2,5 × 10 −4 Gew.%. Der abnehmende Prozentsatz des Verschleißnarbendurchmessers beträgt 43,2 % in 928 Schmieröl und 17,2 % in PAO4-Öl, während das mit Octylamin modifizierte SA-GO mit den Konzentrationen 2,5 × 10 −4 . angewendet wird Gew.-% in PAO4 und 1 × 10 −4 Gew.-% in 928 Öl bzw. Der Schwefelgehalt in Ölproben beträgt nur 0,006~0,001 Gew.-%, was viel niedriger ist als der von ILSAC empfohlene Schwefelgehalt von 0,5 Gew.-%. Die Forschungsarbeit zeigt, dass das SA-GO-Additiv für die Verschmutzungsbehandlung geeigneter ist, die die wesentliche Reduzierung des Schwefelgehalts im Schmieröl unter der Prämisse einer Verbesserung der Schmierfähigkeit konzentriert.
Einführung
Organische Verschleißschutzadditive auf Schwefelbasis werden häufig bei der Anwendung von Schmierölen verwendet, um die Verschleißfestigkeit von Reibpaarungen unter extremem Druck zu fördern, bei denen die Ölmembran die beweglichen Teile nicht trennt, wie z. B. schwefelhaltiges Getriebeöl [1 ]und Poly-α-olefin [2]. Da der übermäßig aktive Schwefel in organischen Verbindungen den ternären Katalysator des Emissionsminderungssystems vergiften könnte, während er auf dem Kolbenring und der Zylinderwand wirkt, was zu einer ernsthaften Umweltverschmutzung führt, wird die kommende verbindliche Norm des International Lubricant Standardization and Approval Committee (ILSAC .) ) [3] fordert, dass der Schwefelgehalt des Schmieröls weniger als 0,5 Gew.-% betragen sollte, da der höhere Schwefelgehalt im Schmiermittel die Qualität der Motorabgase verschlechtern könnte [4]. Um das Problem zu lösen, werden viele Strategien, einschließlich organischer Reibungsmodifikatoren, wie schwefelfreie Alkylcyclen [5], Chinoliniumsalze [6] und Nanomaterial-Verschleißschutzadditive wie BN-codotiertes Graphen [7], SiC@ Graphen [8], zerknittertes Graphen [9] und Graphen-Nanoscroll [10] wurden entwickelt, um den Schwefelgehalt von Schmierölen zu reduzieren oder zu entfernen. Die oben genannten Entwicklungsmethoden benötigen jedoch noch lange Zeit, um die praktische Schmierwirkung, den Umweltfaktor, die Sicherheit und andere Aspekte zu überprüfen, um die tatsächlichen Anwendungsergebnisse endgültig zu bestätigen.
Dieses Papier konzentriert sich auf die Vorbereitung des schwefeldotierten Graphenoxids, um als effizientes Antiverschleißadditiv mit niedrigem Schwefelgehalt für raue Betriebsbedingungen bei hohen Temperaturen zu wirken. Basierend auf den Untersuchungen zur Herstellung von schwefeldotiertem Graphen konnten die einzigartigen Nanomaterialien durch die Reaktionen von Thioharnstoff [11], NaHSO3 . erhalten werden [12], K2 S2 O8 [13], Phenyldisulfid [14, 15], Schwefel [16], Na2 S [17], CS2 [18], P4 S10 [19], H2 S [20], SO2 [21], CS2 [21], Benzyldisulfid [22] und Graphenoxid unter hydrothermalen oder anderen einfachen Bedingungen. Nach dem Schwefeldotierungsprozess könnte schwefeldotiertes Graphenoxid die Verschleißschutzeigenschaften des Basisöls deutlich verbessern. Das wichtigste Merkmal des einzigartigen Anti-Verschleiß-Additivs ist das Schwefelelement, das in der Molekülstruktur von schwefeldotiertem Graphenoxid verankert wurde. Die Zugabe des schwefeldotierten Graphenoxids in Schmieröl würde gleichzeitig die Vorteile von schwefelhaltigen Anti-Verschleiß-Additiven beibehalten und den Schwefelgehalt auf ~ 1/1000 im Vergleich zu organischen Schwefel-Additiven reduzieren.
Ergebnisse und Diskussion
Die XPS-Analyse (Abb. 1) legt nahe, dass im schwefeldotierten Graphenoxid die vier Elemente Sauerstoff, Stickstoff, Kohlenstoff und Schwefel vorhanden sind. Zwei unterschiedliche Herstellungswege, die in der Forschung angewendet wurden, deuten darauf hin, dass die Modifizierungsmethode die chemische Zusammensetzung des schwefeldotierten alkylierten Graphenoxids erheblich beeinflussen würde.
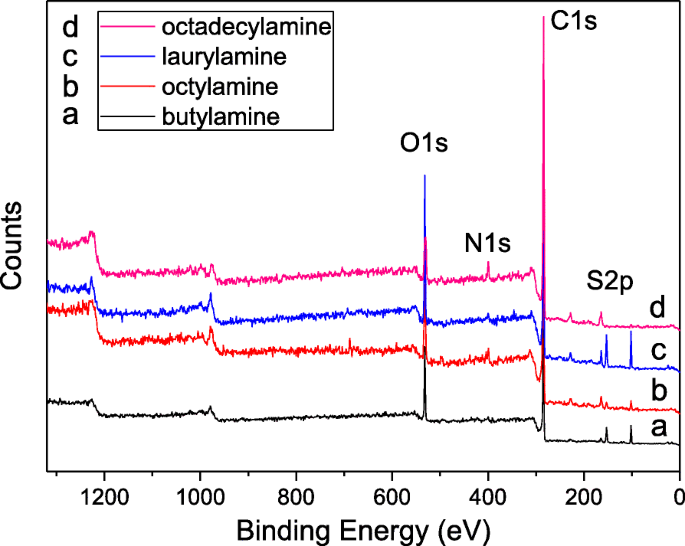
Die XPS-Übersicht des SA-GO, die durch die Reaktionen von Butylamin (a ), Octylamin (b ), Laurylamin (c ), Octadecylamin (d ) und das schwefeldotierte Graphenoxid (die Oxidationszeit des Graphenoxids beträgt 24 h)
SA-GO und AS-GO wurden von XPS untersucht, um die Schwefeldotierungseffizienz der Präparationswege zu bewerten. Im Vergleich zum Schwefelgehalt von AS-GO ist der Schwefeldotierungsprozess von SA-GO viel besser als der von AS-GO. Wie in Tabelle 1 gezeigt, ist der Schwefelgehalt von SA-GO (1,94–3,16 at%) ein paar Dutzend Mal höher als der von AS-GO (0,04–0,08 at%). Die Ergebnisse weisen auch darauf hin, dass die Alkylierung vor der Sulfurierung die aktiven Punkte auf dem Graphenoxid dramatisch reduzieren würde, was zu einer signifikanten Leistungsminderung der nachfolgenden Sulfurierung von AS-GO führt. Da der Schwefelgehalt von AS-GO im Bereich von 0,04–0,08 at% liegt, zeigt die Herstellung von AS-GO seltene Vorteile und Alkylamin-Selektivität der Schwefel-Dotierungsverfahrenseffizienz. Wie in Tabelle 1 gezeigt, ist der Schwefelgehalt von Octadecylamin-modifiziertem SA-GO gegenüber Octadecylamin-modifiziertem AS-GO um das 79-Fache erhöht.
Der Stickstoffgehalt wird auch durch die Herstellungswege von schwefeldotiertem Graphenoxid beeinflusst. Zuerst mit Alkylamin und dann mit P4 . modifiziert S10 , beträgt der Atomprozentsatz von Stickstoff in AS-GO nur 0,36–0,65 at%, was offensichtlich niedriger ist als der von SA-GO (3,42–3,83 at%). Der Stickstoff in SA-GO und AS-GO unterscheidet sich jedoch stark vom Stickstoff des Stickstoff-dotierenden Graphens. Der Stickstoff von SA-GO und AS-GO befindet sich hauptsächlich an den funktionellen Gruppen von Alkylamin, nicht in der Struktur von Graphen. Jedoch basierend auf der SA-GO hinzugefügten Menge von 1~5 × 10 –4 Gew.-% in Ölproben beträgt der Schwefelgehalt in Ölproben nur 0,006 ~ 0,001 Gew.-%, was viel weniger ist als der Schwefelgehaltsstandard von 0,5 Gew.-% von ILSAC [3].
Die Ergebnisse der Peakanpassung zeigen, dass der Bindungsgehalt im SA-GO stark unterschiedlich ist, nachdem schwefeldotiertes Graphenoxid mit Butylamin, Octylamin, Laurylamin und Octadecylamin reagiert hat. In der hochauflösenden S2p-Analyse von SA-GO (Abb. 2) sollten zwei Peaks, die bei 161,9 eV und 164,1 eV zentriert sind, S2p3/2 . zugeordnet werden und S2p1/2 , das sind die Peaks, die sich aus dem S2p-Spin-Bahn-Dublett der –C–S–C–-Bindung ergeben [11, 13]. Die S2p3/2 und S2p1/2 Bindungskonfigurationen können auf die Bildung von C=S- und C-S-Bindungen in der Struktur des SA-GO zurückgeführt werden [16]. Die anderen beiden Peaks bei etwa 165,2 eV und 168,1 eV können –C–SOx . zugeordnet werden –C–-Bindung, die hauptsächlich von Schwefeloxidspezies in SA-GO abgeleitet wird [15,16,17, 22]. Basierend auf den Peak-Fitting-Ergebnissen aus Abb. 2 werden –C–S–C– und –C–SOx –C–-Bindungskonfigurationen in SA-GO werden berechnet und in Tabelle 2 gezeigt. Nach der Sulfurierung und Alkylierung von GO (das GO wird durch Oxidation für 24 h hergestellt) werden die Atomprozente von –C–S–C– Bindung ist im SA-GO ziemlich ähnlich, dass Octylamin, Laurylamin und Octadecylamin als Reagens für die Alkylierung verwendet werden.
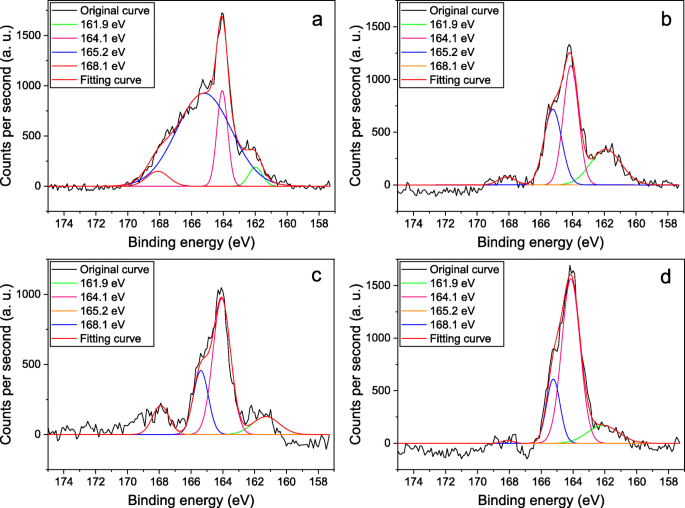
Die hochauflösende Schwefel (2p) XPS-Analyse des SA-GO, das durch die Reaktionen von Butylamin (a ), Octylamin (b ), Laurylamin (c ), Octadecylamin (d ) und das schwefeldotierte Graphenoxid (die Oxidationszeit des Graphenoxids beträgt 24 h)
Obwohl der Schwefelgehalt nach der Sulfurierung deutlich ansteigt, weist die –C–S–C–-Bindungskonfiguration auf die Bindung von Schwefel in der Molekülstruktur von Graphenoxid hin, und die –C–SOx –C–-Bindungskonfiguration wird auf die unvollständige Reduktionsreaktion bei der Sulfurierung zurückgeführt, während P4 S10 angewendet, um mit Graphenoxid zu reagieren. In der hochauflösenden Schwefel-XPS-Analyse zeigt das butylaminmodifizierte Graphenoxid den niedrigsten Gehalt an –C–S–C– unter den vier in dieser Arbeit verwendeten Alkylaminen. Die Ergebnisse zeigten, dass der nachfolgende Alkylierungsprozess die C-S-Bindungskonfigurationen beeinflussen könnte.
Die thermogravimetrische Analyse (TGA) wird angewendet, um die Alkylierungseffizienz der Reaktionen zwischen Butylamin (GO-C4), Octylamin (GO-C8), Laurylamin (GO-C12), Octadecylamin (GO-C18) und dem Schwefel- dotiertes Graphenoxid (die Oxidationszeit des Graphenoxids beträgt 24 h). Wie in Abb. 3 gezeigt, ist der Gewichtsverlust von GO-C12 (80,9 Gew.-%) und GO-C18 (73,9 Gew.-%) viel höher als der von GO-C4 (39,3 Gew.-%) und GO-C8 (42,6 Gew.-%). ) und weist darauf hin, dass der Gehalt an chemisch gepfropften organischen Verbindungen von GO-C12 und GO-C18 viel höher ist. Die gepfropften organischen Verbindungen von GO-C4 und GO-C8 sind jedoch sogar hoch, da der Gewichtsverlust von GO bei 700 °C nur 3,5 Gew.-% beträgt, was darauf hindeutet, dass in GO fast keine organischen Verbindungen vorhanden sind.
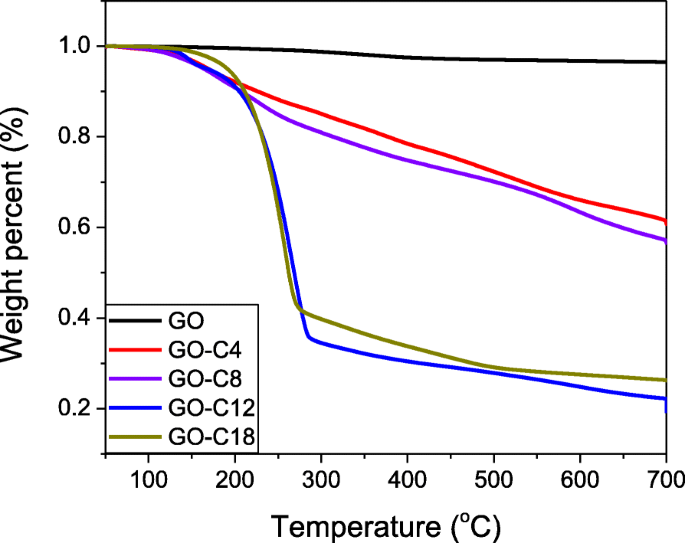
Die TGA-Analyse von SA-GO, die durch die Reaktionen von Butylamin (GO-C4), Octylamin (GO-C8), Laurylamin (GO-C12), Octadecylamin (GO-C18) und dem schwefeldotierten Graphenoxid ( die Oxidationszeit des Graphenoxids beträgt 24 h)
Die Alkylierung von SA-GO konnte auch durch die in Abb. 4 gezeigten ATR-FTIR-Spektren bestätigt werden. Starke Absorptionspeaks bei ~ 2848 cm −1 und ~ 2780 cm −1 werden der Streckschwingung der C–H-Bindungen von –CH3 . zugeordnet und –CH2 Gruppen, was mit den Ergebnissen von TGA übereinstimmt, dass das alkylierte schwefeldotierte Graphenoxid beträchtliche Mengen an organischer Substanz enthält. Der Peak zentriert bei ~ 1540 cm −1 repräsentiert die Schwingung ausserhalb der Ebene von –CH2 Gruppen- und asymmetrische Verformungsschwingung. Und der breite und intensive Absorptionspeak bei ~ 1050 cm −1 wird der Streckschwingung der –C-N-Bindung zugeschrieben, die die Amidobindung (CO-NH) zwischen dem Graphenoxid und den Alkylaminen bildet. Die Ergebnisse von ATR-FTIR (Abb. 4) zeigen, dass der Alkylierungsprozess für die Herstellung von alkyliertem schwefeldotiertem Graphenoxid effektiv ist.
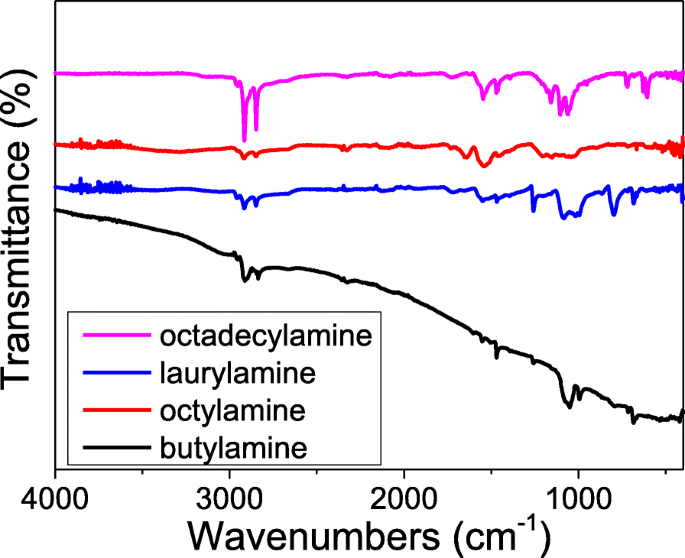
Die ATR-FTIR-Spektren des SA-GO, das durch die Reaktionen von Butylamin, Octylamin, Laurylamin, Octadecylamin und dem schwefeldotierten Graphenoxid hergestellt wird (die Oxidationszeit des Graphenoxids beträgt 24 Stunden)
Die TEM-Bilder und die Profilanalyse der typischen SA-GO-Nanostruktur sind in Abb. 5 gezeigt. Nach der Filtration wird das SA-GO in Abb. 5a gestapelt; eine blattförmige Graphen-Nanostruktur konnte jedoch immer noch durch eine gestrichelte Linie abgegrenzt werden. Abbildung 5b ist das hochauflösende TEM-Bild der in Abbildung 5a hervorgehobenen quadratischen Zone. Gemäß der Profilanalyse (Abb. 5e) betragen die in Abb. 5b gemessenen fünf Schichten 1,452 nm, und somit beträgt der durchschnittliche Schichtabstand 0,363 nm, was stark mit dem Interplanarabstand von Graphit übereinstimmt (JCPDS-Karte Nr. 75- 1621). Selected Area Electron Diffraction (SAED)-Muster (Abb. 5d) von SA-GO sind fast Beugungsringe von Graphit [23]. Gemäß der JCPDS-Karte Nr. 75-1621 sollte der innere Beugungsring der (002)-Kristallebene und der äußere der (101)-Ebene zugeordnet werden, was auf die Graphen-Natur des SA-GO hindeutet.
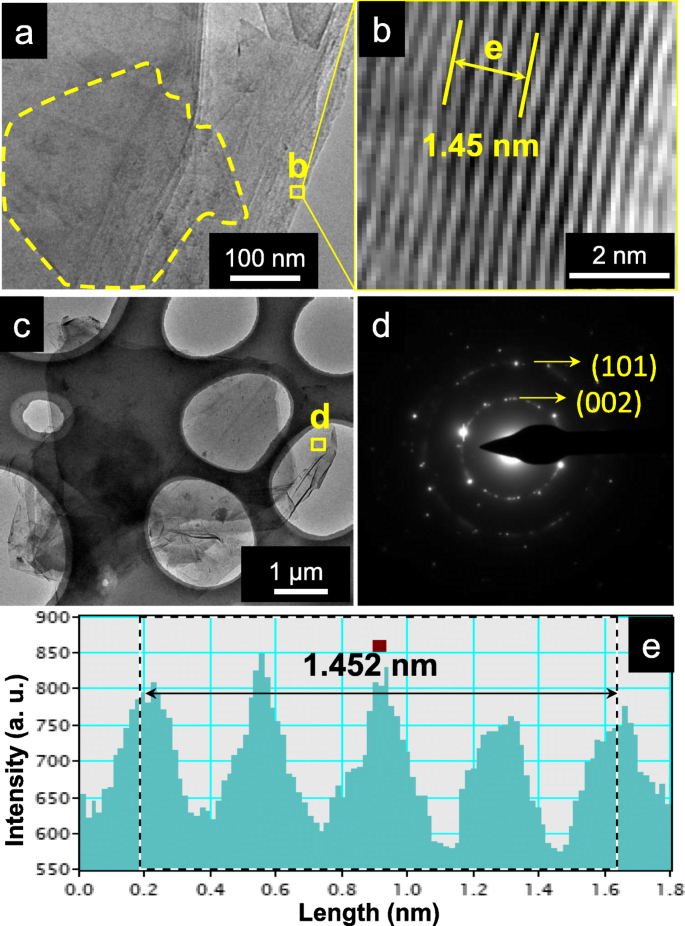
Die TEM-Analyse von SA-GO (die durch die Reaktionen von Octadecylamin und dem schwefeldotierten Graphenoxid hergestellt wird; die Oxidationszeit des Graphenoxids beträgt 24 h). Einschließlich des gestapelten SA-GO (a ), das hochauflösende TEM-Bild der quadratischen Zone, die in a . markiert ist (b ), das verstreute SA-GO (c ), das SAED-Beugungsmuster der quadratischen Zone, die in c . markiert ist (d ) und die Kristallraumanalyse der in b markierten Position (e)
Gemäß der Raman-Analyse des SA-GO (Abb. 6), das durch die Reaktionen von Octadecylamin und dem schwefeldotierten Graphenoxid hergestellt wird (die Oxidationszeit des Graphenoxids beträgt 24 h), sind die beiden Peaks um 1350 und zentriert 1584 cm −1 könnte der D- und G-Bande von SA-GO zugeschrieben werden, während der Peak bei 2690 cm −1 wird den 2D-Bändern des SA-GO zugeordnet [23, 24]. Der Raman-Peak bei etwa 2440 cm −1 wird als C [25] oder D + D″ [26] Band von Graphen vorgeschlagen und konnte in den Raman-Spektren in Veröffentlichungen [27, 28] gesehen werden. Das ID /IG Wert von GO ist 0,986, was etwas niedriger ist als der von SA-GO (ID /IG = 1.05) und zeigt an, dass sich die Graphenstruktur in den Modifikationsreaktionen nicht signifikant verändert hat.
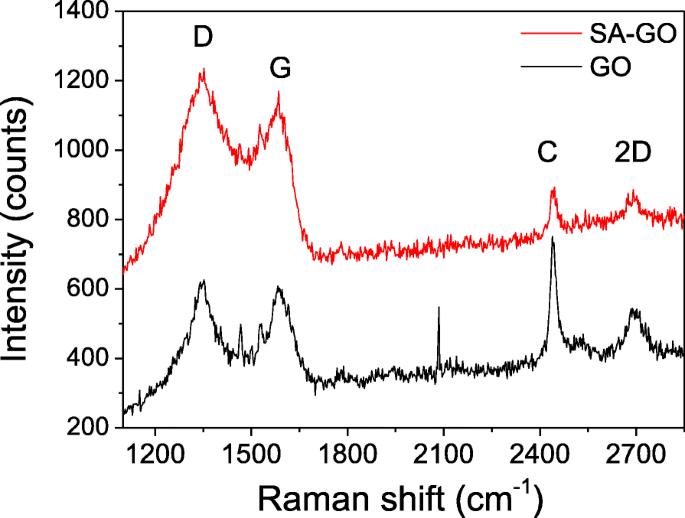
Das typische Raman-Spektrum von SA-GO (das durch die Reaktionen von Octadecylamin und dem schwefeldotierten Graphenoxid hergestellt wird; die Oxidationszeit des Graphenoxids beträgt 24 h) und GO (die Oxidationszeit des Graphenoxids beträgt 24 h)
Das Grundöl von 928 Luftfahrt-Schmieröl ist hauptsächlich Poly-α-Olefin, PAO, das sind gesättigte Alkane mit ~ 30 Kohlenstoffatomen. In diesem Artikel werden das 928 Luftfahrt-Schmieröl und PAO4 (die kinematische Viskosität beträgt ~ 4 mm 2 /s bei 100°C) als Substrat verwendet, und dann wird den Ölen jeweils das alkylierte Schwefel-dotierte Graphenoxid zugesetzt, um deren Dispergiereigenschaften zu untersuchen. Wie in Abb. 7 gezeigt, zeigten die Fotos von SA-GO-Ölproben, dass die Farbe der Ölproben mit zunehmender SA-GO-Menge allmählich dunkler wurde. Dies sollte die zunehmende Absorption von sichtbarem Licht sein, da das SA-GO den Ölen zugesetzt wurde. Auf dem Boden der Küvetten befindet sich jedoch ein wenig Sediment, selbst wenn das Graphenoxid chemisch modifiziert wurde, um die Dispersität zu verbessern. Wie in Abb. 7b und d gezeigt, ist die Farbe der Ölproben hellgelb im Vergleich zur Farbe der PAO4-Ölproben, da die Farbe des Schmieröls 928 hellgelb ist. Offensichtlich könnte die Konzentration des SA-GO die Absorptionsintensität erheblich beeinflussen.
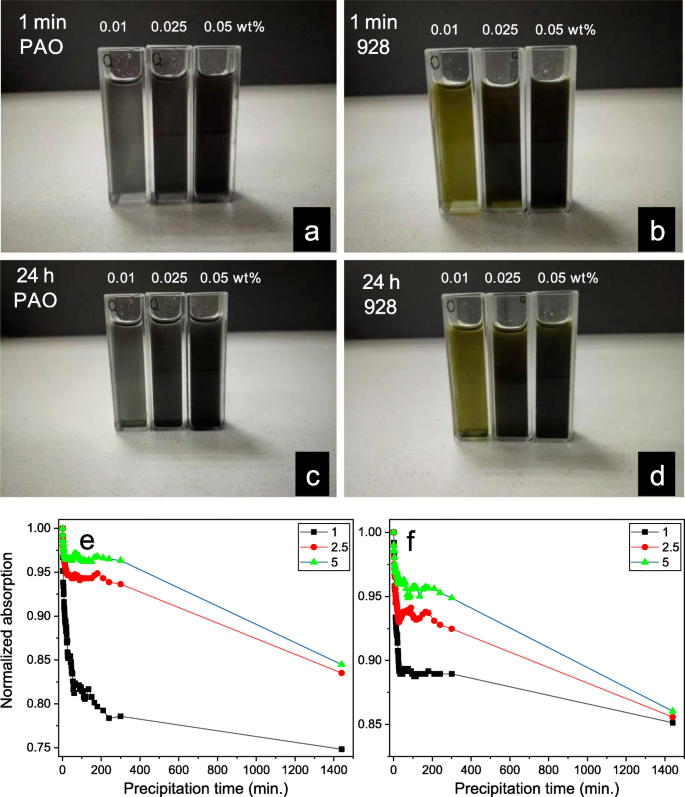
Die optischen Fotografien des SA-GO (das durch die Reaktionen von Octadecylamin und dem schwefeldotierten Graphenoxid hergestellt wird; die Oxidationszeit des Graphenoxids beträgt 24 Stunden), die in dem PAO4-Grundöl (a ) und das 928 Luftfahrt-Schmieröl (b ) und das PAO4 (c ) und 928 (d ) Ölprobenstillstand für jeweils 24 h; die normalisierte Adsorption von SA-GO in PAO4 (e ) und 928 (f ) Ölproben (a –d , untersucht mit einem UV-Vis-Spektrophotometer) mit der Konzentration von SA-GO ist 1, 2,5 und 5 × 10 −4 Gew.-% innerhalb von 1440 min
Um die Dispersität der SA-GO-Ölproben quantitativ zu analysieren, wird das UV-Vis-Spektrophotometer verwendet, um die Absorption der SA-GO-Ölproben zu testen. Die Ergebnisse sind in Abb. 7e und f dargestellt. Nach einer Fällung von 24 h (1440 min) ist die normalisierte Absorption der SA-GO-Ölproben verringert. Interessanterweise ist die Verringerung der normalisierten Absorption von Ölproben mit hoher Konzentration relativ langsamer als die von Ölproben mit niedriger Konzentration. Das Phänomen weist auf die wesentlich verbesserte Dispersität des SA-GO hin, die selbst unter den Bedingungen einer relativ hohen Konzentration keine offensichtliche Aggregation zeigte.
Aus der abnehmenden Tendenz der Kurve in Fig. 7e und f könnte ein Verfahren zum Berechnen der Steigung der linearen Anpassungskurve des linearen Schwanzendes der normalisierten Adsorption des SA-GO die Dispersität quantitativ demonstrieren. Wie in Tabelle 3 gezeigt, zeigen die Berechnungsergebnisse, dass die abnehmende Tendenz von SA-GO-Ölproben mit hoher Konzentration höher ist als die von SA-GO-Ölproben mit niedriger Konzentration, obwohl die Verringerung der normalisierten Absorption von Ölproben mit hoher Konzentration relativ langsamer ist. der Ölproben niedriger Konzentration. Die Dispersionsanalyse legt nahe, dass das SA-GO nach chemischer Modifizierung selbst bei relativ hoher Konzentration eine ausgezeichnete Dispersität aufweist; die hochkonzentrierten SA-GO-Ölproben haben jedoch langfristig eine stärker abnehmende Tendenz. Die tribologischen Eigenschaften von SA-GO-Ölproben werden durch Vier-Kugel-Tester gemessen, um die Schmierungsverstärkungswirkung von SA-GO zu bewerten, das als Schmiermitteladditiv verwendet wurde. Wie im Abschnitt „Methode“ erwähnt, wird der Durchmesser der Verschleißnarben nach Abschluss des Tests gemessen und die maximale Nichtfresslast (P B ) Wert wird ebenfalls erfasst. Der durchschnittliche Durchmesser der Verschleißnarben bei der Anwendung von SA-GO als Schmieradditiv ist in Abb. 8 dargestellt.
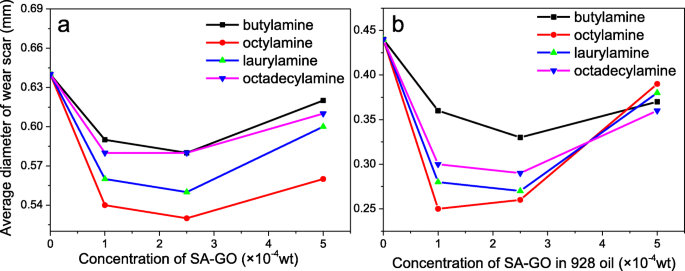
Der durchschnittliche Durchmesser der Verschleißnarbe beim Auftragen des SA-GO (hergestellt aus schwefeldotiertem GO und Butylamin, Octylamin, Laurylamin und Octadecylamin; die Oxidationszeit des GO beträgt 24 h) als Schmieradditiv in PAO4 (a ) und 928 (b ) Öle
Erstens ist der durchschnittliche Durchmesser von SA-GO 928-Ölproben viel kleiner als der von SA-GO-Dispersion in PAO4-Basisöl. Dieses Phänomen könnte auf das Schmieröl 928 zurückzuführen sein, das organische Phosphat-Verschleißschutzadditive enthält, die das Verschleißvolumen beim Gleiten effektiv reduzieren könnten [29]. Das phosphathaltige Verschleißschutzadditiv könnte mit den Stahlreibungspaaren reagieren, um einen Tribofilm zu erzeugen, der Eisenphosphat, Eisenphosphat und andere phosphathaltige Verbindungen unter einer Grenzschmierung enthält.
Zweitens spielt der Modifizierungsweg eine wichtige Rolle für das Antiverschleißverhalten von SA-GO-Ölproben [30, 31]. Das Octylamin-modifizierte SA-GO zeigt unter den Ölproben, die sowohl PAO4- als auch 928-Schmieröle enthalten, bessere Schmiereigenschaften. Die Ergebnisse stimmen mit der in Abb. 4 gezeigten Analyse von TGA und der molekularen Struktur von PAO4 oder dem Grundöl des 928-Schmieröls überein. Laut TGA beträgt der Gewichtsverlust von SA-GO (modifiziert durch Octylamin) nur etwa die Hälfte im Vergleich zu SA-GO modifiziert durch Laurylamin und Octadecylamin, was die Menge an schwefeldotiertem Graphen in den Laurylamin- und Octadecylamin-modifizierten bedeutet SA-GO ist nur etwa halb so groß wie mit Octylamin modifiziertes SA-GO. Da die hinzugefügte Menge an SA-GO nur 1, 2,5 und 5 × 10 −4 . beträgt Gew.%, führt der ernsthafte Mangel an schwefeldotiertem Graphen im Laurylamin- und Octadecylamin-modifizierten SA-GO zu einer Verschlechterung ihrer Antiverschleißfähigkeit. Andererseits weist das mit Butylamin modifizierte SA-GO gemäß der TGA-Analyse einen ähnlichen Gehalt an schwefeldotiertem Graphen wie das durch Octylamin modifizierte SA-GO auf. Die Dispersität von Butylamin-modifiziertem SA-GO ist jedoch intrinsisch geringer als die von Octylamin-modifiziertem SA-GO, da die alkylierte Kohlenstoffkette von Octylamin-modifiziertem SA-GO ziemlich nahe an der Seitenkette von PAO4 oder dem Grundöl des 928-Schmiermittels liegt Öl [32].
Drittens könnte die Konzentration von SA-GO in den Ölproben die Verschleißfestigkeit beeinträchtigen. Viele Untersuchungen haben bewiesen, dass bei einer zu hohen Konzentration von Graphen und/oder seinen Derivaten das Graphen (oder die Derivate) normalerweise dazu neigt, in Flüssigkeit zu aggregieren. Bei Schmieranwendungen konnte das aggregierte Graphen nicht als wirksames Schmieradditiv verwendet werden, sogar schädlich für die tribologischen Eigenschaften. In diesem Fall beträgt die SA-GO-Konzentration 5 × 10 –4 Gew.-% ist zu hoch für Schmieranwendungen sowohl in 928- als auch in PAO4-Ölen aufgrund der abnormalen Zunahme des Verschleißnarbendurchmessers. Somit beträgt die SA-GO (modifiziert durch Octylamin) Konzentrationen von 1 und 2.5 × 10 −4 Gew.-% wurden in der Forschung bestätigt, die eine bessere Schmierwirkung in 928 Schmieröl (der Verschleißnarbendurchmesser beträgt 0,25 mm) bzw. PAO4-Öl (der Verschleißspurdurchmesser beträgt 0,53 mm) haben. Im Vergleich zu reinem 928-Schmieröl und PAO4-Öl beträgt die Abnahme des Verschleißnarbendurchmessers 43,2 % bzw. 17,2 % beim 928-Schmieröl und PAO4-Öl. Die Schmierwirkung von SA-GO im 928-Schmieröl ist viel besser als die im PAO4-Grundöl, was die hervorragende synergistische Schmierwirkung von SA-GO im 928-Schmieröl demonstriert.
Die maximale Belastung ohne Festfressen (P B )-Wert des SA-GO (hergestellt aus schwefeldotiertem GO und Octylamin) in PAO4 (Abb. 9a) und 928 (Abb. 9b) Schmierölen wurde mit dem Vierkugeltester bestimmt. Wie in Abb. 9a gezeigt, ist das P B Die Verbesserung des SA-GO ist ziemlich beträchtlich und hat einen Anstieg von 55,6% für den P B Wert bei der Konzentration von 1 × 10 −4 Gew.% und 72,2% für P B Wert bei einer Konzentration von 5 × 10 −4 Gew.%. Die Ergebnisse von P B Wert legen nahe, dass die Ölmembranfestigkeit wesentlich verbessert wurde, seit SA-GO zu den PAO4-Grundölproben hinzugefügt wurde. Das P B Werte von SA-GO, hergestellt aus schwefeldotiertem GO, Butylamin (Zusatzdatei 1:Abbildung S2a), Laurylamin (Zusatzdatei 1:Abbildung S2b) und Octadecylamin (Zusatzdatei 1:Abbildung S2c) in PAO4 sind in SI gezeigt, was auf ähnliche Ergebnisse hindeutet, dass die höhere Konzentration von SA-GO in PAO4 hilfreich für die Förderung des maximalen Wertes der Nichtanfallsbelastung wäre.
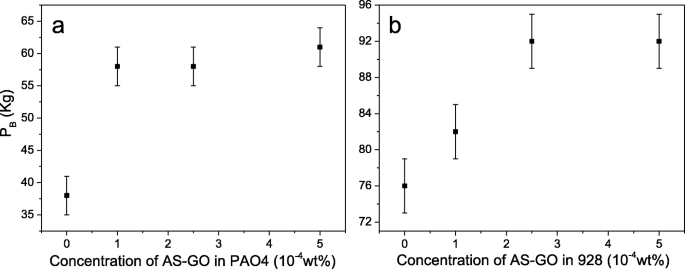
a , b Der maximale Non-Seizure Load (PB)-Wert, während SA-GO (hergestellt aus schwefeldotiertem GO und Octylamin, die Oxidationszeit des GO beträgt 24 h) als Schmieradditiv mit einer bestimmten Konzentration an PAO4 (a ) und 928 (b ) Öl
Das P B Wert von SA-GO (hergestellt aus schwefeldotiertem GO und Octylamin) in 928 Schmierölen (Abb. 9b) steigt auch mit steigender Konzentration von SA-GO bis 2,5 × 10 −4 Gew.%. Darüber hinaus wird SA-GO dem 928-Schmieröl zugesetzt, aber das P B der Wert der SA-GO-Ölprobe war bei der Konzentration von 5 × 10 −4 . unverändert Gew.%. Im Vergleich zu SA-GO, hergestellt aus schwefeldotiertem GO und Butylamin (Zusatzdatei 1:Abbildung S3a), Laurylamin (Zusatzdatei 1:Abbildung S3b) und Octadecylamin (Zusatzdatei 1:Abbildung S3c) im Schmieröl 928, der Butylamin-modifiziertes SA-GO hat einen relativ niedrigeren P B Wert (82 kg) bei einer Konzentration von 2.5 × 10 − 4 Gew.%. Die Laurylamin- und Octadecylamin-modifizierten SA-GO in 928 Schmieröl zeigen jedoch ähnliche P B (92 kg) mit dem Octylamin-modifizierten SA-GO. Das Phänomen legt nahe, dass die hinzugefügte Menge an SA-GO 2,5 × 10 –4 . betragen sollte Gew.-% zur Berücksichtigung des Aggregationseffekts, der Antiverschleißeigenschaften und des P B Wert.
Nach dem Reibungsgleiten zeigt die REM- und EDS-Analyse der Verschleißnarbe, dass der Schwefel von SA-GO wahrscheinlich eine Schlüsselrolle im reaktiven Schmierverhalten spielt, um einen schwefelhaltigen chemischen Grenzschmierfilm zu bilden. Wie in Abb. 10a (REM-Bild der Abnutzungsnarbe) und b (EDS-Spektrum von Abb. 10a, die Integrationsergebnisse der in Abb. 10a gezeigten Linienabtastung, die als gestrichelte Linie markiert ist) gezeigt, ist das EDS-Spektrum der Abnutzungsnarbe zeigt fünf Elemente, einschließlich Fe, O, C, Cr und S, die in der Verschleißnarbe vorhanden sind.
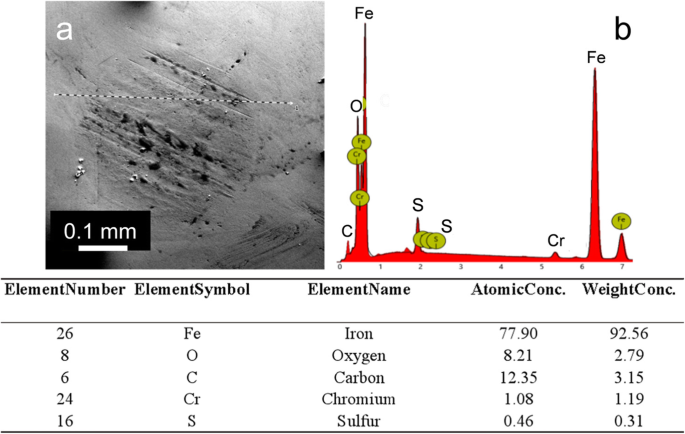
Das SEM-Bild (a ) und EDS-Elementaranalyse (b , die Integrationsergebnisse der Zeilenabtastung in a die als gestrichelte Linie markiert ist) der Verschleißnarbe, während das SA-GO (hergestellt aus schwefeldotiertem GO und Octylamin; die Oxidationszeit des GO beträgt 24 h und die Konzentration des SA-GO beträgt 0,025 Gew.-%) als Schmiermittelzusatz im 928 Schmieröl
Der Schwefelgehalt der Verschleißnarbe erreicht bis zu 0,46 at%, was viel höher ist als der der Verschleißnarbe des reinen 928, das als Schmiermittel verwendet wird (der Schwefelgehalt liegt bei ~ 0 %, Zusatzdatei 1:Abbildung S4). Somit hängt der höhere Schwefelgehalt im Tribofilm stark mit dem durchschnittlichen Durchmesser der Verschleißnarbenanalyse, der Dispersionsstudie und der TGA-Analyse zusammen, was darauf hindeutet, dass die Antiverschleißeigenschaften den höheren Schwefelgehalt und den höheren Graphen-Gewichtsprozentsatz und die Dispersität begünstigen profitiert von der Kohlenstoffkettenlänge ähnlich der Seitenkette von Grundölen.
Schlussfolgerungen
Das SA-GO wird durch Sulfurierung und Alkylierung von Graphenoxid hergestellt. Basierend auf der XPS-Analyse folgt die Sulfurierung dem Alkylierungsweg (das Produkt ist SA-GO), der für die Schwefeldotierung von Graphenoxid viel besser ist als die nach der Sulfurierung (das Produkt ist AS-GO). Verschleißschutztests zeigen, dass das aus schwefeldotiertem GO und Octylamin hergestellte SA-GO den kleinsten Verschleißnarbendurchmesser (0,25 mm) im 928-Schmieröl bei einer Konzentration von 1 × 10 −4 . aufweist Gew.-%, da das Additiv einen relativ hohen Graphen-Gewichtsprozentsatz (57,4 Gew.-%), einen hohen Schwefelgehalt (2,49 Gew.-%) und eine gute Dispersität hat (das Octylamin hat eine ähnliche Kohlenstoffkettenlänge im Vergleich zu PAO4 oder dem Grundöl der 928-Schmierung Öl). Verglichen mit dem reinen 928-Schmieröl und PAO4-Öl beträgt der prozentuale Rückgang des Verschleißnarbendurchmessers 43,2% beim 928-Schmieröl und 17,2% beim PAO4-Öl, während das mit Octylamin modifizierte SA-GO mit den Konzentrationen von 2,5 × 10 . angewendet wird −4 Gew.-% in PAO4 und 1 × 10 −4 Gew.-% in 928 Öl bzw. Die tribologische Untersuchung von schwefeldotiertem Graphenoxid legt nahe, dass SA-GO ein wirksames Anti-Verschleiß-Additiv ist.
Methode
Schwefeldotiertes alkyliertes Graphenoxid in diesem Artikel wird durch die chemische Modifikation von Graphenoxid durch P4 . hergestellt S10 und vier Alkylamine (einschließlich Octadecylamin, Laurylamin, Octylamin und Butylamin). Wichtig ist, dass zwei verschiedene Herstellungswege angewendet werden, um schwefeldotiertes alkyliertes Graphenoxid durch gegenseitigen Vergleich zu erhalten. Eine Route, auf der Graphenoxid zuerst mit P4 . reagiert S10 und dann Alkylamine ergibt das Produkt SA-GO, und ein anderer Weg, bei dem Graphenoxid zuerst mit Alkylaminen und dann mit P4 . reagiert S10 gibt das Produkt AS-GO.
Wie in Abb. 11 gezeigt, sollen die Untersuchungen von SA-GO und AS-GO die Beziehung zwischen chemischer Zusammensetzung und Schmierleistung kontrastierend untersuchen. Die detaillierten Versuchsbedingungen werden gemäß dem Herstellungsweg von SA-GO wie folgt beschrieben.
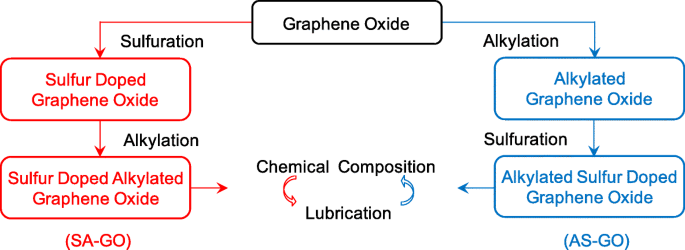
Die kontrastiven Forschungswege von SA-GO und AS-GO
Die Herstellung des schwefeldotierten Graphenoxids
In diesem Artikel wird das schwefeldotierte Graphenoxid durch die Reaktionen zwischen den P4 S10 (chemisch rein) und Graphenoxid, das nach der modifizierten Hummers-Methode hergestellt wird [33]. Die detaillierte Versuchsbedingung wird wie folgt beschrieben:
Drei Chemikalien, 3 g Graphitpulver (3500 mesh, Reinheit> 99,9 wt%, Graphit, das im Papier verwendet wird, ist im Handel von XFNANO Ltd. Co. erhältlich), 1,5 g NaNO3 , und 138 ml H2 SO4 , wurden in einen Dreihalskolben gegeben und 3 min gerührt. Nach dem Überführen in ein Eisbad 3 g KMnO4 (chemisch rein) wurde langsam in die gut vermischte Mischung gegeben, um die Gefahr einer Überhitzung zu vermeiden, dann wurde die Mischung in ein Ölbad gegeben, um unter Rückfluss erhitzt zu werden und 6, 12 bzw. 24 Stunden gerührt.
Die 100 mg Graphenoxid wie hergestellt im obigen Verfahren und 300 mg P4 S10 wurden mit Ultraschall in 20 mL N . dispergiert ,N -Dimethylformamid (DMF) in einem Dreihalskolben. Dann wurde die Mischung in N2 . unter Rückfluss erhitzt Atmosphäre bei 100 °C für 24 Stunden. After that, the temperature was allowed to cool down at room temperature and washed by acetone, alcohol, and DI water while negative-pressure filtration was carried out at the same time.
The Preparation of the Sulfur-Doped Alkylated Graphene Oxide
The as-synthesized sulfur-doped graphene oxide (100 mg) was ultrasonically dispersed in 5 mL DMF and mixed with 20 mL SOCl2 (chemical pure) to react under a refluxing condition at 80 °C for 24 h. After being washed by tetrahydrofuran (THF) for removing SOCl2 , the product ultrasonically dispersed in 2 mL THF which was added with 1 mL alkylamine (octadecylamine, laurylamine, octylamine, and butylamine, respectively), and the system was heated at 80 °C and stirred for 24 h. The light-yellow product, sulfur-doped alkylated graphene oxide, was thoroughly washed and vacuum-dried for further applications.
The Characterization Instruments and Tribological Tests of the Sulfur-Doped Alkylated Graphene Oxide
Products in this paper were characterized by the attenuated total reflection Fourier transform infrared spectroscopy (ATR-FTIR, PerkinElmer Spectra Two), scanning electron microscopy (SEM, Hitachi SU-8000, secondary electron modes, acceleration voltage is 10 kV), transmission electron microscopy (TEM, TECNAI-F20 with accelerating voltage of 300 kV, bright field), selected area electron diffraction (SAED), Raman (Senterra&Veate X70, with excitation argon ion laser at 514.5 nm) and X-ray photoelectron spectroscopy (XPS, Escalab-250Xi; the curve fitting was done by using the Thermo Avantage v4.87 software based on Powell’s iteration method and 100 maximum iterations.), UV-vis spectrophotometer (Thermal Fisher, Genesys180), and TGA measurements were carried out on a TGA 8000 (PerkinElmer) analyzer from 50 to 550 °C under N2 with a heating rate of 10 °C/min.
The 928 aviation lubrication oil (commercially available in Henan Hangcai Science and Technology Co. Ltd.) and poly-α-olefin base oil (PAO, purchased from Shanghai Foxsyn Chemical Science and Technology Co. Ltd.) are applied as lubricants in tribological experiments. All of the sulfur-doped alkylated graphene oil samples were sonicated for 5 min before tribological tests. All of the tribological experiments were performed by a lever-type four-ball tester (Jinan Shijin Group Co. Ltd., MRS-10G and MRS-10P). The rotation speed of MRS-10G is 1450 r/min, the load is 392 N, and the testing time is 30 min; the rotation speed of MRS-10P is 1760 r/min and the testing time is 10 s. Steel balls used in the paper are uniform 12.7-mm GCr15 chrome steel ball which Rockwell hardness is 59-61HRC. The diameter of wear scar was measured by an optical microscope (resolution is ± 0.01 mm). All of the chemicals used in this paper are analytically pure except for the base oils, fully formulated lubricant oils, and the chemicals specifically stated.
Verfügbarkeit von Daten und Materialien
The TG, TEM, and SEM data are available in the Analysis and Measurement Center of China University of Mining and Technology for inspection. The XPS, Raman, and line scanning EDX is available in the Analysis and Testing Center of Tianjin University of Technology for further inspection. Other data are acquired in Air Force Logistics College for inspection.
Abkürzungen
- AS-GO:
-
Sulfur-doped graphene oxide prepared by alkylation and then followed by sulfuration of graphene oxide
- ATR-FTIR:
-
Attenuated total reflection Fourier transform infrared spectroscopy
- BN:
-
Boron nitride
- DMF:
-
N ,N -dimethylformamide
- EDS:
-
Energiedispersive Röntgenspektroskopie
- GO:
-
Graphenoxid
- GO-C12:
-
The alkylated graphene oxide prepared by laurylamine and the sulfur-doped graphene oxide (the oxidation time of the graphene oxide is 24 h)
- GO-C18:
-
The alkylated graphene oxide prepared by octadecylamine and the sulfur-doped graphene oxide (the oxidation time of the graphene oxide is 24 h)
- GO-C4:
-
The alkylated graphene oxide prepared by butylamine and the sulfur-doped graphene oxide (the oxidation time of the graphene oxide is 24 h)
- GO-C8:
-
The alkylated graphene oxide prepared by octylamine and the sulfur-doped graphene oxide (the oxidation time of the graphene oxide is 24 h)
- ILSAC:
-
International Lubricant Standardization and Approval Committee
- JCPDS:
-
Joint Committee on Powder Diffraction Standards
- PAO4:
-
The poly-α-olefin base oil at 100 °C kinematic viscosity is ~ 4 mm 2 /s
- SAED:
-
Ausgewählte Bereichselektronenbeugung
- SA-GO:
-
Sulfur-doped graphene oxide prepared by sulfuration and then followed alkylation of graphene oxide
- SEM:
-
Rasterelektronenmikroskopie
- SiC:
-
Siliziumkarbid
- TEM:
-
Transmissionselektronenmikroskopie
- TGA:
-
Thermogravimetrische Analyse
- THF:
-
Tetrahydrofuran
- UV-Vis:
-
Ultraviolett-sichtbare Spektroskopie
- XPS:
-
Röntgenphotoelektronenspektroskopie
Nanomaterialien
- Graphen-Nanoband
- Mit Titanat-Nanoröhren dekorierte Graphenoxid-Nanokomposite:Vorbereitung, Flammhemmung und Photoabbau
- Biosicherheit und antibakterielle Wirkung von Graphen und Graphenoxid in vitro und in vivo
- Graphenoxid-hybridisierte nHAC/PLGA-Gerüste erleichtern die Proliferation von MC3T3-E1-Zellen
- Bewertung von Graphen/WO3- und Graphen/CeO x -Strukturen als Elektroden für Superkondensatoranwendungen
- Polyanilin-beschichtetes Aktivkohle-Aerogel/Schwefel-Komposit für Hochleistungs-Lithium-Schwefel-Batterien
- Erhöhte Protonenleitfähigkeit und Methanolpermeabilitätsreduktion durch Natriumalginat-Elektrolyt-sulfonierte Graphenoxid-Biomembran
- Niedrigtemperatur-Reduktion von Graphenoxid:Elektrische Leitfähigkeit und Rasterkraftmikroskopie mit Kelvin-Sonde
- Das anionische Tensid/ionische Flüssigkeiten mit interkaliertem reduziertem Graphenoxid für Hochleistungs-Superkondensatoren
- Millstone-Peeling:ein echtes Scher-Peeling für großflächiges, wenige Schichten Graphenoxid