Gichtgas-Recycling-Hochofenprozess
Top-Gas-Recycling-Hochofenprozess
Im Bereich der Produktion von Roheisen (HM) durch Hochöfen (BF) ist die vielversprechendste Technologie zur signifikanten Reduzierung der CO2-Emission (Kohlendioxid) das Recycling von CO (Kohlenmonoxid) und H2 (Wasserstoff) aus dem Gas, das die BF-Spitze verlässt. Der CO- und H2-Gehalt des oberen BF-Gases hat das Potenzial, als reduzierende Gaselemente zu wirken, und daher wird ihre Rückführung zum BF als effektive Alternative zur Verbesserung der BF-Leistung, zur Verbesserung der Nutzung von C (Kohlenstoff) und H2 angesehen den Ausstoß von CO2 reduzieren. Diese „Top-Gas-Recycling“-Technologie (TGR) basiert hauptsächlich auf der Verringerung des Verbrauchs von fossilem C (Koks und Kohle) durch die Wiederverwendung der Reduktionsmittel (CO und H2) nach der Entfernung des CO2 aus dem oberen BF Gas. Dies führt zu einem geringeren Energiebedarf. Aufgrund der Vorteile einer hohen Produktivität, einer hohen PCI-Rate (Pulverized Coal Injection), einer niedrigen Kraftstoffrate und einer geringen CO2-Emission usw.. gilt das TGR-BF-Verfahren als eines der zukunftsträchtigen Eisenerzeugungsverfahren.
Beim TGR-BF wird anstelle von Heißluft Sauerstoff (O2) in den BF geblasen, um Stickstoff (N2) im oberen BF-Gas zu eliminieren. Ein Teil des CO- und H2-haltigen BF-Kopfgases wird in der BF erneut als Reduktionsmittel genutzt. CO2 aus dem BF-Gichtgas wird abgeschieden und gespeichert. Für unterschiedliche Zielsetzungen wurden mehrere Recyclingverfahren vorgeschlagen, bewertet oder praktisch angewendet. Diese Verfahren unterscheiden sich durch (i) mit oder ohne CO2-Entfernung, (ii) mit oder ohne Vorwärmung und (iii) die Injektionsposition.
Das Konzept des TGR-BF (Abb. 1) umfasst viele Technologien, darunter (i) die Injektion der reduzierenden oberen BF-Gaskomponenten CO und H2 in die Schacht- und Herddüsen, (ii) die Senkung des Verbrauchs des fossilen C-Eintrags aufgrund von weniger Koks Rate, (iii) Verwendung von reinem O2-Gas anstelle von heißer Blasluft an der Herddüse (Entfernung von N2 aus dem Prozess) und (iv) Rückgewinnung von reinem CO2 aus dem oberen BF-Gas zur unterirdischen Speicherung.
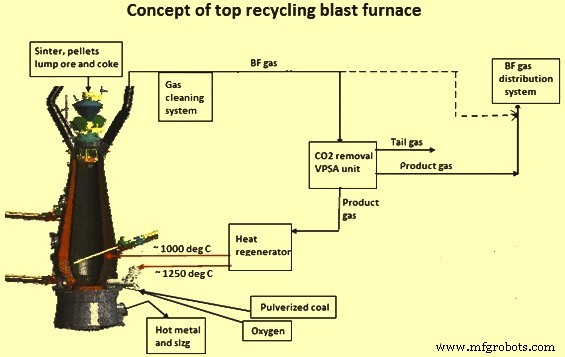
Abb. 1 Konzept von TG-BF
Das Konzept des Gichtgasrecyclings wurde in der experimentellen BF (EBF) des LKAB in Lulea, Schweden, experimentell getestet. Die EBF wurde umgebaut und eine Gastrennanlage basierend auf der VPSA-Technologie (Vakuumdruckwechseladsorption) in der Nähe der EBF errichtet.
Geschichte des BF-Topgasrecyclings
Um die Rate des Reduktionsmittels zu senken und die Produktivität des BF zu erhöhen, wurden während des zwanzigsten Jahrhunderts mehrere neue Konzepte eingeführt, die auf dem herkömmlichen BF-Verfahren basieren.
Bereits in den 1920er Jahren wurde ein Konzept zur Eindüsung des heißen Reduktionsgases in den BF entwickelt. Das geringere Gasvolumen aus den Blasformen im Ofen musste durch die Injektion von vorgewärmtem Reduktionsgas bei 1000 °C mit 27 % CO, 33 % H2 und 26 % N2 in die untere Schachtzone kompensiert werden. Als Ergebnis wurde festgestellt, dass nur 30 % des Kokses (damals 345 kg/tSM) für den BF-Prozess notwendig waren. Mitte der 1960er Jahre wurde diese Idee in Belgien wieder aufgegriffen und Anfang der 1970er Jahre wurden die ersten Versuche an einem BF mit 4,6 m Herddurchmesser in Cockerill-Seraing in Belgien durchgeführt. In den unteren Schacht des BF wurde eine spezifische Menge von 400 N cum/tSM reformiertes Gas, das auf 1000 °C vorgeheizt wurde, eingeblasen. Es wurde ein Austauschverhältnis von 0,22 kg bis 0,26 kg Koks pro N cum Reduktionsgas beobachtet.
Weitere Untersuchungen wurden aus wirtschaftlichen Gründen aufgrund der hohen Erdgaskosten nicht durchgeführt. Ende der 1970er Jahre begannen in Deutschland die Entwicklungsarbeiten für ein neues Verfahren, bei dem die Eindüsung von kaltem reinem O2, Brennstoff und Kreisgas auf zwei Düsenebenen erfolgte. Basierend auf dieser Idee wurde 1984 in Kanada ein Verfahren für einen konventionellen BF ohne zweite Düsenreihe entwickelt. Das Hauptmerkmal dieses Konzepts war das Einblasen von Kohle als Ersatz für Koks. Beide Konzepte wurden nie realisiert und endeten nur als Studie.
Nahezu zeitgleich wurde diese Idee von NKK in Japan weiter genutzt, wo eine zweite Reihe von Blasdüsen in der Schachtmitte installiert wurde. In diese Düsen wurde vorgewärmtes Reduktionsgas, bestehend aus rezykliertem Gichtgas ohne CO2-Entfernung, eingeblasen. Das Gas wurde durch teilweise Verbrennung mit Sauerstoff erhitzt. Kaltes O2, Kohle und kalt zurückgeführtes Gichtgas wurden in die Düsen des Herds eingeblasen. NKK testete das Verfahren in einem experimentellen BF mit 3 Düsen, einem Innenvolumen von 3,9 m³ und einem Herddurchmesser von 0,95 m. Die Kohleinjektionsrate konnte auf 320 kg/tSM erhöht werden, während die Koksrate auf 350 kg/tSM reduziert werden konnte. Die Knappheit an Brenngas im integrierten Stahlwerk aufgrund der Wiederverwertung des obersten BF-Gases stoppte die Entwicklung dieses Verfahrens, da die Preise für elektrische Energie und Erdgas in Japan hoch waren.
Der erste kommerzielle Betrieb eines BF mit Gichtgasrecycling wurde Ende der 1980er Jahre in 12 Kampagnen von RPA Toulachermet in Russland am BF Nummer 2 mit einem Nutzvolumen von 1033 Kubikmeter durchgeführt. Bei diesem Vollkoks-BF-Prozesskonzept wurde heißes und nahezu CO2-freies Topgas zusammen mit reinem O2 in die Herddüsen eingeblasen. Das entkohlte Gichtgas wurde in heißen Öfen auf bis zu 1200 Grad C erhitzt. Mit diesem neuen Verfahren wurden fast 250.000 Tonnen Roheisen (HM) produziert. Die niedrigste erreichte Koksrate betrug 367 kg/tSM, verglichen mit dem Referenzwert von 606 kg/tSM, was eine Reduzierung der Koksrate um 239 kg (39 %) bedeutete. Während dieser Kampagnen wurden schwerwiegende Düsenausbrüche beobachtet, die zu Änderungen im Düsendesign führten. Schwierigkeiten mit dem CO2-Reinigungssystem stoppten schließlich den Prozess. Unter Berücksichtigung dieser Hintergrunduntersuchungen wurde 2004 das Konzept der ULCOS (Ultra Low Carbon Di-Oxide Steelmaking) TGR-BF entwickelt.
Entwicklung von ULCOS TGR-BF
Die Entwicklungsarbeiten wurden in zwei Phasen durchgeführt. In der ersten Entwicklungsphase, die von 2004 bis 2009 lief, wurde das Verfahren als „ULCOS New Blast Furnace Process“ bezeichnet. In dieser Phase wurden drei neue Verfahrenskonzepte entwickelt und getestet. In der zweiten Phase, die 2009 begann und als „ULCOS-Topgasrecycling-Hochofenprozess“ bezeichnet wurde, wurden zwei weitere ULCOS-TGR-BF-Kampagnen durchgeführt.
Bei der Entwicklung wurden Wärme- und Stoffbilanzmodelle sowie ein 3D-Achsensymmetriemodell des BF zur Berechnung der Hauptdaten und des inneren Zustands des Prozesses zur Auswahl der besten Betriebsparameter verwendet. Vier Alternativen wurden definiert und auf die mögliche erreichbare C-Einsparung und die Realisierbarkeit des Betriebs des BF unter diesen neuen Konzepten untersucht. Die Schlussfolgerung war, dass die Alternativen 1, 3 und 4 bei einer hohen Kohlenstaubeindüsung eine Einsparung von fossilem C von 21 % oder mehr erreichen sollten. Alternative 2 wurde aufgrund der geringen zu erwartenden C-Einsparung und der Notwendigkeit der anspruchsvollen Technologie, das Kreislaufgas in zwei Schritten zunächst in einem Rekuperator und dann durch partielle Oxidation weiter aufzuheizen, verworfen. Alle Alternativen umfassten die CO2-Entfernung und die Injektion von CO-reichem Produktgas in die Herddüsen, die Verwendung von reinem O2 und die Injektion von Kohle zusammen mit dem Reduktionsgas. Bei allen Alternativen wurde die Verwendung von Biomasse, teilreduziertem Erz und wasserstoffreichem Gas als Möglichkeit für die Zukunft in Betracht gezogen.
Bei Alternative 1 (Abb. 2) wird das entkarbonisierte Produktgas kalt mit reinem O2 und Kohle an den Herddüsen und heiß an den Schachtdüsen eingeblasen. Ein kritischer Punkt bei dieser Alternative war die geringe Strömungsgeschwindigkeit des kalten Gases auf Höhe der Herddüse, was im Vergleich zum normalen BF-Prozess zu kleineren Kanalgrößen und höheren Flammentemperaturen führte. Außerdem war aufgrund der geringen Gasdurchflussraten ein neues Düsendesign erforderlich.
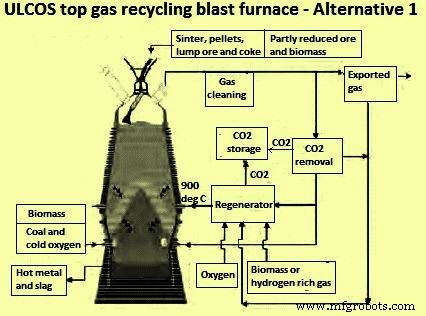
Abb. 2 ULCOS-Gichtgas-Recycling-Hochofen – Alternative 1
Bei Alternative 3 (Abb. 3) wurde das entkarbonisierte Produktgas zusammen mit O2 und Kohle an den normalen Herddüsen heiß eingeblasen. Um eine hohe Kohlenstoffeinsparung zu erreichen, war es notwendig, mit einer niedrigen RAFT (raceway adiabatic flame temperature) und gleichzeitig mit einer hohen Kohleinjektionsrate zu arbeiten.
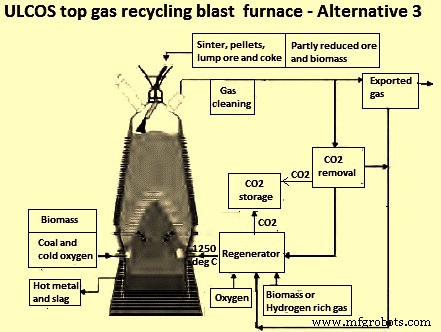
Abb. 3 ULCOS-Gichtgas-Recycling-Hochofen – Alternative 3
Bei der Alternative 4 (Fig. 4) wurde das entkarbonisierte Produktgas heiß an den Herddüsen und heiß am unteren Schacht eingeblasen. Die Temperatur des zurückgeführten Gases variierte von Raumtemperatur bis 1250 Grad C.
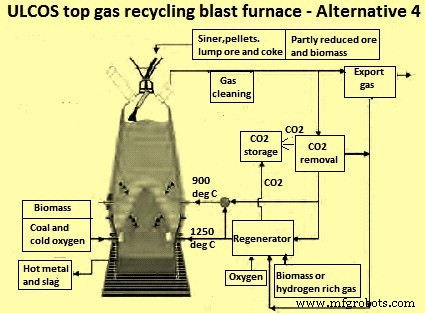
Abb. 4 ULCOS-Gichtgas-Recycling-Hochofen – Alternative 4
Bei den Alternativen 1 und 4 wird Produktgas auch durch Schachtdüsen eingeblasen. Die Unterschiede sind die Gasinjektionstemperatur und die Position der Injektionspunkte. In allen Fällen wurde der geringste Teil des Gases in einem regenerativen System erhitzt. Die erwartete fossile C-Einsparung für Alternative 1 betrug 21 % bei einem Kohlepreis von 170 kg/tSM, Alternative 3 war 24 % bei einem Kohlepreis von 180 kg/tSM und Alternative 4 war 25 % bei einem Kohlepreis von 150 kg/tSM .
Eine mathematische Modellierung der Laufbahnbedingungen und Vergasungstests wurden dann durchgeführt, und es wurden Untersuchungen im Labor- und Pilotmaßstab für die Konstruktion und Konstruktion der Blasdüsen unter den Einschränkungen der gleichzeitigen Injektion von rückgeführtem Gas, reinem O2 und pulverisierter Kohle durchgeführt. Die Geometrie der Düse wurde basierend auf den Ergebnissen der Berechnungen verbessert, um heiße Stellen und Ausfälle während des Betriebs zu vermeiden und einen ausreichenden Impuls des Gasstroms aufrechtzuerhalten, um eine Laufbahn mit ausreichender Tiefe zu bilden.
Kampagnen des TGR-BF-Prozesses im experimentellen BF
Ziel der Versuche war es, den Betrieb des EBF in einem vollständigen TGR-Modus mit reinem O2 und PCI an den Herddüsen zu demonstrieren. Dies wurde unter den drei definierten Alternativen durchgeführt. Die Eisenfracht bestand zu 30 % aus Pellets und zu 70 % aus Sinter. Die Produktionsrate von HM wurde auf einem konstanten Niveau von 1,5 Tonnen pro Stunde gehalten und die PCI-Rate wurde zwischen 130 kg/tSM und 170 kg/tSM variiert. Während der verschiedenen Versuchsperioden wurde die Menge des zurückgeführten Gichtgases maximiert, um eine maximale fossile C-Einsparung zu erzielen. Die bei den Versuchen im EBF gewonnenen Ergebnisse wurden dann mit Modellrechnungen verglichen.
Alternative 3 und Alternative 4 wurden 2007 während der ersten Kampagne nach einem konventionellen Start getestet. Alternative 3 wurde im Herbst 2009 in der zweiten Kampagne auf Optimierung getestet, gefolgt von einem Test von Alternative 1. In der dritten und letzten Kampagne im Jahr 2010 lag der Fokus auf Alternative 4 bei 900 °C. Alternative 4 wurde als geeignet angesehen eine bevorzugte Alternative für das nachfolgende ULCOS BF-Demonstrationsprojekt im industriellen Maßstab. Die 900-Grad-Grenze für die Temperatur des wieder eingespritzten Gases wurde festgelegt, um Probleme der Silica-Reduktion durch H2 der feuerfesten Materialien zu vermeiden.
Während jeder Kampagne wurden in-situ Messungen von Temperatur und Gaszusammensetzung sowie Proben aus dem Möllermaterial mit den beiden Möllersonden aus der EBF entnommen. Zur Untersuchung des Möllermaterialverhaltens unter den neuen Betriebsbedingungen wurden kurz vor Beendigung der Kampagne Körbe mit unterschiedlichen Sinter- und Pelletmaterialien in die EBF eingebracht. Diese Körbe wurden während der Zerlegung des Ofens nach dem Abschrecken mit Stickstoff aus dem EBF geborgen. Dies war während der Kampagnen 2007 und 2010 geschehen. Bei der zweiten Kampagne 2009 konnte aufgrund eines unvorbereiteten Kampagnenendes wegen eines Problems im EBF-Charging-System nur der Quench durchgeführt werden und somit keine Körbe geladen werden.
Während der Kampagnen wurden Proben aus der Kohäsionszone gewonnen und Größe und Form der Laufbahn für weitere Untersuchungen gemessen. Die Kampagnen wurden mit einer Woche konventionellem BF-Normalbetrieb (Heißluftgebläse) mit Sinter gestartet, zunächst zum Aufheizen und thermischen Stabilisieren und dann zum Herstellen einer Referenz für den konventionellen BF-Betrieb. Nach der Referenz wurde angehalten, um das Gebläse abzuschalten und das Produktgas an die Kugelerhitzer (Regeneratoren) anzuschließen. Der Start im TGR-BF-Modus erfolgte durch einen künstlichen Windstoß, bestehend aus kaltem O2 aus den Lanzen und heißem N2 aus den Kugelerhitzern. In sukzessiven Schritten wurde das N2 aus den Kugelerhitzern durch entkarbonisiertes Gichtgas (Produktgas) ersetzt.
Ergebnisse der Kampagnen von ULCOS TGR-BF
Die erste Schlussfolgerung aus den Kampagnen ist, dass das ULCOS TGR-BF-Verfahren betrieben werden kann. Während der Kampagnen mit dem neuen Verfahren sind keine sicherheitsrelevanten Probleme aufgetreten. Der Betrieb der VPSA-Einheit, der zweiten wichtigen Einrichtung, verlief reibungslos und ohne größere Ausfälle. Die mit der VPSA-Einheit gekoppelte EBF hat während der Kampagnen sehr gut funktioniert.
Es muss jedoch beachtet werden, dass der Betrieb der VPSA-Einheit durch die Änderungen der Zusammensetzung des Topgases und des Volumens des Gases aus der EBF beeinflusst wurde. Daher sollten beide Einheiten in einer sehr engen Beziehung betrieben werden. Der während der Kampagnen maximal erreichte Anteil an rezykliertem Gichtgas lag bei rund 90 %.
Während der Kampagnen des TGR-BF-Verfahrens wurde ein stabiler Betrieb des BF mit einem sanften Abfall der Last erfahren, und es war einfach, die thermische Stabilität aufrechtzuerhalten. Die Effizienz des Gases im BF-Schacht war während der verschiedenen Alternativen stabil und es gab eine gute Gasverteilung, wie die Messungen der Schachtsonden im Bürden zeigten. Allerdings kam es während der Kampagnen zu einigen Anlagenausfällen, aufgrund derer die EBF während des Betriebs unter den neuen Prozessbedingungen gestoppt werden musste. Einige lange Unterbrechungen waren erforderlich, um zum Betriebsschritt des „konventionellen Betriebs“ mit künstlichem Heißwind aus kaltem O2 und heißem N2-Betrieb zurückzukehren. Die kleinen Unterbrechungen erforderten nur das Stoppen der Gasinjektion und die Zugabe von etwas zusätzlichem Koks und/oder Kohle.
Nach dem Anfahren mit N2, wenn kein oberes BF-Gas verfügbar ist, könnte das Produktgas innerhalb von etwa 1 Stunde wieder zurückgeführt werden. Alle Probleme wurden wie vorhergesagt gelöst und die thermische Stabilität des BF war nie ernsthaft gefährdet. Während der Kampagne ermöglichten die gesammelten Erfahrungen und das gestiegene Vertrauen, die EBF-Wiederherstellung (auf Produktionsebene) schrittweise zu beschleunigen. Jeweils beim Wechsel der Alternativen (3 auf 4, 3 auf 1) wurde der BF für etwa 8 Stunden angehalten, um die notwendigen Gasanschlüsse an den Schachtdüsen und den Wechsel der Herddüsen herzustellen.
Die auf Laborebene durchgeführten Versuche hatten gezeigt, dass das herkömmliche Möllermaterial für das neue Verfahren kein Problem darstellen würde. Dies wurde während der Kampagnen bestätigt. Mit den Eigenschaften der Beschickungsmaterialien waren keine besonderen Verfahrensprobleme verbunden. Die Ergebnisse sowohl der Sonden als auch der Ausgrabungsproben hatten das Reduktionsprofil eines zentralen Arbeitsofens gezeigt, das sowohl für Sinter- als auch für Pelletproben ein niedriges Reduktionsniveau an der Wand und ein höheres Reduktionsniveau in der Ofenmitte aufweist. Taumelversuche an den Aushubproben hatten ein ähnliches Zerfallsverhalten wie bei einem konventionellen BF-Verfahren gezeigt, das den Laborversuchen entsprach. Aus den Belastungstestarbeiten konnte geschlossen werden, dass die Belastungseigenschaften, wie sie in der heutigen konventionellen BF verwendet werden, kein Problem für das ULCOS TGR-BF-Verfahren zu haben scheinen.
Die während der ULCOS TGR-BF-Kampagnen erzielten Ergebnisse waren hinsichtlich der Einsparung von C (Kohle und Koks) sehr ermutigend. Die Versuche aller drei Kampagnen hatten eine wesentliche Verringerung der Reduktionsmittelrate gezeigt, die durch das Einblasen des entkohlten oberen BF-Gases erreicht wurde. Während der drei Kampagnen sank der Kohle- und Kokseintrag von rund 530 kg/tSM auf 400 kg/tSM, was eine erhebliche Einsparung von C darstellt. Der Kohlenstoffeintrag wurde von 470 kg/tSM auf etwa 350 kg/tSM reduziert, was zu eine C-Einsparung von rund 25 %.
Obwohl Alternative 1 wegen des vorzeitigen Abbruchs der zweiten Kampagne nicht vollständig untersucht werden konnte, betrug die maximale Reduzierung des C-Eintrags über Koks 21 % im Vergleich zum Referenzzeitraum bei konventionellem BF-Betrieb. Für diese Alternative wurde eine neue Düsentechnologie entwickelt. Die Blasdüsenkonstruktion bestand aus koaxialen Rohren, wobei das Innenrohr für die Injektion des Kohlenstaubs und das Außenrohr für die Injektion von O2 verwendet wurde. Die drei verbauten Blasdüsen funktionierten sehr gut und nach der Demontage wurden weder Beschädigungen noch Verschleiß festgestellt. Der VPSA konnte bis zu 88 % des BF-Gichtgases recyceln.
Bei Alternative 3 konnte der C-Verbrauch in der ersten Kampagne um bis zu 15 % reduziert werden bei einer GK-Recyclingquote von rund 72 %. Die Ergebnisse dieser Alternative waren niedriger (ca. 15 %) als aus den Wärme- und Stoffbilanzrechnungen erwartet (24 %), da dies die ersten Erfahrungen mit dem Gichtgasrecyclingmodus waren und das Verfahren nicht optimiert wurde. In der zweiten Kampagne waren die Ergebnisse dieser Alternative deutlich besser, als die maximale Reduzierung des C-Eintrags von etwa 25 % bei einer Gichtgasrückführungsquote von bis zu 90 % erreicht wurde.
Bei Alternative 4 wurde eine C-Einsparung von 24 % bei einer Gichtgasrückführungsquote von 90 % erreicht. Beim Koks- und Kohleverbrauch konnten im neuen Verfahren (Alternative 4) gegenüber der Referenzbetriebszeit bis zu 123 kg/tSM eingespart werden. Aus diesen Ergebnissen konnte eine gute Korrelation zwischen der eingespritzten Gasmenge (CO+H2) und der Reduzierung der Reduktionsmittelrate bestimmt werden. Der C-Eintrag über Koks und Kohle konnte um durchschnittlich 17 kg pro 100 N cum Gas (CO+H2) injiziert werden.
Die Kampagnen von EBF haben bewiesen, dass es möglich ist, einen BF-Prozess mit einem viel niedrigeren Verbrauch an fossilem C zu betreiben, verglichen mit dem Verbrauchsniveau des heutigen BF. Durch die Eindüsung des reduzierend entkarbonisierten Gichtgases wurde eine C-Einsparung von bis zu 25 % nachgewiesen. Dies ist ein signifikanter Rückgang im Vergleich zum derzeit am besten betriebenen BF-Prozess. Tatsächlich wird erwartet, dass die Anwendung der BF-TGR-Technologie auf moderne BF zu einer Reduzierung des C-Verbrauchs von derzeit etwa 405 kg C/tSM auf ein Niveau von etwa 295 kg C/tSM führt.
Die VPSA-Einheit hat stabil funktioniert. Es wurde festgestellt, dass die VPSA-Einheit 97 % des Topgases aus dem BF behandeln konnte. Der durchschnittliche Volumenanteil von CO2 im eingeblasenen Gas lag bei etwa 2,67 % und die CO-Rückgewinnungsrate bei 88 %, was die Anforderungen an Quantität und Qualität erfüllte. In Kombination mit VPSA- und CCS-Einheiten könnten die durch das TGR-BF-Verfahren reduzierten CO2-Emissionen 1270 kg/tSM erreichen, was 76 % der gesamten CO2-Emissionen im Eisenherstellungsprozess ausmacht. 24 % des reduzierten CO2 wurden durch Gasrecycling erzielt, und die anderen 52 % wurden durch CCS transportiert und unterirdisch gespeichert.
Aus Prozesssicht kann festgestellt werden, dass der ULCOS-Betrieb stabiler ist als der konventionelle BF-Betrieb, was Temperatur und Qualität des HM betrifft. Dies scheint im Wesentlichen auf den geringeren Einfluss der Lösungsverlustreaktion im Zusammenhang mit den viel niedrigeren Niveaus der direkten Reduktionsrate (DRR) zurückzuführen zu sein. Der niedrigste beobachtete Wert dieser DRR beträgt 5 %. Aus den Betriebsergebnissen ergab sich kein Hinweis darauf, dass dies tatsächlich der Mindestwert war, der in ULCOS TGR-BF erreicht werden konnte. Die Qualität von HM wurde stark durch den Betrieb von ULCOS TGR-BF beeinflusst. Insbesondere wurde eine deutliche Abnahme des Siliziumgehalts (mehr als 1 % absolut) und eine korrelative Zunahme des C-Gehalts beobachtet. Es muss jedoch darauf hingewiesen werden, dass der Siliziumgehalt im konventionellen BF-Betrieb viel geringer ist (ca. 0,5 % im konventionellen BF gegenüber ca. 2,0 % im EBF), und daher keine so große Änderung während der Anwendung des ULCOS zu erwarten ist BF-TGR-Prozess im industriellen Maßstab.
Die Testkampagnen von ULCOS TGR-BF haben gezeigt, dass das neue TGR-BF-Verfahren machbar und einfach zu bedienen ist. Es kann mit guter Sicherheit, hoher Effizienz und starker Stabilität betrieben werden. Die Testkampagnen haben bewiesen, dass es möglich ist, den EBF-Betrieb zwischen 4 Betriebsarten (konventionell, Alternativen 1, 3 und 4) umzuschalten. Außerdem wurde nachgewiesen, dass es möglich ist, den BF-Prozess und die Gastrennanlage VPSA im geschlossenen Kreislauf zu betreiben. Die erhaltenen C-Einsparungen stimmten mit den Vorhersagen aus den Berechnungen des Flussdiagramms überein. Die Tests zeigten auch, dass herkömmliche Füllmaterialien wie Sinter, Pellets und Koks für das ULCOS TGR-BF-Verfahren geeignet sind.
Basierend auf den Erfahrungen aus EBF-Kampagnen sind die Punkte, die für eine sichere und nachhaltige industrielle Anwendung des ULCOS TGR-BF-Verfahrens beachtet werden müssen, (i) das Risiko eines Gasaustritts auf der Düsenebene kann erfordern, dass die Düsenebene physisch von der Gießerei getrennt ist Brandschutz, (ii) Leckagerisiko durch Biegen der Flansche bei hohen Temperaturen, (iii) Verlängerung des Schornsteins durch heiße Öfen/Heizungen, um giftige Gase in der Umgebung zu vermeiden, (iv) zur Vermeidung von Ausfällen in der Startphase , das Betriebspersonal muss während des Funktionstests mit Kunstgas geschult werden, (v) optimale Einspritzparameter sind wichtig, um Ablagerungen/Verstopfungen an der Blasdüsennase zu vermeiden, (vi) Wichtigkeit einer individuellen Steuerung des Strahlstroms zu den Blasdüsen, um Ablagerungen zu vermeiden von zu viel O2 und Kohlenstaub in der Blasdüse bei Verstopfung, (vii) Auswahl des Feuerfestmaterials und Herstellung von Feuerfestteilen geändert und die Verwendung von Ankern aus C-Stahl nach Möglichkeit vermieden werden, alternativ Es müssen grundsätzlich andere Materialien als C-Stahl oder mit Aluminiumoxid beschichteter Stahl verwendet werden, und (viii) es ist wichtig, Metallstaubbildung durch eine sorgfältige Auswahl von Metallteilen zu vermeiden.
Die Testergebnisse haben gezeigt, dass die Alternative 4 die beste Wirkung bei der Emissionsreduzierung hatte und als erste Wahl für die Erprobung im industriellen BF während der nächsten Stufe ausgewählt wurde.
Herstellungsprozess
- Prozessautomatisierungs-, Mess- und Steuerungssystem für Hochöfen
- Erzeugung und Nutzung von Hochofengas
- Verwendung von Nusskoks in einem Hochofen
- Einblasen von Kohlenstaub in einen Hochofen
- Hochofen Unregelmäßigkeiten während des Betriebs
- Kühlsystem für Hochöfen
- Beschickungssysteme für Hochöfen
- Chemie der Eisenherstellung im Hochofenverfahren
- Feuerfeste Auskleidung des Hochofens
- Gasschweißverfahren verstehen